Shahriar Raian 1, Iftay Khairul Alam 2, Md. Lutfor Rahman 3, Mohammad Rashel Hawlader 4, Tanzeena Refat Tumpa 2
1Department of Textile Engineering, Ahsanullah University of Science and Technology, Dhaka, Bangladesh
2Department of Textile Engineering, Euproean University of Bangladesh, Dhaka, Bangladesh
3Department of Textile, Ahsanullah Institute of TVET, Dhaka, Bangladesh
4Department of Textile Engineering, Northern University Bangladesh, Dhaka, Bangladesh
Correspondence to: Shahriar Raian , Department of Textile Engineering, Ahsanullah University of Science and Technology, Dhaka, Bangladesh.
Email: |  |
Copyright © 2018 The Author(s). Published by Scientific & Academic Publishing.
This work is licensed under the Creative Commons Attribution International License (CC BY).
http://creativecommons.org/licenses/by/4.0/

Abstract
This paper reveals some information regarding quality profiles of rotor spun yarn mainly mass irregularity values (Unevenness in terms of mass Um%, various imperfection value (Thick places, Thin places, Neps, Imperfection Index (IPI), Hairiness (H) and bundle yarn strength (Count-Strength-Product CSP) in respect to change in different rotor speed. To carry out this research several open end yarns of 20 Ne were spun from the same raw material, same roving and on the same drums of the same rotor frame by keeping the doff length and all other machine parameters constant except feed roller speed. Then by using different rotor speed, the changes of above mention quality parameters were observed. In every case with the increase of rotor speed the quality profiles such Um%, CVm% and imperfection index declined but the improved values were obtained interms of H and CSP. It can be predicted the compact structure, wrapping fibers and higher centrifugal force because of higher rotor speeds are the responsible for obtaining better CSP and hairiness values. For each quality parameters in relationship with variation of rotor speeds both coefficient of determination and single linear regression analysis were also established. At last using all the parameters a multiple regression equation was established.
Keywords:
Open End (OE) yarns, Rotor Speed, Single and Multiple Regression Equation
Cite this paper: Shahriar Raian , Iftay Khairul Alam , Md. Lutfor Rahman , Mohammad Rashel Hawlader , Tanzeena Refat Tumpa , A Pairwise Comparison among Different Quality Parameters of Rotor Spun Yarn with Changing in Different Rotor Speeds by Using Regression Analysis, International Journal of Textile Science, Vol. 7 No. 3, 2018, pp. 69-74. doi: 10.5923/j.textile.20180703.02.
1. Introduction
In the last few decades the scientific and technical progress influenced the textile industry all over the world [1]. The rising global competitiveness, high-quality and cost-saving kind of spinning method have become a major issue in the textile industry [2]. It is more competitive than ever as innovation is taking place regularly. To keep space with manufacturers have to produce more sophisticated, less expensive, machines with higher and higher production rates to make them economically and commercially viable [3]. Spinning is one of the most important production processes in the field of textile science [4]. Spinning is a complicated procedure to convert fibers into yarn through many investigations with some new technological and technical process [5]. Spinning technology is much more developed now a days with various spinning methods such as ring spinning, air vortex spinning, friction spinning, disc spinning, solo spun spinning, siro spinning, air jet spinning, wrap spinning and rotor spinning. Now days in competition with ring spun yarn, the production of open end yarns such as rotor spun yarn is increasing significantly because of many quality parameters issues and productivity. From the point of higher productivity with some others property spinning technologies such as rotor, air jet and friction spinning have tremendous potential [6]. Depending on the different arrangement of fibers in each spinning system, the physical and mechanical properties of yarns vary [7]. In rotor spinning it is possible to produce better quality yarn from very poor grade of cotton and even from wastage among other process. Another few important dimensions like reduction in space, process and personnel have given rotor a new era to produce uniform and regular cotton yarn. Rotor spinning is a recognized spinning system mainly for medium and course counts [8]. This technology has gained the reputation of being ‘cotton friendly’, since two-thirds of all fibres used in rotor spinning are cotton [9]. Now a day, the competitive edge of rotor spinning is reflected in the implementation of faster rotor-spinning speeds, more sophisticated monitoring and control systems, and automatic start-up, doffing, cleaning, and repiecing devices. The strength of Rieter’s rotor spinning lies not only in its high productivity but also its great flexibility in terms of raw material and yarn construction. The special feature of the fully-automated rotor spinning machine producer is to achieve highest productivity and lowest energy consumption.Considering above advantages there are also some disadvantages of rotor spinning such as the production of finer yarns. As the yarn count becomes finer, the production advantage of open-end spinning over ring spinning is less. From an engineering point of view, it was observed that open-end rotors can be operated at high speed but most studies shows that high speed damage yarn qualities. In ring spinning, spindle speeds can be increased for finer counts, but the trend in open-end spinning is the opposite [10].A numerous studies have been conducted on rotor spinning, its different parameters, rotor spun yarn qualities and the effect of different fiber parameters.In 1975 Grosberg and Mansour found the properties of yams spun in the speed range from 30,000 to 100,000 rev/min [11].In 1977 Barella and Vigo studied on an application of mini-computers to the optimization of the open-end-spinning process and the influence of the partial drafts between the opening roller and the rotor and the total draft and doubling on the breaking elongation and quality index of open-end-spun viscose staple-fibre yarns [12].In 1978 Jack & Murray concluded on effect of cotton fiber fineness and strength on mechanical processing and open-end spinning and yarn properties to determine their effect on open-end spinning and yarn properties [13].In 1981 Bartuska and Maciel studied on magic-angle spinning system for bullet-type rotors in electromagnets [14].In 1992 Ishtiaque conducted research on Spinning of synthetic fibres and blends on rotor-spinning machine with the discussion of optimization of surface characteristics and physical properties of man-made fibres [15].In 2002 Farshid et. al threw light on spinning conditions and characteristics of open-end rotor spun hybrid yarns [16].In 2006 a study conducted by Pınar Duru Baykal, Osman Babaarslan and Rizvan Erol based on the study to predict both strength and elongation properties of rotor yarn of cotton/polyester-blended to determine the combinations of the fibres mixture ratios using blend ratios and yarn count as predictors [17].The study of Kuo, Wei, Huang, & Su conducted in 2010 based on optimization of processing parameters of multiple quality characteristics of open-end rotor spinning process using bamboo, charcoal and cotton 70%/ polyester 30% (CVC) blended fibers [18].In 2011 conducted research on optimization of open-end rotor spinning frame parameter and estimation of relevant quality characteristics using Lyocell fibers are used to spin the Ne 32 yarns. In 2012 Fallahpour and Moghassem used a multi-criteria decision making named VIKOR method for evaluating parameters selection problem among available alternatives with different significances in rotor spinning.
2. Materials and Methods
2.1. Materials Used
Like others rotor spun yarns mixing of wastages, found in different stages was used with some extent of virgin raw cotton. Here a variety of Indian cotton named Shanker-6 with some other wastages, selected. Their specifications with mixing ratio is given as below:Table 2.1. Specification and mixing ratio of raw materials 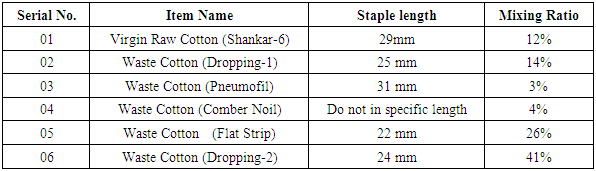 |
| |
|
2.2. Machine Specification
Same Rotor Spinning Frame is used to produce the open end yarn with varying rotor speed. The details specification is given below table.Table 2.2. Specification of Rotor Spinning Frame  |
| |
|
The following parameters are set to the Rotor Frame where all the values are constant except rotor speed. The figure 2.3 shows the specification of spinning particular.Table 2.3. Specification of Spinning Particulars 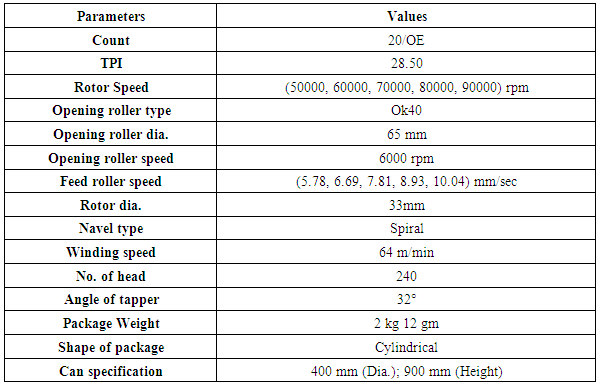 |
| |
|
2.3. Process Flow Chart of Rotor Spun Yarn
As like with rotor spinning process start with the proceesing in blowroom line then to carding and next to drawframe with only the exception that no use of simplex. Here drawn sliver is feed directly to rotor machine.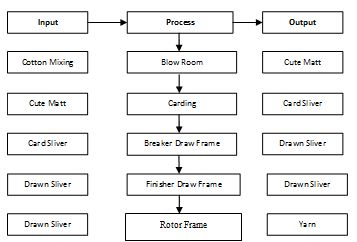 | Figure 2.1. Process Flow chart for manufacturing Rotor Yarn |
2.4. Methodology
The study was conducted on a rotor frame in a spinning mill (which produces rotor yarn) where 20 Ne rotor yarns were produced. After mixing properly with above mentioned ration the materials were fed into blowroom and then passed through carding, breaker draw frame and finisher draw frame. and at last to rotor spinning frame. From a fixed finisher draw frame five sliver can with sliver of equal length was collected and feed to five fixed drums of rotor spinning machine to produce rotor yarn keeping equal doff length with all other machine parameters as constant only. In rotor this process was done with 5 varying rotor speeds. The yarn samples were then taken to Quality Control Department for testing with Uster Tester-5 (UT-5) to get various test results like as Um%, CVm%, IPI and Hairiness. By using bundle yarn test tester CSP value was obtained. By using these obtained values in relationship with various rotor speed the appropriate construction of simple linear regression equation was carried out. Finally, multiple regression equations were established based on all the quality parameters with chang in rotor speeds.To get reliable test result with minimum variability 5 specific drums were used. The yarn tests were carried out on Evenness Tester (UT-5) by ASTM D1425-96 for Um% and hairiness by ASTM D 5647-01 and Lea Strength Tester by ASTM D 1578-93. Above all tests were done under standard atmospheric conditions 27 ± 2°C and 65% RH. Then by using both multiple and single regression analysis the correlation between rotor speed with yarn quality was observed and the construction of multiple regression analysis equations by using these variables.
2.5. Regression Analysis
Coefficient of Correlation is a statistical technique to measure the relationship between two variables known as a dependent and independent variable. The Dependent Variable is the variable being predicted or estimated where as the Independent Variable provides the basis for estimation. It is the predictor variable. Such as to determine the relationship between ring yarn properties and the fiber properties obtained by AFIS. A Scatter Diagram is used to portray the relationship between two variables. It is denoted by R. It varies from -1 to +1. Coefficient of Determination (R2) is the square value of Coefficient of Correlation. It varies from 0 to +1. Higher the value of R2, higher the relationship between them.
2.5.1. Single Regression Analysis
Simple (single) regression analysis simply indicates the value of a dependent variable is estimated on the basis of one independent variable whereas Multiple regression analysis is something which indicates the estimation of the value of a dependent variable in terms of two or more independent variables. Here, Y stands for dependent variable and X for the independent variable. 2.5.1.1. Single Linear Regression EquationRegression Equation is an equation that expresses the linear relationship between two variables.The general form of liner Regression Equation, Yi= a + bXi
2.5.2. Multiple Regression Analysis
In multiple linear correlation and regression, we use additional independent variables (denoted X1, X2…….and so on) that help us better explain or predict the dependent variable (Y). Almost all of the ideas we saw in simple linear correlation and regression extended with the additional independent variables do lead to some new considerations. 2.5.2.1. Multiple Regression EquationGeneral form of multiple regression equation, | (1) |
where, A = Y interceptX1, X2, ………………, Xn = Independent variables.
3. Results and Discussions
The different quality parameters have been found by varying rotor speed are listed below table number 3.1.Table 3.1. Effect of Rotor Speed on Different Yarn Qualities 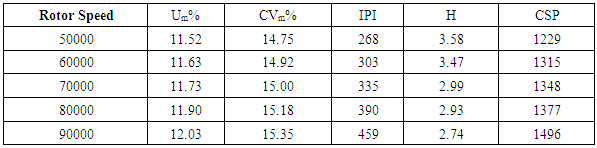 |
| |
|
3.1. Impact of Um% on Rotor Speed
The below graph shows the Um% of rotor yarn samples produced with different rotor speed. It is showed that Um% increases slightly with the increase of rotor speed. Feed speed increases with the increase of rotor speed. But opening roller speed remain constant. Therefore, the draft on the material between the feed roller and combing roller gets reduced with higher rotor speed. That’s why proper opening was hampered. As a result opening quality deteriorated. This resulted in unevenness of yarn. Additionally, the increase in the rotor speed, the fiber feed also increases and uncontrolled feeding of fibers to rotor takes place which may cause haphazard lying of fiber in the rotor groove resulting to unevenness.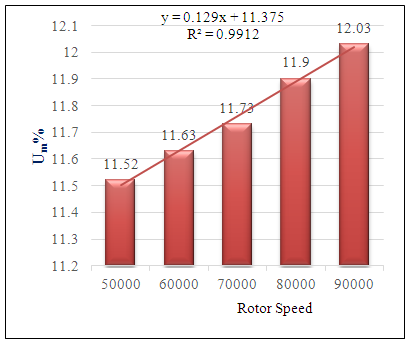 | Figure 3.1. Impact of Um% on Rotor speed |
3.2. Impact of IPI on Rotor Speed
Immature cottons have very much liability to produce neps during processing. However in terms of speed, combing roll speed and pneumofil percentage are significant factors in terms of 95% confidence level. It is seen that yarn imperfection has been increased with the increase of combing roll speed. The occurrence attributed due to impairment of fiber orientation in rotor groove during back doubling process because of increasing damaged fibers of higher speed. At higher speed fibers get less time to be straightened that will be resulted in poor fibers orientation in rotor groove. Ultimately, the graph also showed that yarn imperfections increased with the increase rotor speed. Further the number of wrappers which are closely wound increases in the rotor groove with the increased rotor speed. The closely wound wrappers are normally counted as imperfections in Evenness tester. | Figure 3.2. Impact of IPI on Rotor speed |
3.3. Impact of H on Rotor speed
This graph shows that the hairiness value decreased with the increasing of rotor speed. The centrifugal force increased with increasing rotor speed. As a result, the fibers became highly compacted in the rotor groove, resulting in highly compacted yarn structure. In a compact yarn structure, the loose fibers can be more effectively bound by the wrapper fibers and hence, the hairiness decreased with increasing rotor speed.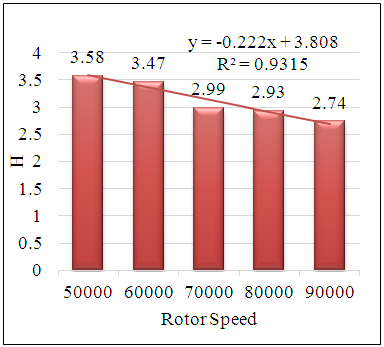 | Figure 3.3. Impact of HI on Rotor speed |
3.4. Impact of CSP on Rotor Speed
The graph shows that, when rotor speed increased CSP also increased. Because in terms of rotor spinning the strength of rotor spun yarn mainly depends on degree of compactness of the yarn. The compact structure can be wrapped easily by the wrapping fiber. The effect of wrapping fiber higher than the effect of thin, thick & neps on yarn. As a result, CSP increased with the increasing of rotor speed.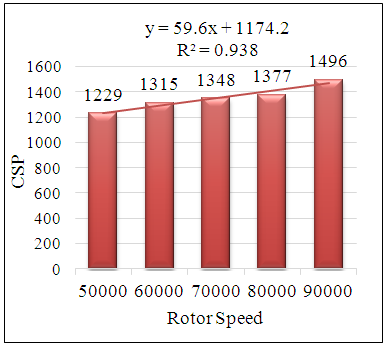 | Figure 3.4. Impact of CSP on Rotor speed |
4. Regression Analysis
By using the Excel software we can easily establish the different equation in regression both for single and multiple regression and the obtained R2 value indicates the strength of relationship between varying the rotor speeds with different rotor yarn quality parameters. Using all the quality parameters with varying rotor speed we can establish the multiple regression equation.Table 4.1. Single regression equations and the values of R2 and R for different relationship between rotor speeds and different quality parameters 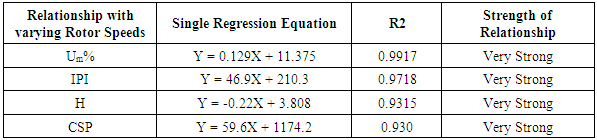 |
| |
|
4.1. Multiple Regression Equation
Y = - 916658 + 84189.9Um% -109.634IPI - 7613.85H + 43.4741CSP
5. Conclusions
Speed of a machine greatly influences the production as well as quality of the product. In case of a rotor spinning machine, rotor rpm is the parameter by which machine speed is set. In this study, we experimented with a view to assess it’s affect on the properties of the produced yarn. The increase of speed had a detrimental effect on the evenness and imperfection level of yarn as the performance of opening roller decreased with increasing material throughput rate. On the other hand improvements were observed in terms of yarn hairiness and yarn strength (CSP). This was attributed to the increase of centrifugal force which compacted the yarn body better into the groove and facilitated better enclosing by the wrapper fibers. Therefore, it can be concluded that the increase of rotor speed have a mixed impact on different quality parameters of the rotor spun yarn.In future, an extensive research can be done by taking other components with rotor speed and can be established different comparison using different Multi Criteria Decision Making (MCDM) like Fuzzy Analytical Hierarchy Process (FAHP) and other fuzzy logic.
Disclosure
No potential conflict of interest was reported by the authors.
References
[1] | Kasparek, J. V. (1992). Future prospects of rotor spinning. Indian Journal of Fibre & Textile Research, 17(12), 238–245. |
[2] | Taylor, P., Kuo, C. J., Kao, C., Wei, H., Kuo, C. J., Kao, C., & Wei, H. (2011). Optimization of Open-end Rotor Spinning Frame Parameter and Estimation of Relevant Quality Characteristics Optimization of Open-end Rotor Spinning Frame Parameter and Estimation of Relevant Quality Characteristics. Polymer-Plastics Technology and Engineering, 50(9), 923–930. |
[3] | Lawrence, A., & Chen, K. Z. (1984). Rotor-Spinning. Textile Progress, 13(4), 1-73. |
[4] | Fallahpour, A. R., & Moghassem, A. R. (2012). Evaluating Applicability of VIKOR Method of Multi-Criteria Decision Making for Parameters Selection Problem in Rotor Spinning. Fibers and Polymers, 13(6), 802–803. |
[5] | Strumiłło, L., Cyniak, D., Czekalski, J. & Jackowski, T. (2007). Quality of cotton yarns spun using ring, compact, and rotor-spinning machines as a function of selected spinning process parameters. Fibres & Textiles in Eastern Europe, 1 (60), 24-30. |
[6] | Salhotra, K. R. (1994). An overview of spinning technologies: Posibilites, applications and limitations. Man-Made Textiles in India, 37(4), 151–158. |
[7] | Erdumlu, N., Ozipek, B., Oztuna, A. S., & Cetinkaya, S. (2009). Investigation of Vortex Spun Yarn Properties in Comparison with Conventional Ring and Open-end Rotor Spun Yarns. Textile Research Journal, 79(7), 585–595. |
[8] | Mamun, R. A, Repon, R., Islam, M. T., & Motaleb, K. Z. M. A. (2017). Promising Effect of Processing Parameters on Yarn Properties in Rotor Spinning. Manufacturing Science and Technology, 4(1), 11–15. |
[9] | Kaplan, S.O. G. (2006). Investigation into Navel Selection for Rotor Spinning Machine Using Cotton Waste. Fibres & Textiles in Eastern Europe, 14(3), 58–62. |
[10] | Simpson, J., & Myles, A. (1979). Effect of Rotor Speed on Open-End Spinning and Yarn Properties. Textile Research Journal, 49(8), 468–473. |
[11] | Mansour, P. G. & S. A. (1975). High-speed open-end rotor spinning. The Journal of The Textile Institute, 66(11), 389–396. |
[12] | Vigo, A. B. & J. P. (1977). An Application of mini-computers to theoptimization of the open-end-spinning process part VII: the influence of the partial drafts between the opening roller and the rotor. Journal of Textile Institution, 12(12), 417–423. |
[13] | Simpson, J., & Murray, M. F. (1978). Effect of Cotton Fiber Fineness and Strength on Mechanical Processing and Open-End Spinning and Yarn Properties. Textile Research Journal, 48(5), 270–276. |
[14] | Bartuska, V. J., & Maciel, G. E. (1981). A magic-angle spinning system for bullet-type rotors in electromagnets. Journal of Magnetic Resonance, 42(2), 312–321. |
[15] | Ishtiaque, S. M. (1992). Spinning of synthetic fibres and blends on rotor-spinning machine. Indian Journal of Fibre & Textile Research, 17(December), 224–230. |
[16] | Pouresfandiari, F., Fushimi, S., Sakaguchi, A., Saito, H., Toriumi, K., Nishmatsu, T., & Shimizu, Y. (2002). Spinning Conditions andCharacteristics of Open-End Rotor Spun Hybrid Yarns. Textile Research Journal, 72(1), 61–70. |
[17] | Baykal, P. D., Babaarslan, O., & Erol, R. (2006). Prediction of strength and elongation properties of cotton/polyester-blended OE rotor yarns. Fibres and Textiles in Eastern Europe, 14(1), 18–21. |
[18] | Kuo, C. F. J., Wei, H. J., Huang, C. C., & Su, T. L. (2010). Processing parameters optimization of multiple quality characteristics of open-end rotor spinning process for Bamboo charcoal and CVC blended fibers. Fibers and Polymers, 11(6), 891–898. |