Sabbir Ahmed Abir1, Ripon Kumar Prasad2, Ajmery Sultana1
1Department of Apparel Manufacture & Technology, BGMEA University of Fashion & Technology, Dhaka, Bangladesh
2Department of Textile Engineering, Dhaka University of Engineering & Technology, Gazipur, Bangladesh
Correspondence to: Ripon Kumar Prasad, Department of Textile Engineering, Dhaka University of Engineering & Technology, Gazipur, Bangladesh.
Email: |  |
Copyright © 2019 The Author(s). Published by Scientific & Academic Publishing.
This work is licensed under the Creative Commons Attribution International License (CC BY).
http://creativecommons.org/licenses/by/4.0/

Abstract
The purpose of the study is to reduce the energy load of Cold pigment dyeing (CPD) process by minimizing process steps. As a representative effort in this direction, the current paper describes the effect of curing treatment on Cold pigment dyed garments considering different properties. Pretreatment of samples were done in the same bath and same method followed for both samples. In case of dyeing, two different methods i.e. existing (Pad-dry-cure) and experimental (pad-dry) were used to develop the samples. Prepared samples were evaluated in terms of CMC∆E value, color fastness properties, drape co-efficient, GSM, fabric strength and surface morphology respectively. Results of the study authenticate better output than the existing process by considering process time and energy savings. Color fastness value of the experimental sample offers comparatively better values than the existing process while other results are within range. Experimental process can reduce up to 6% processing time along with 2.35 Kw power savings for each batch. The experimental (pad-dry) process of CPD will provide a strong economical benchmark for the garments dyeing industry to adopt this sustainable process.
Keywords:
Garments dyeing, Cold pigment dyeing (CPD), Curing, Color fastness properties, Drape co-efficient
Cite this paper: Sabbir Ahmed Abir, Ripon Kumar Prasad, Ajmery Sultana, Sustainable Approach to Modify the CPD Process for Knit Garments and Analysis the Effect of Curing Treatment on CPD, International Journal of Textile Science, Vol. 8 No. 3, 2019, pp. 49-53. doi: 10.5923/j.textile.20190803.01.
1. Introduction
In the fast fashion world when time to market is paramount, the concept of garment dyeing post make up is increasingly adopted by manufacturers [1]. Garment dyeing can be defined [2] as the ‘application of color’ to fully fashioned apparel articles, may be in the form of garments cut and sewn either prepared or unprepared knitted fabrics and then dyed, garments or components knitted from either prepared or unprepared yarn and then dyed. The benefits of processing of goods through garment dyeing procedure revolve around quick response with an abated lead time and improved inventory control [3]. It also increases the challenges of achieving the unique, fashionable & value-added products, while remaining constant in price due to the process reduction in operating margins, the dyeing process should be more economical while producing product of high value [4]. Pigments consist of insoluble colorants used for fibers, yarns and garments very commonly, which can retain stable chemical structure throughout the coloration process in its dispersed solution [5]. Water-based pigment systems are eco-friendly pathways. Pigments are dispersed into water with the assist of auxiliaries; such as dispersants, emulsifiers, anti-setting agents etc. Water-based pigment has been widely applied in coloration for textiles, paints, architecture, and wood and so on [6,7]. The Cold pigment dyeing is one of the garment dyeing processes which precipitates an uneven look at low temperature [8]. This process is also referred to as wave dyeing, top dyeing, oil wash and random dyeing. It is a simple and eco-friendly pigment dyeing process obtained by the usage of a binder, fixer along with pigments (any color). The specialty of this process is wide variation on shade range shall be expected and a special hangtag to inform customer this is not a defect is recommended [9]. When such process is carried out, it leads to a loss of many resources such as water, energy, chemicals and dyestuff, time, man-hour, etc. The concept of cleaner production has been practiced for many years in different countries [10]. Such activities include measures such as pollution prevention, source reduction, waste minimization and eco-efficiency. At its heart, the concept is about the prevention rather than the control of environmental pollution which minimizes the carbon footprint as well [11]. In this work, the concept of cleaner production including the process modification was carried out by eliminating the curing stage at the experimental process. However, conventionally this process was done in three stages namely pad-dry-cure process which is available in most manufacturing unit. But it is possible to accomplish the whole process in two stages i.e. pad-dry, without compromising the garments fastness and other properties. Hence the later process can be more efficacious than existing one, as one step can be eliminated completely which contributes reducing the process time along with power and cost savings. Experimental result shows that sample developed in pad-dry process possess good properties in comparison with the existing process (pad-dry-cure). Thus the experimental process can be used in a manufacturing unit to perform cold pigment dyeing. The purpose of this study is to establish a norm using experimental processes which will lead to a substantial cost reduction and energy saving in manufacturing unit. Therefore, the processes optimization and modification are the alternative procedures to achieve better cold pigment dyeing (CPD) efficiency and environmentally friendly as the cleaner production concept.
2. Methodology
2.1. Raw Materials
The investigation has been carried out with 100% cotton knit fabric with under mentioned specifications-Fabric type: Single jersey, GSM: 150-160, Yarn type: Combed, Yarn count: Ne-30/1s, Composition: 100% cotton, GG: 28, Form: RFD (Ready for dyeing).
2.2. Chemicals
Imarol PCLF .Primafast gold RSL , Acetic acid, Printofix Orange HR, Printofix Red TN, Nk binder R-5HN, Fixarez Resin FS-465E, Sun-softener (A-300), Ultra-196, Citric acid etc.
2.3. Pre-treatment Procedure
Samples were scoured and bleached in the single bath. Recipe followed to pre-treat the samples was H2O2 @ 4 g/l, NaOH @ 4 g/l, Na2CO3 @ 3 g/l, wetting agent@ 1 g/l, sequestering agent@ 1g/l, M:L-1:8, time-55 minutes and temperature 95°C.
2.4. Process Steps of Cold Pigment Dyeing (CPD)
Samples were developed by following existing and experimental process where the former one comprises of fast wash → drying → padding→ drying → curing→ softening respectively and the later one followed fast wash → drying → padding → drying → softening respectively. Existing process, commonly known as pad-dry-cure method, where curing is done for fixation of pigments through binder. On the other hand, the experimental process known as pad-dry method follow padding and drying stages only.
2.5. Conventional Process for Cold Pigment Dyeing
Table 1. Process Time and Energy for Conventional process 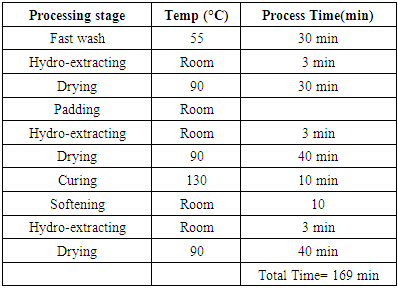 |
| |
|
2.6. Experimental Process for Cold Pigment Dyeing
Table 2. Process Time and Energy for Experimental process 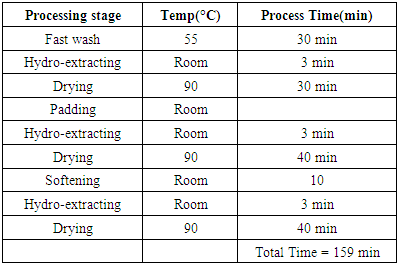 |
| |
|
2.7. Testing and Analysis
Treated samples were tested using Universal testing machine (Brand: Testometric, Model-M250-3CT, Origin: India); Fabric drape tester (Model-M213, Brand –SDL ATLAS, Origin-UK); Fabric drapability was tested according to Cusick Drape test (BS 5058) method, Color fastness to rubbing (Test Method: ISO 105x12), Color fastness to washing (Test Method: ISO 105C06C2S) and CMC∆E value was determined by spectrophotometer (Brand: Data color Spectrum, Origin: USA, Model: 650).
3. Results & Discussion
3.1. Measurement of Color Difference Value at 470 nm
CMCΔE values between two different processes were estimated from the knit dyed garments. CIE color coordinates include color qualities in terms of L* (lightness and darkness), c* (chroma) and H (hue) of the fabrics are shown in Table 3. ΔE value contains the information of color depth, shade, and the hue of a sample. ΔE value is calculated by using the CIE L*, a*, and b* values with the equation ΔE = (ΔL*2 + Δa*2 + Δb*2)1/2 where ΔL*, Δa*, and Δb* values were the difference between L*, a*, and b* values of a pair of color standard and sample (Rashid et al., 2014). The larger the ΔE value, the greater will be the color difference between the pair of color standard and sample. The experiment was carried out under light source of D65 at 100 and the result shows the satisfactory result remarked as “pass”. The acceptable range of CMCΔE value is always less than one. So the experimental process is within the acceptable range.Table 3. CMCΔE value analysis of CPD process  |
| |
|
3.2. Color Fastness to Rubbing
Color fastness to rubbing assessment was done for both samples prepared by existing and experimental process. This test indicates the resistance of color fading during rubbing in wet and dry condition where wet rubbing condition of a sample always remains less than the dry rub. Fig.3.1. Shows the increased values of the samples prepared in experimental process which means color resistance to rub both in dry and wet condition of the experimental samples are much higher than the existing process. This happens when shade become deeper during curing process. There were no significant changes observed between the existing and the experimental process results. However the color fastness for wet condition is lower than the dry process as always pigments shows low in rubbing fastness results.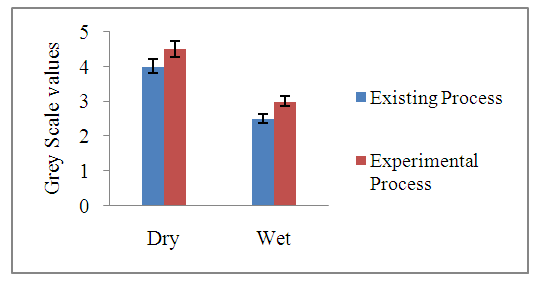 | Figure 1. Analysis of Color Fastness to Rubbing |
3.3. Color Fastness to Washing
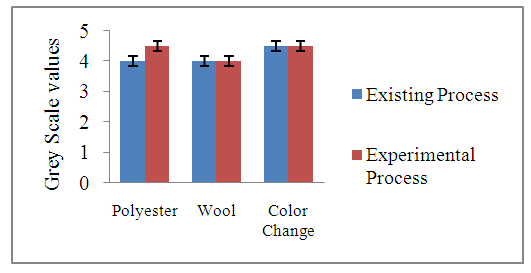 | Figure 2. Analysis of Color Fastness to Washing |
During experiment, color fastness to wash properties of the prepared sample was determined which indicates the resistance of a color during washing. This is assessed by color staining and color change principles where sample is treated with a tertiary fabric constructed with multiple fibers. This test shows (Figure 2) good wash fastness for color changed and staining of the experimental process compared to the existing process.
3.4. Effect of Drape Co-efficient Values
Drape co-efficient value of the samples prepared in existing and experimental process were measured. Four samples from each side were measured during testing. Results shows that existing process sample possesses lower drape co-efficient value than experimental process sample which means the former one is more flexible and drapable than the new one. This may happen due to the curing operation where high temperature is applied to the garments results in softer garments. But the average drape co-efficient values of both samples are very close to each other (Figure 3) with a variation 0.6% which is acceptable.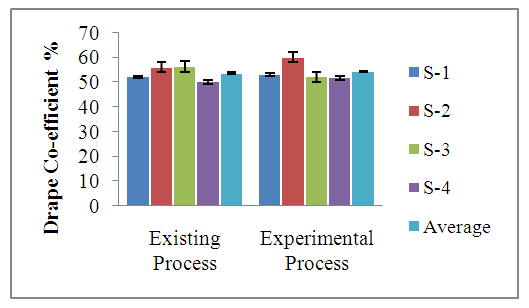 | Figure 3. Change of Drape Co-efficient |
3.5. Effect of GSM Value after Dyeing
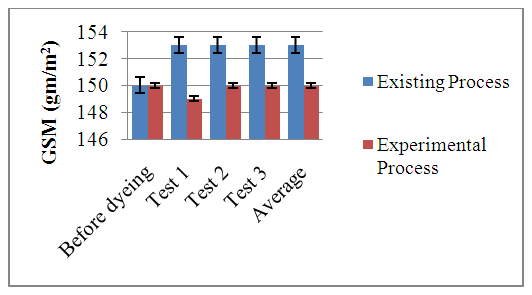 | Figure 4. Measurement of fabric weight (gm/m2) |
GSM value of the samples were determined which indicates that after dyeing gsm has increased in existing process as dye molecules are added during the dyeing process results in an increase in fabric weight per unit area. On the other hand, GSM value of the sample prepared in experimental process gets down which can be the cause of bio-polishing or enzyme wash. It may also happen due to the contractions of knit loops and the effect of curing. As a result, the experimental process samples show minor variation of GSM value to the existing process. The variance between the results was only 1.9% which is less than the standard tolerance limits (5%).
3.6. Bursting Strength
From table 4 and table 5, it can be observed that the average bursting strength for the experimental process is 164.50 N whereas in the conventional process the sample valued 165.77N. Also, the stress at break exhibits an increasing trend. In this analysis, a slightly higher strength is visible in the samples of conventional process. This explains the value of conventional process samples for strength due to the contraction of loops contributing compact structure of the fabric surface. However, the extent of change is not very significant which illustrates that the physical properties of experimental samples are not affected by curing treatment significantly.Table 4. Bursting Strength for Experimental Process 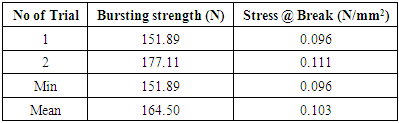 |
| |
|
Table 5. Bursting Strength for Existing Process 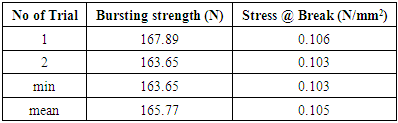 |
| |
|
3.7. Surface Morphology
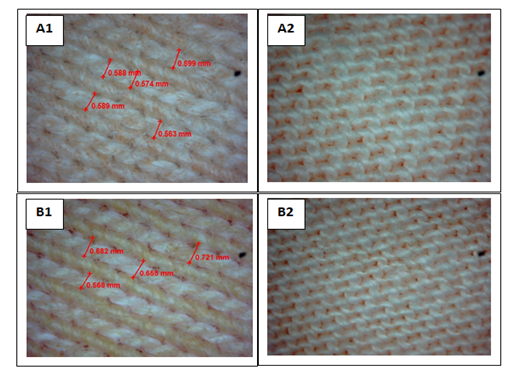 | Figure 5. A1) Face side of experimental sample; A2) Back side of experimental sample; B1) Face side of conventional sample; B2) Back side of conventional sample |
Microscopy analysis was done by digital microscope at 5X zoom. The face part and back part for both experimental and existing process were analyzed. It was noticeable that the existing samples possess sharp lines along the wales, whereas experimental process reflects a relaxed fullness structure. Moreover, curing treatment can also be a reason for influencing the surface difference between conventional (pad-dry-cure) and experimental process (pad-dry).
3.8. Reduction of Processing Time and Energy Saving
A significant difference exists in the processing time and the temperature of existing and experimental process. Reduction in process time also reduces the production cost. Since the experimental process offers the elimination of curing during whole process that’s why it is possible to eliminate the curing time. The experimental process can save up to 6% of total process time and 19% energy for each batch of production. Moreover, if a curing machine consumes 14.1 Kw/hrs; the experimental process can save power up to 2.35 Kw as the curing step was eliminated from the proposed process.
4. Conclusions
In this study, a typical comparison between existing (pad-dry-cure) and experimental (pad-dry) process has been constructed through evaluation of different properties along with processing time and power consumption for samples prepared in both process for cold pigment dyeing. Experiment shows that the existing process posses’ better result for GSM, Drape co-efficient values whereas experimental process values are within tolerance for which these are acceptable so far. For shades both samples CMCΔE value are within accepted limit. But considering color fastness properties to rubbing and washing it can be clearly stated that experimental process is better than the existing one. Besides, the developed process requires less power and processing time which is clearly an indicator for cost reduction.
ACKNOWLEDGEMENTS
Thanks to Unique Washing & Dyeing Limited and Unique Designers Limited for supporting us regarding sample preparation.
References
[1] | Sewing post dyed garments [online] available at: http://www.coatsindustrial.com/en/information-hub/apparel-expertise/sewing-post-dyed-garments (accessed 18th September 2015). |
[2] | Ajgaonkar S.B., “Garment Dyeing – Pros and Cons”, Colourage 1993 (7) 21 – 24. |
[3] | Dyeing of garments-an overview [online] available at: https://0x9.me/nsz7P (accessed 11th September 2015). |
[4] | Thiyagarajan, S. S., & Hari, K. (2014). Optimization of Wash Bath Temperature for Effective Biopolishing of Textile Garments. Journal of Textile and Apparel, Technology and Management, 9(1). |
[5] | Vernardakis, T., & Pigment, Dispersion. (2006). In: Tracton A A, editor., Coatings Technology Handbook Third Edition., Taylor & Francis Group, LLC2006., 76-71. |
[6] | Lan, Y., & Lin, J. (2011). Clay-assisted dispersion of organic pigments in water. Dyes Pigment, 90(1), 21-27. |
[7] | Ricaurte-Avella, G., Osorio, Velez. J., Nino, Cardona. J., Correa, J., & Alberto, Rodriguez. H. (2010). |
[8] | Rahman, E. M. (2013). Practical hand book of wahsing & dyeing. Dhaka: S.A. Corporation. |
[9] | Garmon & Bozzeto. Latest Washing Trend. [ONLINE] Available at: http://wenku.baidu.com/view/efa3217c5acfa1c7aa00ccf4 (accessed 11th September 2015). |
[10] | Kjaerheim G. CP and sustainability. J Clean Prod 2005; 13: 329-339. |
[11] | International institute for sustainable development [online] Available at: http://www.bsdglobal. com/tools/bt_ p.asp ; (accessed 10th September 2015). |
[12] | Raro Chem. Garments pigment dyeing system; room temperature process. [ONLINE] Available at: http://www.rarochem.it/public/rarochem/area/PH/pr77.pdf (accessed 11th September 2015). |
[13] | Rashid, M. A., Hossain, M. D., Kafi, M. A., & Yesmin, S. (2014). Process Modification of Denim Garments Dyeing with Fluorescent Dye. International Journal of Textile Science, 3(2), 33-37. |
[14] | Evaluation of the pigment dispersion in acrylic resins for the manufacture of artificial teeth. Revista `Facultad De Ingenieria-Universidad De Antioquia, 53, 54-63. |