Jamal Haider Hasib1, Md. Mostafizur Rahman2, Shohel Ahmed2, Md. Azharul Hossain2, Shamim Al Azad2, Mainuzzaman2
1School of Textile science and Engineering, Wuhan Textile University, Wuhan, China
2Department of Textile Engineering, Southeast University, Dhaka, Bangladesh
Correspondence to: Jamal Haider Hasib, School of Textile science and Engineering, Wuhan Textile University, Wuhan, China.
Email: |  |
Copyright © 2017 Scientific & Academic Publishing. All Rights Reserved.
This work is licensed under the Creative Commons Attribution International License (CC BY).
http://creativecommons.org/licenses/by/4.0/

Abstract
This research deals with the effect of color difference and other color parameters after dyeing of jute yarn with reactive dyes, acid dyes, basic dyes and direct dyes. Different tests were done in order to carry out a comparison between conventionally bleached batch and non-bleached jute yarn. Here, reactive dyes, acid dyes, basic dyes and direct dyes were applied to jute yarn for achieving good color fastness property to rubbing and washing. Color fastness property to rubbing and washing of jute yarn dyed with basic, direct, acid and reactive dyes were evaluated and compared.
Keywords:
Jute yarn, Reactive dye, Direct dye, Acid dye, Basic dye, Color fastness
Cite this paper: Jamal Haider Hasib, Md. Mostafizur Rahman, Shohel Ahmed, Md. Azharul Hossain, Shamim Al Azad, Mainuzzaman, Consequences and Evolution of Dissimilar Parameters Occurred Due to the Implementation of Different Dyes and Optimization of the Fastness Properties with Qualitative Assessment of Jute Yarn, International Journal of Textile Science, Vol. 6 No. 3, 2017, pp. 92-98. doi: 10.5923/j.textile.20170603.03.
1. Introduction
Jute, a vegetable fiber that can be spun into sackcloth, used to be the “golden fiber” of Bangladesh [1]. It brought much need foreign income to the impoverished nation. But it lost its luster in the 1986 after synthetic materials like polythene & plastics were introduced. Now the material fiber has made a spectacular come back. Diversified jute products are becoming more & more valuable to the customer today. Among these are espadrilles, soft sweeter & cardigans, floor covering, home textiles, high performance technical textiles, geo textiles & more. Jute is mostly dyed with basic dye because it has material affinity to this dye. As a Cellulosic fiber, jute may have to well respond to Reactive dye [2]. The reactive dyes offer a wide range of dyes with varying shades, fastness, and costs with high brilliancy, easy applicability and reproducibility. In case of dyeing of jute with reactive dyes, anionic dyes react with hydroxyl groups of the fiber by either substitution or addition reactions. Many studies have been devoted to improve the substantively of cellulosic fiber for reactive dyes. A few efforts were made to improve the light fastness of jute yarn [3]. So we are going to make a comparative study of fastness properties of dyed jute yarn with Acid, Direct, and Basic & Reactive dye with same shade (1.5 %). Although, as with most of the other vegetable fibers, cellulose forms the main structural component of jute, the noncellulosic components (e.g., lignin and hemicellulose) also play an important part in the characteristic properties of the fibers. Jute is a cellulosic fiber. Its repeating unit is also cellulosic. Jute is composed of 65% cellulose and 35% natural wages, oils and cements (lignin) [4]. Acid dyes normally used for protein fiber and polyamide fiber. Most pre-metallized and mordant dyes are acid dyes. The acids used in the dyebath range from sulphuric acid (dyebath pH < 2.0) to ammonium acetate (dyebath pH > 6.5). Acid dyes are usually sodium salts of sulphonic acids, or less frequently of carboxylic acids, and are therefore anionic in aqueous solution. They will dye fibres with cationic sites [5]. Dyeing involves exchange of the anion associated with an ammonium ion in the fibre with a dye anion in the bath.Fibre + H (aq) + HSO4 (aq) Fibre NH3HSO4 (s)Fibre NH3 DyeFibre NH3HSO4 (s) SO3 (aq) Dye+ SO3 (s) + HSO4 (aq)Acid dyes have molecular weights in the range 300–1000 g mol–1 [6]. Such dyes have slower diffusion in the fibre and therefore less ability to migrate and dye level. The more hydrophobic, high molecular weight dyes therefore have better fastness to wet processes. 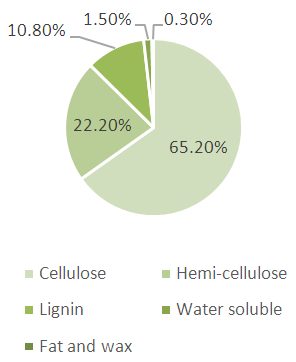 | Figure 1. Chemical Composition of Jute fiber |
Table 1. Physical properties of Jute fiber 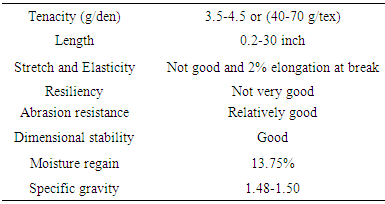 |
| |
|
The idea of immobilizing a dye molecule by covalent bond formation with reactive groups in a fibre originated in the early 1900s. Various chemicals were found that reacted with the hydroxyl groups of cellulose and eventually converted into colored cellulose derivatives [7]. In 1955, Rattee and Stephen, working for ICI in England, developed a procedure for dyeing cotton with fibre-reactive dyes containing dichlorotriazine groups. Dyeing cotton with these dyes under mild alkaline conditions resulted in a reactive chlorine atom on the triazine ring being substituted by an oxygen atom from a cellulose hydroxyl group. This is shown below where Cell–OH is the cellulose with a reactive hydroxyl group, Dye–Cl is the dye with its reactive chlorine atom, and Cell–O–Dye the dye linked to the cellulose by a covalent bond. The role of the alkali is to cause acidic dissociation of some of the hydroxyl groups in the cellulose, and it is the cellulosate ion (Cell–O–) that reacts with the dye [8].
The dyeing had very good fastness to washing. The only way the fixed dye can bleed from the cotton is after hydrolysis of the covalent bond between the dye and the cellulose. The direct dyes, also known as the substantive colours, differ from the basic and acid dyes because cellulosic fibres have a strong affinity for them. Many of them will also dye the protein fibres. Majority is sulphonated azo compounds very similar to the acid dyes in constitution.The first direct dye discovery was quickly followed by the preparation of many similar colours, opening a new era in dyeing. The direct dyes were inexpensive and easy to apply and, although of indifferent wet-fastness, their use spread with great rapidity because they fulfilled an outstanding demand [9]. New members with improved fastness are still being added to this class. A detailed study by the Society of Dyers and Colorists’ Committee on the dyeing Properties of Direct Cotton Dyes it was concluded that determination of four parameters was necessary, i.e., migration (or leveling power), salt controllability and the influence of temperature and of liquor ratio on exhaustion [10]. Tests are prescribed for migration and salt controllability whilst a statement covers the influence of temperature and liquor ratio, no tests being prescribed. The aforementioned SDC committee recommended that direct dyes be classified as follows. Class A Dyes, which are self-levelling, i.e. dyes of good migration or leveling properties. Class B Dyes, which are not self-levelling, but which can be controlled by addition of salt to give level results; they are described as salt controllable. Class C Dyes, which are not self-levelling and which are highly sensitive to salt; the exhaustion of these dyes cannot adequately be controlled by addition of salt alone and they require additional control by temperature; they are described as temperature controllable. The first basic dye, mauve, was synthesized by Perkins in 1856; and shortly afterward fuchsine, methyl violet, aniline blue, and other classical basic dyes were developed. Cationic dyes are currently used in large quantities to dye acrylics (Orlon, Acrilan, Creslan, Zefran) and modified acrylics (Verel) [11]. Basic dyes are water-soluble and dissociate into anions and colored cations. The cations have a strong affinity for the acidic group (sulfonic or carboxylic) and form salts. Because of these strong bonds, wash fastness is usually outstanding, and light fastness varies considerably, depending on the dyestuff. Basic dyes are usually applied in a batch process with skein, stock, and package dyeing more prevalent than piece dyeing on becks or jet machines [12]. Absorption of the basic dyestuff at the fiber surface, which occurs only when the glass transition point of the fiber is exceeded; diffusion of the dye into the fiber as the fiber molecules acquire enough energy to move; formation of the dye-fiber bond; and migration of dyestuff from the dye site to another or from within the fiber to the surface [13]. The degree of migration varies considerably, depending on the dyestuff, but generally basic dyes do not migrate well.
2. Materials and Methods
Yarn: 200 gm jute yarn was collected from local market in Dhaka, Bangladesh 100 gm yarn was bleached with H2O2 and 100 gm was remain non Bleached. This yarn has been used in the present work. Dyes, Chemicals and AuxiliariesFour dyes were used. They were reactive dye, direct dye, acid dye, basic dye. Two auxiliaries were used. Trade name of the chemicals are Pearlavin NDA (Multy functional wetting agent) , Parlavin SRS( soaping agent), Supplier- DR. Petty and Ladiquest (sequestering agent) supplier –Archroma and per oxide killer named T-100. The origin of the chemicals are Germany. Laboratory regent grade sodium carbonate (Na2Co3), sodium chloride (NaCl).
3. Methods
In this research, it was tried to make a comparison between two different pre-treated batches (Bleached and non-Bleached). COPOWER dyeing machine was used for the dyeing process. Here same recipes are shown for bleached and non-bleached jute yarn.The whole process was carried out in two steps. First 200gm jute yarn was collected from the local market and then 100 gm jute yarn was taken for the bleaching process. Jute yarn was bleached with hydrogen peroxide and then neutralized with the help of acetic acid. It is mandatory for cellulosic fiber to kill the peroxide from the fiber after the bleaching process that’s why we used T-100 per oxide killer to kill the peroxide from the yarn. 5gm sample was measured and then taken for the farther dyeing procedure. Yarn was then died with different dyes and then neutralization was done by the help of acetic acid or soda ash as required dependent on the medium of the dye bath.After the finishing of dyeing fixation was carried out by the help of the fixing agent and then the sample was washed well and dried.Same procedure has been followed for the other 100gm of yarn but only the bleaching part was escaped. For this portion of yarn the yarn was measured in 5gm and then washing was carried out and directly subjected to the dyeing. After that the same procedure was followed as described in above. Scouring and bleaching of jute yarnFollowing recipe and techniques were followed to perform the bleaching process of the jute yarn. Detergent: 1gm/lt; NaOH: 1gm/lt; H2O2: 5gm/lt; Soda ash (Na2CO3): 5gm/lt; Wetting agent: 1gm/lt; Sequestering agent: 1 gm/lt; Time: 30 min; Temp: 90° C; pH: 10.5; M:L: 1:10.In this project 100 gm jute was taken. At first the dyeing machine was filled with water and then the sample was feed into the machine, at this stage detergent and auxiliaries with stabilizer has been added for 10 minutes at room temperature. After that caustic was added at forty degree Celsius. At this stage the temperature has been raised up about seventy degree Celsius. After the addition of caustic, peroxide was added to the bath at ninety degree Celsius, after the peroxide dosing the bath was continued for next 30 min and then the bath is drained and washed. Then the yarn was treated with per oxide killing agent. This process taken out at 50 degree Celsius for 10 minutes. After the peroxide killing process the sample was washed well and drained. Dyeing of jute yarn with Reactive dyeDyeing of jute yarn with reactive dyes was performed by using the following recipe and techniques. Reactive dye (Remazol): 1.5%; Glubar Salt: 60gm/lt; Soda: 15gm/lt; NDA: 1 gm/lt; M.F (Ladiquest): 1gm/lt; PH: 10.5; Time: 60 min; Temp: 60° C; M:L: 1:10; Sample weight: 5 gm; Total liquor: 50 ml.At first 5 gm sample was taken and loaded into the dyeing vessel. And then water was filled into the vessel as an M:L ratio of 1:10 and then salt, soda, dyes and all auxiliaries were added at room temperature. Temperature is raised at 60 degree Celsius and dyeing was continued for next 60 min. then the dye bath had been released and rinsing was done for 10 min. As we know during the time of dyeing with reactive dyes need a basic medium of pH level 11.5 to 14, so we need to neutralize the bath using acetic acid and bring the pH within 6 to 7. After the neutralization process the sample was soaped well to enhance the wash fastness.Dyeing of jute fiber with direct dyeDyeing of jute yarn with direct dyes was performed by using the following recipe and techniques. Direct dye: 1.5%; Glubar Salt: 20gm/lt; Soda: 3gm/lt; NDA: 1 gm/lt; Ladyque: 1 gm/lt; Fixing Agent: 1 gm/lt; Time: 45 min; Temp: 90°C; M: L: 1:10; Sample weight: 5 gm; Total liquor: 50 ml.At first 5 gm sample was taken and loaded into the dye bath. And then water was filled into the bath as an M: L ratio of 1:10 and then salt, soda, dyes and all auxiliaries were added at room temperature. Temperature was raised at 90 degree Celsius and dyeing was continued for next 45 min. Salt was added step by step according to the dye bath concentration after 15-20 min. For achieving higher depth of shade more salt concentration was required. After gaining the expected temperature salt was added to achieve more penetration all over the yarn. Then the dye bath had been released and rinsing was done for 10 min. After neutralization and fixation was done and the sample was washed out and dried.Dyeing of jute fiber with basic dye Dyeing of jute yarn with direct dyes was performed by using the following recipe and techniques.Basic dye: 1.5%; Glubar Salt: 20 gm/lt; Acitic Acid: 1 gm/lt; NDA: 1 gm/lt; Ladyquest: 1 gm/lt; Time: 45 min; Temp: 90° C; M:L: 1:10; Sample weight: 5 gm; Total liquor: 50 ml.5 gm sample was taken and loaded into the dyeing vessel. And then water was filled into the vessel as a M:L ratio of 1:10 and then salt, acetic acid, dyes and all auxiliaries were added at room temperature. Temperature is raised at 90 degree Celsius and dyeing was continued for next 45 min. then the dye bath had been released and rinsing was done for 10 min.Dyeing of jute fiber with acid dye Dyeing of jute yarn with Acid dyes was performed by using the following recipe and techniques.Acid dye: 1.5%; Glubar Salt: 20 gm/lt; Acitic Acid: 1 gm/lt; NDA: 1 gm/lt; M.F (Ladiquest):1 gm/lt; PH: 4.5; Time: 45 min; Temp: 90°C; M:L :1:10; Sample weight: 5 gm; Total liquor: 50 ml.5 gm sample was taken and loaded into the dyeing vessel. And then water was filled into the vessel as a M:L ratio of 1:10 and then salt, acetic acid, dyes and all auxiliaries were added at room temperature. Temperature is raised at 90 degree Celsius and dyeing was continued for next 45 min. then the dye bath had been released and rinsing was done for 10 min.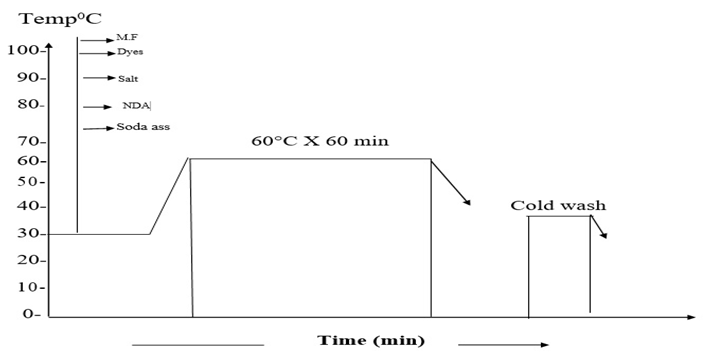 | Figure 2. Dyeing curve for reactive dyes |
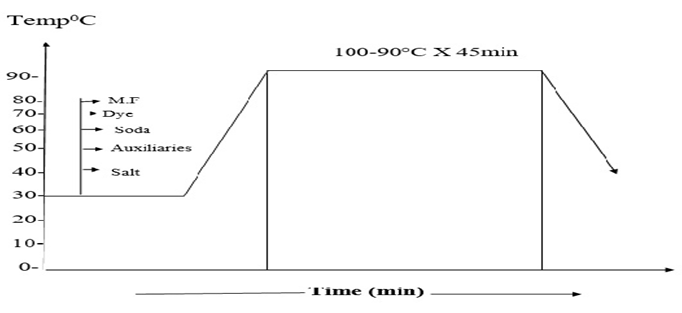 | Figure 3. Dyeing curve for direct dyes |
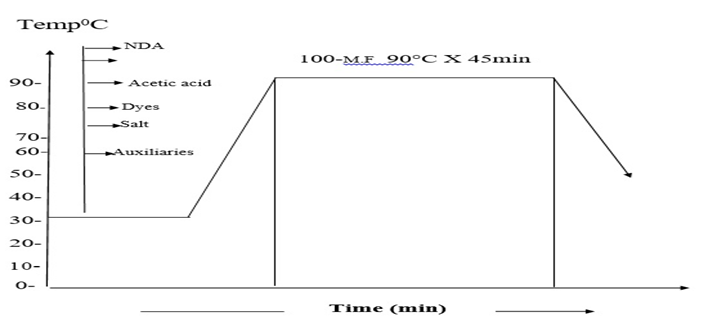 | Figure 4. Dyeing curve for basic dyes |
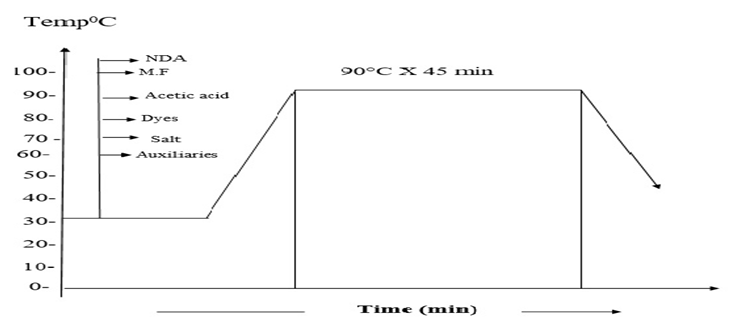 | Figure 5. Dyeing curve for acid dyes |
Testing and Analysis of samplesThe weight of the gray jute yarn were measured using electric balance of 100 gm. Then weight of the after bleaches jute yarn were measured using electric balance of same batches. After then comparison between two batches and measured the weight loss of the jute yarn.Absorbency of the sample was tested by drop test method. A drop of water was fallen on the Bleached and non-bleached jute yarn with a pipette and time in second is measured unit the water drop is absorbed. Sample length 5cm. Observation was if the fabric immersed within 5sec or not.Color Fastness to wash was measured by using test Method: ISO 105-C06 where we the M/C was used name: Gyrowash.Colorfastness to rubbing was measured by using Test Method: ISO 105 X 12 where the M/C was used named: James Heal UK Crockmaster.Color Difference was measured in D65 light, where “Data color D650” M/C was used. At bleached dyed jute yarn was taken as standard and non-bleached dyed jute yarn as batch. Then the standard value in the spectrophotometer was inserted (Data color D650). After that the batch with the standard value was compared and find out the color difference for each color.
4. Result and Discussion
Measurement of weight loss and absorbency after bleachingThe weight of non-bleached jute yarn was 100 gm, after bleaches it found 93.33 gm. So, the weight loss (%) is 6.67%. Jute as cellulosic fiber lose its weight due to Bleaching. A drop of water was fall on bleached and non-bleached jute yarn with a pipette and time was measured that has been taken by the sample to absorb the water. Sample length was 5cm. Bleached jute yarns are absorbed water within 5 sec, but non-bleached jute yarn did not absorbed due to its surface tension.Color fastness to washTable 2. Color change result for bleached jute yarn 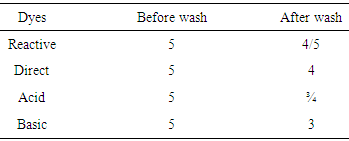 |
| |
|
Reactive dye and direct has good affinity to the cellulosic fiber. That’s why the result of wash fastness with reactive and direct dye to the jute yarn has well except acid and basic dye.Table 3. Color change result for non-bleached jute yarn 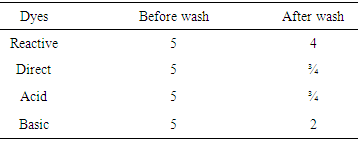 |
| |
|
Here all wash fastness result are comparatively well without basic dye. Color fastness to wash of Basic dye are poor in jute yarn because basic dye does not have good affinity to the cellulosic fiber or jute yarn. Table 4. Color fastness staining grade between reactive dyed bleached and non-bleached yarn  |
| |
|
Here it is seen that all staining values are good, except cotton fiber because Cellulosic fiber has good affinity to reactive dye.Table 5. Color fastness staining grade between direct dyed bleached and non-bleached yarn  |
| |
|
Direct dye have also good affinity to the cellulosic fiber, but its fastness property is not so good. Here, shows that all staining values are good except Acetate and cotton in both bleached and non-bleached dyed yarn.Table 6. Color fastness staining grade between acid dyed bleached and non-bleached yarn  |
| |
|
Acid dyes does not have good affinity to cellulosic fiber like jute. Here, it is seen that all staining values are poor in both bleached and non-bleached except polyester and acrylic in bleached dyed yarn.Table 7. Color fastness staining grade between basic dyed bleached and non-bleached yarn  |
| |
|
Basic dye also have not good affinity to the cellulosic fiber like jute fiber. Here, shows that all staining values are poor in both bleached and non-bleached except polyester and acrylic. Colorfastness to rubbingTable 8. Color fastness to rubbing between reactive dyed bleached and non-bleached yarn  |
| |
|
The dry rubbing values of both bleached and non-bleached is better than wet rubbing values.Table 9. Color fastness to rubbing between direct dyed bleached and non-bleached  |
| |
|
The dry and wet rubbing values of bleached yarn are good except wet rubbing values in non-bleached. Table 10. Color fastness to rubbing between acid dyed bleached and non-bleached  |
| |
|
Here, only dry rubbing values of acid dye are good but poor in wet rubbing both bleached and non-bleached. Table 11. Color fastness to rubbing between basic bleached and non-bleached  |
| |
|
Basic dye have good dry rubbing fastness in both bleached and non-bleached yarn but not so well in wet rubbing. Color differenceTable 12. Color change for reactive dyes  |
| |
|
The batch is darker, more green, more blue than standard and GS value = 2.49, GS rating = 2-3. Table 13. Color change for direct dye  |
| |
|
The batch is darker, more green, more yellow than standard and GS value = 3.36, GS rating = 3-4.Table 14. Color change acid dyes  |
| |
|
Batch is darker, more green, more yellow than standard and GS value = 4.06, GS rating = 4.Table 15. Color change basic dyes  |
| |
|
The batch is darker, more red, more blue than standard and GS value = 2.20, GS rating =2.
5. Conclusions
This research is related to different dyeing process of jute yarn and assessment of different quality parameters that is being done in textile industries. Here different test results, samples, methods, procedures etc. are included for reference. It was observed that incase of bleached jute yarn are lustrous than non-bleached jute yarn after the process of dyeing with different dyes. On the other hand, bleached jute yarn loses its weight after the bleaching process. It was seen here that in case of reactive and direct dyes color fastness to wash is better than acid and basic dyes. In case of color fastness to rubbing it was seen that direct dyes and basic dyes exhibits improved performance. It was also found that reactive dyes gives a higher metamarism index and basic dyes gives the lower metamarism index. Due to the presence of lignin in its composition, jute fiber is not suitable for human skin. Nowadays some textile industries are tried to produce garments that are made by the jute yarn.
References
[1] | Kochhar, S., Economic Botany. 2016: Cambridge University Press. |
[2] | Shukla, S. and R.S. Pai, Adsorption of Cu (II), Ni (II) and Zn (II) on modified jute fibres. Bioresource Technology, 2005. 96(13): p. 1430-1438. |
[3] | Rowell, R.M. and H.P. Stout, 7 Jute and Kenaf. 1998. |
[4] | Biagiotti, J., D. Puglia, and J.M. Kenny, A review on natural fibre-based composites-part I: structure, processing and properties of vegetable fibres. Journal of Natural Fibers, 2004. 1(2): p. 37-68. |
[5] | Hunger, K., Industrial dyes: chemistry, properties, applications. 2007: John Wiley & Sons. |
[6] | McKay, G., et al., Transport processes in the sorption of colored ions by peat particles. Journal of Colloid and Interface Science, 1981. 80(2): p. 323-339. |
[7] | Inman, J.K. and H.M. Dintzis, Derivatization of cross-linked polyacrylamide beads. Controlled introduction of functional groups for the preparation of special-purpose, biochemical adsorbents. Biochemistry, 1969. 8(10): p. 4074-4082. |
[8] | Aspland, J., Reactive dyes and their application. Textile Chemist and Colorist, 1992. 24(5): p. 31-36. |
[9] | El-Daly, H.A., A.-F.M. Habib, and M.A.B. El-Din, Kinetics and mechanism of the oxidative color removal from Durazol Blue 8 G with hydrogen peroxide. Dyes and pigments, 2003. 57(3): p. 197-210. |
[10] | Aspland, J.R., Textile dyeing and coloration. 1997: AATCC. |
[11] | Nelson, E.L., Method for improved dyeing. 1982, Google Patents. |
[12] | Perkins, W.S., A Review of Textile Dyeing Processes. Textile Chemist & Colorist, 1991. 23(8). |
[13] | Vigo, T.L., Textile processing and properties: Preparation, dyeing, finishing and performance. Vol. 11. 2013: Elsevier. |