Tanzeena Refat Tumpa1, Sunchyen Barua1, Tanzim Tabassum1, Md. Wahidur Rahman2, Md. Lutfor Rahman3, Muhammad Tanjil1, Riffat Islam4
1Department of Textile Engineering, National Institute of Textile Engineering and Research, Savar, Dhaka, Bangladesh
2Department of Textile Engineering, City University, Ashulia, Bangladesh
3Textile Vocational Institute, Ministry of Textiles and Jute, Madaripur, Bangladesh
4Department of Textile Engineering, Ahsanullah Institute of TVET, Dhaka, Bangladesh
Correspondence to: Tanzeena Refat Tumpa, Department of Textile Engineering, National Institute of Textile Engineering and Research, Savar, Dhaka, Bangladesh.
Email: |  |
Copyright © 2025 The Author(s). Published by Scientific & Academic Publishing.
This work is licensed under the Creative Commons Attribution International License (CC BY).
http://creativecommons.org/licenses/by/4.0/

Abstract
Surface modification of textile materials is considered as the best way to obtain modern textile treatment. Synthetic chemicals as coating material create an adverse impact on the environment. By using the natural properties of chitosan and egg white, the research work aimed to enhance fabric functionality while maintaining its essential characteristics. Cotton fabric has shortcomings when it comes to some functional elements that modern textile applications are increasingly looking for, like moisture management, antibacterial capabilities, and wrinkle resistance. Chitosan has shown high potential as a biomaterial to facilitate adsorption. Chitosan has already proven it's efficiency to increase shrink resistance, dye uptake, and static resistance along with low toxicity and good biocompatibility. Egg white on the other hand is used as a an alternative starching agent and binding agent. Using the natural properties of chitosan and egg white, the study aimed to enhance fabric functionality while maintaining its essential characteristics. The coating's efficacy was evaluated through comprehensive testing. The Spray Rating Test yielded a score of 70, surpassing standard values and verifying the coating's robust water repellence. Drop tests revealed a rapid-fire penetration time of 35 seconds without washing and 18 seconds after one normal wash, demonstrating sustained water resistance. Wash fastness results, with a standing of 2-3 in gray scale, indicated moderate resistance to washing. In particular, the coated cotton fabric displayed excellent drape ability, emphasizing the successful integration of functionality without compromising flexibility. This specific research work can be vital for manufacturing functional apparels and fabrics.
Keywords:
Coating, Chitosan, Egg white, Water Resistance, Biocompatibility
Cite this paper: Tanzeena Refat Tumpa, Sunchyen Barua, Tanzim Tabassum, Md. Wahidur Rahman, Md. Lutfor Rahman, Muhammad Tanjil, Riffat Islam, Application of Chitosan and Egg White Based Organic Coating on Cotton as Water Resistant, International Journal of Textile Science, Vol. 14 No. 2, 2025, pp. 21-26. doi: 10.5923/j.textile.20251402.01.
1. Introduction
Water resistance which refers to the ability of a material or object to resist the penetration or passage of water to some degree; often achieved through the use of specialized coatings, treatments, or materials that create a barrier, preventing water from permeating or causing damage to the underlying structure or components. This study is an approach to determine the degree of water resistancy of chitosan and eggwhite based coating. The degree of water resistancy can vary from water repellency to waterproofing. This work have been designed to overcome the limitations while enhancing the value of cotton cloth.The amalgamation of chitosan and egg white as a coating material for cotton fabric presents a novel avenue in textile engineering. This research aims to investigate the potential of this combination in enhancing the functional ability of cotton fabric. The hypothesis behind this study lies in the unique properties of chitosan and egg white, such as biocompatibility, antimicrobial activity, and film-forming capabilities, which could impart desirable functional characteristics to cotton fabric without compromising its inherent qualities. This coated fabric can be used as a substitute for synthetic fabric considering temporary water resistancy. Few drops of natural coconut oil was also added to produce an emulsion with chitosan gel and egg white.Chitosan; which is a renewable polyelectrolyte prepared via deacetylation of chitin extracted from crustacean wastes of the fishing industry, represents an interesting biomordant candidate owing to its high positive charge in acidic media [1]. Chitosan has been demonstrated to have many other functional properties, biocompatibility, and antimicrobial activity, that may have a synergistic effect with most natural dyes. The printed samples using chitosan as a mordant showed the equivalent color values to that of prints obtained using alum as a mordant along with excellent antibacterial activity against both gram‐positive and gram‐negative bacteria [2]. Chitosan's nature of pseudo cationic polysaccharide has made it convenient to apply as an effective adsorbent [3]. Considering non-toxicity of chitosan this research was conducted to contribute more in the field of sustainability by examining other functionionalities that can be achieved by using this biomaterial. Chitosan has also been exploited as a textile finishing and sizing agent. chitosan nanoparticles have been used as a finishing agent and not as a bioactive vehicle for textile dyeing [4]. Chitosan is used for surface modification of textile materials to improve the softness of fabric and the result showed durability upto 20 wash [5]. After 20 wash antiwrinkle properties & strength of fabric was decreased. In this research work chitosan powder was mixed with acetic acid to solubilize and make a gel like structure. Egg white is widely used in multiple fields due to its low cost, high yield, abundance, rich nutrition and versatile functional properties. The intermolecular S-S bonds and S-H groups in egg white plays a vital role in the egg white film formation, as well as the hydrophobic and electrostatic interactions, and render excellent flexibility and biocompatibility to the films [6]. The hydrophilicity of egg white films can be reduced by introducing polysaccharides, lipids, or other hydrophobic substances. The chitosan is an excellent linear polysaccharide that showed excellent result as an integral key material for this research. White part of egg contains about 88% water and 11% protein. The protein part is conjugated with carbohydrates; mostly glucose [7]. Free glucose units alongwith free potssium, sulphure, chlorine and sodium ceates bonds with chitosan [7-8]. Egg white protein and phytic acid combination was reported for coating cotton fabrics which improved fire retardancy as a result of the constituent amount of calcium, ferric and phosphorous compounds [9]. polyethylene glycol was added in sample no.02 as a crosslinking agent to determine the effect and compare the the results between other two samples. Previously, a new composite of cellulose and egg white isolate has been reported with better tensile properties that could be used as packaging material or even contribute to produce artificial organs with it's β-sheet type structures [10]. This study also refers to the bonding of cellolose microfibril with eggwhite gel. An environment friendly nanocoating for flame retardant cotton was developed by pairing positively charged egg white proteins (EWP) and a negatively charged mixture of magnesium lignosulfonate (LS)–diammonium phosphate (DAP) solution. Egg white proteins are cheap and easy to prepare nitrogen-containing polyelectrolytes with strong char ability [11]. Egg white's ability to develop stable silver nanoparticles that is effective for blue dye degradation and antimicrobial activity [12] proves it's efficacy as a mediator.The unique part of this research is that the coating or finishing process was done at room temperature where chemical waterproofing results showed that the best water-repellent finishing technology for cotton fabric was at the baking temperature 110°C [13]. According to Loghin, [14] the performance of water-repellent clothing depends on two primary factors: (i) subjective variables, reflecting the user’s comfort requirements, and (ii) objective variables, which consider environmental conditions and risks. To meet up these requirements we tried to use raw materials that are environment friendly and biodegradable. We also did drape test to ensure good bending properties of fabric.The influence of crosslinked polyethylene glycol (PEG) is already reported on properties of 100% polypropylene spunbonded-meltblown-spunbonded (SMS) and 50/50 wood pulp/polyester spunlace fabrics that is used in protective surgical apparel [15]. The crosslinking and adhesion property of polyethylene glycol not only works on cotton but also on PET fibers [16]. For the outstanding thermal property from 38°-300°C polyehtylene glycol is also used to produce phase change material [17]. Polyethylene glycol acts as a solvent, stabilizer, as well as a different co- reducing agent and used in Ag based antimicrobial agent synthesis [18].The exploration of natural substances and their application in textile finishing processes has garnered considerable attention due to their eco-friendly nature and potential functional benefits. Among these substances, chitosan and egg white, a proteinaceous material readily available from poultry, have exhibited promising attributes in various fields due to their inherent properties. The aim of this research is to examine their combined effect as a coating solution over cotton and contribute to the field of textile.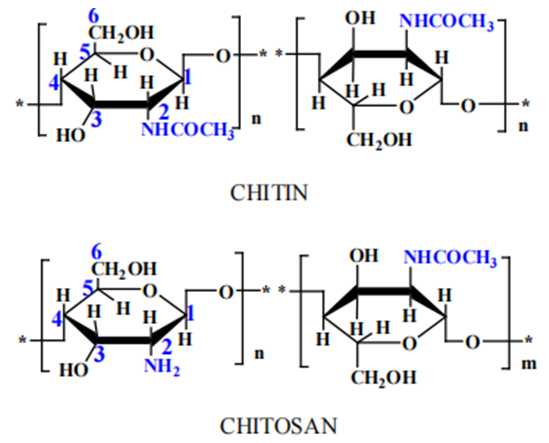 | Figure 1. Chemical structure of chitosan and chitin |
2. Materials & Methods
2.1. Materials
The key raw materials for this experiment are chitosan and eggwhite. Chitosan was extracted from shells of shrimpshell waste. Shrimp shell waste was washed to remove dirt & impurities.After that, shrimp shell waste have been drying in oven dryer at 60°C for overnight. Chitosan powder was acquired after effectively completing demineralization, deproteination, deacetylation processes; followed by drying and making powder of residual solid using a blender. Eggs were collected from local market and then eggwhite was separated from yolk through sieve.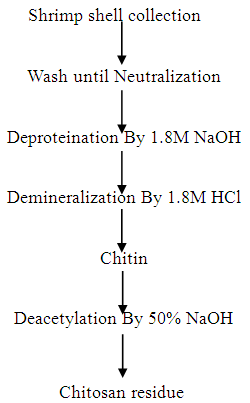 | Figure 2. Process flow of chitosan preparation |
2.2. Sample Preparation
We took a solid dyed cotton fabric to prepare sample 01 (Figure 04). Eggwhite 1% (owf) was taken along with 3% chitosan powder and equal amount of acetic acid with 3 drops of coconut oil; maintaining 1:10 liquor ratio. After solubilizing chitosan in acetic acid other auxiliaries were added. This coating mixture was then applied over fabric. Sample no.02 (Figure 05) was prepared with similar recipe as sample 01; only replacing oil with 3% polyethylene glycol. As sample no.02 and 03 printed cotton fabrics were used to examine color bleeding after coating process. Sample no.03 (Figure 06) was prepared with a diluted coating mixture with 1:30 liquor ratio. For sample no.03 chitosan, acetic acid and eggwhite was taken at 1%; but 6 drops of oil was used. 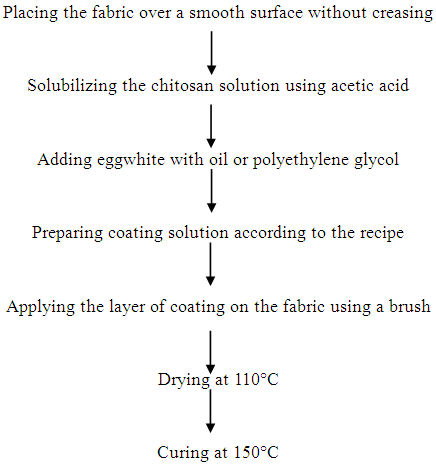 | Figure 3. Process flow of coating method |
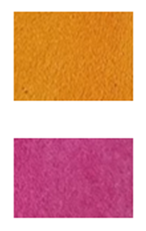 | Figure 4. Sample 01 |
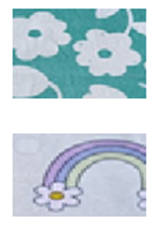 | Figure 5. Sample 02 |
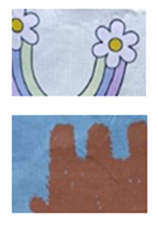 | Figure 6. Sample 03 |
3. Results and Discussion
3.1. Spray Rating Test Effect
The Spray Rating Test was executed according to the standards of ISO 4920-1981 [19]. The test demonstrated an exceptional water resistance with a score of ISO 4 for sample no.03. It seems the dilution of the coating mixture resulted in better penetration for sample no.03. This signifies that the developed coating, incorporating chitosan and egg white, forms an effective barrier against water penetration on cotton fabric.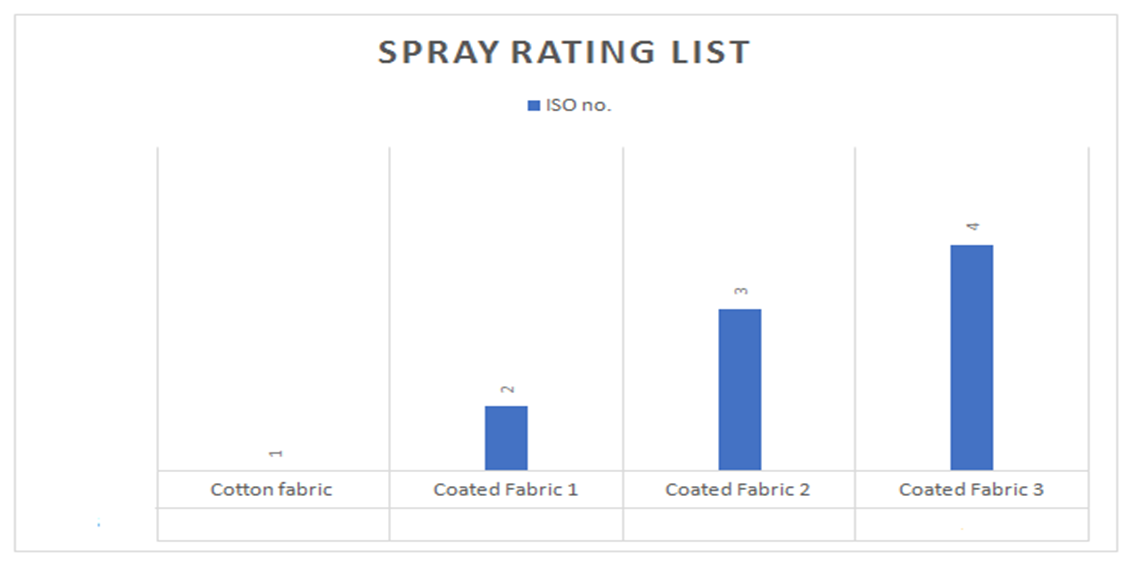 | Figure 7. Spray rating test graph |
The remarkable performance in the Spray Rating Test confirms the successful development of a water-resistant coating. Chitosan's hydrophobic nature, combined with the film-forming properties of egg white, has contributed to the fabric's enhanced ability to repel water. This aligns with the theoretical framework, emphasizing the potential of biopolymer-based coatings for textile applications.
3.2. Drop Test Effect
The drop test results complement the Spray Rating Test findings, affirming the durability of the water-resistant coating. The ability to resist water penetration, even after washing, positions the treated cotton fabric as a promising candidate for applications requiring sustained water repellency. The standard time for drop test is less than 1 second for a well scoured and cleaned fabric. Coated samples showed satisfactory result in laboratory drop test. Without washing the drop test revealed a penetration time of 35 seconds for third sample, showcasing rapid water repellency before any washing. After one normal wash, the fabric maintained a noteworthy penetration time of 18 seconds, indicating sustained water resistance.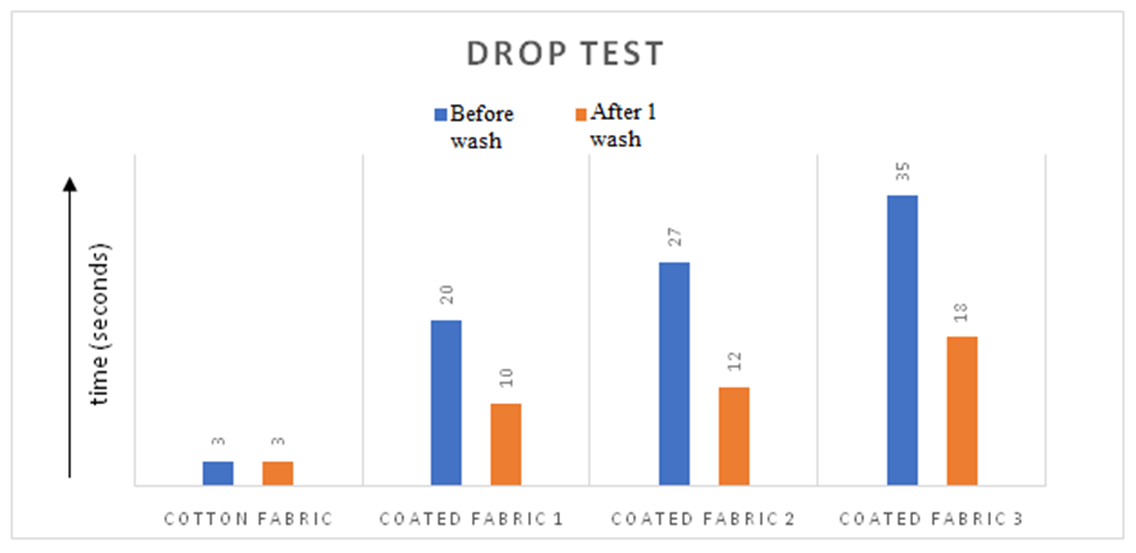 | Figure 8. Drop test graph |
3.3. Wash Fastness Test Effect
While the wash fastness rating falls within an acceptable range, further optimization of the coating formulation may enhance its durability through repeated wash cycles. This aspect is crucial for ensuring long-term performance, especially in garments subjected to frequent laundering. The wash fastness test resulted in a rating of 2-3 according to gray scale, indicating moderate resistance to washing.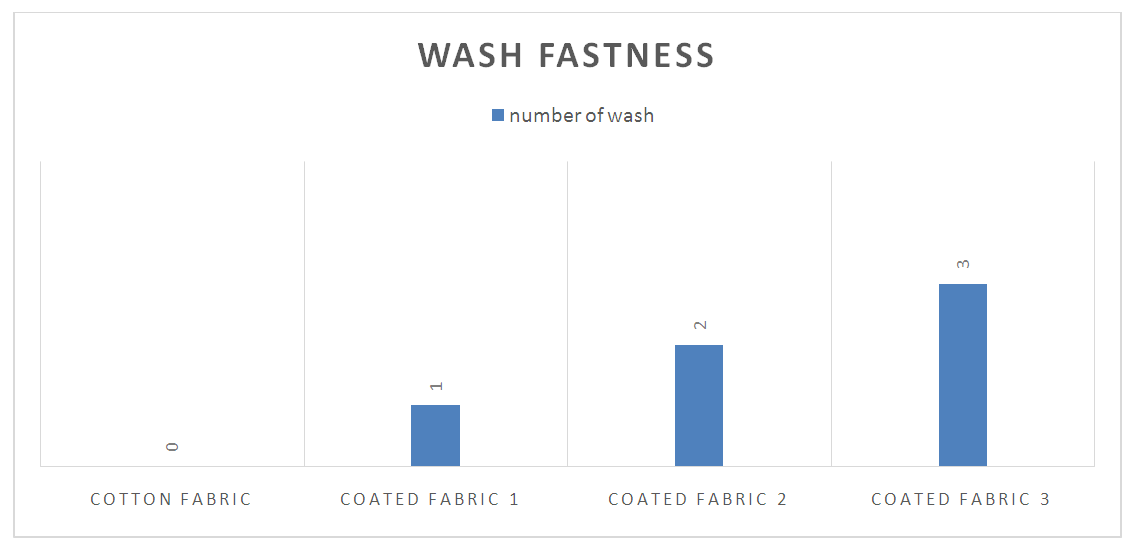 | Figure 9. Wash fastness test graph |
3.4. Drapeability Test Effect
The positive drape ability aligns with the intended goal of developing a coating that not only imparts functional properties but also preserves the inherent characteristics of the cotton fabric. This finding is consistent with the theoretical framework emphasizing the importance of maintaining fabric drape in coating applications. The coated cotton fabric exhibited good drape ability, maintaining its flexibility and suppleness. This characteristic is vital for applications where comfort and aesthetics are essential, such as in apparel.For Knit fabric, Mass of the shaded area = 0.8g Mass of the paper ring = 1.9g Drape co-efficient = 0.8/1.9 = 0.42For coated fabric 1, Mass of the shaded area = 0.75g Mass of the paper ring = 1.9g Drape co-efficient = 0.75/1.9 = 0.39For coated fabric 2, Mass of the shaded area = 0.72g Mass of the paper ring = 1.9g Drape co-efficient = 0.72/1.9 = 0.37For coated fabric 3, Mass of the shaded area = 0.67g Mass of the paper ring = 1.9g Drape co-efficient = 0.67/1.9 = 0.35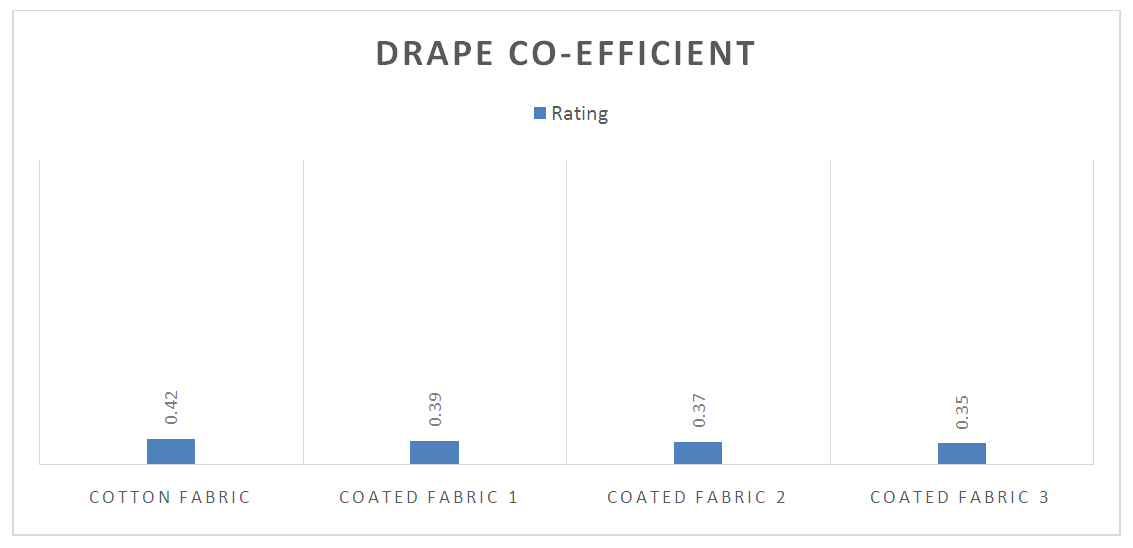 | Figure 10. Drape co-efficient test graph |
4. Conclusions
Combining chitosan and egg white created a partially anti-creasing and water-resistant layer for cotton fabric has produced encouraging results with significant implications for the textile sector. Extensive testing yielded noteworthy results. The novel use of egg white and chitosan as coating agents adds to the growing body of biobased and environmentally acceptable textile treatment methods. This work enhances previous studies by providing a multipurpose, sustainable substitute. The new coating is compatible with cotton fabric, has favorable impacts on drape ability, and is water-repellent. The industry's emphasis on ecologically beneficial practices is aligned with the usage of natural polymers, which expands the possible applications to outdoor gear. This study demonstrates the feasibility of a sustainable approach to textile coatings, offering multifunctional benefits. This natural substitute for coating is an addition to the endeavors to avoid harmful, toxic, carcinogenic chemicals. Future research endeavors may focus on optimizing formulations for enhanced wash fastness, exploring diverse natural polymers, and addressing limitations faced during this thesis work. As the results showed temporary effect but further advancements can be done to achieve durable yet sustainable method of coating by using biodegradable agents.
5. Declaration
Conflict of interest: The authors declare no conflict of interest.
References
[1] | In Situ Adsorption of Red Onion (Allium cepa) Natural Dye on Cellulose Model Films and Fabrics Exploiting Chitosan as a Natural Mordant Rafael Grande, Riikka Räisänen, Jinze Dou, Satu Rajala, Kiia Malinen, Paula A. Nousiainen, Monika Österberg. |
[2] | Exploratory Investigation of Chitosan as Mordant for Eco‐Friendly Antibacterial Printing of Cotton with Natural Dyes MD Teli, J Sheikh, P Shastrakar. |
[3] | Chitosan-based hybrid materials as adsorbents for textile dyes–A review SA Qamar, M Ashiq, M Jahangeer, A Riasat, M Bilal. |
[4] | Chitosan Nanoparticles as Bioactive Vehicles for Textile Dyeing: A Proof of Concept Eduador M. Costa, Sara Silva, Manuela Pintado. |
[5] | Use of Chitosan in Surface Modification of Textile Materials; DANIELA ENESCU. |
[6] | A water-resistant egg white/chitosan/pectin blending film with spherical-linear molecular interpenetrating network strengthened by multifunctional tannin-nisin nanoparticles Xianmin Qin, Xue Cai, Yilin Wang, Linqin Chen, Jingjing Zhao, Yifan Zhang, Shenghui Bi, Ying Zhou, Qiujin Zhu, Yuxin Cheng, Yuanyua. |
[7] | Structure and composition of egg; Sher-e-bangla agriculture university. |
[8] | Development of new natural polymer-based wood adhesives III: effects of glucose addition on properties of chitosan Kenji Umemura · Ayako Mihara · Shuichi Kawai. |
[9] | The Egg White Protein-Hypophosphorous Acid Based Fire Retardant Single Bilayer Coating Assembly for Cotton Fabric (Ajay Vishwakarma, Vennapusa Jagadeeswara Reddy -2021). |
[10] | New product development: Cellulose/egg white protein blend fibers Marta Tomczyńska-Mleko, Konrad Terpiłowski. |
[11] | Egg white proteins/lignin-DAP intumescent multilayer nanocoating for flame retardant cotton fabric Jovana Petkovska, Nina Mladenovic, William Leising, Aliaksandr Baidak, Mishela Temkov, Dejan Mirakovski, Vesna Dimova, Igor Jordanov. |
[12] | Synthesis of Silver Nanoparticles using Egg White: Dye Degradation and Antimicrobial Potential Ankush Kaushik, Deepak Gola, Jyoti Raghav, Dhriti Gupta, Arvind Kumar, Meenu Agarwal, Nitin Chauhan, Sunil Kumar Srivastava, Pankaj Kumar Tyagi. |
[13] | Waterproof and Oil Repellent Treatments of Cotton Fabric Md. Iusuf Khan, Sheikh Sha Alam, Fatema Jannat, Md. Safiqul Islam. |
[14] | Introduction to waterproof and water repellent textiles. In Waterproof and Water Repellent Textiles and Clothing; Elsevier: Amsterdam, The Netherlands, 2018 Loghin, C.; Ciobanu, L.; Ionesi, D.; Loghin, E.; Cristian, I. |
[15] | Influence of a Polyethylene Glycol Treatment on Surface, Liquid Barrier and Antibacterial Properties. Jinkins, Renita S.; Leonas, Karen K. |
[16] | Surface and adhesion properties of poly(ethylene glycol) on polyester(polyethylene terephthalate) fabric surface: Effect of air-atmospheric plasma treatment V. Takke, N. Behary, A. Perwuelz, C. Campagne. |
[17] | Polyethylene glycol grafted cotton as phase change polymer Amit Kumar, Prashant S Kulkarni, AB Samui. |
[18] | Antimicrobial finishing of cotton textile with nanosized silver colloids synthesized using polyethylene glycol Wei Su, Shan Shan Wei, Shun Qin Hu, Jian Xin Tang. |
[19] | Textile fabrics - Determination of resistance to surface wetting (Spray test) Etoffes - Determination de Ia rhistance au mouif/age superficiel (Essai darrosage). |