Shaima Islam, Joyjit Ghosh, Nahida Akter
Department of Textile Engineering, Ahsanullah University of Science and Technology, Dhaka, Bangladesh
Correspondence to: Joyjit Ghosh, Department of Textile Engineering, Ahsanullah University of Science and Technology, Dhaka, Bangladesh.
Email: |  |
Copyright © 2020 The Author(s). Published by Scientific & Academic Publishing.
This work is licensed under the Creative Commons Attribution International License (CC BY).
http://creativecommons.org/licenses/by/4.0/

Abstract
In this research work, an attempt was made to increase the crease resistant property of silk fabrics by using citric acid and dimethylol dihydroxy ethylene urea (DMDHEU) as crosslinking agents. Variables were curing time, curing temperature, concentration of catalysts and crosslinking agents. Sodium hypophosphite (NaPO2H2) and magnesium chloride (MgCl2) were used as catalyst for citric acid and DMDHEU respectively and silicone was used as softener. The properties of the treated fabrics like crease recovery angle (CRA), whiteness index, tensile strength, tear strength and stiffness were measured and compared with the untreated fabric. The results report that 150°C curing temperature and 2 minutes curing time is suitable for both citric acid and DMDHEU as with increasing curing temperature and time whiteness index reduces (around 23% in case of citric acid and 27.55% in case of DMDHEU). Samples treated with dimethylol dihydroxy ethylene urea (DMDHEU) shows better crease recovery angle (up to 189°) than citric acid (up to 161°). The finished fabrics treated with citric acid retained 81.51% to 99.81% breaking strength and there was an increase in its tear strength (up to 121%). On the other hand, the finished fabric treated with dimethylol dihydroxy ethylene urea (DMDHEU) retained 82.12% to 97.89% breaking strength and showed maximum tear strength retention (%) of 123%. The drape co-efficient of fabrics treated with both finishing agents were increased significantly.
Keywords:
Silk Fibre, Crosslinking Agent, Citric Acid, Dimethylol di hydroxyl ethylene urea (DMDHEU)
Cite this paper: Shaima Islam, Joyjit Ghosh, Nahida Akter, Comparative Study on Crease Recovery Finishing of Silk Fabric with Citric Acid and Dimethylol Dihydroxy Ethylene Urea (DMDHEU) as Finishing Agent, International Journal of Textile Science, Vol. 9 No. 1, 2020, pp. 1-7. doi: 10.5923/j.textile.20200901.01.
1. Introduction
Silk is one of the oldest fibres known to man. It is an animal fibre produced by certain insects to build their cocoons and webs. Although many insects produce silk, only the filament produced by the mulberry silk moth bombyx mori and a few others in the same genus is used by the commercial silk industry [1]. Textile silk from the moth bombyx mori has a much simpler protein composition. There is no cystine to crosslink chains. About 80% consists of amino-acid residues with the three simplest side-groups, –H, –CH3 and –CH2OH [2]. It is the world’s most favored textile materials and has been known as the ‘queen of fibers’ since its discovery. Fabric made from silk fibre are manifestly luxurious and have many excellent qualities including luster, wearing comfort, soft handle, good air permeability, excellent draping quality [3]. Silk is produced in small quantities: about 130,000 tons per year and has remained a special fiber for the human skin, hence it can also be used in biomedical applications such as sutures, prosthetic arteries and bandages. Silk fabric has the tendency to crease easily during home laundering or when wet. This disadvantage causes considerable inconvenience in the use of silk textiles, and world consumption of silk is directly influenced [4]. Therefore modifying the properties of silk and expanding its new uses have attracted great attention in the world. The main reasons for the formation of creases are the low crystallinity and high void content of silk fibroin, and the large number of hydrogen bonds and salt bonds between the silk fibers. Under an external force, the silk fibers can slip and form hydrogen bonds in new positions. When the external force is removed, the fibers do not recover completely, resulting in crease formation. Crease-resistant finishes function by filling the amorphous regions with resin and inducing chemical crosslinking to prevent the silk fibers from slipping [5]. Unlike wool keratin, silk fibroin has no cysteine residue, so that there are no chemical cross linkages between the protein polymers. When the fiber absorbs water and swells, the salt linkages between polymers, which give the fiber high crease recovery property, are broken. Adding chemical cross linkages to the structure restricts the relative movement of the polymers of silk fiber; therefore the crease recovery property of silk can be improved [6]. A considerable amount of work has been carried out on the chemical modification of silk with a view to improve its crease resistance property. P.K. Hari, M.L. Gulrajani and N.K. Pal studied to improve the crease recovery of silk fabrics, dimehylol ethylene urea (DMEU) was applied to control, photo-graded and esterified silk fabrics [7]. Z. Cai and G. Jing and S. Yang used an epoxy silicone cross-linking agent (EPSIA) to enhance the performance properties, especially crease resistance of silk fabrics [2].A number of formaldehyde based cross linking agents is available to improve the creasing property of silk fabric due to wet treatment. The release of formaldehyde vapors is a problem with those agents. The most likely used cross linking agents are N- Methylol or N- Methyl amides because of their efficiency and low price. Formaldehyde free cross linking agents for producing crease resistant properties are of interest to replace N-methylol compounds. Polycarboxylic acids are non-formaldehyde based reactants. The main advantage of using polycaboxylic acids is that they are formaldehyde free, do not have bad odor, and produce very soft fabric hand [8].The aim of this study is to bring a comparison between crease resistant properties of formaldehyde and non-formaldehyde based crosslinking agent. For this purpose, citric acid and dimethylol dihydroxy ethylene urea (DMDHEU) are used as crosslinking agents. The effectiveness of DMDHEU is based on its two methylol groups, which releases free formaldehyde vapor from treated fabrics during industrial production and home treatments such as laundering and ironing. The ether linkages of DMDHEU gradually hydrolyze to become N-methylol groups. Consequently free formaldehyde is released continuously during the entire life of the finished garment [9]. The compounds with three or four carboxyl groups are the most effective crosslinking agents, and sodium hypophosphite is the best catalyst. Since the prices of the tetra-carboxylic acids, such as 1, 2, 3, 4,-butanetetracarboxylic acid (BTCA) and cyclo pentane tetra carboxylic acid, are relatively high, their popularity is limited [6]. It seems reasonable to consider citric acid as a lower priced substitute to the tetra carboxylic acids.
2. Materials and Methods
2.1. Materials
FabricThe fishing treatments were carried out on raw silk fabric purchased from a local silk market. The construction properties of fabric include the followings: warp count 22 Denier, weft count 27 Denier, ends per cm 130, picks per cm 120 and fabric weight 24 g/m2.ChemicalsThe crosslinking agents used were citric acid and dimethylol dihydroxy ethylene urea (DMDHEU). Sodium hypophosphite (NaPO2H2) and magnesium chloride (MgCl2) were used as catalyst for citric acid and DMDHEU respectively and silicone softener was used as softening agent.
2.2. Experimental Methods
At first, the degummed silk fabric was treated with (DMDHEU) and citric acid according to recipe given on the Table 1 and Table 2 respectively varying curing time and temperature given on Table 3. Here total 40 samples (20 treated with DMDHEU & 20 treated with citric acid) were treated and analyzing the test results suitable curing time and temperatures were fixed. Then varying the concentration of (DMDHEU), citric acid and catalysts given on Table 4, again 24 (12 treated with DMDHEU and 12 with citric acid) samples were treated to find out the suitable concentration of catalyst and finishing agents. Other finishing parameters were given on Table 5.Table 1. Recipe of Finishing with DMDHEU & Softener 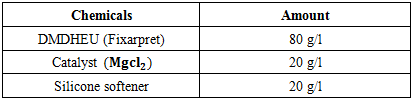 |
| |
|
Table 2. Recipe of Finishing with Citric Acid and Softener 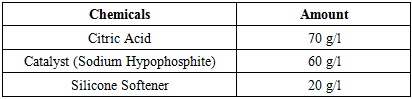 |
| |
|
Table 3. Variation in Curing Time and Temperature 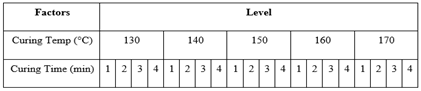 |
| |
|
Table 4. Recipe of Finishing with Different Concentration of Cross-linking Agents and Catalysts 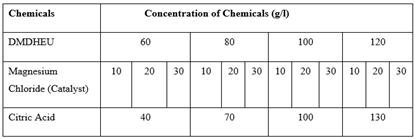 |
| |
|
Table 5. Other Finishing Parameters 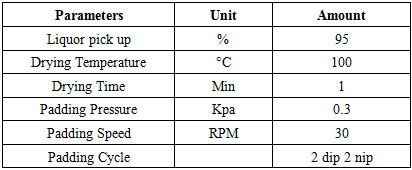 |
| |
|
2.3. Testing Methods
Crease recovery is a measure of crease resistance, specified quantitatively in terms of the crease recovery angle (CRA). The CRA of both untreated and treated fabric specimens were measured by using the standard method of ISO 2313-1972. Tear strength of fabrics using ballistic pendulum was done by following test method: ISO 13937-1:2000. The tensile strength of the silk fabric specimen was measured according to the standard method of ASTM D 5035-2014 by using a tensile testing machine (Titan Universal Strength Tester). Whiteness Index of the treated sample was measured according to the test method of AATCC 110-2000 and drape co-efficient was measured by following the test method of BS 5058.
3. Results and Discussions
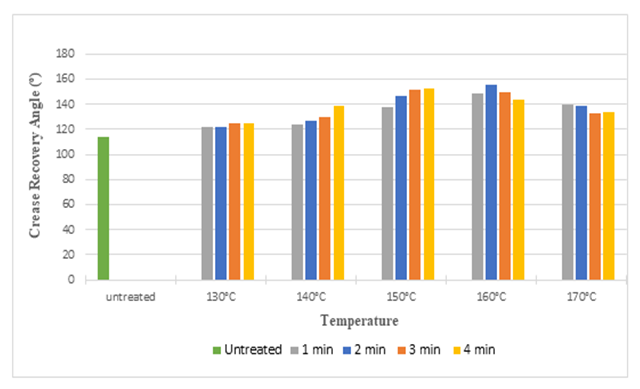 | Figure 1. Crease Recovery Angel of Silk Fabric at Different Curing Time and Temperatures after Citric Acid Treatment |
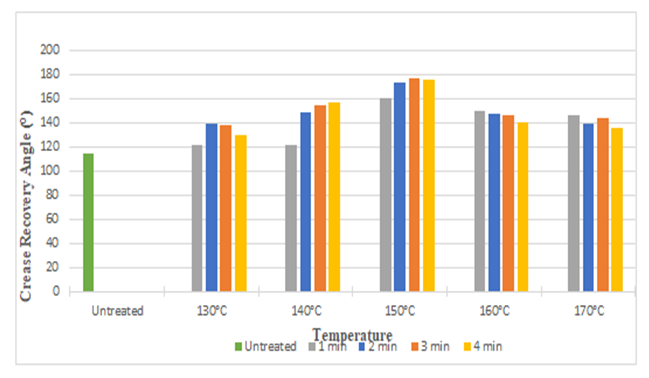 | Figure 2. Crease Recovery Angel of Silk Fabric at Different Curing Time and Temperatures after DMDHEU Treatment |
The above bar diagrams illustrates that, after treating silk fabric with citric acid and DMDHEU the crease recovery angle increased from 114° to 156° and 114° to 177° respectively. It may be due to the fact that crosslinking agent produced crosslinks among fibroin molecules of the silk and masked the free hydroxyl side groups, which in turn improved the crease resistant properties of treated fabrics. With increasing time and temperature crease recovery angle increased up to 150°C (with few exception) and then start to decrease, it may be due to inadequate degree of crosslinking at higher curing time and temperature.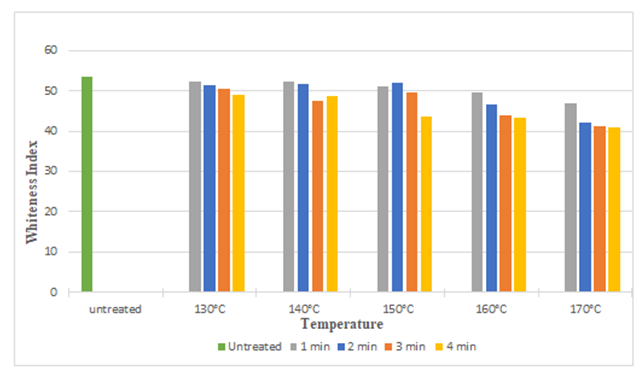 | Figure 3. Whiteness Index of Silk Fabric at Different Curing Time and Temperatures after Citric Acid Treatment |
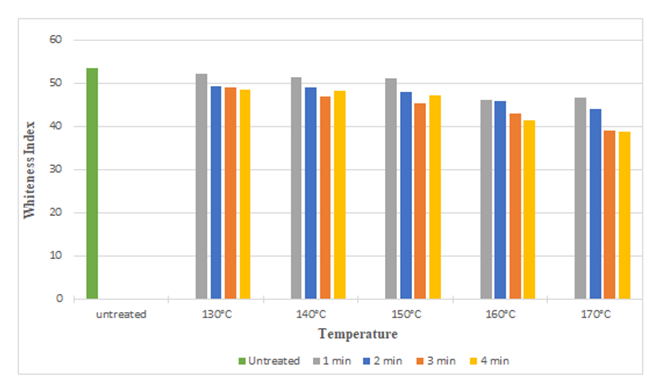 | Figure 4. Whiteness Index of Silk Fabric at Different Curing Time and Temperatures after DMDHEU Treatment |
The diagrams illustrates the whiteness index of samples treated with citric acid and DMDHE. Whiteness index decreased with increasing curing time and temperature from 53.45 to 40.92 (around 23%) and 53.45 to 38.72 (around 27.55%) respectively. Lowest whiteness index was found at the curing temperature of 170° C and at curing time of 4 min.Figure 5 and Figure 6 illustrates the tear strength retention (%) in warp and weft direction after citric acid treatment. With increasing curing time and temperature tear strength retention (%) slightly increases (up to 115%). Figure 7 and Figure 8 illustrates the tear strength retention (%) in warp and weft direction after DMDHEU treatment. With increasing curing time and temperature tear strength retention (%) slightly increases (up to 119%). The addition of softeners is probably the major reason for the increase in tear strength and its retention (%).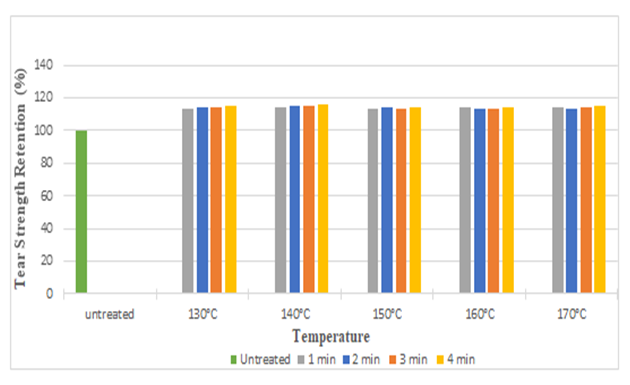 | Figure 5. Tear Strength Retention (%) in Warp Direction at Different Curing Time and Temperature after Citric Acid Treatment |
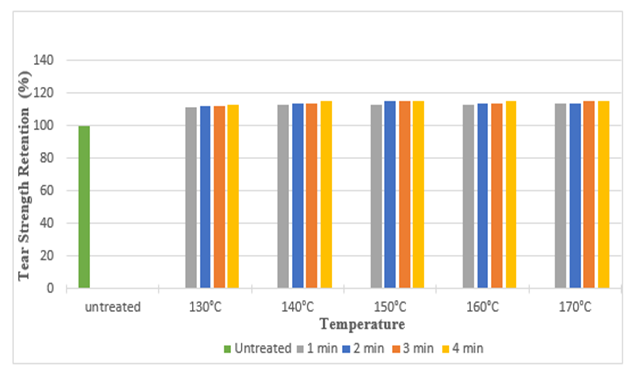 | Figure 6. Tear Strength Retention (%) in Weft Direction at Different Curing Time and Temperatures after Citric Acid Treatment |
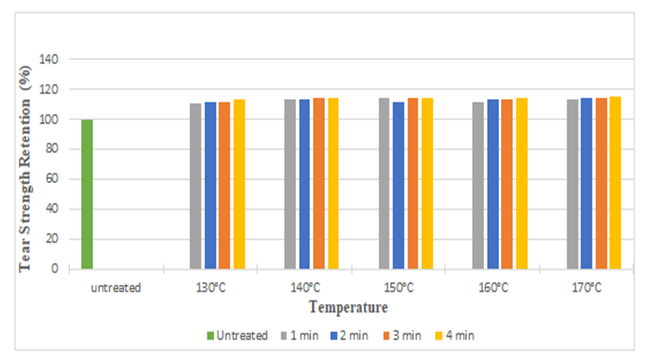 | Figure 7. Tear Strength Retention (%) in Warp Direction at Different Curing Time and Temperatures after DMDHEU Treatment |
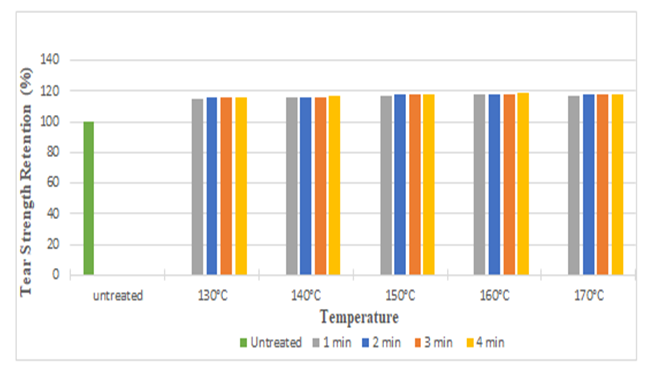 | Figure 8. Tear Strength Retention (%) in Weft Direction at Different Curing Time and Temperatures after DMDHEU Treatment |
The tensile strength retention (%) of silk fabric in warp and weft direction after citric acid treatment is depicted in the Figure 9 and Figure 10. No doubt, substantial strength retention was found after the treatment. We found approximately strength loss of 14% in warp direction and 12% in weft direction at the highest curing temperature (170°C). It can be noted that, with the increase in curing time and temperature, the tensile strength as well as strength retention (%) decreased. It may be due to the acidity of the treatment solution and acid catalyzed depolymerization (partial hydrolysis of silk protein) during the curing process, especially at high curing temperature.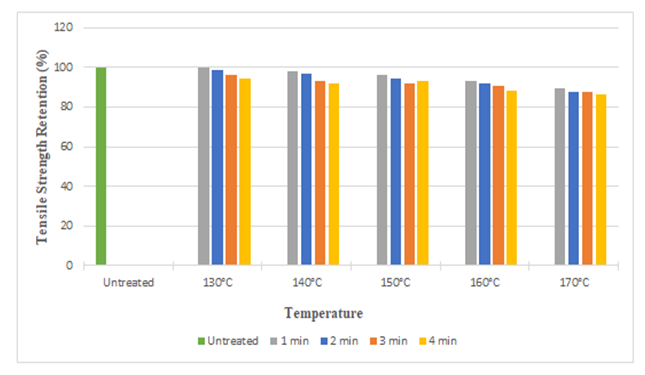 | Figure 9. Tensile Strength Retention (%) in Warp Direction at Different Curing Time and Temperatures after Citric Acid Treatment |
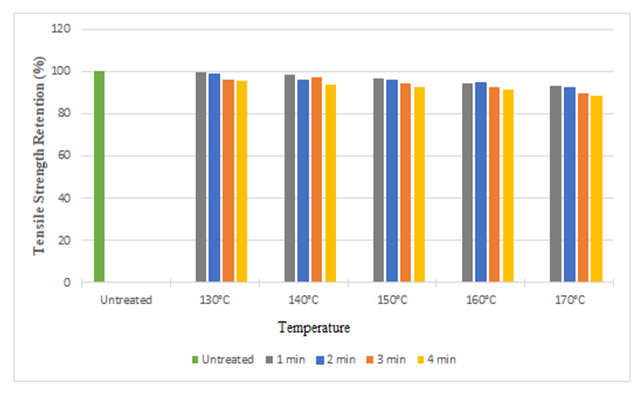 | Figure 10. Tensile Strength Retention (%) in Weft Direction at Different Curing Time and Temperatures after Citric Acid Treatment |
The tensile strength retention (%) of silk fabric in warp and weft direction after DMDHEU treatment is depicted in the Figure 11 and Figure 12. It shows approximately a strength loss of 16% in warp direction and 11% in weft direction at the highest curing temperature (170°C). It can be noted that, with increase in curing time and temperature, the tensile strength as well as strength retention (%) decreased.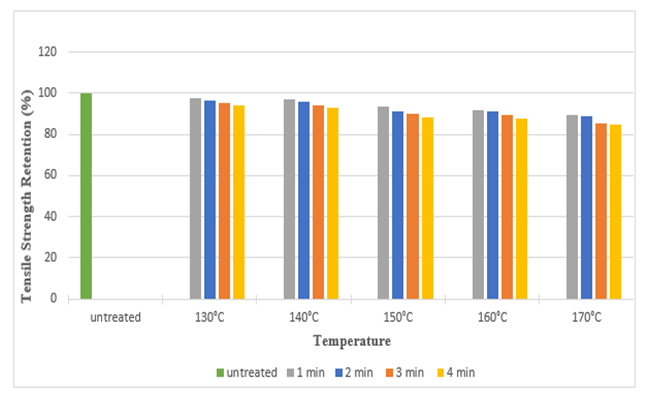 | Figure 11. Tensile Strength Retention (%) in Warp Direction at Different Curing Time and Temperatures after DMDHEU Treatment |
 | Figure 12. Tensile Strength Retention (%) in Weft direction at Different Curing Time and Temperatures after DMDHEU Treatment |
Figure 13 and Figure 14 indicates that with the increase in concentration of citric acid, the crease recovery angle (CRA) increased up to 161° (around 41%) and whiteness index decreased up to 37.63 (around 29.59 %). This was due to the increase in the cross-linkages between silk polymer molecules. However, when the concentration was too high, the finishing agent reacted too severely with the fibre and formed a thick layer on the surface of the fabric which reduces the whiteness of the silk fabric. Highest crease recovery angle (CRA) was found at the concentration of 130 g/l for citric acid and at the concentration of 70 g/l for catalyst (Sodium Hypophosphite) whereas at that concentration whiteness index was lowest. It can also be seen from the graph that the effect of catalysts on crease recovery angle (CRA) and whiteness was not that much significant.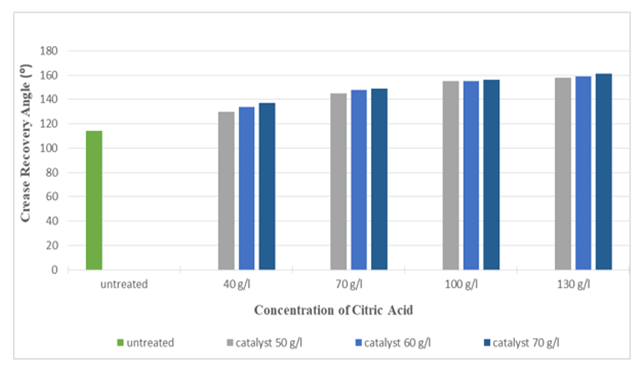 | Figure 13. Crease Recovery Angle of Silk Fabric after Citric Acid Treatment at Different Concentrations |
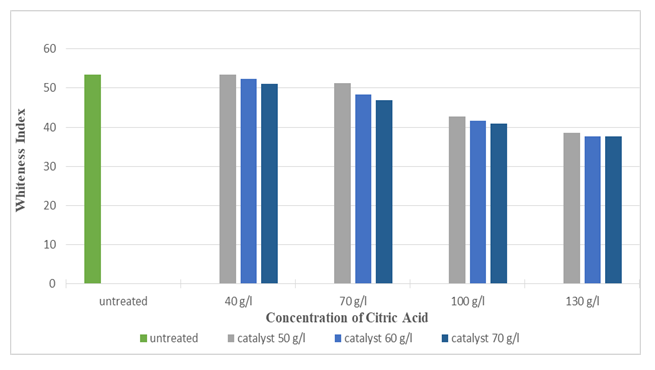 | Figure 14. Whiteness Index of Silk Fabric after Citric Acid Treatment at Different Concentrations |
Figure 15 and Figure 16 illustrate as the concentration of DMDHEU increased, the crease recovery angle (CRA) also increased up to 189° (around 65.78%) and whiteness index decreased up to 34.21 (around 35.99%). Highest crease recovery angle (CRA) was found at a concentration of 120 g/l for DMDHEU and concentration of 30 g/l for catalyst (Magnesium Chloride) whereas, at that concentration, whiteness index was lowest. It can also be seen from the graph that the effect of catalysts on crease recovery angle (CRA) and whiteness was not that much significant.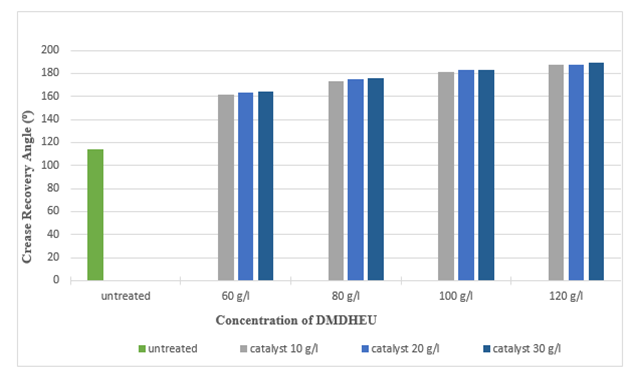 | Figure 15. Crease Recovery Angle of Silk after DMDHEU treatment at Different Concentrations |
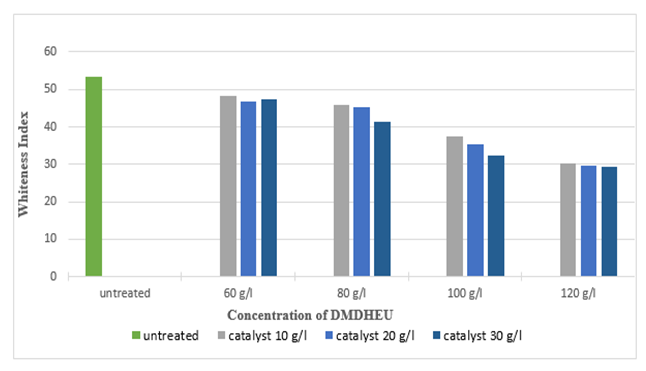 | Figure 16. Whiteness Index of Silk Fabric after DMDHEU Treatment at Different Concentrations |
Figure 17 and Figure 18 shows the tensile strength retention (%) of silk fabric in warp and weft direction after citric acid application. As the concentration of citric acid increased, tensile strength retention (%) slightly decreased (up to 81.51%).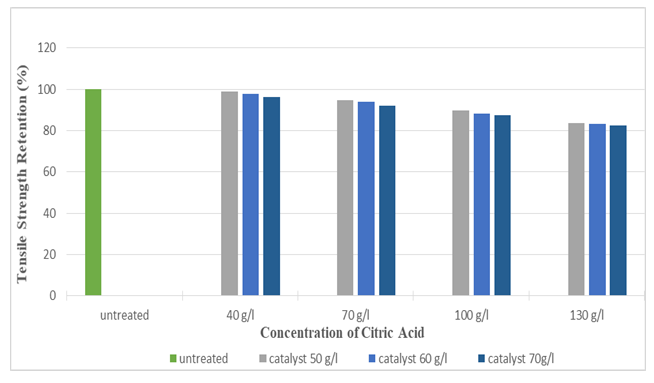 | Figure 17. Tensile Strength Retention (%) in Warp after the application of Citric Acid at Different Concentrations |
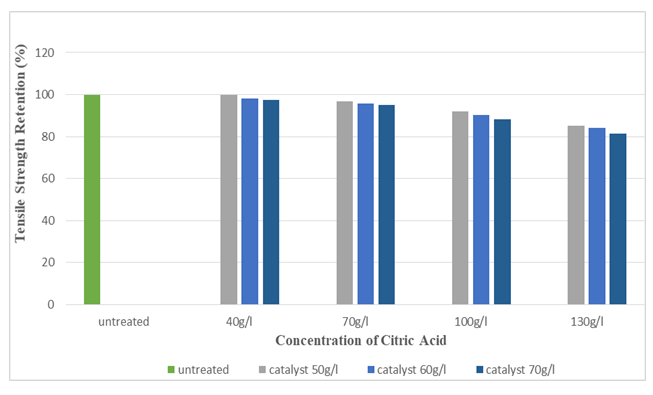 | Figure 18. Tensile Strength Retention (%) in Weft after the application of Citric Acid at Different Concentrations |
Figure 19 and Figure 20 shows the tensile strength retention (%) of silk fabric in warp and weft direction after DMDHEU application. With the increase in the concentration of DMDHEU the tensile strength retention (%) decreased, lowest tensile strength retention (%) was found at the concentration of 120 g/l for DMDHEU.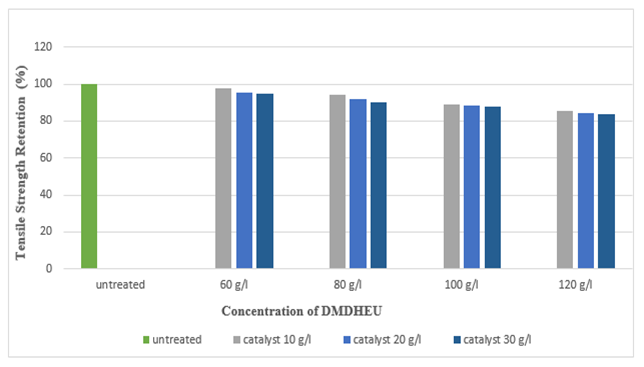 | Figure 19. Tensile Strength Retention (%) in Warp after DMDHEU Treatment at Different Concentrations |
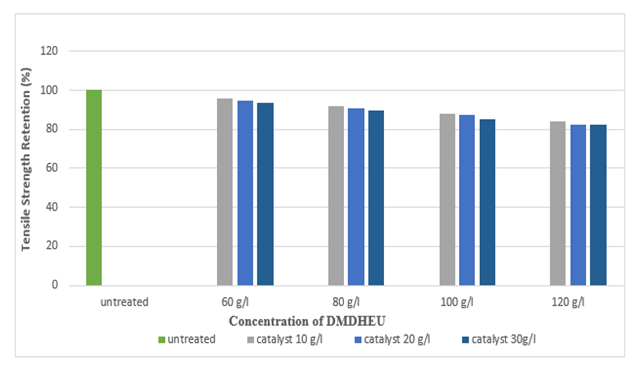 | Figure 20. Tensile Strength Retention (%) in Weft after DMDHEU Treatment at Different Concentrations |
Figure 21 and 22 shows the effect of drapability of treated silk fabric. The drape co-efficient is increased (up to 53.19%) and (up to 57.44%) with increasing concentrations of citric acid, DMDHEU and catalysts. The increase in overall drape co-efficient may be due to the fact that the crosslinks formed between the adjacent fibroin molecules which control the degree of swelling and lower degree of swelling makes the fibre more compact and stiff. The greater the overall drape co-efficient the stiffer the fabric is.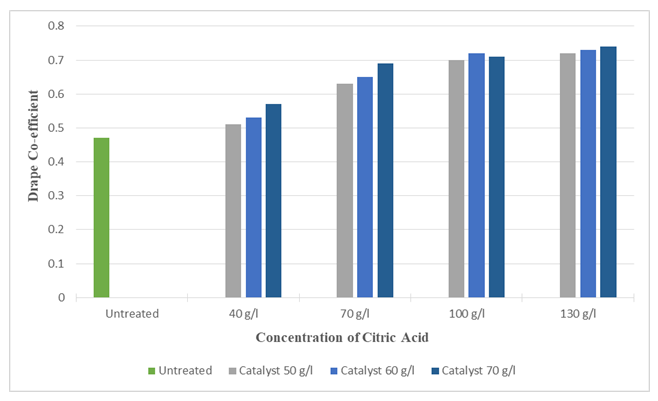 | Figure 21. Drape Co-efficient of Silk Fabric after Citric Acid Treatment at different Concentrations |
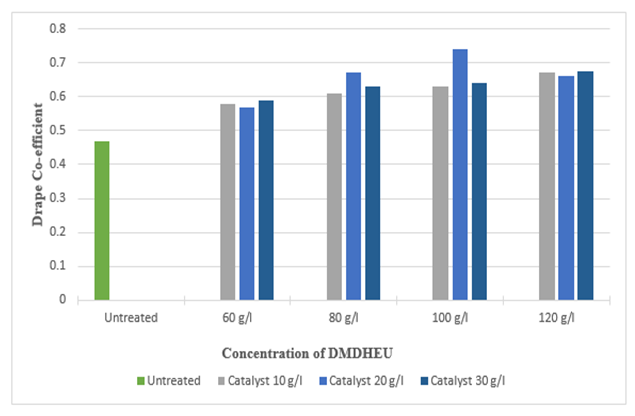 | Figure 22. Drape Co-efficient of Silk Fabric after DMDHEU Treatment at Different Concentrations |
4. Conclusions
This work reveal, after treating silk fabric with both Citric acid and DMDHEU, the crease recovery angle (CRA) increased remarkably than that of untreated silk fabric. But DMDHEU treated fabric showed better crease recovery than citric acid treated samples. DMDHEU is a toxic finishing agent, which has a disadvantage to release formaldehyde that may cause severe breathing problem of the wearer. Though to improve crease recovery angle was primary goal, but after considering the fact that citric acid being a non-toxic as well as cheap chemical and it also improved a substantial amount of crease recovery property of silk fabric, moreover, a better whiteness index, tensile strength retention % was also found while treating the fabric with citric acid. So citric acid can be a better alternative option to increase crease recovery property of silk fabric.
References
[1] | Babu KM. Silk: processing, properties and applications. Woodhead Publishing; 2018 Dec 6. |
[2] | Eichhorn S, Hearle JW, Jaffe M, Kikutani T, editors. Handbook of Textile Fibre Structure: Volume 2: Natural, Regenerated, Inorganic and Specialist Fibres. Elsevier; 2009 Oct 26. |
[3] | Cai Z, Jiang G, Yang S. Chemical finishing of silk fabric. Coloration technology. 2001 May; 117(3): 161-5. |
[4] | Raza ZA, Anwar F. Low-formaldehyde hydrophobic cum crease resistant finishing of woven silk fabric. Fibres & Textiles in Eastern Europe. 2015. |
[5] | Feng H, Wu Y, Feng X, Zhong L, Zhang F, Zhang G. A new acrylamide-glyoxal-based, formaldehyde-free elastic and stiffness finishing process for silk fabric. Textile Research Journal. 2018 Apr; 88(8): 873-81. |
[6] | Yang YQ, Li S. Silk fabric non-formaldehyde crease-resistant finishing using citric acid. Journal of the Textile Institute. 1993 Jan 1; 84(4): 638-44. |
[7] | Hari PK, Gulrajani ML, Pal NK. Crease Recovery of Silk Fabrics. |
[8] | Bajaj P. Ecofriendly finishes for textiles. |
[9] | Peng H, Yang CQ, Wang S. Nonformaldehyde durable press finishing of cotton fabrics using the combination of maleic acid and sodium hypophosphite. Carbohydrate polymers. 2012 Jan 4; 87(1): 491-9. |