Nahid Hasan Nishad
Dept. - Apparel Engineering, Bangladesh University of Textiles, Dhaka, Bangladesh
Correspondence to: Nahid Hasan Nishad, Dept. - Apparel Engineering, Bangladesh University of Textiles, Dhaka, Bangladesh.
Email: |  |
Copyright © 2018 Scientific & Academic Publishing. All Rights Reserved.
This work is licensed under the Creative Commons Attribution International License (CC BY).
http://creativecommons.org/licenses/by/4.0/

Abstract
This study is based on proper utilization of standard process through providing proper training to the fresh operator about QQT(Quality, Quantity & Time), operational skill development, foundation skill improvement, handling time reduction & proper work station implementation that can improve their performance & potential output.
Keywords:
QQT(Quality, Quantity & Time), Foundation Skill, Operational Skill, Movement, Work Station Layout
Cite this paper: Nahid Hasan Nishad, Impact of Process Standardisation on Performance & Potential Output of Fresh Operators, International Journal of Textile Science, Vol. 7 No. 1, 2018, pp. 27-34. doi: 10.5923/j.textile.20180701.03.
1. Introduction
Today in the competitive world, maximum garments industries focus is directed towards the phase of producing products rather than focusing on development of operators and their learning. It impacts badly in their long term production policy specially due to improper process standardisation. The process standard demonstrates the best and safest way of performing a job. They should ensure that the company maintains knowledge and expertise within the organization (Imai, 2007). When standards are implemented, it becomes possible to measure performance and also to visualize the relationship between an error and its cause. Without operational standards, it is almost impossible to follow-up problems and ensures that they are eliminated (Imai, 2007; de Treville, Antonakis & Edelson, 2005). By standardizing work instructions and creating stable processes, continuous improvements can be made. Standardized work instructions shall, according to Liker (2004) include the time needed for operators to finish work requested by customers, target time and it has to show the sequence when performing work. Freivalds and Niebel (2009) stress that the information needed to create standards is an outcome from performed time studies and work measurements. The results from these studies provide information on how to perform work tasks with consideration taken to target time and the employees’ work environment (Freivalds & Niebel, 2009). If a problem occurs within the manufacturing, the first thing checked is if the standards where followed (Liker, 2004). Operators within the company receive benefits from using standardized work. The benefits are easier education and learning process of new operations. Monotones are reduced because they are able to shift between different work stations and lines (Productivity press development team, 2002). Standardized work makes it easier for operators to detect problems and contribute with improvement ideas (Productivity press development team, 2002). Follow-up is an important step in the procedure of implementing new methods or assignments. This is because follow-up confirms that new methods are used and understood and if the goal for implementation is fulfilled or not (Freivalds & Niebel, 2009; Sörqvist, 2004). By performing follow-up, one investigates, at a regular basis, if employees work according to the standardized work instructions (Sörqvist, 2004). Follow-up should be performed every week to make sure that the instructions are updated and that the process is stable (Ortiz, 2006). If the result deviates from the instructions, measures have to be performed to ensure that everyone follows the decided work method (Sörqvist, 2004). Follow-up could also be the foundation for new ideas to be created because the field is always monitored and the motivation for improvements gets higher (Freivalds & Niebel, 2009; Ortiz, 2006). Wall (2005) stresses the importance of performing follow-up when a change has been made. This information should be communicated to employees so that they get involved in change process and so they are able to see how their contributions have affected the result. Furthermore, Ortiz (2006) argues that operators should be involved in the continuous improvement work. This is because they are the experts of the work at line and they are the ones who can change the culture on the shop-floor. Ohno (1978) discuss the importance of people that writes standardized work instructions should be devoted to the work and understand the benefits it brings to implement them successfully. 7 The operators should perform the development of standardized work instructions, which will result in that the acceptance of working according to them will increase. When operators are involved in the development of standardized work instructions, they will be more satisfied with their work because they have an opportunity to affect their own situation (Liker, 2004; de Treville, Antonakis & Edelson, 2005; Ohno, 1978). de Treville, Antonakis and Edelson, (2005) also argue that it is very important to encourage employees to improve the standardized work instructions at all times; this is to increase their motivation. Imai (1986) also discuss that it is important to involve everyone within the organization in the improvement work due to that employee's work ethic is increased when they are able to identify problems and provide the company with solutions.
2. QQT
Q- Quality; Q-Quantity; T-Time. So, QQT means Quality & Quantity in Time.Suppose, production target is 100 pieces/hr. Now,
Among operators A, B & C no one is good performing operator because no one can achieve the target in time.Here,
D is a good performing operator as he/she achieves the target in time. So, it should be kept in mind that "Target should be achieved, we can't change it."But, a fresh operator can't achieve QQT in primary step. He/she has to follow some stages to earn it.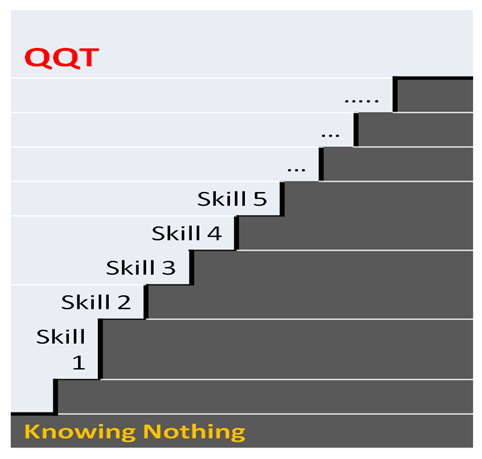 | Figure 1. QQT Stage |
M/C knowledge:A fresh operator who has no knowledge about m/c has to provide m/c knowledge.- Machine maintenance: Thread up Change bobbin Change needle (Refer Needle policy) Clean Cover up- Health & Safety: Sitting Posture No loose clothing and loose hair Switch off the machine and keep away the feet from treadle while changing bobbin and threading machine Use of needle guard and belt guard
3. Foundation Skill (Loop Exercise)
After machine knowledge the fresh operator has to do loop exercise and for that 100cm×15cm two pieces fabric are required & join the two pieces to make loop.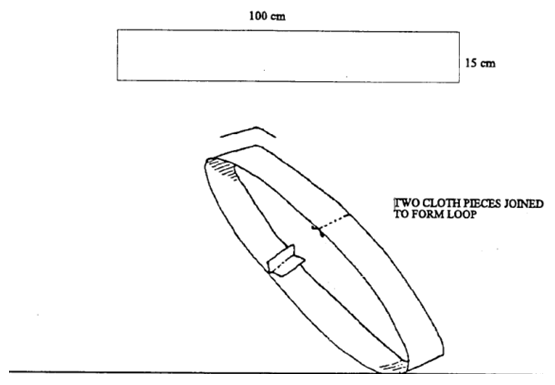 | Figure 2. Loop Formation |
Steps in Loop Exercise: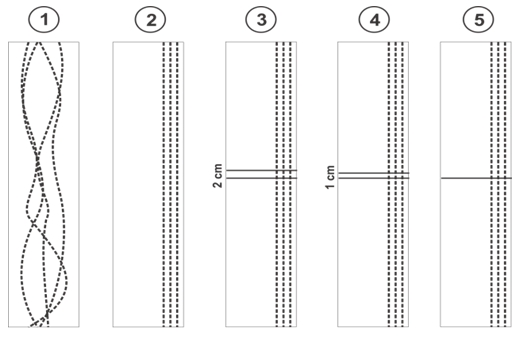 | Figure 3. Loop Practice |
Loop Ex-1 Target:§ Round the loop in 1 burst of sewing§ Machine running as fast as it can§ Achieve speed & rhythmLoop Ex-2 Target:§ Round the loop in 1 burst of sewing§ Machine running as fast as it can.§ Follow fabric edge/previous row of stitching with foot edge.§ Achieve speed, rhythm & qualityLoop Ex-3 Target:§ Round the loop in 1 burst of sewing§ Machine running as fast as it can.§ Follow fabric edge/previous row of stitching with foot edge§ Stop between 2cm, 1cm and thick line.§ Achieve speed, rhythm, quality & accuracy to stopFinally to do curve stitch, a curve has to draw on loop & stitch along with the curve.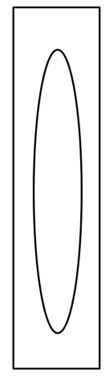 | Figure 4. Curve Stitch Practice |
4. Grading Operators
Normally operator's wage has to pay according to category of operator. There are different types of categories such as skilled, semi skilled, unskilled and A,B,C which is done according to their experience. Without these, garments manufacturing factories followed some systems or methods in doing sewing operators grading which are mentioned in below:1. Grading according to types of operation,2. Grading according to operators capability in various operations. Grading according to types of operation:First operations those are performed in making garment on basis of-I. Critical and non critical operations,II. Skill level required to perform an operation,III. Machine using capacity, IV. Operations in various parts of garments.For an example, list of operations has been shown here for shirt manufacturing factory. Operations are graded into three categories, such as A, B and C graded operations. Refer to the following table
Grading according to sewing operators capability in various operations:Here operators are categorized according to the number off operations performed by an operator from the A, B and C grade operations. It also shows the efficiency level of sewing operator. Grading table has presented in the below-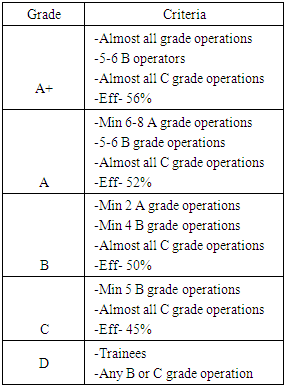
5. Operation Skill Development
After allocating operations to each operator they have to practice by mock up piece but step by step. Example of a Box Pleat Operator (Kansai M/C):§ Step 1:Take a 60cm×10cm piece and do straight stitch without folder until the stitch becomes straight.
§ Step 2:Take a 60cm×10cm piece and do straight stitch using folder with 4 notches match until the stitch becomes straight.
§ Step 3:Now have to practice check match.
§ Step 4:Now check match with lining (fusing).
For each step, the operators have to give 5 pieces to take cycle time & identify alter piece number & the process will be going on until the cycle time goes under target time with zero alter.
After completing all the steps with zero alter the operator will practice mock piece & within few days can perform in production line.
6. Cycle Time
Total time taken to do all works to complete one operation, i.e. time from pick up part of first piece to next pick up of the next piece.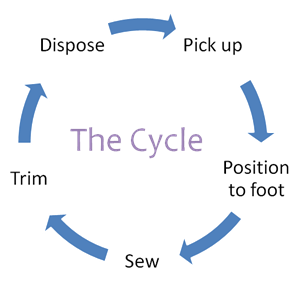 | Figure 5. Cycle Time |
7. Process Standardisation
In the garments industry it has been seen that, the operators perform many unnecessary movement & their WSL (work station layout) isn't properly arranged. If they make optimum movement & follow the WSL in proper way then standard process will be possible & the target production can be achieved in time.
8. Movement
In a production floor, the operators only do three movements of hands, finger & leg. Through these movements they can do the following controls:1. Speed Control2. Machine Control3. Fabric Control &4. Quality Control.An operator spends his/her time by handling & sewing for each operation. Generally sewing time is required to run the needle & do the operation. Handling time is required to touch the piece, alignment, entering under presser foot, disposing etc.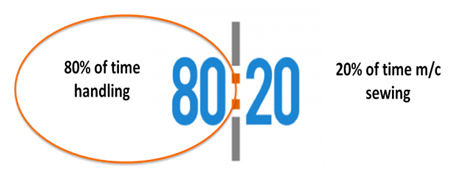 | Figure 6. Handling time: Sewing time |
Here, focusing point is handling time, if it is minimized then production will be increased. To reduce handling time there should be good knowledge about good movement & wrong movement.§ Wrong movement:1. Excessive movement: When fabric/garments have to collect from far distance.2. Slow movement: If operator is slow in handling.§ Good movement:1. Simultaneous - Two hands working together from start to finish2. Minimum - Near as much as possible, till ankle and eye movement3. Rhythmic - Story of cuff setter – automatic, body front and back movement5. Symmetrical - Rotate hands in opposite direction, running, throw ball6. Natural – Take from bottom/ back, Machine bench7. Continuous – Continuous pick up at right and dispose at left, Single piece flow8. Habitual/ Automatic – Long term memory. thinking & doing.After getting knowledge about good & wrong movement we can change the process & make it standard in the production but in that case following questions we have to keep in mind.♣ Which hand?♣ Fingers/thumbs use?♣ Where was the piece picked up?♣ How was it picked up?♣ Other parts of hands used?Now, we have to focus on the WSL (work station layout).
9. Work Station Layout
It is the arrangement of input pieces and placement of output pieces in relation to work station and the operator.Before drawing a standard Work Station Layout we have to think about the process name, m/c name, pick up point, disposing place, garments arrangement etc & it should be comfortable for the operator to produce target pieces in time with good quality.Here is a WSL of side attach.Principles of work station layout:- Touching point and sewing point should be same - The pieces for pick up and dispose need to be closer to the operator. - Piece should be handled in a way to directly present to the needle. - Pieces should be kept as to be sewing need to be done. - Dispose need to be done as next operator picks as discussed above 4 points If the QQT gets priority, unnecessary movements are reduced & all the principles of work station layout are followed then handling time will be reduced & quality will be developed as well because the operator can get time to focus on the quality beside the target. | Figure 7. Work Station |
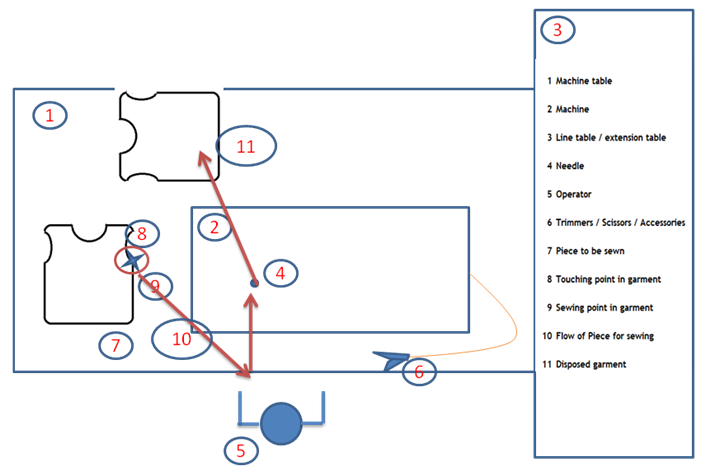 | Figure 8. Sewing work station layout |
10. Formula
§ Performance analyzing through cycle time:♣ Take cycle time (5 cycles) ♣ Average. ♣ Discard any non-standard e.g. Thread break.♣ Ascertain Basic time (SMV – Bundling - Allowances)♣ Performance
§ Performance percentage of operator:Step 1: SMV in Seconds=SMV × 60Step 2: Basic Time in Seconds= (SMV in Seconds – Bundling Time) ×
Step 3: Performance in %
§ Potential Output of the operator (Pieces):Step 1: Cycle time with allowances (Sec)= (Cycle time in sec. + Bundling time) ×
Step 2: Potential output in pieces/ hour
A-Grade Operation: Collar Attaching× Performance percentage of operator:Let,Primary cycle time= 36 secBundling time= 5 secAllowance=15%SMV= 0.535Step 1: SMV in sec= .535×60 = 32.1secStep 2: Basic time in sec= (32.1-5)×(100-15/100) = 23secStep 3: Performance% = (23/36)×100 = 63%Now through process standardization excessive movement is reduced by keeping the pieces close to the operator & stages such as burst time & alignment time are reduced. As a result handling time as well as cycle time will be reduced.Assume that corrective cycle time is 28sec.Now, Corrective performance% = (23/28)×100 =82%× Potential output of the operator:Let,Primary cycle time= 36secBundling time= 5secAllowance= 15%Step 1: Cycle time with allowances (Sec)= (36 + 5) × (100+15/100) = 47.15secStep 2: Potential output in pieces/ hour=(3600/47.15) = 76piecesNow, Corrective cycle time= 28secCorrective cycle time with allowances = (28 + 5) × (100+15/100) = 37.95secCorrective potential output= (3600/37.95) = 94piecesB-Grade Operation: Collar Top Stitch× Performance percentage of operator:Let,Primary cycle time= 25 secBundling time= 5 secAllowance=15%SMV= 0.34Step 1: SMV in sec= .34×60 = 20.4 secStep 2: Basic time in sec= (20.4-5)×(100-15/100) = 13secStep 3: Performance% = (13/25)×100 = 52%Now, Corrective cycle time=18 sec Corrective performance% = (13/18)×100 =72%× Potential output of the operator:Let,Primary cycle time= 25secBundling time= 5secAllowance= 15%Step 1: Cycle time with allowances (Sec)= (25 + 5) × (100+15/100) = 34.5secStep 2: Potential output in pieces/ hour= (3600/34.5) = 104piecesNow, Corrective cycle time= 18secCorrective cycle time with allowances = (18 + 5) × (100+15/100) = 26.45secCorrective potential output= (3600/26.45) = 136piecesC-Grade Operation: Cuff Hemming (single cuff)× Performance percentage of operator:Let,Cycle time= 19 secBundling time= 5 secAllowance=15%SMV= 0.26Step 1: SMV in sec= .26×60 = 15.6secStep 2: Basic time in sec= (15.6-5)×(100-15/100) = 9secStep 3: Performance% = (9/19)×100 = 47%Assume that corrective cycle time is 13sec.Now, Corrective performance% = (9/13)×100 =69%× Example (Potential output of the operator):Let,Primary cycle time= 19secBundling time= 5secAllowance= 15%Step 1: Cycle time with allowances (Sec)= (19 + 5) × (100+15/100) = 27.6secStep 2: Potential output in pieces/ hour= (3600/27.6) = 130piecesNow, Corrective cycle time= 28secCorrective cycle time with allowances = (13 + 5) × (100+15/100) = 20.7secCorrective potential output= (3600/20.7) = 173pieces
11. Result & Discussion
From the above analysis, the progressive graph of Performance percentage & Potential output have been found.For, A-Grade Operation: Collar Attaching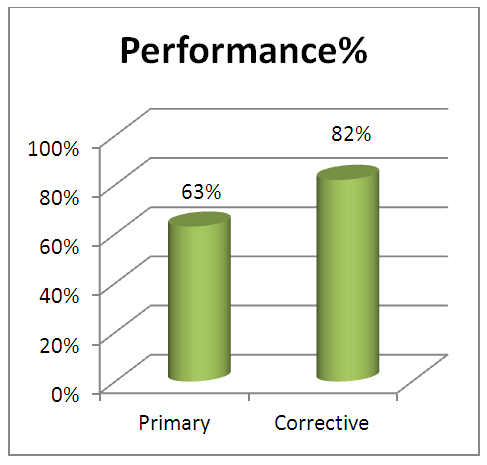 | Graph 1. Performance% Improvement |
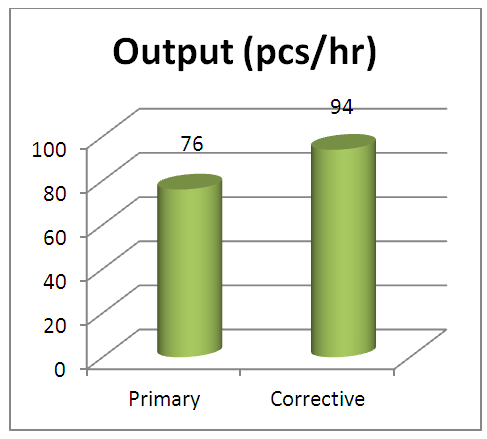 | Graph 2. Potential Output Increases |
For, B-Grade operation: Collar Top Stitch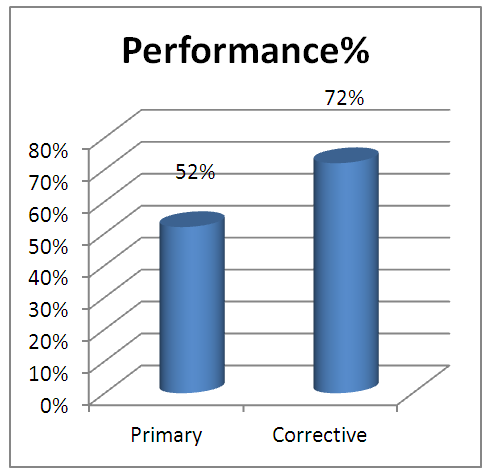 | Graph 3. Performance% Improvement |
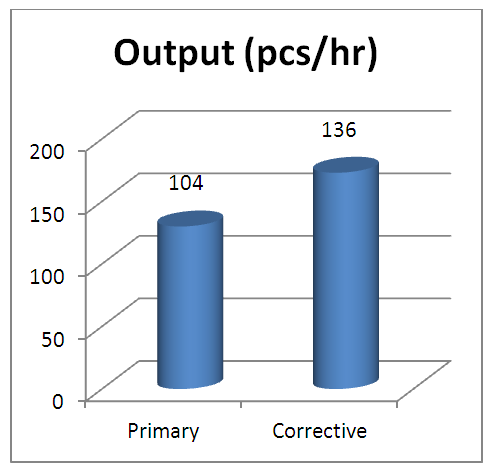 | Graph 4. Potential Output Increases |
For, C-Grade operation: Cuff Hemming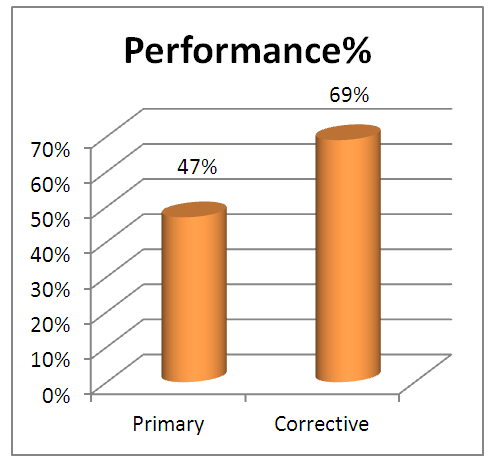 | Graph 5. Performance% Improvement |
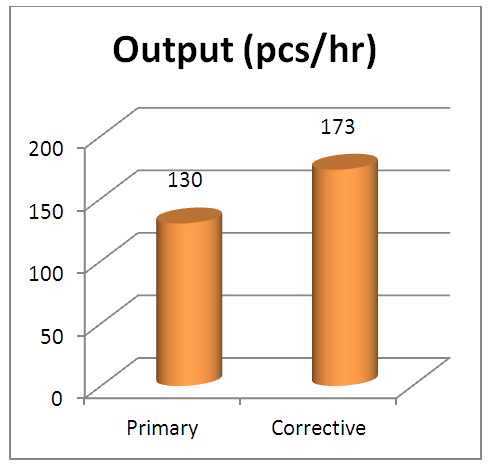 | Graph 6. Potential Output Increases |
The impact of process standardization through QQT knowledge, foundation skill development, operation skill improvement, movement correction & proper workstation layout make it possible to improve the quality, increases performance percentage as well as potential output of all A,B,C grade operators. As a result, more quality product can be manufactured within the lead time.
12. Conclusions
In the garments industry, there are many difficulties to achieve the goal specially if the operators are not expert enough to do their work efficiently. To make them effective, it is necessary to standardise their work. Producing companies focus is directed towards the phase of producing products rather than focusing on development of operators and their learning. This antagonism is usually based upon a lack of employees and it creates difficulties in educating new and experienced operators as well as participation in developing procedures during ordinary working hours. Especially in the later aspect there is a problem in finding enough time to document existing problems in the production process, to meet in groups for discussions and to follow-up identified problems. The basic condition for maintaining a well-functioning company, a learning organization for the operators. In the industry today, there is a crying need of potential developmental learning specially about process standardisation. By establishing standardised work instructions, it becomes easy to evaluate the process and make sure that the work tasks are performed in the right quality level. For this to be successful, company policy needs to involve and respect the quality work. Responsibility areas has to be clear and procedures needs to be developed throughout the whole organization. Standards need to be followed and documentation has to be accurate to view operations and maintenance of every.
References
[1] | Bell, D., McBride, P., & Wilson, G. (2002) Managing Quality. Jordan Hill, Oxford: Butterworth-Heinemann. |
[2] | de Treville, S., Antonakis, J. & Edelson, N. M. (2005) Can Standard Operating Procedures be Motivating? Reconciling Process Variability Issues and Behavioural Outcomes. Total Quality Management, vol. 16, p 231-241. |
[3] | Freivalds, A., & Niebel, B. W. (2009) Niebel's Methods, standards, and work design. New York, United States of America: McGraw-Hill. |
[4] | Imai, M. (1986) Kaizen: Att med kontinuerliga, stegvisa förbättringar höja produktiviteten och öka konkurrenskraften. Kristianstad: Kristianstads Boktryckeri AB. |
[5] | Liker, J. K. (2004) The Toyota Way: 14 Management Principles from the World´s Greatest Manufacturer. New York, United States of America: McGraw-Hill. |
[6] | Ohno, T. (1978) Toyota Production System: Beyond Large-Scale Production. New York, United States of America: Productivity Press. |
[7] | Ortiz, C. A. (2006) Kaizen Assembly: Designing, Constructing and Managing a Lean Assembly Line. Unites States of America: CRC Press Taylor and Francis Group. |
[8] | Productivity press development team (2002) Standard Work for the Shopfloor. New York, United states of America: Productivity Press. |
[9] | Sörqvist, L. (2004) Ständiga förbättringar. Studentlitteratur. |
[10] | Wall, S. J. (2005) The Protean Organization: Learning to Love Change. Organizational Dynamics, vol. 34, p 37-46. |