Zbigniew Stepien1, Wieslawa Urzedowska1, Jan Czerwinski2
1Oil and Gas Institute, 31-429, Krakow, Poland (INIG)
2University of Applied Sciences, 2501 Biel-Bienne, Switzerland (AFHB)
Correspondence to: Jan Czerwinski, University of Applied Sciences, 2501 Biel-Bienne, Switzerland (AFHB).
Email: |  |
Copyright © 2012 Scientific & Academic Publishing. All Rights Reserved.
Abstract
In the Diesel sector the fatty acid methyl esters (FAME’s) – in Europe mostly RME *) (rapeseed methyl ester) and in US mostly SME (soja oil methyl ester) – are used as a various share, % volume blends with the Diesel fuel (B5, B7, B10, B20, Bxx). The present joint project focuses on RME being the most important representative of the biofuels of 1st generation in Europe. The influences of RME blend fuels on emissions and on lube oil deterioration are emphasised.Emissions were investigated on a modern engine with exhaust gas aftertreatment devices like SCR and (DPF+ SCR) with blend fuels containing different share of RME (B7, B20, B30 & B100).The most important findings are:•the increased share of RME w/o aftertreatment causes an increase of NOx by higher engine load and reduction of CO & HC; at transient operation (ETC) these tendencies are less pronounced and only B100 shows an increase of NOx,•with SCR alone there are no differences of NOx and of NOx reduction rate (KNOX) with increasing RME portion; there is lowering of CO & HC,•with DPF+SCR KNOX-values are slightly higher, than with SCR alone, due to the production of NO2 in the catalytic DPF (upstream of SCR),•there is excellent count filtration efficiency of DPF, up to 99.9%; with SCR alone there is usually a small reduction of nanoparticles concentrations (in the range of 10-20%, similar like an usual oxidation catalyst).The paper describes as well significant problems related to the influences of biofuels on engine lube oils deterioration demonstrated by monitoring the engine lube oil aging during its operation in heavy duty (HD) and modern high speed direct injection (HSDI) light duty (LD) engine through the bench tests. Increasing usage of Diesel biofuels has an impact on accelerated degradation of engine oil performance. On the basis of the obtained results it can be stated that:•the presence of bio-components in the fuel has significant impact on multidirectional hastening of engine lube oil destruction processes,•kind of base lube oil, lube oil additives components and RME-portion, as well as engine design and its operating conditions are very essential factors influencing the engine lube oil performance degradation,•the processes taking place in an engine lubricant, adversely influence the limited possibilities of bio-componentsevaporation from engine lube oil and contribute to initiation of accelerated, deeper engine lube oil oxidation and degradation. Oxidation causes the oil to thicken, to form acids and generally to lose the lubrication qualities which are important for engine performance. The aged lube oil shortens the engine life by creation deposits on engine pistons, in combustion chambers and on valves, stucking rings and provoking the bore polishing.
Keywords:
Bio Diesel, Emissions, Lube Oil Quality, SCR with Bio Diesel, Engine Testing, Lube Oil Testing
Cite this paper: Zbigniew Stepien, Wieslawa Urzedowska, Jan Czerwinski, Research on Engine Lube Oil Deterioration and Emissions of Diesel Engines with BioFuels (RME), Energy and Power, Vol. 4 No. 1A, 2014, pp. 32-49. doi: 10.5923/s.ep.201401.03.
1. Introduction
The removal of NOx from the lean exhaust gases of Diesel engines (also lean-burn gasoline engines) is an important challenge. Selective catalytic reduction (SCR) requires and uses a supplementary substance – reduction agent – which in presence of catalysts produces useful reactions transforming NOx in N2 and H2O. The preferred reduction agent for toxicological and safety reasons is the water solution of urea (AdBlue), which due to reaction with water (hydrolysis) and due to thermal decomposition (thermolysis) produces ammonia NH3, which is the real reduction substance.A classical SCR deNOx system consists of 4 catalytic parts:• precatalyst converting NO to NO2 (with the aim of 50/50 proportion)• injection of AdBlue (with the intention of best distribution and evaporation in the exhaust gas flow)• hydrolysis catalyst (production of NH3)• selective catalyst (several deNOx reactions)• oxidation catalyst (minimizing of NH3 slip)The main deNOx-reactions between NH3, NO and NO2 are widely mentioned in the literature[1, 2, 3, 4]. They have different rate according to the temperatures of gas and catalysts, space velocity and stoichiometry. All these influences cause a complex situation of reactions during the transient engine operation.Additionally to that there are temperature windows for catalysts and cut off the AdBlue-injection at low exhaust gas temperatures to prevent the deposits of residues.Several side reactions and secondary substances are present. An objective is to minimize the tail pipe emissions of: ammonia NH3, nitrous oxide N2O, isocyanic acid HNCO and ammonium nitrate NH4 NO3 (also known as secondary nanoparticles).The combination of particle filtration (DPF) and of the most efficient deNOx technology (SCR) is widely considered as the best solution, up to date, to minimize the emissions of Diesel engines[5].It is important that modern internal combustion engines need to be made tolerant to alternative fuels and multi fuel blends, and to the use of efficient, fuel-compatible lubricants.Biodiesel, especially in form of biodiesel fuel blends, as an alternative, renewable fuel is a partial replacement of petroleum Diesel as a pathway to energy diversity and reduced petroleum dependency in the transportation sector. Due to numerous, well known advantages as for example renewability, high lubricity, high flashpoint, low sulphur content and no aromatics, good biodegradable property, non-toxic, relatively high cetane number, lower particulate exhaust emissions and life cycle CO2 emissions in compa- rison with Diesel fuel derived from mineral oils, biodiesel is regarded as a fuel of the nearest future. In Europe rapeseed methyl ester (RME) is the most common sort of fatty acid methyl ester (FAME), which according to newest standard EN 590:2009 can be blended with standard Diesel fuel in a portion of up to 7% (V/V).For use of biocomponents the limiting of impurities and phosphorus in biofuels according to the present standards is an obligatory prerequisite for successful operation.Unfortunately beside undoubted advantages, biodiesel has many disadvantages, a part of which is attributed to dilution of engine lube oil, and consequently oil related failures of engines. Usually the oil breakdown is promoted by oxidation and polymerization of unsaturated fuel constituents. So, a serious threat to engine is the possibility that unburnt biodiesel entering the oil sump may be oxidized, thus promoting lubricant degradation and thickening sometimes by severe sludge precipitation and significant loss of its dispersion. On the other hand, oil thinning may be due to fuel dilution or share of polymers used as viscosity modifiers. Apart from that, certain metals such as copper and lead become leached from bearings due to biodiesel fuel in the lubricating engine oil. Since the state of oil deterioration depends also on operation conditions, oil performance grade, engine type and its service, the life span of engine oil is until now not well understood. There are limited data concerning how the FAME might interact with lubricating oil additives either in the bulk of the lubricant or in thin film on metal surfaces influencing the lubricating oil performance changes. Possibility of incompatibility problems emergence between the crankcase lubricants and the biofuels additives should be also further clarified by studying the complicated physicochemical processes between modern engine lube oils and biofuels[6, 7, 8]. Essential is the additional search and enhanced, extended or new evaluation test methods. To determine when and how the engine lubricants properties have been depleted in the research work described in this paper different methods were applied: standard oil analysis, in house developed innovative methods, analysis of engine lubricants oxidation stability tests, thin lubricant film oxidation tests and bulk lubricant oxidation tests.The present paper shows some results of research of SCR-and (DPF+SCR)-systems with different rates of biocomponents (RME). Taking into account the above indicated issues a research program about the impact of biofuels on engine lube oils deterioration was performed.
2. Tested Engines, Fuels, Lubricants
The tested engines and engine data are represented in Fig. 1 and Table 1.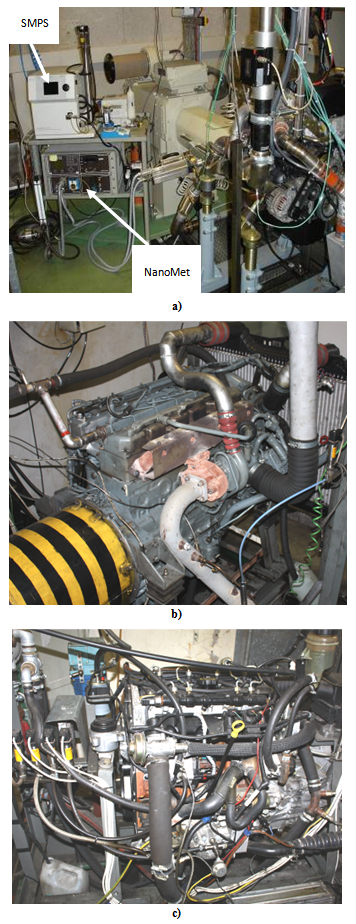 | Figure 1. Tested engines. a) IVECO and aparatus for nanoparticle analytics SMPS & NanoMet at the University of Applied Sciences, Biel-Bienne, Switzerland, b) MAN and c) FORD, engines used for lube oils aging at the Oil and Gas Institute, Krakow, Poland |
Table 1. Specifications of tested engines 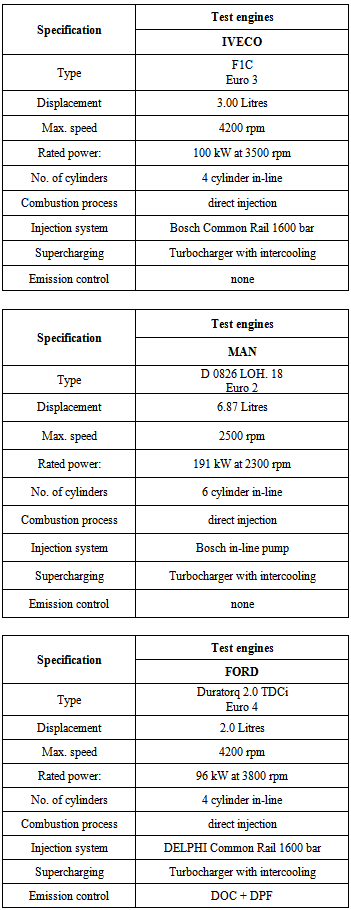 |
| |
|
For the research of Diesel biofuels influence on emissions of a Diesel engine with SCR were used four blend fuels containing different share of RME (B7, B20, B30 & B100). Following base fuels were used for preparation of above fuels:•Shell Formula Diesel fuel Swiss market summer quality (10 ppm S) according to SN EN 590•Rapeseed Oil Methyl Ester RME from Flamol, Berne, CHFor testing of Diesel biofuels influence on engine lube oils deterioration was used a typical polish commercial low sulfur (up to 10 ppm S) Diesel fuel meeting requirements of EN 590 standard and containing 3,5 % (V/V) RME meeting requirements of EN 14214 standard. This fuel has been utilized to prepare three test blend fuels containing different share of RME (B7, B20 & B30).Quality diversification in respect of oxidation and thermo-oxidation stability has been postulated as a selection criterion of engine lube oils tests. The engine lube oil quality determined by above performance properties is both dependent on oil base stock composition and properties of improver additives package. Selected lubricating oils met tested engines Original Equipment Manufacturers (OEM) requirements.For the tests following engine lube oils have been received:•For HD Diesel engine (MAN D 0826. LOH 18) has been selected fully mineral lubricating oil SAE 15W-40 blended in API Group I base stock and fulfilled the requirements of ACEA A2-96/B2-98/E2-96; API CG-4/SJ; CCMC D4/PD-2/G4 standards. That lubricant is denoted as “OM”. The second lubricating oil for this HD engine was fully synthetic lube oil SAE 5W-40, blended in API Group IV (PAO) base stock, and fulfilled the requirements of ACEA E5/E4/E3; API CI-4 PLUS/ CI-4/CH-4/CG-4/ CF/SL/SJ; JASO DH-1 standards. That lubricant is denoted as “OS”.•For LD HSDI Diesel engine (FORD Duratorq 2.0 TDCi) two lubricating oils have been selected for tests. The first was mineral lubricating oil SAE 5W-30 blended in API Group II+ base stock (from hydrocracking) and fulfilled the requirements of ACEA A-1/B-1; API SL; ILSAC GF- 3 standards. That lubricant is identified as “OMH”. The second lubricating oil for this LD engine was synthetic oil SAE 5W-30, blended in mixed API Group IV (PAO) base stock (25%) and API Group III base stock (75%), and fulfilled the requirements of ACEA A-1/B-1 standards. That lubricant is identified as “OSS”.
3. Instrumentation for Emissions Testing
Engine dynamometer and test equipment for emissions measurements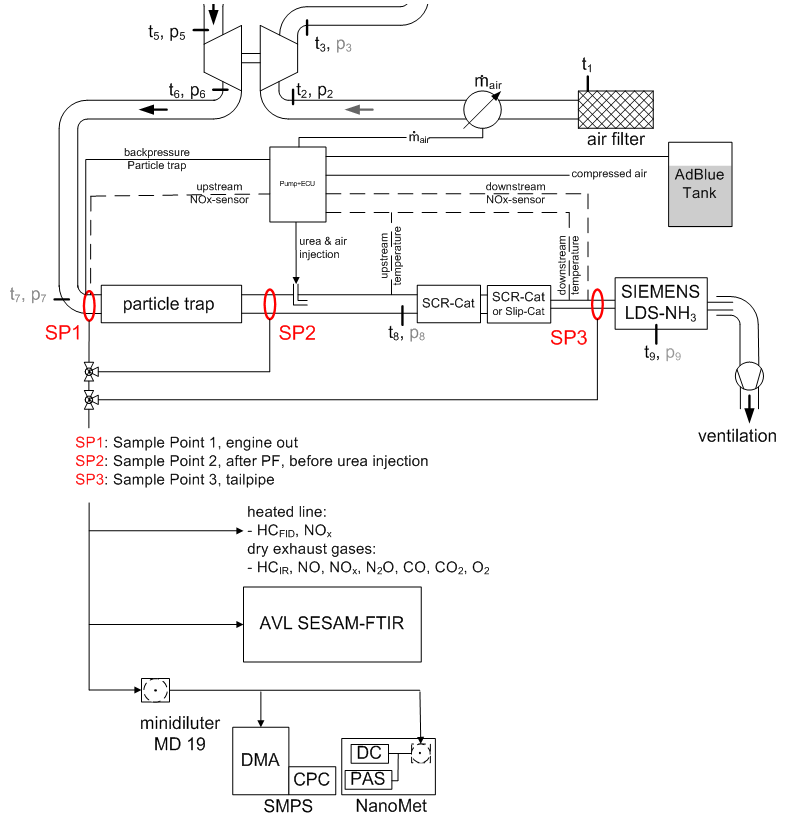 | Figure 2. Emission measuring equipment on engine dynamometer |
Fig. 2 represents the special measuring systems installed on the engine, or in its periphery for analysis of the regulated and unregulated emissions. Laboratory equipment employed:•Dynamic test bench•Exhaust gas components: CO2, CO, HCIR, O2, HCFID, NO, NOx, CLD•FTIR (Fourier Transform Infrared) Spectrometer with the possibility of simultaneous, time-resolved measurement of approximate 30 emission components – among those validated are: NO, NO2, NOx, NH3, N2O.The particle size and number distributions were analysed with SMPS – Scanning Mobility Particle Sizer, TSI (DMA TSI 3071, CPC TSI 3025 A).The nanoparticle results represented in this paper are obtained with sampling at tail pipe with MD19 tunable minidiluter and with thermoconditioner (300°C).
4. Test Procedures
4.1. Emissions
In the present work a 7 steps-test at 2200 rpm was used, Fig. 3a. The operating points were chosen in such way that the urea switch-on was included in the test (between 20% and 30% load).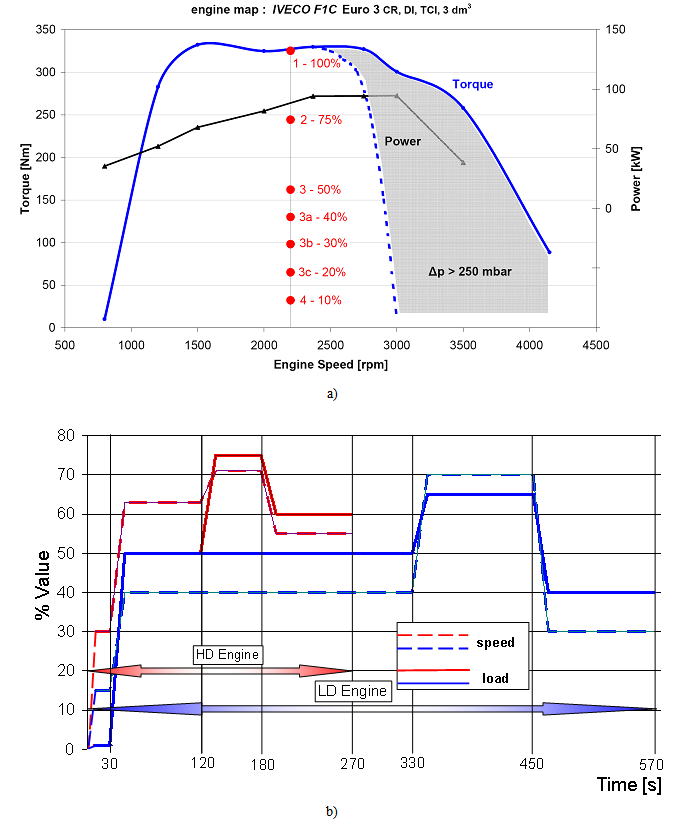 | Figure 3. Engine test operating conditions. a) limited engine map of the IVECO engine and 7 points test for investi- gations of emissions, b) engine test cycles for aging of investigated lube oils |
As sampling position (SP3) was used (see Fig. 2) for all variants with/without exhaust gas aftertreatment.The dynamic testing was performed according to ETC (European Transient Cycle), which in this work was defined on the basis of the non limited engine operation map (NEM).The tests were driven after a warm-up phase, when the engine coolant temperature and lube oil temperature reached their steady-state values (stationary points tests).Before the start of each dynamic cycle the same procedure of conditioning was used to fix as well as possible the thermal conditions of the exhaust gas aftertreatment system.The conditioning was: 5 min pt. 1 and 0.5 min idling.The test program consisted of:•test procedures: steps-test at 2200 rpm and ETC (NEM);•aftertreatment systems: without, with (DPF+SCR), or with SCR only.
4.2. Lube Oils
Taking into account the necessity of creation of conditions promoting lubricating oil aging, a HD Diesel engine, which favors oil deterioration, was chosen. The employed LD Diesel engine applied common rail injection system. The late injection events used as a regeneration strategy for DPFs, increased the opportunity for unburned fuel to reach the cylinder walls, to enter the lubricating oil and to promote its deterioration. The total time of engine oil aging test for both engines was similar. It has been established for about 200 hours taking the oil consumption quantity into consideration. During endurance engine tests, oil was sampled at regular intervals which were concentrated closer to the end of the test.Simulating tests for both engines were configurated as a repeatable four mode tests conducting for different engine loads and speeds, reflecting engine operating conditions during city driving. The endurance engine tests cycles are given on the Fig. 3b.
5. Tested Exhaust Gas Aftertreatment Systems
The combined exhaust gas aftertreatment system (DPF+SCR) was installed on the IVECO research engine in the ICE-laboratory in Biel, CH. This system is designed for dynamic on-road applications.The filters and catalysts are exchangeable modules, for SCR alone the DPF modulus was removed.The investigated combinations were: a coated Cordierite DPF upstream and Vanadium based SCR catalyst downstream of the urea injection point (see scheme Fig. 2).Additionally to the elements in the engine exhaust system an Ad Blue-tank and Ad Blue injection unit with pump, sensors and electronic control were installed in the laboratory.There are following sensors, which enable the open-loop control of urea dosing:•2x Temperature sensors (PT200)•1x Ad Blue level sensor•1x Mass Air Flow sensor•2x NOx sensors (upstream & downstream DPF).Urea dosing and control unit has an open loop control.Optional: GPRS Flight recorder enables:•data logging of system performance, state and alarms on a remote server/database•changing and checking of configuration parameters of urea dosing unit via internet.The SCR-system, which was investigated in the present work, is without mixer (only mixing tube 1.0 m).The DPF has a VERT-conform filtration quality, in average for NP filtration efficiency FE > 99%.
6. Oil Analysis Methodology
For laboratory analysis of the engine lubricating oils and their quality deterioration assessments during engine operation several standardized tests and methods have been accepted. So, determination of physicochemical properties of engine oils monitored under service conditions included: kinematic viscosity, TBN, TAN, dispersion degree of degradation products, wear metals levels and fuel dilution level of crankcase oil.These widely used analyses gave some basic information about the engine lubricants quality changes in use. Unfortunately the kit of lubricating oil deterioration indicators obtained on the base of the above determined physicochemical properties is very often not sufficient for proper, reliable assessment. Therefore, additional determination methods were applied about: oil soot content according to DIN 51-452, high temperature dynamic viscosity (HTHS) under CEC L-36-90 and carbon residue under EN- ISO 103070. Beside conventional test methods for the analysis of used lube oils a few additional, in house developed or enhanced innovative methods were utilized in this study. These methods allowed for comprehensive analysis of engine lubricants oxidation stability tests including thin lubricant film oxidation tests and bulk lubricant oxidation tests. In conditions, which occur between the piston ring and liner or between cam and cam follower the engine lubricating oil is exposed to particularly high heat load and is subject to exacerbated thin film accelerated oxidation. To evaluate the thin film oxidation stability of lubricants aged in engine tests a modified version of ASTM D 4742 procedure has been developed. The purpose of this modification was adoption of the procedure for evaluation of Diesel engine lubricating oils in the appropriate scope of the investigated parameters. Oxidation stability of engine lubricating oils was also evaluated in ASTM D 7545 modification test of (PetroOXY).Since a FT-IR spectroscopy has become a routinely used technique to analyze used oils the FTIR spectroscopic “In-house” O&GI test method 91.06, based on the ASTM E 2412-04 standard was applied. In these tests the large soot content is a cause of serious difficulties because the samples have very low transparency in measured IR region. The use of centrifuge for the soot removing from sample did not give satisfied results because the removing of soot was incomplete, but measurements were easier because the soot background was lowered.
7. Results
7.1. Emissions
The increased share of RME w/o aftertreatment causes in steps-tests: increase of NOx by higher engine load, reduction of CO & HC (here always HCFID) and slight lowering of texh (not represented) – Fig. 4.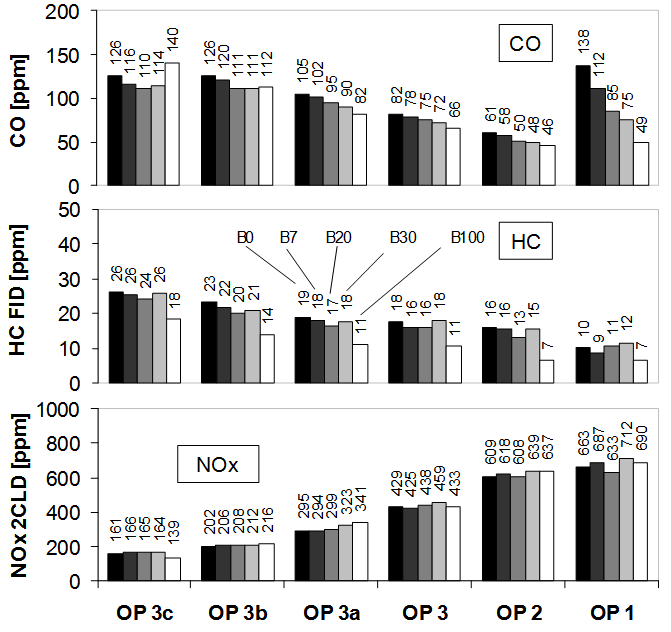 | Figure 4. Limited emissions in steps-test at 2200 rpm with different fuels w/o aftertreatment |
It is to remark that all part load operating points are driven exactly at the same torque and speed. The full load point OP 1 in contrary has always the same speed but the torque results from different heat values of the used fuels. That means the results at OP 1 are overlapped by the effect of different torque.At transient operation in ETC, Fig. 5, these tendencies are present, but less pronounced, than at stationary steps-tests.With DPF+SCR the higher share of RME provokes principally similar effects, which nevertheless are superimposed by the exhaust gas aftertreatment.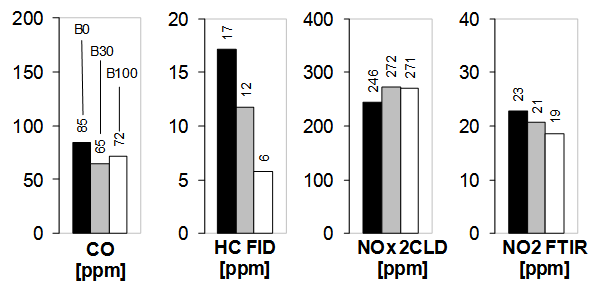 | Figure 5. Emissions in ETC with different fuels w/o aftertreatment |
Fig. 6 shows the results of interesting NOx-components in function of exhaust gas temperature with B0, B30 & B100 for SCR alone.In steps-tests there is no clear influence of RME portion on NOx. There is reduction of CO at higher load and general reduction of HC (not represented here). There are very little influences on NO2 & NH3.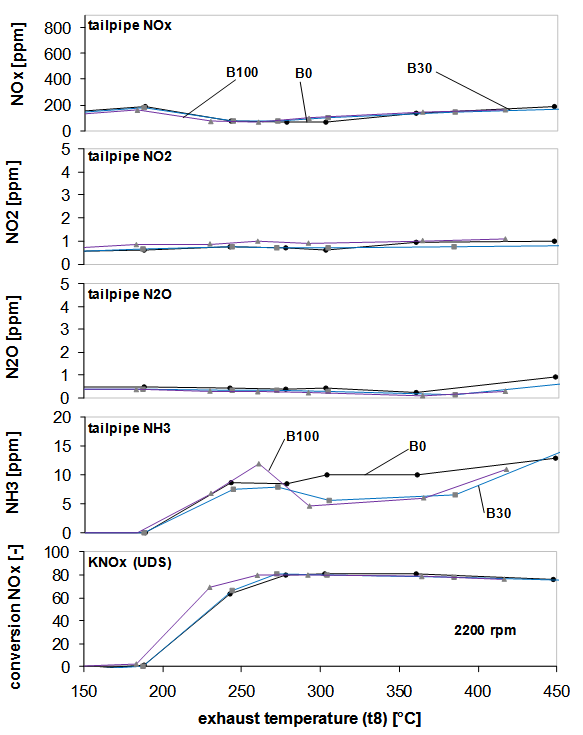 | Figure 6. Comparison of emissions in steps-tests with SCR and B0, B30 &B100; α=0.9; FTIR |
The light-off of the SCR alone is with RME 100 at a slightly lower temperature, than with B0 & B30 (Δt ∼ 10-20°C).Except of that there are no other clear effects of the RME-content on the presented parameters.In dynamic operation (ETC), Fig. 7, there are no differences of NOx, NO2 & NH3 and there is lowering of CO & HC with higher RME content.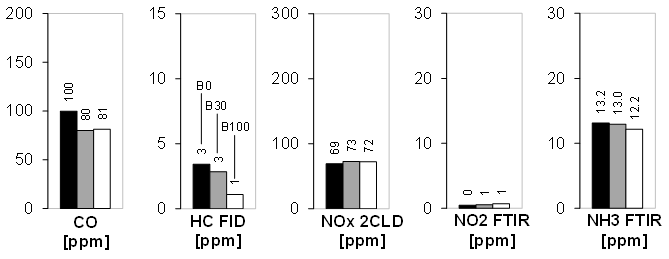 | Figure 7. Emissions in ETC with different fuels with SCR |
The influence of RME on NO2 with DPF+SCR which was remarked at stationary operation (more NO2 with more RME in certain texh range) is no more present or even inversed at transient operation. Similarly for NH3, which was reduced by RME (with DPF+SCR) in stationary steps-tests and is not reduced or even increased in the dynamic test.In general, it can be said, that some relationships of results, which are remarked at stationary operation can disappear or even be inverted at transient operation. This is to explain with the running chemical reactions in the aftertreatment system, which meet quite different changing conditions (p, T) during the transients.Fig. 8 represents the nitric emissions in function of exhaust gas temperature, with Diesel base fuel, for the three investigated variants:•reference case (Ref.) without exhaust gas aftertreatment,•combined aftertreatment system (DPF+SCR) and•SCR alone.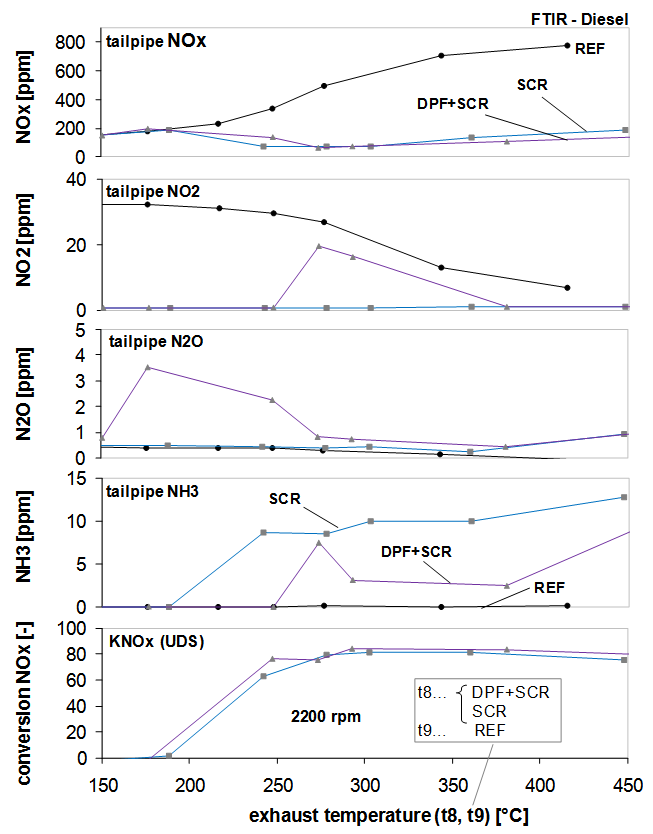 | Figure 8. Comparison of emissions in steps-tests with DPF+SCR and SCR, with the base fuel; α=0.9; FTIR |
With the catalyzed DPF there is a production of NO2 in the temperature range 250°C – 350°C. With the combined system (DPF+SCR) there is a slight emission of N2O (up to 4ppm) in the lowest temperature range and there are lower NH3- values, than with SCR alone.The increase of NOx conversion rate KNOX is with the combined system at a slightly lower temperature (Δt 10-20°C).The reduction efficiencies in ETC with B0, B30 & B100 and with both investigated exhaust aftertreatment systems are depicted in Fig. 9 (reduction efficiency RE and conversion rate Kx are synonyms, they are calculated in this figure from the FTIR-results SP0 & SP3). With the combined system (DPF+SCR) there are clearly higher RE for NOx and lower RE for NO2. There is no clear influence of biocomponent content on the reduction efficiency (except of a slight monotone tendency of lowering RE for NO2 with SCR alone).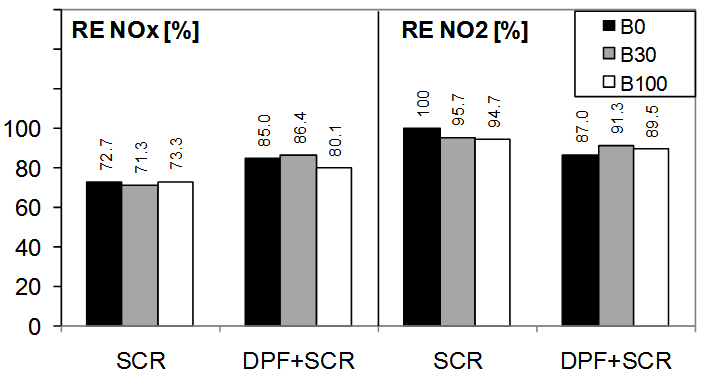 | Figure 9. Comparisons of reduction efficiencies in ETC; α=0.9; FTIR |
The particle filter of the combined system had the filtration efficiency, which fulfilled the actual VERT quality requirements (PCFE > 99 %). I was interesting to state if there are some influences of biocomponents on the filtration resp. reduction efficiency of NP’s of the combined system (DPF+SCR) and how is the influence of SCR alone on NP’s ?Fig. 10 shows the SMPS particle size distribution spectra without and with SCR at OP1 with B0, B30 & B100. There is a reduction of NP count concentration due to increasing B-content. This is in accordance with the other research results which generally state lower PM emissions with FAME’s at full load (higher O2-content in fuel, lower accumulation mode).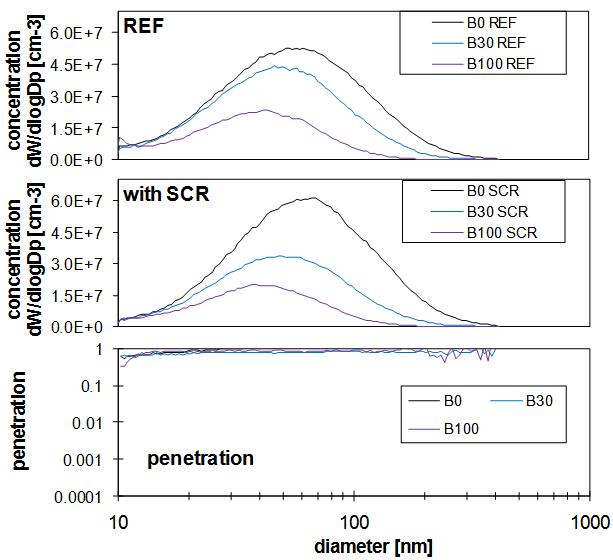 | Figure 10. SMPS-PSD spectra with B0, B30 &B100 and SCR; α= 0.9; 2200rpm/100% load |
The penetration nevertheless stays similar for all fuel variants at approx. 90%. This small reduction of nanoparticles concentration represents the diffusion losses in the mixing tube and in the SCR catalyst.Penetration is a parameter representing the portion of particulates passing through the aftertreatment device; it is a ratio of down – to upstream concentrations.Penetration = 1 – filtration efficiency.
7.2. Lube Oils
In order to study the effect of biodiesel blends on engine lubricating oils degradation, twelve long time engine tests of 200 hrs were carried out using three test Diesel biofuels containing respectively 7, 20 and 30% (V/V) RME, four different engine lube oils and two type of engines (HD and LD) were used. The lube oil performance changes were monitored through in-depth oil sample analysis. In case of HD engine tests have been observed:dilution of the tested engine lubricating oils by RME in the range of 2 to 2,3% (V/V) for biofuel B20 and in the range of 3,3 to 3,5% (V/V) for biofuel B30. For this engine, influence of RME level contained in biofuel on mineral lubricating oil (OM) degradation process was followed by 125 hrs test. For synthetic oil (OS) significant increase of viscosity in case of engine fuelling with biofuels B20 and B30 was observed from the beginning of test – Fig. 11a.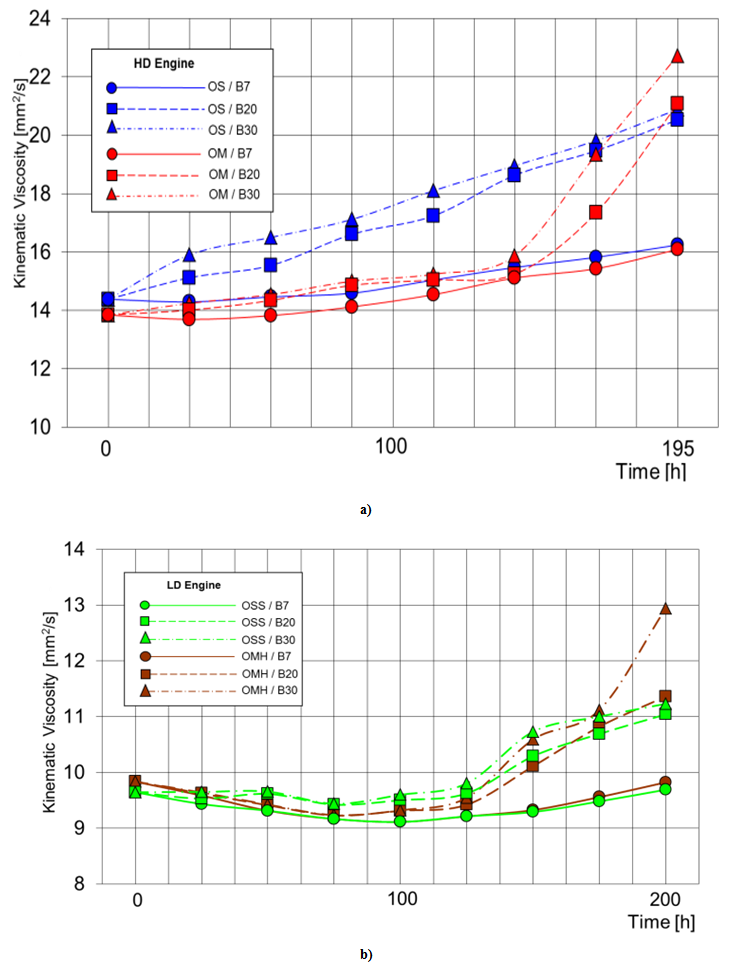 | Figure 11. Kinematic viscosity changes of studied lube oils for HD engine (a) and for LD engine (b) |
In case of LD, HSDI engine tests have been observed:dilution of the tested lubricating oils by FAME in the range of 5,4 to 5,5% (V/V) for biofuel B20 and in the range of 8,5 to 8,7% (V/V) for biofuel B30. Under engine oil tests circumstances significant difference in viscosity characteristics of lubricating oil subjected to impact of biodiesel blend B20 and B30 has been stated. For tests where engine was fuelled by above mentioned biofuels accelerated increasing viscosity trend of both tested engine oils over 125 hrs of test duration was observed. For LD engine, progressive increase in viscosity may be due to poor oxidation stability of the biofuel by which engine oil was successively diluted during the test – Fig. 11b.The rate of TAN increase with both tested lubricating oils is very similar for B7 Diesel fuel in HD engine – Fig. 12a. As level of FAME contained in biofuel was growing, poor oxidation stable biodiesel has induced the formation of oxidative products, leading to relatively faster TAN increase, which is more progressive for mineral oil especially at the end of the test.Fig. 12b shows a propensity to faster increase of lube oil TAN for the tests where LD engine was fuelled with biofuel contained increased blend ratio of RME. This can be attributed to poor oxidation stability of RME gradually diluting engine oil, which induces the formation of oxidative products and in turn leads to a relatively faster acidity increase. Changes of TAN for mineral engine oil (OMH) show more increasing patterns with the test hours, because of higher acidity of biofuels with growing RME blend ratio.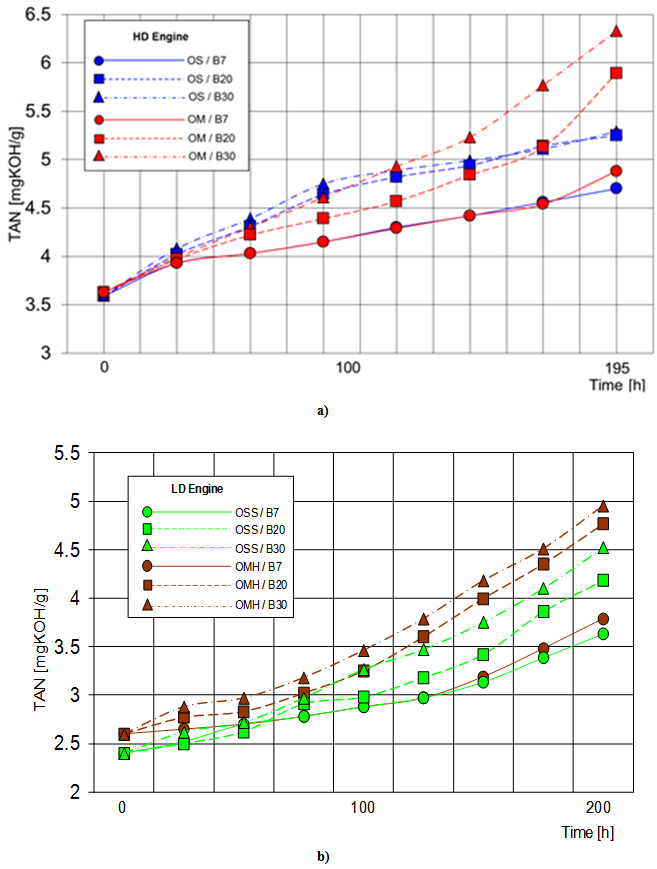 | Figure 12. Acid number changes of studied lube oils for HD engine (a) and for LD engine (b) |
For HD engine, the tests point out a similar resistance to oxidation of both lube oils. In case of mineral lube oil (OM), obtained results show no adverse influence of used biofuel as far as the 30% (V/V) RME level – Fig. 13a. Similar influences of biofuels on the level of engine lube oil bulk oxidation have been observed for mineral (OMH) and synthetic (OSS) engine oils during tests of LD engine, see curves inclination in Fig. 13b. Significant oxidation resistance changes of both engine lube oils were noticed after 50 hrs of test duration, where RME content in the Diesel fuel makes a great difference for the degree of oil degradation.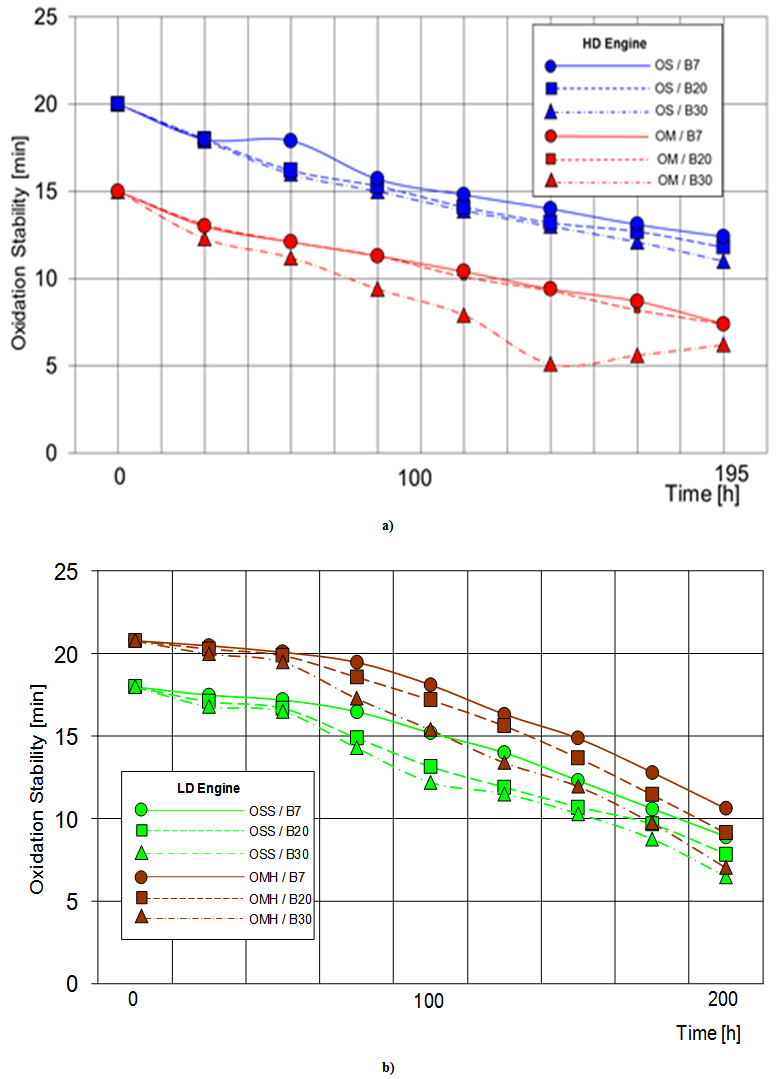 | Figure 13. Oxidation stability changes of studied lube oils for HD engine (a) and for LD engine (b) |
It was noteworthy that for HD engine (Fig. 14a) lubricating oil dilution with biofuels can have a significant impact on its oxidation stability in thin film. For both tested lube oils (mineral - OM and synthetic - OS) depreciation of oxidation resistance in thin film oil develops continuously but for synthetic lube oil the impact on rate of its degradation depends stronger on volume fraction of RME in biofuel.For tests of LD engine, kind of used blend fuel (RME content) is the factor which has the major influence on engine lube oil degradation rate under circumstances of thin film. For biodiesel B30, rapid decrease of oxidation stability of the tested engine oils (faster for mineral oil – OMH) is observed in the entire test duration – Fig. 14b.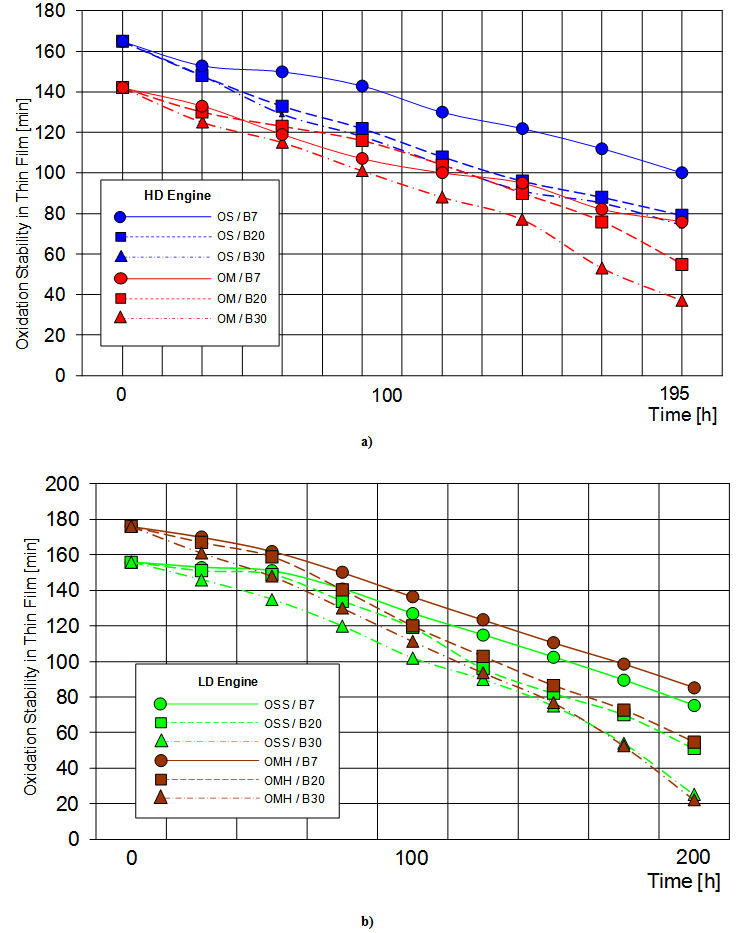 | Figure 14. Oxidation stability in thin film changes of studied lube oils for HD engine (a) and for LD engine (b) |
Assessment of lubricating oils degradation by using FTIR analysis proves that for HD engine tests the rate of degradation process is considerably higher for fuels with increased level of RME content (20 and 30%) as shown in the Fig. 15a. With higher biofuels levels, particular engine oils degradation has been observed for mineral lube oil (OM).FTIR analysis for engine lube oils oxidation stability evaluation showed, that the shape of curves, representing oxidation stability for both tested oils (mineral & synthetic) is very similar using 7% (V/V) RME blend (B7) for engine fuelling – Fig. 15b. As RME content in diesel fuel increases, processes of oxidation resistance depletion proceed more rapidly, especially for mineral engine oil (OMH).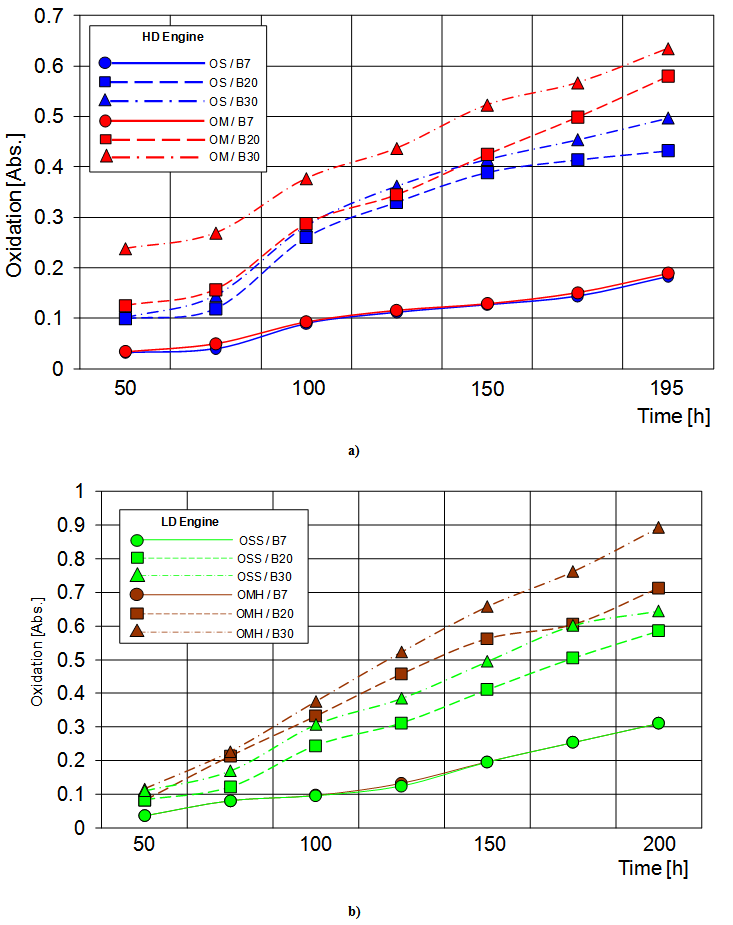 | Figure 15. Oxidation stability (by FT-IR) changes of studied lube oils for HD engine (a) and for LD engine (b) |
8. Conclusions
From the present tests performed at stationary engine operation in steps-tests and at dynamic engine operation in ETC several results can be remarked. The most important are:
8.1. For RME Content
•the increased share of RME w/o aftertreatment causes an increase of NOx by higher engine load and reduction of CO & HC; at transient operation (ETC) these tendencies are less pronounced and only B100 shows an increase of NOx,•with DPF+SCR in the stationary conditions, where NO2 is produced RME causes higher NO2- values and in the conditions, where NH3 is produced RME causes lower NH3-values,•in dynamic tests (ETC) with DPF+SCR only higher NOx-emissions with RME 100 are to remark, CO & HC are for all fuels at zero level (catalytic conversion),•with SCR alone there are no differences of NOx and of NOx reduction rate (KNOx) with increasing RME portion; there is lowering of CO & HC,•in dynamic tests (ETC) with SCR there are no differences of NOx and there is lowering of CO & HC with RME,•there are generally no influences of RME-portion in fuel on the conversion values KNOx & KNO2,•the light-off of the SCR alone is with RME 100 at a slightly lower temperature, than with B0 & B30 (Δt ∼ 10-20°C).
8.2. For Exhaust Aftertreatment System
•with DPF+SCR KNOx-values are slightly higher, than with SCR alone, due to the production of NO2 in the catalytic DPF (upstream of SCR),•with DPF+SCR the CO- and HC-emissions are mostly eliminated,•with DPF+SCR in certain range of the exhaust tem-perature there are higher NO2-values than with SCR alone; these NO2-values are further increased with RME,•with DPF+SCR the NH3-emissions are lower than for SCR,•the reduction efficiencies in ETC with the combined system DPF+SCR, are for NOx higher and for NO2 lower.
8.3. For Nanoparticle Emissions
•without aftertreatment and with increasing RME-share the maximum of the count concentration of the PSD moves to smaller sizes and it decreases at full load,•with DPF+SCR there is excellent filtration efficiency of DPF, up to 99.96%,•at stationary full load operation with DPF+SCR and with RME 100 there is an intense production of secondary nanoparticles from the SCR part; this effect lowers remarkably the overall NP - reduction efficiency; it is almost not visible at dynamic operation,•with SCR alone there is usually a small reduction of nanoparticles concentrations (in the range of 10-20%) losses in the mixing tube and in the two in line SCR catalysts; in dynamic operation this reduction is smaller (below 10%),•with SCR at full load there is a slight increase of NP-counts due to the secondary NP-production,•certain results with SCR show surprisingly high variations of reduction rates; this is explained with the emitting dispersion during certain measuring series. The emitting dispersion can originate from some memory effects (store-release) of the entire system (engine + exhaust system). The measuring dispersion for nanoparticles is excluded by conformity of results obtained with different measuring methods. The NP reduction rates in SCR were regarded in further research, which confirmed these explanations.
8.4. For Engine Lube Oil Deterioration
•applied extended methods were found to be useful in multidirectional in-depth assessment of engine oils performance change during long time engine tests,•extended methods enabled better discriminating of degradation processes occurring in engine oils. Oil operating run time after which loss of oil performance potential is essential from the point of view of its further operation had been indicated,•one of the key factors related to engine oil degradation is biodiesel oil dilution range and level of FAME included in biodiesel blends,•the results obtained in these investigations indicate the kind of lubricating oil base stock and its improvement way, as well as type of engine and its service conditions as very important factors affecting the engine oil performance depreciation,•reliable evaluation of FAME impact on modern engine oil accelerated aging requires multidirectional assess- ment by using prevalent and also non standard test methods with increased sensitivity and measuring accuracy,•more and more complicated, not always beneficial interactions between modern engine oils and alternative fuels will require further development of novel test methods for dependable distinguishing of the stages of used oil degradation.
Abbreviations
AFHB
Abgasprüfstelle FH Biel, CHAir min
stoichiometric air requirementBxx
blend fuel with biocomponent share xx%CFPP
cold filter plugging pointCLD
chemoluminescence detectorCNC
condensation nuclei counterCPC
condensation particle counterDC
Diffusion Charging SensorDCFE
diffusion charge filtration efficiencydePN
de Particles + deNOxDMA
differential mobility analyzerDPF
Diesel Particle FilterECU
electronic control unitEMPA
Eidgenössische Material Prüfund ForschungsanstaltEPA
Environmental Protection AgencyETC
European Transient CycleFAME
fatty acid methyl esterFE
filtration efficiencyFID
flame ionization detectorFL
full loadFTIR
Fourrier Transform Infrared SpectrometerHCFID
HC measured with FIDHCIR
hydrocarbons measured with infrared analyserHD
heavy dutyHTHS
high temperature/high shear (viscosity)HSDI
high speed direct injectionICE
internal combustion enginesINIG
Oil and Gas Institute, Krakow, PLKx
conversion rate of “x”LD
light dutyLDS
Laser Diode Spectrometer (for NH3)LEM
limited engine mapMD19
heated minidiluterNanoMet
NanoMet nanoparticle summary surface analyser (PAS + DC + MD19)NEM
nonlimited engine mapNP
nanoparticles < 999 nm (SMPS range)OEM
original equipment manufacturerO&G
IOil and Gas Institute (INIG)OM
mineral oil HDOMH
mineral oil LDOP
operating pointOS
synthetic oil HDOSS
synthetic oil LDPAS
Photoelectric Aerosol SensorPC
particle countsPCFE
particle counts filtration efficiencyPM
particulate matter, particle massPMFE
particle mass filtration efficiencyPSD
particle size distributionRE
reduction efficiencyRME
rapeseed methyl esterSCR
selective catalytic reductionSME
soya oil methyl esterSMPS
Scanning Mobility Particle SizerSP
sampling positionTAN
total acid numberTBN
total base numberTC
thermoconditioner. Total CarbonTTM
Technik Thermische MaschinenULSD
ultra low sulfur DieselVERT
Verification of Emission Reduction TechnologiesVERTdePN
VERT DPF + VERT deNOxα
feed factor of urea dosing;
ratio: urea injected / urea stoichiometric;
calculated by the ECU.
References
[1] | Willems, F.; Cloudt, R.; van den Eijnden, E.; van Genderen, M.; Verbeek, R.; de Jager, B.; Boomsma, W.; van den Heuvel, I.: Is Closed-Loop SCR Control Required to Meet Future. |
[2] | Emission Targets? SAE Techn. Paper 2007-01-1574. |
[3] | Hosoya, M.; Kawada, Y.; Sato, S.; Shimoda, M.: The Study of NOx and PM Reduction Using Urea Selective Catalytic Reduction System for Heavy Duty Diesel Engine. SAE Techn. Paper 2007-01-1576. |
[4] | Görsmann, C.: Retrofit SCRT® – A retrofit system for the simultaneous reduction ofcarbon monoxide, hydrocarbon, soot particulate and oxides of nitrogen emissions from commercial vehicles, 4. FAD – Konferenz, Dresden, Nov. 2006, p. 155.M. |
[5] | Girard, J-W.; Cavataio, G.; Lamber, Ch. K.: The Influence of Ammonia Slip Catalysts onAmmonia, N2O and NOx Emissions for Diesel Engines. SAE Techn. Paper 2007-01-1572. |
[6] | Czerwinski, J.; Zimmerli, Y.; Mayer, A.; Heeb, N.; Lemaire, J.; D’Urbano, G.; Bunge, R.;Testing of Combined DPF+SCR Systems for HD-retrofitting VERTdePN. SAE Techn. Paper 2009-01-0284. |
[7] | Thornton, M.J.; Alleman, T.L.; Luecke, J.; McCormic, R.L.; Impacts of Biodiesel Fuel Blends Oil Dilution on Light-Duty Diesel Engine Operation. 2009 SAE International Powertrains, Fuels, and Lubricants Meeting, June 15 – 17, 2009 Florence, Italy. |
[8] | Watson, A.G.; Wong, V.W.; The Effects of Fuel Dilution with Biodiesel on Lubricant Acidity, Oxidation and Corrosion – a Study with CJ-4 and CI-4 PLUS Lubricants. 2008. |
[9] | Shimokoji, D.; Okuyama, Y.; Analysis of Engine Oil Deterioration under Bio Diesel Fuel Use. SAE Number 2009-01-1872. |