Md. Zayedul Hasan 1, A. K. M. Ayatullah Hosne Asif 1, Md. Abdullah Al Mamun 1, Priti Sarker 1, S. M. Farhana Iqbal 2
1Department of Textile Engineering, Mawlana Bhashani Science and Technology University, Tangail, Bangladesh
2Department of Yarn Engineering, Bangladesh University of Textiles, Dhaka, Bangladesh
Correspondence to: A. K. M. Ayatullah Hosne Asif , Department of Textile Engineering, Mawlana Bhashani Science and Technology University, Tangail, Bangladesh.
Email: |  |
Copyright © 2018 The Author(s). Published by Scientific & Academic Publishing.
This work is licensed under the Creative Commons Attribution International License (CC BY).
http://creativecommons.org/licenses/by/4.0/

Abstract
Crinkling or resin washing is one of the major dry process techniques that are done on almost all fashionable denim trousers. Generally crinkling means to form wrinkle in the specific position of the denim trouser by applying resin, then wrinkle formation and finally by curing. But resin changes the physical properties such as stiffness, weight loss due to abrasion, tensile strength etc. In this research work, four denim fabric of different GSM (gm/m2) were taken and then resin was sprayed on them randomly as simulating the actual resin spraying process that is done for resin wash or crinkling process. Then different physical properties of those denim fabrics were measured. These physical parameters were evaluated by different tests specifically bending length measurement, tensile strength test etc. These tests result gives a clear concept that, after resin spraying denim fabric gets stiffer, harsh and abrasive, more brittle that may affect the durability of the life time of denim garments.
Keywords:
Dry process, Denim, Vintage, Right handed twill, Stiffness
Cite this paper: Md. Zayedul Hasan , A. K. M. Ayatullah Hosne Asif , Md. Abdullah Al Mamun , Priti Sarker , S. M. Farhana Iqbal , Effect of Resin Finish for Crinkle Appearance on Bending and Tensile Properties of Denim Fabrics, International Journal of Textile Science, Vol. 7 No. 3, 2018, pp. 75-81. doi: 10.5923/j.textile.20180703.03.
1. Introduction
Garments’ washing is one of the finishing methods applied on garment, with the use of new technologies and equipment enables to obtain the desired results [1]. For finishing of denim garments a range of treatment methods such as enzymatic treatment, bleaching treatment, acid treatment and silicon treatment are used widely [2-4]. They all are aimed at new possible effects of fabric appearance. Different types of washing technique can be done to introduce vintage look in denim garments [5]. Particularly the dry washing creates many effects on denim fabric, it will stimulate the customers to buy and also it increases the market potential of the denim market [6]. Crinkling is one of the common dry process techniques. It is also known as resin washing. Crinkling means to form wrinkle in the specific position of the denim trouser by applying resin, then wrinkle formation and finally by curing [7, 8]. A wrinkle, also known as a rhytide, is a fold, ridge or crease in the cloth or garments [9]. In modern textile industry, different types of knit garments like T-shirt, Polo shirt and trouser also washed by using different techniques such as enzymes wash, softener wash, Silicone wash, tie dye wash, pigment wash, caustic wash, etc. are used to improve the physical and mechanical property changes [10-12]. Acid washing in garments comprised with knit structure is a new technique which is done by potassium permanganate and pumice stone or other substitutes [13-14]. Wrinkle gives fabric a vintage and aged appearance. The wrinkled jeans look is created with chemicals and machines that manipulate the denim fabric and wrinkle it in the desired areas [15]. Resins are viscous liquids that are capable of hardening permanently [16]. Resins mainly full into two groups; one is deposition type of resins. This type of resins is deposited on the fabric as surface coating. No reaction will take place between the fiber and resin. They include phenol-formaldehyde resin, urea formaldehyde resin, alkyl resins, vinyl resins and another is cross linking type of resins. These types of resins chemically react with the fiber and cross link the fiber molecules [17]. Resin and its use in denim garments industry create unique and vintage looks (crinkle effect) which add value to denim garments and improves it credibility in market. In 80’s resin being used to give non press, iron free trousers and now it is being used in denims to make wrinkles and creases to look natural vintage which stays after multiple home laundries [18-19]. Various effects of change while changing concentration of KMnO4 and processing time on physico-mechanical properties of denim jeans during acid washing reflected that the tensile strength, seam strength, stiffness and fabric weight were decreased after application of potassium permanganate with increasing processing time during washing treatment while yarn count (Ne), EPI, PPI and dimensional change were increased [20]. So, that new fashion can be achieved, but on the contrary some characteristics of the denim such as stiffness, abrasion resistance, tensile strength, crease recovery angle may also be changed. As a result, characteristics and quality of final denim product may be changed from its initial state. But, the buyers are not significantly concerned about that fact. So, the buyer should be aware of these changes in denim garments due to crinkling, because life cycle of garments may also be lessened due to resin washing or crinkling. This research work will discuss about the effect of resin finish (crinkle appearance) on physical properties of denim. The aim of the present work will be on the study about resin spraying process for crinkling. Calibration of tensile strength, stiffness before and after sample of different denim fabrics will be done in order to evaluate the change of different properties due to resin wash.
2. Materials and Method
In this research work, four different types of denim fabrics were used.
2.1. Materials Used
Table 2.1. Specification of different fabric samples 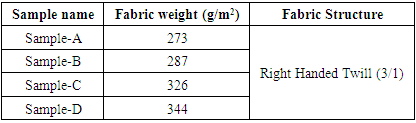 |
| |
|
2.2. Specification of Resin
Table 2.2. Specification of resin along with technical perspectives  |
| |
|
2.3. Specification of U-Turn Conveyor Type
Continuous Curing Machine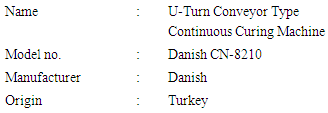
2.4. Specification of Shirley Stiffness Tester
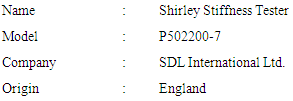
2.5. Specification of Martindale Abrasion and Pilling Tester
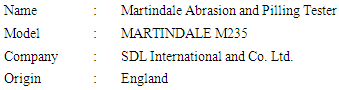
2.6. Specification of Tensile Strength Tester
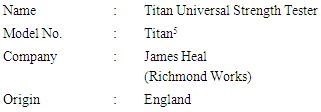
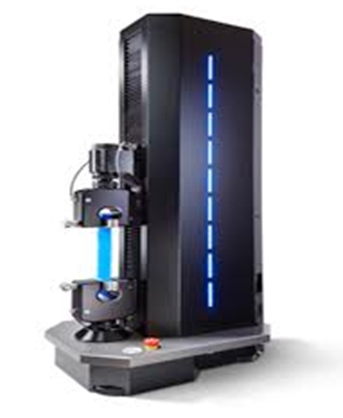 | Figure 2.1. Universal Strength Tester (James Heal) |
2.7. Methodology
2.7.1. Sample Preparation
At first, the denim fabrics of four different GSM (gm/m2) were taken and placed the fabrics of different type one after one on a table. According to the test methods, fabrics are marked by a chalk following the sizes required. With the help of scissors fabrics are cut according to the marked line. Thus samples are prepared for different test methods. Then tests are done.
2.7.2. Resin application Procedure
 | Figure 2.2. Process flow diagram for resin application |
2.7.3. Test Methods
Determination of Bending Length Test Method: BS 3356:1990 Principle: A form of the cantilever stiffness test is often used as a measure of a fabric's stiffness as it is an easy test to carry out. In the test a horizontal strip of fabric is clamped at one end and the rest of the strip allowed hanging under its own weight. When the tip of the specimen reaches a plane inclined at 41.5° below the horizontal the overhanging length is then twice the bending length. This angle is used in the Shirley apparatus to increase the sensitivity of the length measurement and the slide on this instrument is directly calibrated in centimeters. For bending length measurement sample size is (6 inch ×1 inch).Procedure: At first specimen was laid on a smooth horizontal surface terminated at one end by a straight edge, so that the length of specimen was at right angles to, and one end was level with, that edge. Then the specimen was moved lengthwise over the edge at a uniform rate of approximately 25mm in 5second, until the end of the specimen was come into line with the two positions. The length of fabric protruding beyond the edge was measured. The other face of the same end of the specimen was made a similar determination with uppermost. The others samples were tested in the same way [21].Determination of Fabric StrengthTest Method: ASTM D5034-09Principle:This method covers the grab and modified grab test procedures for determining the breaking strength and elongation of most textile fabrics. Provisions are made for wet testing. The grab test procedure is applicable to woven, nonwoven, and felted fabrics, while the modified grab test procedure is used primarily for woven fabrics. This test method is not recommended for glass fabrics or for knitted fabrics and other textile fabrics which have high stretch (more than 11%). This test method provides the values in both inch-pound units and SI units. An inch-pound unit is the technically correct name for the customary units used in the United States. SI unit is the technically correct name for the system of metric units known as the International System of Units. Each specimen were cut 100±1 mm (4±0.05 in.) wide by at least 150 mm (6 in.) long with the long dimension parallel to the direction of testing and force application [22].Procedure:Specimens were mounted in the clamp jaws with the previously drawn parallel line adjacent to the side of the upper and lower front, or top, jaws which is nearest this edge, and with approximately the same length of fabric extending beyond the jaw at each end. The parallel line serves as a guide to ensure that the same lengthwise yarns of woven fabrics are gripped in both clamps and that the force application is not at an appreciable angle to the test direction of nonwoven fabrics. The tension on the specimen should be uniform across the clamp width. For high-strength fabrics where the specimen cannot be satisfactorily held in clamps, place each specimen around pins and between jaws as illustrated in. Tighten the clamps to distribute the holding pressure along the clamping surface of the top (front) jaw. Clamps which are too tight will produce breaks at the front of the jaws; clamps which are too loose will cause slippage or breaks at the back of the jaws.
3. Results and Discussion
Effect of resin finish for crinkle appearance on physical properties of denim fabrics are constituted by specifically for bending length and tensile properties of that respected sample. Results and discussion of resin treatment on different types of denim fabrics based on before and after treatment to observe change in bending length and tensile strength are presented below:
3.1. Analysis of Bending Length
Bending length of Sample-A in warp and weft direction is shown in figure indicate change of bending length as function of resin treatment between before treatment and after treatment on receptive denim fabric sample.
3.1.1. Bending Length of Sample–A (273 g/m2)
From figure 3.1, it has been observed that, resin treatment has significant influence on bending strength of 273 g/m2 fabric sample. Highest bending length was achieved at back side of the respective fabric sample along with warp direction. Bending length of sample A along with its back side of the fabric is increased after resin treatment. The greater bending length along the warp direction of the fabric tells us that the fabric more stiff in the warp direction than in the weft direction. This can be due to the result of fabric density which is more in the warp direction of the then the weft direction.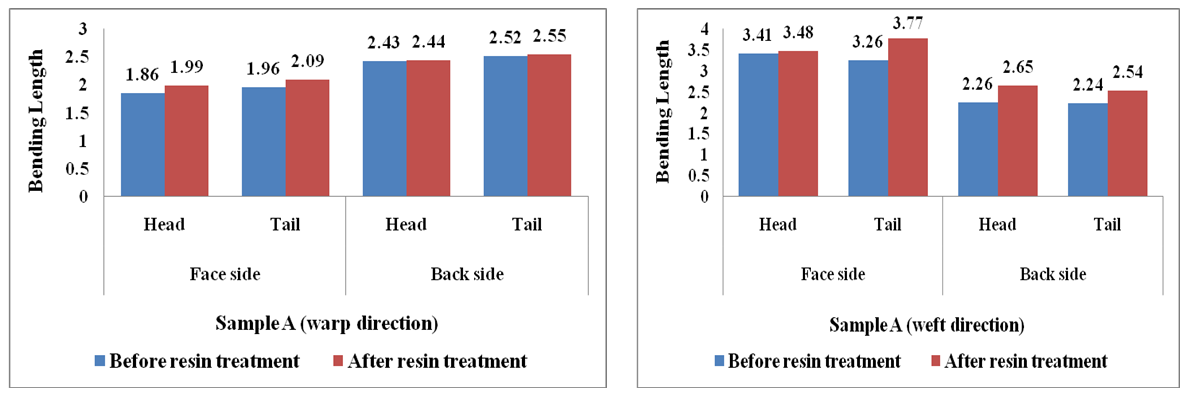 | Figure 3.1. Bending length of Sample-A in warp and weft direction |
3.1.2. Bending Length of Sample–B (287 g/m2)
From figure 3.2, it has been observed that, resin treatment has significant influence on bending strength of 287 g/m2 fabric sample. Highest bending length was achieved at face side of the respective fabric sample along with warp direction. Bending length of sample B along with its face side of the fabric is increased after resin treatment. The greater bending length along the warp direction of the fabric tells us that the fabric is stiffer in the warp direction than in the weft direction. This can be due to the result of fabric density which is more in the warp direction then the weft direction.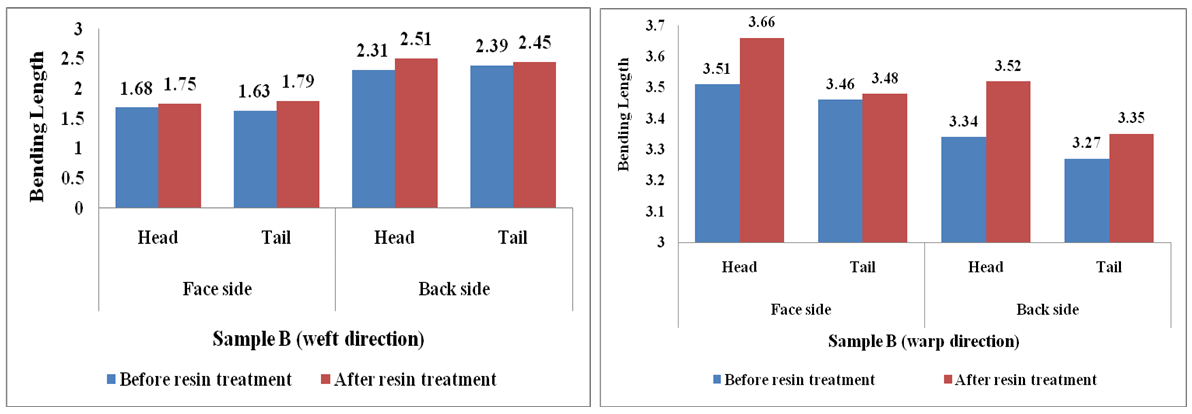 | Figure 3.2. Bending length of Sample-B in warp and weft direction |
3.1.3. Bending Length of Sample–C (326 g/m2)
From figure 3.3 and 3.4, it has been observed that, resin treatment has significant influence on bending strength of 326 g/m2 fabric sample. Highest bending length was achieved at face side of the respective fabric sample along with weft direction. Bending length of sample C along with its face side of the fabric is increased after resin treatment. The greater bending length along the weft direction of the fabric tells us that the fabric more stiff in the weft direction than in the warp direction.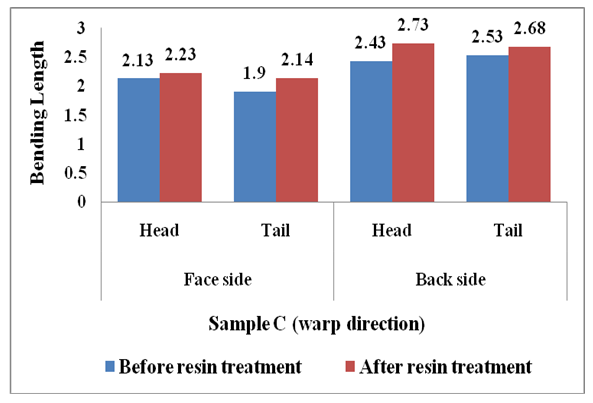 | Figure 3.3. Bending length of Sample-C in warp direction |
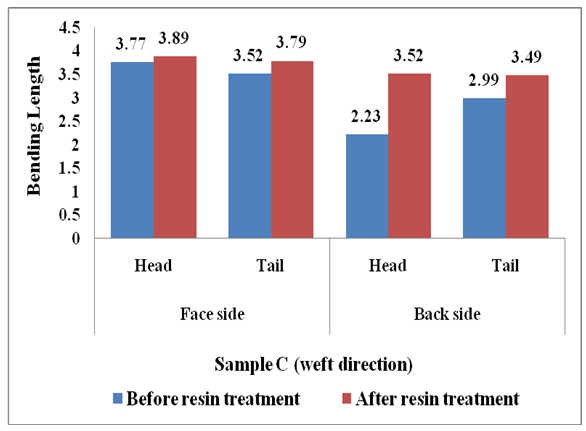 | Figure 3.4. Bending length of Sample-C in weft direction |
3.1.4. Bending Length of Sample–D (344 g/m2)
From graphs 3.5 and 3.6, it has been observed that, the bending length of different samples is increased after the resin spraying. It indicates that after resin spraying, stiffness of fabric is also increased. The reason behind the increasing of bending length is that, at the time of curing hydroxyl groups of cellulose forms covalent bond with the cross-linking agent in high temperature. So that the cross sectional area of fibre is also increased and other factors remain same which results in the increase of stiffness of denim fabric.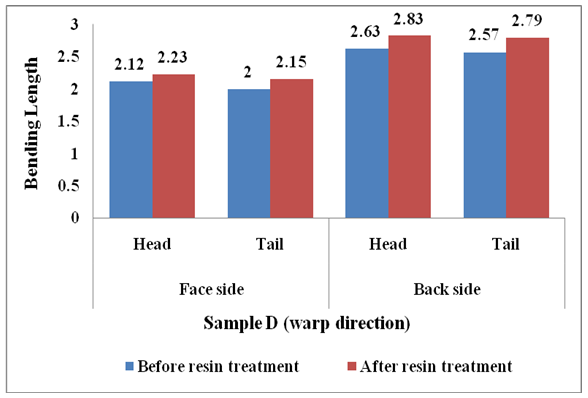 | Figure 3.5. Bending length of Sample-D in warp direction |
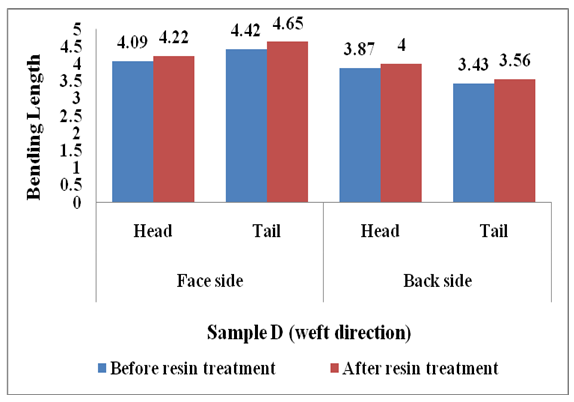 | Figure 3.6. Bending length of Sample-D in weft direction |
3.2. Analysis of Tensile Strength
Tensile strength of different samples of denim fabrics in warp and weft direction are shown in tables and figures indicate change of tensile strength as function of resin treatment between before treatment and after treatment on receptive denim fabric samples. | Table 3.1. Tensile strength of sample –A, B, C and D (both before and after resin treatment) in warp direction |
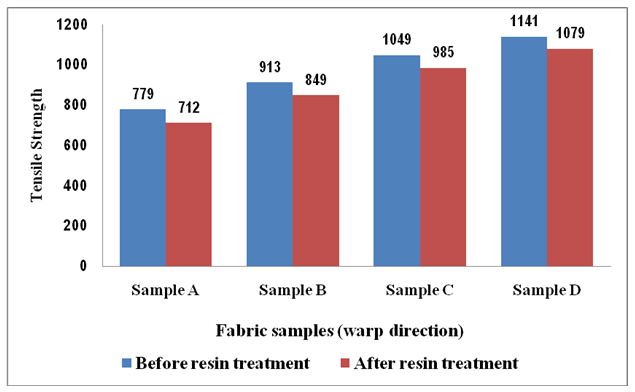 | Figure 3.7. Tensile strength of sample –A, B, C and D (both before and after sample) in warp direction |
 | Table 3.2. Tensile strength of sample –A, B, C and D (both before and after resin treatment) in weft direction |
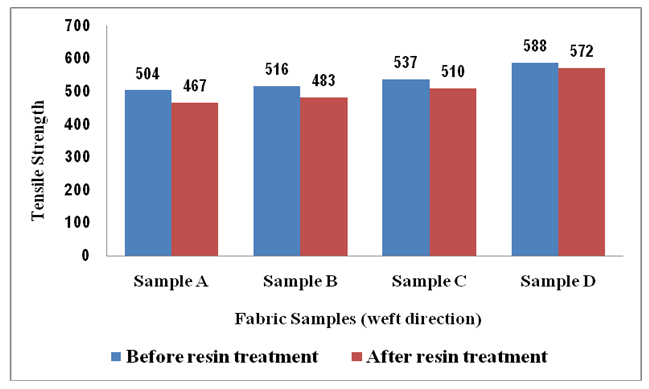 | Figure 3.8. Tensile strength of sample –A, B, C and D (both before and after resin treatment) in weft direction |
From above results and graph, it has been observed that, tensile strength decreases gradually for the entire sample after resin spraying. It indicates that, in warp direction for sample –A, tensile strength decreases about 8.61%, for sample–B it decreases about 7.02%, for sample–C it decreases about 6.12% and for sample–D it decreases about 5.42%. Again in weft direction, for sample –A tensile strength decreases about 7.43%, for sample –B it decreases about 6.51%, for sample –C it decreases about 5.17% and for sample –D it decreases about 2.67%. The causes behind the tensile strength losses are; after resin spraying, the samples became stiffer and brittle. That’s why it takes less force to break the warp yarn after resin sprayed on the sample than the before resin sprayed sample.
4. Conclusions
From this study, it has been observed that after resin spraying on denim fabric, it became stiffer and its surface became harsh. As a result some physical properties specifically bending length and tensile strength of denim fabric also changed. From this study, it has been found that the stiffness, tensile strength of denim fabric is decreased. All this changes occurred gradually by keeping a linear relation with the denim sample of different g/m2. This research work has been performed to draw the attention of buyer to the fact that, if resin is used for crinkling and other fashion purpose like wrinkle formation or any other process, it changes the physical properties of actual fabric; as a result the durability or lifetime of garments will also be decreased. So, buyer should be concerned about the garment’s quality which will be deteriorated if crinkling is done for fashion purposes. As denim fabric is used for manufacturing high performance and long durable garments but crinkling decreases its performance rate and durability, which is fully opposite to the actual purpose of denim garments.
References
[1] | Juciene, M., Dobilaite, V., and Kazlauskaite, G. (2006). Influence of industrial washing on denim properties. Materials science, 12(4), 355. |
[2] | Mondal, M.I.H. and Khan, M.M.R. (2014). Characterization and process optimization of indigo dyed cotton denim garments by enzymatic wash. Fashion and Textiles, 1(1), pp: 1-12. |
[3] | Khan, M.M.R., Mondal, and Uddin, M.Z. (2013). Sustainable washing for denim garments by enzymatic treatment. Journal of Chemical Engineering, 27(1), pp: 27-31. |
[4] | Joy Sarker, Elias Khalil, M.S. (2014). Effect of Enzyme washing combined with pumice stone on the physical, mechanical and color properties of denim garments. International Journal of Research in Advent Technology, 2(9), pp: 65-68. |
[5] | Khan, M.M.R., Mondal, M.I.H., Uddin, M.Z. (2011). Effect of bleach wash on the physical and mechanical properties of denim garments. International Conference on Mechanical Engineering (Vol.3). |
[6] | Sarker, J. and Khalil, E. (2014). Effect of industrial bleach wash and softening on the physical, mechanical and color properties of denim garments. IOSR Journal of Polymer and Textile Engineering, 1(3), pp: 46-49. |
[7] | Haq, U.N., M.M.R. (2014). Technology of acid wash on woven denim apparel with damp pumice stone. International Journal of Science, Environment and Technology. Vol.3, No. 6, pp: 2090-2095. |
[8] | Mazumder, S (2010). Effects of sand blasting with industrial enzyme silicon wash on denim apparel characteristics. Daffodil International University Journal of Science and Technology, 5(1), pp: 6-9. |
[9] | Denim Dry Finishing: Flourishing the value of denim By Aravin Prince Periyasamy, Govardhana Rao Chilukoti and K. Thavasiappan retrieved from www.fibre2fashion.com. |
[10] | Resin Treatments: Giving Value addition to Vintage Denim garments, By Sandeep Agarwal, Retrieved from http://www.denimsandjeans.com/. |
[11] | Wrinkle finishing technique by Azmir Latif, retrieved from http://www.slideshare.net/. |
[12] | H. L. Yi (2012). A study of the resin finishing on wrinkle property of light weight 100% cotton plain fabric. Institute of Textiles and Clothing, Hong Kong Polytechnic University. |
[13] | Solaiman, M., Rahman, M.M., Khalil, E. and Sarkar, J. (2014). Consequences of Enzyme Rinse on Physical Properties of Knit Garments. International Journal of Research in Advent Technology, 2, pp: 112-116. |
[14] | Islam, M. Types of Wash Applied on Knit Garments. Retrieved on 31 January 2016. |
[15] | Gokarneshan, N., Durairaj, C., Krishnamurthy, P., Shanmugasundaram, S., Subhash, R. and Su, P. (2009). Chemical Finishing and Washing of Knit Wear. |
[16] | Resin Finishing, By Aravin prince, retrieved from https://www.scribd.com. |
[17] | Rahman, M.S. (2014). Practical Handbook of Washing and Dyeing. University Campus Publishing, Dhaka, 73. |
[18] | Zhao, W.B. (2008). Common Denim Washing Technologies. Dyeing Finish, 34, 34-36. |
[19] | Khalil, E. and Islam, M.M. (2015). Wrinkle Finish on Denim by Resin Treatment: A Review. AASCIT Communication, 2, pp: 82-87. |
[20] | Khalil, E., Rahman, A. and Solaiman, M. (2015). Investigation on Simultaneous Effect of KMnO4 Concentration and Processing Time on Tensile Strength, Weight and Stiffness of Denim Jeans During Acid Washing with Pumice Stone. International Journal of Research and Review, 2, pp: 546-550. |
[21] | BS 3356:1990. Method for determination of bending length and flexural rigidity of fabrics. |
[22] | ASTM D5034 – 09 (2013). Standard test method for breaking strength and elongation of textile fabrics (Grab Test). |