Tipu Sultan1, Hosne Ara Begum2
1Department of Textile Engineering, Southeast University, Dhaka, Bangladesh
2Department of Yarn Engineering, Bangladesh University of textiles, Dhaka, Bangladesh
Correspondence to: Tipu Sultan, Department of Textile Engineering, Southeast University, Dhaka, Bangladesh.
Email: |  |
Copyright © 2017 Scientific & Academic Publishing. All Rights Reserved.
This work is licensed under the Creative Commons Attribution International License (CC BY).
http://creativecommons.org/licenses/by/4.0/

Abstract
Carding is the heart of the whole spinning process, which causes convert the reeds of jute into a uniform supply of fibrous material which can then be drafted with a little more fiber breakage and provides further opportunity for removal of non-fibrous matter. This action occurs in jute breaker card and finisher card machine between cylinder and worker. Carding ratio is the ratio of surface speed of cylinder and worker. This study has carried out to find a speed range of cylinder and worker to get a suitable carding ratio of finisher card which is appropriate to have best processing performance and sliver quality. 21 lb/100 yards sliver have produce from the 100% Tossa jute at five different carding ratio of finisher card by changing the speed of worker and cylinder. Fiber individualization, parallization, strength, elongation%, tensile modulus, short fiber% and CV% of finisher card sliver have tested. Higher carding ratio ruptures longer fiber and generates additional short fiber, reduce fiber tenacity. In contrary higher carding ratio make the fiber more individual, parallel and thus improve sliver uniformity.
Keywords:
Sliver, Finisher card, Carding ratio, Tensile properties, Fiber
Cite this paper: Tipu Sultan, Hosne Ara Begum, Effect of Carding Ratio of Jute Finisher Card on Processing Performance and Sliver Quality, International Journal of Textile Science, Vol. 6 No. 4, 2017, pp. 99-104. doi: 10.5923/j.textile.20170604.01.
1. Introduction
Chemically, jute has three main constituents: (1) cellulose; (2) hemi cellulose; (3) lignin. Small amounts of nitrogenous and inorganic material are present as well as variable amounts of water. The cellulose, hemi cellulose, and lignin all exist in the form of long chain molecules, as indeed do all the principal chemical compounds in textile fibers. Now we have to process jute at both chemically and mechanically with right speed range of finisher card cylinder and worker to get suitable carding ratio. [2] The heart of the carding machine is a large cylinder and covered with small pins set at an angle to its surface. Arranged round the periphery of this main cylinder are complementary pairs of smaller rollers with pins, these rollers being known as the workers and strippers. [3]The pins of the worker are set to work against those of the main cylinder whereas the stripper pins are set in the same direction as the cylinder pins. Carding action takes place between the worker and cylinder. Carding ratio is the ratio of surface speed between cylinder and worker. Carding action enhance when carding ratio increase. As the cylinder, workers, and strippers rotate, their pins split and open the jute which is passing between them. On a breaker card there are usually only two pairs of workers and strippers but finisher cards commonly are made with four or five pairs. [2]Two main functions, which take place in carding, are (a) carding action and (b) stripping action. These two main functions are dependent for their surface speeds and activates upon the method of pinning number of pins per square inch, the manner in which the two active surfaces are placed in relation to each other. So this experiment will carry out the impact of carding action and ratio on jute sliver processing performance and quality. [2]As jute is feed in the carding machine, the pins of faster moving cylinder split-up and vigorously comb away the ribbon of fibers so that it is fleeced-out and carried on the cylinder. Pins of the cylinder are set at such an angle so that the material is being combed. This combing action plays a vital role for uniform carded sliver i.e. good quality yarn. But excessive speed of cylinder effects damages of fibers. So this study may carry out to find a suitable cylinder and worker speed for a suitable carding ratio which involves optimum combing action and parallelization of individual fiber to spin jute yarn. [2]The essential feature of the carding operation at the workers and strippers is one of combing, teasing, and splitting as the fibre is transferred first from the cylinder to the worker, then from the worker to the stripper and finally from the stripper back on to the cylinder. As the pins of the stripper point in the same direction as those on the cylinder the bulk of the jute descending on the cylinder passes between the cylinder and the stripper though there is a certain amount of build-up where the two rollers meet. The jute then comes in contact with the backward-facing pins of the worker and as the surface speed of this roller is very low compared with that of the cylinder the fibers are arrested by the worker pins. Those fibbers which are firmly held by the cylinder pins pass underneath the worker and continue until they meet the next worker/stripper pair, but the remainders are pulled away from the cylinder pins by the worker pins. [2]The fibbers do not lie as a uniform fleece on the pins of the worker, some being held by the pins but the greater majority resting quite lightly on the top of the pins. It will be appreciated that inside the shrouding of the card air currents and eddies are set up by the rapidly rotating cylinder; these tend to blow the fibbers into a fleecy conglomeration on the workers and strippers. This fibre mass continues round the worker until it comes under the influence of the stripper where the pins, by virtue of their direction and greater surface speed, lift the upper layers of the fibre mass off the worker pins, splitting and opening it as they do so. The more firmly held fibers pass round the workers again until they meet the faster moving cylinder pins and the cycle is repeated. Once the bulk of the fibre has been transferred from the worker to the stripper it continues round on the stripper until it meets the cylinder where it is removed from the stripper by the cylinder pins working back-to-back with the stripper pins. In this way the fibre networks are gradually split into a fibrous mass. [2]
2. Methodology
2.1. Material
Bangla Tossa-B (BT-B) jute fibre has selected as raw material for this experiment. It is light to medium grey in color, good texture, average luster, and clean cut and well hackled. 100 pieces of Jute morah having weight 150 lb has processed.Table 1. Specification of Spreader machine 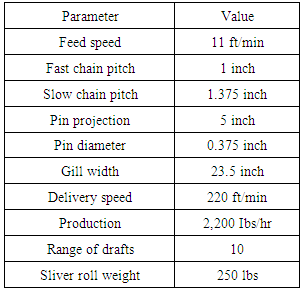 |
| |
|
2.2. Method
Fiber has been processed at jute softener machine with the application of 20% normal emulsion (i.e. 20% JBO as mineral oil, 78.5% water and 1.5% Nekanil as emulsifier) and kept for 48 hours for maturation. Breaker card jute sliver of 21 lbs/100 yards have processed through finisher card machine at five carding ratio eg. 33.7, 40.74, 44, 47.82 and 50 by changing surface speeds of Cylinder and worker. Doubling at all the stages of finisher card machine has been 11:1. Table 2. Specification of Breaker card machine 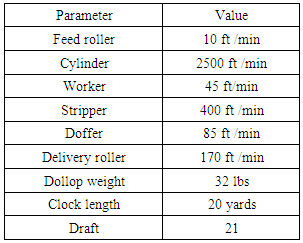 |
| |
|
Table 3. Carding ratio for different speed of Worker and Cylinder 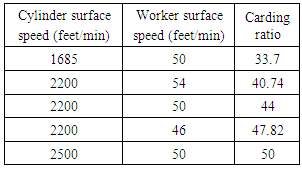 |
| |
|
Table 4. Specification of Finisher card machine 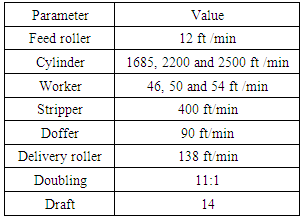 |
| |
|
2.3. Experimental Testing Procedure
2.3.1. Fiber Length
Fibers were separated from specific length sliver and placed according to length of fiber to make a sorter diagram. Percentage of different length jute fiber has measured by weighting for each of those carding ratio.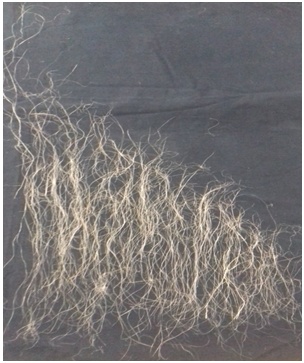 | Figure 1. Fibers of finisher card sliver in decreasing order of length |
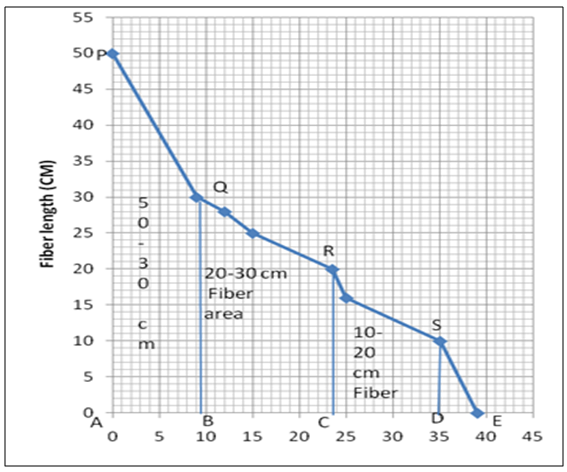 | Figure 2. Fiber length of finisher card sliver (carding ratio 33.7) |
2.3.2. Fiber Strength
The bundle strength and elongation of jute fiber of finisher card sliver have tested from 20 samples for each of carding ratio at Stelometer as per standard ISO 3060.
2.3.3. Fiber Elongation
If E is the true elongation, E0 the elongation at zero gauge length, and E1 the elongation at inch gauge length. ThenE= E1-E0
2.3.4. Fiber Parallization and Individualization
A bundle of fibers from finisher card sliver has collected by random sampling procedure. Then individual fibers were checked visually in several places.
2.3.5. Sliver Weight
5 yards Finisher card sliver have taken for 20 times randomly for each of the different carding ratio, have weighted. Then CV% of the sliver weight was calculated.
3. Result & discussion
3.1. Effect of Carding Ratio on Jute Fiber Length
Percentage of different length jute fiber has measured by weighting for each of those carding ratio and the result has placed on table no. 5.Table 5. Percentage of jute fiber at different carding ratio 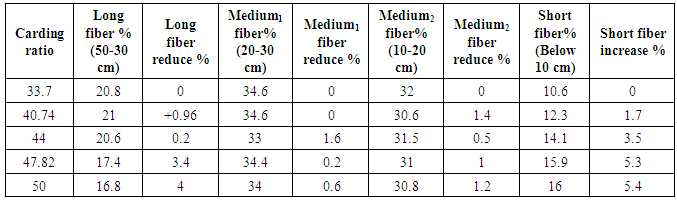 |
| |
|
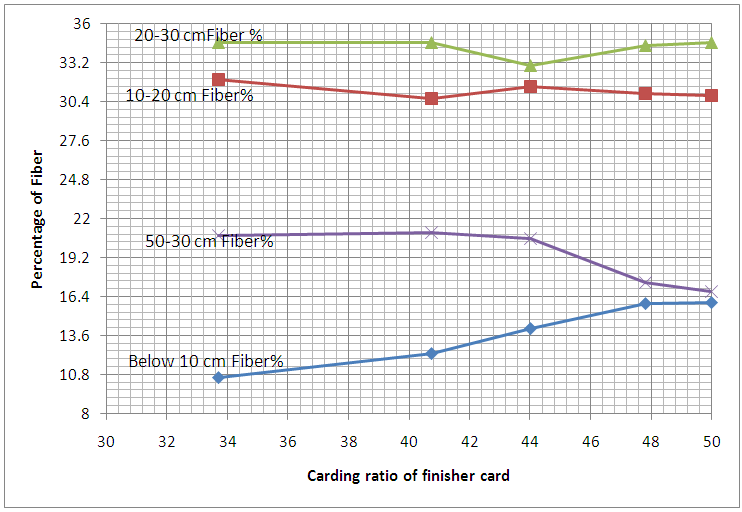 | Figure 3. Percentage of jute fiber at different carding ratio |
At figure no. 3 it can be said that when increase carding ratio from 33.7 to 44 longer (50-30 cm) jute fiber reduced 0.2%. For further increased of carding ratio from 33.7 to 50 this longer fiber reduced 4% which is about 20 times higher than previous one.When carding ratio increased from 33.7 to 50, then medium1 and medium2 length jute fiber reduce 0.6 and 1.2% respectively. So it can be said that increasing carding ratio have not any significant effect on these length fiber.It can also be said from figure no. 4.3 that when increase carding ratio from 33.7 to 44 short (below 10 cm) jute fiber increased 3.5%. For further increased of carding ratio from 33.7 to 50 this short fiber increased 5.4%.It may be said that higher carding ratio causes in longitudinal splitting, opening and breaking of the jute reed of mesh structure into individual fiber without entanglement. This ultimately reduces percentage of longer fiber and increase percentage of short fiber. Basically much more increase in carding ratio will significantly increase fiber rupture, which in turn greatly decreases longer fiber content.
3.2. Effect of Carding Ratio on Tensile Properties of Fiber
From figure 4 it can be said that when carding ratio increased from 33.7 to 44 then fiber strength reduce about 14.51%. For further increasing of carding ratio from 33.7 to 50, fiber strength decrease about 23.88%. Therefore it can be said that with increase carding ratio up to 44 strength decrease gradually and after this phenomenon strength reduce rapidly. It may be due to longer fiber breakage take place rapidly after carding ratio 44.Table 6. Tensile properties of jute fiber at different carding ratio 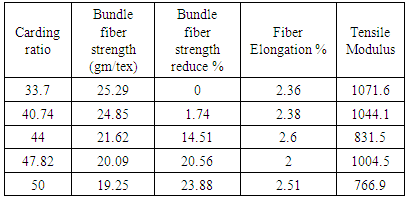 |
| |
|
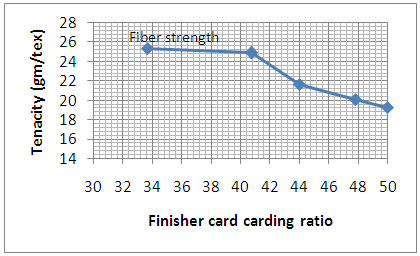 | Figure 4. Tenacity of jute fiber at different carding ratio |
3.3. Effect of Carding Ratio on Jute Fiber Parallelization
Jute fiber orientation at finisher sliver for different carding ratio was observed carefully and remarks on fiber parallelization at table no.7.Table 7. Fiber parallelization at different carding ratio 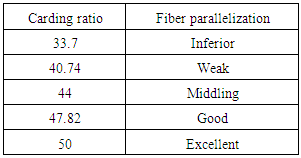 |
| |
|
From Table 7 it can be said that fiber parallelization in finisher sliver improve with the increase in carding ratio. Since the carding action increase with the increase of cylinder speed and thus improve individualization of jute fiber at carded sliver. With better opening, the distribution of fibers over the cylinder surface is fine as fibers are more individual, thereby improving the individualization and parallelization of fiber.
3.4. Effect of Carding Ratio on Sliver Irregularities
Average CV% of jute finisher card slivers (lb/100 yards) for different carding ratio are placed on following table no.8.Table 8. Jute sliver and yarn CV% at different carding ratio 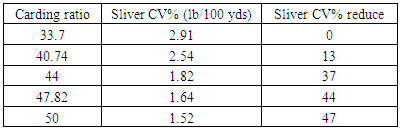 |
| |
|
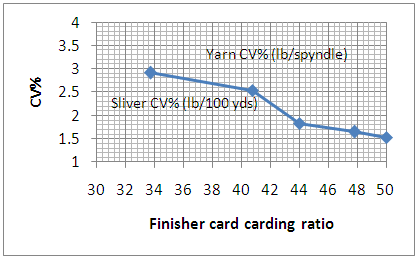 | Figure 5. Sliver CV% at different carding ratio |
From figure 5 it can be said that when carding ratio increased from 33.7 to 44 then sliver CV% reduce 1.09%. For further increasing of carding ratio from 33.7 to 50, sliver CV% decrease 1.39%. Therefore it can be said that with increase carding ratio up to 44 sliver CV% decrease rapidly and after this phenomenon there is no significant reduction of sliver CV%. It may be due to longer fiber breakage take place rapidly after carding ratio 44 which ultimately effect on increase short content and irregularities of the sliver.
3.5. Effect of Carding Ratio on Jute Processing Performance
Processing performance of jute fiber individualization was estimate at different carding ratio.
3.5.1. Effect of Carding Ratio on Fiber Individualization
Fibers individualization of finisher sliver for different carding ratio was observed carefully and remarks on fiber individualization at table no.9.Table 9. Fiber individualization of sliver at different carding ratio 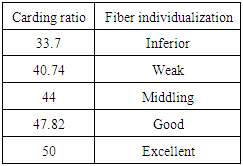 |
| |
|
From table 9 it is found that when carding ratio increase then more individualization of fiber can be achieved. The carding action involves the transfer of jute fibers from the cylinder surface to worker surface and vice versa. During the multiple transfer, the wire point in the cylinder try to retain the fibers, and at the same time wire point of the worker try to pluck the fiber. But, most of the fibers are retained at the cylinder wire point, as the worker rotate at much slower speed than the main cylinder and the result leads to split-up the jute fiber mesh structure and finally individualization of fiber. With better opening, the distribution of fibers over the cylinder is good when carding ratio more, thereby improving the individualization of fiber.
4. Conclusions
It is seen that higher carding ratio reduce percentage of longer fiber and thus fiber strength. In contrary higher carding ratio improve jute sliver quality by reduce CV%. It also improves fiber parallelization and individualization in finisher card sliver.
References
[1] | Ahmed, H, 1979. Jute spinning. 2nd Edition, Begum Fatima Ahmed(Ed), Tejgaon, Dacca publication, pp: 10-60. |
[2] | Atkinson, R.R., 1964. Jute fiber to yarn. 1st edition, Heywood Books, London, pp: 61-100. |
[3] | Mahabubuzzaman AKM, Kabir MK, Latifa BL (2002) Study of the effect of Speed Variation at Breaker Card Cylinder on Fibre length and Yarn Quality. Asian journal of Plant Sciences, 6(1), 648-649. |
[4] | Ranjan, T.C, 1985. Hand book on jute. 2nd edition, New Delhi, Oxford and IBH publication Co. PP: 118-127. |