Md. Enamul Haque, Rajib Kabiraj, Md. Mostafa Khan, Md. Suja Uddin Kaiser, Md. Bokthier Rahman
Department of Textile Engineering, Khulna University of Engineering & Technology (KUET), Khulna, Bangladesh
Correspondence to: Md. Enamul Haque, Department of Textile Engineering, Khulna University of Engineering & Technology (KUET), Khulna, Bangladesh.
Email: |  |
Copyright © 2023 The Author(s). Published by Scientific & Academic Publishing.
This work is licensed under the Creative Commons Attribution International License (CC BY).
http://creativecommons.org/licenses/by/4.0/

Abstract
Fabric quality is important from the view of customer satisfaction. About 90% of the fabric defects in the grey fabric originate during weaving in the loom shed. Denim fabric is highly sensitive for defects, mainly like starting marks, broken pick, snarl and missing end etc. One of the most significant weaving-related flaws in woven cloth is the starting mark. This Starting mark, for which fabric quality degrades, is affected by a number of factors and circumstances. This study mainly emphasized on the control of fabric defects in denim weaving at weaving stage by conducting the trials on the respective machine settings of air-jet loom. In this work the appropriate factors for the starting mark in the different construction of the fabric have been investigated and it also has been observed that mechanical settings affect strongly on this starting mark than electrical settings. Trial results show significant reduction of fabric defects and also rejection percentage.
Keywords:
Denim, Woven Textiles, Weaving Machine, Starting Mark, Warp Tension, Mechanical Setting, Electrical Setting
Cite this paper: Md. Enamul Haque, Rajib Kabiraj, Md. Mostafa Khan, Md. Suja Uddin Kaiser, Md. Bokthier Rahman, Effect of Machine Parameters on Starting Mark in Textiles Denim Weaving Process, International Journal of Textile Science, Vol. 12 No. 1, 2023, pp. 1-9. doi: 10.5923/j.textile.20231201.01.
1. Introduction
Bangladesh is the second vast garments exporter of western fashion brands. Among them, 60% of contracts are with European buyer, and 40% is with American buyer. The textile and clothing industry of Bangladesh has been the foremost driver of national exports and the GDP for the last 40 years. In 2016-2017 the RMG industry raised US$28.14 billion, which was 80.7% of the total export earnings in exports and 12.36% of the GDP. Because of some weaknesses in textile processes and systems, the textile industry of Bangladesh has been unable to sustain itself in some sectors. Denim is one of the most prominent and rising parts in Bangladesh RMG. As of now, Bangladesh is the largest exporter of denim products to Europe topping China with a 27% market share, with a 14.20% market share the largest exporters of clothing products to both Europe and the US. Bangladesh is also considered the third largest exporter of denim products in the US after Mexico and China. To improve the performance of their manufacturing processes, industries are turning towards effective management techniques and quality improvement methodologies [1].Quality is the most variable thing that thoroughly relies upon the customer’s demand. Similar properties in a material could be the most attractive quality for a customer however it is not for the other shopper. It has an incredible connection with the style of the time. For instance, the blurring impact in the pants jeans is the most alluring quality for youthful age individuals, and additionally, it is conceded as a most in-vogue texture however then again it isn’t the quality for old age individuals. The feeling of texture qualities, it is a deficiency because of loss of quality [2]. Among all this faults loom bar or starting mark is the most common fault. Due to this starting mark fabric is rejected in dyeing and printing. It creates a lot of problems in the fabric. There is frequently a start-up mark (stop mark) on the fabric where the local pick density deviates from the expected value when a loom is stopped and restarted. The start-up marks' existence and severity directly affect the price of the fabrics produced. The relaxation of the warp and fabric, as well as the loom's dynamic properties during startup, are the main causes of start-up marks in woven fabrics. Start-up marks can be lessened in impact by a variety of techniques. An innovative technique to get rid of the start-up marks has been put out in this study. In this method, when the loom pauses, the warp tension is reduced to almost zero, and the loom parameter is readjusted when the loom restarts. The efficiency of the current method is mostly unaffected by the length of the loom halt, which is one of its key advantages. Any loom with digital let-off and take-up controls can use the low-tension approach for preventing startup marks. The steps to manage the location of the cloth to stop start-up marks are described. The technique's efficacy, simplicity, and adaptability have all been tested in industrial settings creating many sorts of fabrics.
2. Objective
• To know the root causes of the starting mark. • To know the problem associated with starting mark in the fabric. • To analyze the different machine setting parameters that affect the starting mark. • To execute the new setting on machine. • To know the effect of starting mark on different fabric construction.
3. Experimental Details
The analysis should be diagnostic in character to make it easy to identify defective looms and ineffective weavers that cause damage that occurs repeatedly. It is important to accumulate information on fabric flaws from looms that produce an excessive amount of defects, and then provide an appropriate statement that includes the loom numbers, sort number, type of flaw, shift, and data occurrences. Sending this to the weaving department for correction is a good idea. If the problem is loom-related, the appropriate setting should be changed, and if the problem is the weaver's fault for being careless, it should be brought to his notice. 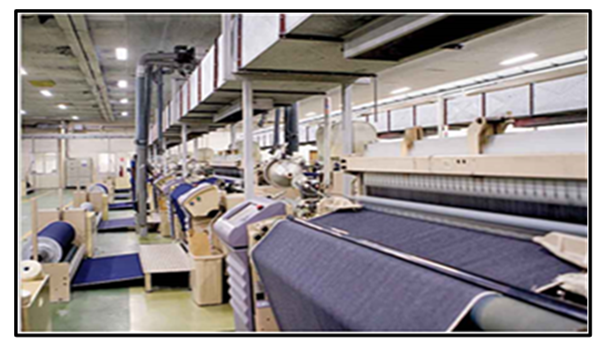 | Figure 1. Fabric Manufacturing Machine |
3.1. Starting Mark
A band running across the full width of the cloth due to difference in appearance from its adjacent surface. This is a general term covering a number of specific defects as follow: Starting Mark, Pick Bar, Tension Bar or Shiner, Weft Bar [3]. Set marks are defined as fabric faults which occur when a loom is started after a stoppage. The definition applies to a variety of faults of this kind. For example, a set mark is "an isolated narrow bar running parallel with the picks, starting abruptly and gradually shading away to normal fabric. This is due to an abrupt change in the pick spacing followed by a gradual return to normal pick spacing. Such a bar may occur on restarting weaving after:- i. Pick finding ii. Unweaving or pullback iii. Prolonged loom stoppage [4-9]. These bars may be also referred to as start-up marks, setting-on places, standing places or pullback places if the precise cause is known. [10] Start-up marks were first investigated by Greenwood and Cowhig (1956) who wrote a series of three papers. In the first paper, a theoretical analysis of the factors governing pick was carried out as a part of an investigation into the problem of start-up marks. They derived and analyzed mathematical relationships between beat-up forces, cloth fell position, take-up rate, and pick space. [11] This analysis was then extended to explain various causes of irregular pick spacing with reference to the effect of warp and fabric relaxation during loom stoppage. The effects of the free length of warp and fabric as well as that of type of let-off motion on the severity of marks were also examined. [12] The third paper, an experimental investigation reports that the loom and warp investigated, the effect of loom speed was so small that slight variations in it, either during running or after staring up, did not cause any appreciable irregularity in the pick spacing. It was also concluded that the main cause of start-up marks is the relaxation of warp and cloth. [13] According to Inui (1968,1969), deviation of warp tension during first picks (after restarting) from that in the steady running state is the most important cause of start-up marks. He also observed that the variation in warp tension was related to the inertia of the oscillating backrest [14]. 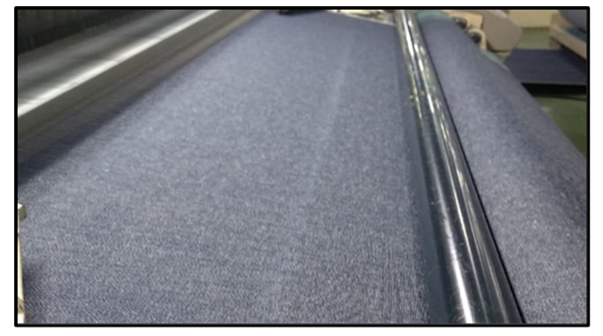 | Figure 2. Starting Mark (Thick or Dense mark) |
He reported that “thin” start-up marks (pick spaced less closely) are a result of lower warp tension and “thick” start –up marks (pick spaced more closely) are due to higher tension during restarting in comparison to steady running state tension. [15] Plate and Hepworth (1971, 1973) observed that the picks at cloth fell slip back when the reed recedes after beating up resulting non-uniform pick spacing at the cloth fell [16-17]. According to Ding Xin (1983), the backward movement of the picks at the cloth fell, may be due to both slipping and rolling back. Rolling back is easier than slipping back as it requires less energy. Energy stored in a twisted yarn could be released to promote rolling back. [18] Most of the work reviewed above dealt either with mathematical models, experimental models or laboratory experiments which were useful in explaining how start-up marks were created. In the experimental investigations, only shuttle looms were employed. In a paper, Wulfhorst and Obolenski (1990) report on an image processing technique which they used to study on start-up marks. They found, where the tendency towards formation increases with fabric tightness, other factors such as stoppage time, stop position, warp let–off control and backrest damping had insignificant effects on both the starting and the fabrics produced. However, some of their findings contradicted the results of previous research work and they also did not investigate the validity of various theories developed by previous researchers. [19] In recent years, new weaving machines with start-up prevention mechanisms had been introduced. Although the machines have equipped with electronics devices to prevent the formation of start-up marks by the machine manufactures. But the determination of proper machine setting before restarting remains problematic. (Industrie Textile, 1996) [20]. 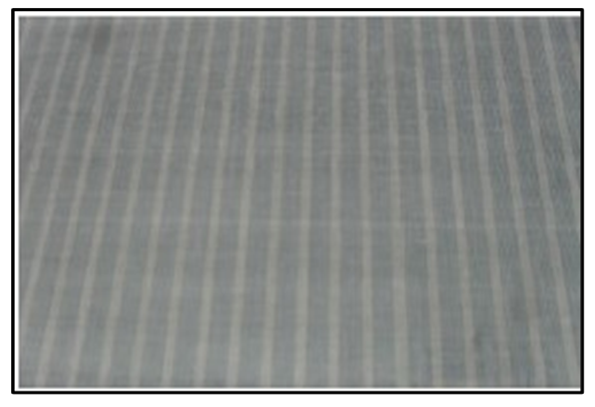 | Figure 3. Starting Mark (Thin or Open mark) |
3.1.1. Causes
Weft breaking causes a loom to stop, which requires turning it over to the shed entrance where the broken weft is located. During this turning over, the reed strikes the fabric, causing it to fall. The take up is higher than the let off, and occasionally the let off is greater than the take up, due to the reed's striking of the fell during this turning of the loom. This typically results from improper warp tension. When the machine stops, the tension on the warp yarn relaxes, which could lead to a disparity between take up and let off. Again, the flexibility of the yarn may alter if the machine is stopped repeatedly. Consequently, more yarn is obtained, and result starting mark is created. [21] Incorrect take-to-let-off ratio; occasionally, take is greater than let, and conversely, let is greater than take. This typically results from improper warp tension. When the machine stops, the tension on the warp yarn relaxes, which could lead to a disparity between take up and let off. Again, the flexibility of the yarn may alter if the machine is stopped repeatedly. More yarn is therefore gathered, and the result is the starting mark. Other thing is that machine stoppage for long time, back rest roller position, electrical setting, drop wire height and position, position of reed, pick spacing, beam collars cracked, broken, or bent.
3.1.2. Remedies
When a loom stops as a result of a weft break, the start mark preventer is adapted to be pre-set so that the fell can be moved forwardly of the reed beat-up position a pre-selected distance to meet the requirements of a particular type of fabric when the loom is turned over to the shed opening containing the broken pick. After removal of the broken pick of weft, the device is again actuated and the fell is caused to return to precise position whereat weaving can be resumed without creating a start mark in the fabric. [21] By making sure the take up to let off ratio is appropriate and by keeping the warp yarn under the proper tension, this may be made sure of. Not only that, but we also need to choose yarn of high quality and adequate elasticity. By minimizing the longer machine stoppage time. The position of the back rest roller should be chosen carefully in order to prevent any loom bars or starting marks. Tension on warp yarn should be maintained properly. It is possible to avoid using a loom bar or starting mark by setting the microcontroller appropriately. To prevent starting marks, drop wire height and position must be appropriately. By keeping the correct reed angle in both the starting and stopping positions. In order to prevent loom bars, fabric construction needs to be thoroughly analyzed and configured according to the loom settings. Proper pick space must be maintained. Beam collars need to be sufficiently tight, and cracked or fractured beams shouldn't be used.
3.2. Machine Parameters
3.2.1. Stoppage Time
Warp yarn tension is kept constant while the machine is working, but when it stops, the warp yarn becomes relaxed, allowing the constant warp yarn tension to fluctuate. Starting mark can appear like that. So stoppage time should be lower at every stop.
3.2.2. Back Rest Roller
Back rest roller height is one of the most important setting for loom bar or starting mark. Depending on the height of the back rest roller the angle of warp passage is changed, as a result tension of the warp is changed so loom bar or starting mark may come. But we cannot say that which height should be given. This may depends on fabric construction and other parameters. It is important to find out the exact height of the back rest roller to avoid starting mark or loom bar.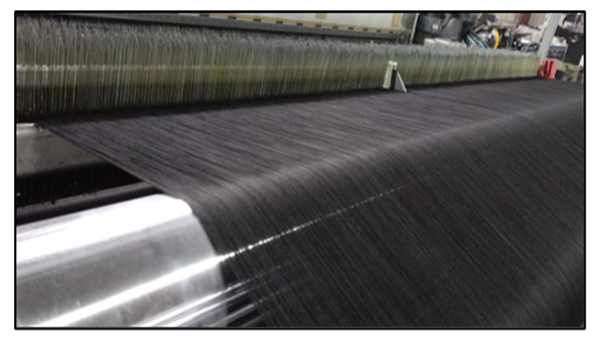 | Figure 4. Back Rest Roller |
3.2.3. Shed Depth
Starting marks may develop as a result of the warp yarn's tension being altered by adjusting the shed's depth. Smaller sheds are sometimes preferred for avoiding loom bars, whereas larger sheds with more depth are sometimes preferred for avoiding starting marks or loom bars. 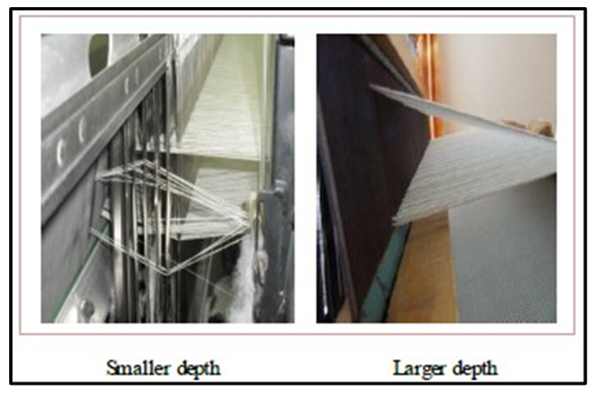 | Figure 5. Depth of Shed |
3.2.4. Electrical Settings
In electrical settings the change is done by microprocessor. There are two main settings named ASO, ASP. ASO stands for automatic start off set, it indicates how many time a reed will give a slow beat up before it gives its original beat up at full velocity. For example, if it is set that ASO is 1, that will indicate that the reed will give 2 slow beat up before it gives its original high speed beat up. This is usually done because when there is a ratio difference between take up and let off is occurred then these slow beat up will minimize the ratio difference between take up and let off. ASP stands for automatic start position, it indicates in which position reed will start to move after a stoppage. For example if it is set ASP is 45°, it will indicate that after the stoppage the reed will start to move at 45°. [22] 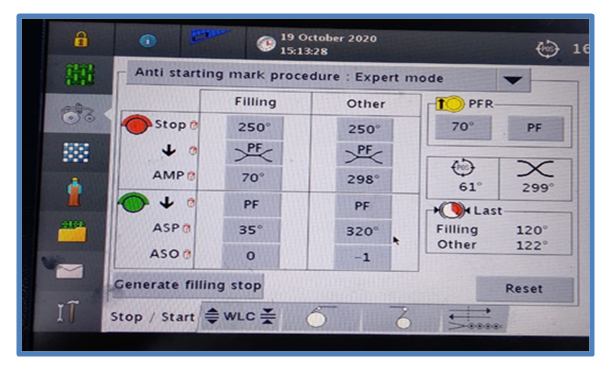 | Figure 6. Electrical Setting of Machine |
4. Experimental Data
4.1. Style: T2926
Table 1. Machine Parameter of T2926 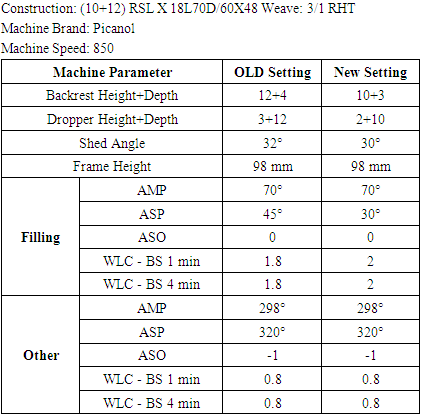 |
| |
|
Fabric Inspection: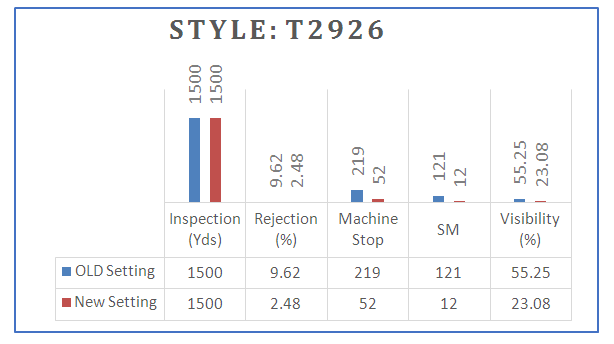 | Figure 7. Trial Outcome Report of T2926 |
4.2. Style: T2227
Table 2. Machine Parameter of T2227  |
| |
|
Fabric Inspection: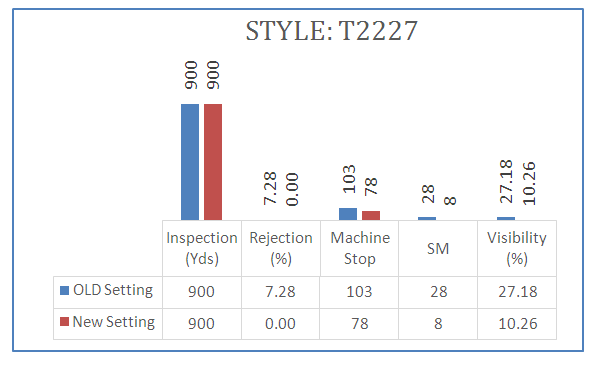 | Figure 8. Trial Outcome Report of T2227 |
4.3. Style: T1108
Table 3. Machine Parameter of T1108 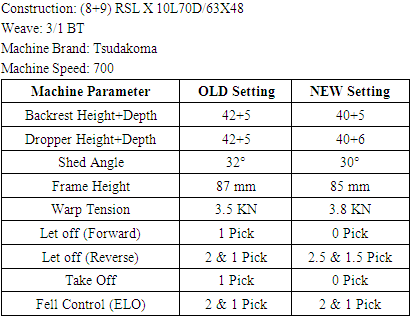 |
| |
|
Fabric Inspection: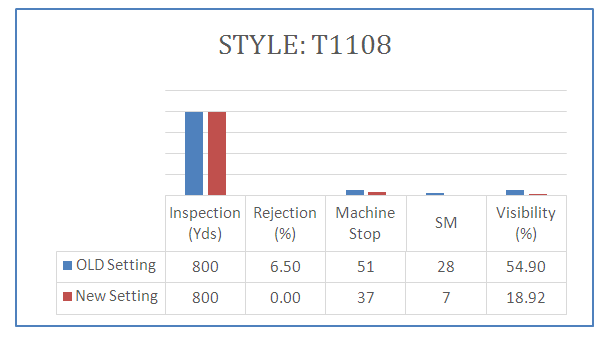 | Figure 9. Trial Outcome Report of T1108 |
4.4. Style: RE-64N
Table 4. Machine Parameter of RE-64N 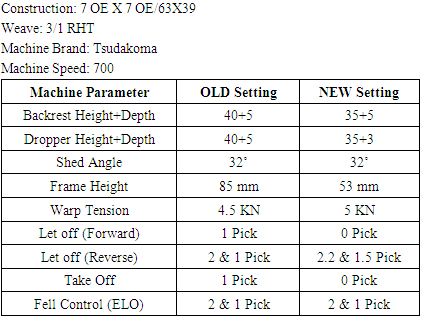 |
| |
|
Fabric Inspection: 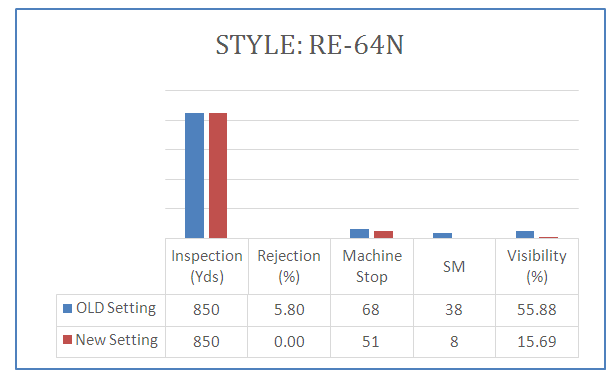 | Figure 10. Trial Outcome Report of RE-64N |
4.5. Style: Env-9026
Table 5. Machine Parameter of ENV-9026 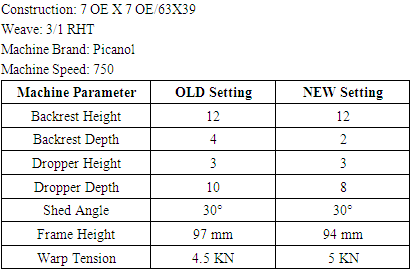 |
| |
|
Fabric Inspection: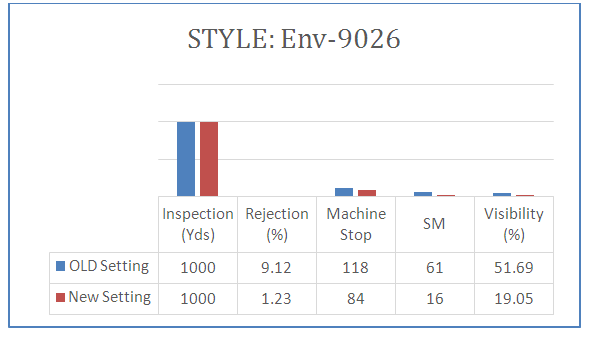 | Figure 11. Trial Outcome Report of ENV-9026 |
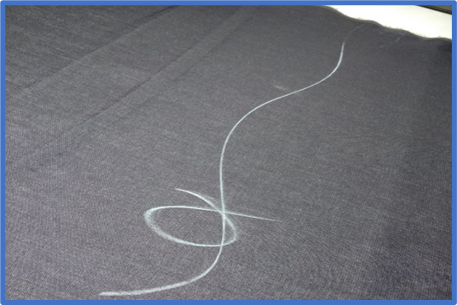 | Figure 12. Sample Fabric of ENV-9026 |
5. Summary
Table 6. Summary of Experiment Data 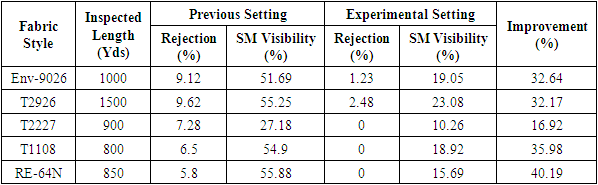 |
| |
|
6. Analysis & Findings
6.1. Analysis
a) In table-01, for this construction of fabric style T2926, we changed the mechanical setting as well as the electrical setting in the Picanol machine which is shown in the table. As we compare the fabric of the new setting with the old setting, we found in Fig 7 that starting mark (SM) quantity and visibility percentage is lower that’s why the rejection percentage also decreased. b) In table-02, for this fabric we emphasized on electrical setting rather mechanical setting. We also found in fabric inspection graph that the rejection percentage is zero and SM also lower.c) In table-03, this also performed in Tsudakoma loom and we saw that performance is same to previous construction. d) In table-04, this trial is performed in Tsudakoma machine which function is different than picanol. We need to change only mechanical setting because electrical setting of this loom is auto adjusted. So after completing this project we found a remarkable change in fabric which shown in Fig 10.e) In table-05, weight of this fabric is more than 15 oz that’s so we only applied the mechanical setting and after that we got our desired result.
6.2. Findings
a) We analyzed the above experimental data & graph and we found that Starting Mark visibility in the finished fabric decreased to 50% with compare to previous parameters. For that ultimate fabric rejection percentage due to SM was also reduced which is a great benefit to the company.b) Dense mark happened in heavy twill fabric whereas open mark found in light plain fabric.c) Due to the higher stoppage time, more thickness of open or dense marks though few inverse results were also obtained and for this explanation, further research is required.d) Mechanical settings affect the starting mark more than electrical settings.
7. Conclusions
During the weaving of the denim fabrics, major fabric defects like starting marks are generated because of improper machine settings. Difference in tension on the warp layers during shedding operation is mostly affected by the position of the backrest roll. From the above work done it has been concluded that loom settings has to be done appropriately to control the fabric defects like starting marks. Not every fabric construction calls for the same setup settings. The starting mark problem can be resolved by adjusting the back rest height, electrical settings, etc. So, before weaving, the proper configuration parameters for a given loom must be defined. Once a high-quality fabric has been created, it will be simple to apply the setting requirements to that construction and loom the following time. Therefore, it is necessary to write and use the parameters in order to address the starting mark defect.
References
[1] | Hasan Sheikh, Ibrahim Khalil, Saruar Hossain & S.M. Rafio Morshed, ‘’Reducing Defects in Denim Weaving by Applying Six Sigma Methodology: A Case Study’’ Global Journal of HUMAN-SOCIAL SCIENCE: H Economics Volume 19 Issue 1 Version 1.0 Year 2019. |
[2] | Denim: Manufacture, Finishing and Applications Edited by Roshan Paul. |
[3] | Dr. M.K. Talukdar, P.K. Sriramulu, D.B. Ajgaonker (1998),’’ Weaving Machines, Mechanism, Management”. P 511-512. |
[4] | Islam S (1998a), ‘Tomorrow’s Textiles’, Leeds, England, Second Edition, February 1998. |
[5] | Islam S (1998c), 'A Novel Technique for Measuring On-loom Warp and Fabric Creep' (In press, accepted on 26 September 1997, Publication Date February 1998). |
[6] | Islam S (1998d), 'Prevention of Set Marks in Weaving' (Submitted to the Journal of the Institution of Textile Engineers and Technologists, ITET on 7 January 1998). |
[7] | Islam S and Bandara M P U (1996a), 'Cloth Fell Control to Obviate Start-up Marks in Fabrics Woven on Power Looms'. University of Leeds Innovations Ltd. ULIS, British Patent Priority Application No. 9627143-2, 24 Dec. |
[8] | Islam S, and Bandara M P U (1996c), 'Aspects of Cloth Fell Control to Minimise Set Marks in Fabrics Woven on Power Looms'. Proceedings, 25th Textile Research Symposium, Mt. Fuji, Japan, 2-5 Aug. 247-254. |
[9] | Islam S and Bandara M P U (1996d), 'Yarn Spacing Measurement in Woven Fabrics with Specific Reference to Start-up Marks', J. Text. Inst., Vol. 87, No. 1, Part 1, 107-119. |
[10] | TextInst (1995) 'Textile Terms and Definitions', Textile Inststitute, Manchester, 10th Ed., 18. |
[11] | Greenwood K. and Cowhig W.T, 1956, The position of cloth fell in power looms-Part-1, Journal of the Textile Institute, T241-T254. |
[12] | Greenwood K. and Cowhig W.T, 1956, The position of cloth fell in power looms-Part-2, Journal of the Textile Institute, T255-T273. |
[13] | Greenwood K. and Cowhig W.T, 1956, The position of cloth fell in power looms-Part-3, Journal of the Textile Institute, T274-T285. |
[14] | Inui N. 1968, Thick and thin places in fabrics during weaving, Journal of the Textile Machinery Society, Japan, P. 143-152. |
[15] | Inui N.1969, Thick and thin places in fabrics during weaving- Part-2, Journal of the Textile Machinery Society, Japan, 85-87. |
[16] | Plate D.E.A. and Hepworth K, 1971, Beat-up forces in weaving - part1, Journal of the Textile Institute, 505-531. |
[17] | Plate D.E.A. and Hepworth K, 1973, Beat-up forces in weaving – part 2, Journal of the Textile Institute, 233-249. |
[18] | Ding Xin, 1983, Movement of the pick at cloth fell, Journal of China Textile University, 3, 32-41. |
[19] | Wulfhorst B., Obolenski B., 1990, Assessment of measures for preventing starting marks in woven fabrics, Melliand Textilberichte, E11-E15. |
[20] | Avoiding Start-up Marks, Industrie Textile, 1996, 27-30. |
[21] | Ralph H. Brown 1979, Start Mark Preventer for Looms, United States Patents. |
[22] | Picanol (1993); Technical Publication, Picanol, Belgium, c.1993. |