Rijesh M.1, James Valder2, Jithin D.1, Dileep C. R.1, Abin R. N.1, Shibin F.1, Havila M. M.1
1Department of Metallurgy, Amal Jyothi College of Engineering, Koovapally, Kanjirapally, Kerala
2Department of Mechanical Engineering, St. Joseph Engineering College, Mangalore, Karnataka
Correspondence to: James Valder, Department of Mechanical Engineering, St. Joseph Engineering College, Mangalore, Karnataka.
Email: |  |
Copyright © 2016 Scientific & Academic Publishing. All Rights Reserved.
This work is licensed under the Creative Commons Attribution International License (CC BY).
http://creativecommons.org/licenses/by/4.0/

Abstract
Aluminium matrix composite with aluminium dioxide as a reinforcement has gained wide popularity because of their high physical, mechanical and other desirable characteristics like high thermal conductivity, low coefficient of thermal expansion and low density. They have a wide verity of applications in the emerging fields like automobile, aerospace, biomedical and industrial purposes. In the present study Al/Al2O3 particulate metal matrix composite was processed by conventional powder metallurgy route. A customized punch and die was fabricated using EN-8 grade steel and composite with different weight % of Al2O3 particle (5, 10 & 15 weight % of Al2O3) were compacted in it. The green compacts were sintered in a furnace with optimum temperature and time for densification. The composites manufactured were subjected to tungsten inert gas welding without any filler. The microstructure and macrostructures were analyzed to study the feasibility of fusion welding. The microstructures in the base metal and fusion zone reveal a decrease in volume fraction of Al2O3 in the fusion zone. The cause for this phenomenon was investigated.
Keywords:
Aluminium matrix composites, Fusion welding, Microstructure
Cite this paper: Rijesh M., James Valder, Jithin D., Dileep C. R., Abin R. N., Shibin F., Havila M. M., Production of Al-Al2O3 MMC by P/M Route and to Study the Feasibility of Fusion Welding, American Journal of Materials Science, Vol. 6 No. 4A, 2016, pp. 99-101. doi: 10.5923/c.materials.201601.19.
1. Introduction
Aluminium and its alloys are used commonly in aerospace and transportation industries because of their low density and high strength to weight ratio. Especially Al-based Metal Matrix Composites (MMC) exhibit high strength, high elastic modulus, and improved resistance to fatigue, creep and wear; which make them promising structural materials for many industries [1]. However, in comparison with other materials such as ferrous alloys, their strength and stiffness are still inferior. Improvement of aluminium alloy can be done by several ways such as new alloy design, heat treatment, or reinforcement with various materials in a matrix to manufacture a composite material. Welded components and structures are widely used in almost all industries. Present day engineering industries relies heavily on welded components and structures. Therefore, weld integrity becomes important for adequate and reliable performance of components, structures, and plants. Weld integrity is dependent on the base material, specifications, and welding processes. With the ever-increasing sophistication of processes, materials, and specifications, one must have a broad, comprehensive knowledge of the metallurgy of welding processes. Fusion welding of MMCs has been found difficult because of difference in properties of the base matrix and the particulate reinforcements. All these provide hindrances in effective and reliable weld joints in composites. For instance, concerns such as solidification defects due to difference in the densities of the aluminum matrix and the reinforcement, chemical reactions when subjected to prolong heating during welding, and lastly, precise and accurate weld preparation to avoid tear out or cracking have limited their applications [2].In the present study processing of an aluminum metal matrix composites (Al-MMC’s) reinforced with aluminium dioxide by powder metallurgy route was carried out and further it was fusion welded. The welding process and its impact on the microstructure were analyzed.
2. Experimental Procedure
A die and punch with a circular cross section of 15 mm was designed and fabricated using EN - 8 grade steel. Particle size analysis of the powders (Al & Al2O3) was carried out by metallographic method. Al & Al2O3 were mixed in a mortar and pestle along with zinc stearate which is a binder as well as a lubricant to produce 3 different compositions of composites which is shown in Table 1. The mixture was cold compacted using a die of 15 mm diameter under a pressure of 340 MPa, and subsequently sintered at 600°C for 2 hrs (Figure 1). The composite pellets which were produced by powder metallurgy were chamfered to obtain a V-groove and were held at a gap of 1 mm. TIG welding was carried out on the specimens at 17.2 V at a speed of 2 mm/s without a filler rod. Microscopic examination of the parent composite, fusion zone and the interface was carried out to study the feasibility of fusion welding for the same. 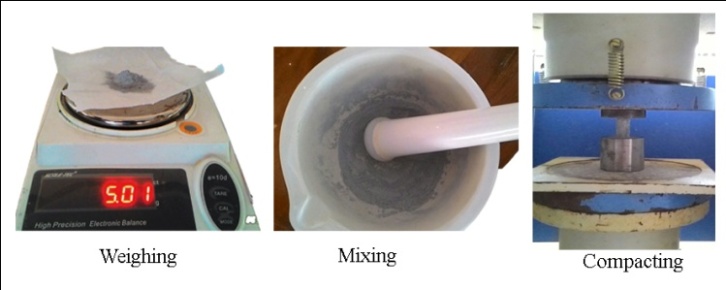 | Figure 1. Different stages of composite manufacturing |
3. Results and Discussion
Microstructural analysis of composites Figure 2 shows the microstructure of Al-Al2O3 with various wt % of Al2O3 (5, 10&15). The microstructure reveals uniform distribution and no preferential alignment of Al2O3 particles in the matrix.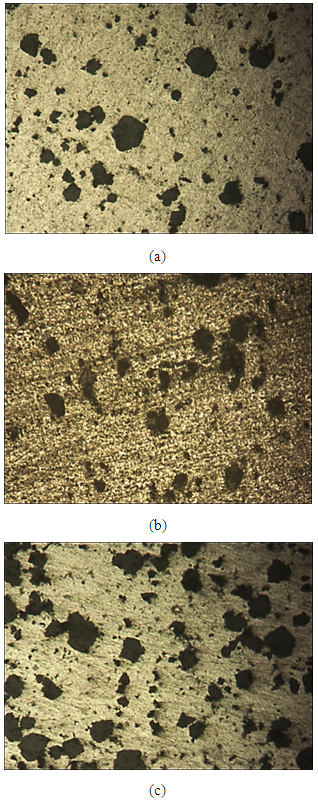 | Figure 2. Microstructure of Al-Al2O3 composites with (a) 5wt % Al2O3 (b) 10 wt % Al2O3 and (c) 15 wt% Al2O3 observed at 100 X magnification |
A.A. Mazen and A.Y. Ahmed [3] studied processing these composites at different wt% of reinforcement and found similar results. It can be evidently seen that as the wt % reinforcement increases the volume % of Al2O3 increases proportionately.Figure 3 shows the weld composite interface of the entire three composites selected for the study.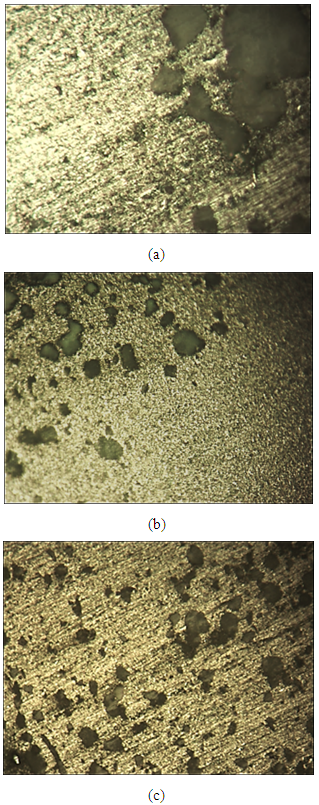 | Figure 3. Microstructure of weld - composites interface for (a) 5wt % Al2O3 (b) 10 wt % Al2O3 and (c) 15 wt% Al2O3 observed at 100 X magnification |
From the microstructure, it can be clearly observed a clumping of Al2O3 at the interface of fusion zone and only a little amount of Al2O3 particles has flown into the fusion zone. As the weight percentage of Al2O3 increases the flowability increased slightly. This can be an inferior weld and do not possess sufficient strength at the fusion zone. This may be due to the dissociation of Al2O3 to Al during TIG welding process [4]. But under certain conditions deterioration of reinforcements can be avoided. Energy density plays an important role in deterioration and peak temperature in the molten pool is related to energy density, it is obvious that deterioration is directly linked with the temperature achieved in the pool [5]. Thermodynamics calculations to determine the stability of Al2O3 at various temperatures are recommended for proper fusion welding of composites. Effect of particle size of reinforcement on flowabilty into the fusion zone is also to be investigated.Table 1. Compositions selected for the study 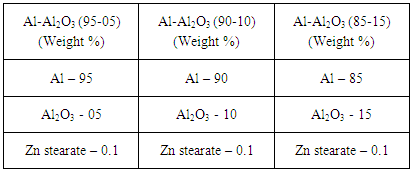 |
| |
|
4. Conclusions
The tendency of degradation of Al- Al2O3 composites was observed during TIG welding. It is suggested to control of peak temperature to avoid the degradation of reinforcements and to obtain a quality weld during TIG. Control of particle size of reinforcement is also suggested for a good weld.
References
[1] | Kok, M., 2005. Production and mechanical properties of Al2O3 particle-reinforced 2024 aluminum alloy composites. J. Mater. Proc. Tech. 161, 381–387. |
[2] | A. Chidambaram, S.D. Bhole, Particle Denuded Zones in Alumina Reinforced Aluminum Matrix Composite Weldments, Scripta Materiala, Vol. 35, No.3, pp. 373-378, 1996. |
[3] | Mazen A.A. and Ahmed A.Y.’Mechanical Behaviour of Al-Al2O3 MMC Manufactured by PM Techniques Part I’—Scheme I Processing Parameters, Journal of Materials Engineering and Performance volume 7:393-401, 1998. |
[4] | M.B.D. Ellis, M.F. Gittos, and P.L. Threadgill: The Welding Institute, Report No. 501/1994, The Welding Institute, Cambridge, UK, 1994. |
[5] | D. Storjohann, O.M. Barabash, S.S. Babu, S.A. David, P.S. Sklad, E.E. Bloom, Fusion and friction stir welding of aluminum metal–matrix composites, Metall. Mater. Trans. A, 36A (2005), pp. 3237–3247. |