Md. Hasan-Al Mamun1, MD. Anwar Hossain1, Zakaria1, Md. Kawshar Ahmed1, Md. Forhad Hossain1, Romjan Ali2, Most Sabina Yeasmin3, Lutfor Rahman4
1College of Chemistry and Chemical Engineering, Wuhan Textile University, Hubei, China
2College of Textile Science and Engineering, Wuhan Textile University, Wuhan, China
3Department of Chemistry, National University, Gazipur, Bangladesh
4Department of Textile Engineering, City University, Dhaka, Bangladesh
Correspondence to: Md. Hasan-Al Mamun, College of Chemistry and Chemical Engineering, Wuhan Textile University, Hubei, China.
Email: |  |
Copyright © 2017 Scientific & Academic Publishing. All Rights Reserved.
This work is licensed under the Creative Commons Attribution International License (CC BY).
http://creativecommons.org/licenses/by/4.0/

Abstract
Bleaching is the removal of unwanted colour from the textile fibres and typically involves the use of one of the four main bleaching agents, namely sodium hypochlorite, calcium hypochlorite, sodium chlorite and hydrogen peroxide. Cotton must be properly prepared for dyeing, printing and finishing. To prepare the cotton fabric for dyeing, printing and finishing process scouring & bleaching is the fundamental step. Prior to bleaching, most of the impurities present in the cotton material are removed by pressure boil under alkaline conditions. The H2O2 bleaching is the most common bleaching method, and is environmentally friendly (degradable into water and oxygen). The best bleaching whiteness can be obtained at pH 11 adjusted using caustic soda. When dyeing is performed without a drying process after the H2O2 bleaching, the problem of residual H2O2 arises. 10ppm of residual H2O2 or more causes dyeing problems, bleaching is used for destructing of natural coloring matters to impart pure permanent and basic white effects suitable for the production of white finishes, level dyeing and desired printed shade.
Keywords:
Cotton Fabric, Biopoloshing, Scouring, Bleaching, Colourfastness, Spectra flash SF650
Cite this paper: Md. Hasan-Al Mamun, MD. Anwar Hossain, Zakaria, Md. Kawshar Ahmed, Md. Forhad Hossain, Romjan Ali, Most Sabina Yeasmin, Lutfor Rahman, Effect of Different Types Scouring against Different Types of Bleaching Process on Dyeing of Cotton Fabric with Monochlorotriazine (Hot Brand) Reactive Dye, International Journal of Textile Science, Vol. 6 No. 5, 2017, pp. 128-134. doi: 10.5923/j.textile.20170605.02.
1. Introduction
The bleaching process includes three main steps, namely (i) saturating the fabric with the bleaching agent and other necessary chemicals (ii) raising the temperature to the recommended level for the particular textile and maintaining that temperature for necessary duration and (iii) thoroughly washing and drying the fabric. [1] Conventionally, bleaching with bleaching powder or sodium hypochlorite was carried out at room temperature. However, hypochlorite bleaching units of textile bleaching processes generate more AOX 17.2–18.3 mg L-1) and hence they belong to the category of banned chemicals, being non-ecofriendly in nature. From quality control point of view, the drawback is that the whiteness produced by these bleaching agents is not permanent. They also consume more water (45–80 L/ kg of yarn/cloth). On the other hand, bleaching with hydrogen peroxide hardly generates the AOX in the effluents and the water consumption is also comparatively less (40 L/ kg of yarn/cloth)2. [1]Hydrogen peroxide bleaching is also performed under alkaline conditions and, as a result, may be combined with the scouring process. Hydrogen peroxide bleaching is ecofriendly and it is carried out at pH (10.5–11) and temperature (80–85)°C for 4 h conventionally in the presence of sodium silicate as a stabiliser. However, sodium silicate is not ecofriendly and also imparts harshness to cotton material. Bleaching with hydrogen peroxide requires a large amount of steam (2.5 kg/kg of fabric), thereby adding to the fuel cost. Now-a-day’s fuel is becoming expensive due to fast depletion in fuel reservoir. Thus, although it is environment friendly, the rising fuel cost tends to make hydrogen peroxide bleaching an uneconomical process. [1]Conservation of energy is the only step essential to overcome the mounting problems of the worldwide energy crisis and environmental degradation. The approach, therefore, should be based on the process intensification, making most of the energy used in a process and, if not possible, process modification so as to reduce the energy requirements. One such approach is the combined scouring and bleaching of cotton, which has the potential of saving the energy as well as time required for making cotton ready for further value additions such as dyeing, printing, finishing, etc. [1]The other possibility is to keep the temperature low for bleaching. This may appear possible since the scouring process removes almost all impurities from cotton, leaving behind only the coloring matter to be removed through oxidative bleaching. [1]
2. Experimental Part
2.1. Materials & Machine Used
2.1.1. Fabric Used
Cotton fabrics are collected from our lab for performed this experiment, which is single jersey knitted fabric.
2.1.2. Chemicals Used
Caustic Soda (NaOH), Hydrogen peroxide (H2O2), sequestering agent, Detergent, Acetic acid (CH3COOH), Bio-Scouring agent (pectinase enzyme), Bio-Polishing agent (Celluloses enzyme) is used in this experiment. Reactive Dye, Salt, Soda Ash (Na2CO3), wetting agent are also used, which are collected from our lab. used chemicals provide by Color root chemical company, china & Colorant chemicals, India.
2.1.3. Machines Used
We use the several numbers of machines in this experiment. Sample Dyeing M/C: scouring and dyeing machine. Machine Capacity is 50kg. Bursting Tester: Fabric strength testing machine. Washing M/C, Color fastness testing machine, Crock meter: For rubbing fastness. Most of machines are Chinese origin.
2.2. Alkali Scouring Process
The following recipe is used to alkali scouring process.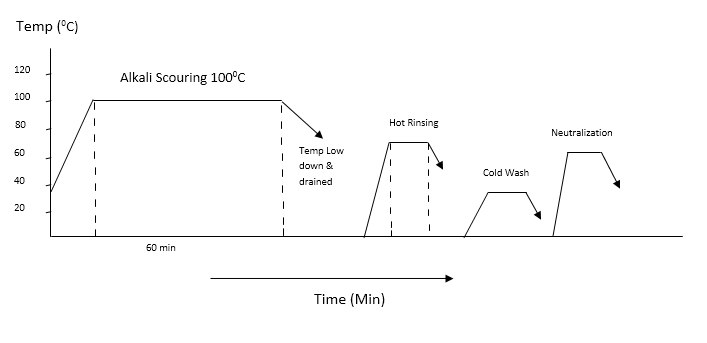 | Figure 1. Scouring Curve with alkali |
Description of the scouring processAt first the fabric is taken in dye bath. The process is run with fabric at room temperature with required amount of water. Then Sequestering agent and detergent are added in the dye bath. After few min. alkali is added and raised the temperature to 95-100°C. The process is run in this temperature for 60 minutes. After completing scouring drain out the liquor from the dye bath. Rinse twice with hot (around 70°C) and cold water. Neutralize the fabric with acetic acid treatment and carry out next process.
2.3. Bio-scouring Process
The following recipes are used to bio-scouring process: Enzymes or biocatalysts are very specific in their reactions and there are different enzymes for each part of a series of reactions, such as those occurring in vegetable and animal life processes. The specificity of function of enzymes is often compared with the lock-and-key system, but actually their functioning is much more complex than this simple analogy. Enzymes themselves are biodegradable and are converted into harmless substances in the effluent after the process [10].Enzymes are high molecular weight proteins that are produced by living organisms. These are composed of ca.200–250 amino acids that catalyse (i.e. lower the activation energy) of many organic reactions without being consumed in the process. Enzyme activity can, however, be reduced or even completely destroyed (denatured) by high temperatures, extremes of pH and high concentrations of electrolytes that destroy their three-dimensional structures. Heavy metal ions andoxidizing and reducing agents also deactivate theenzymes [11].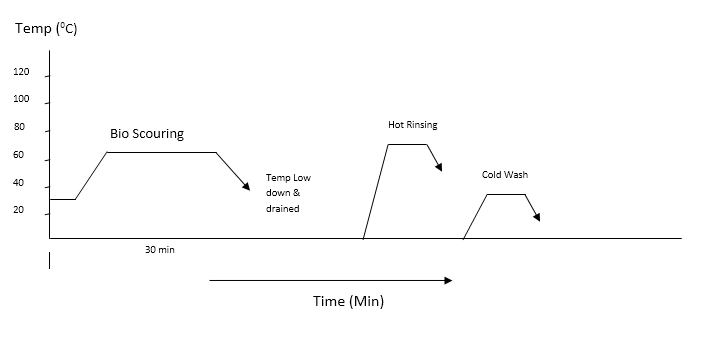 | Figure 2. Scouring curve with enzyme |
Description of bio-scouring processThe dye bath is set with fabric at room temperature with required amount of water. The temperature set at 40°C and kept it about 15 minutes. Then the Bio-Scouring agent added and raises the temperature to 60°C, kept it for 20 minutes. Cool down the bath temperature and drain out the liquor from the dye bath. Washed in 80°C for 5 minutes. Then the samples were rinsed with cooled water and dry it by using dryer. Then it’s prepared for next process.
2.4. H2O2 Bleaching
Working Procedure for H2O2 Bleaching:At first the weight of the sample was taken and the required amount of chemical was calculated. Then the required amounts of chemicals were taken into a bowl. After that the fabric was impregnated in the bath. Then the temperature was slowly raised until 90-95 degree centigrade. During this process the PH of the bath was checked very frequently. The process continued for 40-45 minutes. Then drain and hot wash, cold wash.
2.5. Bio-polishing
Bio-polishing is a finishing process that enhances fabric quality by decreasing the pilling tendency and fuzziness of (cellulose) knitted fabrics. This finishing process applied to cellulose textiles that produces permanent effects by the use of enzymes. This process removes protruding fibres & slubs from knitted fabrics, significantly reduces pilling, softens fabric hand and provides a smooth fabric appearance. Working Procedure for Bio-polishing:At first the weight of the sample was taken and the required amount of chemical was calculated. Then the required amount of chemicals were taken into a bowl. After that the fabric was impregnated in the bath. Then the temperature was slowly raised until 60-70 degree centigrade. During this process the PH of the bath and temperature was checked very frequently. The process continued for 10-15 minutes. Then drain and hot wash, cold wash.
2.6. Estimation of Scouring Effect
2.6.1. Drop Test
In a pipette a solution of 0.1% direct red is taken and is dropped on the fabric sample. Then the absorption of the colored drop is observed visually. There required some second to spread the drop. We noted the time taken to spread the drop. We also capture some image to differentiate the shape of the drop and compare them to the standard shape. It is important to the same amount of color dropped on the fabrics; otherwise the result may be changed. So extra care should be taken to drop color solution on the fabric. This test is very popular and easy to execute within a short tine. In this method, a 0.1% direct red solution is used. A drop of the dye solution is taken by a pipette orglass rod and put softly onto the sample surface. The nature of the absorption is observed carefully. Two thinks should be considered.a) The time for absorption the drop.
b) The shape of the absorbed area on the sample surface. [3]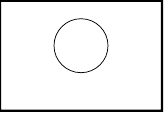
2.6.2. Scoured Fabrics Strength Test
Bursting tester is used to measure the strength of scoured fabric. At first insert the specimen under the tripod, drawing the specimen taut across the plate, and clamp specimen in place by bringing the clamping lever. At the instant of rupture of the specimen, swing the latch as far as it will go to bring the operating handle to a neutral position. Record the total pressure required to rupture the specimen. After rupture, and in rapid succession, release the clamping lever over the specimen.
2.7. Dyeing of Bio-Polish & without Bio-Polish Fabric
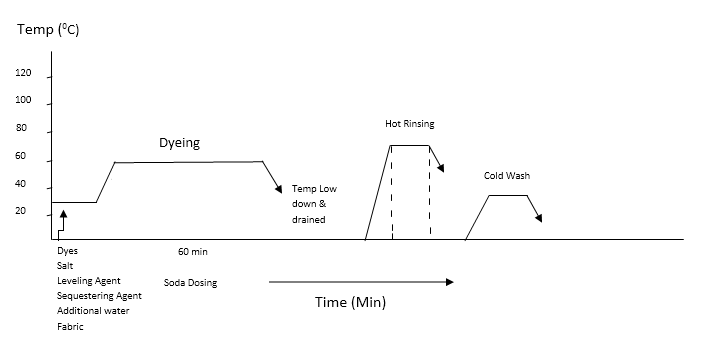 | Figure 3. Process curve for dyeing of cotton fabric with reactive dye |
Description of dyeing processThe dye bath is set at 30°C with the scoured fabrics and required water. Then sequestering agent, leveling agent are added and run it for 5 minute. The dye solution is added, after that the salt is added and run it for 5 min. Then soda is added by progressive dosing at 40°C and run the machine for 10 min. After that the temperature raised to 60°C within 10 min. and the m/c is run 60 min for dyeing. Drop out the dye bath liquor after the dyeing process.In after treatment process, the dyed fabric rinsed with cold water for 10 min. after rinsing the dyed fabric washed with soap and hot water. Then the dyed fabric dried by using dryer. And conditioning must be done before continuing the next process.
2.8. Evaluation of Fastness Properties
2.8.1. Wash Fastness
Wash fastness of the samples dyed under the optimized conditions was tested according to the ISO 687-1979 method. The test specimen of 10x4 sq. cm was placed in between the two adjacent, undyed test cloth pieces (cotton and wool for cotton and sewn along all four sides to form a composite specimen. Washing solution was taken with a liquor ratio of 1:50. The specimen was treated for 30 minutes at 60°C in sample washing machine. [3]The specimen was removed and rinsed with cold water. The stitch was opened on three sides and dried in a dryer. Evaluation was done for change in color of the treated test specimen and the degree of staining of the two pieces of adjacent fabrics with the help of grey scale and the rating was also noted.
2.8.2. Color fastness to Rubbing/Crocking Test Procedure
IS0 test method 766-1988 was followed to measure the rubbing fastness. For dry rubbing, a test specimen of 15x5 sq. cm was placed on the base of the crock meter so that it rests flat with its long dimension in the direction of rubbing. 5x5 sq. cm undyed bleached cotton was mounted on the tip of the finger. A spherical spiral wire clip holds the test cloth in place. The crock meter is operated to rub the specimen in a straight line along a track of 10cm long for 10 times in 10 seconds with a downward force of 9N. After rubbing, the degree of staining on the undyed fabric is evaluated using grey scale.
3. Results and Discussion
The NaClO bleaching is characterized in that the bleaching is performed at room temperatures without requiring a heating apparatus such as a steamer, and that the chemical cost is low. However, the disadvantages of the NaClO bleaching include relatively low bleaching whiteness and embrittlement of fabrics.No particular pH adjustment is required in the NaClO bleaching. The NaClO bleaching is usually employed for bleaching fabrics after Kier-scouring, or for bleaching towels. For towels, the two-step bleaching comprising the NaClO bleaching and the H2O2 bleaching is preformed to obtain full whiteness. The NaClO bleaching is also employed for jeans fade adjustment, etc.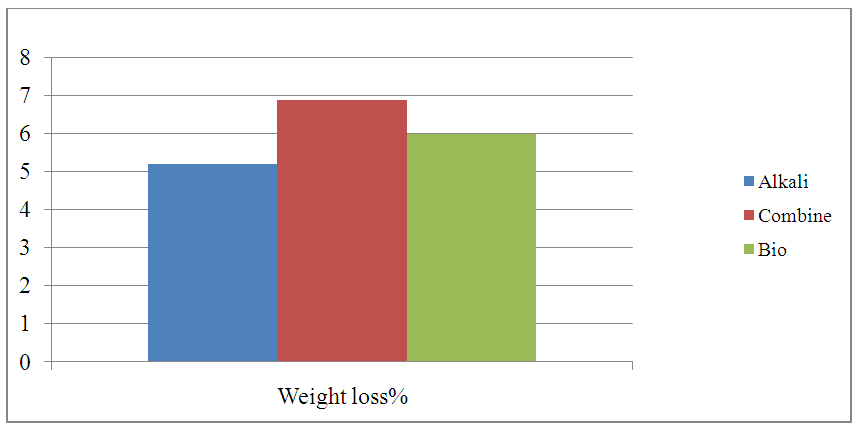 | Figure 4. Graphical Representation of Weight loss |
Table 1. Measurement of colored fabric strength 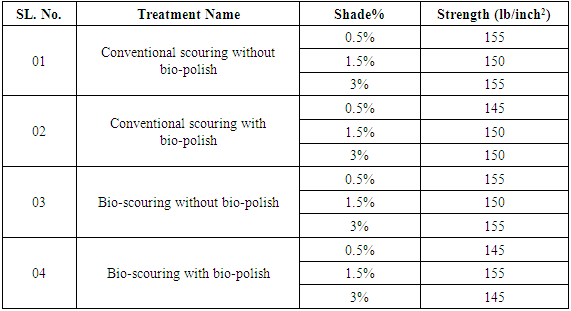 |
| |
|
From the figure 5 and 6 it can be said that the strength of all fabric is decreased after different treatment. In scouring & bleaching the strength loss is more than the others process. Because the fabric degradation is occurred due to use of alkali & hydrogen peroxide.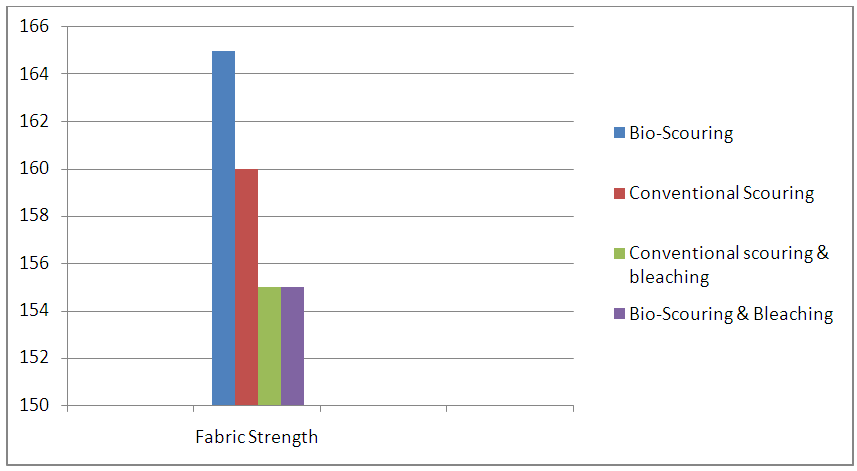 | Figure 5. Graphical Representation of Fabric Strength |
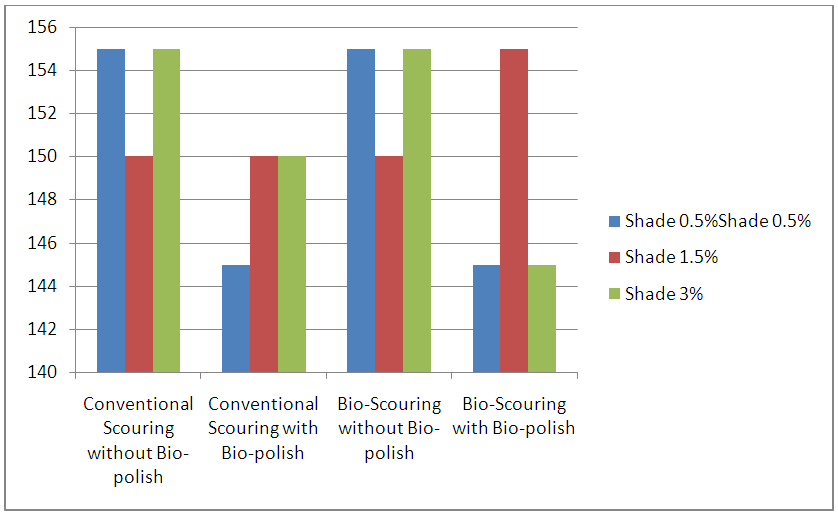 | Figure 6. Graphical Representation of Dyed Fabric Strength |
3.1. Wash Fastness Test
From the table 2 & 3 it can be said that the result of staining & change value of all fabric is nearly same, which is shown very good result for staining value of 0.5%, 1.5%, 3% shade, and from the table 3 it can be said that the result of change value of all fabric is same, which is shown very good result of Conventional scouring without bio-polish for 0.5%, 1.5%, 3% shade, Conventional scouring with bio-polish for 0.5%, 1.5% shade is very good and for 3% shade, which shown a good result.Table 2. Wash fastness for color staining 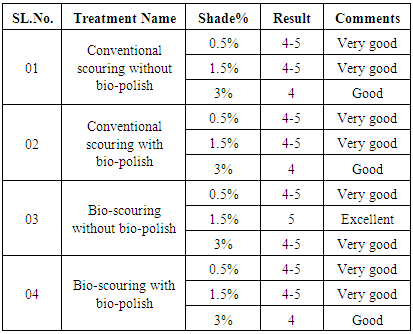 |
| |
|
Table 3. Wash fastness for color change 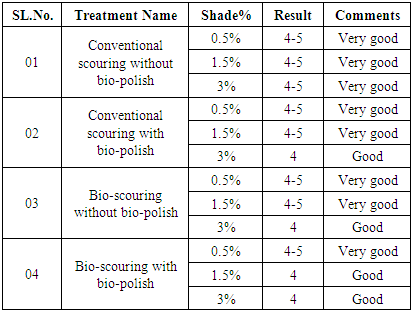 |
| |
|
3.2. Rubbing Fastness
From the table 4 it can be said that the result of rubbing fastness for dry of all fabric is nearly same, which is shown excellent, very good result. From the table 4 it can be said that the result of rubbing fastness to dry of Conventional scouring with bio-polish for 0.5%, 1.5% shade, excellent and for 3% is good. And for Bio-scouring with bio-polish 0.5% is excellent, 1.5% is good and for 3% is very good. So above the discussion, we can say that bio-scoured and bi polish fabric has very good rubbing fastness to dry.Table 4. Rubbing fastness to Dry 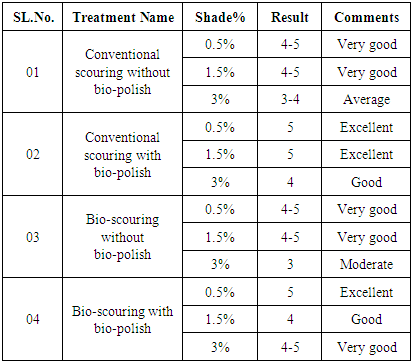 |
| |
|
From the table 5 it can be said that the result of rubbing fastness to wet of Conventional scouring with bio-polish for 0.5%, 1.5% shade, very good and for 3% is good. And for Bio-scouring without bio-polish 0.5%, 1.5% is average and for 3% is good. So above the discussion, we can say that Conventional scouring with bio-polish fabric has very good rubbing fastness to wet.Table 5. Rubbing fastness to wet 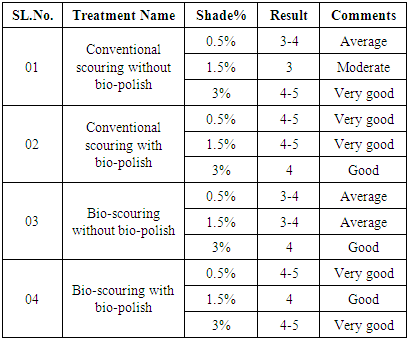 |
| |
|
4. Conclusions
From this project work, we have gained a brief practical knowledge about different types of Scouring (alkali, bio scouring) and bleaching (hydrogen peroxide, optical brightening agent, thio-sulphate). We have compared different types of pretreatment process and also identified their effect on dyeing process. We believe this little effort taken by us can play a significant role in future practical life. to improve practical knowledge to work in a textile factories. beleaching & scouring is a common problem in our textile factories so its help to know how can minimize those types of problems.
References
[1] | Ibrahim, N., et al., Effect of cellulase treatment on the extent of post-finishing and dyeing of cotton fabrics. Journal of Materials Processing Technology, 2005. 160(1): p. 99-106. |
[2] | Amorim, A.M., et al., The application of catalase for the elimination of hydrogen peroxide residues after bleaching of cotton fabrics. Anais da Academia Brasileira de Ciências, 2002. 74(3): p. 433-436. |
[3] | Gulzar, T., et al., Eco-friendly dyeing of gamma ray induced cotton using natural quercetin extracted from acacia bark (A. nilotica). Journal of natural fibers, 2015. 12(5): p. 494-504. |
[4] | Zhi-qin, W., A Research on the Mercerizing of Naturally Colored Cotton Knitted Fabric by means of Biological Finish Technique [J]. Journal of Huizhou University, 2003. 6: p. 005. |
[5] | El-Zawahry, M., H. Helmy, and A. Abou-Okeil, Enzymatic treatment and its influence on finishing and dyeing properties of jute fabrics. Research Journal of Textile and Apparel, 2009. 13(4): p. 34-44. |
[6] | Moin, C.J. and A. Mahabubuzzaman, Process for level dyeing of 100% cotton knit fabrics with reactive dye. J Innov Dev Strategy, 2009. 3: p. 1-8. |
[7] | Varadarajan, G. and P. Venkatachalam, Sustainable textile dyeing processes. Environmental chemistry letters, 2016. 14(1): p. 113-122. |
[8] | Galante, Y.M. and C. Formantici, Enzyme applications in detergency and in manufacturing industries. Current organic chemistry, 2003. 7(13): p. 1399-1422. |
[9] | Xiumei, Z. and X. Liming, The Application of Cellulase in Bio-finishing of Cellulosic Fabrics [J]. Journal of Textile Research, 2004. 3: p. 048. |
[10] | Duran, N. and M. Duran, Enzyme applications in the textile industry. Coloration Technology, 2000. 30(1): p. 41-44. |
[11] | Hao, L., et al., The synchronized wash-off of reactive-dyed cotton fabrics and decolorization of resultant wastewater using titanium dioxide nano-fibers. Carbohydrate polymers, 2015. 125: p. 367-375. |
[12] | Samanta, K.K., S. Basak, and S. Chattopadhyay, Eco-friendly coloration and functionalization of textile using plant extracts, in Roadmap to Sustainable Textiles and Clothing. 2014, Springer. p. 263-287. |
[13] | Rémi, E., et al., Studies on photofading and stable free radical formation in reactive dyed cellulosic systems under their exposure to light. Radiation Physics and Chemistry, 1996. 47(3): p. 461-463. |
[14] | Cavaco-Paulo, A., L. Almeida, and D. Bishop, Effects of agitation and endoglucanase pretreatment on the hydrolysis of cotton fabrics by a total cellulase. Textile Research Journal, 1996. 66(5): p. 287-294. |