Md. Rafiul Islam, A. K. M. Ayatullah Hosne Asif, Abdur Razzaque, Abdullah Al Mamun, Md. Maniruzzaman
Department of Textile Engineering, Mawlana Bhashani Science and Technology University, Santosh, Tangail, Bangladesh
Correspondence to: Abdullah Al Mamun, Department of Textile Engineering, Mawlana Bhashani Science and Technology University, Santosh, Tangail, Bangladesh.
Email: |  |
Copyright © 2020 The Author(s). Published by Scientific & Academic Publishing.
This work is licensed under the Creative Commons Attribution International License (CC BY).
http://creativecommons.org/licenses/by/4.0/

Abstract
The purpose of this study was to investigate the seam performance for commercially available 100% cotton plain woven fabric. The eminence of seam is characterized by strength of the seam, the elongation of seam and efficiency of the seam. Seam strength along with seam efficiency can contribute as important factor in determining the durability of a garment. Seam strength is related to the type of seam, the strength, efficiency of the seam and the seam density as well. Specifically, 100% cotton plain woven fabric was used for seam performance analysis because of its availability in market. Four different types of stitch structures along with three types of sewing threads like Ne 40s/2, 50s/2, and 60s/2 were used. Seam strength and efficiency of plain woven fabric was changed consecutively with different stitch types in conjunction with increasing stitch density and more specifically, maximum seam strength and efficiency were observed at cotton plain woven fabric for four thread overlock stitch structure together with 12 stitches per inch rather than others. Seam that contains more stitches per inch illustrates more seam strength and efficiency.
Keywords:
Seam, Sewing Thread, Stitch Density, Woven Fabric, Tensile Strength
Cite this paper: Md. Rafiul Islam, A. K. M. Ayatullah Hosne Asif, Abdur Razzaque, Abdullah Al Mamun, Md. Maniruzzaman, Analysis of Seam Strength and Efficiency for 100% Cotton Plain Woven Fabric, International Journal of Textile Science, Vol. 9 No. 1, 2020, pp. 21-24. doi: 10.5923/j.textile.20200901.04.
1. Introduction
The nature of the fabric affects not only the durability of the garments, but also the simplicity of which the shell framework may be constructed out of smooth fabric [1]. The requirements of the fabrics for the manufacturing of clothing can be regarded in terms of primary and secondary consistency characteristics [2]. The main consistency characteristics are the static physical proportions and the secondary characteristics are the reactions of the cloth to the dynamic force applied [3]. Stitches are accustomed to be a part of the clothing element along and seams characterize the form of the outfit for wear and typically for ornamental functions. These factors along with their performance properties improve the quality of the clothing [4]. The quality of the fabric affects not only the quality of the clothing, but also the ease with which a smooth structure can produce a shell structure [5]. More attention has been given in current years to the design, comfort and fitness of apparel in the textile industry. The most important features required from a garment are consistency, durability, serviceability, aesthetics and compliance. Style and aesthetic beauty are also relevant to consumers perception [6]. Clothing manufacturers are mainly interested in the tributary appearances of the fabric and focus on the quality of the seam during the manufacturing and production of clothing while applied to active coerce [7].At present, the garment industry has adopted various parameters to evaluate the seam performance of commercial fabrics, such as the seam efficiency which is used to assess seam durability [8]. It should be noted that the durability of the seam represents the relationship between the strength of the seam and the strength of the fabric. Predicting the performance of a seam on a fabric based on the properties of the fabric and the sewing parameters, has been considered by many researchers; indeed, many studies have been conducted to predict the effect of seam performance [9] [10]. Specifically, seam drops a line to the fabric components to ensure the durability of the best products [11]. The visual and technical requirements of dress depend on various specifications [12]. The design and competence of the seams depend on the stitch and fabric forms, the stitch width, the configuration of the sewing machine and the consistency of the sewing threads while the seam output of the garment depends on the structural and mechanical properties of the fabric along with the strength, extensibility, protection, flexibility, beauty and quality of the seams [13]. The fabric with the proper seam class enhances the serviceability and resilience of functional features of clothing [14]. Seam strength affects the functional and aesthetic performance of the clothing in terms of reliability and durability [15]. Clothing manufacturers set standards as guidelines for product development, and these standards are based on customers' preferences [16] [17]. Tensile strength and stitching properties are key performance indicators to guarantee whether the end product is suitable for end-use [18] [19].
2. Experimental Methodology
2.1. Material
2.1.1. Fabric
The fabric selected for this experiment was 100% cotton pain woven fabric. The GSM (gram per square meter) of the fabric was 104, EPI (Ends per Inch) and PPI (Picks per Inch) were comprised about 114 and 64 respectively along with warp yarn count and weft yarn count were both accounted for 70s/1 Ne.
2.1.2. Sewing Parameters
To continue this study, four different types of stitches were used (lockstitch, three thread flatlock stitch, four thread overlock stitch and chain stitch). Different sewing machines (Brand name: Juki, Kansai, Yamato) were employed to produce these stitches. Stitch density was accounted for 6, 8, 10 and 12 and needle size was 14.
2.1.3. Sewing Thread Specification
For this experiment, three different types of sewing thread count was used like 40s/2, 50s/2 and 60s/2 Ne respectively. All of the threads were spun polyester with double ply formation. Besides these materials, the following materials were also used-• Measuring Tape• Electronic balance• Tensile Strength Tester (James heal)• Scissor and tailoring chalk
2.1.4. Tensile Strength Testing Machine Specification
• Name: Titan Universal Strength Tester• Model No.: Titan5• Company: James Heal (Richmond Works)• Origin: United Kingdom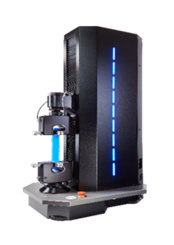 | Figure 1. Universal Tensile Strength Testing Machine (James Heal) |
2.2. Methodology
The experiment was performed by ASTM method for sample preparation and testing. Five samples from each stitch type (lockstitch, four thread overlock, three thread flatlock and chain stitch) along with sewing thread count (40s/2, 50s/2, 60s/2 Ne) with different stitch density (6, 8, 10, 12) were employed to conduct the study. Then Sewn fabrics were tested for seam strength and efficiency on James heal tensile strength testing machine at a speed of 305 mm/min and 75 mm gauge length as per ASTM-D1683 standards [20]. Five tests were conducted consecutively in warp direction for each sample. The tensile strength of un-seamed fabric was measured by James Heal tensile strength testing machine and the result was found about 702N. For seam strength testing, the sample of (10×10) cm2 was cut from the base fabric and sewn in warp direction with seam allowance of 1 inch. Seam efficiency was measured by following formula: Seam efficiency (%) = (Seamed fabric tensile strength / Un-seamed fabric tensile strength) × 100
3. Results and Discussion
3.1. Determination of Seam Strength and Efficiency for Ne 40s/2
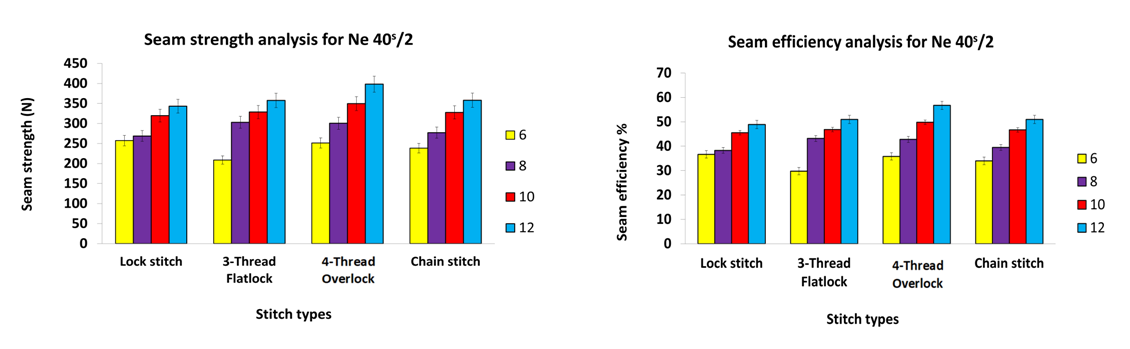 | Figure 2. Seam strength and efficiency for Ne 40s/2 |
The following figures demonstrate about the seam strength and efficiency analysis for Ne 40s/2 at 100% cotton plain fabric. It is perceived from the above figures that; seam strength is increased with the increase of stitch per inch (SPI) at plain woven fabric. In case of same woven fabric, seam strength is increased gradually with different stitch types by increasing SPI. Maximum seam performance observed for cotton plain fabric upon four thread overlock stitch (398N) structure in comparison with other stitches for Ne 40s/2 specifically for 12 SPI because overlock stitch encloses seam while using multiple threads to lock each edge which prevents it from fraying. Seam that contains more stitches per inch in seam line illustrates more seam strength along with seam efficiency as it grips the fabric more tightly.
3.2. Analysis of Seam Strength and Efficiency for Ne 50s/2
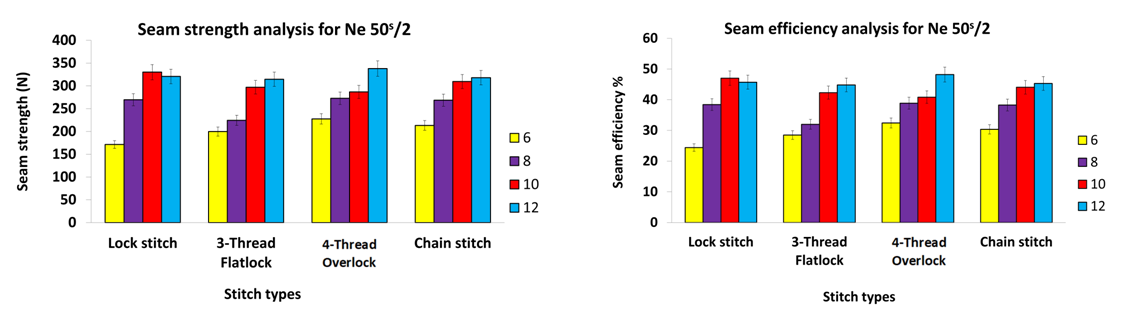 | Figure 3. Seam strength and efficiency analysis for Ne 50s/2 |
The above charts display about the seam strength and efficiency at Ne 50s/2 sewing thread. For different types of stitches, seam strength and efficiency increased with the surging of stitch density. Among different stitch types, specifically for four thread overlock stitch, maximum seam strength (338N) and efficiency demonstrated in case of 12 SPI rather than other stitch density. Chain stitch structure along with higher stitch density also represents better seam performance than others. This is due to the fact that, for higher stitch density maximum stitches constitute in seam line which holds the fabric more tightly than others for cotton plain woven fabric.
3.3. Formulation of Seam Strength and Efficiency for Ne 60s/2
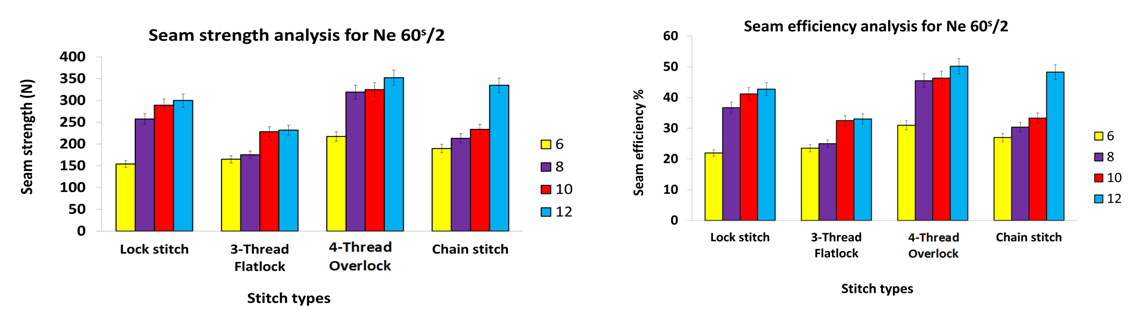 | Figure 4. Seam strength and efficiency analysis for Ne 60s/2 |
The following charts demonstrate about the seam strength and efficiency for Ne 60s/2 at cotton plain woven fabric. It is observed that, seam strength and efficiency increased successively for each stitch structures with the increase of stitch per inch (SPI) for plain fabric. Overall, the seam performance was excellent for four thread overlock stitch (352N) rather than other stitch types. From the above figures it can be clearly stated that, maximum seam strength shows at plain fabric for Ne 60s/2 by 12 SPI. Seam that contains more stitches per inch shows more seam strength and efficiency.
4. Conclusions
In this work, 100% cotton plain woven fabric was used to understand seam performance in context with seam strength and efficiency because this kind of fabric is commercially available around the world more than any other fabrics. Three different types of sewing thread along with four different types of stitches in warp direction and four different stitch density were used to measure seam performance. It has been clearly noticed that, seam strength and efficiency increased while surging the stitch density upon different stitch structures like lockstitch, three thread flatlock stitch, four thread overlock stitch and chain stitch for 100% cotton plain woven fabric. Among the stitch density 6, 8, 10 and 12; 6 SPI was recorded as low quality due to smaller number of stitches present in seam line which results in meagre seam strength along with efficiency. By increasing the amount of stitch density like 8, 10, 12; for each type of stitch structures like lockstitch, three thread flatlock, four thread overlock, chain stitch; overlock stitch encompasses seam structure by means of several threads to latch individual edge averting it from fraying successively and for 12 SPI, it shows the best performance than other stitch density in case of Ne 40s/2 rather than other counts. Based on the results of this study, apparel manufacturers will be mindful about the use of suitable threads and stitches for garments sewing. Such kind of knowledge will help consumers and manufacturers to achieve the desired results from end products in terms of the seam.
Compliance with Ethics Requirements
This article does not contain any studies with human or animal subjects performed by any of the authors.
ACKNOWLEDGEMENTS
The authors gratefully acknowledge the Research Cell of Mawlana Bhashani Science and Technology University for financial support of this work.
References
[1] | Choudhary, A. K. and Goel, A. (2013) Effect of Some Fabric and Sewing Conditions on Apparel Seam Characteristics. Journal of Textiles, 1–7. |
[2] | Tarafder, N., Karmakar, R. and Mondal, M. (2007) The effect of stitch density on seam performance of garments stitched from plain and twill fabrics. Man-Made Textiles in India, 50(8), 298–302. |
[3] | Bharani, M., Shiyamaladevi, P. S. S. and Mahendra Gowda, R. V. (2012) Characterization of seam strength and seam slippage on cotton fabric with woven structures and finish. Research Journal of Engineering Sciences, 1, 41–50. |
[4] | Seram, N. and Cabon, D. (2013) Investigating the possibility of constructing different seam types for clothing using ultrasonic. International Journal of Clothing Science and Technology, 25(2), 90–98. |
[5] | Milda, J. and Vaida, D. (2008) Seam pucker indicators and their dependence upon the parameters of a sewing machine. International Journal of Clothing Science and Technology, 20, 231–239. |
[6] | Öztaş, H. and Gürarda, A. (2019) Investigation of the effects of different bias angles of stitching on seam performance of wool suits. Autex Research Journal, 19(4), 324–331. |
[7] | Najwa, A. A. N. (2013) Evaluation of seam pucker of woven cotton fabrics using two different methods. Journal of American Science, 9, 205–210. |
[8] | Shi, H., Zhang, L. and Wang, J. (2017) Influence of seam types on seam quality of outdoor clothing. International Journal of Clothing Science and Technology, 29(4), 553–565. |
[9] | Dobilaite, V. and Juciene, M. (2006) The influence of mechanical properties of sewing threads on seam pucker. International Journal of Clothing Science and Technology, 18(5), 335–345. |
[10] | Yildiz, Z., Dal, V., Ünal, M. and Yildiz, K. (2013) Use of artificial neural networks for modelling of seam strength and elongation at break. Fibres and Textiles in Eastern Europe, 5, 117–123. |
[11] | Namiranian, R., Saeed, S. N., Sayed, M. E. and Albert, M. M. (2014) Seam slippage and seam strength behavior of elastic woven fabrics under statistic loading. International Journal of Fibre and Textile Research, 39, 221–229. |
[12] | Thanaa, M. A. S. (2013) Interaction between sewing thread size and stitch density and its effects on the seam quality of wool fabrics. Journal of Applied Sciences Research, 9, 4548–4557. |
[13] | Zervent Ü. B. (2012) The prediction of seam strength of denim fabrics with mathematical equations. The Journal of The Textile Institute, 103, 744-751. |
[14] | Raj, D. V. K. and Devi, M. R. (2017) Performance analysis of the mechanical behaviour of seams with various sewing parameters for nylon canopy fabrics. International Journal of Clothing Science and Technology, 29(4), 470-482. |
[15] | Mohanta, R. (2006) A study on the influence of various factors on seam performance. Asian Textile Journal, 15(10), 57-62. |
[16] | Nayak, R., Padhye, R. and Gon, D. P. (2010) Sewing performance of stretch denim. Journal of Textile and Apparel, Technology and Management, 6(3), 1–9. |
[17] | Phebe A. K. and Chandrasekaran, B. (2014). Studies on Influence of Stitch Density and Stitch Type on Seam Properties of Garment Leathers. AATCC Journal of Research, 1(6), 8–15. |
[18] | Iftikhar, F., Hussain, T., Malik, M.H., Ali, Z., Nazir, A. (2018) Fabric Structural Parameters Effect on Seam Efficiency-Effect of Woven Fabric Structural Parameters on Seam Efficiency. Journal of Textile Science and Engineering, 8(3), 358. |
[19] | Malcauskiene, E., Milasius, A. and Milasius, R. (2012) Influence of fabric structure parameters on seam slippage. Fibres and Textiles in Eastern Europe, 20, 98–101. |
[20] | ASTM D1683 / D1683M-17(2018), Standard Test Method for Failure in Sewn Seams of Woven Fabrics, ASTM International, West Conshohocken, PA. |