Abdul Baten Chowdhury1, Md Rashedul Islam2
1Lecturer, Department of Apparel Merchandising & Management, Chattogram BGMEA University of Fashion and Technology (CBUFT), Chattogram, Bangladesh
2Department of Civil & Environmental Engineering, Lamar University, Texas, US
Correspondence to: Abdul Baten Chowdhury, Lecturer, Department of Apparel Merchandising & Management, Chattogram BGMEA University of Fashion and Technology (CBUFT), Chattogram, Bangladesh.
Email: |  |
Copyright © 2025 The Author(s). Published by Scientific & Academic Publishing.
This work is licensed under the Creative Commons Attribution International License (CC BY).
http://creativecommons.org/licenses/by/4.0/

Abstract
Single jersey (s/j) cotton knitted fabric has deformation problems and is now commonly knitted with Lycra (Spandex) yarn to improve the fabric's performance. The Lycra has a significant effect on the physical properties of the knitted fabric. This study conducts a comparative analysis of the physical properties of 100% cotton and 95% cotton- 5% Lycra blended single jersey knit fabrics in both the grey and finished stages. The primary purpose of this project work is to analyze the comparison between the physical properties of grey and finished 100% cotton and cotton with Lycra single jersey knitted fabric. The physical properties of grey and finished cotton-lycra single jersey knitted fabric such as fabric weight (Grams per square meter-GSM), bursting strength, shrinkage, pilling, and abrasion resistance were investigated, and the results were compared between the 100% cotton and cotton-lycra single jersey knitted fabric at both grey and finished fabric stage. It was found that fabric weight, bursting strength, and abrasion resistance were increased for cotton-lycra blended knitted fabric. In contrast, the shrinkage percentage decreased for grey and finished cotton-lycra fabric.
Keywords:
Knitted fabric, Single jersey, Lycra (Spandex), Bursting strength, Shrinkage, Abrasion
Cite this paper: Abdul Baten Chowdhury, Md Rashedul Islam, Comparative Study of Physical Properties of Cotton and Cotton-Lycra Single Jersey Knit Fabrics: Grey Stage vs. Finished Stage, International Journal of Textile Science, Vol. 14 No. 1, 2025, pp. 5-14. doi: 10.5923/j.textile.20251401.02.
1. Introduction
The term that describes the technique of constructing fabrics by forming a continuous length of yarn into columns of vertically intermeshed loops is known as knitting. There are two types of knitting techniques, which are weft knitting and warp knitting [1]. In weft knitting, the loop is formed from a single yarn and runs in the crosswise direction of fabric, but in warp knitting, all the needles work together to form the loop from a full warp sheet, and the loop runs in the lengthwise direction of fabric [2]. In the 5th century, it was believed that knitting originated in the Middle East. In the early history of knitting, Egypt used cotton fibers in the knitting process. Knitting machines were used to knit hosiery for elite classes in the 16th century. By the 20th century, knitting technology became part of modern fashion as it produced a variety of outerwear such as jersey dresses, cardigans, and jumpers for men and women [3]. The fabric that is produced by following the knitting technology is called knitted fabric. Among various knitted fabrics, single jersey knitted fabric is the most common one. Single jersey knitted fabric is made by a single jersey circular knitting machine in which one set of needles, known as cylinder needles, is used. The main characteristic of single jersey knitted fabric is that it has an identical face and backside, which can be identified easily. Single-jersey (s/j) knitted fabric is mostly used for outer garments and undergarments such as T-shirts and Polo-shirts because it has greater comfort ability compared to woven fabric [4]. Knitted fabric relies heavily on the availability of fine, strong, uniformly spun yarn [1]. The most common yarn that is used for producing single jersey knitted fabric is cotton. Cotton fiber, which is soft and flexible, has more absorbency capability and crease tendency. There are two types of cotton yarn, such as carded yarn and combed yarn, which are widely used in knitting factories. The most popular count of cotton yarns that are available in the market is 7s, 10s, 14s, 16s, 20s, 24s, 26s, 30s, 32s, 34s, and 40s [5]. As the cotton yarn is not elastomeric, single-jersey knitted fabric easily undergoes permanent deformation. To recover this problem, nowadays a small amount of Lycra (spandex) fiber is knitted with cotton yarn. The process of knitting cotton yarn with Lycra is known as plating. There are two types of plating systems, such as full plating and half plating. When Lycra is knitted with cotton yarn in every course, it is considered as full plating. On the other hand, when Lycra is knitted with cotton yarn in alternative courses, it is known as half plating. Spandex fiber, which is also commercially known as Lycra fiber, was invented in 1958 by chemist Joseph Shivers at Duponts Benger Laboratory in Waynesboro, Virginia. Lycra is a synthetic fiber in which the fiber-forming substance is a long-chain synthetic polymer composed of at least 85 percent polyurethane by weight [6]. Lycra is also considered the world's best-known elastane fiber brand because it can stretch up to six times its length and return to its original shape. In recent years, the use of lycra yarn in knitted fabric has increased due to its excellent wear comfort and fit ability [7]. Lycra yarns are always processed with one or more other yarns, such as cotton, polyester, wool, or silk. The elasticity of spandex yarn varies from 60% to 300%, and this is reflected in the final characteristics of knitted fabric. Spandex yarn is available at different counts and types in the market, such as 20D, 40D, and 75D [8]. The percentage of spandex yarn knitted with other yarn depends on the fabric stretch and fabric properties [6]. When spandex yarns are processed with cotton yarns, the physical properties of single jersey cotton knitted fabric, such as bursting strength, shrinkage, abrasion resistance, pilling resistance, GSM, air permeability, crease, and spirality, are affected. There are several research works available that examined the effect of spandex yarn on finished s/j knitted fabric, but these may not help to conclude the effect on knitted fabric of gray stage. However, this study tried to mitigate this gap by examining the physical properties such as Grams per Square Meter (GSM), bursting strength, shrinkage, pilling, and abrasion resistance of 100% cotton and cotton/spandex s/j knitted fabric in both grey and finished stages.
2. Literature Review
From the previous studies, several research works have been done about the physical and mechanical properties of single jersey cotton knitted fabric. The majority of the research has considered the spandex yarn effect as the basis, while others considered spandex yarn and stitch length as the basis for their research.Sadek et al. studied the effect of lycra extension percentage on s/j knitted fabric properties. In this study, they investigated the geometrical, mechanical, and physical properties of plain jersey fabrics. The main purpose of this research was to predict the optimal lycra extension percentage for improving fabric quality. These properties were investigated for half plating and full plating cotton/spandex fabric at five different levels of lycra extension. All of these samples were finished with plain jersey knit fabric. The results showed that fabric weight and thickness were increased, but the air permeability of half-plating and full-plating fabrics was reduced with lycra percentage extension. The results also showed that the breaking load, extension also increased, and abrasion resistance also increased in the case of full-plating cotton/spandex s/j knitted fabric than half-plating fabric [9].Sitotaw researched on the dimensional characteristics of knitted fabric made from 100% cotton and cotton/elastane yarns. He investigated the dimensional characteristics such as loop length, wales per centimeter (wpc), courses per centimeter (cpc), stitch density, tightness factor, loop shape factor, and take-up rate of s/j, 1x1 rib. 1x1 interlock, single pique, and two-thread fleece. He compared the results with 100% cotton knitted fabric. It was apparent that the loop length of s/j was 1x1 rib. 1x1 interlock fabrics made with spandex yarn were decreased, but for single pique, and fleece, the loop length was increased with elastane yarns. He also found that the wpc and cpc of those knitted fabrics were increased for cotton/elastane yarns. The stitch density of single jersey, single pique and fleece fabrics increased whereas the stitch density of rib and interlock decreased due to elastane yarns. The results also showed that the tightness factor of rib and interlock fabrics was decreased while single pique and fleece fabrics increased with cotton elastane yarns [10].Abdessalam and Abdelkader studied the influence of lycra consumption on plated plain knitted fabric dimensional and elastic behavior. They studied the three main parameters, which are width, weight, and elasticity of plated plain knitted fabrics. Their research aimed to analyze the relationship between lycra consumption and fabric dimensional and elastic behavior. They examined the fabric made with combed yarn, and the plating yarn was 22-dtex lycra. The results showed that the fabric weight linearly increased with the increase in lycra consumption, and the fabric recovery increased with the amount of lycra increases [11].Eltahan investigated the effect of lycra percentage and loop length on the physical and mechanical properties of single jersey knitted fabrics. For the research, he examined the dimensional, physical, and mechanical properties of finished back-plaited cotton/spandex single jersey knitted fabrics, and the results were compared with 100% cotton knitted fabric. He worked with 100% cotton fabric with different loop lengths and cotton knitted fabric with different lycra ratios. In this study, he found that when loop length is increased, specific fabric hand and extension increased, but bursting strength and fabric recovery were decreased, whereas the loop length did not affect the weave density of the fabrics. The results also showed that fabric course density, thickness, and recovery would be increased while fabric width, porosity, and fabric extension were decreased due to the presence of lycra [12].Haji studied the physical and mechanical properties of cotton/spandex fabrics, and the results were compared with 100% cotton knitted fabric. The effect of loop length was also investigated in this research. He used the fabrics, which are made with cotton yarn of 30/1 Ne and spandex yarn count of 44dtex. The investigated results showed that bursting strength, fabric weight, crease recovery, course density, wales density, and pilling resistance rating were improved with spandex yarn whereas air permeability was reduced. In the case of higher loop length, he found that the fabric weight, crease recovery, dimensional stability in the lengthwise direction, and bursting strength were decreased, whereas air permeability and pill formation tendency were improved [13]. Eryuruk analyzed the performance properties of knitted fabric containing elastane. For the research, he examined the performance properties of 12 s/j half- and full-palting knitted dyed fabrics. The main purpose of his study was to analyze the effect of elastane yarn count and ground yarn count on fabric performance properties. The results showed that for all types of fabric, the bursting strength value increased while the spirality and air permeability values decreased with the increase in elastane amount and count [14].Herath and Kang studied the dimensional stability of core-spun cotton/spandex s/j fabrics of different tightness factors under dry, wet, and full relaxation. From the results, it was apparent that spandex yarn increases the tightness factor and gives better dimensional stability to the fabrics. It was also found that course, wale, and stitch density increased with progression of relaxation and increase in spandex, while course and wale spacing decreased [15]. Tezel and Kavusturan studied the experimental effects of spandex and the tightness factor on the physical and dimensional properties of s/j knitted fabrics. In this experimental work, they examined tight, medium, and loose cotton/spandex s/j fabrics that were produced with three different adjustments of the positive yarn feeding mechanism and with four different spandex yarns. The results showed that fabric weight, cpc, stitches per cm, and fabric thickness increased while air permeability value decreased as the spandex yarn amount increased [16].Kumar and Sampath did an investigation on the physical and dimensional properties of s/j fabrics made from cotton/elastane core spun yarn. The main purpose of this study was to investigate the suitability of cotton/elastane core spun yarn for circular knitting machines and the effect of stitch length variables on knitted fabric geometric quality attributes such as weave density, course density, stitch density, and aerial density under different stages of relaxation. It was apparent that the stitch length effect is inversely proportional to fabric geometric attributes [17].Bayazit studied the dimensional and physical properties of cotton/spandex s/j knitted fabrics. In this research, he compared the investigated value with 100% cotton s/j knitted fabrics and found that the loop length remained the same while course and wale spacing decreased as the amount of spandex increased. The results also showed that the air permeability, pilling grade, and spirality were lower, whereas fabric weight per unit area was increased with an increase in spandex yarn [18].In the literature, all the research work was done by investigating the s/j cotton knitted fabric of the finished stage. Some studies [9,11,14] considered the lycra extension percentage of full-plating and half-plating systems as the basis for their research works. While some research [12,13] described the effect of spandex on s/j knitted fabric about lycra% and loop length. Other studies [15,16,17] were done on the basis of core-spun cotton yarn and the tightness factor to investigate the effect of spandex on s/j knitted fabric.All the research is only concerned with the knitted fabric of the finished stage. So the work that analyzes the physical properties of 100% cotton and cotton/spandex knitted fabric in grey stage is scanty. Consequently, this project tried to mitigate this gap by investigating the physical properties of 100% cotton and cotton/spandex (cotton 95% + spandex 5%) s/j knitted fabric in both grey and finished fabric stages.
3. Materials and Methods
3.1. Materials
For this project work, four separate single jersey knitted fabric samples were used. Two of them were grey fabric, while the rest were finished fabric. Between two grey fabric samples, one sample was knitted with 100% cotton yarn and the other was knitted with 95% cotton and 5% lycra. In the case of finished fabric, they were also knitted as same as the grey fabric knitted technique. Here, the carded cotton yarn count was 166 denier and the lycra count was 20 denier for both grey and finished stage fabrics. All of the samples were knitted in a Lisky Single Jersey Circular Knitting Machine containing a 30-inch diameter and 24 gauge. Among the four fabric samples, the two finished fabrics were subjected to similar dyeing, washing, and finishing processes. The finished fabric samples were dyed in the Winch dyeing machine. Pretreatment, dyeing, and after-treatment recipe for finished 100% cotton and cotton/spandex s/j knitted fabric: Pre-treatment:
Dyeing:
After treatment:
Finishing process for 100% cotton s/j knitted fabric: Ø Squeezing Ø Slitting Ø Compacting for shrinkage control Finishing process for cotton/spandex s/j knitted fabric: Ø Slitting before dyeing Ø Heat setting by stenter machine Ø Squeezing Ø Stentering for dia adjust Ø Open compacting Identification of four samples: § G-1: 100% cotton single jersey grey knitted fabric§ G-2: Cotton-Lycra (cotton 95% and lycra (spandex) 5%) single jersey grey knitted fabric§ F-1: 100% cotton single jersey finished knitted fabric§ F-2: Cotton-Lycra (cotton 95% and lycra (spandex) 5%) single jersey finished knitted fabric
3.2. Machineries
All of the machineries that were used in conducting the project work were from SM Knitwears Limited, Dhaka. 1. Machine Name: Single Jersey Circular Knitting MachineBrand: Lisky Machine Diameter: 30 inchMachine Gauge: 24No. of Feeder: 90Origin: Taiwan2. Machine Name: Opti-Burst (Bursting Strength Tester) Brand: Roaches Origin: UK 3. Machine Name: Washing Machine Brand: Electrolux Model no. W555HOrigin: Sweden 4. Machine Name: Tumble DryerBrand: Electrolux Model No. T5130 Origin: Sweden 5. Machine Name: Martindale (Abrasion and Pilling Tester) Brand: Roaches Origin: UK 5.1. Methods List of the test:- Ø Fabric Weight (GSM) Ø Bursting Strength Ø Shrinkage Ø Pilling Resistance Ø Abrasion Resistance Table 1. Method of the tests and equipment’s 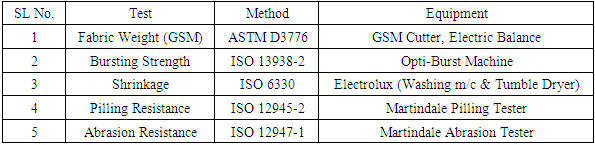 |
| |
|
4. Experimental Works
The physical properties of grey and finished cotton-lycra single jersey knitted fabric, such as fabric weight (GSM), bursting strength, shrinkage, pilling, and abrasion resistance, were examined.
4.1. Fabric Weight (GSM)
The samples were cut from the fabric by using a GSM cutter and weighed on an electrical balance. Among the four samples (G-1, G-2, F-1, F-2) each sample was tested three times. The test was conducted according to the ASTM D3776 standard.
4.2. Bursting Strength
The bursting strength of samples was measured by an automatic bursting strength tester. Each sample was set on the machine and followed the diaphragm bursting strength test method to test bursting strength. Each fabric sample was tested three times, and the mean value was considered as the result. The specimen size was 15 cm in diameter.
4.3. Shrinkage
The sample of 50 cm x 50 cm was cut from fabric by a scissor. A template was placed on the sample and the inside area of 35 cm x 35 cm. Then the sample was run on the washing machine for 30 minutes at 40°C temperature; after that, it was dried by a tumble dryer. A measuring scale was used to measure the dimensions of the tested sample. Every sample was tested three times to get an accurate result. The result was calculated using the formula of shrinkage percentage for both length and width directions.
4.4. Pilling Resistance
For the pilling test, the sample fabrics were tested in a Martindale pilling tester. The sample was cut from the fabric and mounted on the machine through the holder. Each sample was tested three times. The sample size is 140 mm in diameter. The pilling grading results were recorded two times; the first one was after 500 cycles, and the rest one was after 1000 cycles.
4.5. Abrasion Resistance
The abrasion resistance test was done by using a Martindale abrasion tester. After cutting the specimen of 38 mm diameter, the weight of the sample was noted. The sample was held by a holder and was mounted on the machine. A pressure of 9 kpa was applied to the fabric through the spindle, and after 5000 cycles of the machine, the weight of the specimen was recorded again. All of the samples were tested three times, and a mean value was considered as the result.
5. Results
5.1. Fabric Weight (GSM)
Table 2. GSM of the grey knitted fabric samples 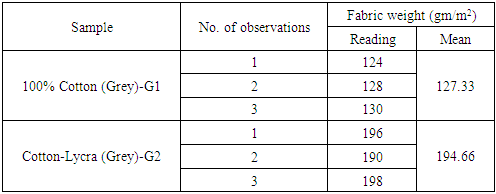 |
| |
|
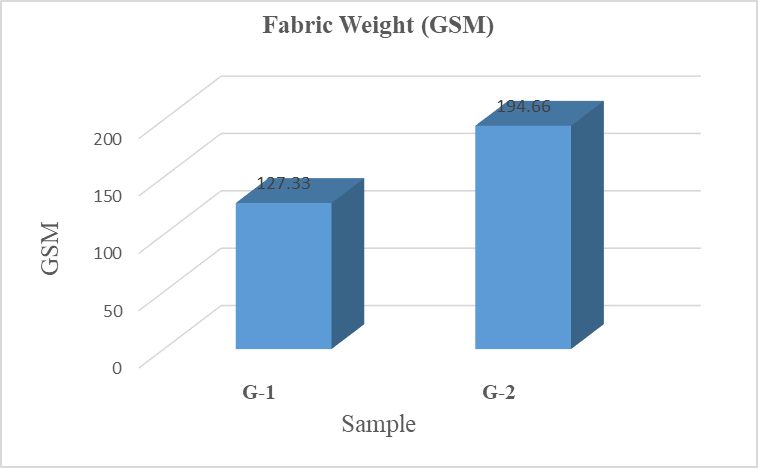 | Figure 1. Fabric weight of 100% cotton and cotton-lycra s/j knitted fabric in grey stage |
From the results, it was apparent that the weight of cotton-lycra is around 52% higher than that of 100% cotton s/j knitted fabric.Table 3. GSM of the finished knitted fabric samples 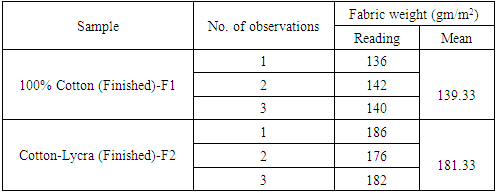 |
| |
|
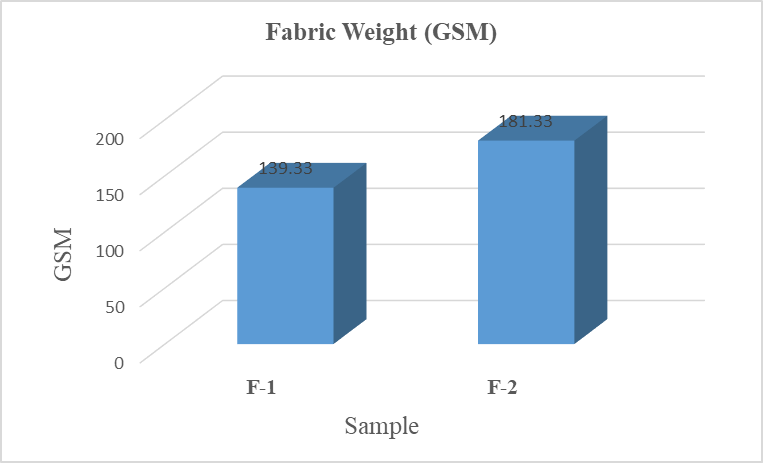 | Figure 2. Fabric weight of 100% cotton and cotton-lycra s/j knitted fabric in the finished stage |
In the case of the finished fabric stage, the weight of cotton-lycra knitted fabric was around 30% higher than that of 100% cotton s/j knitted fabric.
5.2. Bursting Strength
Table 4. Bursting strength of the grey knitted fabric samples 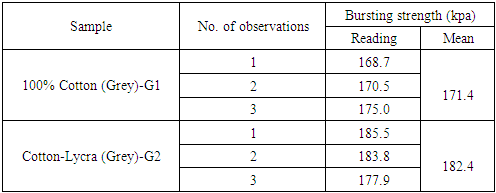 |
| |
|
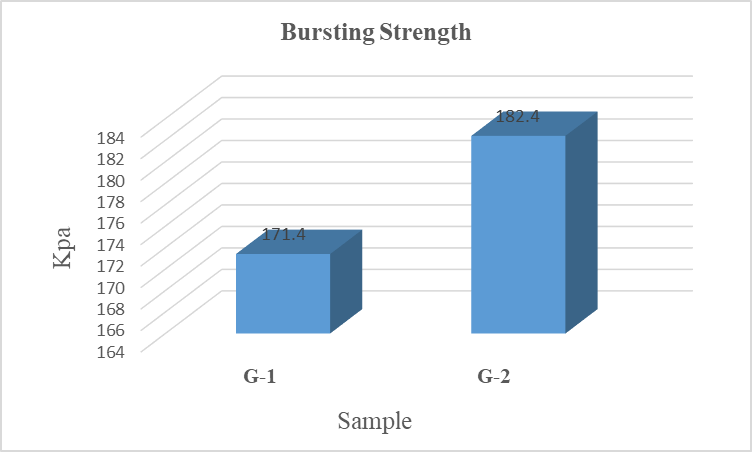 | Figure 3. Bursting strength of 100% cotton and cotton-lycra s/j knitted fabric in grey stage |
It was apparent that the bursting strength of cotton-lycra knitted fabric is around 6% higher than that of knitted fabric with cotton alone. Table 5. Bursting strength of the finished knitted fabric samples 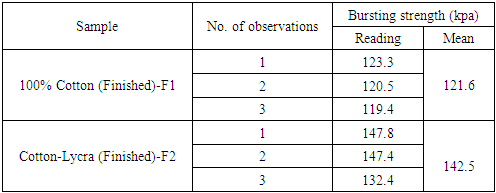 |
| |
|
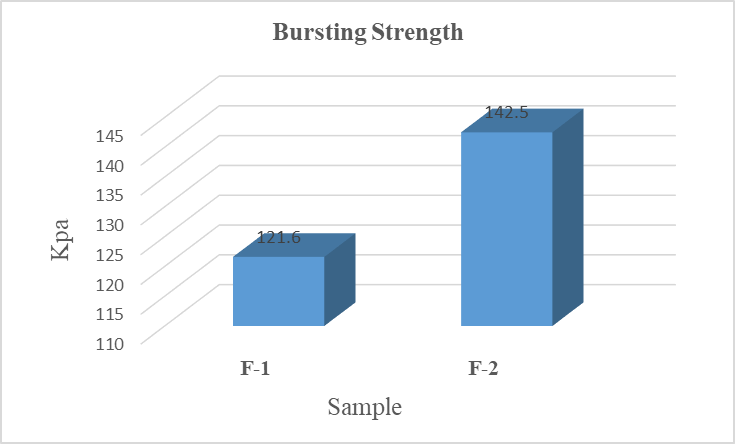 | Figure 4. Bursting strength of 100% cotton and cotton-lycra s/j knit fabric in the finished stage |
It was shown that the bursting strength of cotton-lycra knitted fabric is around 17% higher than that of knitted fabric with cotton alone.
5.3. Shrinkage
Table 6. Dimension change of grey and finished knitted fabric samples 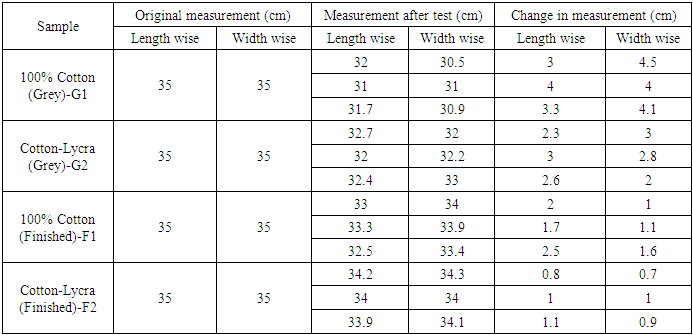 |
| |
|
Table 7. Shrinkage (%) of the grey knitted fabric samples 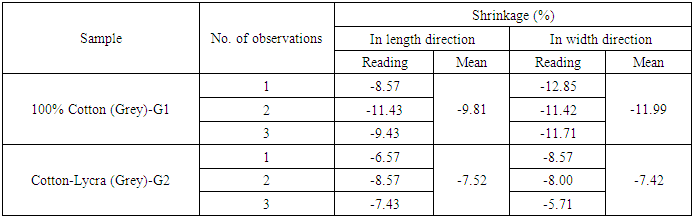 |
| |
|
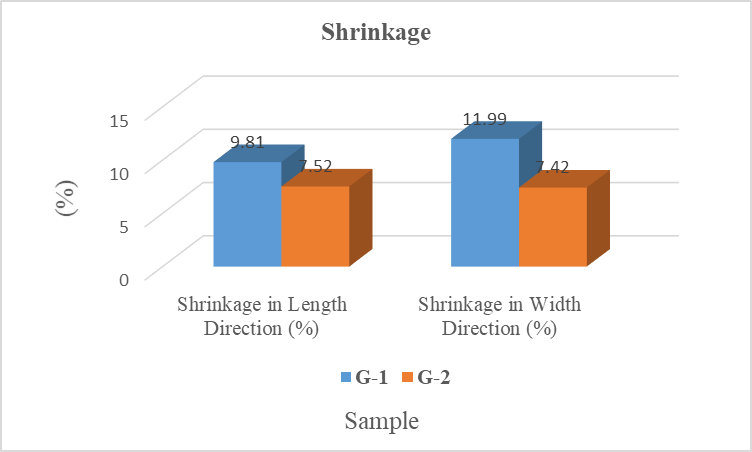 | Figure 5. Shrinkage (%) of grey 100% cotton and cotton-lycra s/j knitted fabric in the lengthwise and widthwise direction |
From the results, it was seen that shrinkage in length direction for 100% cotton knitted fabric was around 30% more than that of cotton-lycra knitted fabric and in width direction the difference was significantly high and value was around 61%. Table 8. Shrinkage (%) of the finished knitted fabric samples 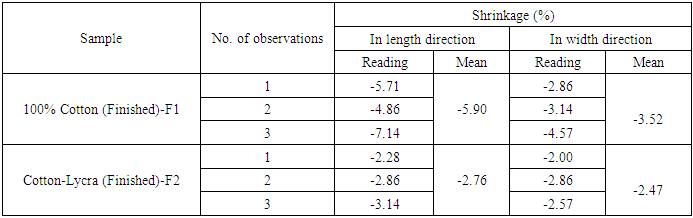 |
| |
|
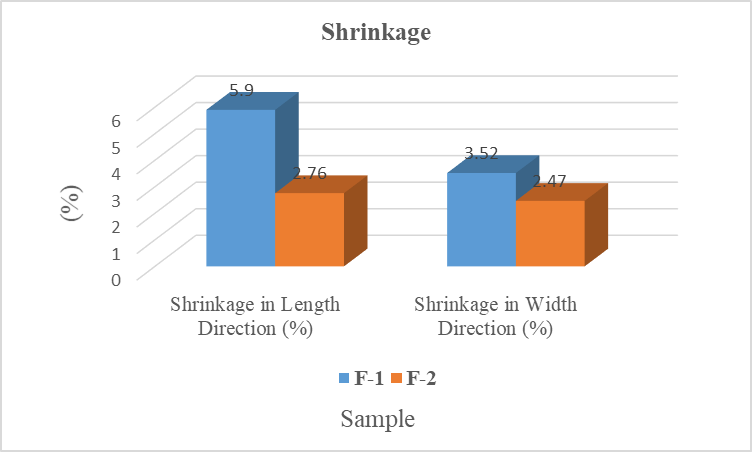 | Figure 6. Shrinkage (%) of 100% cotton and cotton-lycra s/j knitted fabric in lengthwise and widthwise direction of finished stage fabric |
From the results, it was seen that shrinkage in length direction for 100% cotton knitted fabric was around 113% more than that of cotton-lycra knitted fabric and in width direction, the difference between 100% cotton and cotton-lycra knitted fabric was around 42% higher in favor of 100% cotton knitted fabric.
5.4. Pilling Resistance
Table 9. Pilling resistance of the grey knitted fabric samples 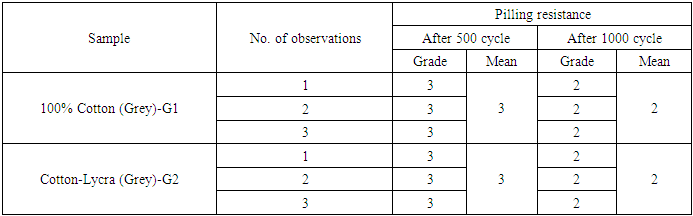 |
| |
|
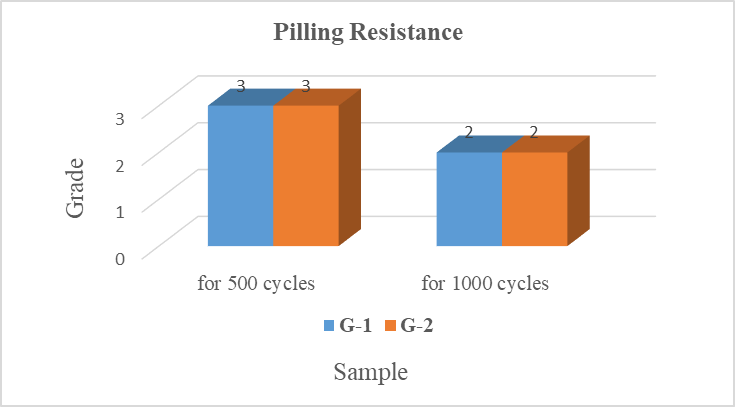 | Figure 7. Pilling resistance of 100% cotton and cotton-lycra s/j knitted fabric in grey stage |
There was no difference in the case of the pilling test for both 100% cotton and cotton-lycra s/j knitted fabric in the grey stage. Table 10. Pilling resistance of the finished knitted fabric samples 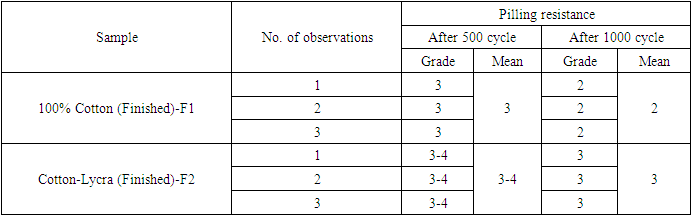 |
| |
|
 | Figure 8. Pilling resistance of 100% cotton and cotton-lycra s/j knitted fabric in the finished stage |
In the case of finished stage fabric, cotton-lycra knitted fabric shows more resistance to pilling than 100% cotton knitted fabric.
5.5. Abrasion Resistance
Table 11. Abrasion resistance of the grey knitted fabric samples 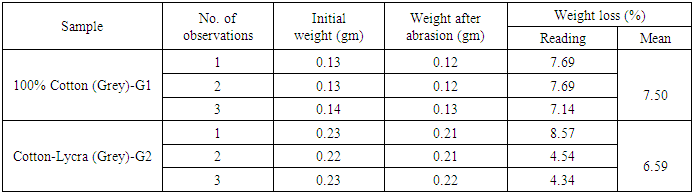 |
| |
|
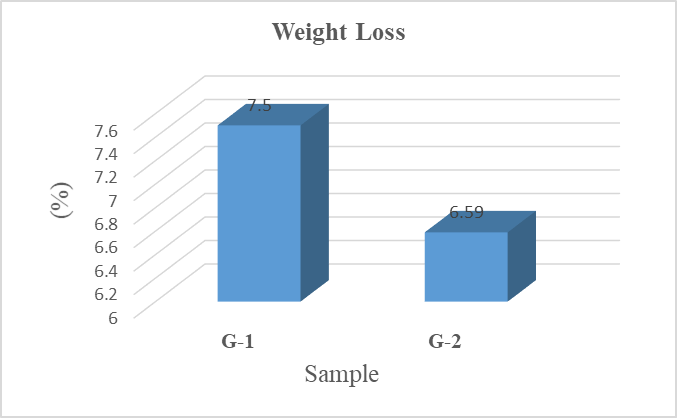 | Figure 9. Weight loss (%) of grey 100% cotton and cotton-lycra s/j knitted fabric |
It was apparent that weight loss for 100% cotton knitted fabric was around 13% higher than that of cotton/spandex knitted fabric which means the cotton-lycra fabric showed more resistance to abrasion. Table 12. Abrasion resistance of the finished knitted fabric samples 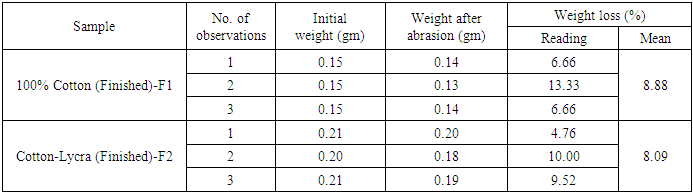 |
| |
|
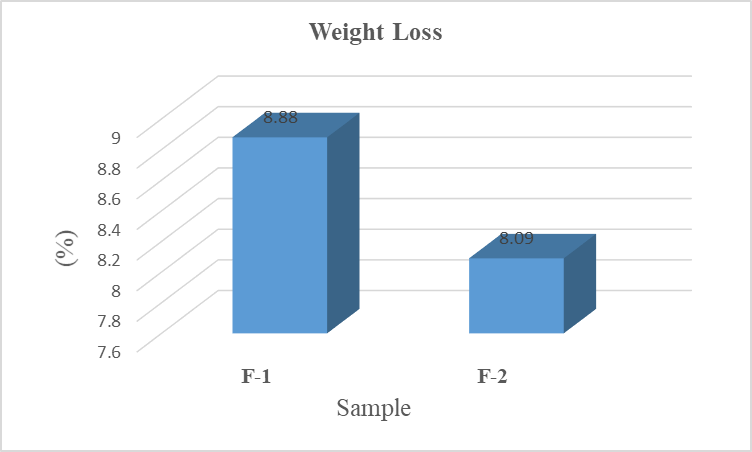 | Figure 10. Weight loss (%) of 100% cotton and cotton-lycra s/j knitted fabric in the finished stage |
In the case of finished stage fabric, weight loss for 100% cotton knitted fabric was a little bit 9.76% higher than that of cotton-lycra knitted fabric which means the cotton-lycra fabric showed more resistance to abrasion.
6. Discussions
6.1. Fabric Weight (GSM)
From the results, it was apparent that the GSM of cotton-lycra s/j knitted fabric was more than that of 100% cotton fabric because when lycra is knitted with cotton yarn, the space between the wales decreased, and as a result, wpc was increased because the lycra in the fabric tends to contract the loops to each other. So the fabric becomes tighter and the fabric thickness is increased. This condition is applicable for both gray and finished stages of fabric. The statistical analysis also showed that the difference in GSM between 100% cotton and cotton/spandex s/j knitted fabric was greater in grey stage fabric because in grey stage fabric weight was not controlled by the finishing process as in finished stage fabric. In the case of finished stage fabric, GSM was adjusted in the finishing process according to requirements by overfeed and underfeed mechanisms in the stenter and compactor machines.
6.2. Bursting Strength
The statistical analysis showed that the bursting strength of cotton-lycra knitted fabric is greater than that of 100% cotton/j knitted fabric for both grey and finished fabric stages. When spandex fiber is knitted with cotton yarn in the fabric, it allows the fabric to expand more, makes the fabric tighter, and increases compactness. As cotton-lycra knitted fabric is tighter and more compact than 100% cotton knitted fabric, more pressure is required to burst the fabric. While comparing grey and finished stage fabric, the bursting strength of finished fabric for both 100% cotton and cotton/spandex is less than grey fabric because finished fabric undergoes various processes such as scouring, bleaching, enzyme treatment, dyeing, washing, and finishing, and it loses its strength due to different process pressure. From the observation, it is also said that the difference in bursting strength between finished 100% cotton and cotton-lycra knitted fabric was more, but in the case of grey fabric samples, this difference was a little bit less between 100% cotton and cotton-lycra s/j knitted fabric.
6.3. Shrinkage
In the case of the shrinkage test, the shrinkage percentage both in the lengthwise and widthwise direction of 100% cotton s/j fabric is higher than that of cotton-lycra fabric for both grey and finished stage fabric. As the spandex yarn has more elastic capability and good dimensional stability, it helps to retain the dimensional stability of the fabric after washing. Spandex yarn also increases the gsm of the fabric; as a result, higher gsm allows a low shrinkage percentage. The cotton/spandex knitted fabric has higher gsm and better capability to retain its original shape after washing due to the presence of spandex yarn. As a result, cotton/spandex knitted fabric showed less shrinkage than s/j knitted fabric, which was produced with cotton alone. The shrinkage percentage is higher in the case of the grey fabric stage than that of the finished fabric stage because there is no finishing process applied to the grey fabric like in the finished fabric.
6.4. Pilling Resistance
From the observation, it is said that there was no significant difference between 100% cotton and cotton-lycra s/j knitted grey fabric in the pilling test because pilling formation is largely dependent on yarn quality and all the fabric samples were made from the same quality yarn. But in the case of finished fabric, there was a little bit of a change in pilling grade between 100% cotton and cotton-lycra s/j knitted fabric, where cotton/spandex knitted fabric tends to show more resistance to pill formation than 100% cotton knitted fabric because spandex yarn made the fabric tighter and smoother. Spandex yarn also increased the compactness of fabric construction; as a result, fiber migration became more difficult, so cotton-lycra finished knitted fabric showed more resistance to pilling.
6.5. Abrasion Resistance
In the case of the abrasion test, the weight loss percentage of 100% cotton s/j knitted fabric was a little bit more than that of cotton-lycra s/j knitted fabric for both grey and finished fabrics. When spandex yarn is knitted with cotton yarn in s/j knitted fabric, the fabric becomes tighter, smoother, and increases hand feel. As a result, cotton/spandex knitted fabric showed more resistance to abrasion. While comparing grey and finished fabric, it was apparent that the grey fabric had a lower weight loss tendency than the finished fabric because in the finished stage fabric, some finishing chemicals were applied to the fabric, which was partially reduced during the abrasion resistance test due to friction. The fabric that had a lower weight loss tendency had higher abrasion resistance. So grey stage fabric cotton-lycra s/j fabric has more resistance to abrasion than finished stage fabric as well, and cotton-lycra knitted fabric showed more abrasion resistance than that of 100% cotton s/j knitted fabric.
7. Conclusions
This project study studied the comparative analysis of fabric physical properties between 100% cotton and 95% cotton & 5% lycra blended s/j knitted fabric at both grey and finished stages. Among the various physical properties of GSM, bursting strength, shrinkage, pilling, and abrasion resistance were examined. Here the physical properties of cotton-lycra single jersey knitted fabric were compared with the result of the physical properties of 100% cotton single jersey knitted fabric in both grey and finished stages. All of the investigated fabric was made with the same yarn type and count and in the same knitting machine. The results obtained from the test indicated that fabric knitted with spandex yarn has a significant impact on the fabric's physical properties. It has been shown that the fabric weight, bursting strength, and abrasion resistance were higher in cotton-lycra s/j knitted fabric than that of 100% cotton knitted fabric. The shrinkage tendency was less in cotton/spandex knitted fabric. The impact of lycra on the fabric's physical properties varies in the case of the gray and finished fabric stages. Besides lycra attachment, other parameters such as yarn type, yarn count, stitch length, and machine performance also affect the physical properties of the knitted fabric. Like all other research works, this study has its limitations. There was the limitation of time and collection of the samples; if more samples were tested, then the results would be more accurate. We tried our best to get an accurate result, and for this reason, each fabric sample was tested three times for more accuracy. This project basically helped us to gain knowledge about the physical properties of s/j knitted fabric. It also helps the knitting factory to get an idea about the physical properties of s/j knitted fabric in different stages. The researchers of the country who are interested in conducting such comparative work will also benefit and get ideas and respective data from this project work.
CRediT Authorship Contribution Statement
Abdul Baten Chowdhury: Writing- original draft, Methodology, Investigation, Formal analysis, Conceptualization, Data Curation. Md Rashedul Islam: Writing- review & editing, Methodology, Data curation, Visualization, Funding Acquisition.
Declaration of Competing Interest
The authors declare no conflict of interest.
Data Availability
Data will be made available on request.
ACKNOWLEDGEMENTS
The authors would like to thanks SM Knitwears Limited, Dhaka for their support in conducting respective tests regarding this project work. Special appreciation to the BGMEA University of Fashion & Technology (BUFT), Dhaka and Lamar University, Texas for support in the experimental study.
References
[1] | D. J. Spencer, Knitting Technology, Leicester: Woodland Pblishing Limited, 2001. |
[2] | A. B. Siddique and H. A. Begum, Introduction to Textile Engineering, Dhaka: Books Fair Publications, 2016. |
[3] | "Knitting History," 2017. [Online]. Available: https://www.the-sustainable-fashioncollective.com/2017/05/04/knitting-brief-history-knitting-uses. [Accessed 14 August 2024]. |
[4] | E. S. A. Belal, Understanding Textiles for a Merchandiser, Dhaka: BMN Foundation, 2009. |
[5] | D. M. A. Sayeed, General Knowledge in Textiles & Garments, Dhaka: University Campus, 2016. |
[6] | R. Meredith, Elastomeric Fibers, Woodhead Publishing Limited, 2004. |
[7] | "Definition of Lycra," 2023. [Online]. Available: https://www.lycra.com/en/lycra-about-lycra-fiber/what-lycra-fiber. [Accessed 13 August 2024]. |
[8] | D. Gupta and S. Gupta, "Fusing Developments in Pressing and Finishing," ATA Journal, vol. 2, pp. 98-99, 2009. |
[9] | R. Sadek, A. M. El-Hossini, A. S. Eldeeb, A.A. Yassen, "Effect of Lycra Extension Percentage on Single Jersey Knitted Fabric Properties," Journal of Engineered Fibers and Fabrics, vol. 7, no. 2, pp. 11-16, 2012. |
[10] | D. B. Sitotaw, "Dimensional Characteristics of Knitted Fabrics Made from 100% Cotton and Cotton/Elastane Yarns," Journal of Engineering, vol. 2018, no. 1, pp. 1-9, 2018. |
[11] | S. B. Abdessalem, Y. B. Abdelkader, S. Mokhtar and S. Elmarzougui "Influence of Elastane Consumption on Plated Plain Knitted Fabrics Characteristics," Journal of Engineered Fibers and Fabrics, vol. 4, no. 4, 2019. |
[12] | E. Eltahan, "Effect of Lycra Percentage and Loop Length on the Physical and Mechanical Properties of Single Jersey Knitted Fabrics," Journal of Composites, vol. 2016, no. 1, pp. 1-7, 2016. |
[13] | M. Haji, "Physical and Mechanical Properties of Cotton/Spandex Fabrics," Pakistan Textile Journal, vol. 62, pp. 52-55, 2013. |
[14] | S. H. Eryuruk and F. Kalaoglu, "Analysis of the performance properties of knitted fabrics containing elastane," International Journal of Clothing Science and Technology, vol. 28, no. 4, pp. 463-479, 2016. |
[15] | C. N. Herath and B. C. Kang, "Dimensional Stability of Core Spun Cotton/Spandex Single Jersey Fabrics under Relaxation," Textile Research Journal, vol. 78, no. 3, pp. 209-216, 2008. |
[16] | S. Tezel and Y. Kavuşturan, "Experimental Investigation of Effects of Spandex Brand and Tightness Factor on Dimensional and Physical Properties of Cotton/Spandex Single Jersey Fabrics," Textile Research Journal, vol. 78, no. 11, pp. 966-976, 2008. |
[17] | V. Kumar and V. R. Sampath, "Investigation on the Physical and Dimensional Properties of Single Jersey Fabrics made from Cotton Sheath - Elastomeric Core Spun," Fibres & Textiles in Eastern Europe , vol. 21, no. 3, 2013. |
[18] | A. B. Marmarali, "Dimensional and Physical Properties of Cotton/Spandex Single Jersey Fabrics," Textile Research Journal, vol. 73, no. 1, pp. 11-14, 2003. |