Israt Zebin Ansari1, Zulfa Ferdous1, Israt Zerin1, Syed Fuad Irfan1, Sujan Sharkar2
1Department of Textile Engineering, Southeast University, Dhaka, Bangladesh
2Soorty Denim Enterprise
Correspondence to: Israt Zebin Ansari, Department of Textile Engineering, Southeast University, Dhaka, Bangladesh.
Email: |  |
Copyright © 2019 The Author(s). Published by Scientific & Academic Publishing.
This work is licensed under the Creative Commons Attribution International License (CC BY).
http://creativecommons.org/licenses/by/4.0/

Abstract
Apparel sector is the most promising and rapid growing sector of Bangladesh. To sustain and survive in the global competition, machine automation is becoming the demand of time. Now-a-days apparel manufacturing industries are trying to improve their production efficiency to cope with the emerging challenges of this sector. The aim of this research is to improve productivity of sewing line by using extra mechanical automation on sewing machine in affordable cost. These reduce the cycle time, increase productivity in SMV wise 73.81 to 83.1 and manpower wise from 21.42 to 24.19. Which saves a remarkable cost and helps to beat the lead time successfully as well.
Keywords:
Apparel, Productivity, SMV, Lead time
Cite this paper: Israt Zebin Ansari, Zulfa Ferdous, Israt Zerin, Syed Fuad Irfan, Sujan Sharkar, Improving Productivity by Using Extra Mechanical Automation on Different Sewing Machine, International Journal of Textile Science, Vol. 8 No. 1, 2019, pp. 26-30. doi: 10.5923/j.textile.20190801.04.
1. Introduction
Bangladesh has already occupied the 2nd position in RMG export in the world [1]. In the financial year 2016-2017 the RMG industry generated US$28.14 billion, which was 81.23% of the total export earnings in exports and 12.36% of the GDP [2]. To retain this growth & safeguard our position in world RMG market there is no alternative to increased productivity [3]. Productivity is evaluated by achievement toward established goals based on relationships between inputs and outputs of industry [4].In project management, productivity is the process by which resources are optimized in order to achieve the desired outcomes of the project. There are various components that are involved in the productivity of a workplace which are human resources (labor), machinery, and the working condition of the workplace [5].Many people think of automation on a large scale; But automation can be added to machine tools in many other, more affordable ways as well [6]. A study showed increase of productivity of garment industry with their existing industry set up. It has been observed that there is scope to improve the productivity with improving the flap design. With regular flap design only one pocket flap can be manufacture, but with change in flap design, the double flap can be produced at less time. [7]Technological advancements like high speed sewing machine, CAD and computer- aided manufacturing (CAM) applications, new techniques in cutting, fusing and pressing, and application of robotics on the process of garment production, a substantial increase in productivity can be achieved [8].In this research we try to increase productivity by reducing sewing time. We develop some self-made automation through air cylinder commonly known as Pneumatic cylinder.
2. Material and Methodology
2.1. Product Specification
Item: Short PantBuyer: PrimarkFabric construction: 100% cottonOrder quantity: 108400pcsColor: Black, dark blue, indigoSewing data:Sewing SMV: 20.32Working hour: 10Manpower required: 70Daily target: 1500pcs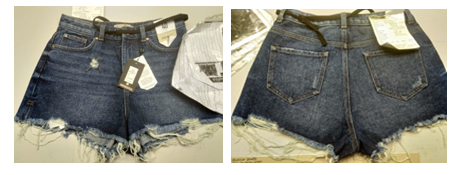 | Figure 1. Front and back side of Short pant |
Operation 1: Auto DisposerProcess: Zipper Attach to single flyMachine: Double needle lock stitch machineMachine parts:• Air Cylinder• Compressed air• Rubber pad• Air trigger | Figure 2. Added automation on double needle lock stitch machine |
For adding zipper at fly position at first zipper needs to attach in single fly. Here requirement was used single needle machine earlier but we replace this machine with double needle lock stitch machine as 2 stitches with ¼ gap needs to give in zipper fly. Here we are adding one auto disposer also, so that operator doesn’t need to dispose zipper by hand. Operation 2: Auto thread cutterProcess: Waist belt attachMachine: KANSAIMachine parts:• Air Cylinder• Compressed air • Scissor• Steel Base• Air Pipe• Air trigger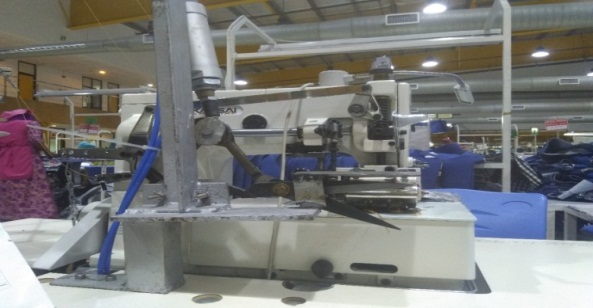 | Figure 3. Adding auto thread Cutter on a Kansai machine |
After attaching waist band by kansai machine loose threads comes, though Kansai machine doesn’t have auto thread cutting system that’s why after joining waist band loose threads needs to cut by hand. Operator dose this by hand cutter before. We are adding here one auto thread cutting automation, so that we can reduce the thread cutting time.Operation 3: Auto mouth cutterProcess: Waist belt mouth closeMachine: Self-made cutterMachine parts:• Air Cylinder• Compressed air • Steel Base• Air Pipe• Air trigger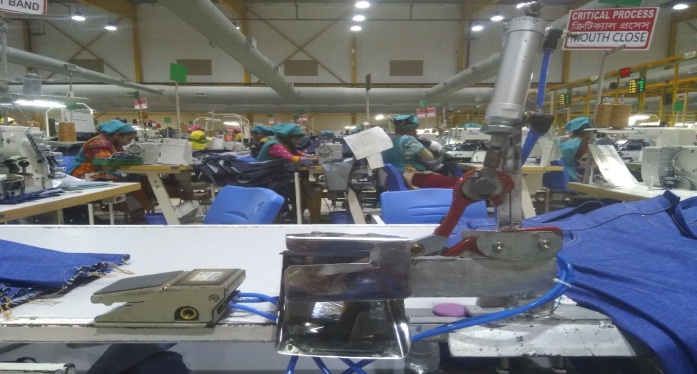 | Figure 4. Auto Mouth Cutter |
For doing Waist band mouth close operation extra fabric piece needs to cut by hand cutter. We are added automation here to increase the helper capacity, also easier the process and savings the cutting time.Operation 4: Auto hem cutterProcess: Hem cutting for Distortion effect Machine: OverlockMachine parts:• Vertical Knife• Plastic Base 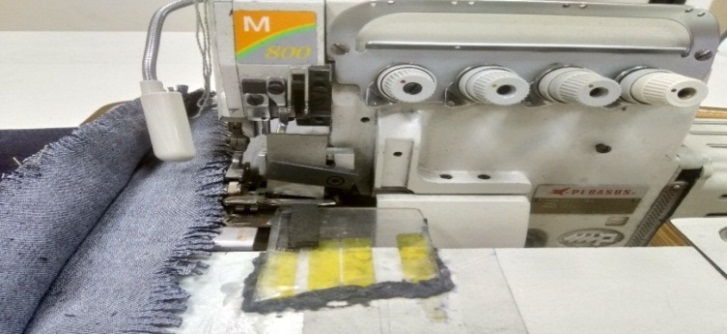 | Figure 5. Auto hem cutter |
Buyer requirement was to bring distortion effect in bottom hem by wash, but at first hem needs to cut so that it creates a distortion effect after washing. This process is too slow, a lot of manpower needed. We are innovating a easier way to cut it by overlock machine including a vertical knife.Operation 5: Auto Pocket hem foldingProcess: Back Pocket Hem Machine: Single Needle Chain Stitch machineMachine parts:• Air Cylinder• Compressed air• Steel Base plate• Air Pipe• Air trigger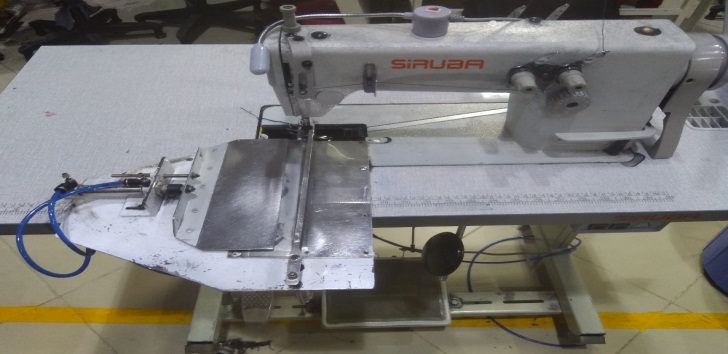 | Figure 6. Auto pocket turner |
For attaching back pocket, at first back pocket mouth position have to fold by hand thus it consumes time. So we are adding a automation to fold the pocket automatically.
2.2. Methodology (Working Flow Chart)
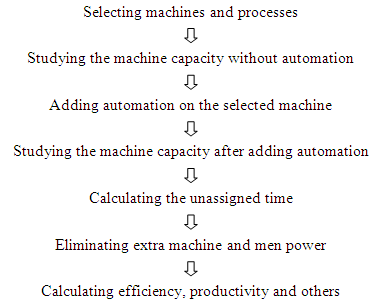
3. Data Analysis
Daily Production target 150pcs/hr needed to beat the lead timeTarget in 100% efficiency=60/SMVCapacity=3300/Actual cycle time (5mins was allowance time)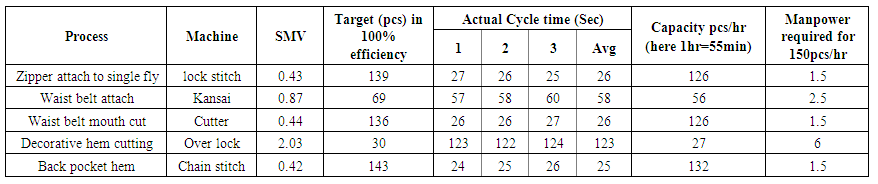 | Table 1. Capacity before Adding Automation |
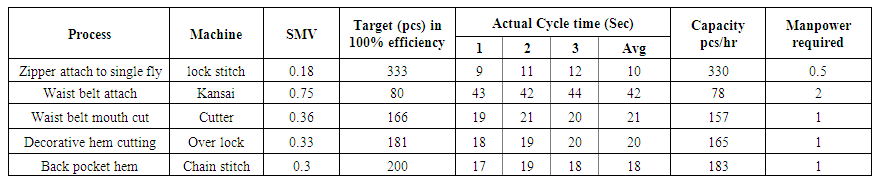 | Table 2. Capacity after Adding Automation |
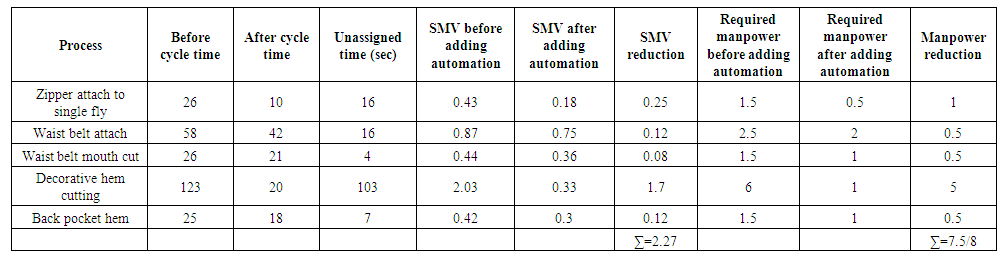 | Table 3. Calculation of Unassigned time, SMV and Manpower reduction |
4. Results and Discussions
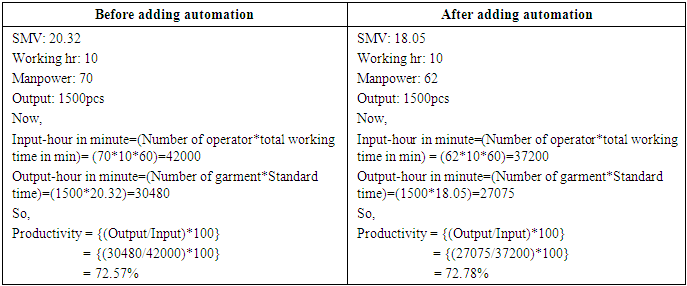
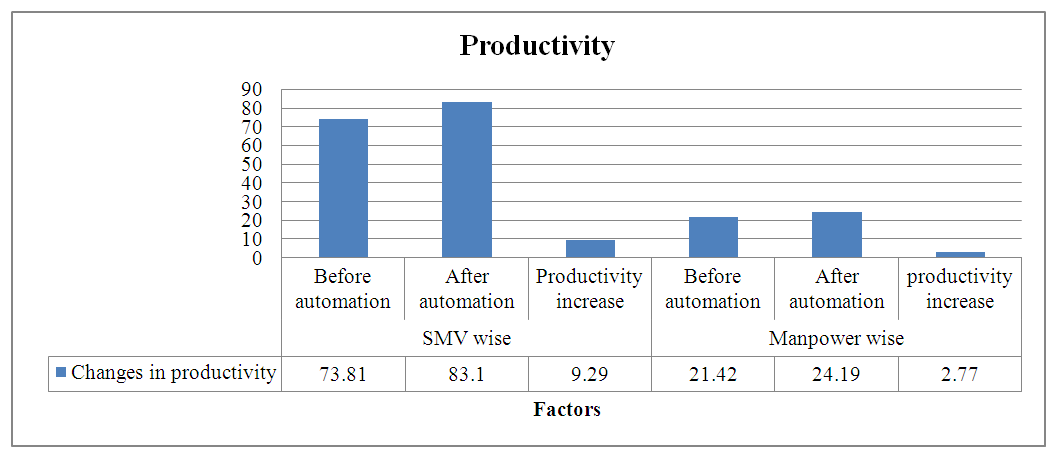 | Figure 7. Productivity changes in SMV wise and manpower wise |
Figure 7 shows productivity changes in SMV wise and manpower wise before and after adding automation. Productivity increase 9.29 in SMV wise and 2.77 in manpower wise.
5. Conclusions
To meet and beat the buyer’s lead time, machine automation has no alternate. In our country, the order quantity is increasing day by day but the lead time and price of the product are decreasing. So, it’s high time to introduce and implement lean manufacturing and machine automation as well.In this part we want to summarize our work and also point out our findings;We implement different automation in five operations in this work these are-i. Auto disposer to attach zipper with single ply, ii. Auto thread cutter in waist belt attachment, iii. Auto mouth cutter in waist belt mouth cut, iv. Auto hem cutter in hem cutting for distortion effect, v. auto pocket hem folding for back pocket hem joining. All these effort increase the productivity by reducing the cycle time and ultimately saves huge cost in respect of by reducing SMV and operator. Our findings are:- Sewing SMV reduces to produce primark short pant from 20.32 to 18.05.- The number of operators is reduced from 70 to 62 after adding automation.- Line productivity increases from 72.57% to 72.78% after adopting automation.- The effect of automation is also considered in terms of productivity in SMV wise and Manpower wise. The productivity in terms of SMV is increased from 73.81 to 83.1 which is about 12.6% and in respect of manpower, the productivity reaches from 21.42 to 24.19 which is also about 12.93%.Thereby we can conclude that there is a remarkable improvement in cost and productivity by introducing very simple existing technology and locally available equipment. Our main focus is to increasing the productivity by existing technique and parts without purchasing a full automatic machine.
6. Limitations
- We cannot provide actual costing of automation because of company privacy.- Further research can be done in this respect.
ACKNOWLEDGEMENTS
We acknowledge to all the members of IE and maintenance & mechanical department of Soorty denim enterprise for their kind co-operation.
References
[1] | Kabeer, N., & Mahmud, S. (2004). Rags, riches and women workers: export-oriented garment manufacturing in Bangladesh. Chains of fortune: Linking women producers and workers with global markets, 133-164. |
[2] | http://www.bgmea.com.bd/home/pages/tradeinformation. |
[3] | Ahmed, N. (2009). Sustaining ready-made garment exports from Bangladesh. Journal of Contemporary Asia, 39(4), 597-618. |
[4] | Mustafa A., Locating defects on shirt collars using image processing, International Journal of Clothing Science & Technology, Vol.10, 1998, 365– 378. |
[5] | Key Factors Affecting Productivity in Workplace, https://www.sinnaps.com/en/project-management-blog/factors-affecting-productivity. |
[6] | https://www.productionmachining.com/columns/the-effects-of-automation-on-manufacturing. |
[7] | Suprit Borse, Venkatesh Shrinivasan, V.S. Shivankar; Improving the Garment Productivity by Using New Designs of Folder; International Journal on Textile Engineering and Processes ISSN 2395-3578 Vol. 2, Issue 2; April 2016. |
[8] | Global Scenario of Automation in Garment Industry; http://fashion2apparel.blogspot.com/2018/02/automation-garment-industry.html. |
[9] | Md. Monirul Islam (Rajib), ATM Adnan (2016). Improving Ready-Made Garment Productivity by Changing Worker Attitude. European Scientific Journal, vol.12, No.4 ISSN: 1857 – 7881 (Print) e - ISSN 1857- 7431. |
[10] | Dhanashree Rajput, Madhuri Kakde, Pranjali Chandurkar, P. P. Raichurkar. Enhancing Efficiency and Productivity of Garment Industry by Using Different Techniques. International Journal on Textile Engineering and Processes Vol. 4, Issue 1. |
[11] | Dheeraj Nimawat and Ashish Shrivastava, Increasing Productivity through Automation. European Journal of Advances in Engineering and Technology, 2016, 3(2): 45-47, ISSN: 2394 - 658X. |