Faridul Islam Ovi1, Shihab Mahmud2
1Department of Wet Process Engineering, Shahid Abdur Rab Serniabat Textile Engineering College, Barishal, Bangladesh (R&D and Product Development Officer, Amazing Fashion Limited, 10/1 Dagerchala, National University, Gazipur, Bangladesh)
2Department of Wet Process Engineering, Shahid Abdur Rab Serniabat Textile Engineering College, Barishal, Bangladesh (Audit Officer, Control Union, Dhaka, Bangladesh)
Correspondence to: Faridul Islam Ovi, Department of Wet Process Engineering, Shahid Abdur Rab Serniabat Textile Engineering College, Barishal, Bangladesh (R&D and Product Development Officer, Amazing Fashion Limited, 10/1 Dagerchala, National University, Gazipur, Bangladesh).
Email: |  |
Copyright © 2021 The Author(s). Published by Scientific & Academic Publishing.
This work is licensed under the Creative Commons Attribution International License (CC BY).
http://creativecommons.org/licenses/by/4.0/

Abstract
Disperse dyes are very important for every textile industry in dyeing polyester fabrics. They are used for hydrophobic fiber like nylon or polyester because they give excellent shade during dyeing. Their dyeing mainly depends on time, temperature and PH. Depending on time and temperature, disperse dye shows different level of sensitivity because of their structure. For proving its sensitivity four types of dyes including two medium energy dyes and two high energy dyes was taken and standard time and temperature for both energy dyes were considered for carrying out the experiment. Dyeing was carried out with standard condition. The dyeing also carried out by varying the standard conditions (by changing Time and Temperature). The different colorimetric data (DE*) was produced by comparing standard shade and the resulting shades by using spectrophotometer. From the investigation it is clearly seen that disperse dyes shows significant sensitivity towards time and temperature at the time of little deviation from the standard time and temperature. Overall, medium energy disperse dyes represent more deviation from standard condition than high energy disperse dye when time and temperature changes.
Keywords:
Sensitivity, Disperse dye, Dyeing, High Energy, Medium Energy
Cite this paper: Faridul Islam Ovi, Shihab Mahmud, Sensitivity Analysis of Medium & High Energy Disperse Dyes in Polyester Dyeing, International Journal of Textile Science, Vol. 10 No. 2, 2021, pp. 27-38. doi: 10.5923/j.textile.20211002.02.
1. Introduction
More than 10,000,000 tons dyes which are mostly used every year in polyester or cotton dyeing [1,2,3]. More than two-thirds of these dyes are used by the textile industry for dyeing polyester or cotton or CVC fabric [4,5]. So dyeing is one of the major sectors in textile which is growing day by day. Standard color of textile is desirable by the consumer but achieving it as per standard is quite hard task even with the help of modern colorimetric system and computer color matching due to the complexity of dying process. Mainly two types of dyes i.e. disperse dyes and polyester dyes are used in textile [6]. For the polyester fabric, disperse dyes are used which are very sensitive to time, temperature, PH, electrolyte, concentration etc. This sensitivity is quite alternative to correctness which is produced by the color difference of one unit between the correct recipe and incorrect recipe. The 100% polyester is tended to be hydrophobic as the polymer chain in a sample of polyester are highly crystalline and quite tightly packed together [7]. As consequences, polyesters have very low affinity for large ionic dyes- the dyes simply can’t either distribute between the chains, or form satisfactorily intermolecular interactions. That’s why acid dyes and direct dyes account as useless for this polyester. Disperse dye despite having low solubility can interact with polyester chains by forming dispersed particles. So, for that their main use is for dyeing polyester having minor use for dyeing cellulose acetates and polyamides [8]. The disperse dye comes into action at temperature above 100°C which is mostly 130°C [8]. At high temperate, thermal agitation bring the polyester structure to become swell and less crystalline, opening gaps for the dye molecules to enter using the van-der-Waals and dipole forces. The volatility of the dye can cause loss of color density and staining of other materials when there are temperature variations or time variations or PH variations. A little difference of these parameter from standard brings the significant change in the shade of fabric which observed by this research. The ultimate purpose of this work is to help the exhaust dyer to select the right recipe for higher production with lower sensitivity and higher correctness.Objectives # To evaluate the sensitivity performance of disperse dye on polyester using different temperature and time.# To investigate color differences of experimented samples comparing with standard sample.# To find out the best possible dyeing conditions for disperse dye on polyester.Properties of Disperse DyeThe properties of disperse dyes are mentioned below:v Generally, disperse dyes are nonionic dyes. So that they are free from ionizing group.v Disperse dyes are insoluble in water or they have very low water solubility.v They are organic coloring substances which are suitable for dyeing hydrophobic fibers.v Disperse dyes are used for dyeing man-made cellulose ester and synthetic fibers specially acetate and polyester fibers and sometimes nylon and acrylic fibers.v During dyeing with disperse dyes Carrier or dispersing agents are required.v Disperse dyes have fair to good light fastness with rating about 4-5.v Wash fastness of disperse dyes is moderate to good with rating about 3-4.v Of all dyestuffs disperse dyes are of smallest molecular size.v Normally, disperse dyes are derivatives of azo, anthraquinone, nitro and quinine groups.v During dyeing, they do not undergo any chemical change.v In presence of nitrous oxide, textile materials dyed with certain blue and violet disperse dyes with an anthraquinone structure will fade. This is called gas fading of disperse dyes which is a defect of this dye. [9]Classification of disperse dyes for polyesterDisperse dyes for a compound shade on polyester can have incongruous dyeing characteristics. The SDC classification of disperse dyes is based on migration capability in time of exhaust dyeing, color build-up, sensitivity to changes in temperature and the rate of dyeing.This kind of dye is often categorized on the basis of dyeing rate and sublimation fastness, especially for polyester dyeing. These two properties are a function of molecular weight and the number of polar groups in the dye molecule. It applies to the dyeing of acetate, of polyester with or without carrier, and of polyester/cotton.Table 1. Classification of Disperse dye for polyester  |
| |
|
Most dyeing and fastness behavior change by the passage of time with increase in molecular size. Little dye molecules with low polarity are leveling, rapid dyeing dyes with less heat resistance. These are known as low energy disperses dyes. More polar, higher molecular weight dyes have poor dyeing rates, less transformation in the time of dyeing but well heat and sublimation fastness. These formed the high energy disperse dyes. The improvement of disperse dyes of developed sublimation fastness needed dye particles with comparatively polar and hydrophilic substituents to eliminate their steam pressure at high temperatures. This promotes somewhat higher solubility in water but the improved in molecular size eliminates the dyeing rate at a mentioned temperature. The high energy disperse dyes are those needed a higher Thermosol temperature [10]. The light fastness does not rely on the molecular size.Generally, Dyes in a mixture are selected from the similar energy class. Build-up of the color on shade needs that the dyes all have about the similar dyeing rate. Experimenting of dye recipes is necessary because a lot of disperse dyes, even dyes of the similar dyeing group, are incongruous in mixtures. This is true even they may have the similar dyeing rates and made-up properties when examined separately. The dye manufacturers supply considerable information associating the dyer to fix appropriate dyes for a mentioned application. [11]Fastness properties of disperse dyesDisperse dyes have moderate to good washing and light fastness on synthetic and acetate fiber. The washing fastness of nylon particularly for deep shade is only fair. After dyeing, the results of washing fastness tests on deep polyester dyeing’s often depend upon how well residual disperse dye elements on the fiber surface have been cleared. When disperse dyes replaced from inside the polyester fiber to the outside during thermal treatments such as drying or heat setting the dyeing may have decreased fastness to washing, rubbing and dry cleaning. When the dyes are soluble in hydrophobic surface such as softener this effect is enhanced. The compendium in (table 1) shows that dyeing of synthetic fibers with disperse dyes normally have good fastness properties. In addition, for any fiber, a definite fastness property depends on greatly from dye to dye. [12]Table 2. Typical fastness properties of disperse dyes on all synthetic fiber 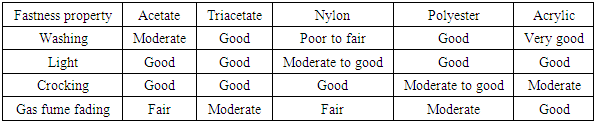 |
| |
|
Mechanism of DyeingMain mechanism of dyeing is to swelling the fiber so that dye molecule gets enough space to stay inside the fiber. In hydrophilic fiber such as cotton this swelling is done by wetting. But when we dye polyester fiber, due to compact structure it is not able to swell on wetting. So, it is hydrophobic fiber. It’s MR% is .04% so it is highly hydrophobic. So, it needs special arrangement.Swelling is done by applying chemical or heat. The chemical which swell fiber called carrier. Heating of dye liquor swells the fiber to open up and assists the dye to penetrate the fiber polymer system. Thus, the dye molecule takes its place in the amorphous regions of the fiber. Once taking place within the fiber polymer system, the dye molecules are held by hydrogen bonds and Van Der Waals’ force. When the system is taken off the molecular area shrunk & dye molecules are entrapped into the polymer.
Before Dyeing Swelling due to heat/carrier After DyeingDye-NH-CH2SO3Na (aq) + H2O → Dye-NH2(s) + CH2O(aq) + NaHSO3(aq)Dye(s) ↔ Dye (aq) ↔ Dye(fiber)Polyester fiber contains pores or canals within its structure which, when heated to 100°C, expand to allow particles of the dyes to enter. The expansion of the pores is limited by the heat of the water – industrial dyeing of polyester is carried out at 130°C in pressurized equipment [13] [14].The dyeing is considered to take place in the following simultaneous steps:1. Diffusion of dye in solid phase into water by breaking up into individual molecules. This diffusion depends on dispersibility and solubility of dyestuff and is aided by the presence of dispersing agents and temperature.2. Adsorption of the dissolved dye from the solution on to the fiber surface. This dyestuff adsorption by fiber surface is influenced by the solubility of the dye in the dye bath and that in the fiber.3. Diffusion of the adsorbed dye from the fiber surface into the interior of the fiber substance towards the center. In normal condition, the adsorption rate is always higher than the diffusion rate. And this is the governing step of dyeing. When equilibrium dyeing is reached, the following equilibria are also established: 1. Dye dispersed in the bath Dye dissolved in the bath 2. Dye dissolved in the bath Dye adsorbed on the fiber 3. Dye adsorbed on the fiber Dye diffused in the fiberProblems of Dyeing Polyester with Disperse DyesPolyester is the man-made or synthetic fiber. They are almost undyeable below 70–80°C, leaving only a 20– 30°C range for increasing the dyeing rate before touching the boiling temperature. At any temperature, the rate of dyeing of polyester with a given disperse dye is quite lower than for cellulose acetate or nylon fibers. The rate of penetration of disperse dyes into the polyester not above 100°C is so low that dyeing at the boil does not give adequate exhaustion. The rate of dyeing is higher for dyes of small molecular size that have higher penetration coefficients. Dyeing is quicker when using fiber swelling agents called carriers to develop the fiber accessibility, or when dyeing at higher temperatures above 100°C to increase the dye diffusion rate. Dyeing of polyester with disperse dyes have pretty light fastness. This does not always related with the light fastness on other fiber such as cellulose diacetate. [15]Effect of Various Conditions on Disperse Dyeing: Effect of Temperature:In case of dyeing with disperse dye, temperature plays an important role. For the swelling of fiber, temperature above 100°C is required if high temperature dyeing method is applied. Again, in case of carrier dyeing method, this swelling occurs at 85-90°C. If it is kept for more time, then dye sublimation and loss of fabric strength may occur.Effect of pH:For disperse dyeing the dye bath should be acidic and pH should be in between 4.5-5.5. For maintaining this pH, generally acetic acid is used at this pH dye exhaustion is satisfactory. During color development, correct pH should be maintained otherwise fastness will be inferior and color will be unstable [16].
2. Materials and Methods
2.1. Materials
Fabric100% polyester knit grey fabric, 160 GSM, from AHSAN KNIT COMPOSITE LTD, holding no. 7,99/D, Pollibiddut Road, Chandra, Gazipur, Dhaka, Bangladesh.DyeA dye is a colored element that chemically bonds to the element to which it is being applied.Characteristic of dye:Must contain chromophore group. This chromophore groups may be different types.Example, -No2,,-NH2,-CO-,-N=O etc.Must be able of preparing dilute solution by dissolving water.Must be power of entering dyestuff to fiber from dye bath.Should have fastness property.Disperse dye:Disperse dyes are normally use for polyester fabric. Medium and High Energy disperse dyes are used in this test which are given below- Table 3. List of disperse dyes and their properties  |
| |
|
CHEMICALS: Three types of chemicals are used. such as-Acetic acid: Acetic is also known as formic acid. It consists of methyl group attached to a carboxyl groupTable 4. Properties of Acetic Acid 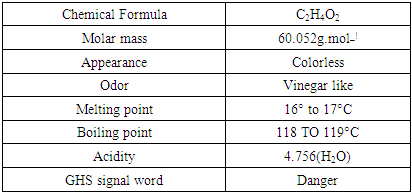 |
| |
|
To maintain, an acidic ph (4.5-5.5) acid is used in polyester dyeing. it is important to maintain that desired Ph.Table 5. Used acetic acid name  |
| |
|
Dispersing agent:A dispersing agent is a surface-active polymer.Functions of Dispersing Agent1. Dispersing agent effects on the rate of dyeing.2. It maintains the solubility of disperse dye in water.3. It helps for particle size reduction.4. Dispersing agent helps the recon version of the power into a dispersion which is too much necessary for textile dyeing.5. This type of agent enables the dye to be formed in the powder form.Table 6. Dispersing Agent name  |
| |
|
Sequestering agent:To remove hardness of water during dyeing an auxiliary is used is called sequestering agent.Use of sequestering agent:Sequestering agents mix with calcium magnesium ions and other heavy metal ions in hard water. They form molecules in which the ions are held so compactly that no longer react.The most unwanted impurities in fiber, common salt, gluber salt and caustic soda and soda ash are the di and tri- valent cations e.g.., ca++, mg++, cu++, Fe++ etc. These ions promote hardness of the process bath and generate iron oxides in the bath. Calcium and magnesium react with alkali and engage as sticky matter on the textile material, which creates incompatible dyeing and discoloration of the fiber. The ferric oxide with cellulose and male small pinhole on the fibers also damages the machinery by scale formation in the nozzle and base.To overcome these baleful effects in the scouring and bleaching bath adequate amount sequestant must be used. sequestrants forbear di and trivalent metal ions from interfering with the chemical processing of the textile material. It restrains catalytic damage of cellulosic fibers in bleaching bath during hydrogen peroxide bleaching.Table 7. Sequestering agent name  |
| |
|
Table 8. Dyeing Machine Specification 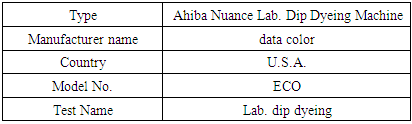 |
| |
|
Table 9. Dryer M/C Specification 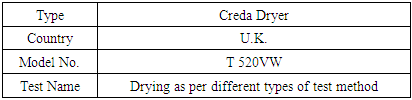 |
| |
|
Spectro photometerIt was used to determine the lightness value (L*) and color difference value
of dyed and pretreated samples.Table 10. Spectro Photometer Specification 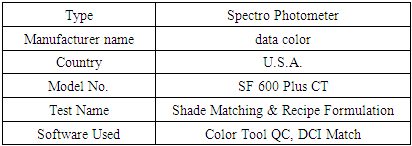 |
| |
|
Other Equipment:1. Barret2. pipette3. conical flux4. weight meter5. scissor & Digital PH Meter
2.2. Methods
2.2.1. Fabric Preparation
For starting polyester dyeing operation, pretreatment of polyester was carried out because it was necessary to remove the lubrication oils and other auxiliaries used during spinning or knitting operation. The following simple process have been done for removing those impuritiesRecipe: Lissopal D Paste: 2gm/lSoda ash: 2gm/lTreat with the above receipe at 90-95°C for 20 minutes.Drain-Hot wash @ 70°C for 10 minutes, then cold wash & neutralize with 1cc/l Acetic Acid. Check the pH: 5.5-6.00.
2.2.2. Dyeing
Polyester dyeing required heat setting before dyeing for eliminating internal tension within the fiber generated during manufacture and the new state can be fixed by rapid cooling. Heat setting fixed the fabrics in the relaxed state and thus avoids subsequent shrinkage or creasing of fabrics. Batch dyeing method was used for dyeing 100% Polyester fabric. Dyeing was carried out in AHIBA IR™ lab dyeing machine with Disperse dye with three shade depth 0.5% owf (Light), 1.5% owf (medium) and 3% owf (Dark) at temperature of 120, 125, 130, 135°C & time of 50min, 30min and their standard recipes of dyeing are mentioned below-Table 11. Dyeing recipe with Dianex Blue XF2 Dye 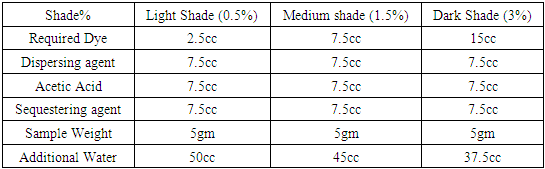 |
| |
|
Table 12. Dyeing recipe with Dianex Rubine XFS Dye 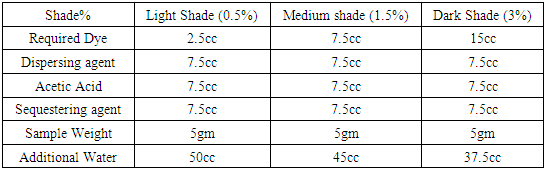 |
| |
|
Table 13. Dyeing recipe with Dianex Blue CC Dye 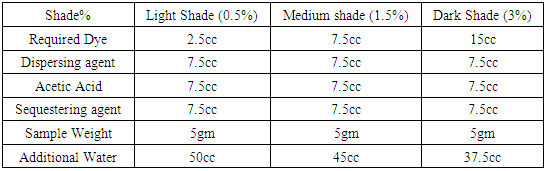 |
| |
|
Table 14. Dyeing recipe with r Dianex Yellow brown Dye 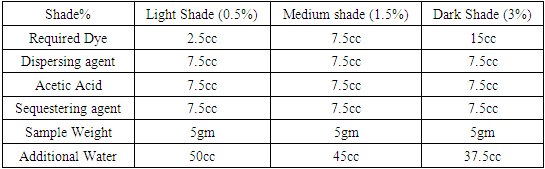 |
| |
|
2.2.3. Dyeing Flow Chart For 100% Polyester
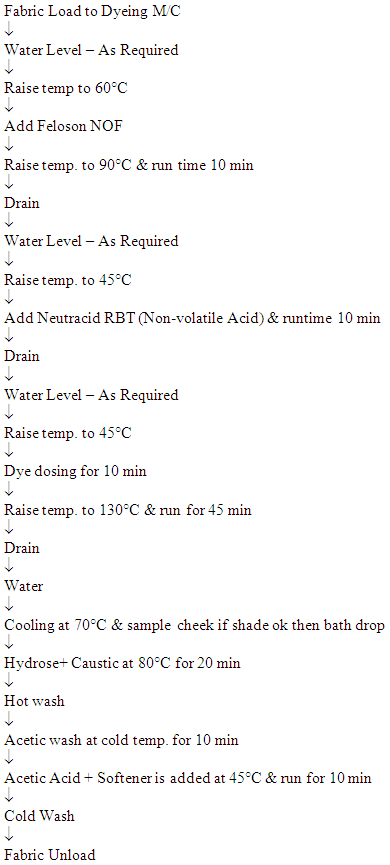
2.2.4. Colorimetric Values of Dyed Fabric
Before any permanent samples are measured and stored into the computer, a repeatable measurement technique must be established and observed. Samples should be observed multiple times with the largest area view available on the data color being used as long as the samples are large enough to cover the viewing area. Samples condition is also taken into account because variations in temperature and moisture content can contribute to variations in measurement data. Two or four layers is sufficient to achieve opaque sample for presentation to the instrument. If material is not opaque, light will easily pass through the sample and reflect off the backing material or sample holder and produce misleading reflectance data.Colorimetric values are very important parameters for evaluation of sensitivity of disperse dye. The more the color difference below one from standard sample, the lower the sensitivity. These values were determined using X-Rite instead Data Color 500 considering one standard sample and others as experimental sample. and measurements was taken using illuminant D65 and 10° Standard Observer. The samples were folded to ensure opacity and an average of two readings was calculated.
3. Results & Discussion
For determining color difference spectrophotometer was used. For better convenience of result discussion, a grading system for sensitivity has been introduced.Table 15. Grading system 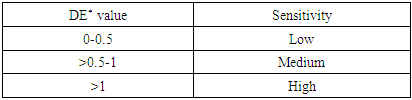 |
| |
|
The Sample dyeing at temperature 130°C & for 50min is used as standard sample for measuring colour difference of other sample for below figure 1, 2, 3 & 4.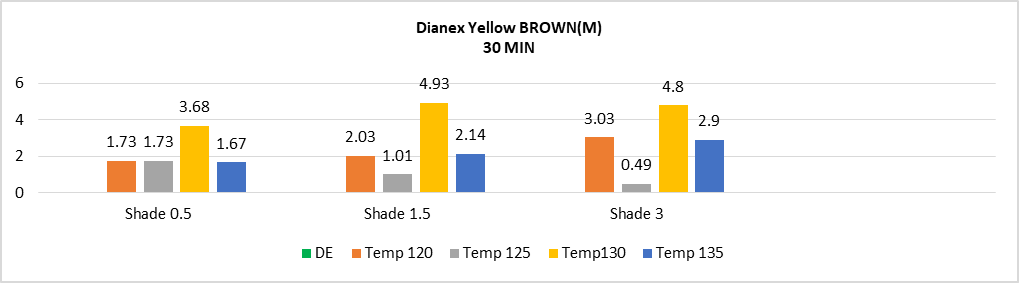 | Figure 1. Color difference (DE*) of medium energy Dianex Yellow Brown (DYB) VS Temperature VS varying shade at 30min |
The above bar chart showing the fluctuation value of color difference of medium energy dianex yellow brown at constant time of 30 min when the temperature is varying. It can be said that DYB Disperse dye shows higher sensitivity to temperature 120°C, 125°C, 130°C, 135°C and at temperature 125°C when the shade percentage was 3%, it shows low sensitivity. The highest sensitivity is shown at the temperature of 130°C. The percentage of color difference from 125°C to 130°C among three shades 0.5%, 1.5%, 3% is 72.1%, 131.98%, and 162.95%. So medium energy DYB Disperse dyes has significant sensitivity value to temperature. A little change in temperature brings sufficient change in color difference when the time is fixed (which is 30 minutes).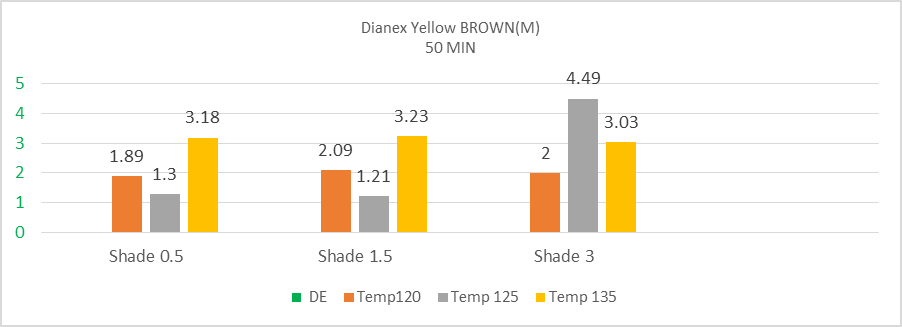 | Figure 2. Color difference (DE*) of medium energy Dianex Yellow Brown (DYB) VS Temperature VS varying shade at 50min |
The above bar chart showing the fluctuation value of color difference of medium energy dianex yellow brown at constant time 50 min when the temperature is changing. It can be said that DYB Disperse dye shows higher sensitivity to temperature 120°C, 125°C, 135°C. The highest sensitivity is shown at the temperature 135°C for 0.5% shade. The percentage of color difference from 125°C to 135°C between two shades 0.5%, 1.5% is 83.93%, 90.99%. The percentage of color difference from 120°C to 125°C is 76.73%. So medium energy DYB Disperse dyes has significant sensitivity value to temperature. A little change in temperature brings sufficient change in color difference when the time is fixed (which is 50 minutes). So, it needs a careful concentration when working with medium energy DYB Disperse dye because they have higher sensitivity to temperature. 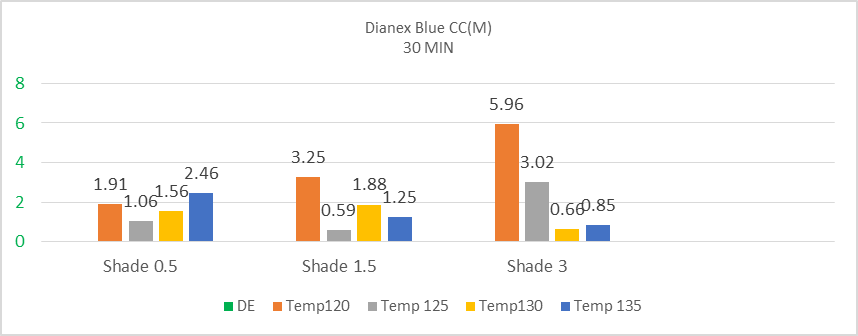 | Figure 3. Color difference (DE*) of medium energy Dianex Blue CC VS Temperature VS varying shade at 30min |
From the above bar chart, it’s clear that the changing temperature has greater influence to color difference. It shows higher sensitivity to the temperature of 120°C, 125°C, 130°C, 135°C. For Shade 1.5% and 3%, it shows medium sensitivity at the temperature 125°C, 130°C & 135°C when time is fixed which is 30min. For 0.5% shade color difference of samples dyeing at 120°C, 125°C, 130°C, 135°C temperature comparing to standard sample is 1.91, 1.09, 1.56, 2.46. For 1.5% shade color difference of samples dyeing at 120°C, 125°C, 130°C, 135°C temperature comparing to standard sample is 3.25, 0.59, 1.88, 1.25 where 0.59 is accepted.. For 3% shade color difference of samples dyeing at 120°C, 125°C, 130°C, 135°C temperature comparing to standard sample is 5.96,3.02,0.66,0.85 where 0.66 & 0.85 is accepted. The highest deviation from standard sample is obtained 2.46 for 0.5% shade at 135°C, 3.25 for 1.5% shade at 120°C, 5.96 for 3% shade at 120°C.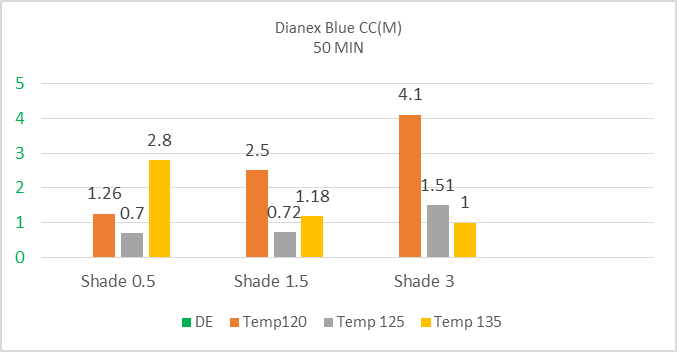 | Figure 4. Color difference (DE*) of medium energy Dianex Blue CC VS Temperature VS varying shade at 50min |
The above bar chart shows there is a difference in DE* value when there is a change in temperature. Here three kinds of shade are used namely 0.5%, 1.5% & 3%. There is a fluctuation in colour difference for 0.5% & 1.5% shade but decreasing trend is observed for 3% shade when temperature is increasing. So medium energy Dianex Blue CC dye show sensitivity depending on temperature.The Sample dyeing at temperature 135°C & for 50min is used as standard sample for measuring colour difference of other sample for below figure 5, 6, 7 & 8.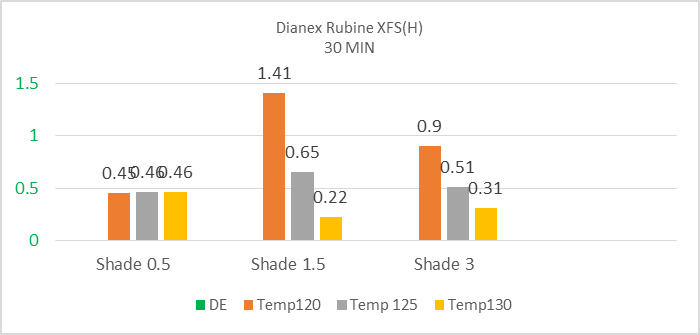 | Figure 5. Color difference (DE*) of High energy Dianex Rubine XFS VS Temperature VS varying shade at 30min |
The above bar diagram shows that the high energy Dianex Rubine XFS is showing low sensitivity with the increase of temperature for 0.5% shade but it shows high sensitivity towards the temperature of 120°C for 1.5% shade but for high temperature like 125°C & 130°C it’s sensitivity medium to lower. When the temperature is 120°C, 125°C & 130°C then the color difference value is slightly decreasing towards accepted value. So the high energy Dianex Rubine XFS Disperse dye represents lower sensitivity with the increase in temperature.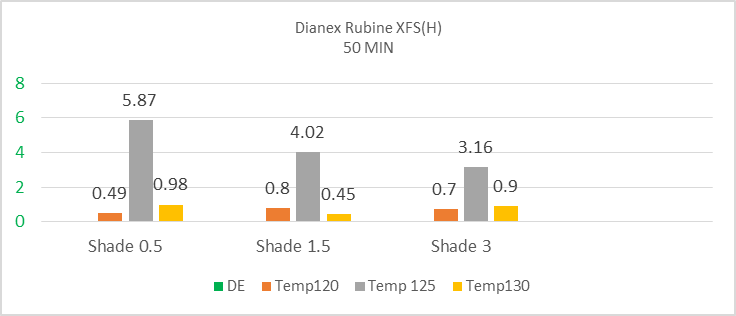 | Figure 6. Color difference (DE*) of High energy Dianex Rubine XFS VS Temperature VS varying shade at 50min |
The above diagram represents highest colour deviation at 125°C for all the shade of 0.5%, 1.5% and 3% where the DE* value is 5.87, 4.02 and 3.16. Rather than 125°C, the other temperature like 120°C, 130°C gives accepted value of colour difference. So, when the temperature is going towards standard value, it is showing less sensitivity. Overall it can be said that high energy Dianex rubine is less sensitive to temperature and time.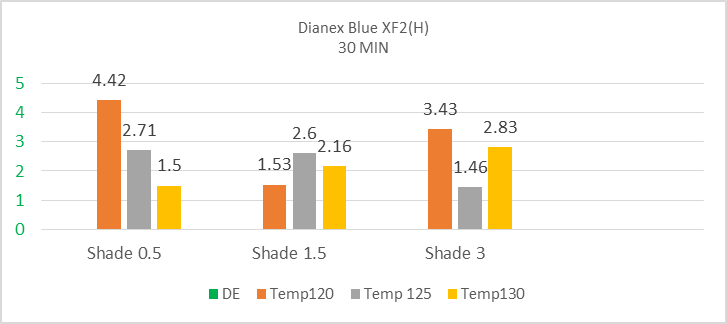 | Figure 7. Color difference (DE*) of High energy Dianex Blue XF2 VS Temperature VS varying shade at 30min |
The above diagram illustrates the upward and downward fluctuation of color difference depending on varying temperature and shade %. The high energy Dianex Blue XF2 Disperse dye shows higher sensitivity towards temperature. When temperature become lower the sensitivity is higher for 0.5% shade but when temperature increase the DE* slightly decrease. The temperature with time plays a significant role in the sensitivity of disperse dye. For 1.5% shade, there is fluctuation in color difference with the increase in temperature. For temperature 120°C, 125°C & 130°C the DE* value is 1.55, 2.6 & 2.16. The fluctuation is also observed for 3% shade where it gives the DE* value of 3.43, 1.46 & 2.83 at 120°C, 125°C & 130°C temperature. The above values ensure that the high energy Dianex Blue XF2 is higher sensitive dye depending on time & temperature.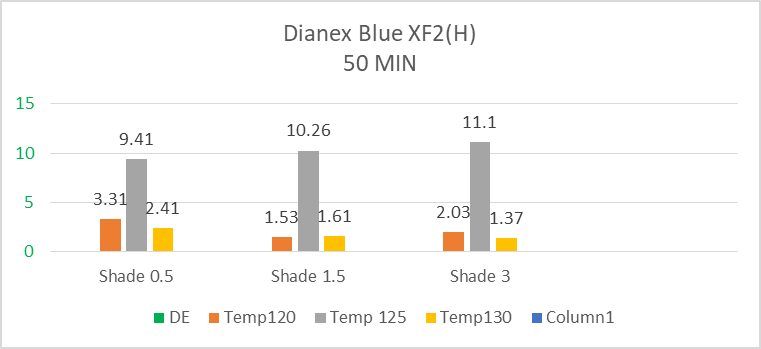 | Figure 8. Color difference (DE*) of High energy Dianex Blue XF2 VS Temperature VS varying shade at 50min |
The above bar diagram shows us the changes in colour difference of high temperature Dianex Blue XF2 relying on time and temperature. The highest sensitivity is found at 125°C temperature for all the experimental shade i.e. 0.5%, 1.5%, 3% comparing with the standard value when the time is fixed (50min) for all the shade. The 0.5% shade represents higher sensitivity towards temperature at 120°C comparing to 1.5% & 3% shade but dye for 1.5% shade is lower sensitive than 3% shade. For 0.5% shade Dianex Blue XF2 dye is also more sensitive to temperature than 1.5% & 3% shade at 130°C. Here neither medium nor lower sensitive value is found. Dianex Blue XF2 is higher sensitive dye.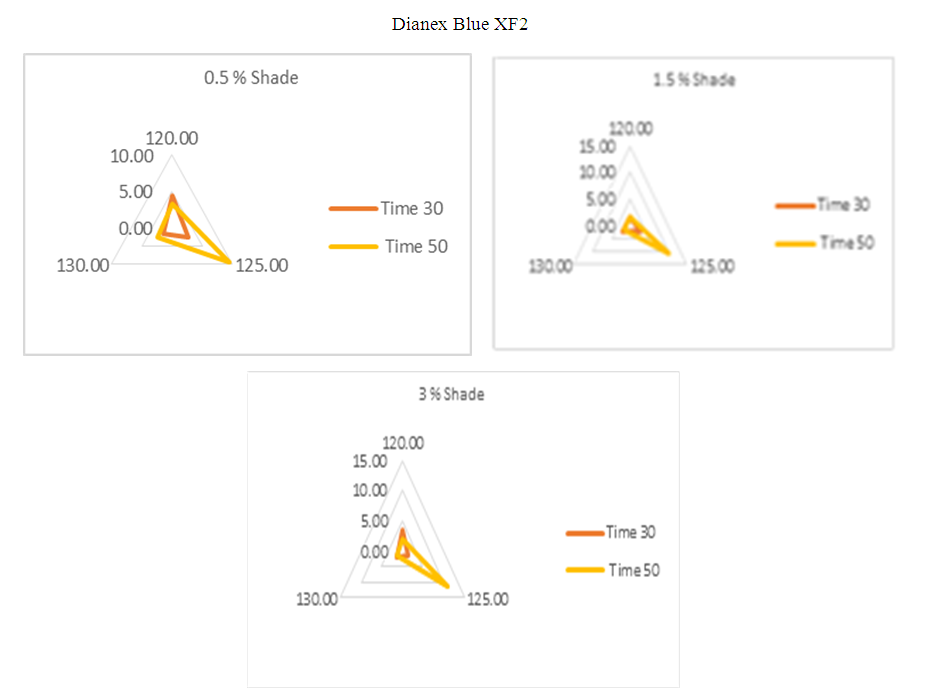 | Figure 9. Radar diagram for high energy Dianex Blue XF2 showing color difference at varying temperature and time among 0.5% shade, 1.5% shade and 3% shade |
The above diagram illustrates the detail deviation of color difference for 0.5%, 1.5% & 3% shade when temperature and time is changing. It gives the clear conception of color fluctuation at a glance.For 0.5% shade, it is observed that when the temperature is 125°C and dyeing time is 50min, the Dianex Blue XF2 Disperse dye shows highest sensitivity. Overall it represents deviation of color difference when the time and temperature slightly move down from standard where the standard temperature and time is 135°C and 50min.For 1.5% shade, the standard time and temperature is kept as 135°C and 50min. comparing to this standard highest deviation of DE* is found 10.26 at 125°C and 50min. On contrary, it becomes 2.6 at same temperature but in this moment, dyeing time is 30min. But overall consideration shows, there is significant deviation of color difference.For 3% shade considering the same standard, we observed that there is highest sensitivity of this dye comparing the other shade at the same temperature of 135°C and at the same dyeing time is 50min. it also shows higher sensitivity toward time and temperature.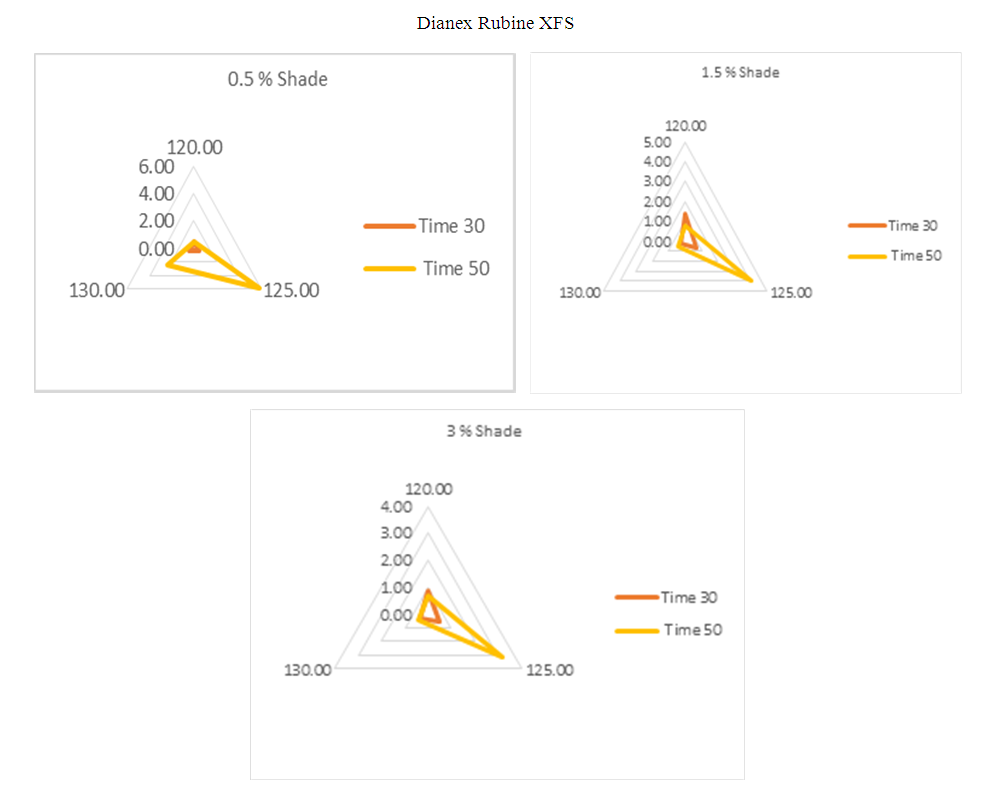 | Figure 10. Radar diagram for high energy Dianex Rubine XFS showing colour difference at varying temperature and time |
For the above shade of 0.5%, 1.5% & 3%, the standard time and temperature is taken as 135°C and 50min.For 0.5% shade, the Dianex Rubine XFS represents medium sensitivity at the all experimented temperature of 120°C, 125°C, 130°C when dyeing time time is 30min. This medium sensitivity is accepted but on contrary, the sensitivity is higher at 125°C when dyeing time is 50min where the two values of DE* is accepted at 120°C & 130°C.For 1.5% Shade, the higher sensitivity is observed at 120°C following dyeing time30min but for dyeing time 50min, the higher sensitivity is found at 125°C. The other remaining values for both the dyeing time 30min & 50min is accepted which are clearly seen from the diagram.For 3% shade, all the DE* values are showing medium sensitivity at the temperature of 120°C, 125°C & 130°C when the dyeing time for that is 30min but when the dyeing time is 50min then there is sensitivity observed at 125°C. The other remaining values are expressing medium sensitivity.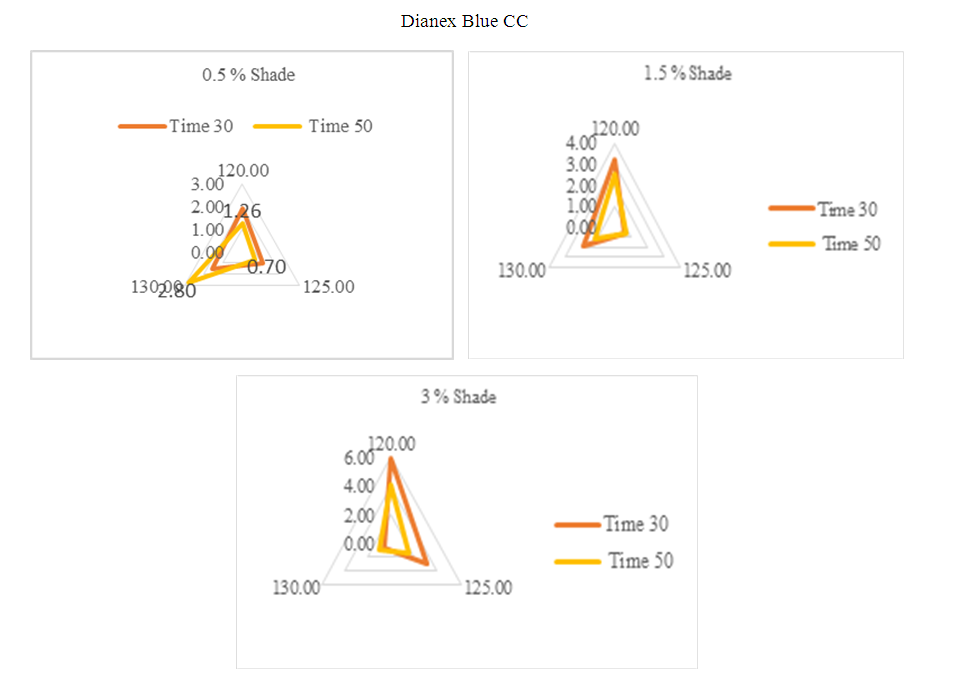 | Figure 11. Radar diagram of colour difference for medium energy Blue CC |
For the above diagram considering the standard sample at 130°C where dyeing time 50min for comparing other sample. it can be clearly seen that when temperature change from standard, the dye shows sensitivity for all the experimented shade of 0.5%, 1.5% & 3%. But meanwhile they also show some medium sensitivity towards time and temperature but low sensitivity is rear. So, it can be said that Dianex Blue CC has high sensitivity to time and temperature.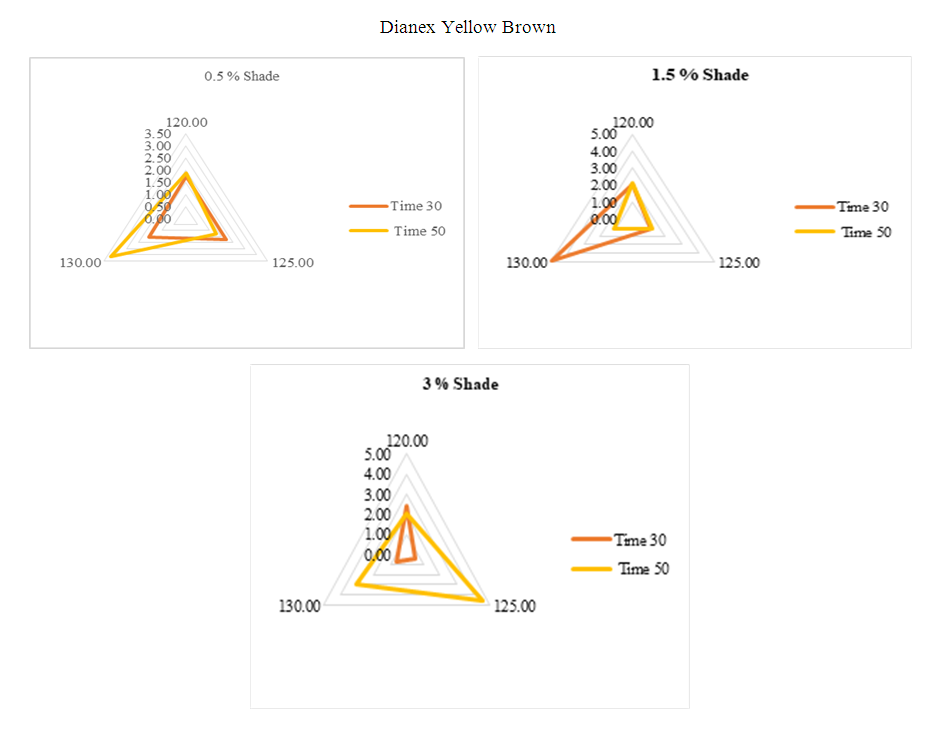 | Figure 12. Radar diagram for medium energy DIanex Yellow Brown (DY B) showing colour difference at varying temperature and time |
Sample dyeing at 130°C & use time 50min is considered as standard sample for getting convenient result. For the above three shade there is clear result that DYB Disperse dye has higher sensitivity to time and temperature except one case where it shows low sensitivity which is for 3% shade at 125°C temperature & dyeing time 30min. Rather than that for other experimented time i.e. 30min & 50min and temperature i.e. 120°C, 125°C. 135°C, the medium energy DYB has higher sensitivity and it is maximum at the temperature 130°C and time 30min for 1.5% shade. So overall, we can come to a conclusion that DYB disperse has sensitivity toward time and temperature.
4. Conclusions
The structured makes disperse dye simpler for the dye to slide between the tightly packed polymer chains, and the polar groups improve the water solubility, improve the dipolar bonding between dye and polymer and influence the colour of the dye. Therefore, their tiny nature means that they are volatile and tend to sublime out of the polymer at high temperatures.From results and discussion, it is observed that disperse dyes have showed high sensitivity toward varied temperature and time. A little variation in time and temperature brought significant change in colour difference which can be the cause of not having desired shade during dyeing. The medium energy disperse dye have shown more sensitivity which mean that when the temperature and time change from standard, their colour difference value significantly moved which is mostly higher than one. In comparison with medium energy disperse dye, the high energy disperse is less sensitive to time and temperature variations whereas sometime the colour difference (DE*) value is more than one. So, time and temperature should be strictly maintained during dyeing of fabric with high energy and medium energy disperse dyes for having desired shade.
ACKNOWLEDGEMENTS
We have been able to complete this research program with the support and active co-operation of concerned bodies and authorities and several persons. We owe our dept and would like to express deep feelings of gratitude to our teacher Mr. Engr. Nayon Chandra Ghosh, Assistant Professor, Department of Wet Process Engineering, Shahid Abdur Rab Serniabat Textile Engineering College for his valuable guidance at different stages of this research program. We are intensely indebted to our honorable principal Engr. Md. Mozibur Rahman who selected us for accomplishing the research program and for his overall support and motivation.
References
[1] | Ghorpade, B, Darvekar, M, & Vankar, PS. (2000). Ecofriendly cotton dyeing with Sappan wood dye using ultrasound energy. Colorage, 45(1), 27–30. |
[2] | Goodarzian, H, & Ekrami, E. (2010). Extraction of dye from madder plant (Rubia tictorium L) and dyeing of wool. World Appl Sci J, 9(4), 434–436. |
[3] | Saravanan, P, Chandramohan, G, Mariajancyrani, J, & Kiruthikajothi, K. (2014). Eco friendly dyeing of wool fabric with a natural dye extracted from barks of Odinawodier. Der Chemica Sinica, 5(1), 28–33. |
[4] | Anouzla, A, Souabi, S, Safi, M, Aboulhassan, A, Rhbal, H, & Abrouki, Y. (2009). Valorization of steel industry wastewaters in the decolorization of dyes containing solutions. Scientific Study & Research, 10(3), 277–284. |
[5] | Shertate, RS, & Thorat, PR. (2013). Biotransformation of sulphonated azo dye direct red 5B by marinobacter sp. dr-7- a bioremedial aspect in marine environment. Int J Pharma Bio Sci, 4(3B), 524–534. |
[6] | Prof. Dr. Engr. Shah Alimuzzaman belal. CText. FTI (UK).Understanding Textiles For a Merchandiser. 2nd ed. Bangladesh: LB Graphics & Printing, 2009, P. 623. |
[7] | Saleh Mohammed Al-Mousawi, Morrsy Ahmed El-Apasery, Huda M. Mahmoud, Disperse Dyes Based on Aminothiophenes: Their Dyeing Application on Polyester Fabrics and Their Antimicrovial Activity, Moleculers 2013, 18, 7081-7092. |
[8] | M. Clark, Hand Vook of textile and industrial dyeing, volume 2: Applications of dyes, Woodhead Publishing india private Limited, 2011 P. 41. |
[9] | Textile Dyes by NN. Mahapatra. |
[10] | Collishaw P S, Bradbury M J, Bone J A, and Hyde R F (1998), High performance reactive and Disperse dye technology to meet the needs of the globalized textile industry, colourage Ann., 117-125. |
[11] | SDE Committee on Disperse Dyes, J.S.D.C. , 80 (1964) 237. |
[12] | J Bowels, A Puntener and J R Aspland, Text. Chem. Colorist, 26(3) (1994) 17. |
[13] | Derbyshire A N (1974), The development of dyes and methods for dyeing polyester, JSDC, 90(8), 273-280. |
[14] | Peter Hauser (Ed.), Dyeing with Disperse Dyes, Textile Dyeing, Joonseok Koh 2011. ISBN: 978-953-307-565-5. |
[15] | M. Clark, Hand Vook of textile and industrial dyeing, volume 2: Applications of dyes, Woodhead Publishing india private Limited, 2011 P. 73-74. |
[16] | Nur-Us-Shafa Mazumder, Md. Mehedi Hasan Tusher, Md. Ashif Hossain Shuvo, Effect of Dyeing Parameters PH and Temperature in disperse dyeing. |