Md. Hasan-Al Mamun1, Asheke Mostofa2, Md Anwar Hossain1, Monir Khan2, Md. Zakaria1, Most Sabina Yeasmin3
1College of Chemistry and Chemical Engineering, Wuhan Textile University, Hubei, China
2College of Textile Engineering, Wuhan Textile University, Hubei, China
3Department of Chemistry, National University, Gazipur, Bangladesh
Correspondence to: Md. Hasan-Al Mamun, College of Chemistry and Chemical Engineering, Wuhan Textile University, Hubei, China.
Email: |  |
Copyright © 2017 Scientific & Academic Publishing. All Rights Reserved.
This work is licensed under the Creative Commons Attribution International License (CC BY).
http://creativecommons.org/licenses/by/4.0/

Abstract
Modal fiber is a regenerated cellulosic fiber and it is more absorbent than cotton or other synthetic fiber. The aim of our project work is to dye the modal fabric with two types of reactive dye i.e MFT+VS type reactive dye and MCT+VS type reactive dye. And observe the color yield on modal fabric & also compare the wash & rubbing fastness on dyed textile. For this we produce 4 type of shade 0.5, 1.5, & 4 using MFT+VS and MCT+VS type reactive dye. Here we see that color yield on modal fabric in case of MCT+VS type reactive dye is better than MFT+VS type reactive dye. Also we observed that wash & rubbing fastness of MCT+VS type reactive dye is better than MFT+VS type reactive dye.
Keywords:
Modal Fabric, Reactive dye, Scouring, Bleaching, Colorfastness, Wash fastness, Rubbing fastness
Cite this paper: Md. Hasan-Al Mamun, Asheke Mostofa, Md Anwar Hossain, Monir Khan, Md. Zakaria, Most Sabina Yeasmin, Effect of Reactive Groups of Reactive Dyes on Dyeing of Modal Fabrics, International Journal of Textile Science, Vol. 6 No. 6, 2017, pp. 158-164. doi: 10.5923/j.textile.20170606.04.
1. Introduction
Modal is a kind of man-made material. It's a variation of rayon, made by spinning Cellulose fibers. It's more absorbent than cotton or other synthetic fabrics. It also takes Dye well, and is very colorfast. It has a soft, slinky texture, making it comfortable to wear [1]. Modal is essentially a variety of rayon. It is made from beech trees and is about 50% more water-absorbent than cotton. So dye can be absorbed more quickly than cotton Modal is a registered trademark of Lensing AG. Modal fabric will not pill like cotton, and is resistant to shrinkage and fading. It is extremely smooth and soft. Modal can be ironed. Modal has many uses. It's soft and comfortable, so it works well for clothing. It's also Colorfast, which means it doesn't fade after wearing and washing. It's for women's Clothing more often than men's, as it has a draping, slinky effect that goes well with Women’s tops and dresses. Since it's very absorbent, it's often blended with cotton and other fibres to make things like towels, bath mats, and bathrobes. It's also a popular fibre for bed sheets, because its colorfast quality can withstand a lot of washing in hot water. Modal is fairly colorfast, so can be washed in warm or hot water. Can withstand washing them with r regular laundry at any temperature with any detergent [2]. However modal can get pilly, and it stretches out easily. It should wash on the delicate cycle. Hand washing clothing in cold water keeps pieces looking new for longer. Sheets and towels made from modal fabric are fairly maintenance-free. However, clothing is a different story. Modal stretches out easily, so should be avoid hanging modal on wire hangers; the shoulders may become misshapen. Using padded hangers, or folding pieces [3]. This fabric is also prone to pilling pressing too hard can damage the fabric. Reactive dyes was introduced in 1956, primarily belongs to a class of highly colored organic substances. While dyeing the reactive groups of reactive dyes forms covalent bond between fiber polymer and dye which makes dye integral part of fibre. Hence, they are known for its enhanced fastness property [4]. These dyes have stable electron arrangement which protect fiber from the adverse effect of ultra-violet rays. The significant chemical bonding improves the overall color stability and wash ability of the product makes these dyes most permanent of all other dye types. Undoubtedly, it is one of the most popular dyes used in textile industry all across the world. Reactive Dye is the dye of choice for all cellulose (plant) fibers, like cotton, Rayon, hemp, linen, Tencel, Modal, bamboo, etc. (For dyeing silk, wool and other protein fibers, see Dyeing Wool and Silk with Fiber Reactive Dyes) The chemical bond of these dyes is permanent, so once all the excess dye is washed out an infant can chew on the fabric and it will not come off [5].
2. Experimental Part
2.1. Materials & Machine Used
2.1.1. Fabric Used
Take (100%) modal fabrics from lab its standard weight 135g/m2 and gray color.
2.1.2. Chemicals Used
Here mention some chemicals name those are Chinese and German origin. Used famous chemicals company Color root’s chemicals & Some famous German’s chemicals, those are Wetting agent, Hydrogen peroxide (50%), Sodium Hydroxide, Sodium Carbonate, Stabilizer, Detergent, Reactive Dye (MCT-VS), Reactive Dye (MFT-VS), Hydroze.
2.1.3. Machines Used
We use the several numbers of machines in this experiment. Sample Dyeing M/C: scouring and dyeing machine. Machine Capacity is 50kg. Bursting Tester, Fabric strength testing machine. Washing M/C, Color fastness testing machine, Crock meter: For rubbing fastness. Sample dyeing m/c, Washkator, Electric Balance, Chrokemeter.
2.2. Scouring & Bleaching
Recipe for normal scouring & bleaching: 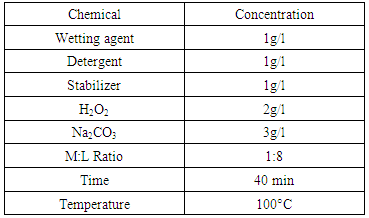 |
| |
|
Scouring & Bleaching of modal fabric is carried out in Open bath Process at temperature (i.e 100°C), three M:L ratio(1:40) using following recipes. Time is kept for temp. 100°C is 40 min.
2.2.1. Dyeing Recipe
For 0.5% Shade (1% stock solution):Salt =50gm/L (25% stock solution)Soda Ash=5gm/L (5% stock solution)Wetting Agent=1cc/LFor 1.2% Shade (1% stock solution):Salt =65gm/L (25% stock solution)Caustic Soda=1.5gm/L (5% stock solution)Wetting Agent=1cc/LFor 2.5% Shade (1% stock solution):Salt =80gm/L (25% stock solution)Caustic Soda=2.25gm/L (5% stock solution)Wetting Agent=1cc/LFor 4% Shade (1% stock solution):Salt =80gm/L (25% stock solution)Caustic Soda=2.5gm/L (5% stock solution)Wetting Agent=1cc/LTime = 40 minTemperature = 60°CPH = 10 - 13
2.2.2. Dyeing Procedure
1. Sample dyeing machine pots are washed by hydroze and sodium hydroxide.2. 16 pots are taken for dyeing 16 samples.3. Dye and other chemical auxiliaries and fabric are taken according to recipe in 16 pots.4. Pots are sealed properly.5. Pots are set in sample dyeing machine.6. Machine temp set to 60 degree and dyeing time is 40 minutes after temp. Reaching 60°C7. After dyeing samples are removed from the pots and hot wash is done at 60°C for 10 minutes.8. Then sample are washed by cold water.9. Then samples are dried by drier.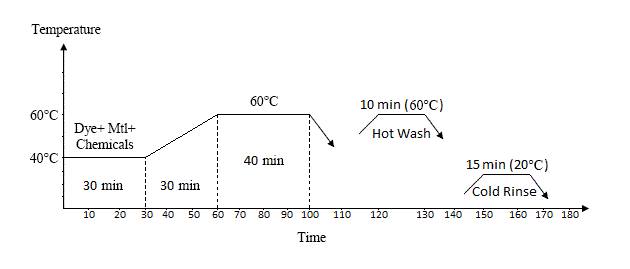 | Figure 1. Rest of calculations are given in the chart |
2.3. Wash Fastness Test
The property of a dye to retain its color when the dyed (or printed) textile material is exposed to conditions or agents such as light, perspiration, atmospheric gases, or washing that can remove or destroy the color. A dye may be reasonably fast to one agent and only moderately fast to another. Degree of fastness of color is tested by standard procedures. Textile materials often must meet certain fastness specifications for a particular use.It is always useful and interesting to test the dye which is to be used on a sample of the yarn or fabric to be dyed. The outcome will depend on the fabric, the mordant that has been used and dye that has have been chosen. Testing is best carried out on a series of Groundnuts marked (for identification) samples, which have been mordant with a number of different mordents. Tests can be carried out for light, water Tests can be carried out for light, water and washing fastness using simple standard test methods.
Washing Fastness Follow these Steps:• Take two pieces of fabric about 5cm by 5cm, one of which is undyed cotton and the other undyed wool. Stitch them together along one side.• Take some sample strips of the dyed yarn and spread them evenly between the two pieces of cloth so that they overlap both sides. If dyed fiber is being tested a combed sample can be used in place of the yarn.• Sew around all four sides of the cloth so that the yarn is held in place.• Prepare a similar specimen with dyed materials that has satisfactory properties and place them in two jars with screw lids containing a solution of 5gm per liter, Licaple solution at 30°C.• Agitate the two jars gently for 30mins, then remove the fabrics and wash them gently in clean water for 5mins. Open the stitching and separate the pieces to dry in air. Examination:• Place the dyed yarn next to a sample of the same material which has not been tested, and compare the change which has taken place. Compare also with the control sample with satisfactory properties. If the dyeing being tested shows equal or less change than the satisfactory sample, then it is as good as the satisfactory sample.• Place the wool and cotton cloths next to samples of the same material which have not been tested and compare them with the cloths that have been tested with a satisfactory dyeing. Equal or less staining shows equal or better fastness.
2.4. Rubbing Fastness
Fastness to rubbing is an off line quality assurance system. Rubbing fastness measurement is important one to know the ability of the dyed fabrics against the rubbing or staining. This type of test shows the fixation of the dyes with the fabric. When rubbing fastness is found good then it also determine that the washing fastness of the fabric will be good.
Rubbing fastness is measured in dry and wet form of the fabric. The rubbing fastness properties of the textile material are measured by comparing the tested fabrics with the grey scale and staining scale.Rubbing fastness of the material is measured as the following way in most of the dyeing industry.Sample: Following sample is required to measure the rubbing fastness.• Dyed fabric -15 cm x 5 cm• White Test Cloth -5 cm x 5 cm
2.5. Features of Crock meter
v To determine the Color Fastness of Textiles.v The equipment consists of a counter.v It is provided with a flat peg.v It also consists of an operating handle.v Tests the color fastness of the textile in a very accurate manner.v It gives not only accurate but quick results also.
2.5.1. Specifications of Crock Meter
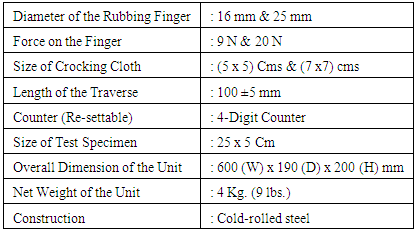
2.6. Rubbing Fastness Measurement Procedure
It is a step by step method to measure the rubbing fastness properties. Rubbing fastness of the material is done in dry and wet form like the following way.Dry Rubbing: • Properly mount your specimen and test cloths. The counter has to be reset by moving the knob on the left side of the counter. The finger is positioned on the specimen at the base’s front end and handle is rotated in the clockwise direction at the rate of approximately 1 revolution per second. The handle is then rotated equal to the number of strokes specified by the test method. • When the desired number of strokes is reached, the crocking cloth is removed from the finger and its degree of staining has to be evaluated by SDC grey scale.Wet Rubbing: • A fresh piece of crocking cloth is soaked in distilled water and the excess water is removed so that it contains its own mass of water. • The wet piece of the crocking cloth is fixed over the end of the finger of the Crockmeter and the test is undertaken. • The dyed or printed fabric has to be mounted on a lower platform. • Then 10 cycles are rubbed with a white fabric, which is mounted on a peg in the upper rubbing arm. • Then the extent of color that rubs away onto the white fabric against a color transference scale has to be determined. • The rubbing action of the peg+ enabled fibers from the upper colored flannel fabric surface to be transferred onto the white backing fabric mounted on the lower platform. • The cloth is then removed to evaluate the discolor level in comparison with a gray-scale.
3. Result & Discussion
3.1. Result of Wash Fastness Test
MFT+VS {Staining Value (Gray Scale)}  |
| |
|
MFT+VS {Change Value (Gray Scale)}  |
| |
|
Discussion: For MFT+VS Dye we observe that with increasing Shade% Wash fastness property decrease gradually, for light shade Fastness properties are excellent and for deep shade they are good or fairly good.MCT+VS {Staining Value (Gray Scale)}  |
| |
|
MCT+VS {Change Value (Gray Scale)}  |
| |
|
Discussion: For MCT+VS Dye with increasing Shade% Wash fastness property decrease gradually, for light shade Fastness properties are excellent or good and for deep shade they are fairly good.
3.2. Result of Rubbing Fastness Test
MFT+VS {Dry Staining Value (Gray Scale)) MFT+VS {Wet Staining Value (Gray Scale))  |
| |
|
Discussion: For MFT+VS Dye we observe that with increasing Shade% Rubbing fastness property decrease gradually, for light shade Fastness properties are excellent and for deep shade they are good or fairly good. Basically in case of Dry Rubbing, it shows excellent fastness Property. MCT+VS {Dry Staining Value (Gray Scale))  |
| |
|
MCT+VS {Wet Staining Value (Gray Scale))  |
| |
|
Discussion: For MCT+VS Dye we observe that with increasing Shade% Rubbing fastness property decrease gradually, for light shade Fastness properties are Good and for deep shade they are fairly good. Basically in case of Dry Rubbing, it shows Good fastness Property and for wet Rubbing, fastness properties are moderate.
4. Conclusions
In this project work we used two types of reactive dye i.e MFT+VS & MCT+VS. To observe the dyeing effect we produce 4 types of shades 0.5%,…………… like cotton dyeing process for both types of reactive dyes. Also we measure the wash fastness & rubbing fastness for all kinds of shades. It is observed visually that color yield on modal fabric with MCT+VS type reactive dye is better than MFT+VS type reactive dye for all shade%. From this we can conclude that the tectorial strength of MCT+VS type reactive dye is better than MFT+VS type reactive dye due to presence of chlorine. Also we observe that the wash & rubbing fastness of dyed fabric using MCT+VS type reactive dye is better than MFT+VS type reactive dye. From here we can conclude that the bond strength between –OH group of cellulose and MCT+VS group of reactive dye is stronger than MFT+VS type reactive dye. Main aims of this project different reactive groups on reactive dye apply on modal fabrics.
References
[1] | Vankar, P.S., R. Shanker, and A. Verma, Enzymatic natural dyeing of cotton and silk fabrics without metal mordants. Journal of Cleaner Production, 2007. 15(15): p. 1441-1450. |
[2] | Ibrahim, N., et al., Effect of cellulase treatment on the extent of post-finishing and dyeing of cotton fabrics. Journal of Materials Processing Technology, 2005. 160(1): p. 99-106. |
[3] | Amorim, A.M., et al., The application of catalase for the elimination of hydrogen peroxide residues after bleaching of cotton fabrics. Anais da Academia Brasileira de Ciências, 2002. 74(3): p. 433-436. |
[4] | Gulzar, T., et al., Eco-friendly dyeing of gamma ray induced cotton using natural quercetin extracted from acacia bark (A. nilotica). Journal of natural fibers, 2015. 12(5): p. 494-504. |
[5] | Zhi-qin, W., A Research on the Mercerizing of Naturally Colored Cotton Knitted Fabric by means of Biological Finish Technique [J]. Journal of Huizhou University, 2003. 6: p. 005. |
[6] | El-Zawahry, M., H. Helmy, and A. Abou-Okeil, Enzymatic treatment and its influence on finishing and dyeing properties of jute fabrics. Research Journal of Textile and Apparel, 2009. 13(4): p. 34-44. |
[7] | Moin, C.J. and A. Mahabubuzzaman, Process for level dyeing of 100% cotton knit fabrics with reactive dye. J Innov Dev Strategy, 2009. 3: p. 1-8. |
[8] | Varadarajan, G. and P. Venkatachalam, Sustainable textile dyeing processes. Environmental chemistry letters, 2016. 14(1): p. 113-122. |
[9] | Galante, Y.M. and C. Formantici, Enzyme applications in detergency and in manufacturing industries. Current organic chemistry, 2003. 7(13): p. 1399-1422. |
[10] | Xiumei, Z. and X. Liming, The Application of Cellulase in Bio-finishing of Cellulosic Fabrics [J]. Journal of Textile Research, 2004. 3: p. 048. |
[11] | Duran, N. and M. Duran, Enzyme applications in the textile industry. Coloration Technology, 2000. 30(1): p. 41-44. |
[12] | Hao, L., et al., The synchronized wash-off of reactive-dyed cotton fabrics and decolorization of resultant wastewater using titanium dioxide nano-fibers. Carbohydrate polymers, 2015. 125: p. 367-375. |
[13] | Samanta, K.K., S. Basak, and S. Chattopadhyay, Eco-friendly coloration and functionalization of textile using plant extracts, in Roadmap to Sustainable Textiles and Clothing. 2014, Springer. p. 263-287. |
[14] | Rémi, E., et al., Studies on photofading and stable free radical formation in reactive dyed cellulosic systems under their exposure to light. Radiation Physics and Chemistry, 1996. 47(3): p. 461-463. |
[15] | Cavaco-Paulo, A., L. Almeida, and D. Bishop, Effects of agitation and endoglucanase pretreatment on the hydrolysis of cotton fabrics by a total cellulase. Textile Research Journal, 1996. 66(5): p. 287-294. |