Md. Nazmul Haque1, Prof. Md. Abul Kashem2, Prof. Dr. Md. Mashiur Rahman Khan3
1Lecturer, Department of Textile Engineering, Southeast University, Dhaka, Bangladesh
2Head, Department of Apparel Engineering, Bangladesh University of Textiles, Dhaka, Bangladesh
3Dean, Faculty of Textile Fashion Design & Apparel Engineering, Bangladesh University of Textiles, Dhaka, Bangladesh
Correspondence to: Md. Nazmul Haque, Lecturer, Department of Textile Engineering, Southeast University, Dhaka, Bangladesh.
Email: |  |
Copyright © 2018 Scientific & Academic Publishing. All Rights Reserved.
This work is licensed under the Creative Commons Attribution International License (CC BY).
http://creativecommons.org/licenses/by/4.0/

Abstract
The aim of this work is to analysis worker fatigue and boredom in a garments production. This experiment has been done in AMTRANET group factory Export Village limited. Throughout this experiment three worker their three days productivity with faults percentage has been calculated. Their three days work, work breakdown has been monitored and the amount of rest that they have taken in different time interval has been monitored and noted. Three workers their lively-hood had been noted and work in progress has been monitored. It has been found that, in case of progression of day, Individual worker may have certain amount of impact of fatigue and boredom in different day basis but overall result shows it was a negligible amount of impact of fatigue and boredom. In case of progression of time at the end of the day few hour production slot, there is moderate amount of impact of fatigue and boredom in garments production.
Keywords:
Fatigue, Boredom, Faults, Critical operation, Work in progress
Cite this paper: Md. Nazmul Haque, Prof. Md. Abul Kashem, Prof. Dr. Md. Mashiur Rahman Khan, Analyzing the Impact of Worker (Machine Operator) Fatigue and Boredom in Garments Production (Critical Process Operation), International Journal of Textile Science, Vol. 7 No. 1, 2018, pp. 1-13. doi: 10.5923/j.textile.20180701.01.
1. Introduction
Bangladesh's ready-made garments industry has taken the low road to competitive advantage. Local capitalists, the big retailers and western governments are reaping the benefits of the super-exploitation and repression of the (mostly women) workers. The annual turnover in ready garments industry is now 9 billion dollar and it employs around 3.5 million workers and more than 80% of them are women [1]. Work environment important criteria in any workplace. The work environment can implicate the social relation at workplace and also maintain the relationship between colleague, supervisor and the organization. It describes the neighboring circumstances in which employees are working together. A satisfied, happy and hardworking employee is biggest asset of any organization. Effective results & productivity for any organization is depend on the level of satisfaction of employees and work environment is one of the most important factor which influence the satisfaction & motivation level of employees [2]. Doing repetitive job creates fatigue and boredom in worker. For many years, psychologists and other students of work behaviour have been pointing out that boredom is a subjective experience and refers to the individual's reaction to the environmental situation, whereas repetition or monotony is a characteristic of a task as perceived by an individual. Simply put, some repetitive or monotonous tasks are experienced as boring by some people. The aim of this article is to explore the sorts of repetitive tasks which lead to feelings of boredom, the effects of repetitive tasks on boredom and performance, and the methods that both workers and employers can use to reduce these effects [3]. Fatigue is defined as lassitude, or exhaustion of mental and physical strength resulting from bodily labour or mental exertion. It is a concern of workers in many occupations throughout the world. While occupational safety and health has improved in recent decades, fatigue remains a common problem in developed countries Fatigue is a serious threat to quality of life and severely compromises work performance when it becomes chronic or excessive. Unfortunately, its complex and dynamic nature makes fatigue difficult to define, observe and measure. Fatigue is a very common experience at work especially for workers who do shift work or extended work shifts, as they are at higher risk of being affected. Many individual factors, such as age, health, and living conditions, influence a worker’s ability to adapt to shift work or changes in shift sequences, timing or duration. Likewise, extended work shifts and overtime introduce unique fatigue issues. Shift design strategies are essential to preventing both mental and localized physical fatigue. The effect of extended work shifts is highlighted because long working hours can negatively affect workers’ health and well-being [4]. Garments production process involves different types of sewing operation. All of this process involves precise care and concentration. Long hour of work without any sorts of break increases faults percentage [5]. Contrary to popular wisdom, boredom is not the result of having nothing to do. It is very hard to come up with a situation where a person’s options are so limited that he or she literally can do nothing. Boredom is thought by some to be a distinct emotional state in which the level of stimulation is perceived as unsatisfactorily low [6]. Boredom is an emotional state that has a long history in organizational research. Despite recent changes in technology and the organization of work, boredom remains a part of the experience of work [7]. Garments production process involve in participation of different types of worker among the line. Performance improvements are realized through coordination among the team members as a result of their ability to self-regulate work, eliminate bottlenecks, resolve conflicts, help one another solve problems, and make improvements in the production process [8]. Garment industry contributes a high percentage in the country’s total revenue but still facing many challenges. Ten years ago if a catalog order was placed, the expected delivery was four to six weeks. Today after two or three days, consumer begins to wonder where and why their merchandise is being delayed. These days, customers have become more demanding [9]. Production fault that has been found in garments production process in different portion of time and it also varies day-wise. These faults reduce product quality. Due to impact of fatigue and boredom it is very difficult to produce quality product. Fault that has been found in garments are- major, minor and critical faults [10]. For this research work, three particular operators with three particular operation has been observed in three days and their particular operation, their resting time and impact of fatigue and boredom has been observed. How this fatigue and boredom effects their total whole days work it has been monitored. Perhaps better guideline in near future that can be given to factory to reduce this impact of fatigue and boredom in worker.
2. Experimental
2.1. Materials
2.1.1. Product Details with Production Sequence
This experiment has been done in AMTRANET Group factory Export village Ltd. Product that has been carried out for this experiment is a reputed buyer product. Product name mans long sleeve shirt. There are 47 different sorts of operation involved to produce these garments. Out of these 47 operations, only three of the major critical operation that has been taken into account for this research experiment. There are three operators who involved their subsequent machine to produce this garments parts components. Each of the operator target production 55pcs/Hr. Operation names gives in figure 1 with sequence.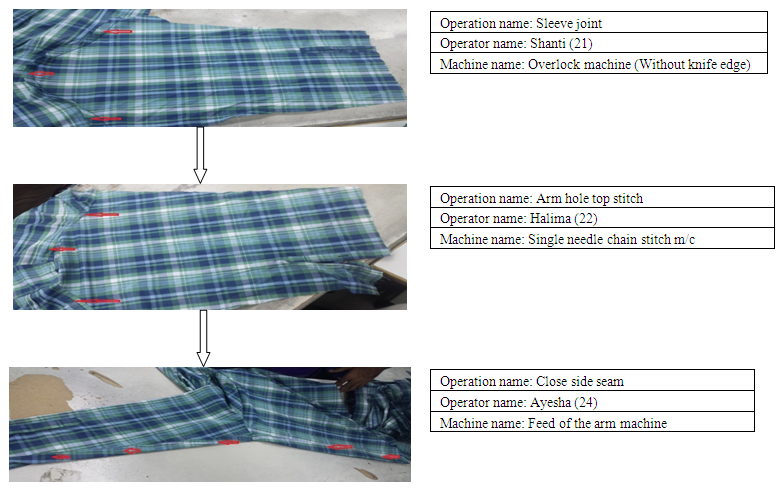 | Figure 1. Production operation sequence |
2.1.2. Product Details with Production Sequence
To do this particular critical operation (sleeve joint, Armhole top stitch and closed side seam) there are 6 workers involved in that task. For every particular operation two workers involves in there. Workers name with particular machine name given in figure 2.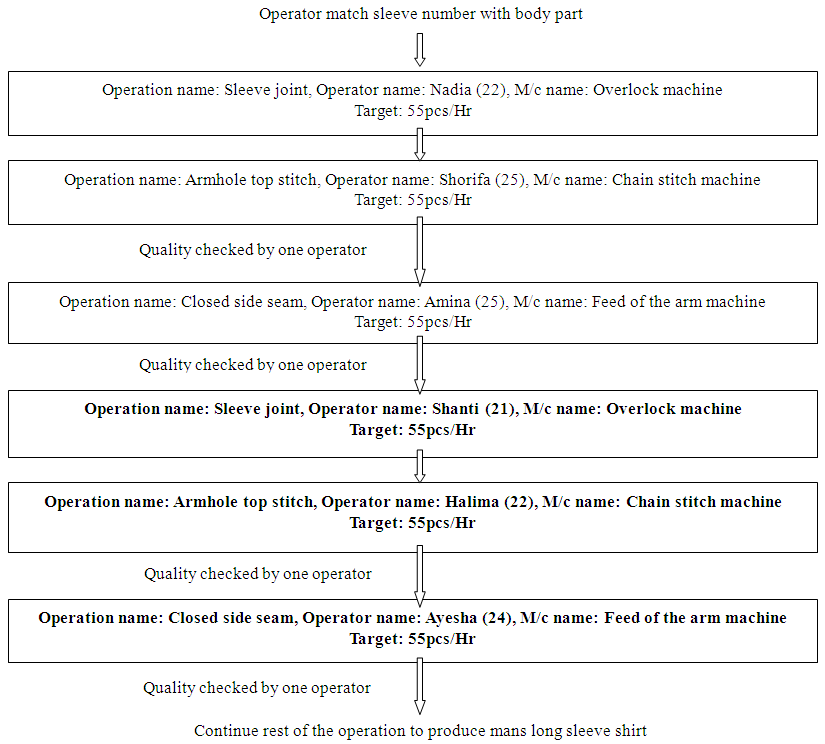 | Figure 2. Production line layout for critical operation |
In Figure 2, last three operator Shanti (21), Halima (22) and Ayesha (24) has been taken into account for this experiment.
2.1.3. Operator Details with Their Livelihood
2.1.3.1. Shanti (21)Marital status: Unmarried.Experience: 1 year 5 month.She has three sisters and two of them getting married. She has to take care of her father and mother. Wake up 05.30 am in the morning, making food for family and it took her 45 minutes walking distance to reach factory. During lunch break stayed in factory and take the food that she carried. She is the only earning member in her family.2.1.3.2. Halima (22)Marital status: MarriedExperience: 2 year 3 month.She has two children. She has lots of responsibilities for her husband and his family. Wake up 05.00 am in the morning, making food for family and it took her 45 minutes walking distance to reach factory. During lunch break stayed in factory and take the food that she carried. 2.1.3.3. Ayesha (24)Marital status: MarriedExperience: 4 year 1 month.She has one child. She has lots of responsibilities for her husband and his family. Wake up 05.00 am in the morning, making food for family and it took her 40 minutes walking distance to reach factory. During lunch break stayed in factory and take the food that she carried.
2.2. Methods
2.2.1. Operators Work Break Time during Different Time Interval
After 4 days starting of production, 3 consecutive days three operators name shanti (21), Halima (22) and Ayesha (24) their work break during different time interval has been monitored from before and after lunch time. These three operators take their work break in different time interval with excuses like going washroom, tiredness, headache, drowsiness, bring drink water, stop working to talk with someone and machine maintenance problem etc. The amount of time that they have taken during different time interval has been noted in Table 1, Table 2, Table 3, Table 4, Table 5, Table 6, Table 7, Table 8 and Table 9.Table 1. Work break time operator name shanti (21) in Day-1 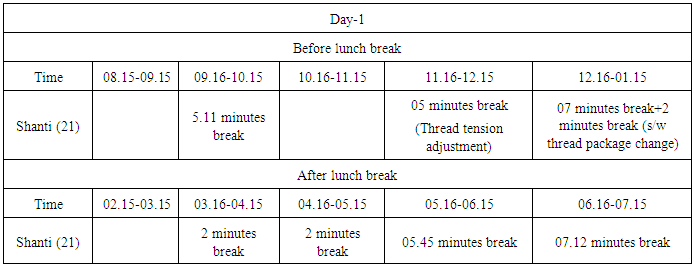 |
| |
|
Table 2. Work break time operator name shanti (21) in Day-2 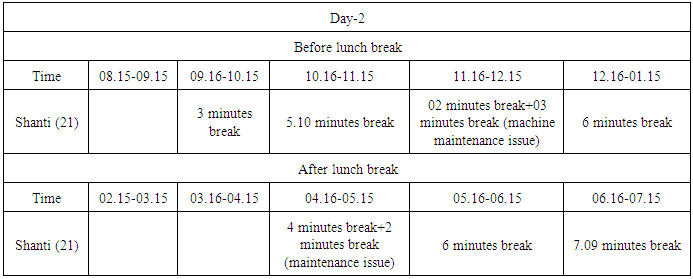 |
| |
|
Table 3. Work break time operator name shanti (21) in Day-3 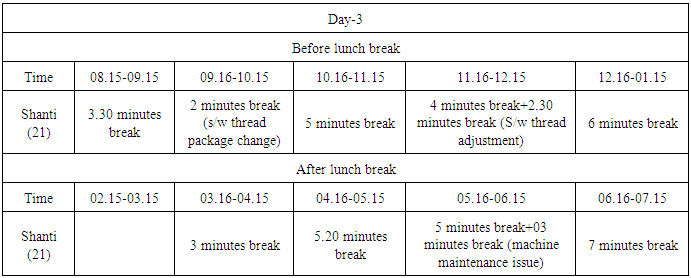 |
| |
|
Table 4. Work break time operator name Halima (22) in Day-1 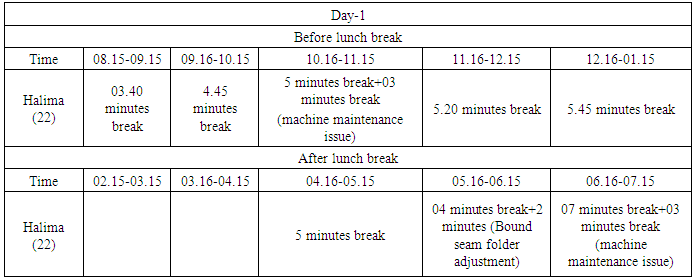 |
| |
|
Table 5. Work break time operator name Halima (22) in Day-2 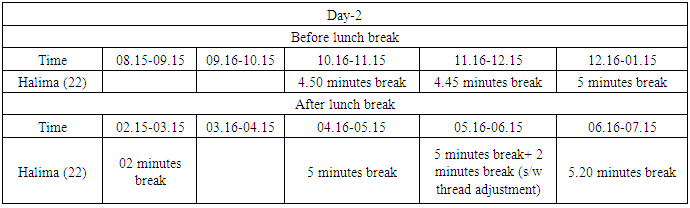 |
| |
|
Table 6. Work break time operator name Halima (22) in Day-3 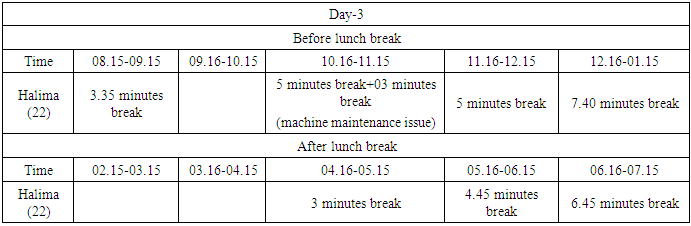 |
| |
|
Table 7. Work break time operator name Ayesha (24) in Day-1 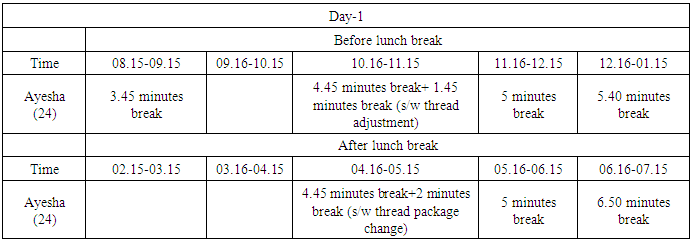 |
| |
|
Table 8. Work break time operator name Ayesha (24) in Day-2 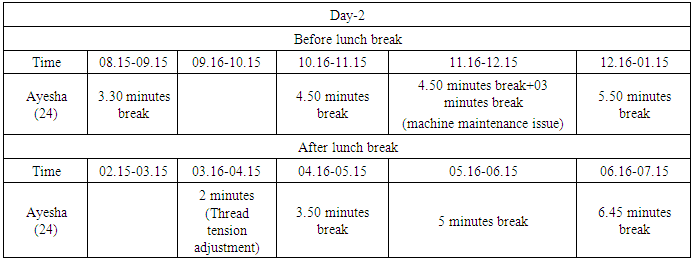 |
| |
|
Table 9. Work break time operator name Ayesha (24) in Day-3 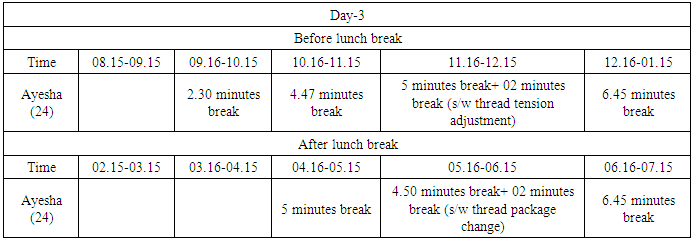 |
| |
|
2.2.2. Productivity Calculation in Progression of Day and Progression of Time
2.2.2.1. Progression of Day Productivity CalculationThree operator shanti (21), Halima (22) and Ayesha (24) their production has been monitored from Day1 to Day3. Each days production average has been calculated at the end of the day. In Table 10, total average productivity of shanti (21), Halima (22) and Ayesha (24) has been calculated from Day1 to Day3. Shanti (21) operate overlock machine to produce sleeve joint, Halima (22) operate chain stitch machine to produce arm hole top stitch and Ayesha (24) operate feed of the arm machine to join side seam. Their productivity from Day1 to Day3 has been monitored at the end of the day.Table 10. Operator name-Shanti (21), Halima (24) and Ayesha (24), average productivity/Day 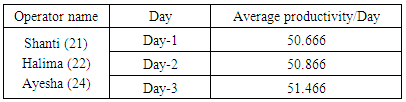 |
| |
|
2.2.2.2. Progression of Time Productivity CalculationThree operator shanti (21), Halima (22) and Ayesha (24) their production has been monitored from 08.15am to 7.15pm hourly interval in each day. In Table 11, total average productivity/Hr of shanti (21), Halima (22) and Ayesha (24) has been calculated from 08.15am to 07.15pm. Shanti (21) operate overlock machine to produce sleeve joint, Halima (22) operate chain stitch machine to produce arm hole top stitch and Ayesha (24) operate feed of the arm machine to join side seam. Their productivity from 08.15am to 07.15pm has been monitored at each hour interval.Table 11. Operator name-Shanti (21), Halima (24) and Ayesha (24), average productivity/Hour  |
| |
|
2.2.3. Faults Percentage Calculation in Progression of Day and Progression of Time
2.2.3.1. Progression of Day Faults Percentage CalculationThree operator shanti (21), Halima (22) and Ayesha (24) their production has been monitored and faults (%) has been calculated from Day 1 to Day 3. Operator name Shanti (21) who operate overlock machine to create sleeve joint produces faults like raw edge, width irregular, top side loose, puckering and allowance uneven etc. Operator name Halima (22) who operate chain stitch machine to create armhole top stitch produces faults like improper edge, raw edge, width irregular, top side loose, puckering and allowance uneven etc. Operator name Ayesha (24) who operate feed of the arm machine to create side seam join produces faults like side pleat, U/D improper edge, raw edge, width irregular, top side loose, puckering and allowance uneven etc. Each days faults (%) average has been calculated at the end of the day. In Table 12, total average Faults (%)/Hr of shanti (21), Halima (22) and Ayesha (24) has been calculated from 08.15am to 07.15pm. Shanti (21) operate overlock machine to produce sleeve joint, Halima (22) operate chain stitch machine to produce arm hole top stitch and Ayesha (24) operate feed of the arm machine to join side seam. Their faults (%) from 08.15am to 07.15pm has been monitored at the end of the each day.Table 12. Operator name-Shanti (21), Halima (22) and Ayesha (24), average Faults (%)/Day 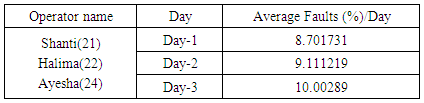 |
| |
|
2.2.3.2. Progression of Time Faults Percentage CalculationThree operator shanti (21), Halima (22) and Ayesha (24) their production has been monitored and faults (%) has been calculated from 08.15am to 07.15pm. Operator name Shanti (21) who operate overlock machine to create sleeve joint produces faults like raw edge, width irregular, top side loose, puckering and allowance uneven etc. Operator name Halima (22) who operate chain stitch machine to create armhole top stitch produces faults like improper edge, raw edge, width irregular, top side loose, puckering and allowance uneven etc. Operator name Ayesha (24) who operate feed of the arm machine to create side seam join produces faults like side pleat, U/D improper edge, raw edge, width irregular, top side loose, puckering and allowance uneven etc. In Table 13, total average Faults (%)/Hr of shanti (21), Halima (22) and Ayesha (24) has been calculated from 08.15am to 07.15pm. Shanti (21) operate overlock machine to produce sleeve joint, Halima (22) operate chain stitch machine to produce arm hole top stitch and Ayesha (24) operate feed of the arm machine to join side seam. Their faults (%) from 08.15am to 07.15pm has been monitored at the end of the each hour interval.Table 13. Operator name- Shanti (21), Halima (22) and Ayesha (24), average Faults (%)/Hour 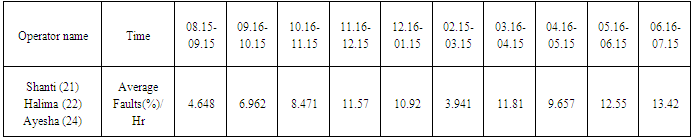 |
| |
|
3. Results and Discussion
3.1. Impact of Fatigue and Boredom in Progression of Day (Individual Operator)
Figure 3, it has been seen that productivity starts to increase from Day 1 to Day 3. Continuous involvement and habituate in work improved productivity with progression of day. Figure 4, observable fact that Day 1 productivity decreases but faults (%) also increases. Adjusting with the new work and sudden involvement in work may create moderate amount of fatigue in worker, that’s why this faults percentage increases. From Day 2 to Day 3 as productivity increases, faults percentage also increases. As productivity increases faults percentage also increases. So this over-lock machine operator does not have the impact of fatigue and boredom in Day 2 to Day 3.Figure 5, it has been seen that productivity starts to increase from Day 1 to Day 3. Continuous involvement, progress in work and habituate in work improved productivity with progression of day. Figure 6, observable fact that productivity increases, side by side faults (%) also increases. Day 1 productivity is low, perhaps after one holiday adjusting with the new work and sudden involvement in work may decrease productivity. From Day 1 to Day 3 as productivity increases, faults percentage also increases. Table 4, Table 5 and Table 6, it has been that significant amount of rest in different time interval perhaps keeps away this worker to feel the impact of fatigue and boredom. So this chain stitch machine operator does not have the impact of fatigue and boredom in Day 1 to Day 3.Figure 7, it has been seen that productivity was lower in Day 2. Figure 8, observable fact that productivity increases, side by side faults (%) also increases except Day 2. Day 2 productivity decreases but fault percentage increases. Because tensioner tension adjust problem in this feed of the arm machines cause problem to the operator to adjust with that machine. Table 8 shows the amount of rest of this worker in different time interval in Day 2. But that’s quite enough for this worker to kept her away the impact of fatigue and boredom. In Day 1 and Day 3 as productivity increase, faults percentage also increases. So this feed of the arm machine operator does not have the impact of fatigue and boredom in Day 1 and Day 3.
3.2. Overall Impact of Fatigue and Boredom in Progression of Day
Figure 9, it has been seen productivity increases with the progression of day. Continuous involvement, progress of work and habituate with work environment improved productivity with progression of day. Figure 10, it also shows that faults percentage increases as the day progress which for this three operator as productivity increases faults percentage also increases. This certainly shows as the progression of day, there is no certain impact of fatigue and boredom in these three operators. From Table 1 to Table 9 shows these three operators has taken certain amount of rest in different time interval perhaps kept away from them to feel the impact of fatigue and boredom. Also after each working day worker get sufficient rest at home to come back next day in work. However if individually trying pointing out these three operator, it has been seen that operator shanti in Day 1 (Figure 3, Figure 4) and operator Ayesha in Day 2 (Figure 7, Figure 8), as productivity decreases, faults percentage increases which shows individual worker may have certain amount of impact of fatigue and boredom in different day basis but overall result of these three worker shows it was a negligible amount of impact of fatigue and boredom. 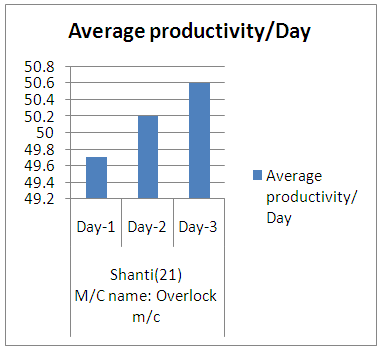 | Figure 3. Average productivity/Day of shanty |
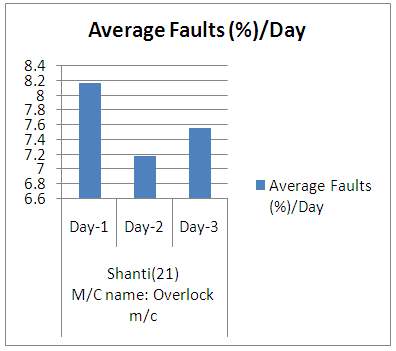 | Figure 4. Average Faults (%)/Day of shanti |
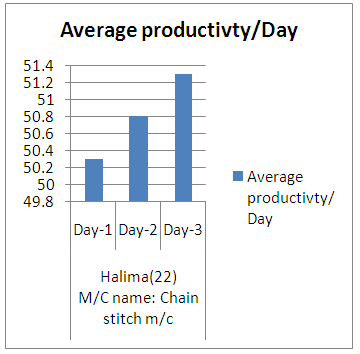 | Figure 5. Average productivity/Day of Halima |
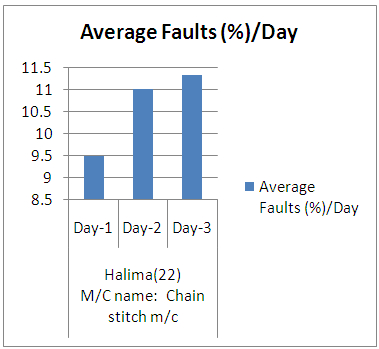 | Figure 6. Average Faults (%)/Day of Halima |
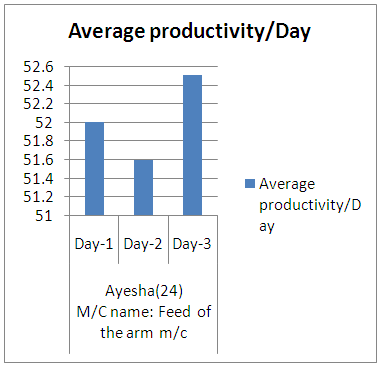 | Figure 7. Average productivity/Day of Ayesha |
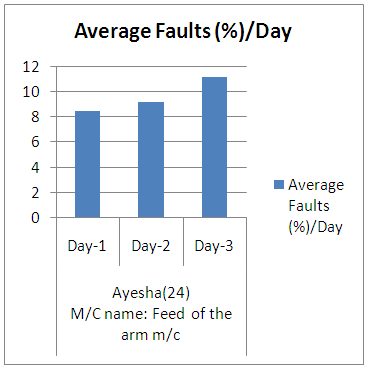 | Figure 8. Average Faults (%)/Day of Ayesha |
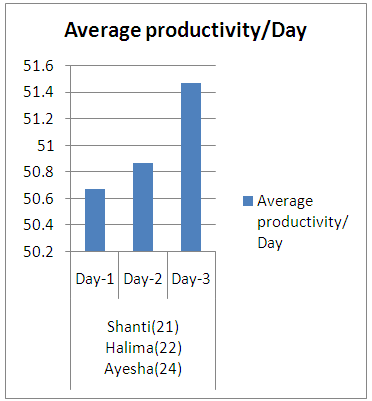 | Figure 9. Average productivity/Day |
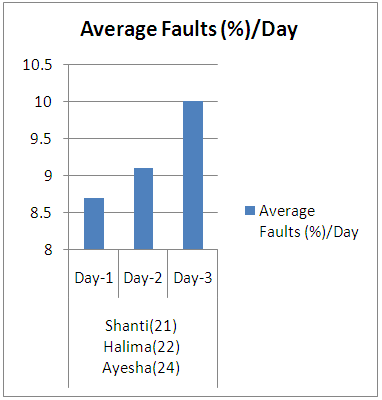 | Figure 10. Average Faults (%)/Day |
3.3. Impact of Fatigue and Boredom in Progression of Time (Individual Operator)
From Figure 11, it has been seen that productivity lower in morning time and it increases before lunch time. Because suddenly introduction of work in factory after long hours of break, cope up with the sudden environment and adjusting with the work creates low productivity in morning time. Figure 12, it has been seen that productivity increases side by side faults percentage also increases. After lunch break operator shanty she completes her meal in 10-15 minutes and rest of the time they spend sleeping on the floor. From sleeping condition all of a sudden introduction of work creates sluggishness and drowsiness among worker which creates few hour low productivity after lunch break. After three hours of production, productivity starts to decrease. From Figure 12, it has been shown that, from 5.16pm to 07.15pm, productivity decreases significantly. This scenario shows after long hours of work this operator feel the impact of fatigue and boredom which reduces her productivity.From Figure 13, it has been seen that productivity lower in morning time and it increases before lunch time. Because suddenly introduction of work in factory after long hours of break, cope up with the sudden environment and adjusting with the work creates low productivity in morning time. Figure 14, it has been seen that productivity increases side by side faults percentage also increases. After lunch break operator Halima she completes her meal in 10-12 minutes and rest of the time they spend sleeping on the floor. From sleeping condition all of a sudden introduction of work creates sluggishness and drowsiness among worker which creates few hour low productivity after lunch break. After three hours of production, productivity starts to decrease. From Figure 14, it has been shown that, from 5.16pm to 07.15pm, productivity decreases significantly. This scenario shows after long hours of work this operator feel the impact of fatigue and boredom which reduces her productivity.From Figure 16, it has been seen that productivity lower in morning time and it increases before lunch time. Because all of a sudden introduction of work in factory after long hours of break, cope up with the sudden environment and adjusting with the work creates low productivity in morning time. Figure 17, it has been seen that productivity increases side by side faults percentage also increases. After lunch break operator Ayesha, she completes her meal in 10-15 minutes and rest of the time they spend sleeping on the floor. From sleeping condition all of a sudden introduction of work creates sluggishness and drowsiness among worker which creates few hour low productivity after lunch break (1.15am-02.14am). After few hours of production, productivity chronologically increases. From Table 7, Table 8 and Table 9, it has been seen that worker Ayesha get sufficient amount of rest in different portion of time interval before lunch break. Sufficient amount of rest in different time interval help her to kept away from the impact of fatigue and boredom.
3.4. Overall Impact of Fatigue a Boredom in Progression of Time
Before lunch time, From Figure 17, it has been seen that productivity lower in morning time but faults percentage increased on continuous basis. Morning time worker shows slow progress in their work. Each worker they are having a fixed salary for their 08.15am to 07.15pm duty in each day. When supervisor reported operator for their low productivity in work, then they improve their productivity. Also sudden introduction of work in factory after long hours of break, cope up with the sudden environment and adjusting with the work creates low productivity in morning time. Figure 18, it has been seen that productivity increases side by side faults percentage also increases. This scenario indicates that there is no significant impact of fatigue and boredom in garments production. After first three hours production, productivity increases because of worker get sufficient amount of rest in different portion of time interval before lunch break. Three workers shanty (21), Halima (22) and Ayesha (24), their work breakdown table shows that after three hours of production, every hour interval they take significant amount of rest which help them to prevent themselves from fatigue and boredom. After lunch time, From Fig 17, it has been seen that productivity lower in after lunch break. During lunch break, three worker shanty (21), Halima (22) and Ayesha (24) they complete their meal in 10-15 minutes and rest of the time they spend sleeping on the floor. From sleeping condition all of a sudden introduction of work creates sluggishness and drowsiness among worker which creates few hour low productivity after lunch break. After three hours of production, productivity starts to decrease. From Figure 18, it has been seen that, from 5.16pm to 07.15pm, though productivity decreases but faults percentage increases. Three workers shanty (21), Halima (22) and Ayesha (24) their work breakdown table shows that after first two hours, every hour interval significant amount of rest that they have taken to continue their work. These scenario indicate that, progression of time at the end of the day few hour production slot, there is moderate amount of impact of fatigue and boredom in garments production.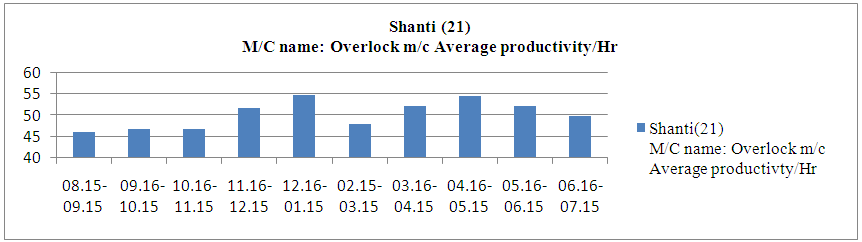 | Figure 11. Average productivity/Hr of shanti |
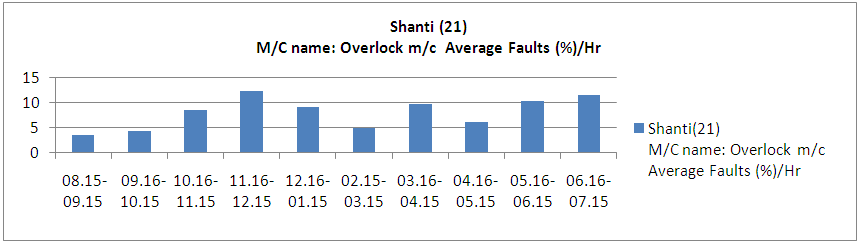 | Figure 12. Average Faults (%)/Hr of shanti |
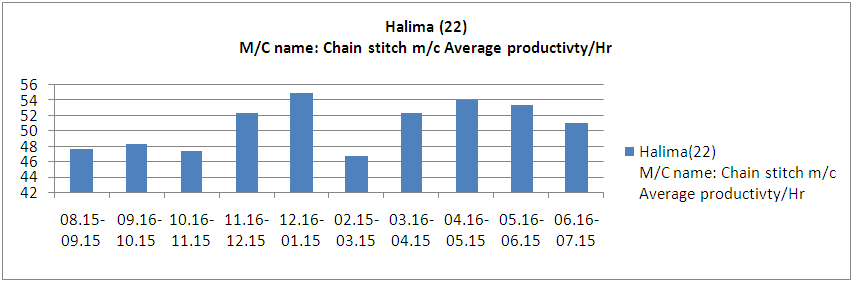 | Figure 13. Average productivity/Hr of Halima |
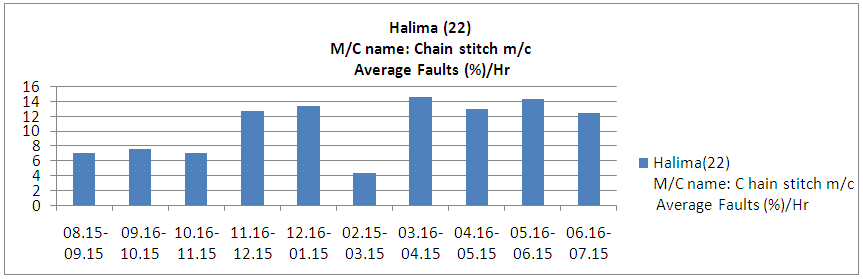 | Figure 14. Average Faults (%)/Hr of Halima |
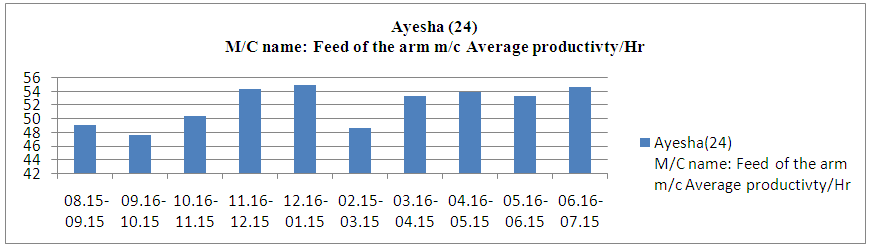 | Figure 15. Average productivity/Hr of Ayesha |
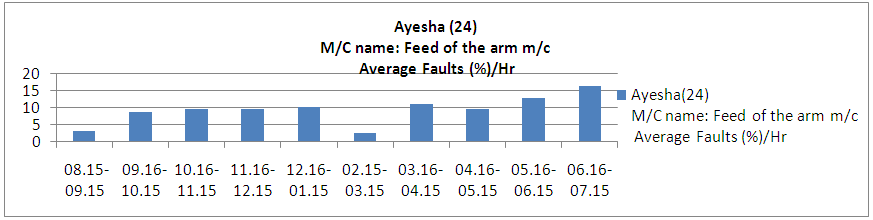 | Figure 16. Average Faults (%)/Hr of Ayesha |
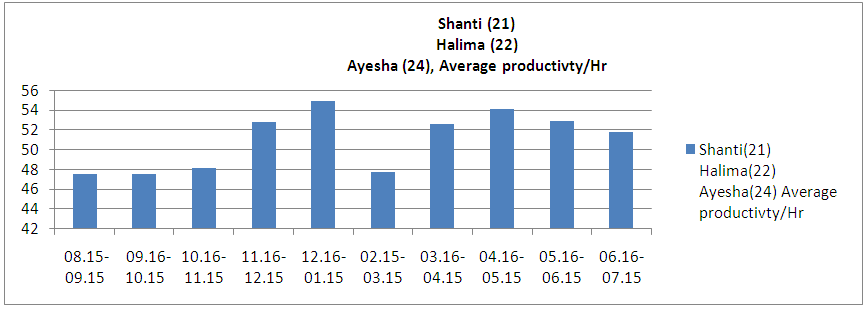 | Figure 17. Average productivity/Hr |
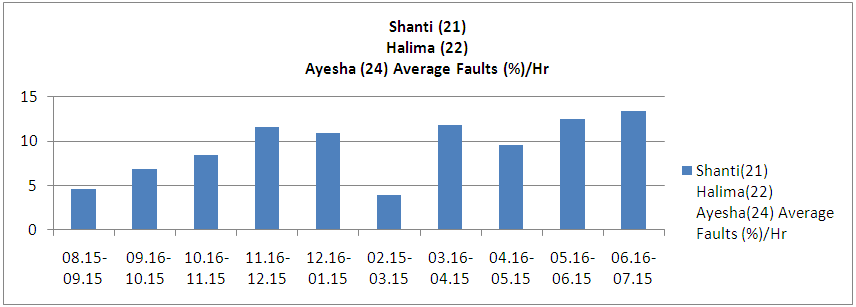 | Figure 18. Average Faults (%)/Hr |
3.5. Overall Finding of These Research
Progression of day, It has been observed that productivity increases side by side faults percentage also increases except some cases. Research shows that Shanti in Day 1 and Ayesha in Day 2 as productivity decreases but faults percentage increases. This shows that progression of day perhaps worker can feel moderate amount of impact of fatigue and boredom. Research shows that it will not follow any pattern or difficult to predict which day they will feel the impact of fatigue and boredom. Progression of day impact of fatigue and boredom depends not only the working environment but also depends on responsibilities of worker in their personal life. Research shows that three worker Shanti, Halima and Ayesha they have taken significant amount of rest in different portion of day which perhaps keeps them away from the impact of fatigue and boredom. Individual worker may have certain amount of impact of fatigue and boredom in different day basis but overall result of these three operator shows it was a negligible amount of impact of fatigue and boredom. Progression of Time, It has been observed that productivity increases side by side faults percentage and productivity was lower in morning time. Each worker they are having a fixed salary for their 08.15am to 07.15pm duty in each day. When supervisor reported operator for their low productivity in work, then they improve their productivity. For that reason, morning time worker shows slow progress in their work. Suddenly introduction of work in factory after long hours of break, cope up with the sudden environment and adjusting with the work creates low productivity in morning time. Before lunch break, this scenario indicates that there is no significant impact of fatigue and boredom in garments production. Research shows that three operator their work breakdown table shows that after few hours of production, every hour interval they take significant amount of rest which help them to prevent themselves from fatigue and boredom in before lunch break. It has been seen that productivity lower in after lunch break. During lunch break, three workers they complete their meal in short time and rest of the time they spend sleeping on the floor. From sleeping condition all of a sudden introduction of work creates sluggishness and drowsiness among worker which creates few hour low productivity after lunch break. After few hours of production, productivity starts to decrease but faults percentage increases. Three worker their work breakdown table shows that after first few hours, every hour interval significant amount of rest that they have taken to continue their work. Though they have taken rest different reason like headache, drowsiness, pain and sluggishness but that’s not quite enough to kept away them from the impact of fatigue and boredom. These scenario indicates that, progression of time at the end of the day few hour production slot, there is moderate amount of impact of fatigue and boredom in garments production.
4. Conclusions
Clothing industry is one of the largest industries in Bangladesh. Most of the workers in that industry are women. They have their family burden to be carried out. Worker living one condition but when they go for work they will have to be accepts another condition. Even a skilled worker will behave like unskilled worker if he or she got the impact of fatigue and boredom. This work has been done in only one garments factory in Bangladesh and calculating faults percentage of garments for one particular style. Also this experiment carried through woven only tops item (Mans woven dress shirt). In near future more research can be done for different factory, different buyer different products, Workers with different ages and different working condition to make comparison between them. Also this experiment can be carried out through different season like summer, winter and spring. Near future worker blood pressure, heart beat rate and pulse oximetry oxyhemoglobin saturation (SpO2) can be measured during their work in production at different production slot in a interval basis.
References
[1] | Muhammad., A. (2011). Wealth and Deprivation: Ready-made Garments Industry in Bangladesh. Economic and Political Weekly, Vol. 46, No. 34, pp. 23-27. |
[2] | Jain, D.R. (2014). Impact of work environment on job satisfaction. International Journal of Scientific and Research Publications, Volume 4, Issue 1, pp.1-8. |
[3] | Shackleton, V. (1981). Boredom and Repetitive Work: A Review. Emerald Insight, 31-35. |
[4] | Jahandideh, S. (2012). Job Scheduling considering both. Ottawa: University of Ottawa, In Mechanical Engineering-Ottawa-Carleton Institute for Mechanical and Aerospace Engineering. |
[5] | Haque, M.N. (2016). Impact of worker fatigue and boredom in garments production line. Institutional Engineering and Technology, Volume 6, Issue 1, pp.1-10. |
[6] | Mann, S (2015). The british psychological society. Retrieved from www.thepsychologist.bps.org.uk: https://thepsychologist.bps.org.uk/volume-20/edition-2/boredom-work. |
[7] | Loukidou, L., Clarke, J.L. & Daniels, K. (2009). Boredom in the workplace: More than monotonous tasks, International Journal of Management Reviews, Volume 11, Issue 4, pp.381-405. |
[8] | Berg, P., Appelbaum, E., Bailey, T & Kalleberg, A.L. (1996). The performance effects of modular production in the apparel industry, Volume 35, Issue 3, pp.356-373. |
[9] | Haque, M.N. (2016). Impact of marker efficiency in fabric consumption. International journal of textile science, Volume 5, Issue 5, pp.96-109. |
[10] | Patwary, M. R. (2013). Faults in garments. Retrieved 2013, from Define Textile: http://www.definetextile.com/2013/08/faults-in-garments.html. |