Md. Khalilur Rahman Khan
Department of Textile Engineering, Bangladesh University of Business and Technology, Mirpur, Dhaka, Bangladesh
Correspondence to: Md. Khalilur Rahman Khan, Department of Textile Engineering, Bangladesh University of Business and Technology, Mirpur, Dhaka, Bangladesh.
Email: |  |
Copyright © 2017 Scientific & Academic Publishing. All Rights Reserved.
This work is licensed under the Creative Commons Attribution International License (CC BY).
http://creativecommons.org/licenses/by/4.0/

Abstract
Designers are concentrating on using of colored fancy yarns in all types of apparel having decorative effect, either knitted or woven, with creative ideas that can attract consumers of dynamically stimulated markets by adding minimum costs. In this study, the production techniques of some colorful mono fancy yarns are briefly described. Although colorful fancy yarn can be produced by plying operation after spinning stage by using two or more single yarns but here we would like to highlight only colorful mono fancy yarns those are produced by using ring spinning frame. Here, Glow yarn that is mainly produced by direct spinning system is also discussed briefly.
Keywords:
Fancy Yarn, Gradient yarn, Mottle Yarn, Injected Slub Yarn, Mosaic Yarn, Vario-Siro Yarn, Glow Yarn
Cite this paper: Md. Khalilur Rahman Khan, Study on the Production Techniques for Various Colorful Mono Fancy Yarns in Ring Spinning Frame and Glow Yarn, International Journal of Textile Science, Vol. 6 No. 4, 2017, pp. 105-109. doi: 10.5923/j.textile.20170604.02.
1. Introduction
Fancy yarns, also called novelty or effect yarns, and represents a category of yarns in which deliberate irregularities, discontinuities and color variations are introduced into the yarn structure with the primary intention being to produce enhanced aesthetic and fashionable impressions [1]. Nowadays, interest in fancy yarns creation, production, and applications is increasing to improve the appearance of the garment. Such yarns, because of their decorative effect in knitted and woven fabrics, have considerable commercial significance. Unending search for novelty applies to both men’s and women’s wear to give greater sales appeal. It also carries significant demand for children outerwear. Furnishing is also an important market area particularly curtains, blinds and wall coverings and upholstery [2]. In general, fancy yarn may be divided into two major categories: mono-fancy yarns and compound fancy yarns. The former are made from a single step fiber strand or multi-filament yarn in which irregularities are introduced during the conversion from fiber to yarn; the latter consists of two or more fiber strands used to provide the desired combined effects [1]. Fancy yarns having impression of lively color has leading impact in terms of fashion and appearance to the textile products. The impact of colorful fancy yarn in the fabric can also be heightened by careful planning of the contrast between fancy and plain yarns. Colorful fancy yarn finds applications in normal and high-fashion clothing. In most cases fancy yarns have a multithread structure composed of such components –core, effects and binder [3]. These types of fancy yarns are produced after spinning stages. In this paper, we will review only colorful fancy yarns produced during spinning stages. Ring spinning technology is widely used as the benchmark for staple yarn quality. Although production rate of ring spinning system is very much lower in comparison with that of the modern spinning system, but the opportunity of ring spinning system to produce fancy yarns by doing simple modifications in its structure enable this spinning system still best competent in the arena of yarn production unquestionably. In general, Literature reviews are in great demand in most scientific fields. The studies on already invented methods open the doors in the way of modifications by researchers. From this perspective, it is attempted to make a study on the methods of colorful mono fancy yarn production by ring spinning frame. In addition, applications of such colorful mono fancy yarn will be mentioned also. In this study, It is also tried to discuss the glow yarn in brief.
2. Production Techniques for Colorful Fancy Yarn
A. Gradient yarn:Gradient yarn is one where the colors change evenly from one color to the next [4]. The arrangement of roller drafting system for blending slivers of two colours on the draw frame in a controlled manner is shown in Fig. 1. The drafting system consists of two main sections: pre-drafting section and the main drafting section. The slivers of different colours are first pre-drafted separately, in the respective pre-drafting zones, and then fed together into the main-drafting section. Between the two drafting sections is a zone where no draft is applied on the slivers. This zone has been named as convergence zone. Changing its pre-draft can control the ratio of any colour in the output sliver. It is very important that the linear density of the output sliver remains constant with time. As long as drafts in the two pre-drafting zones are changed such that the mean pre-draft remains constant an output sliver with varying colour composition and constant linear density is obtained [5].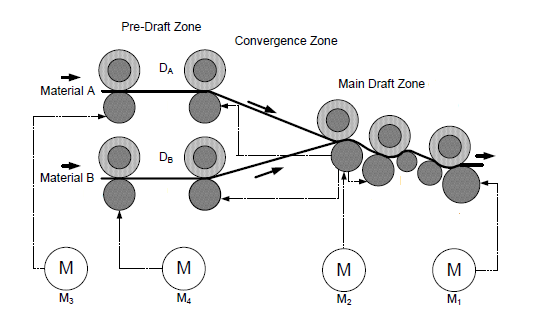 | Figure 1. Drafting arrangement for gradient yarn production |
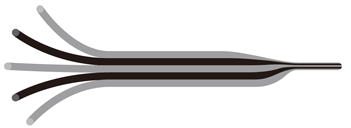 | Figure 2. Sliver blending |
The production process is fully controlled by the microprocessor. It can control the multi-motor coordinating movement. All moving parts can move respectively or co-operate with each other. Following the design it will deliver the exact quantity (acceleration) and length (time) of each sliver over the base sliver, to match the desired pattern in the sliver of multiple colors that can be spun on the spinning frame. Final yarn can be used as printed yarn. The gradient fancy yarn produced by this method can be used for knitted or woven to produce all kinds of color gradient applications [6]. A limitless range of gradient yarns can therefore be produced, varying the percentage and length of the color insertions continuously or in stretches as desired, keeping the slivers either constant or not constant.The yarn will be blended from several side-by-side slivers. By this method, the yarn color marbling will be grainier. Fabrics made from gradient yarn are shown in fig-3. Gradient yarn can be used for producing shawl, scarf, hat, tops etc.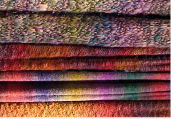 | Figure 3. Fabrics produced from gradient yarn |
B. Mottle Yarn: Mottle yarn is made by spinning from two rovings of different colors. The appearance is like mouline (made by folding two or more different colored yarns) but with less sharp contrast [7]. This system is a combination of spinning and doubling process at Ring Frame. In this system, similar mechanism of siro yarn production is used in ring spinning frame but with different colored rovings. A spinning triangle of mottle yarn is shown in fig-4.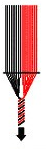 | Figure 4. Mottle Yarn production |
C. Injected slub yarn production:This system is the integration of slub producing mechanism with doubling process of colored rovings prior to spinning operation in order to produce a color injected slub yarn in ring spinning frame. It is also called patch yarn [8]. Injection slub yarn' is a specialized fancy yarn and it is made up of two different materials, one for 'Slub Portion ‘and the other for 'Base Yarn' shown in fig-5. Both the material will be dissimilar in nature, colour and character. Base Yarn Roving' will be directly fed through the middle roller and it is continuously producing 'base yarn' by the machine drive. One set of additional roving guide will be provided at the back zone to guide the base yarn Roving.Instead of machine drive, one servo motor is used to drive the back bottom fluted roller. Injected portion of roving will be only fed through the back pair of drafting rollers and it is running intermittently by servo motor with Variator Gear Box. Advance Digital encoders help to monitor the speed of Front roller and Back roller separately and act as 'Slub missing Stop Motion' [9]. Injected slub yarns are used for producing ladies shawl, pillow covers, shirting fabric, woven and knitting fabric, home furnishing and other types of slub fabrics. 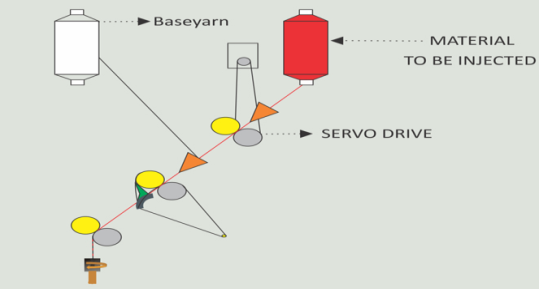 | Figure 5. Production of color injected slub yarn |
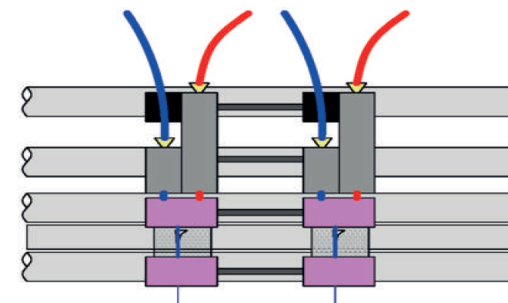 | Figure 6. Mosaic yarn production |
D. Mosaic Yarn:The mosaic yarn is a new revolutionary yarn. It is a trademark of Toyota Industries Corporation. Mosaic yarn for colour effects by the replacement of one roving by another of different colour. The count remains the same. It is produced by maintaining same thickness to get a printed yarn. The yarn suddenly changes color, not by dyeing or printing but by a change of the fed roving. The transition from one color to the next is extremely short, less than 1 cm, so the change is clean and precise, no tails of the previous color are dragged behind. The different color (or material) rovings are fed in the drafting system. One is fed at the 3rd roller and the second roving is fed at the second roller. The first roving is not affected by the speed of the second roller and the second roving is not affected by the third roller. The two roving are thus drafted without any break draft. When one roving is stopped the other has to start immediately after, otherwise the yarn would break. In order to join the end of one roving with the beginning of the other, a compact system is necessary to make the splicing of both yarns [10]. Mosaic yarns can be used for any type of plain fabric or knitted fabric.It is also possible to integrate the mosaic and slub effect in a printed yarn. In the mosaic slub yarn which is shown in fig-7(a, b, c). There is no portion in final yarn body of mosaic slub yarn where two different rovings are doubled. But in the injected slub yarn, two rovings are doubled together in final yarn body that means there have always a continuous base portion and an intermittent effect portion. This is the basic distinction between mosaic slub and injected slub yarn. 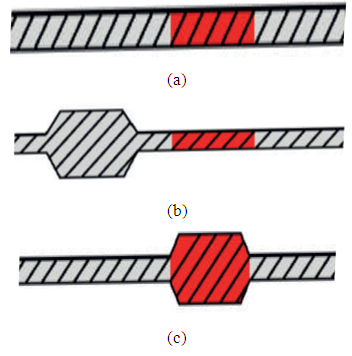 | Figure 7. (a) Plain mosaic yarn, (b) Slub in mosaic yarn & (c) Adding slubs to create mosaic effect |
E. Vario-siro yarn:For producing colorful vario-siro yarn in ring spinning frame, the two rovings are fed continuously but with different speed. Feeding speeds for the two rovings are changed in such a way that the mean thickness of fiber strand entering the main drafting zone remains constant. As a result, it is possible to produce a yarn with varying colour composition and constant linear density (shown in fig-8).  | Figure 8. Colorful vario-siro yarn |
3. Glow Yarn
Latest inventions and technologies play an integral part in the textile industry. The glow yarn is another example for the innovativeness of textile researchers [11]. Currently high-visibility clothing is worn to alert others in low light and dark conditions. Cyclists, railway and highway workers, airport workers, emergency services are common users of high-visibility clothing. However, these types of textiles are made from glow yarn. Glow yarns can be used creatively in many applications for embroidery, sewing thread, shoes, ropes, tents, beads etc. Glow yarn can be produced by direct spinning system. Glow yarn is generally two types: (i) Electroluminescent (EL) glow yarn and (ii) Photo luminescent (PL) glow yarn.
3.1. Photo Luminescent (PL) Glow Yarn
Photoluminescence is the one form of the luminescence in which the excitation energy source is incident light [12]. Photo luminescent (PL) glow yarn (shown in fig-9(a), (b)) is a new revolutionary luminous filament yarn developed by mixing, melting and extruding polyester chips with photo luminescent pigments. This is with strong light absorbing-storing-emitting luminescent materials. It automatically glows in the dark after absorbing sunlight for 3 minutes or luminous light for 20 minutes. One hour of sunlight exposure would enable the glow yarn to emit light for upto 3 hours continuously. This light absorbing process of absorbing-emit-storing-emitting can be repeated indefinitely [13].
3.2. Electroluminescent (EL) Glow Yarn
Researchers at The University of Manchester have developed high-tech battery-powered textile yarns that can be used to make clothing glow in the dark [14]. The yarn consists of an inner conductive core yarn, coated with electroluminescent ink -- which means it emits light when an electric current is passed through it -- and a protective transparent encapsulation, with an outer conductive yarn wrapped around it that is shown in fig-9(c) [15].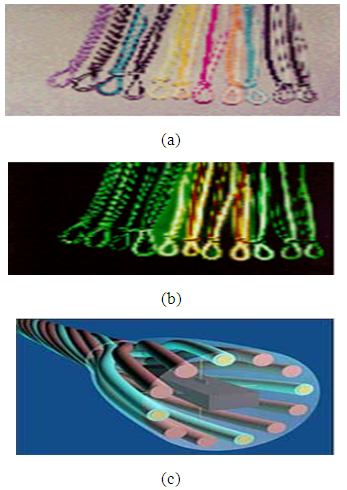 | Figure 9. Photo luminescent glow yarn (a) in normal light, (b) in dark & (c) Cross-sectional view of EL glow yarn |
Power from a battery is applied, and flows through the yarn and ink, creating an electric field, causing the fabric to glow. When the yarn gets power from the inverter, the resultant electric field between the inner and outer conductor causes the electroluminescent coating to emit light [11]. EL yarn can be easily incorporated into a knitted or woven fabric and the resultant active illuminating fabric provides illumination when it is powered. The luminance of a single strand of the EL yarn is greater than that of photo luminescent glow yarns, which are currently used in some high visibility applications [16]. A photo of fabric made from EL glow yarn is shown in figure- 10(b). 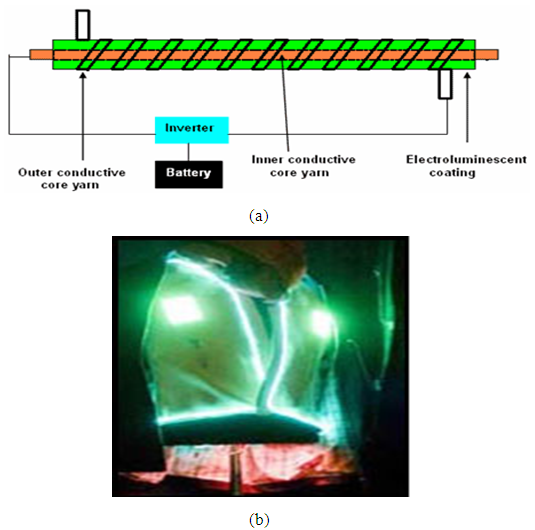 | Figure 10. (a) Electroluminescent (EL) glow yarn & (b) Fabric made from EL glow yarn in dark |
4. Conclusions
The basic purpose of producing colored fancy yarn is to add color that is mainly attributed to the value addition obtained in terms of visual effects of fashionable apparel. On the other hand, the application of glow yarn in apparels is increasing day by day for visibility purposes in dark area. Now a days many companies offer a wide range of above mentioned products. It is expected that in future market value of colored fancy yarn will exploit huge profits. It is highly predictable and also expected that new methods for producing more colored fancy yarns will be discussed by researchers in near future.
References
[1] | Y El Mogahzy, “Engineering Textiles: Integrating the Design and Manufacture of Textile Products”, Published by CRC press, Boca Raton, USA. Page-255. |
[2] | Dr. (Mrs.) Shaikh Tasnim Nisarahmed, Dr. S.S. Bhattacharya & Mrs. Sweety Agrawal, “Colour Analysis of Fancy Yarns Produced on Innovative Mechanical Crimp Texturising Apparatus”, International Journal of Engineering Research and Development ISSN: 2278-067X, Volume 1, Issue 10 (June 2012), PP.72-79. |
[3] | S. Petrulytė, “Complex Structure Fancy Yarns: Theoretical and Experimental Analysis”, ISSN 1392–1320 Materials Science (MEDŽIAGOTYRA). Vol. 9, No. 1. 2003. |
[4] | http://www.instructables.com/id/How-To-Spin-a-Rainbow-Gradient-Yarn/ |
[5] | S.M. Ishtiaque, J.K. Chatterjee, A.K. Battu, Apurba Das, V.K. Yadav and Narendra Kumar. , Proceedings of the 10th Asian Textile Conference ~ATC-10 ~ September 7-9, 2009 Ueda, Japan. |
[6] | Wenya Li, Xueqin Ren and Yan Sun, “A new technology of producing color gradient products”, Applied Mechanics and Materials Vols. 215-216 (2012) pp 368-371. |
[7] | http://0x9.me/yIkK2 |
[8] | http://lrtindia.com/lci/iss.html |
[9] | http://skaatindia.com/injslub.htm |
[10] | http://www.pintercaipo.com/en/products/mosaic |
[11] | Glow yarn for special effect textiles by: technicaltextile.net. |
[12] | https://www.google.com/patents/WO2003002794A1?cl=en |
[13] | http://www.swicofil.com/glow_yarn.html#Spinning%20Yarn |
[14] | https://www.sciencedaily.com/releases/2007/10/071026112117.htm |
[15] | https://www.photonics.com/Article.aspx?AID=31277 |
[16] | http://www.manchester.ac.uk/discover/news/article/?id=3174 |