Harby E. Ahmed1, Mie Ishii2, Noriko Hayakawa3, Masahiko Tsukada4
1Department of Archaeology, Cairo University, Cairo, Egypt
2Faculty of Art and Regional Design, Saga University, Saga, Japan
3Tokyo National Institute for Cultural Property, Center for Conservation Science, Tokyo, Japan
4Department of Conservation, Graduate School of Fine Arts, Tokyo University of the Arts, Tokyo, Japan
Correspondence to: Mie Ishii, Faculty of Art and Regional Design, Saga University, Saga, Japan.
Email: |  |
Copyright © 2020 The Author(s). Published by Scientific & Academic Publishing.
This work is licensed under the Creative Commons Attribution International License (CC BY).
http://creativecommons.org/licenses/by/4.0/

Abstract
Poly(vinyl alcohol) (PVA) and poly(vinyl acetate) (PVAc) polymers have been used in the conservation of textiles for over 50 years. This study examines the physical and mechanical behavior of PVA- and PVAc- (Jade 403N) coated silk fabrics dyed with five type of natural dyes Japanese madder (Rubia akane L.), shikon (Lithospermum erythrorhizon L.), kihada (Philodendron amurense Rupr.), enjyu (Sophora japonica L.), and kariysu (Miscanthus tinctorius L). An ozone-producing UV lamp (8W X 2.GL8ZH. Sankyo Denki Co.) with an emission at 254 nm was used as the light source. The distance between the lamp and the samples was 28 cm, the duration of the exposure was 102 h. The fabric surfaces were photographed using a digital microscope (VHX-6000 Series Keyence, Japan) (×200) and an SEM (Hitachi SU-1500) (x 140, x 100). The surface color of the samples was measured with a spectrophotometer (CM-700d and CM-600dJ, Konika Minolta, Japan). The color difference was calculated according to CIELAB∆1E*. The tensile strength and elongation of the samples were measured using a universal material tester (Shimadzu universal tester S-500, Japan). The polymers are affected earlier than the silk fabric with exposure to light. The PVAc (Jade 403N) film showed the largest and the PVA film showed the least color difference among all the samples after UV irradiation. The color change pf the dyes has an effect on the optical appearance and that the dyes may disguise the overall discoloration caused by the polymer. Application of PVA and PVAc showed a decrease in tensile strength, which further decreased with UV irradiation. The results of this study showed that contrary to the intention, coating silk fabrics dyed with natural dyes with PVA and PVAc polymers does not exhibit stabilization as a conservation treatment, and when exposed to excessive light, the physical and chemical properties decrease further compared with that of the untreated silk fabric and the color change is influenced by the type to dyes. The common polymer treatment actually degrades the mechanical properties of the fabric. Historic textiles treated with PVA and PVAc need to be monitored and displayed under low levels of light and short duration. Careful consideration is necessary when applying PVA and PVAc to historic textiles as conservation treatments.
Keywords:
Polyvinyl alcohol, Polyvinyl acetate, Textile conservation, Tensile strength, Natural dyes, UV irradiation
Cite this paper: Harby E. Ahmed, Mie Ishii, Noriko Hayakawa, Masahiko Tsukada, Optical Characteristic and Tensile Strength of Silk Textiles Dyed with Natural Dyes Coated with PVA and PVAc Exposed to UV Light, International Journal of Textile Science, Vol. 9 No. 1, 2020, pp. 8-16. doi: 10.5923/j.textile.20200901.02.
1. Introduction
This study examines the physical and mechanical behavior of PVA- and PVAc- (Jade 403N) coated silk fabrics dyed with five type of natural dyes and assess its use as a conservation material for historic textiles. Polyvinyl alcohol (poly(1-hydroxy-ethylene; PVA) and polyvinyl acetate (poly(1-acetoxy-ethylene; PVAc) polymers have been used in the conservation of textiles for over 50 years, and the effects of the initial treatment have become an issue. In textile conservation laboratories, there have been reports of embrittlement, hardening, and the discoloration of adhesive coated textiles, and there are challenges in terms of issues related to retreatment and maintenance. Although there have been studies on the aging properties of PVA and PVAc alone, there is little information that explains the condition of these textiles. When textile conservators and scientists are consulted with historical textiles that appear to be coated with these polymers, they are asked about the state of these polymers over time, and how their conditions can be diagnosed, enabling the development of a plan of action for the next step in conservation. We believe that the degradation of these polymers on historic textiles cannot be explained only by the degradation mechanisum of the polymers alone, for which there are many studies, and that coating silk fabrics with these polymers is not “strengthening” the textile, contrary to the initial good intent with respect to the preservation of the textiles. In order to answer this question and hypothesis, we chose to experiment with PVA and PVAc (Jade 304N) because the former was used in treating historic textiles in Japan, and the latter is being used today in the conservation field, which is available from conservation suppliers. This study aims to give a better understanding of the effect of past treatments as well as to present information for decision making when considering the usefulness of PVAc on the conservation market. We chose to use standard silk plain weave fabric, and dyed them with natural dyes to mimic the fabric of historic Japanese kimonos. This approach was taken because this study is part of a series of experiments investigating the effect of PVA polymers used in conservation in Japan, notably in relation with studies by Okada and Hayakawa et al. [1] on PVA and PVA enzymes. The fragility of certain deteriorated fibers and textiles has caused particular conservation problems, and a range of adhesives has been applied in an attempts to enhance their long-term preservation. The aim is to hold together deteriorated fibers and thereby impart physical strength to yarns or textiles. In textile conservation, two methods are employed to apply adhesive polymers. The first is to use the polymer as a consolidant or coating that is applied in its liquid phase by brushing or spraying on the polymer and impregnating the fibers. [2] The second is to cast a fine film on the surface of an open membrane support, dry it, and then adhere it to the historical textile by means of heat or solvent activation of the polymer. [3]PVA is a water-soluble synthetic polymer with a chemical composition of (C2H4O)n, and it has a wide range of molecular weights. PVA has excellent film-forming, emulsifying, and adhesive properties. When dry, in the film form, it exhibits a high tensile strength and flexibility. Under high humidity, it absorbs water, which acts as a plasticizer, and the tensile strength will decrease. However, its elongation will increase. Because of these properties, PVA was one of the earliest synthetic polymers to be used for the treatment of historic textiles, which is done when fibers are degraded beyond stitching. The first reports appeared in 1956 from Germany [4] and 1957 from the Netherlands [5]. In 1961, Geijer, who was a Swedish pioneer in textile conservation, expresed doubts about its longtime effectiveness [6]. In Japan, Takage reported the use of PVA in 1951 as an adhesive for repairing crafts and works of art [7], and by the 1960’s, it was used in a spray form as a strengthening adhesive on the degraded silk fabric of historic kimonos [8]. The aging properties of PVA and PVAc in conservation were studied by Down et al. in 1996 and by Mori et al. in 2015 [9,10] However, the conservation community is more aware of the types of adhesives used than the effects of aging. A previous study on the light aging of PVA explains that the degradation of polymers is a result of oxidation processes involving free radicals and hydrolytic processes of an ionic type, and that the auto-oxidation process is caused by thermal or photochemical energy input [11]. It is known that the reduction in the tensile strength and elongation of the polymers results in an increase in the carbonyl peak (C==O) at 1730 cm-1, with a decrease of the hydroxyl peak at 3100– 3600 cm-1. In addition, the polymers exhibit hardness, decreased flexibility, and change in color due to long-term aging [12,13].We know that PVA hydrolyzes with accelerated light aging, and the redisssolving of aged polymers will involve washing in changes of hot water. In addition, the treatment is irreversible in practice [14]. PVAc is a water-soluble synthetic polymer with a chemical composition of (C4H6O2)n, and it also has a wide range of molecular weights. It exhibits flexibility, good formability, piezoelectric, pyroelectric, and ferroelectric properties, and it is prepared by the polymerization of vinyl acetate monomer. PVAc has been shown to be dissolvable from objects after more than 30-40 years. [15] In this study, we chose Jade 403N, which is a co-polymer with polyvinyl alcohol, and polyvinyl acetate with soap and polyacrylamide because it has been tested for use in conservation. Furthermore, it is currently available from conservation suppliers [16].
2. Experiment
2.1. Materials
Polyvinyl alcohol (MW: 1500-1800) in powder form was supplied by Wako Pure Chemical Industries, Japan. Jade 403N in solution form was supplied by PaRet, Japan. For dyed fabric samples, the plain weave silk (16 monme) that was used to test the fastness of the color was obtained from JIS L 0803. With respect to the dyes, Japanese madder (Rubia akane L.) dye was purchased from Kinnohitsuji, Japan, and shikon (Lithospermum erythrorhizon L.), kihada (Philodendron amurense Rupr.), enjyu (Sophora japonica L.), and kariysu (Miscanthus tinctorius L) dye were purchased from Tanaka Nao Senryo-ten., Japan. Alum (Al2(NH4)2(SO4)4.24H2O) mordant was purchased from Fluka, UK.
2.2. Sample Preparation
The dyeing process was performed in beakers. A liquor ratio (LR) of 1:50 was measured for both the dye and mordant bath. The dyeing of silk fabrics was carried out according to the following steps: 10 g of dye was soaked in 100 ml of distilled water for 12 h, and it was then heated to 90°C for 2 h with continuous stirring. Water was added to compensate for the evaporated water during the heating process. The extract was cooled and then filtered, resulting in a clear colored solution. The silk fabrics were soaked in the dye bath for 1.5 h with stirring, and the bath temperature was heated to approximately 90°C. With respect to the mordant bath, 0.5% (v/v) aqueous solution was prepared, and the silk fabric was immersed for 0.5 h with stirring at approximately 60°C. Then, the fabric was rinsed three times with cold water and dried.The PVA and PVAc polymers were applied to the silk fabrics as follows. To cast a polymer film, a polyester clear sheet was fixed on a flat surface of the tabletop and fixed to the table with masking tape on four sides. The adhesive was applied onto the casting bed by distributing evenly with a glass rod, rolling it over the masking tape along the sides of the rod to achieve a constant thickness. Then, it was left to dry after which the tapes were removed and the polymer film was peeled off. To apply the PVA and PVAc adhesive on the silk fabric samples, the polyester sheet was fixed to the tabletop with masking tape. In addition, the silk fabrics were fixed to the polyester sheet with masking tape. The adhesive was then applied onto the surface of silk samples, and was distributed evenly with a glass rod, after which it was left to dry. Finally, the silk samples were peeled off the polyester sheet. The fabric samples are shown in Figures. 1 and 2 and the list of samples are shown in Table 1 and 2.Table 1. CIEL *a*b* value of PVA Samples Before and After UV Irradiation 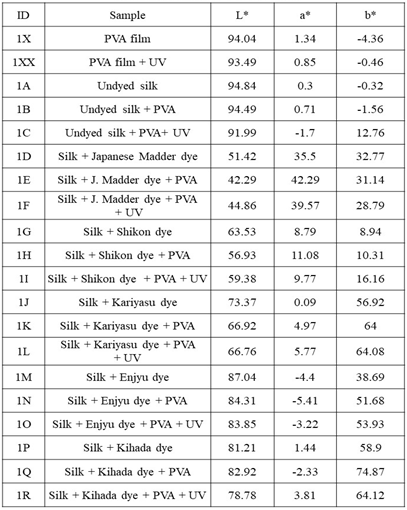 |
| |
|
Table 2. CIEL *a*b* value of PVAc Samples Before and After UV Irradiation 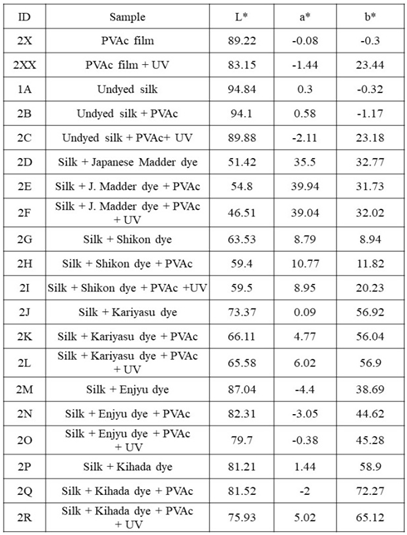 |
| |
|
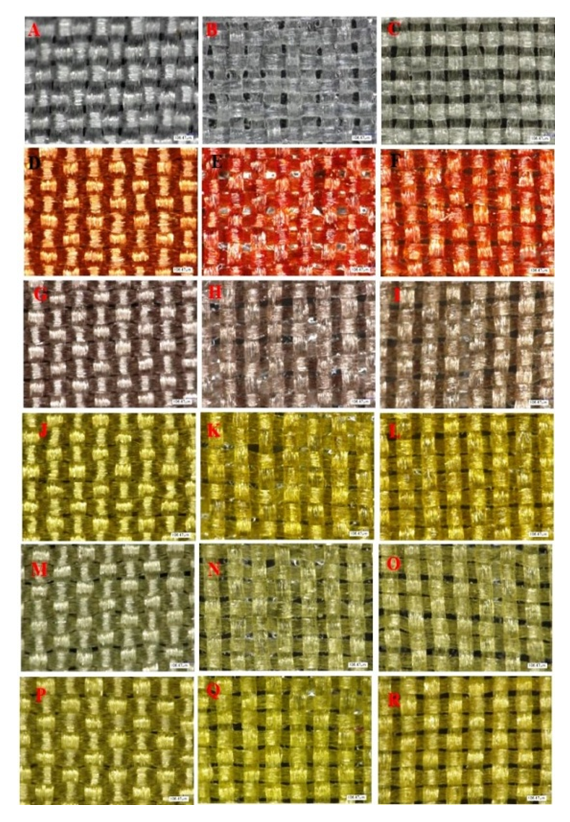 | Figure 1. PVA: Microphotograph of silk fabric samples before and after UV irradiation at a magnification of ×200. Left control without PVAc, centre with PVAc before UV aging, and right after aging. (A, B, C) undyed, (D, E, F) dyed with Japanese madder, (G, H, I) dyed with Shikon dye, (J, K, L) dyed with Kariysu dye, (M, N, O) dyed with Enjyu dye, (P, Q, R) dyed with Kihada dye |
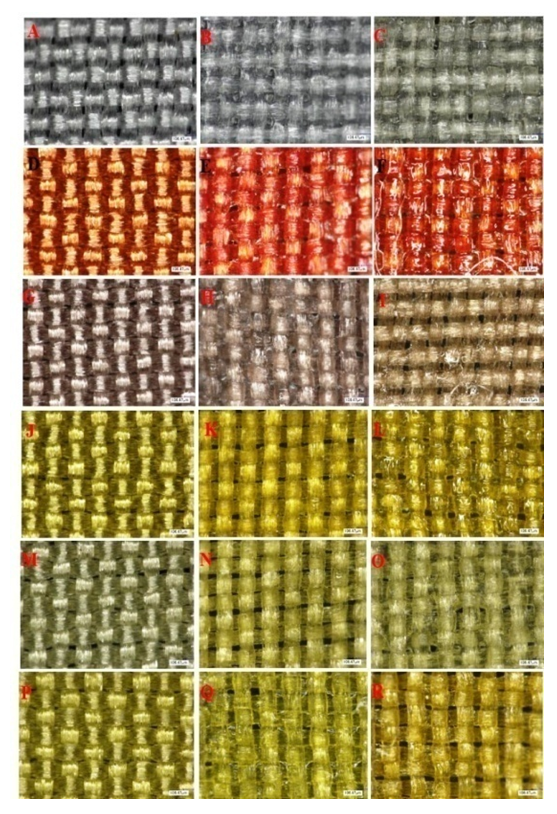 | Figure 2. PVAc (Jade 403N): Microphotograph of silk fabric samples before and after UV irradiation at a magnification of ×200. Left control without PVAc, centre with PVAc before UV aging, and right after aging. (A, B, C) undyed, (D, E, F) dyed with Japanese madder, (G, H, I) dyed with Shikon dye, (J, K, L) dyed with Kariysu dye, (M, N, O) dyed with Enjyu dye, (P, Q, R) dyed with Kihada dye |
The PVA and PVAc films were prepared as follows: a 10% solution (w/v) of PVA polymer powder in 100 ml distilled water was prepared in a beaker with continuous stirring. 20 ml of Jade 403N (1/1 v/v) was prepared using distilled water with continuous stirring.
2.3. Light Aging of Samples by UV Irradiation and Water Vapor Exposure
The aging process of the samples was conducted according to a previous study by Hayakawa et al. [17]. An ozone-producing UV lamp (8W X 2.GL8ZH. Sankyo Denki Co.) with a maximum emission at 254 nm and a minor emission at 185 nm was used as the light source. The distance between the lamp and the samples was 28 cm. The duration of the exposure was 102 h. The samples were exposed only on the adhesive coated side. After exposure, the samples were hung in a desiccator at around 80% RH for 3 h at ambient temperature to simulate the humidity-induced degradation, which causes the adhesives to turn slightly white. Finally, the samples were dried over silica gel in a desiccator.
3. Methods of Examination and Analysis
As the first step of the examination, the samples were examined visually and by touch, and were photographed using a digital camera and white fluorescent lamps (5000 K) before and after aging. Changes in color, surface appearances, flexibility, and hardness were observed, and the following instrumental examination was conducted.
3.1. Surface Morphological Examination
The changes of the fabric surface on a microscale were studied and photographed using a digital microscope (VHX-6000 Series Keyence, Japan) at a magnification of ×200. A scanning electron microscope (SEM) (Hitachi SU-1500) was also used to further examine the surface characteristics of the samples.
3.2. Color Measurement
The surface color of the samples was measured with a portable spectrophotometer (CM-700d and CM-600dJ, Konika Minolta, Japan). The CIE L*a*b* values were used for reading, and the color difference ∆E was calculated according to CIELAB∆1E*.
3.3. Mechanical Property
The tensile strength and elongation of the samples before and after aging were measured using a universal material tester (Shimadzu universal tester S-500, Japan) with reference to ASTM 2000, D 3822-96 at room temperature 22°C, 55% RH.
4. Results
4.1. Surface Morphological Examination
Figure. 1 (PVA) and Figure. 2 (PVAc) show microphotographs of samples without the application of polymers (left column), after the application (mid column), and after UV light aging (right column). Overall, after UV aging, PVA and PVAc feel hard and appear yellower. In Figure 1, with the application of PVA onto the silk samples, the polymer creates a coating on the surface of the yarns, and produces a clear film between the weave structures (see mid column of Figure. 1 and 2). It is clearly observed that the polymers have a sheen. After UV aging, the film between the weave structures disappears, and the sheen becomes less visible (right column). In Figure 2 with the application of PVAc, the optical appearance of the polymers is similar to that of PVA. From visual observation with a magnification of ×200 along, between PVA and PVAc, the type of polymer that is applied on the surface of the textile is not distinguishable. In both cases, from an optical perspective, the polymers appear to be affected earlier than the silk fabric. These observations will help the conservator to detect and diagnose degraded polymers during condition assessments.SEM images of silk fabrics coated with PVA (sample 1C) and PVAc (Jade 403N) (sample 2C) are as shown in Figures 3 and 4, respectively, before and after UV irradiation. The PVAc forms a uniform film over the weave structure compared with PVA. After UV irradiation, (B) PVA shows the formation of holes and irregularities on the polymer film, (D) PVAc shows wrinkles and cracks on the film, both indicating the physical micro-deformation of the polymer. | Figure 3. (A) SEM image of silk coated with PVA before aging (sample 1B), (B) SEM image of dyed silk coated with PVA, ×100 after UV irradiation (sample 1C) |
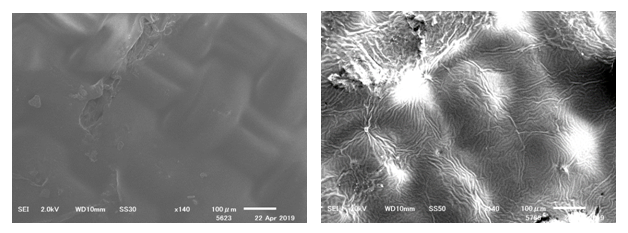 | Figure 4. (C) SEM image of silk coated with PVAc (Jade 403), x140 before UV ageing (sample 2B), (D) SEM image of silk coated by PVAc (Jade 403N), x140 after UV irradiation (sample 2C) |
4.2. Color Difference and Color Transition of Sample Fabrics Before and After Aging
Color measurements were taken three times and the average was calculated as show in Table 1 and Table 2. Color differences and transitions are shown in Figure. 5 and 6. The color difference The color difference (∆E) of control samples without PVA and with PVA after UV irradiation is as follows in the order of largeness (Figure 5a): Enjyu (15.61) > undyed silk (13.53) > Kariyasu (11.27) > Japanese madder (8.68) > Shikon (8.38) > Kihada (6.2) > PVA film (3.96).The color difference (∆E) of samples without PVAc and with PVAc after UV light irradiation is as follows in the order of largeness (Figure 5b): PVAc film (24.54) > Undyed silk (24.13) > Shikon (11.98) > Enjyu (10.65) > Kariyasu (9.79) Kihada (8.9) > Japanese madder (6.24).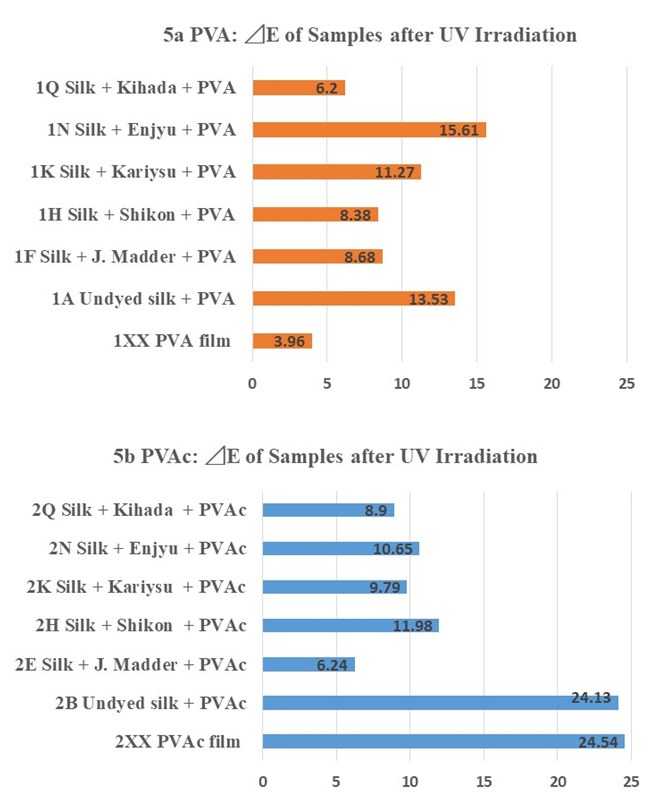 | Figure 5a-b. Color difference of PVA (5a) and PVAc (Jade 403N) |
PVA and PVAc film (Figure. 6a)The lightness of the PVA film was negligible (∆L* -0.55) but the yellowness increased slightly (∆b* -3.9). On the other hand, PVAc film showed darkening (∆L* -6.07) and a large increase in yellowness (∆b* -23.44). The darkening and yellowing of the PVAc film was noticeable by the naked eye and was confirmed by the measurements. Silk with PVA and PVAc (Figure. 6b)The lightness of the silk coated with PVA was unnoticeable (∆L*1.4), but became greener (∆a* -2.00) and yellower (∆b*12.44). PVAc showed darkening (∆L*4.96), negligible greenness (∆a*1.81) but a large increase in yellowness (∆b*26.38), which was in agreement with the PVAc film. There were added influences of the discoloration of the silk fabric in combination with the PVA and PVAc polymers which raised the rate of the values in all elements.Japanese madder on silk coated with PVA and PVAc (Figure. 6c)PVA caused darkness (∆L* -9.13) to the red color when coated. With UV irradiation, the color became lighter (∆L* 2.57) and there was an increase in the red (∆a*2.72) and in the yellow coordinates (∆b* 2.35). PVAc caused lightness (∆L* 3.38) to the red color when coated. With UV irradiation, the color became lighter (∆L* 8.29) but the changes in the red and yellow coordinates were negligible (<1). PVA changed the surface color of Japanese madder more than the PVAc after application of the polymers. With UV irradiation, the colors of the PVA and the PVAc became redder which was noticeable with optical examination. The main coloring compound of Japanese madder is purpurin and the noticeable lightness is possibly caused by its fading. Shikon dye on silk with PVA and PVAc (Figure. 6d)The color change of shikon (main compound shikonin) dyed sample with the application of the PVA and PVAc polymers showed the leased color shifts among the dyed samples before and after UV irradiation. PVA showed lightning (∆L* 2.45) and a small change in the redness (∆a*1.31) and a slight increase in the yellowness (∆b* 5.85). PVAc showed negligible change in the lightness and the yellowness, and very small change in redness (∆a*1.82).Kariysu dye coated with PVA and PVAc (Figure. 6e)PVA caused darkness (∆L* 6.45) to the yellow color and increased the redness (∆a*4.88) and the yellowness (∆b* 7.08) when coated. With UV irradiation, the lightness, redness and yellowness showed only a small change (> 1). PVAc caused darkness (∆L* 7.26) to the yellow color and increased in the redness (∆a*4.68) but the yellowness was negligible when coated. With UV irradiation, the lightness, redness, and yellowness was negligible (> 1.3).The main color compound of kariyasu is luteolin. The largest color change occurred when the polymers coated the surface of the dyed silk fabric. The discoloration caused by UV irradiation appeared small, possibly “disguised” by the overlapping yellowing color of the polymers and the yellow color of the dye. Enjyu dye on silk coated with PVA and PVAc (Figure. 6f)PVA caused darkness (∆L* 2.73) to the yellow-green color when coated. With UV irradiation, the change in lightness was negligible, and there was a small change in the green (∆a*2.19) and a small increase in the yellow (∆b* 2.27) coordinates. PVAc caused lightness (∆L* 4.73) when coated. With UV irradiation, the color became darker (∆L* 2.61), and there was a small change in the green (∆a*2.67), and a negligible change in the yellow. The main color compound of enjyu is rutin. The effect of the UV irradiation in combination with the polymers had a larger effect on the PVAc than the PVA. Kihada dye coated with PVA and PVAc (Figure. 6g)PVA caused lightness (∆L* 1.71), and the greenness (∆a*3.47) and the yellowness (∆b* 15.91) increased the yellow color when coated. With UV irradiation, the increase of the lightness was noticeable (∆L* 4.14) and the redness increased (∆a*6.44) but the yellowness decreased (∆b* 10.75). PVAc caused negligible lightness, and the greenness (∆a*3.44) and the yellowness (∆b* 13.37) increased the yellow color when coated. With UV irradiation, the increase of lightness was noticeable (∆L* 5.59) and the redness increased (∆a*6.44) but the yellowness decreased (∆b* 7.15).The main coloring compound of kihada is berberin which is known to darken upon light exposure. [19] The color shift appears to be a combination of the yellowing of the polymer and darkening of the dye. 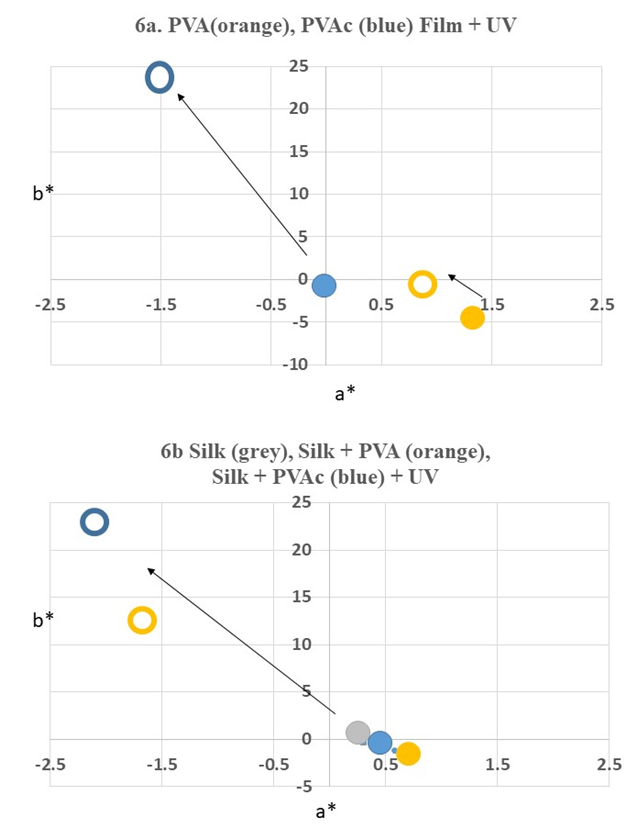 | Figure 6a-b. Color transition of PVA and PVAc (Jade 403N) films and undyed silk samples coated with and without polymers before and after UV irradiation. Notation: a*=red (+) – green (-), b*= yellow (+)-blue (-), ● before irradiation, ○ after irradiation |
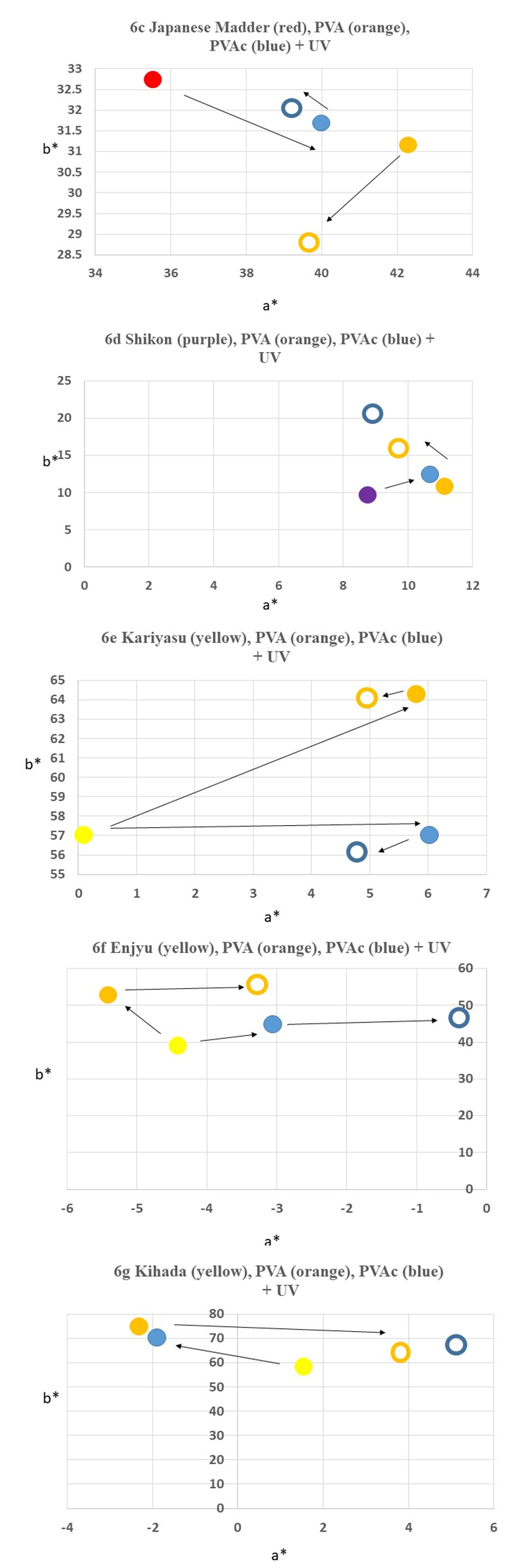 | Figure 6c-g. Color transition of PVA and PVAc (Jade 403N) films and undyed silk samples coated with and without polymers before and after UV irradiation. Notation: a*=red (+) – green (-), b*= yellow (+)-blue (-), ● before irradiation, ○ after irradiation |
EvaluationOverall, the PVAc (Jade 403N) film showed the largest color difference among the samples after UV irradiation. The PVA film showed the least color difference among the samples after UV irradiation. The average color difference of the dyed fabrics with PVA was ∆E 10.00 and PVAc was ∆E 9.5 which suggests that despite the large color differences of the polymer films, the color difference rate of the dyed silk samples was almost equal. This indicated that the color change of the dyes has an effect on the surface color after UV irradiation, and that the dyes may ‘disguise’ the discoloration of the polymers, especially when the PVAc is applied to a silk fabric with a yellow dye such as kariyasu which is known to lose its chroma with light. [20] Its main coloring compound is luteolin which is a flavonoid common to many natural yellow dyes, such as the Weld (Reseda Luteora. L.) common in Europe.When the fabric is dyed, for some dye groups, the color change of the silk fiber blends in with the dyed color, making the color difference smaller; alternatively, when the dyes fade or become significantly discolored by light, the color difference becomes greater. Overall, upon exposure to UV light, the color change of silk fabrics dyed with natural dyes is more influenced by the type of dye rather than the applied PVA.
4.3. Mechanical Properties of Undyed Sample Fabrics
Figure 7 shows the tensile strength (N) and elongation (mm) of undyed silk fabric coated with PAV and PVAc before and after aging. Three samples were tested and the average was calculated. The tensile strength of undyed silk decreased from 198.29 to 192.16 N, and the elongation increased from 11.56 to 12.48 mm after aging. There was a decrease in the tensile strength of the aged silk fabric when the elongation increased. The tensile strength of silk coated with PVA decreased from 129.89 N to 91.36 N and the elongation decreased from 7.55 to 6.2 mm after aging. The results show a large decrease in the tensile strength and elongation of silk coated with PVA after aging. The tensile strength of the silk coated with PVAc decreased from 121.4 to 77.89 N, and the elongation decreased from 9.42 to 6.42 mm. The results show a large decrease in tensile strength and elongation of the silk coated with PVAc after aging. The undyed silk fabric shows a decrease in tensile strength and an increase in the elongation, indicating that after light aging, it is susceptible to tearing. Overall, both PVA- and PVAc-coated silk fabrics showed a decrease in tensile strength, meaning that coating with these polymers does not substitute for the tensile strength and elongation properties of silk textiles. This means that despite the initial intent to “strengthen the fibers” with the application of these polymers in textile conservation, the treatment in fact has the opposite effect.Previous studies have reported the reduction of the mechanical properties of the PVA polymer with accelerated aging [21,22]. Our study adds information on the aging effect of polymers that are used in textile conservation in combination with silk textiles.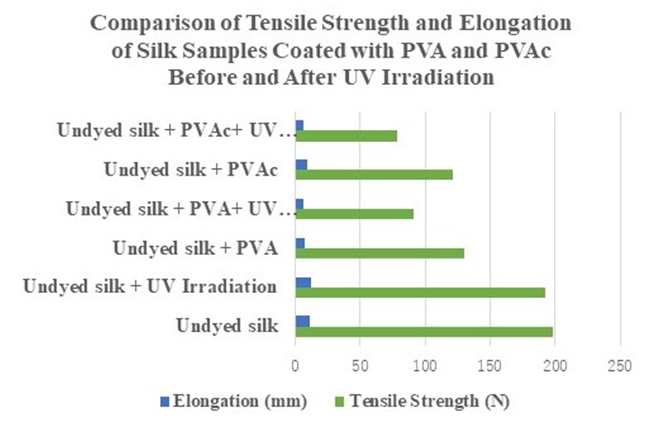 | Figure 7. Comparison of tensile strength and elongation of silk samples coated with PVA and PVAc (Jade 403N) after UV irradiation |
5. Conclusions
In response to the questions “What is the state of PVA- and PVAc-treated textiles over time? and “How can we diagnose its condition so that we can plan an action for the next step in conservation?,” our hypothesis was that the degradation of these polymers on historic textiles cannot be explained only by the degradation mechanism of these polymers alone, and that there exist more complex physical and chemical mechanims. In conlusion, we have found these results:1. Under a magnification of ×200 with a digital microscope, PVA and PVAc, whether it is aged or not, is not distinguishable on the surface of the silk textile. In both cases, from an optical perspective, the polymers loose sheen and film properties, and are affected earlier than the silk fabric with exposure to UV light. These observations indicate that the application of PVA and PVAc polymers to historic silk textiles for treatment will physically change before the silk itself. This contradicts the intent of the conservation treatment, and explains why many past PVA-treated textiles employed in the 1950’s–60’s are currently in need of conservation attention.2. SEM images showed that PVAc formed a more uniform film compared with PVA. Both polymers showed micro-deformation such as wrinkles and cracks of the films after light aging. 3. When PVA and PVAc polymers are applied to the silk fabric, dyed or undyed, the surface color changes. After UV irradiation, the color transition is obvious by optical examination and is confirmed by instrumental measurement. When considering new applications of PVA and PVAc to dyed silk textiles, it is advisable to take color measurements before application and keep a record within the institution as an activity of conservation management. 4. The PVAc (Jade 403N) film showed the largest color difference. The PVA film showed the least color difference among all the samples after UV irradiation. There were added influences of the discoloration of the silk fabric in combination with the PVA and PVAc polymers which raised the rate of the values in all three elements of measurements. However, despite the large color differences of the polymer films, the color difference rate of the dyed samples was almost equal. This indicates that the color change of the dyes has an effect on the optical appearance, and that the dyes may ‘disguise’ the overall discoloration.5. By measuring the surface color of dyed samples, with and without PVA and PVAc coatings and both before and after UV light aging, overall, upon exposure to UV light, the color change of silk fabrics dyed with Japanese madder (Rubia akane L.), shikon (Lithospermum erythrorhizon L.), kihada (Philodendron amurense Rupr.), enjyu (Sophora japonica L.), and kariysu (Miscanthus tinctorius L) are more influenced by the dye type rather than the applied PVA or PVAc coating. 6. Measuring the mechanical properties of undyed silk samples, with and without PVA and PVAc coatings both before and after UV light aging, the coated silk fabrics showed a decrease in tensile strength, which further decreased with UV aging, meaning that these polymers do not substitute for the tensile strength and elongation properties of silk textiles. This means that despite the intent to “strengthen the fibers” with the application of these polymers in conservation treatments, this in fact has the opposite effect by reducing the strength of the fibers. This study shows that contrary to the intention, coating silk fabrics dyed with natural dyes with PVA and PVAc polymers does not exhibit stabilization as a conservation treatment, and when exposed to excessive light, the physical and chemical properties decrease further compared with that of the untreated silk fabric. Historic textiles treated with PVA and PVAc need to be monitored and displayed under low levels of light and short duration. [22,23] Careful consideration is necessary when considering application of new PVAc to historic silk textiles although it is available from conservation suppliers. We hope that this study will answer some of the questions on the condition, aid the diagnosis of textiles treated with PVA and PVAc, and will contribute to decision making for the next step in conservation treatments.
ACKNOWLEDGEMENTS
This work was supported by the Japan Society for the Promotion of Science (JSPS) Fellowship ID: L18557 (Harby E. Ahmed) and JSPS Grant-in-aid for Scientific Research (B) 16H03099 (Masahiko Tsukada) and JSPC Grant-in-aid for Scientific Research (C) 19K01127 (Mie Ishii). Furthermore, we express gratitude to Mikio Maseda and Yuko Tokuyama, Kanae Mori of The Analytical Research Center for Experimental Sciences, Saga University, and Satoshi Morita from Konica Minolta Japan, Inc., and Enjoji Takashi from the Saga Technology Center, Japan, and Dr. Asmaa Mohamoud Mohamed of Egyptian National Research Center.
References
[1] | Y. Okada, W. Kawanobe, and N. Hayakawa, et al., “A mechanism for ultraviolet light irradiation-induced whitening of poly (vinyl alcohol) film”. Materiaru Raifu Gakkaishi, vol. 24(1), pp. 27-33, 2012. |
[2] | Á. Tímár-Balázsy and D. Eastop, Chemical Principles of Textile Conservation. London: Butterworth-Heinemann, 1998, pp. 304-331. |
[3] | S. Landi, “Three examples of textile conservation in the Victoria and Albert Museum,” Studies in Conservation, vol. 11(3), pp. 143-139, 1966. |
[4] | S. Mueller-Christensen, “Textilrestaurierung,” Bericht des Bayerischen Landesamtes für Denkmalpflege, vol. 15, pp. 63-71, 1957. |
[5] | R. Sieders, J. W. H. Uytenbogaart, and J. E. Leene, “The restoration and preservation of old fabrics: A new method of mounting on a rigid backing,” Studies in Conservation, vol. 2(4), pp. 161-169, 1956. |
[6] | Á. Geijer, “Dangerous methods for conservation of textiles,” Bulletin de Liasion du entre International d’Étude des Textile Anciens, vol. 13, pp. 19-26, 1961. |
[7] | S. Takaage, “Application of synthetic resins to the preservation of antiques and art crafts,” Kobunkazai no kagaku, vol. 1, pp. 25-26, 1951. (In Japanese) |
[8] | S. Kawakami, “Senshoku-hin no syūri (Repair of textiles),” Nihon no bijyutu, vol. 435, p. 48, 2004. (In Japanese) |
[9] | J. L. Down, et al., “Adhesive testing at the Canadian Conservation Institute - an evaluation of selected poly (vinyl acetate) and acrylic adhesives,” Studies in Conservation, vol. 41(1), pp. 19-44, 1996. |
[10] | Y. Mori, et al., “Ultraviolet degradation of poly (vinyl alcohol) used in restoration of historical and cultural properties,” Polymer Degradation and Stability, vol. 114, pp. 30-36, 2015. |
[11] | S, Wei, V. Pintus and M. Schreoner, “Photochemical and degradation study of polyvinyl acetate paints used in artworks by Py–GC/MS,” J. Analytical and Applied Pyrolysis, vol. 97, pp. 158-163, 2012. |
[12] | Y. Zhang and L.Ye, “Structure and property of polyvinyl alcohol/precipitated silica composite hydrogels for microorganism immobilization,” Engineering, vol. 46, pp. 746-755, 2014. |
[13] | L. Masschelein-Kleiner and E. Bergiers, “Influence of adhesives on the conservation of textiles,” Studies in Conservation, vol. 29(1), pp. 70-73, 1984. |
[14] | C. V. Horie, Materials for Conservation: Organic Consolidants, Adhesives and Coatings. London: Routledge, 2010, p. 145. |
[15] | Note 14 (Horie) p. 137. |
[16] | Note 9 (Down). |
[17] | N. Hayakawa, K. Sakai, and K. Kida et al., “ Effectiveness of PVA-fegrading enzymes against deteriorated polyvinyl alcohol (PVA) in the conservation of Japanese paintings,” Bunkazai Hozon-Syuhuku Gakkaishi, vol. 56, pp. 27-36, 2013. (In Japanese) |
[18] | T. Gaaz, et al., “Properties and applications of polyvinyl alcohol, halloysite nanotubes and their nanocomposites. Molecules,” vol. 20(2), pp. 22833-22847, 2015. |
[19] | M. Ishii, and M. Saito, “Yellow dyes in Japanese kimono,” Scientific Analysis of Ancient and Historic Textiles: Informing Preservation, Display and Interpretation: Postprints, pp. 258-266, 2005. London: Archetype. |
[20] | M. Ishii,. and M. Saito, “Fading behavior of natural yellow dyes and the maintenance of Japanese yellow kosode,” Bunkazai Hozon-Syuhuku Gakkaishi, vol. 51, pp. 14-37, 2006. (In Japanese) |
[21] | T. Madera-Santana, Y. Freile-Pelegrín, and J. Azamar-Barrios, “Physicochemical and morphological properties of plasticized poly (vinyl alcohol)–agar biodegradable films,” International Journal of Biological Macromolecules, vol. 69, pp. 760-184, 2014. |
[22] | M. Ishii, K. Kohmoto and M. Saito. “Color degradation of textiles with natural yellow dyes under exhibition lighting and evaluation of CIE standard of museum lighting,” Journal of the Illuminating Institute of Japan, vol. 90 (5), pp. 281-287, 2006. |
[23] | M. Ishii, T. Moriyama, M. Toda, K. Kohmoto and M. Saito. “Color degradation of textiles with natura dyes and blue scale standard exposed to white LED lamps: evaluation for effectiveness as musuem lighting,” Journal of Light and Visual Environment, vol. 32 (4), pp. 30-38, 2008. |