C. Oliveira1, 2, J. C. Nascimento1, I. M. Martin1, K. G. Grigorov1, 3, G. J. P. Abreu1, V. W. Ribas1, B. N. Sismanoglu1
1Technological Institute of Aeronautics (ITA), Physics Department, São José dos Campos, Brazil
2Laboratório Nacional de Ciência e Tecnologia do Bioetanol–CTBE/CNPEM, Campinas, Brazil
3Space Research and Technology Institute, Acad. G. Bonchev Str. bl.1, Sofia, Bulgaria
Correspondence to: B. N. Sismanoglu, Technological Institute of Aeronautics (ITA), Physics Department, São José dos Campos, Brazil.
Email: |  |
Copyright © 2014 Scientific & Academic Publishing. All Rights Reserved.
Abstract
Spectral and electrical characterizations were carried out on low current (2-8 mA), 40 Torr microplasma device aimed to polyethylene surface modifications, such as wettability (work of adhesion). A mixture of argon and oxygen (2%) was used as working gas and as far as the oxygen is ionized between the electrodes polarize the treated surface resulting in its increased surface energy. The argon has an important role too, as well as it is carrying gas with higher atomic weight providing better efficacy of the process. By conducting optical measurements the plasma parameters was estimated. The average gas temperature was about 350 K for current ranging from 1 to 8 mA at the cathode nozzle exit and was 300 K at 2 mm from the cathode borehole. From Balmer Hβ spectral line it was estimated the electron number density ne= (1.2± 0.2) ×1019 m-3. The electron excitation temperature was found to be Texc = (0.65 ± 0.05) eV. To increase the wettability of the HDPE surface, the best experimental parameters to obtain low contact angle are as follows: flow of 100 ml/min, peak current of 5 mA and operation of 250 s.
Keywords:
Microplasma, Gas temperature, Optical measurements, Wettability, HDPE
Cite this paper: C. Oliveira, J. C. Nascimento, I. M. Martin, K. G. Grigorov, G. J. P. Abreu, V. W. Ribas, B. N. Sismanoglu, 40 Torr Glow Discharge Used for Polyethylene Treatment, American Journal of Condensed Matter Physics, Vol. 4 No. 3A, 2014, pp. 28-31. doi: 10.5923/s.ajcmp.201401.04.
1. Introduction
Non-thermal (cold) microplasma devices are widely used for materials processing in a large number of applications to cover metals and polymers (polyaramid – Kevlar, polyethylene (PE), polyvinylidenefluoride, polytetrafluoroethulene, polypropylene (PP), polyolefines, polyesters, polyamides, to name a few). As mentioned before, the main target of this kind of discharge are the solid film surfaces treatment, modification and plasma etching [1]. The discharge is usually characterized by low gas temperature compared to the electron temperature (Te>>Tg) which enables various new applications. [1]. The high electrons energy present in high-pressure glow plasmas, known as microplasmas or plasma microjets [2-8], enables the creation of chemically high energy species, fundamental for materials processing. Microplasmas operated at atmospheric pressure are both new and cheap plasma-based tools that enable the deposition of material and surface modification of metals and polymers, because the gas temperature of these systems varies between room temperature to hundreds of kelvin [2-8]. At low temperature (about room temperature) it is very known the application of such cold oxygen or a mixture of rare gases with oxygen plasmas to make hydrophilic the polymers surfaces [1]. Biomaterial polymers, used as biosensors, are a kind of material that need room temperature plasma to modify they surface in order to avoid several damage on its surface structure, reducing their compatibility with live materials, like live biological tissues [1]. Microplasmas are an important also source of both ozone and OH molecules formation. The OH radical is crucial for the treatment of polymers. Blajan et all proposed a technology using the microplasma to increase the hydrophilic properties of glass surface [9]. They observed the generation of active species by microplasma could be considered the reason for improving the wettability of glass surface. These experiments showed the lowest contact angle for the microplasma discharge in Ar. The emission spectrum of Ar microplasma shows the presence of excited ArI and OH and a decrease in the intensity of these species when N2 orO2 was added. They concluded that these active species have a major role in the surface treatment process of glass by microplasma. In Dielectric Barrier Discharges (DBD) at 10Khz [10], the treatment increases the wettability of the polymer surface. Balcon et all used glow discharge by pulsing the 13.56Mhz generator as an efficient method in decreasing the hydrophobicity of polymer films at low plasma temperature [11]. They used pulsed RF discharge as an efficient method for the treatment of polyethylene terephthalate (PET) polymer films at low gas temperature to avoid the damage of the polymer surface, at Tg< 80℃, at the glow mode. It is important to note that, above this temperature, the plasma shows filamentary behavior, disabling the application for surface treatment. Benedikt et all used microplasma jet aiming thin film deposition [12]. Their low temperature microplasma jet (Tg< 400 K) with high electron number density (8.5 ×1020m−3 for Ar and 7.0 ×1020m−3 for He discharges) is suitable for numerous applications, such as thin film growth or surface treatment. Deposition of hydrogenated amorphous carbon and silicon oxide films have been modified using Ar/C2H2 and Ar/hexamethyldisiloxane/O2 mixturesin SiOx deposition exploring the possibility of carbon-free SiOx deposition, where the growth rate was in the 1–2 nms−1 range. In this work we used an array of four glow microplasmas in coupled in parallel regime as a tool for polyethylene organic substrate surface modification using with argon as a working gas.
2. Experimental
Microdischarges or microplasmas consist of a cathode and anode thin foil with a borehole separated by mica insulator, where a hole is drilled through a cathode-mica-anode parallel-plate structure. Its I-V characteristics show distinct modes of operation, such as Townsend with positive resistivity (at low current), self-pulsed (negative resistivity) and normal mode (non-variable discharge voltage). Stable operation is achieved at low and high pressure operation. The electrodes are made by 100μm thick cuprum foils separated by a 200μm mica spacer with 500 μm hole diameter. The glow maintaining discharge voltages were in the range of 200 - 400 V for Ar/O2 = 98/2 gas mixture at 0.10 ℓ/min total gas flow. The discharge current Id varied between 1 and 8 mA and the operating gas mixture was running from moderate to high-pressure, between 20and 500Torr. The electrode system was placed in a cylindrical quartz chamber with 10cm diameter and 16cm length. Before each experiment the chamber was cleaned, dried and evacuated to about 1 mTorr. Then, the discharge chamber was filled with pure argon gas and placed at the desired pressure. Ballast resistors of 55KΩ were located to the cathode side and were used to limit the discharge current. A pico-ammeter model Keithley 414S and Minipa-brand digital voltmeter were used to measure the current and voltage in the pre-breakdown phase. Figure 1 shows the described microplasma device with one opening, placed in chamber suitable for electrical and optical emission characterizations. The radiation emitted from the cathode borehole was focused onto optical fiber through convergent lens. The collected radiation was send onto the entrance slit of Czerny-Turner (Jobin-Yvon) monochromator (THR1000).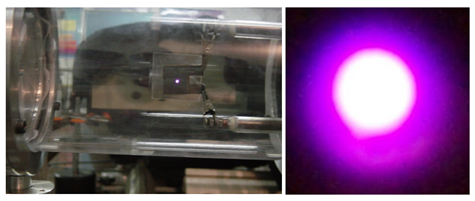 | Figure 1. Gas discharge chamber (left). The microplasma deviceis mounted inside the vacuum chamber evacuated at50 Torr. Right, the Ar gas glow discharge |
3. Results and Discussion
Figure 2 shows the microplasma device with four microholes lit on and in figure 3 the current-voltage curve are drawn for each microplasma devices set with 1, 2, and 4 holes. We have used copper and mica foilsas dielectric with 250µm thickness, and hole diameter of 500µm, where Ar/2%O2 mixture at 40 Torr feeds the discharge. From the positive slope of the I-V graphics shown in Figure 3 the following value of the electrical resistance are obtained -R1 = 32 kΩ; R2 = 15 kΩ and R4 = 7 kΩ respectively for 1, 2 and 4 microholes. 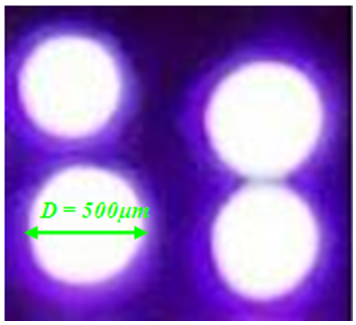 | Figure 2. Four microholes lit on placed in one microplasma device at parallel operation |
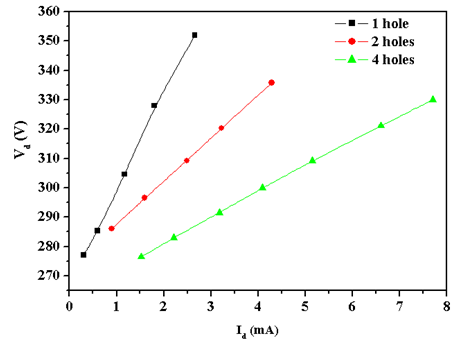 | Figure 3. Current-voltage characteristic curve (see the text) |
The approximate ratio R1 = 2R2 = 4R4 shows that for a given value of the discharge voltage Vd, the intensity of the total current is I4 = 2I2 = 4I1 respectively and the intensity of the current flowing through the plasma for a given hole will always be equal to I1 with electric resistance R1. For a given Vd, the intensity of the current for the system with one hole is given by Vd = R1I1, and for a system with n holes, the current is obtained by Vd = RnnI1, resulting in R1 = nRn. The advantage of this type of discharge is the possibility to operate in Townsend regime with low current.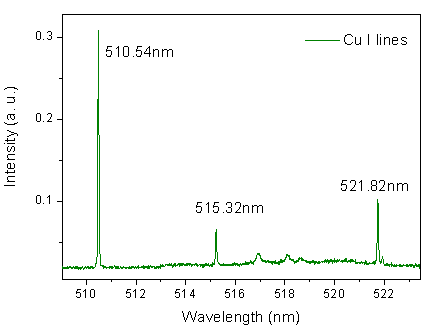 | Figure 4. Cu I spectral lines. Cu is sputtered from cathode surface and excited at the glow plasma (negative glow) |
Table 1. Line parameters of the Cu I and hydrogen Balmer lines [13] 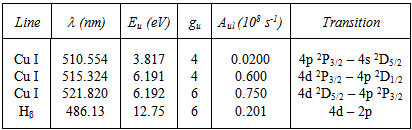 |
| |
|
The region between500and550 nm was scanned (Fig. 4) to observe the presence of Cu I lines placed in the negative glow. The copper ions are released from the cathode surface due to the argon ion bombardment. The listed Cu I lines (Table 1) were the strongest ones allowing the best estimation of Texc. One can use the following relation to estimate the excitation temperature [4-6].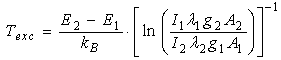 | (1) |
Eq (1) could be calculated choosing two pair of lines from the table 1, which yields for ex. Texc = (0.65 ± 0.05) eV for a range of current varying from 1 to 8 mA. The gas temperature can be estimated calculating the rotational band of the OH molecule (first order, ultra-violet,
observed due to the humidity of the chamber, that remains in the vacuum system. Then the temperature can be obtained from the slope of the plot ln(Iλ/A) as a function of the upper state energy, where I is the rotational line intensity, λ is the transition wavelength and A- the transition probability [4-6]. The average gas temperature was found to be about 350 K for current ranging from 1 to 8 mA at the cathode nozzle exit and 300 K at 2 mm from the cathode borehole. From Balmer Hβ one can estimate the electron number density (see Table 1) resulting in ne = (1.2± 0.2)×1019 m-3 [4-6]. This high density explains the richness of the active species that appears in glow microplasmas, turning it as suitable tool enabling various applications in material processing.The main goal for building and investigating the proposed microplasma glow source is focused on the possibility of modifying the surface energy of the HDPE surface. HDPE has density of 9.5×10-10kg.m-3and melting point at 410 K, and it is characterized by long linear molecules (-H2C-CH2). HDPE is a thermoplastic commonly used in the packaging industry due to their low cost and easiness of production in large scale. It has excellent chemical resistance and hydrophobicity characteristics and the aim of this work is to increase the wettability of the polymer surface, changing the morphology and it surface properties. The wide range of chemical species present in the plasma offers numerous possibilities for modifying the atmosphere that covers the surface of the material to be treated, thus altering the chemical and morphological nature of this surface. The nature of the changes depends mainly on the composition of the gaseous medium and on the process parameters, like the current, the gas flow, the pressure and the composition of the gas mixture. HDPE surfaces are polyolefin having low wettability and are nonpolar, which is incompatible with inks and adhesives that are polar. When applying a liquid ink onto a polyethylene film (PE), droplet formation occurs because the surface tension of the ink is greater than the adhesive forces between the film and the ink. The plasma treatment is important to modify their surfaces and improve the adhesion characteristics. It is important to add oxygen to the Ar gas because the effect of surface modification is feasible mainly by ionization of the oxygen between the electrodes that polarize the film surface and increases its surface energy. The discharge located at 2 to 4 mm from the cathode borehole has an area of approximately 4.5×10-6 m2 and the chemical species are scattered over the HDPE target located at this axial position. Ar gas with a little admixture of O2was used to treat HDPE (100μm thick) film. The contact angle of the untreated HDPE surface was approximately 110°. The gas flow of 100 ml/min was found to be optimal to achieve the minimum angle of 50° and there is no need for longer treatment operation beyond 250 s. Current of 5mA and 100 ml/min gas flow are quite sufficient to obtain the smallest contact surface angle. Higher currents could damage the device, and will not increase the contact angle. Finally it appears that the ideality to obtain lower contact angle are: flow of 100ml/min, peak current of 5mA and operation time of 250s.
4. Conclusions
Large number of materials such as metals, polymers, biomaterials and live tissues could be successfully treated by non-thermal (cold) plasma in order to improve drastically their surface chemistry without running the risk of any damages. In this work we used an array of four glow microplasmas in parallel regime as a tool aiming the polyethylene organic substrate surface modification, with argon as a working gas. 40 Torrglow microplasma device parallel operated at low current (2 – 8 mA) was used to conduit spectral and electrical investigations and to implement important surface modifications onto high density polyethylene (HDPE) surface. The plasma treatment is important to modify surfaces and to improve their adhesion characteristics. It is necessary to add oxygen to the Ar gas because the effect of surface modification is obtained mainly by ionization the oxygen between the electrodes that further polarize the film surface and increases its surface energy. By applying optical measurements the plasma parameters was estimated. The average gas temperature was about 350 K for current ranging from 1 to 8 mA at the cathode nozzle exit and was 300 K at 2 mm from the cathode borehole. From Balmer Hβ spectral line it was estimated the electron number density ne= (1.2± 0.2) ×1019 m-3. The electron excitation temperature was Texc = (0.65 ± 0.05) eV. To increase the wettability of the HDPE film, the best combinations to obtain lower contact angle are: flow of 100 ml/min, peak current of 5 mA and operation time of 250 s.
ACKNOWLEDGMENTS
The authors acknowledge the financial support of the programs CAPES, FAPESP and CNPq for the partial financial support under Grant No. FAPESP/12/13064-4, CNPq/MCTI/SECIS 406035/2013-0, CNPq/306095/2013-0 PQ, CNPq/310419/2012-3 DT,CAPES/88881.030340/2013-01 BJT and CAPES/PVE/BEX9796/12-6.
References
[1] | Cold Plasmas in Materials Fabrication, Alfred Grill, IEEE Press, New York, 1994. |
[2] | B. N. Sismanoglu, J. Amorim, J. A. Souza-Corrêa, C. Oliveira, and M. P. Gomes, Spectroch. Acta Part B 64, 1287 (2009). |
[3] | R. Caetano, Y. D. Hoyer, I. M. Barbosa, K. G. Grigorov, and B. N. Sismanoglu, Int. J. Mod. Phys. B 27, 1350089 (2013). |
[4] | Y. D. Hoyer, B. N. Sismanoglu, and K. G. Grigorov, The Eur. Phys. J. D 66,1712012 (2012). |
[5] | B. N. Sismanoglu, K. G. Grigorov, R. A. Santos, R. Caetano, M. V. O. Rezende, Y. D. Hoyer, and V. W. Ribas, The Eur. Phys. J. D 60, 479 (2010). |
[6] | B. N. Sismanoglu, K. G. Grigorov, R. Caetano, M. V. O. Rezende, and Y. D. Hoyer, The Eur. Phys. J. D 60, 505 (2010). |
[7] | M. P. Gomes, B. N. Sismanoglu, and J Amorim, Braz. J. Phys. 39, 25 (2009). |
[8] | C. Oliveira, J. A. Souza Corrêa, M. P. Gomes, B. N. Sismanoglu, and J. Amorim, Appl. Phys. Lett. 93, 041503 (2008). |
[9] | M. Blajan, A. Umeda, and Kazuo Shimizu, IEEE Transactions on Industry Applications 49, 2 (2013). |
[10] | F. Massines and G. Gouda, J. Phys. D: Appl. Phys. 37, 3 (1998). |
[11] | N. Balcon, A. Aanesland, and R. Boswell, Plasma Sources Sci. Technol. 16, 217–225 (2007). |
[12] | J. Benedikt, V. Raballand, A. Yanguas-Gil, K. Focke, and A. von Keudell, Plasma Phys. Control. Fusion 49, B419–B427 (2007). |
[13] | http://physics.nist.gov/PhysRefData/ASD/lines_form.html, accessed in september 2014. |