Md. Mehedi Hashan1, K. M. Faridul Hasan1, Md. Fazle Rabbi Khandaker1, Krisna Ch. Karmaker2, Zhongmin Deng1, Masud Jamil Zilani3
1School of Textile Science and Engineering, Wuhan Textile University, Wuhan, China
2School of Textile Chemistry and Chemical Engineering, Wuhan Textile University, Wuhan, China
3School of Textile Science and Engineering, Mawlana Bhashani Science and Technology University, Tangail, Bangladesh
Correspondence to: Md. Mehedi Hashan, School of Textile Science and Engineering, Wuhan Textile University, Wuhan, China.
Email: |  |
Copyright © 2017 Scientific & Academic Publishing. All Rights Reserved.
This work is licensed under the Creative Commons Attribution International License (CC BY).
http://creativecommons.org/licenses/by/4.0/

Abstract
This paper presents a study on the comfort properties of socks manufactured by different types of yarns like cotton, viscose, bamboo, wool, acrylic and their blends. The air permeability, thermal conductivity, thermal resistance of plain socks and plated socks with polyester and lycra threads were investigated. It was found that the higher air permeability was shown in case of single yarn socks, lower air permeability for plated socks with polyester yarn and the lowest for plated with lycra threads. Polyester or lycra threads change the structure of plated knit socks as the constructions of such socks were thicker and tighter. It was determined that a higher thermal conductivity coefficient was occurred for single yarns, lower-for plated with polyester thread, lowest for plated with lycra thread. It was also determined that a higher thermal resistance was shown for plated socks with lycra thread, lower for plated with polyester and the lowest for single yarn socks.
Keywords:
Socks, Air Permeability, Thermal Conductivity, Thermal Resistance, Humidity
Cite this paper: Md. Mehedi Hashan, K. M. Faridul Hasan, Md. Fazle Rabbi Khandaker, Krisna Ch. Karmaker, Zhongmin Deng, Masud Jamil Zilani, Functional Properties Improvement of Socks Items Using Different Types of Yarn, International Journal of Textile Science, Vol. 6 No. 2, 2017, pp. 34-42. doi: 10.5923/j.textile.20170602.02.
1. Introduction
Socks under took a complementary of accessory duty in outer clothing as well as their property of protection from cold [1]. Socks are one of textile product having the least life among clothing goods since they can be produced with lower cost than other textile products and so much consumed and used according to fashion and needs during human life [2, 3]. A state of comfort can only be achieved when the most complex interactions between a range of psychological and physical factors have taken place in a satisfactory manner [4]. Hence, the comfort provided by clothing depends on such factors as softness, flexibility, moisture, diffusion, air permeability, thermal comfort, etc.There have been some researches on the thermal comfort of various fabrics. They all noted that the wickability, air permeability and heat transfer influence the thermal comfort of a garment. compared the thermal comfort of single jersey, 1×1 rib and interlock structures [5]. The general conclusion of these studies was that 1×1 rib and interlock fabrics, due to their high thermal insulation values, should be preferred for winter garments in order to protect from the cold. Comparing 1×1 rib and interlock fabrics, it would be better to use 1×1 rib fabrics for a warmer feeling on first contact. On the other hand, single jersey structures should be chosen for active sports or summer garments [3, 6]. However, there have no investigation on thermal comfort properties of plain or blended knits for socks from natural yarns and plated knitted socks with polyester and elastane (Lycra). The main goal of this work was to investigate the thermal comfort properties of socks, such as, air permeability, thermal conductivity coefficient and thermal resistance made from cotton, bamboo, wool, acrylic, viscose and their blends [7].Softness is a necessary property for consumers to feel more comfortable when they wear socks. Softening operation is made for softer touch. The operation of washing with silicon is one of these methods. When brighter appearance is desired in socks, mercerized threads are used. In socks made of synthetic fibers, antistatic finishing operations are applied [8]. This operation prevents trousers to adhere to socks and inhibits foreign substance accumulation on socks during use and washing. In long time wearing, heating and sweating occur in the feet remaining closed within shoes. 99% of sweat is water and it forms a perfect medium for bacteria to grow. These bacteria causes foot odor. Antibacterial substances used within the fiber decrease the formation of bacteria and consequently the odor [9].The measurement of the resistance to abrasion of textile and other materials is very complex. The resistance to abrasion is affected by many factors, such as the inherent mechanical properties of the fibers, dimensions of the fibers, structure of the yarns, construction of fabrics, and the type, kind, and amount of finishing material added to the fibers, yarns or fabric [10]. The measurement of resistance to abrasion is also greatly affected by the nature of the abradant, variable action of the abradant over the area of specimen abraded, the tension of the specimen, and the dimensional changes in the specimen [10, 11]. Found that the use of coarse yarns, addition of polyester, polyamide fibers or elastane filaments to the structure and application of the mercerization process increase the abrasion resistance of socks. However, the silicone softeners decrease this value. The resistance of wool socks is higher than acrylics.
2. Experimental
2.1. Material
There are ten types of yarns are used to knit sample socks. All the yarns were same count (30Ne) except lycra (40D) and polyester (150D). The yarns used in knitting socks are as follows- Pure Yarn: Wool (100%), Acrylic (100%), Cotton (100%), Viscose (100%), Polyester (100%), Lycra (100%) Blended Yarn: wool-acrylic (50% + 50%), cotton-acrylic (50% +50%), cotton-bamboo (50% + 50%), mélange (85% cotton + 15% viscose) [12].
2.2. Instruments
Matec - Tecno New socks knitting machine (14 gauge, 168 needle and 3¾” diameter), Sunsky socks dyeing machine from BYC Socks Limited, Dhaka.
2.3. Methods
2.3.1. Preparation of Sample
There are eight sample socks are knitted with same stitch length (6.2 mm). First four sample are knitted from single yarn and last four sample are knitted from single yarn plated with polyester and lycra (Table 1). Testing socks sample are perpetrated by the following way-Ø Sample 1: knitted from only pure wool yarn.Ø Sample 2: knitted from only pure acrylic yarn.Ø Sample 3: knitted from blended wool-acrylic yarn.Ø Sample 4: knitted from blended cotton-acrylic yarn.Ø Sample 5: made from cotton plated with polyester yarn. Sample 6: made from viscose plated with lycra yarn.Ø Sample 7: made from blended cotton-bamboo plated with polyester yarn.Ø Sample 8: made from mélange plated with polyester.Table 1. Variants of the plain knitted samples and their structural parameters 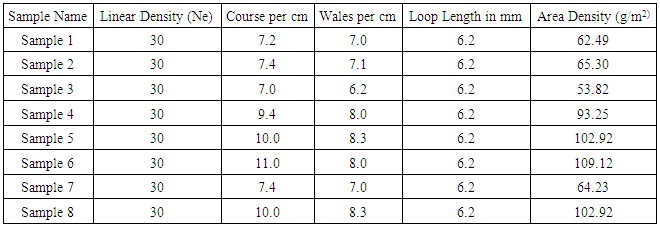 |
| |
|
2.3.2. Testing Methods
There are three testing methods are used to measure comfort ability of socks. They are given below -Ø Air permeability testØ Thermal conductivity testØ Thermal resistance test
2.3.2.1. Air Permeability Testing
Air permeability is defined as the volume of air in mm which is passed in one second through 100mm2 of the fabric at a pressure difference of 10 mm head of water.This test method covers the measurement of the air permeability--the rate of air flow passing perpendicularly through a known area under a prescribed air pressure differential between the two surfaces of a material--of textile fabrics [13].In this research air permeability tests of the knits investigated were conducted according to EN ISO 9237: 1997 [14]. The air permeability was measured using an L14DR air permeability tester (Karl Schroder KG, Germany) with a head area of 5 cm2. In order to get comparable results, coefficient 4 was multiplied with a specified area. The knitted samples were kept in a steam box for 20 minutes. Before investigation, the test knits were conditioned in standard conditions: relative humidity (65±2)%, temperature (20±2) °C. The air flow rate was measured over 20 tests per sample variant. The airflow rate determines the air permeability of test specimens, hence after the tests, the values of air permeability were calculated using equation [15]: | (1) |
where:R – air permeability in mm/s;qv – mean of airflow yield in dm3/min;A – specified area in cm2.The courses and wale density of the samples were calculated in the direction of the length and width of the knits at a 10 cm distance, and evaluated per cm. The area density of the samples was obtained from measurements of 10 × 10 cm samples, which is reported in g/m2. The yarn count was estimated before knitting. The stitch length l of a plain knitted sock was determined from the area density, which may be calculated using expression [15, 16]: | (2) |
where:l – Stitch length in mm;M – Area density of knitted sample in g/m2;A – Wales spacing of knitted sample in mm;B – Course spacing of knitted sample in mm;T – Linear density of yarns in teIt is known that the majority of knit features depend on the loop length and yarn linear density. The tightness of knits was characterized by the tightness factor (TF) [17]. It is know that TF is a ratio of the area covered by the yarns in one loop to the area occupied by the loop. It is also an indication of the relative looseness or tightness of the plain knitted weft structure. For determination of TF the following formula was used [17, 18]: | (3) |
where:T – the yarn linear density in tex;l – the loop length of knitted samples in cm.
2.3.2.2. Thermal Conductivity Testing
Thermal conductivity is the property of a material that relates to its ability to conduct heat.A measure of the ability of a material to transfer heat. In physics thermal conductivity is the amount of heat per unit time per unit area that can be conducted through a plate of unit thickness of a given material, the faces of the plate differing by one unit of temperature [18].Here,1 – Multilayer fabric,2 - Glass tube,3 - Distilled water,4 - Thermo insulation material,5, 6 – Incoming and outgoing water pipes, L - Width of sample,Lc - part of constant temperature of glass tube, ts - temperature of inner layer of glass tube,t0 - temperature of inner layer of fabric, t1 - temperature of first layer of fabric, t2 - temperature of middle layer of fabric, t3 - temperature of outer layer of fabric,A-A – cross-section of glass tube and three layers of samples: ds - diameter of inner layer of glass tube,d0 - diameter of inner layer of fabric, d1 - diameter of first layer of fabric,d2 - diameter of middle layer of fabric, d3 – diameter of outer layer of fabric.Thermal conductivity was determined with a measuring device described in. A basic scheme of this device is presented in Figure 1. The principal element of this device is glass tube 2, whose ends are insulated with a thermo-insulation material so that the temperature field created by the device would remain unaffected. Inside the glass tube distilled water of 40°C temperature flows. The temperature of the water is accurately maintained by an impulse thermostat. Sample 1 was wound on the glass tube in three layers [19]. Temperature measurements were then carried out with thermocouples, which were located in five places – on the inside and outside of the glass tube and between every layer of the sample i.e. at point’s ts, t0, t1, t2, t3. The thermocouples were located according to methodology of temperature measurement [7]. When the temperature became constant, measurement was registered. Temperatures were registered using an ALMEMO 2590-9 device with microprocessor data processing and accumulation systems. The resolving power of the device is 0.1°C. The variation coefficient of the temperature measurements did not exceed 3.68%. The thermal conductivity of the fabric (λ in W/mK) can be found using the following equation [12]: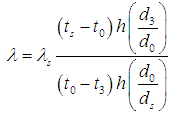 | (4) |
where:λs - thermal conductivity coefficient of the glass tube,ts - temperature of the inner layer of the glass tube in °C, t2 - temperature of the inner layer of the sample in °C,t1 - temperature of the first layer of the sample in °C,t2 - temperature of the middle layer of the sample in °C, t3 - temperature of the outer layer of the sample in °C, ds - diameter of the inner layer of the glass tube in m, d0 - diameter of the inner layer of the sample in m,d1 - diameter of the first layer of the sample in m, d2 - diameter of the middle layer of the sample in m, d3 - diameter of the outer layer of the sample in m.By using an indirect method of determining the thermal conductivity coefficient, it is possible to calculate the thermal conductivity coefficient of separate layers of multilayer fabric when the thermal, conductivity coefficient of the first layer λi = λs is known (determined by equation 1). In this case, the thermal conductivity coefficient of any layer of the fabric (λi) is found from the equation 2 [17]: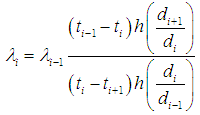 | (5) |
Where,I= 2……,n.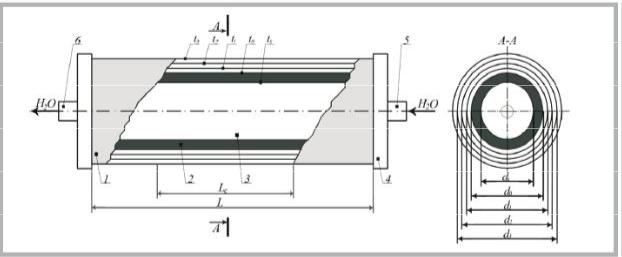 | Figure 1. Principle scheme of the temperature measurement device |
2.3.2.3. Thermal Resistance Testing
Thermal resistance is a heat property and a measurement of a temperature difference by which an object or material resists a heat flow (heat per time unit or thermal resistance). Thermal resistance is the reciprocal of thermal conductance. Thermal resistance R has the units (m2K)/W. Thermal conductivity coefficient measurements were repeated 6 times for randomly chosen parts of samples and thickness thereof, as in our previous work. Thermal resistance (R, m2 K/W) is calculated as a quotient of thickness and thermal conductivity parameters from the following: | (6) |
Where,b - thickness of the sample in m;λ - thermal conductivity coefficient of the sample in W/mK.
3. Results & Discussions
We investigated the main characteristics of the knits that have an impact on air permeability: the linear density of the yarns, area density, loop length, the tightness factor and raw material of the yarn s. Regarding air permeability, the range of values obtained is significant, ranging from 223-2460 mm/s. Obviously air permeability decreases if the area density increases due to the knit structure becoming thicker, a result of which being worse air flow. Air permeability of pure wool and acrylic respectively 2460 mm/s and 1786 mm/s. here air permeability of wool is higher than acrylic due to wool fibre structure is more floppy than acrylic. When wool and acrylic combined it found air permeability (1800 mm/s) which is higher than acrylic. Cotton-acrylic (1653) air permeability is lower than acrylic. Air permeability of cotton + bamboo + polyester is (293 mm/s), mélange + polyester (223 mm/s), viscose + lycra (226 mm/s), cotton (comb) + polyester (296 mm/s) and cotton + acrylic (1653 mm/s).
3.1. Experimental Results of Air Permeability
Table 2. Results of Air Permeability test of different samples 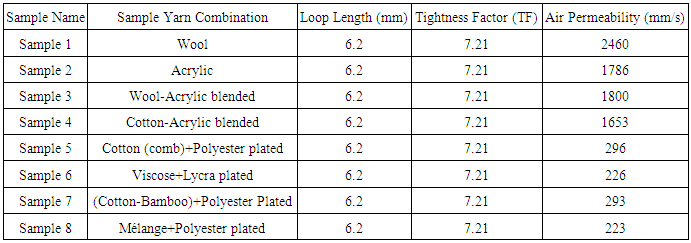 |
| |
|
3.2. Graphical Representation of Air Permeability Testing Results
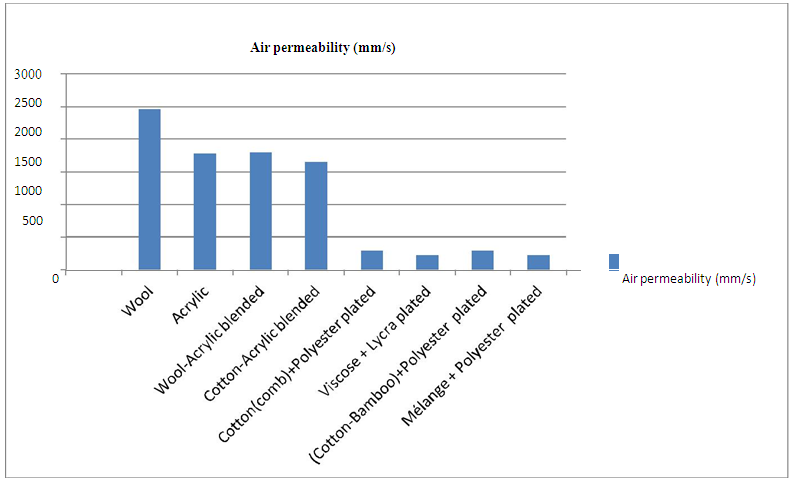 | Figure 2. Correlation between samples and air-permeability |
We investigated the main characteristics of the knits that have an impact on air permeability: the linear density of the yarns, area density, loop length, the tightness factor and raw material of the yarn s. Regarding air permeability, the range of values obtained is significant, ranging from 223-2460 mm/s. Obviously air permeability decreases if the area density increases due to the knit structure becoming thicker, a result of which being worse air flow. Air permeability of pure wool and acrylic respectively 2460 mm/s and 1786 mm/s. here air permeability of wool is higher than acrylic due to wool fibre structure is more floppy than acrylic. When wool and acrylic combined it found air permeability (1800 mm/s) which is higher than acrylic. Cotton-acrylic (1653) air permeability is lower than acrylic. Air permeability of cotton + bamboo + polyester is (293 mm/s), mélange + polyester (223 mm/s), viscose + lycra (226 mm/s), cotton (comb) + polyester (296 mm/s) and cotton + acrylic (1653 mm/s). It was found that higher air permeability is characterized for knit manufactured only from pure yarns and a lower permeability for knits with polyester and the lowest for knit with lycra thread. The air permeability of knits depends on linear density and raw materials composition. Polyester increases air permeability compared with lycra thread. By interchanging these stretch threads, we can control the area density, loop length and most importantly air permeability. Here mélange + polyester more prefer ability in winter season due to lower air permeability compared cotton (comb) + polyester. Similarly cotton-acrylic is more preferable then wool-acrylic in summer season due to more air permeability.
3.3. Experimental Results of Thermal Conductivity
In this work the thermal conductivity coefficient of socks manufactured from various yarns such as pure, blended and plated with Polyester or Lycra thread was investigated. Measurements were repeated 6 times at randomly chosen parts of the samples, the average values of which are presented in (Table 1) and Relative error values of the thermal conductivity coefficient were calculated and found to range from 1.8 – 13.2 %.Table 3. Results of thermal conductivity test of different samples 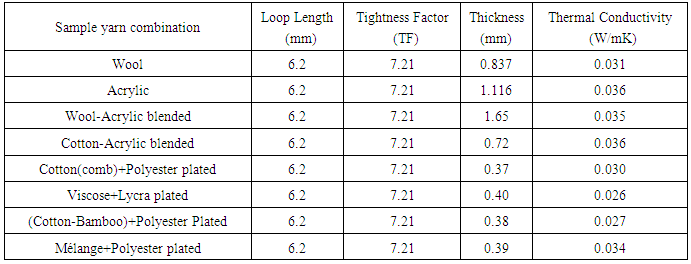 |
| |
|
3.4. Graphical Representation of Thermal Conductivity Testing Results
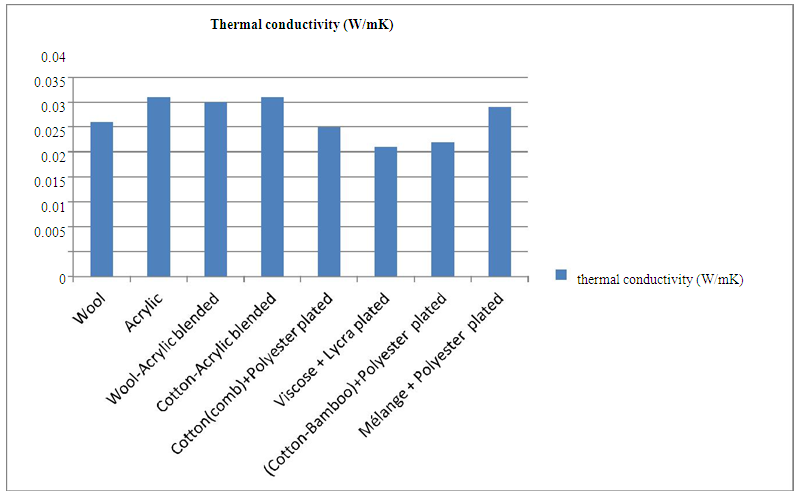 | Figure 3. Correlation between samples and thermal conductivity |
Regarding the thermal conductivity coefficient, the range of values obtained is significant, ranging from 0.026 to 0.036 W/mK. Here we see the result for knits from pure wool and acrylic’s thermal conductivity coefficient respectively 0.031W/mK and 0.036 W/mK due to more compact fibre structure of manmade fibre acrylic yarn, its thermal conductivity is more than wool. Blended wool-acrylic thermal conductivity is less than pure acrylic [19]. When polyester is plated with other yarn it produce higher thermal conductivity than plated with lycra. Cotton (comb) + polyester thermal conductivity (0.030) is higher than viscose + lycra thermal conductivity (0.026). (Cotton-Bamboo)+Polyester thermal conductivity lower than mélange polyester due to bamboo fibre has less thermal conductivity.
3.5. Experimental Results of Thermal Resistance
Table 4. Results of thermal resistance test of different samples 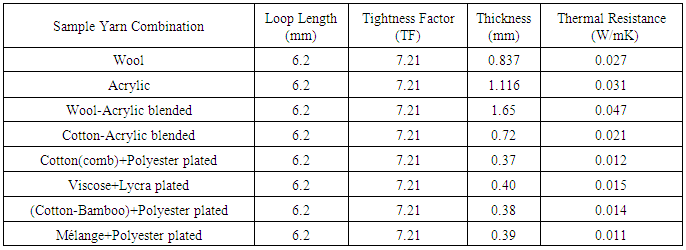 |
| |
|
3.6. Graphical Representation of Thermal Resistance Testing
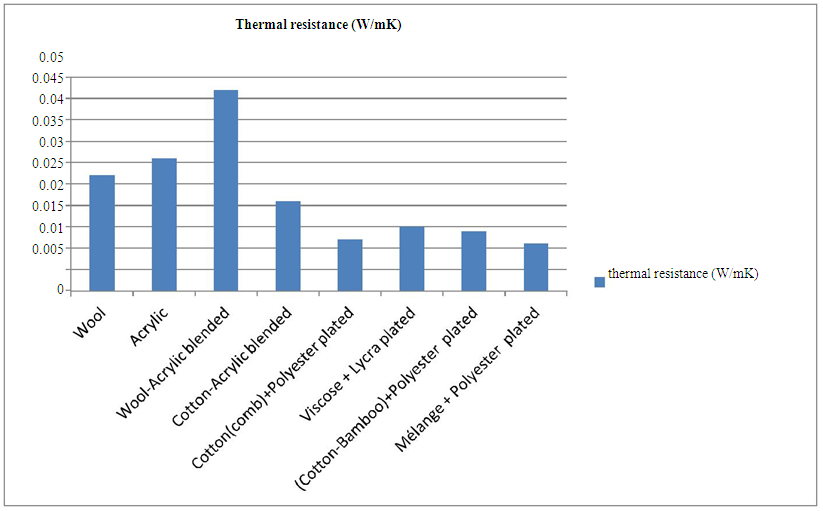 | Figure 4. Correlation between samples and thermal resistance |
The thermal resistance of socks manufactured from various yarns, such as pure, blended and a combination with polyester or elastane Lycra thread was analysed in this work.Regarding the thermal resistance coefficient, the range of values obtained is significant, ranging from 0.02 to 0.047 m2K/W. Here we see the result for knits from pure wool and acrylic’s thermal resistance coefficient respectively 0.027 m2K/W and 0.031 m2K/W. Thermal resistance values of wool-acrylic socks are higher than % 100 acrylic socks and give warm sense at first contact. When polyester is plated with other yarn it produce lower thermal resistance than plated with lycra. Cotton (comb) + polyester thermal resistance (0.0123) is iower than viscose + lycra thermal resistance (0.0154). (Cotton-Bamboo)+Polyester thermal resistance (0.0141) higher than cotton (comb) + polyester (0.0123) due to bamboo fibre has higher thermal resistance.
4. Conclusions
A “Warm – cool feeling” is a very important property, as a result of which a human can feel comfort or discomfort in various activities and environmental conditions. This feeling could be achieved by using different types of yarns. It was determined that higher air permeability is characterized for knits manufactured only from pure yarns, a lower air permeability for knits with polyester, and the lowest for knits with Lycra threads. The air permeability of knits depends on the linear density and raw material composition. Polyester increases air permeability compared with Lycra thread. By interchanging these stretch threads, we can control the area density, loop length and, most importantly, air per-meability. There was no correlation between the air permeability, tightness factor and loop length of knits manufactured from compositions with textured PA and Lycra threads. A weak correlation exists between the air permeability and tightness factor of knits manufactured from pure yarns. Cotton –acrylic fiber reduces the air permeability of the knits examined compared with knits manufactured from pure cotton yarns, where the linear density is the same. Regarding the thermal resistance coefficient, the range of values obtained is significant, ranging from 0.02 to 0.047 m2K/W. Here we see the result for knits from pure wool and acrylic’s thermal resistance coefficient respectively 0.027 m2K/W and 0.031 m2K/W. Thermal resistance values of wool-acrylic socks are higher than % 100 acrylic socks and give warm sense at first contact. When polyester is plated with other yarn it produce lower thermal resistance than plated with lycra. Cotton (comb) + polyester thermal resistance (0.0123) is iower than viscose + lycra thermal resistance (0.0154). (Cotton-Bamboo)+Polyester thermal resistance (0.0141) higher than cotton (comb) + polyester (0.0123) due to bamboo fibre has higher thermal resistance. Comparing socks knitted from different fibers (cotton, bamboo, viscose etc.) the most comfortable socks for a warm season would be those knitted from a combination of yarn with Polyester thread, as these are characterized by a higher thermal conductivity coefficient, and the person would feel more comfortable wearing such socks. Socks plated with (Lycra) should be used for a cold season, as these are characterized by a lower thermal conductivity coefficient. For summer, socks knitted from pure yarns of cotton or bamboo blends and their combination with polyester could be used. For winter the most comfortable would be socks knitted from a combination of cotton or bamboo blends with Lycra thread [12].
ACKNOWLEDGEMENTS
This research is performed in different socks industries of Bangladesh named BYC Socks Limited, Shahrian Apparels Ltd etc. We are extremely grateful to the authorities of those textile industries for giving us the permission to perform these knitting processes & parameters in their production floor.
References
[1] | Malt, B.C. and E.E. Smith, Correlated properties in natural categories. Journal of verbal learning and verbal behavior, 1984. 23(2): p. 250-269. |
[2] | Thompson-Schill, S.L. and J.D. Gabrieli, Priming of visual and functional knowledge on a semantic classification task. Journal of Experimental Psychology: Learning, Memory, and Cognition, 1999. 25(1): p. 41. |
[3] | Ricci, G., et al., Use of textiles in atopic dermatitis, in Biofunctional textiles and the skin. 2006, Karger Publishers. p. 127-143. |
[4] | Hasan, K.F., Study on the changes of gsm (gm/m2) of grey knitted fabric from pretreatment to finishing. International Journal of Textile Science, 2015. 4(6): p. 119-136. |
[5] | Mia, M.S., et al., Effective Processing Time & Cost Management of Dyes, Chemicals & Utilities Used in the Combed & Compact Knit Fabric Colouration in the Dyeing Textile Industries. American Journal of Energy and Environment, 2016. 1(1): p. 1-16. |
[6] | DeMott, R.P., K.C. Gillis, and E.G. Stringer, Absorbent fabrics, products, and methods. 2004, Google Patents. |
[7] | Nadzeikienė, J., et al., Plant protection by foam in the thermal control process. Agronomy Research, 2009. 7 (Special Issue 1): p. 425-429. |
[8] | Stegmaier, T., J. Mavely, and P. Schneider, 6-High-Performance and High-Functional Fibres and Textiles. In Textiles in Sport, 2005: p. 89-119. |
[9] | Garbellano, D.W., Diving apparel. 1961, Google Patents. |
[10] | Watkins, W.B.C., Fabric having improved elasticity, modules and breathability, and garment made thereof. 2001, Google Patents. |
[11] | Meinander, H. and M. Varheenmaa, Clothing and textiles for disabled and elderly people. VTT TIEDOTTEITA, 2002. |
[12] | Hursh, D.F. and J.B. Johnston, Anti-friction two-ply athletic sock. 1989, Google Patents. |
[13] | Fung, W., Coated and laminated textiles. Vol. 23. 2002: Woodhead Publishing. |
[14] | Benltoufa, S., et al., Porosity determination of jersey structure. AUTEX Research Journal, 2007. 7(1): p. 63-69. |
[15] | Čiukas, R. and D. Sadauskas, Theoretical Determination of Area Density and Tightness Factor for Weft knitted Fabrics International Textile, Clothing and Design Conference. Proceedings. Dubrovnik, Croatia, 2004: p. 669-674. |
[16] | Soane, D.S. and D.A. Offord, Modified textiles and other materials and methods for their preparation. 2003, Google Patents. |
[17] | Čiukas, R., J. Abramavičiute, and P. Kerpauskas, Investigation of the thermal properties of socks knitted from yarns with peculiar properties. Part II: thermal resistance of socks knitted from natural and stretch yarns. Fibres & Textiles in Eastern Europe, 2011. 19(3): p. 86. |
[18] | Čiukas, R., J. Abramavičiūtė, and P. Kerpauskas, Investigation of the Thermal Properties of Socks Knitted from Yarns with Peculiar Properties. Part I. Thermal Conductivity Coefficient of Socks Knitted from Natural and Synthetic Textured Yarns. Fibres & Textiles in Eastern Europe, 2010. 18(3): p. 80. |
[19] | Bivainytė, A., D. Mikučionienė, and P. Kerpauskas, Investigation on thermal properties of double-layered weft knitted fabrics. Materials Science, 2012. 18(2): p. 167-171. |