Fahmida Faiza Fahmi, Sanjida Sultana, Nadvi Mamun Pritha, Mahfuza Pervin
Department of Textile Engineering, Primeasia University, Dhaka, Bangladesh
Correspondence to: Fahmida Faiza Fahmi, Department of Textile Engineering, Primeasia University, Dhaka, Bangladesh.
Email: |  |
Copyright © 2022 The Author(s). Published by Scientific & Academic Publishing.
This work is licensed under the Creative Commons Attribution International License (CC BY).
http://creativecommons.org/licenses/by/4.0/

Abstract
Maintenance of adequate fabric width is a mandatory factor of consideration during the weaving process. The weaving process can be cost-effective if the fabric's predetermined width can obtain by using a sufficient amount of yarn. Assurance of fabric production with a predetermined amount of raw material and beneficiary functional properties can make the weaving process effective. Weaving is the process of cloth making with the mechanism of yarns interlacement which occurs in looms. Weaving speed and warp beam tension variation can directly impact the fabric width. The width of newly weaved fabric can vary significantly with the diversity in weaving speed. Increasing warp yarn tension will reduce the bending property and make the yarns straighter. As a result, the interlacement property becomes interrupted, and the EPI of the fabric will increase slightly. In this scenario, more warp yarns are necessary to construct a fabric with a predetermined width. Some physical properties of fabric also vary by considering these factors. The comfortability of fabric can diversify widely with changing warp beam tension and weaving speed. At higher loom speed, the interlacement nature of the fabric changes and the moisture absorption will also deviate. This property directly impacts the comfortability of the fabric. So assessing the level of diversity in fabric properties is an essential factor of consideration to obtain the required performance. This assessment evaluates the physical properties of the 1/1 rib-stop plain fabric sample according to the diversification of weaving speed and warp beam tension. In this assessment, the variation of some fabric properties will measure by changing the weaving principles in four samples of similar construction. Calculating various measurements like warp contraction%, crimp%, cover factor, and GSM will assess the deviation of results. The crimp% impacts the comfort performance, whereas the cover factor analyses the cost-effectiveness by detecting the requirement of yarns to produce a fabric. GSM of fabric deals with the weight of fabric samples, and warp contraction% determines the most suitable condition to perform the weaving procedure. This analysis will help the technical professionals set the standard weaving process to obtain their mandated width and physical properties cost-effectively.
Keywords:
Weaving Speed, Rib-stop, Warp tension, Crimp%, Cover factor, GSM
Cite this paper: Fahmida Faiza Fahmi, Sanjida Sultana, Nadvi Mamun Pritha, Mahfuza Pervin, Assessment of the Impact of Weaving Speed and Warp Beam Tension on the Physical Properties of 1/1 Rib-Stop Plain Fabric, International Journal of Textile Science, Vol. 11 No. 1, 2022, pp. 6-11. doi: 10.5923/j.textile.20221101.02.
1. Introduction
One of the principal parameters to evaluate fabric performance is the assessment of its physical properties [1]. The value of various properties in a fabric sample shows an impact on the requirement of raw material for construction, comfortability, the width of the fabric sample, cost-effectiveness and many other factors. Several factors impact fabric properties in various stages of fabric production, including the conditioning of raw materials, construction, and processing after the fabric construction. Woven fabrics carry a significant portion of fabric manufacturing. Diversification in fabric construction during weaving makes this area more versatile. Rib-stop plain fabric is a derivative of plain construction in woven fabric design. The significant potency of this construction is its satisfactory reinforcement property. Rib-stop plain fabric construction has reinforcing yarns with the general structure of plain fabric at a regular interval in crosshatch designing. The weaving mechanism shows a significant impact on fabric properties [2]. The assurance of fabric width is the most considerable impact of proper weaving speed and warp beam tension during the fabric construction. The diversity in weaving speed and beam tension changes some essential properties of a fabric sample, directly impacting the fabric width. Fabric width is a vital factor for ensuring the cost-effectiveness of a cloth. The raw material cost will increase if more yarns are necessary to achieve an actual fabric width. That directly impacts the cost-effectiveness of the sample preparation process. Warp contraction% and crimp% are the properties which directly affect the fabric width. These properties show variation with the change of weaving speed and warp beam tension. Diversified weaving speed impacts the warp contraction%. The average difference between the length of the warp yarn and the length of the fabric produced from a similar beam of warp yarn is known as warp contraction% [3]. Warp contraction% variation is responsible for weaved fabric length variation. The warp contraction% property restricts the waviness of yarns by which the proper interlacement property affects significantly [4]. Due to interlacement in several points at a specific interval, the original length of a single yarn will reduce after weaving into cloth. Fabric crimp% denotes that particular property of a sample. Measurement procedure of crimp% states the differences between the original lengths of yarn with the length of yarn after weaving compared to the initial length of the yarn. It is expressed in percentage value [5]. When the crimp% decreases, yarns will become straighter, and the requirement of total yarn to weave a definite length of the cloth increases its value. Therefore, the necessity of yarns is more to weave a fabric than the fabric construction with a smaller crimp% value. Increasing warp tension lessens the crimp% of warp yarns because of the reduction in bending properties of yarns due to elevated yarn tension [6]. Crimp% also impacts the GSM and cover factor of a fabric identically.Another important consideration of clothing is its comfortability. Various factors have an impact on the comfortability of fabric. The cover factor and the GSM value of fabric samples are among them. These two properties directly affect the considerable parameters of the weaving process. The crimp% of the fabric sample directly impacts the fabric cover factor proportionally. The total area of fabric wrapped with a single set of yarn in a particular direction is known as the cover factor [7]. The variation in warp tension during weaving is responsible for the cover factor's diversity. The cover factor value indicates the comfort properties of a fabric sample. It is inversely proportionate to the value of porosity and permeability of fabric, which are noteworthy detectors of fabric comfortability. The tension of warp yarns during the weaving process greatly impacts the fabric cover factor. Cover factor affects the fabric's stitch density, directly affecting the permeability property [8]. A higher amount of air permeability is an indicator of greater fabric comfort and vice-versa. Lightweight clothing is another parameter for measuring the comfortability of a fabric sample. GSM is the property of assessing the weight of fabric samples. The weight per unit length can count as the GSM value of a fabric. It is another considerable property that varies with weaving speed and warp tension. The increase in warp yarn tension minimizes the crimp% in warp yarns, which impacts the GSM value of the fabric [9]. Therefore the cover factor also has a direct effect on fabric GSM. A higher GSM value indicates more weight which decreases the comfortability of clothing.Ensuring a good condition during the weaving procedure is crucial to achieving the desired output. In the weaving process, weaving speed and warp beam tension are the factors which directly impact the fabric properties. So controlling and maintaining these properties during weaving is essential to get a better result. Changes in weaving speed and warp beam tension affect the fabric's physical parameters, from cost-effectiveness to comfortability [10]. So, determination, control and maintenance of proper weaving speed and warp beam tension are mandatory.This assessment measures some significant properties of fabric concerning the change in weaving speed (RPM) and warp beam tension. Parameters are changed manually by using an automated sample preparation weaving loom to determine its impact on the properties of woven fabric. During the assessment, the physical properties of four samples evaluate according to the variation in machine speed and warp beam tension. Warp contraction%, the cover factor of the fabric, crimp%, and GSM of the fabric samples are the selected measurements for consideration. This investigation will determine the degree of variation in fabric properties with changing weaving conditions and assure the preferable property of the fabric sample by implementing the same situation during weaving in the bulk production stage. After completing the analysis, the experts and professionals can gain a clear conception of the impact of weaving parameters on fabric properties, which will facilitate them in detecting and implementing the desired condition of the weaving process (machine RPM and warp beam tension) while preparing a sample fabric with specific requirements and physical properties.
2. Material & Method
2.1. Description of Fabric Samples
The raw material used for the assessment was woven samples of 1/1 rib-stop cotton plain fabric. The construction of 1/1 rib-stop plain fabric is represented in figure 1.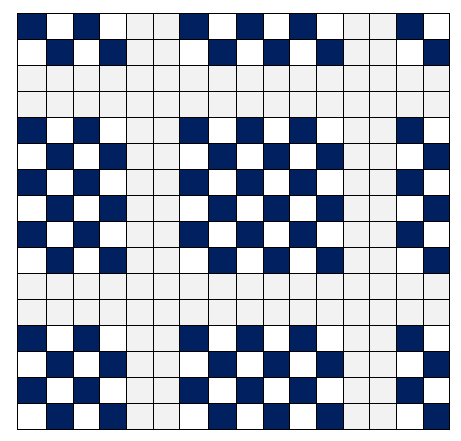 | Figure 1. 1/1 rib-stop plain fabric construction |
Four (04) rib-stop plain samples were made with 100% cotton to execute the analysis. The count of the yarns was 16 Ne in both warp and weft directions. Slight incrementation was found on warp count due to sizing. CCI evergreen sample preparation loom conducted the weaving process. Single-side rapier design mechanism was the weft insertion process in this automated loom. Controlling the weaving principles like the weaving speed and warp beam tension could be done manually. Some considerable weaving properties (weaving speed and warp beam tension) varied in every sample. In the samples, loom RPM was 413, 413, 470, and 518 when ware beam tension was consecutively 200 N, 250 N, 350 N, and 300 N. Measurement of properties in four different samples with diversified weaving conditions executed the assessment correctively. For facilitation in further discussion, fabric samples were marked A, B, C, and D according to the denotation in table 1:Table 1. Marking of the samples 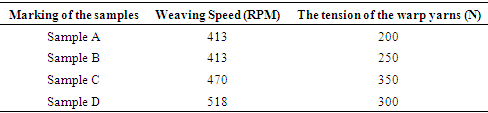 |
| |
|
2.2. Variation in Warp Contraction%
Warp contraction value of fabric had a multifarious impact on weaving speed. The warp contraction value of a sample was expressed in percentage (%). The warp contraction% could assess by using the mentioned equation 1. | (1) |
2.3. Crimp%
Crimp% of a fabric sample was measured by following the standard method ISO 7211-3:1984. Conditioning of the sample fabrics made the process accurate. The standard atmosphere (20°C ± 2°C temperature and 65% RH) should be maintained to ensure proper conditioning of the samples. AccuCrimp tester was the instrument to accomplish the evaluation. The measurement requires collecting yarns from the warp and weft direction from the samples prepared with diversified weaving speed and beam tension. Then the taken yarns were analyzed in the crimp tester to provide adequate tension on the yarns. Finally, the crimp% of the fabric was calculated by assessing the samples by using the below-mentioned equation 2. | (2) |
2.4. The Cover Factor of Fabric
The evaluation process measured the value of the cover factor for four samples in diversified RPM and warp beam tension. Initially, the samples should be conditioned in the standard atmosphere (20°± 2°C temperature and 65% RH). The cover factor of woven fabric should be calculated separately for both sets of yarns (i.e., weft and warp). Then the summation of the resulted value for both warp and weft yarns cover factor denoted the value of the total cover factor of the fabric sample. Equation (3) discussed the mathematical formula for determining the value of the cover factor.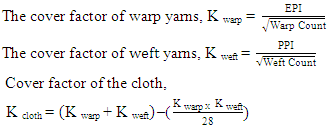 | (3) |
2.5. GSM of the Fabric
The GSM calculation concept measured fabric weight (in grams) per square meter area. The samples' weight was calculated using a GSM cutter consisting of a round GSM cutter and GSM pad. The area of the GSM cutter measured 1/100 m2. Five measurements from each fabric sample were taken to calculate the fabric weight with an electric balance. The average sample weight value was multiplied by 100 to convert the unit into a square meter (m2). The samples should be conditioned in a standard atmosphere to acquire accurate measurements of GSM. Equation 4 denoted the formula for calculating the GSM value of the fabric samples.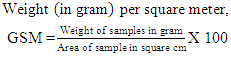 | (4) |
3. Result & Discussion
3.1. Variation in Warp Contraction Percentage
The effect of various weaving speeds and warp beam tension in warp contraction% of fabric samples was shown in Figure 2. 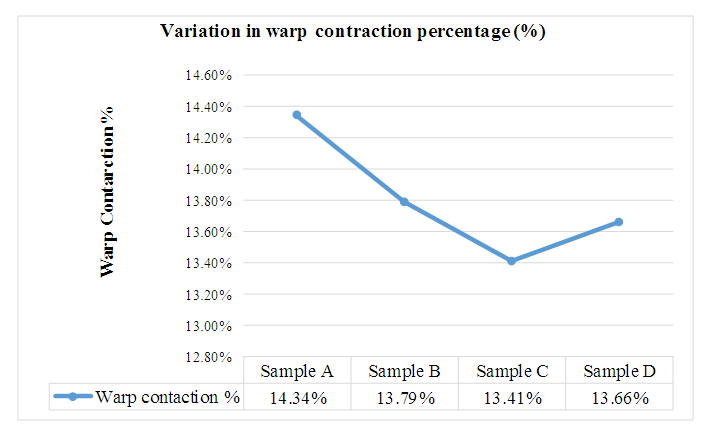 | Figure 2. Variation in warp contraction percentage |
Weaving speed (RPM) and warp yarn tension significantly impacted the warp contraction% in a fabric sample. The calculated warp contraction% value was increased with the increment of weaving speed in the samples. The increased tension reduced the waviness effect of warp yarns around the weft yeans and made the warp contraction% effect more prominent. The CCI weaving loom manually controlled the weaving speed and warp tension in the experimental assessment. The machine RPM was similar in sample A and sample B (413 RPM), but the warp beam tension was higher in sample B (warp beam tension for samples A and B were consecutively 200 N and 250 N). Despite the same RPM, the resulting warp contraction% value was higher in sample A than in sample B due to an increment in warp yarn tension. Warp contraction% value continued its reducing tendency in sample C, where the weaving speed and warp yarn tension increased (weaving speed 470 RPM and warp tension 350 N). In sample D, the loom speed was at peak value (518 RPM), but warp tension was reduced slightly (300 N), so the contraction value was also increased scarcely. So, from sample A to sample C, the warp contraction value reduced from 14.34% to 13.41%, and in sample D, after decreasing the warp yarn tension, the warp contraction value increased slightly (13.66%). The maximum warp contraction value was 14.34% during the experimental procedure, representing sample A.
3.2. Diversity in Crimp% of Weft and Warp
During the experimental procedure, the warp yarn tension was significantly higher. Due to high warp tension, the difference of the crimp% between the warp and weft yarns was prominent.
3.2.1. Crimp% of Weft Yarns
Incremented tension in the warp direction increased the bending requirement of weft yarns. Due to higher tension, warp yarns became straighter. As a result, the weft yarn had to bend more to ensure adequate interlacement. Figure 3 expressed the diversity of crimp% in the weft direction. 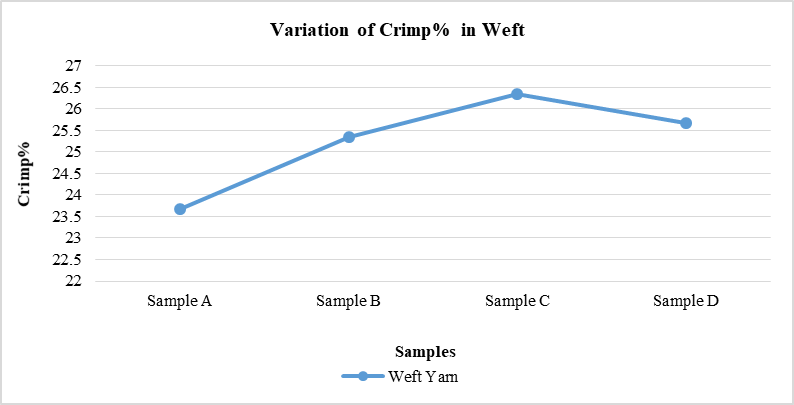 | Figure 3. Variation of crimp% in weft direction with diversified warp yarn tension |
It could state that the crimp% of weft warn was increasing proportionally with the increment of warp yarn tension. Sample C contained the maximum value of crimp%, where the tension of warp yarns was maximum (350 N). In the weft direction, sample A had the minimum value of crimp%, where the amount of tension applied in warp yarns was the lowest (200 N).
3.2.2. Crimp% of Warp Yarns
Figure 4 represented the variation of crimp% value for warp yarns.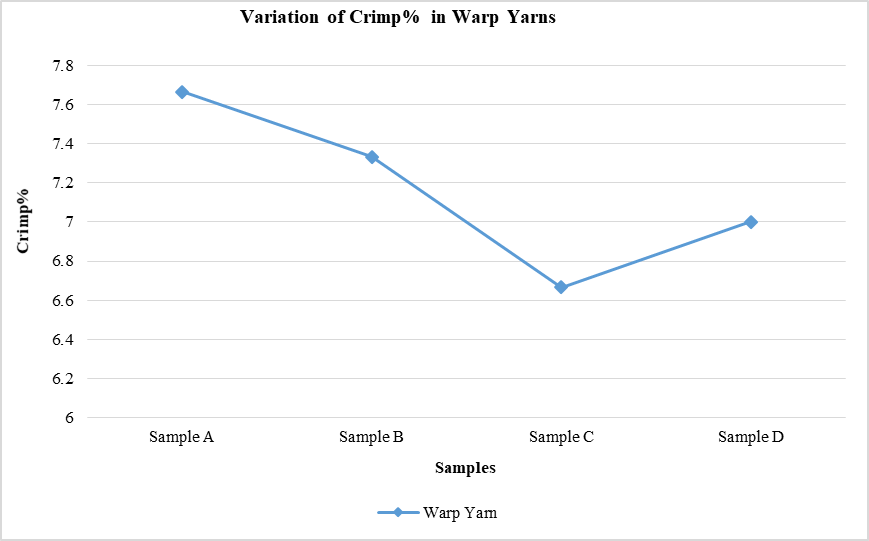 | Figure 4. Variation of crimp% in warp direction with diversified warp yarn tension |
Warp yarns lost their crimp due to high tension. When more tension was applied, the warp yarns tended to become straighter and lost the crimp of yarn. During the assessment, the crimp% of warp yarns was reduced with increasing tension. Sample A delivered the peak value of warp crimp% due to the least amount of yarn tension (200 N), whereas sample C showed the least amount of crimp% in warp yarns with an increment of warp yarn tension (350 N).Among all four samples, the variation of warp and weft crimp% were higher in samples A and C. In sample A the crimp% of warp yarns was maximum with lower warp tension, so the weft yarns required to bend least by comparing all other samples. Nevertheless, sample C showed the reverse characteristics where the yarns became straighter due to the least amount of warp crimp%. As a result, the weft yarns need to bend more, which denoted higher crimp%.
3.3. Cover Factor
Increasing warp beam tension made the warp yarns straighter, and the weft yarns needed more interlacement and bending to prepare the fabric sample. Due to the loss of bending property of warp yarns in higher tension, the value of EPI could increase minimally. As a result, more warp yarns need to be used to complete the predetermined width of the samples. For the higher crimp% in weft yarns, the stitch density of the fabric became affected. The porosity of the fabric was minimized, which as a result, created a higher value of cover factor in fabric samples. Figure 5 illustrated the effect of cover factor variation of fabric samples by considering the diversity in warp tension and machine speed.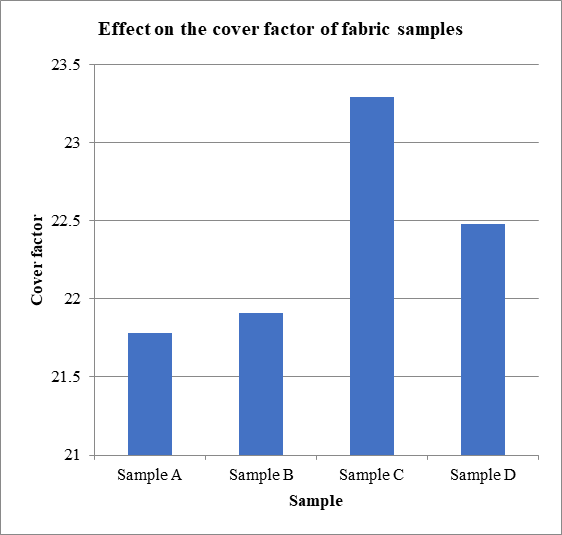 | Figure 5. Effect on cover factor of the fabric samples |
In sample A, the tension of warp yarns was minimum (200 N) compared to the rest of the three samples. So the bending property of warp yarns was better, and the crimp% was more. The EPI value of warp direction was not increased much for this sample. The value of stitch density and crimp% of weft yarn was lower. For that reason, the porosity was higher than in other samples, directly reducing the cover factor's value for the mentioned sample. So the cover factor of sample A was least (21.78) compared to others. Similarly, for sample C, the warp yarn tension was maximum (350 N), and the crimp% of warp yarns was at its minimum value. So the bending property of weft yarns of that sample was increased, which created more interlacement and less porosity in the fabric. Sample C had the maximum (23.29) value of cover factor during the experimental procedure due to higher warp yarn tension. In sample D, the experimented value of cover factor was lower than sample C due to lower tension in warp yarn despite containing more loom speed while weaving the fabric.
3.4. Variation in GSM
Figure 6 illustrated the diversity in GSM between the fabric samples below: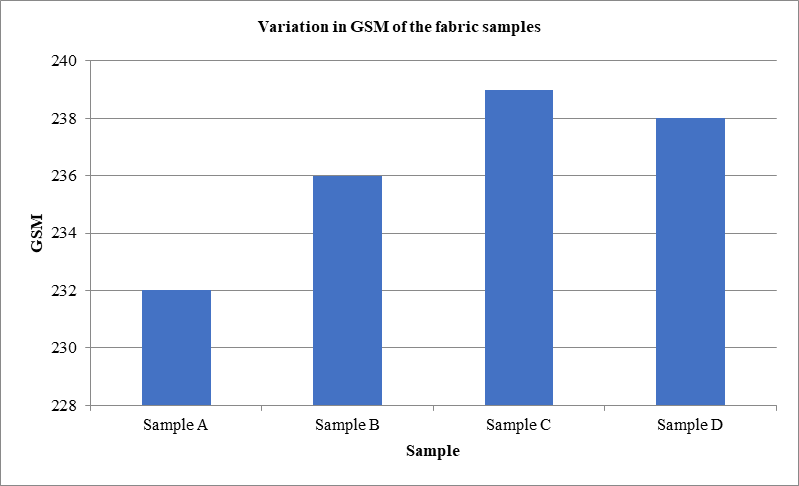 | Figure 6. Variation in GSM of fabric samples during the experimental evaluation |
The diversity in fabric weight depended on stitch density, porosity, yarn count, EPI, PPI and many other factors. As explained earlier, due to higher warp yarn tension, the porosity of the samples was decreased, and the crimp% of weft yarns increased. As a result, the weight of the fabric sample would elevate slightly at a higher value of warp yarn tension. The process was carried out inversely for lower warp yarn tension. According to figure 6, the value of GSM was higher (239 g/m2) in sample C, where the tension of the warp yarns was also high (350 N), and similarly, the GSM of sample A was lower due to the decreasing amount of warp yarn tension (200 N) on that sample.
4. Conclusions
Diversification of the physical properties of 1/1 rib-stop plain fabric is assessed in this experimental analysis by considering the variability of weaving loom speed and warp yarn tension. The evaluation concludes with the statements below:a) The value of warp contraction% shows a reducing tendency with the increment of weaving loom speed. The higher the loom speed, the warp contraction% will be relatively lower.b) The tension of warp yarns significantly impacts the crimp% of fabric. The crimp% value of weft yarns will increase with the maximization of warp beam tension, while the warp yarns show the opposite nature of performance.c) The cover factor is another vital property of a fabric sample which varies with yarn tension. Increasing warp yarn tension reduces the fabric's porosity, creates a more robust structure, and increases the fabric cover factor value.d) The weaving speed and tension variation can also impact the overall fabric weight. Due to the higher value of the cover factor, the GSM of a fabric sample will be higher with the increment of warp beam tension and shows a reversible impact when the tension is reduced. Ensuring the preferable physical property is essential to obtaining good performance from the clothing. By evaluating the impact of changing the physical property of the samples at different machine speeds and tension required, this analysis will help the professionals to identify the preferable weaving condition while weaving a cloth according to the required performance standards.
ACKNOWLEDGEMENTS
This project would not have been possible without the cooperation of the persons involved with the CCI sample-making lab of Bangladesh University of Textiles (BUTEX) and the testing laboratory of Primeasia University. The authors are highly grateful to all of them for their cordial support and assistance.
References
[1] | M. Mebrate, N. Gessesse, and N. Zinabu, "Effect of Loom Tension on Mechanical Properties of Plain Woven Cotton Fabric," Journal of Natural Fibers, vol. 19, pp. 1443-1448, 2020. |
[2] | S. J. Kim and H. A. Kim, "Effect of fabric structural parameters and weaving conditions to warp tension of aramid fabrics for protective garments," Textile Research Journal, vol. 88, pp. 987-1001, 2017. |
[3] | S. S. Yukhin and Y. A. Yukhina, "A Theoretical Consideration of the Warp and Weft Contractions in Woven Fabrics," Journal of the Textile Institute, vol. 87, pp. 532-541, 1996. |
[4] | S. S. Gulhane, "Effect of Loom Speed on Warp Contraction Percentage of Cotton Fabric," Trends in Textile Engineering & Fashion Technology, vol. 3, 2018. |
[5] | M. Maqsood, T. Hussain, Y. Nawab, K. Shaker, and M. Umair, "Prediction of warp and weft yarn crimp in cotton woven fabrics," The Journal of The Textile Institute, vol. 106, pp. 1180-1189, 2014. |
[6] | A. S. Farhana Afroz, "EFFECT OF WARP YARN TENSION ON CRIMP% IN WOVEN FABRIC," European Scientific Journal, vol. 10, 2014. |
[7] | M. Tàpias, M. Ralló, J. Escofet, I. Algaba, and A. Riva, "Objective Measure of Woven Fabric's Cover Factor by Image Processing," Textile Research Journal, vol. 80, pp. 35-44, 2009. |
[8] | M. E. Zuhaib Ahmad, Shoaib Iqbal, ADNAN AHMED MAZARI, "Effect of yarn structure on cover factor in woven fabrics," industria textila, vol. 69, pp. 197-201, January 2018. |
[9] | W. MENGIE, "THE EFFECT OF WEFT YARN TWIST LOSS AND WEFT TENSION ON FABRIC PROPERTIES PRODUCED BY AIR JET LOOM," Ethiopian Institute of Textile and Fashion Technology, Bahir Dar University, 2017. |
[10] | M. M. Haque, "EFFECT OF WEFT PARAMETERS ON WEAVING PERFORMANCE AND FABRIC PROPERTIES," Daffodil International University Journal of Science and Technology, vol. 4, July 2009. |