Sanjida Sultana, Fahmida Faiza Fahmi, Afsana Ferdous, Mahfuza Pervin, Tanzima Zoha Chowdhury, Mayesha Maliha
Textile Engineering, Primeasia University, Dhaka, Bangladesh
Correspondence to: Sanjida Sultana, Textile Engineering, Primeasia University, Dhaka, Bangladesh.
Email: |  |
Copyright © 2022 The Author(s). Published by Scientific & Academic Publishing.
This work is licensed under the Creative Commons Attribution International License (CC BY).
http://creativecommons.org/licenses/by/4.0/

Abstract
Coir fibre obtained from the husk of the coconut is a natural fibre. It is a cellulosic fibre. Coconut is available in tropical regions. Depending on the age of the coconut, this fibre is divided into two categories. One of them is Brown fibre which is obtained from matured coconut and another one is White fibre which is obtained from immature coconut. In this paper the manufacturing process, structure, cross-sectional diagram, their properties and uses were reviewed. It is very important that now a day, besides many other uses, coir fibre has very important use in reinforcement in different sections in different ways.
Keywords:
Coir fibre, Brown fibre, White fibre
Cite this paper: Sanjida Sultana, Fahmida Faiza Fahmi, Afsana Ferdous, Mahfuza Pervin, Tanzima Zoha Chowdhury, Mayesha Maliha, Coir Fibre – A Cellulosic Fibre, International Journal of Textile Science, Vol. 11 No. 1, 2022, pp. 1-5. doi: 10.5923/j.textile.20221101.01.
1. Introduction
Coconut fibre is also known as Coir fibre. It is a natural cellulosic fibre [1]. It is found in the outer husk of the coconut. Coconut is available in tropical regions. According to the official website of International Year for Natural fibres 2009, approximately 500 000 tons of coconut fibres are produced annually worldwide, mainly in India and Sri Lanka [2]. Its total value is estimated at $100 million [2]. India and Sri Lanka are also the leading Exporters, followed by Thailand, Vietnam, the Philippines and Indonesia [2]. Depending on the age, coconut fibre is divided into two categories. One of them is Brown fibre which is extracted from matured coconuts and another one is White fibre which is extracted from immature coconuts. Brown fibres are thick, strong and have high abrasion resistance [2]. On the other hand, white fibres are smoother and finer but also weaker [2]. There is another type of fibre which is commercially available named as decorticated fibre and this is a mixed fibre.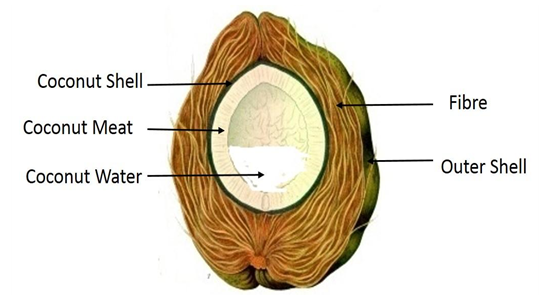 | Figure 1. Structure of coconut |
Coconut has an outer shell, coconut shell, coconut meat, and coconut water. Fibre is collected from the husk (between coconut shell and outer shell or skin). The common name of the plant is Coir; the Scientific name is Cocos Nucifera and Arecaceae. Some advantages of this fibre are handles high water velocities, UV resistant synthetics, high tensile strength, biodegradable after 4-10 years, Water absorbent, flexible - easy to handle and traps sediment-builds deposition, etc.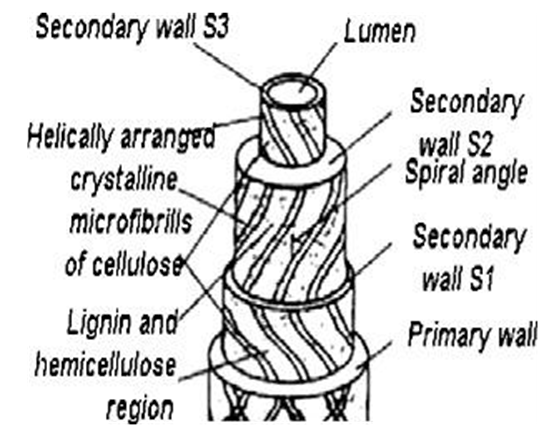 | Figure 2. Cross sectional view of coir fibre [4] |
2. Materials & Methods
Some papers were collected and reviewed. Based on their information manufacturing process, structure, properties and uses were studied.
2.1. Manufacturing Process
2.1.1. Harvesting and Husking
Coconut is harvested from the tree or from the ground if it is fallen from the tree. People can collect coconuts manually and those who collect coconuts are called climbers. They can collect by hand at about 25 feet high. If the height is more than 25 feet, they use a bamboo pole with a knife attached at the top. Unripe coconut husking is done after seasoning for a month by spreading them in a single layer on the ground to keep them dry. Ripe coconuts are husked as early as possible after collection.
2.1.2. Retting
Then retting process is performed. In this process, husks are kept in an environment that encourages the action of naturally occurring microbes. This process decomposes the husk’s pulp and separates the coir fibre from residue named pith. Fresh water is used for retting ripe coconut husks and salt water is used for retting green husks. For freshwater retting, ripe husks are buried in pits dug along riverbanks, immersed in water-filled concrete tanks, or suspended by nets in a river and weighted to keep them submerged. The husks typically soak for at least six months [2]. For saltwater retting, green husks are soaked in seawater or artificially salinated fresh water [2]. Often this is accomplished by placing them in pits along riverbanks near the ocean where tidal action alternately covers them with seawater and rinses them with river water [2]. Saltwater retting usually takes eight to 10 months, although adding the proper bacteria to the water can shorten the retting period to a few days. Mechanical techniques have recently been developed to hasten or eliminate retting. Ripe husks can be processed in crushing machines after being retted for only seven to 10 days. Immature husks can be dry milled without any retting [2]. After passing through the crushing machine, these green husks need only be dampened with water or soaked one to two days before proceeding to the defibering step. Dry milling produces only mattress fibre [2]. 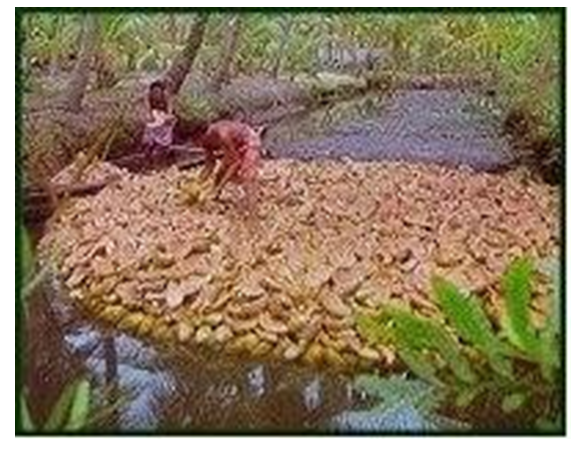 | Figure 3. Retting of coir fibre |
2.1.3. Defibering and Finishing
Depending on the types of fibres and end use, defibering and finishing process is done in different ways.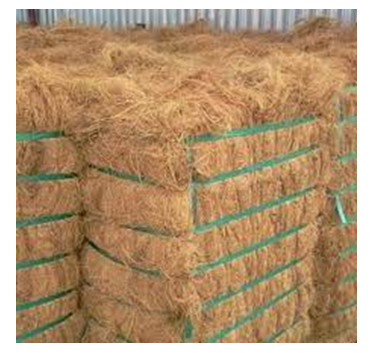 | Figure 4. Coir fibre bale |
• Fibres are separated from the pith and the outer skin by hand with a wooden mallet or in a machine consisting of a rotating drum fitted with steel spikes. In this process, Bristle fibres are separated. The fibres which will not be further processed are rolled and tied into loose bundles for storage. For upholstery padding, bristle fibre is loosely spun into yarn and allowed to rest. Then the curly fibres are separated. • Mattress fibres are separated from the pith by washing the residue from the defibering process and combing through it by hand or tumbling it in a perforated drum or sieve. Then the fibres are baled with a hydraulic press. If more processing is needed, the fibres are combed with mechanical or manual carding tools, then loosely twisted into a thick yarn and wound into bundles [2]. Later, the wick can be re-spun into a finer yarn where spinning can be done by hand spinning which is a hand-operated spinning wheel or by a fully automated spinning machine.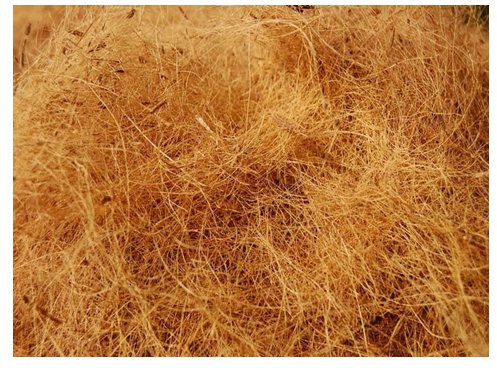 | Figure 5. Coir fibre |
2.2. Chemical Composition of Coir Fibre
It is seen that the lignin content of coir fibre is high and cellulose content is low. Hemicellulose is also present in this fibre. The chemical composition of coir fibre is as follows [2]:Table 1. Chemical composition of coir fibre 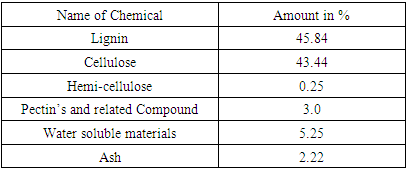 |
| |
|
2.3. Thermal Properties
The thermal stability of alkali (NaOH) treated coir fibre increases with the increase in activation energy and is highest for 5-15% alkali concentration [5].
2.4. Flammability
It easily burns and causes fire upon ignition.
2.5. Effect of H2O2
For removal of waxy and fatty acid residues, treatment with H2O2 shows the most efficiency [6]. In case of green coconut fibres treatment with H2O2 promoted an increase in thermal stability [6].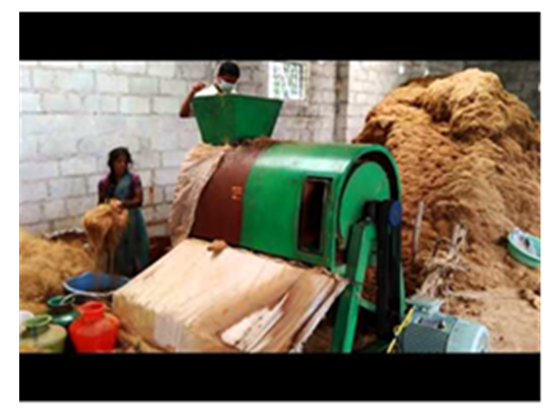 | Figure 6. Defibering process in machine |
2.6. Physical Properties of Coir Fibre
The physical properties of coir fibre are given below [2]:Table 2. Physical properties of coir fibre 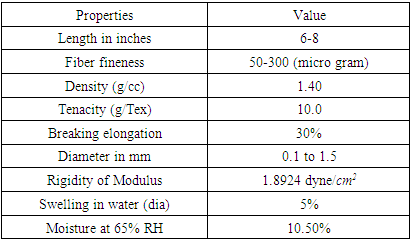 |
| |
|
2.7. End Uses of Coir Fibre
1. Brown coir is used in the preparation of carpets, formation of door mates and manufacturing of mattresses.2. It has also use in automobiles.3. Coir Fiber is environmentally friendly and its liners are used for indoor gardening. These products offer outstanding drainage and aeration to roots and prevent the plant from root rot.4. It is also used in making sofas.5. Coir fibre bricks are used for many purposes.6. White coir fibre is used in the manufacture of rope. 7. It is used in geo-textile [7]. Coir meshes are durable, absorb water, resist sunlight, facilitate seed germination and are 100% biodegradable.8. Coir fibre is also used for soil treatment and a hydroponic growth medium.9. For producing home decoration products, coir fibres are used.10. Coir fibre is also used in making toys. 11. Different types of brushes can be produced from coir fibre.12. Cosmetics can also be made from coir fibre. 13. Coir fibre is used in reinforced polymer composites [8] such as coir-polypropylene, coir-epoxy, coir-polylactic, etc.14. The coir-epoxy reinforced polymer can be used in ballistic applications [9].15. Tannin–phenolic polymers reinforced with coir fibers can be used in automotive vehicles [10].16. Surface-modified coir fibres can be used as cement composite reinforcement [11].17. This fibre can be used in soil erosion control and road embankments. 18. This fibre can be used in roof greening.19. It has also use in Indoor and Out Door Horticultural Décor.20. It can be used in bioengineering.21. Coir bio fibres are used as a soil conditioner.22. It can be used in Re-sedimentation projects.23. It has use in silt fencing.24. Coir fibre dust can be used as moisture-retaining agent in potting mixtures for horticultural and agricultural applications and also used for producing domestic or industrial fuel, producing hard boards, thermal insulators and hydroseeding.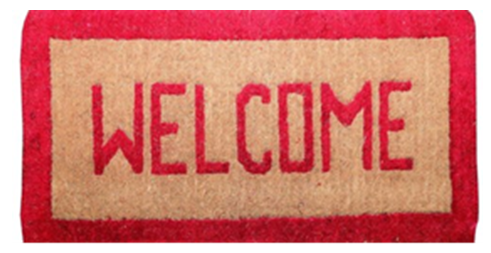 | Figure 7. Floor Mat of coir fibre |
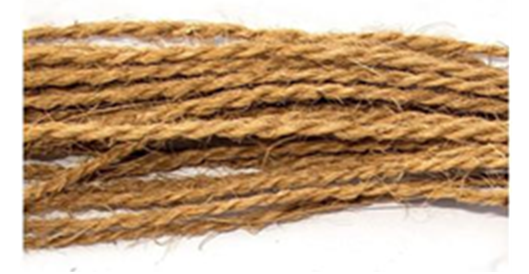 | Figure 8. Rope made of coir fibre |
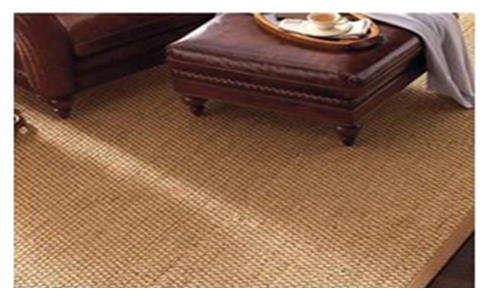 | Figure 9. Carpet made of coir fibre |
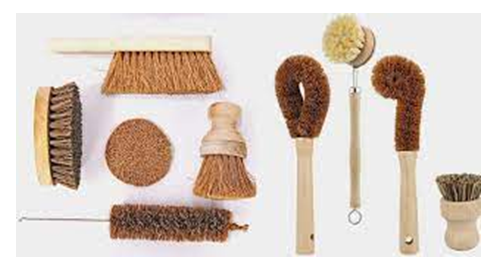 | Figure 10. Brushes made of coir fibre |
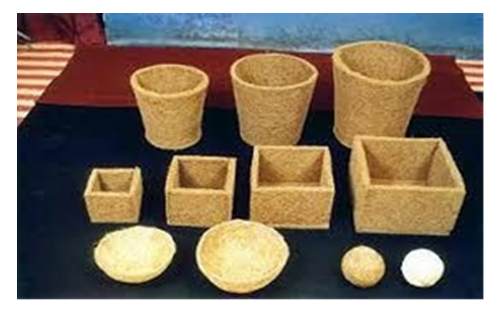 | Figure 11. Pots made of coir fibre |
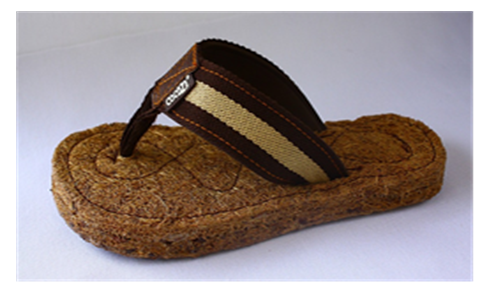 | Figure 12. Shoe made of coir fibre |
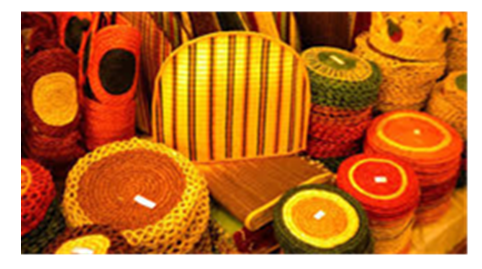 | Figure 13. Decorative products of coir fibre |
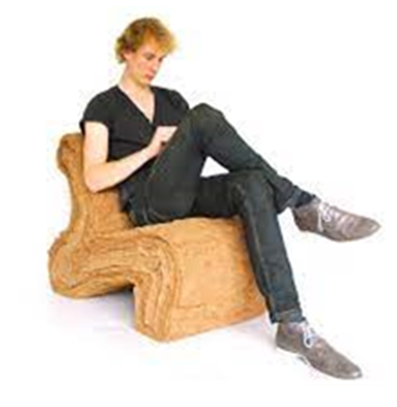 | Figure 14. Chair made of coir fibre |
3. Conclusions
In Bangladesh, there are plenty of coconut trees. So, we can produce a vast amount of coconuts and manufacture coir fibre. This fibre can be used in all sectors mentioned above and more research can be done on this fibre. Geo-textile has a huge prospect for using this fibre in the engineering sector. The Government shall have to be concerned and take necessary steps to increase the production and use of this fibre.
ACKNOWLEDGEMENTS
I would like to thank all authors who have made their research on coir fibre. I was able to do my work with the help of their works which has selective informations in this field. Gathering knowledge about the coir fibre has broadened my horizon in the area of fibres, a core topic of textile engineering. Therefore, I would like to express my heartfelt gratitude to all the researchers in this sector who are working day and night to know the unknown as well as spread the ray of intellect among the general mass.
References
[1] | Textile fibres, dyes, finishes and Processes by Howard L. Needles (Page- 42, 43). |
[2] | Coconut / Coir Fiber: Properties, Manufacturing Process and Uses, Huzaifa Wazir, Textile Learner, Last Updated on 31/12/2020. |
[3] | https://kalpatarucarbon.wordpress.com/about-us-kalpataru-carbon-indonesia/ |
[4] | http://985.so/c927 |
[5] | Effect of alkali treatment on thermal stability and moisture retention of coir fibre, D N Mahato, B K Mathur & S Bhattacherjee, Indian Journal of Fibre & Textile Research, Vol: 20, December 1995 (Pages- 202-205). |
[6] | Effect of chemical treatments on properties of green coconut fiber, A.I.S. Brigida, V.M.A. Calado, L. R. B. Gonclaves, M. A. Z. Coelho, Carbohydrate Polymers, Volume 79, Issue 4, 17 March 2010 (Pages 832-838). |
[7] | Uses of coir fibre, its products & implementation of Geo-Coir in Bangladesh, Belas Ahmed Khan, Daffodile International University Of Science & Technology, Volume 2, Issue 2, July 2007. |
[8] | A review of coir fiber reinforced polymer composites, Adewale George Adeniyi *, Damilola Victoria Onifade, Joshua O. Ighalo, Akorede Samson Adeoye, Composite Part B, Elsevier, 176 (2019) 107305 (Pages- 2-10). |
[9] | Ballistic Application of Coir Fiber Reinforced Epoxy Composite in Multilayered Armor, Fernanda Santos da Luza Sergio Neves Monteiroa, Eduardo Sousa Limaa, Édio Pereira Lima Júniora, Materials Research. 2017; 20 (Suppl. 2): (Pages-23-28). |
[10] | Biobased composites from tannin–phenolic polymers reinforced with coir fibers, Vilmar Barbosa Jr., Elaine Cristina Ramires, Ilce Aiko Tanaka Razera, Elisabete Frollini ∗, Industrial Crops and Products, Elsevier, 32 (2010), (Pages-305–312). |
[11] | Cement Composites Reinforced with Surface Modified Coir Fibers, ZHIJIAN LI, LIJING WANG AND XUNGAI WANG*, Journal of COMPOSITE MATERIALS, Vol. 41, No. 12/2007 (Pages-1445-1457). |