Maitry Bhattacharjee1, Avik Kumar Dhar2, Md. Minhazul Islam2, Md. Abdur Rashid3
1Department of Textile Engineering, Shyamoli Textile Engineering College, University of Dhaka, Dhaka, Bangladesh
2Department of Textile Engineering, Chittagong Textile Engineering College, University of Chittagong, Bangladesh
3Department of Textile Engineering, Dhaka University of Engineering and Technology, Gazipur, Bangladesh
Correspondence to: Maitry Bhattacharjee, Department of Textile Engineering, Shyamoli Textile Engineering College, University of Dhaka, Dhaka, Bangladesh.
Email: |  |
Copyright © 2019 The Author(s). Published by Scientific & Academic Publishing.
This work is licensed under the Creative Commons Attribution International License (CC BY).
http://creativecommons.org/licenses/by/4.0/

Abstract
Denim garments are most preferred of today’s youth for the amelioration of its aesthetic sensibilities after washing which can be delineated as a magnanimous approach of imparting worn-out look, embellishment of appearance and improvement in the comfort ability of the garments. This project aimed to represent the pragmatic scope of reactive dye as an alternative of profusely used vat dye and has been successfully introduced on woven denim to mitigate the drawbacks of water insolubility of dye, extra processing of dye reduction, physical attachment of dye-fiber and finally long dyeing time of indigo, vat or sulphur dye. Various washing effects like Bleach, Potassium Permanganate (PP), Enzyme and Enzyme-Stone washing techniques were developed assiduously to obtain the desired fashion effect in terms of color fading and high wear performance in terms of longevity/minimum breaking strength losses of denim. 100% cotton denim (woven) with twill weave 3/1 construction was used in this project. At the denouement of the project, physical and mechanical properties of treated and untreated cotton denim fabric was investigated in terms of breaking strength, elongation at break, weight loss%, shrinkage% and color fading. Reflectance, whiteness, K/S value and CMC value of the washed samples were also investigated to bolster the washing performance of reactive dyed denim.
Keywords:
Reactive dye, Denim fabric, Dyeing, Denim wash, Performance
Cite this paper: Maitry Bhattacharjee, Avik Kumar Dhar, Md. Minhazul Islam, Md. Abdur Rashid, Development of Washing Effects on Reactive Dyed Denim Fabrics: A Value Added Approach of Denim Wash, International Journal of Textile Science, Vol. 8 No. 2, 2019, pp. 41-48. doi: 10.5923/j.textile.20190802.03.
1. Introduction
Denim is sturdy cotton warp-faced twill weave textile fabric in which the weft passes under two or more warp threads and produces a diagonal ribbing that distinguishes it from cotton duck and is considered a very strong, stiff and hard wearing fabric [1,2]. Popularity of garment washing especially of denim garment in the world market is increasing day by day. Large number of washing factory is being established in Bangladesh to execute the buyer increasing requirement [3,4]. In the rough, washing technology is used to modify the appearance, size, outlook, comfort ability and fashion of the garments and mainly applied on denim goods and any other garments to provide with a lucrative economical and glassy appearance along with performing the key treatments like removing insoluble matters, matters already in solution or an emulsion of other impurities from the fabric [5-7]. It is drastically one of the most widely used finishing treatments that have vastly used due to its effect on appearance and comfort ability and without washing, denim garment is uncomfortable to wear due to its weaving, printing and dyeing effects. It essentially needs a finishing treatment to make it soft, supple and smooth which enhance wearer’s comfort [8,9].From the very beginning, natural indigo are being extensively used for denim dyeing specially the warp yarn since dyeing of cotton warp yarns with indigo is usually considered key to the denim fabric manufacturing process and usually colored warp and grey or white weft yarn and used for jeans, work clothes, casual wear even for Vehicles and art business also [10]. Though in earlier stages, warp of denim used to be dyed with natural indigo but with the development and characterization of first synthetic indigo dye in 1880's German chemist Adolf von Baeyer has brought a revolution in textile dyeing techniques which triggered off the culmination gradually with the improvement in denim wear [11]. Due to the reason of its insolubility in water and lack of affinity to the fiber, in ancient years indigo dyestuff used to be fermantated in wooden vats in vatting process, is supposed to be the origin of vat dyes. Indigo dyes are used for fashion dyeing of denim and fibers dyed with indigo are not included in fiber-transfer examinations rather the dye remains on surface through ring dyeing mechanism which refers to lack of full penetration of dye all the way to the core of the yarn [12,13]. Maximum dyes are stained on to the fiber surface that form layer of dyes there while only a few dyes are partially diffused to the interior of fiber in perimeter dyeing mechanism and show poor washing fastness also [14]. Before dyeing denim warp, indigo dye needs to be activated and converted into water soluble leuco-form to increase the affinity towards fiber. Activation or reduction of indigo dye takes place in certain conditions with the presence of hydrosulfite in alkaline medium and caustic soda (NaOH) is used to assert the medium. Reduction of indigo dye is highly hazardous for human health and environment since toxic, carcinogenic reducing agents are used for this purpose and fume generated during dye reduction causes different health hazard also. Due to this reasons a big portion of industries are now motivated to practice sustainable design and production throughout the textiles, like the use of prereduced indigo, vat or sulphur dye which is considered environmentally safe. The another reason for indigo dyestuff not being fully penetrated into the fiber is its bigger molecule size and hence dye only adheres to the surface and remains at outer surface of the fiber. The inside stays white. After reducing and dyeing, dyed ropes have to be aerated through oxidation process so that the dye and fiber can be fixed together [15,16]. All of these characters of indigo lets denim fabric to have its final look with different types of washing and finishing applications and enables denim fabric to gives a real life to the fabric since it abrades or fades continually.Different wet washing processes of garments like normal wash or rinse wash, pigment wash, caustic wash, silicon wash, enzyme wash, stone wash, stone enzyme wash, bleach wash, acid wash are being frequently used [17,18]. Characterization and process optimization of indigo dyed cotton denim garments along with investigation of sustainable and consumer friendly approach are practiced by researchers [19]. To keep up with the quickly changing demands of customers and environment issue, technologists are experimenting with new design and fashions not only by using different washing methods for denim garments but also different dyeing techniques also. Scope of knit denim and dyeing of knit denim with reactive dye are also discussed by researchers and established a motto that besides indigo dye, reactive dye has also been used now-a-days in denim dyeing which creates strong covalent bond with cellulose and fixed with fiber with a strong dye-fiber interaction [20].Though indigo dyeing of denim provides a real and living look after washing, it consumes time and money more and extra processes like reduction of dye before yarn dyeing process, oxidation after dyeing, desizing before implementation of washing techniques and extra manpower is also needed to handle those processes. In This study, to overcome the limitations reactive dye (Novacron group) has been proposed and successfully introduced on woven denim (denim of 100% cotton yarn). By this way extra process of reduction which is considered hazardous for human health, oxidation, yarn dyeing and even fabric desizing before washing can also be omitted. Denim fabric dyeing with reactive dye also provides washing effect when treated with different wet washing techniques like bleach wash, PP wash, Enzyme wash and enzyme-stone wash also. Characterization in terms of mechanical and physical properties of the washed sample shows that it can be a good alternative for the high cost indigo dye in near future.
2. Materials and Methods
2.1. Materials
The denim (woven) fabric comprised 100% cotton having specification Warp Count of yarn - 7.10s, Weft Count of yarn - 7.94s, EPI-71, PPI-40, GSM (Grams per Square Meter) 368, 3/1 warp faced twill. The denim fabric was dyed using a typical recipe with reactive dye (Novacron, Bangladesh) yellow, red, blue and Combine (RYB) and followed by different washing techniques. During these processes different auxiliaries were used like, Sequestering agent (Resotex-600S, India), Detergent (SDC Enterprise, UK), Bleaching powder (Eastern scientific LTD. Dhaka, Bangladesh), Soda Ash (Merck KGaA, Germany), Potassium Permanganate (Merck KGaA, Germany), Cellulase Enzyme (Dysin, China), Anti back staining agent (Dysin, China), Hydrose (Dysin, China), Caustic Soda (Merck specialties Pvt. Ltd, India), Acetic Acid (India), Sodium metabisulfite (Merck specialties pvt. ltd, India), Pumice Stone (Bangladesh), L-histidine mono hydrochloride mono hydrate (Sigma-Aldrich, USA), Disodium hydrogen orthophosphate dehydrate (Sigma-Aldrich, USA) etc.
2.2. Methods
2.2.1. Dyeing Method
To prefer the effective dyeing process a typical recipe of dyeing was used where 2% shade of reactive blue, reactive yellow, reactive red and reactive combine (RYB) dye (Novacron) was used separately to get 4 reactive dyed samples. Common salt (50g/l) and soda (10g/l) were used by dosing. Dyeing was carried out in sample dyeing machine at 1:30 (M: L) ratio. Hydro extraction after dyeing was carried out to remove excess water from fabric and finally fabric was dried at 60°C temperature. Reactive blue dyed sample is indicted as S1, reactive yellow by S2, reactive red by S3 and reactive combine (RYB) dyed sample was marked as S4 for easy understanding.
2.2.2. Washing Effect on Reactive Dyed Sample
Bleach WashBleach wash of reactive dyed samples were carried out by a typical recipe of bleaching powder (10g/l), soda ash (5g/l), sequestering agent (2ml/l) at pH –10, and 1:5 material-liquor ratio. Washing was carried out for 20 min at 40°C temperature in Rota Wash machine (SDLM228B, SDL Textile Machine Co. England). After washing hot wash was carried out at 60°C for 5 min and followed by cold wash for 5 min. After that processed denim fabric was squeezed in a laboratory scale hydro-extractor machine (NISHO-NH-EX-10, CHU CHEONG CO. PFE. LTD, Singapore) at 200 rpm for 4 min and dried in a tumble drier (TVR2, SDLATLAS, UK)) at 75°C for 40 min.Potassium Permanganate (PP) WashPotassium Permanganate wash of reactive dyed samples were carried out by a typical recipe of Potassium permanganate (5g/l), Sodium metabisulfite (1.5g/l), Sequestering agent (2ml/l) at 1:5 material-liquor ratio. Washing was carried out at 40°C for 20 min in Stone washing m/c (NISHO-NH-WH-25, CHU CHEONG CO. PFE. LTD, Singapore). After PP wash, hot wash was carried out at 60°C for 5 min followed by cold wash for 5 min and finally neutralized in Sodium metabisulfite solution for 20 minutes. After that processed denim fabric was squeezed in a laboratory scale hydro-extractor machine (NISHO-NH-EX-10, CHU CHEONG CO. PFE. LTD, Singapore) at 200 rpm for 7 min and dried in a tumble drier (TVR2, SDL ATLAS, UK) for 30 min.Enzyme WashThe process was conducted in liquor containing acetic acid (1ml/l), anti back staining agent (2g/l), wetting agent (1g/l), sequestering agent (2ml/l) at pH 5.5 and material to liquor ratio of 1:5 with cellulase enzyme in the washing machine. Concentration of cellulase enzyme was kept 1.5g/l. The process was carried out at 50°C temperature for 40 min. After enzymatic treatment hot wash (60°C) and cold wash were carried out chronologically. Finally Processed denim fabric was squeezed in hydro-extractor machine (7min) and dried in tumble drier for 30 minutes.Enzyme & Stone WashEnzyme and stone wash was carried out in liquor containing Acetic acid (1ml/l), Anti back staining agent (2gm/l), Wetting agent (1gm/l), Sequestering agent (2ml/l) at pH 5.5, material to liquor ratio 1:5 with cellulase enzyme (1.5g/l) and pumice stone (10kg). The process was carried out for 40 minutes at 50°C in stone washing machine. After enzymatic treatment hot wash (60°C) and cold wash were carried out chronologically. Finally Processed denim fabric was squeezed in hydro-extractor machine (7min) and dried in tumble drier for 30 minutes.
2.2.3. Testing and Analysis
To obtain product performance, washed denim fabric samples were tested using Abrasion Tester (SDL, UK), perspirometer (FINEETE, Hong Kong), crock meter (MESDAN, Italy) and tensile strength tester (Goodman, England). The specimens used for breaking strength investigation were cut in the warp direction only. Before testing samples were conditioned in testing laboratory at 65% relative humidity and at 20°C for 24 hour (ASTM D 1776 2008). All experiments were carried out in standard atmosphere for testing according to the standard ISO 139.Color fade of the fabric due to rubbing (ISO 105 X12) wash (ISO 105 CO3) and alkaline perspiration (ISO 105 – EO4 1994) was examined and rated using gray scale for color change according to AATCC test method 61 (2010). Verivide Light Cabinet (K-50-3, Verivide, UK) was used to assess the samples. Breaking strength and elongation at break was determined using fabric strength tester according to ASTM D 5034 (2009). Dimensional changes (shrinkage %) was calculated from the difference in fabric length before and after treatment according to AATCC test method 96 (2009). Abrasion resistance was examined by Martindale (Abrasion Tester). Weight loss (%) in fabric was calculated from the difference in fabric weight (GSM) before and after the treatment according to ASTM D 3776 (1996). Electric Balance (Precisa, BJ1000C, Precisa Gravimetrics AG, Switzerland) was used for precision weighing of samples and chemicals. CMC, Whiteness and reflectance were assessed by using Data color spectrophotometer & K/S values were examined by -Kubelka - Munk equation,
Where, K/S is the color strength and R represents reflectance of the sample.
3. Result and Discussion
3.1. Measurement of Weight Loss%
Weight loss% of the denim washed samples is a crucial aspect of washing as it is related to profit, washed fabrics quality, durability, comfort ability & other properties. Weight loss% of reactive dyed denim fabric is negligible than the typical vat or indigo dye which merely attached with yarn by physical attachment. This is because, reactive dye creates strong fiber-dye covalent bond with cellulose chain; hence there is less scope to provide chance to the other agencies to destroy fiber. However, among all types off washing techniques in case of bleach wash & PP weight loss% is moderately high because oxidative treatment of cellulose caused some damage on cellulose. In contrary, during enzyme wash, cellulase hydrolyzes cotton attacking projecting fibers (micro-fibrils) on surface, then attacked on yarn portion but hydrolyzes them very slowly. That’s why, cellulose degradation or weight loss% in case of enzyme and enzyme-stone wash is insignificant.Table 1. Weight loss% of washed samples 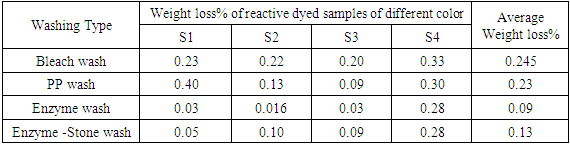 |
| |
|
3.2. Dimensional Change & Shrinkage% after Washing
Denim shrinkage after washing is closely related to the change in its structural characteristic. In the phase of garment design, it is necessary to assess fabric shrinkage; otherwise dimensions of a ready-made article will mismatch with the designed ones. Analysis of the obtained results demonstrates that upon the influence of washing a garment shrinks, however, with different shrinkage value. From below table (Table 2) it is clearly noticed that, none of the samples of reactive dyed denim exceeds the allowable standards of Shrinkage % (allowable standard is 2% according to LST EN 25077:1996) in the both warp and weft direction. From the below graph of average shrinkage% of the washed samples it can be observed that, average shrinkage% in warp direction (lengthwise) in case of bleach wash process is more than others but in weft direction (widthwise) Enzyme wash shows more average shrinkage% than other washing techniques.
3.3. Breaking Strength and Elongation at Break
Washing processes should not create any adverse effect on the breaking strength and elongation at break of the samples while compared with the untreated samples. Noticeable higher drop in breaking strength values after PP wash than any other wash is clearly indicative of a relatively higher response of the PP (oxidative reagent) on cotton yarns. Moderately higher breaking strength and negligible change in elongation at break after enzyme and enzyme-stone wash than the other washes is the sign of slow and mild attack or hydrolysis of projecting fibers or micro-fibrils and then on the yarn portion by cellulase and minimal distortion of the fabric samples after enzyme treatment.Table 2. Dimensional Change & Shrinkage% after washing 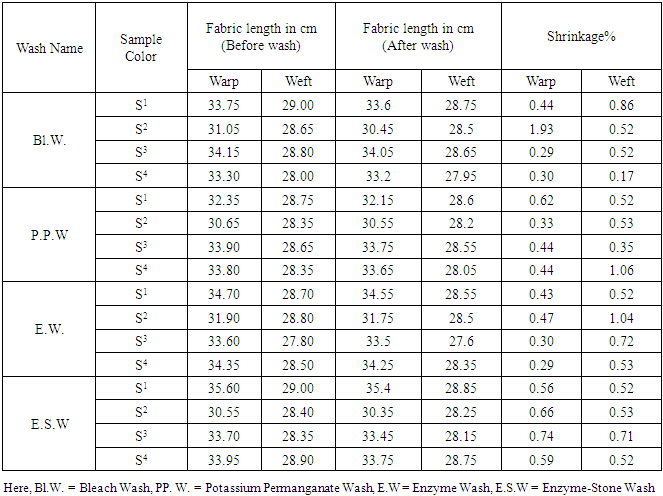 |
| |
|
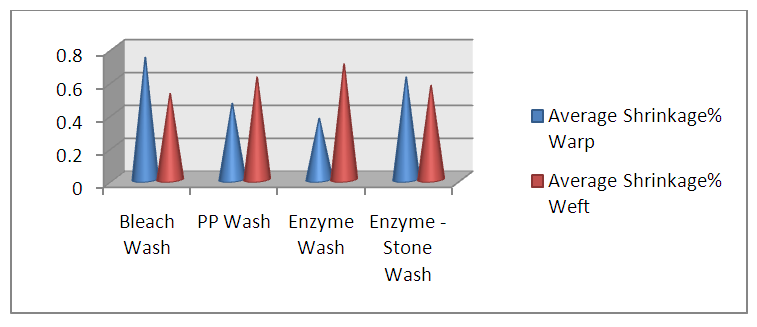 | Figure 1. Average Shrinkage% of samples after washing |
Table 3. Breaking Strength and elongation at break (Warp) of samples before and after wash 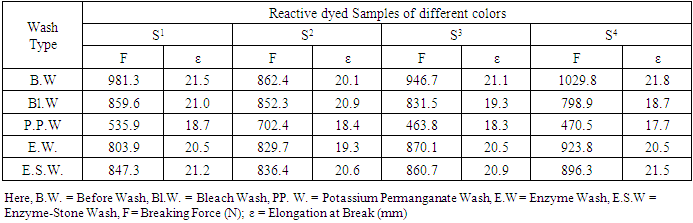 |
| |
|
3.4. Reflectance
Spectrophotometers differ from colorimeters in that they measure reflectance for various wavelengths in the spectrum. In the case of reflectance measurement, the quantity measured is termed Reflectance Factor and is defined as the reflectance of the sample at a given wavelength compared to the reflectance of the perfect diffuse white measured under the exact same conditions.The reflectance value describes the reflection of a particular dye by a particular fiber. The reflectance values of the tested specimens are shown in Table 4. It has been found that reflectance% of the samples after PP wash and enzyme-stone wash show comparatively better performance than the other samples. This is the pellucid indication that oxidative agent like potassium permanganate (PP) increases the reflectance of washed samples. When reactive dyed samples are treated by enzyme along with pumice stone, reflectance also increased due destruction of floating fibers by enzyme and strike of pumice stones.Table 4. Reflectance of samples before and after wash 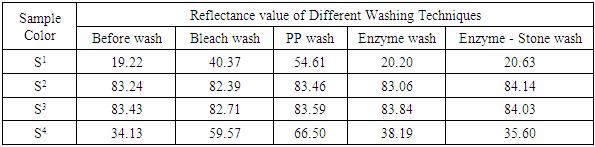 |
| |
|
3.5. Whiteness
In general, the hair-like cotton fibrils are degraded and partly detached from the main fiber chain and indigo dye bonds are broken from the yarn surface. Rotating garments inside washing machine hydrolyzes more bonds due to mechanical friction, restores their original white color. But, reactive dye is not merely surface attached rather it is strongly bonded with cellulose that’s why restoring original color of the denim yarn is hardly happened in this case. This is the reason of finding the decrease of whiteness index of samples after wash. The values of whiteness of different washed samples are depicted in Table 5. After bleach wash there is a little bit increase of whiteness due to bleaching action. Table 5. Whiteness of samples before and after wash 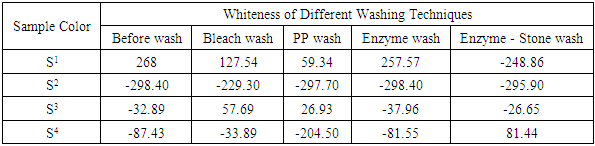 |
| |
|
3.6. Colour Strength
It was observed that color strength of denim fabric decreased significantly after they were exposed to bleach wash and PP wash but after enzyme treatment decrease in color strength is minimal. A portion of the primary wall of cotton is always in contact with enzyme during washing and hence at the contact point, surface of fibers are decomposed by the aqueous solution of the enzyme. Consequently, enzyme washed denim become duller and color is faded than the original one. But adverse effect of oxidative agent breaks the conjugated bond of dyes and hence destroy the color making the denim fabric fade and duller. For this reason color strength after bleach wash and PP wash was drastically reduced.Table 6. K/S of samples before and after wash 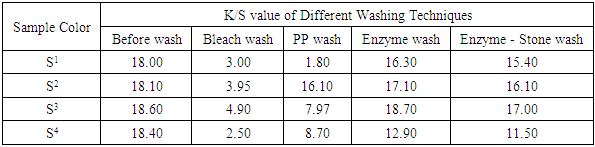 |
| |
|
3.7. CMC
During washing, the part of the primary wall of cotton is always in contact with washing agent like bleaching powder, PP, enzyme or stone etc., so at the contact point fiber surfaces are hydrolyzed by the catalysis of the washing agents and then treated fabric becomes duller and color is faded which is not a curse rather willingly obtained during washing. L, C, H values of washed fabric samples along with the original one is shown in Table 7. The color difference values which describe how far closes the trail closed to standard sample are also listed in Table 7. It has been found that, the color difference values of washed sample are more for bleach and PP wash than enzyme and enzyme-stone wash. This is due to the reason that concentration of enzyme or activity of enzyme is not strong enough to break covalent bond between dye and fiber. Hence enzyme and enzyme-stone washed sample shows negligible deviation of the before washed samples in terms of lightness/darkness, chroma, hue angle and finally CMC value. But in case of PP wash and bleach wash washed samples color was adversely deviated from the untreated one and shows a great change in appearance and outlook. Table 7. CMC values of samples before and after wash 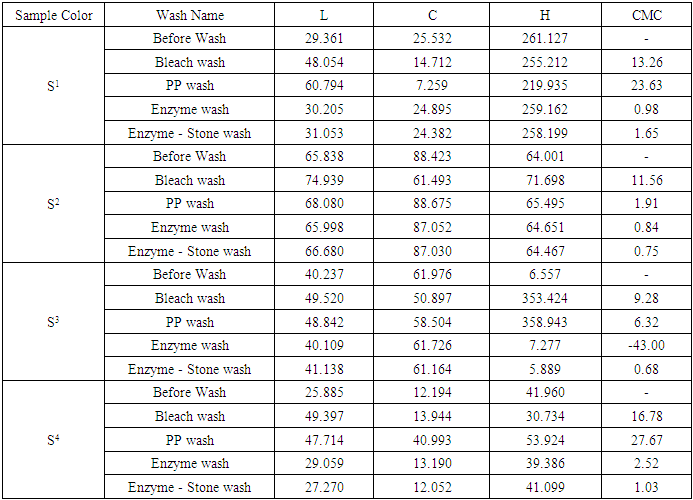 |
| |
|
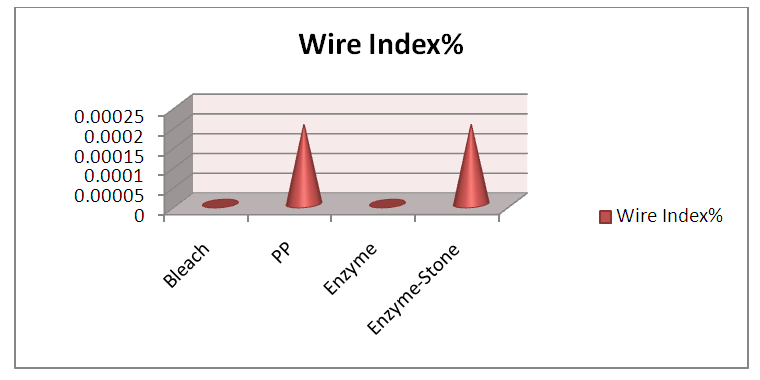 | Figure 2. Abrasion resistance of washed samples in terms of wire index% after 5000 cycles |
3.8. Abrasion Resistance
Abrasion resistance shows the ability of a fabric to resist surface wear caused by flat rubbing contact with another material in terms of wear index%. From the graph stated below it is clear that, all the reactive dyed denim washed samples show a great resistance against abrasion result is almost zero which is the indication of maximum longevity, serviceability and wear ability of the washed fabric.
3.9. Color Fastness
After washed fabric should show resistance towards different agencies like wash, water, perspiration, rubbing etc which is described in a short term ‘color fastnesses. Washed samples show moderate to high rubbing fastness and comparatively better result was obtained in case of enzyme and enzyme-stone wash. This is because dye –fiber interaction was rarely disturbed by the enzyme during washing and enzyme did not engender any potential scope of losing color due to rubbing. Comparatively less rubbing fastness was observed in case of PP and bleach washed sample for their retaining effect on washed samples. Washed samples show excellent fastness properties to wash and perspiration. Almost all the samples retain their original color against further which is the indication of problem free end-uses of the washed fabric. In case of enzyme washed sample, denim fabric was noticed to show excellent fastness to color fading and color staining.Table 8. Color fastness to rubbing of samples after wash 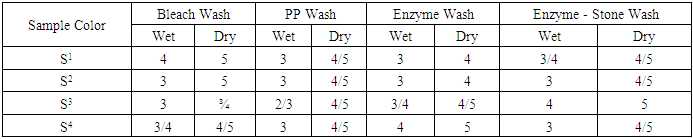 |
| |
|
Table 9. Color fastness to washing of washed samples 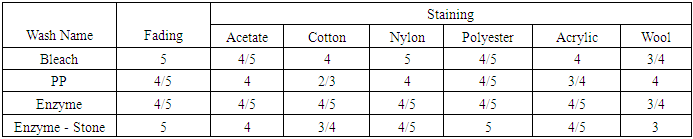 |
| |
|
Table 10. Color fastness to alkaline perspiration of washed samples 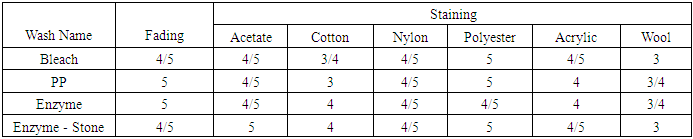 |
| |
|
4. Conclusions
Denim dyeing with reactive dye saves time, cost and extra arrangement of processes eradicating extra processes like vatting before dye application, oxidizing after dyeing and even desizing before implementing denim washing effect also. Rudimentary step of denim fabric dyeing with reactive dye and washing effect on different reactive dyed denim fabric was investigated in this work and then different characterization such as breaking strength, elongation at break, shrinkage, weight loss%, depth of shade, finally color fastness to rubbing, wash and perspiration were done. After completing the project, on the basis of different test results it was found that, weight loss% of bleach washed sample is more than that of PP wash, Enzyme wash, and Enzyme Stone washed sample. The shrinkage% in warp direction of bleach wash is more than others but in weft direction enzyme wash shows more shrinkage % than others. Reflectance of PP washed sample is better than all other washed samples even though whiteness of every sample is lower. K/S value is greater in case of Enzyme washed sample while CMC value of PP washed sample is greater than all other samples. Rubbing fastness of bleach washed sample is greater in both wet and dry condition. Wash fastness of bleach and enzyme wash are almost same and greater than the others. Perspiration of enzyme washed sample may be considered as good than others. Bleach and enzyme washed sample are more abrasion resistant than others. In a nutshell, different fastness properties are commendable. And it can’t be gainsaid that, washing effects with chemical treatment are the best for reactive dyed denim. For the above possibilities in future denim with reactive dye will cover the most of the consumers demand.
ACKNOWLEDGEMENTS
The authors appreciate the support of department of Textile Engineering and Textile Engineering lab of Textile Engineering College, Chittagong and department of Textile Engineering, DUET, Gazipur, Dhaka - 1208.
References
[1] | Mogahzy, Y.E., 2009, Engineering Textiles: Integrating the Design and Manufacture of Textile Products (First ed.) Woodhead Publishing. p. 362. |
[2] | Razzaque, M.A., 2004, Garment & Textile Merchandising (1st ed., Dhaka: Popular publications) pp. 223–226. |
[3] | Islam, M.T. 2010, Garments washing & dyeing (1st ed., Dhaka: Ananto publications) p. 220–222. |
[4] | Molnar, B.D., McGrath, D.T., Dausch, M.E. and Badami, V.V. 1994, Whipple III W. Machine for cleansing articles. |
[5] | Brenner, R.A. and Hardaway, A.H. 1988, High performance washing process for vertical axis automatic washer. |
[6] | Pazarlıoǧlu, N.K., Sariişik, M. and Telefoncu, A. 2005, Laccase: Production by trametes versicolor and application to denim washing. Process biochemistry. 40: p 1673-1678. |
[7] | Sarkar, J. and Khalil, E. 2014, Effect of industrial bleach wash and softening on the physical, mechanical and color properties of denim garments. IOSR Journal of Polymer and Textile Engineering.1: p 46-49. |
[8] | Li, S., Lewis, J.E., Stewart, N.M., Qian, L. and Boyter, H. 2008, Effect of finishing methods on washing durability of microencapsulated aroma finishing. The Journal of the Textile Institute. 99: p 177-183. |
[9] | Yang, H.C., Wang, W.H., Huang, K.S. and Hon, M.H. 2010, Preparation and application of nano chitosan to finishing treatment with anti-microbial and anti-shrinking properties. Carbohydrate Polymers. 79: p 176-179. |
[10] | A World in Denim. http://www.ianberry.org/about. |
[11] | New Cloth Market. Indigo Dyeing: An Overview. https://www.fibre2fashion.com/industry-article/7331/indigo-dyeing-an-overview. |
[12] | Grieve, M., Biermann, T. and Schaub, K. 2006, The use of indigo derivatives to dye denim material. Science & Justice, 46, p 15–24. |
[13] | Grieve, M. and Biermann, T. 1997, The population of colored textile fiber on outdoor surfaces. Science & Justice, 37, p 231–239. |
[14] | Choudhury, A.K.R. 2006, Textile Preparation and Dyeing, Oxford & IBH Publishing Co. Pvt. Ltd. New Delhi, India, p. 579-580. |
[15] | Gohl, E.P.G. and Vilensky, L.D. 1983, Textile Science, Second Edition. |
[16] | Hossain, M.F. 2009, Practice of Textile Coloration (Volume-1), 1st Edition, BUTEX, Bangladesh. |
[17] | Kalliala, E. and Talvenmaa, P. 2000, Environmental profile of textile wet processing in Finland. Journal of Cleaner Production. 8: p 143-154. |
[18] | Kashem, M.A. 2008, Garments Merchandising (1st ed., pp. 69–71). Dhaka: Lucky-one traders. |
[19] | Mondal I.H. and Khan, M.R. 2014, Characterization and process optimization of indigo dyed cotton denim garments by enzymatic wash. Fashion and Textiles, 1:19. |
[20] | Hannan, A., Sheikh, S., Kabir, S.M.F. and Rouf, A. 2014, Scope of Knit Denim Products Using Reactive Dye and Convenient Washing Effects, International Journal of Recent Development in Engineering and Technology, 3(5). |