Mohamed E. Khalifa1, 2
1Department of Chemistry, Faculty of Science, Taif University, Taif, Saudi Arabia
2Department of Chemical Engineering, Higher Institute for Engineering and Technology, New Damietta, Egypt
Correspondence to: Mohamed E. Khalifa, Department of Chemistry, Faculty of Science, Taif University, Taif, Saudi Arabia.
Email: |  |
Copyright © 2017 Scientific & Academic Publishing. All Rights Reserved.
This work is licensed under the Creative Commons Attribution International License (CC BY).
http://creativecommons.org/licenses/by/4.0/

Abstract
Merecerization treatment for cotton yarn fibers is very essential process to increase the luster, tensile strength and enhancement their dyability. In this investigation, a selection of three common yarn patterns (2/9.5, 984 and 3/8) was subjected to different mercerization experiments under factory conditions, to optimize the caustic soda concentration for highest quality and economic impact. Each of mechanical and color properties were measured, where the experimental evidences indicated that optimum benefits of caustic soda concentration for improving color yield and mechanical properties can be obtained at 25% caustic soda concentration. The retrieval study of the wasted caustic soda was also performed.
Keywords:
Cotton yarns, Mercerization, Luster, Caustic soda, Dyability
Cite this paper: Mohamed E. Khalifa, Mercerization of Cotton Yarn Fibers. Optimization of Caustic Soda Concentration via Degree of Mercerization, Dyability and Mechanical Properties, International Journal of Textile Science, Vol. 6 No. 1, 2017, pp. 15-19. doi: 10.5923/j.textile.20170601.03.
1. Introduction
Mercerization treatment process is subjecting the vegetable fibres (e.g. Cotton) to the action of a concentrated solution of a strong base at a proper temperature, to produce great swelling with resultant changes in the fiber structure. In industry, mercerization of cotton fabrics and yarn fibers is an essential preparation process in wet-wet or wet-dry processing technology for treating textile materials that enhances dyeing behaviour besides improving dimensional stability, tensile strength, and luster as well [1-4]. Changes in microstructure, morphology, and conformation of the cellulose chains also occur during mercerization depending on the treatment processes, mechanisms of their actions, temperature, duration, as well as the degree of applied tension during the treatment and physical state of cellulose. Cotton yarn mercerization can be applied in hank, cheese, single-end mercerization, or tow mercerization on raw or scoured, wet or dry. Hank mercerization process is carried out by slack or tension treatment, but combination of slack and tension treatment is usually done to prevent a loss in yardage and to produce the high luster [5-10]. Upon treating the cotton fibers with caustic soda (sodium hydroxide), they swell laterally and shrink longitudinally due to diffusion of water and alkali, and by application of tension to the yarn in the swollen state, a permanent luster is developed, while in the absence of tension, the resulting product gains in elasticity and becomes suitable for use as a stretch yarn or fabric [11]. The degree of swelling depends on the concentration of caustic soda, where at low caustic soda concentration, the sodium hydroxide molecules are hydrated by large number of water molecules and the diameter of the hydrated ions is too large to penetrate into the macromolecular structure of cotton, while increasing of its concentration will decrease the number of water molecules available for the formation of hydrates and thus formation of hydrated ion pairs which are capable of penetrating into the fiber structure of cotton by breaking hydrogen bonds and weak Van der Waal forces between cellulose chains resulting in fiber swelling and the corresponding fiber shrinkage [12-14]. The main objective of this study is to establish experimentally, under factory conditions and in production scale, the most appropriate concentration of caustic soda to be applied for selected patterns of industrially important cotton yarns at which higher degree of mercerization, mechanical properties and dyability are achieved as a research study in Misr Beida Dyers factory, Egypt.
2. Results and Discussion
The fibre cell structure reflects the incident light as per its cell structure in a regular or irregular way, thus affecting the luster of the fibre surface. The regular reflection from the fibre is obtained by passing through a mercerizing treatment, where the cotton fibres' shape become round when it shrinks in the solution of caustic soda (figure 1). As the result of reducing the cell lumen and increasing the cell wall, both the luster and the swelling power of the fibre increase, and the strength of the fibre increases up to 20-30% as well.  | Figure 1. Electron microscope image of cotton fibers (x2200), a, natural; b, mercerized cotton |
It is a well-known fact that cotton fibers can be considerably modified during mercerization in terms of crystallinity, orientation of crystallites, as well as orientation of macromolecular chains resulting in increase of the mechanical properties. Fibers become more amorphous and less crystalline but with improved orientation of fiber’s micro and macro units [15]. The reactions of concentrated sodium hydroxide with the cellulose fibers in mercerization process are assumed to be intramicellar reactions. That is the sodium hydroxide penetrates inside the micelles (crystallites) and reacts with the hydroxyl groups inside the macromolecule in such a way that it either produces sodium cellulosate (Cell-ONa) or it links to the molecules through the pulling forces [16]. It is estimated that the number of available hydroxyl groups are increased by about 25% as a result of causticization process for the fiber. This increase in the amorphous part and availability of hydroxyl groups is assumed to be directly related to the increase moisture sorption, reactivity and dye absorption (dye uptake) of mercerized cotton [17]. In this study, mercerization process for three different cotton yarn patterns (2/9.5, 984 and 3/8) was performed in Jaeglli Hank Mercerizer at 18C by rolling the hanks in 15%, 20%, 25% and 30% caustic soda solution under factory conditions, in order to optimize alkali concentration that obtain highest quality. The ability of mercerized cotton fiber to absorb more iodine, dyes, moisture and alkalis, and to undergo oxidation or hydrolysis at increased rates compared to unmercerized cotton, is expressed by the efficiency of mercerization and has been measured in term of Barium Activity Number, according to AATCC test method 89-1998, where the most successful method for determining the degree of mercerization is measuring the preferential absorption of barium hydroxide from its dilute solution by mercerized cotton. The extent of this absorption is more than that by unmercerized cotton under the same conditions. Thus, the barium activity number, barium number or baryta number is given by equation 1 [18].  | (1) |
For b, s and u being the absorption quantities of barium hydroxide of the blank, mercerized and unmercerized samples, respectively. Full mercerization is indicated by a value over 150, which produces the good luster and high dyability for the yarn fiber. The degree of mercerization could be tested using an optical microscope, where it depends on number of swollen cellulose cells in the cross section of the fiber and expressed as poor, incomplete and full mercerization. The barium activity number results and mercerization efficiency description were tabulated in table 1. Table 1. Barium activity number measurements and mercerization efficiency for different yarn types in different caustic soda concentrations 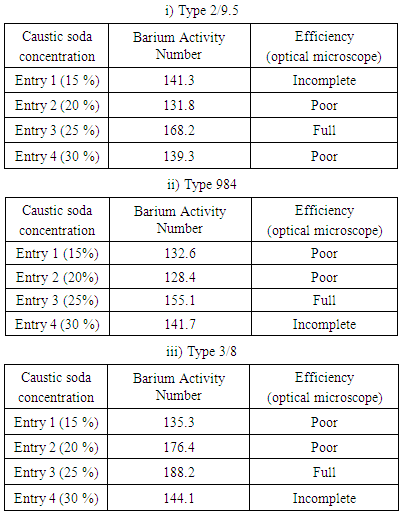 |
| |
|
The data obtained from table 1 revealed that the most acceptable caustic soda concentration that yield the highest mercerization efficiency is 25% (Entry 3), while increasing the caustic soda concentration up to 30% led to dramatically decrease in mercerization efficiency. That may due to increase the viscosity of the alkali and hence resulted in poor mercerizing of the core and lack of uniformity as the reaction is restricted mainly to the surface of the yarn, which in agreement with the previously studies [19]. Therefore, entry 4 was excluded from our further tests.Tensile strength (breaking strength) and elongation were measured for the yarns before and after mercerization for the selected three entries (1-3), in order to describe the effect of mercerization process on fiber mechanical properties as shown in table 2. The tensile strength and elongation are enhanced in directly proportional to the caustic soda concentration.Table 2. Tensile strength (breaking strength) and elongation measurements 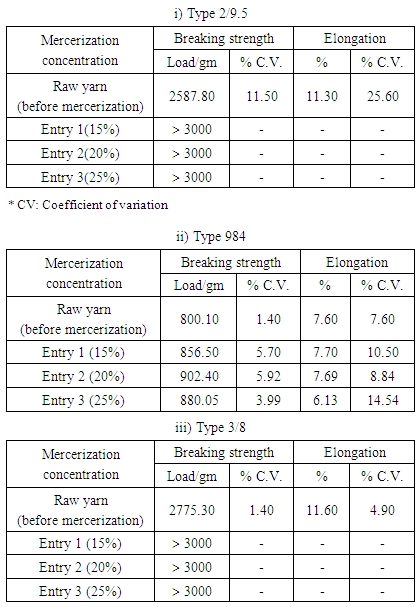 |
| |
|
On the other hand, testing the dyeability of the mercerized fibers will be very effective to measure the ability of the mercerized cotton fibers to dye absorption (dye uptake). For dyeing the selected cotton fibers, in practical terms, reactive dye was applied by 2% shade on the weight of fiber (o.w.f.). The dyeing process resulted in excellent leveling, uniformity of coloration and good exhaustion of dye liquor. The dyeing properties of cotton yarn fibers were evaluated in terms of their dye-uptake (K/S values) and fastness properties (e.g. fastness to washing, perspiration, and light) using a standard method [20]. The results were given in Table 3 and they revealed that the different entries shared good fastness properties, while the dye-uptake increased for entry 3 related to the increase of caustic soda.Table 3. Fastness properties and dye-uptake for the selected cotton yarn fibers at different caustic soda concentrations 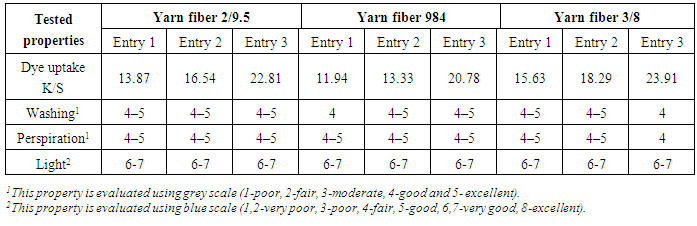 |
| |
|
It is very interested to analyze the remaining caustic soda concentration in waste bath after different washing cycles of the mercerization process, which is very useful to evaluate the efficiency of washing process. Retrieval and reconcentrating of the wasted caustic soda, were performed by a special unit available in the factory using evaporation technique. The concentrations of remaining caustic soda were determined by volumetric analysis against normal solution of sulfuric acid and the calculated percentages were presented in table 4. It is obviously clear that the economic caustic soda retrieval steps are the 1st and 2nd wash cycles as the waste caustic soda concentration is in the range of 13-22% and 2-5% respectively, while the lower concentrations of remaining caustic soda after the 3rd wash cycle will cause a high dilution in the Caustic Soda Retrieval Unit which will then consume more energy to be re-concentrated and will not be an economic choice.Table 4. Percentage of caustic soda remaining after different washing cycles 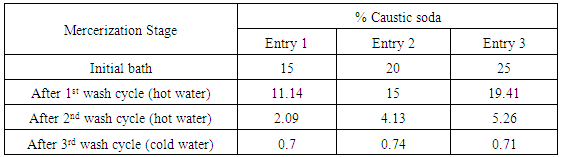 |
| |
|
3. Experimental
3.1. Material and Methods
All chemicals and auxiliaries are of commercial grade, and purchased from local (Egyptian) and international companies. Yarn fibers with three different spinning types 2/9.5, 984 and 3/8 were supplied by Kafr El-Dawar for spinning and weaving Co., Bohaira, Egypt. Mercerization experiments were performed in production scale using Jaeglli Hank Mercerizer (Jaeggli-Meccanotessile Co., Italy). Tensile strength and elongation were measured on Tenso lab tester (Mesdan Co., Italy) in an environment at 65% humidity and 21°C. The dye-uptake measurements for the dyed cotton yarns were carried out using a reflectance spectrophotometer (GretagMacbeth CE 7000a, GretagMacbeth Co., Windsor, UK). Fastness to washing was carried out using the automatic Rota dyer launder (Texcare Co., Delhi, India), fastness to perspiration was assessed according to the test sponsored by the British Standard Institute-Society of Dyers and Colourists (BSS), and fastness to light was carried out using the “Weather-o-meter” (Atlas Electric Devices Co., Chicago, IL, USA). All production experiments, chemical, physical tests, dyeing process and colorimetric measurements were performed by the yarn factory and chemical laboratories of Misr Beida Dyers Co., Alexandria, Egypt and in accordance to the American Association of Textile Chemists and Colorists (AATCC) standard methods.
3.2. Method of Application
The three types of yarn fibers were mercerized at 15%, 20%, 25% and 30% of caustic soda solutions in four separate entries in presence of an anionic wetting agent (Floranit 4028, product of Henkel Co., Germany), at 18°C for 120 sec. immersion time under the tension of the machine. The hanks were extended by application of tension to the original length, rinsed with hot water (80°C) for two times and cold water (18°C) for 60 sec., neutralized using 10% acetic acid solution and finally rinsed with cold water. The mercerized cotton yarns in form of hanks were centrifuged and dried by hot air drying room. The yarns were bleached by hydrogen peroxide bleaching bath at 100C for 1 hour, and finally dyed using reactive dye (Levafix Royal Blue E-FR, supplied by Dystar Co., Singapore) at 40C for 90 min. by reactive dyeing technique.
3.3. Barium Activity Number Method [18]
One gram of mercerized and unmercerized cotton yarns were each cut into small pieces, dried over phosphorous pentoxide for 5 h, then conditioned at 65 % relative humidity at 31C before testing and consequently treated with 30 ml of 0.25 N barium hydroxide solution in 100 ml conical flasks. After 2 h, 10 ml of the solution is titrated against 0.1 N hydrochloric acid. A blank was also run without any yarn sample. The titration readings of the blank (b), mercerized (s) and unmercerized (u) samples, were recorded and the barium activity number values are calculated using equation 1. Appropriately large numbers of conditioned samples were taken, considering the moisture regain of the samples. Thus, if the moisture regains 8%, 1.08 g of the conditioned cotton sample was weighted to get 1g of the bone-dry cotton.
3.4. Dyeing Method and Color Fastness
For dyeing cotton fibers, in practical terms, reactive dyes are suitable. Levafix Royal Blue E-FR dyestuff was applied to the selected cotton yarns by 2% shade (o.w.f.) in presence of 50 gm/l glauber salt (Na2SO4.10H2O) and 15 gm/l soda ash (Na2CO3). The cotton yarns were exhausted in the dye bath at 40°C for 90 min. The dyes fibers were then soaped using non-ionic detergent, washed by hot and cold water intervalley and dried by hot air. The color fastness properties of the dyed fibres to washing, perspiration and light were evaluated using standard methods. The staining of adjacent cotton fabrics was assessed using the grey scale: 1-poor, 2-fair, 3-moderate, 4-good and 5-excellent, other than light fastness which scaled from 1–8 on the grey scale.
3.5. Color Yield Assessment
The color yield of the cotton yarn fibers (Dye-uptake) was determined in term of K/S values given by the reflectance spectrometer at λmax according to the Kubelka–Munk equation: K/S= (1 − R)2/2R, where K= absorbance coefficient, S= scattering coefficient, R= reflectance ratio, where the measurement of K/S expressed the comparative color yield or dye uptake and not the absolute quantity of dye present on dyed sample.
4. Conclusions
The mercerization process of different common types of cotton yarns showed that the degree of mercerization, dyability and tensile strength are gradually increased by increasing caustic soda concentration, while elongation character is not extremely changed. The optimum caustic soda concentration for efficient mercerization is 25% which produces the best mercerizing degree and mechanical properties rather than highest dyability based upon dye-uptake values.
ACKNOWLEDGEMENTS
The author wishes to extend his sincere thanks and appreciation to the management and staff members of the Chemical laboratory and Yarn sector, Misr Bieda Dyes Co., Alexandria, Egypt for their technical support and great cooperation.
References
[1] | C. M. Conrad and E. E. Berkley, "Some Possibilities and Limitations of X-Ray Methods for Measuring the Strength of Raw Cotton," Textile Res. J., vol. 8, pp. 341-352, Aug. 1938. |
[2] | P. H. Hermans, "Physics and Chemistry of Cellulose Fibre," London, England: Elsevier Publ. Co., 1949. |
[3] | T. Radhakrlshnan, B. V. Iyer, G. S. Viswanathan and H. Wakeham, "The Relation between Crystallite Orientation and Tensile Properties of Mercerized Cotton," Textile Res. J., vol. 29, pp. 322-331, Apr. 1959. |
[4] | L. Loeb and L. Segal., "The Treatment of Cotton Cellulose with Aqueous Solutions of Ethylamine," Textile Res. J., vol. 25, pp. 516-519, June 1955. |
[5] | S.I. Kim et al., "Mercerization in degassed sodium hydroxide solution," Fiber Polymer, vol. 7, pp. 186-190, June 2006. |
[6] | T. Haga and T. Takagishi, "Structural change in mercerized cotton fibers on cellulose treatment," J. Appl. Polym. Sci., vol. 80, pp. 1675-1680, Nov. 2002. |
[7] | T. Wakida et al., "Hot mercerization of cottons," Fiber, vol. 58, pp. 304-307, March 2002. |
[8] | S.O. Rollin et al., "Physical properties of mercerized and decrystallized cottons: Part I: Effects of Swelling Solutions on Fibers and Yarns," Textile Res. J., vol. 29, pp. 349-355, Apr. 1959. |
[9] | Y. Yuichi et al., "The liquid ammonia treatment of cotton fibers," Fiber, vol. 62, pp. 100-105, 2006. |
[10] | J. T. Marsh, "Mercerising," London, England: Chapman & Hall Ltd., 1951, vol. 458. |
[11] | Theory of mercerizating, http://textilelearner.blogspot.com/2012/12/theory-of-mercerizing-purpose-of.html#ixzz4SPyHygSn. |
[12] | J. O. Warwicker, "A Review of the Literature on the Effect of Caustic Soda and Man-Made Fibres," Research Association. Manchester, UK. (1966) |
[13] | L. Menachem, Hand book of fiber chemistry, 3rd ed. London, England: Taylor & Francis, 2007. |
[14] | S. R. Karmakar, "Chemical technology in the pre-treatment technology of textile processes," ELSEVIER, Amsterdam, Netherlands. (1999) |
[15] | G. F. S. Hussain et al., "Influence of Mercerization and Crosslinking on the Dynamic and Static Moduli of Cotton Yarns," Text. Res. J., vol. 52, pp. 663-665, Oct. 1982. |
[16] | Mercerizing | Definition Mechanism and effects of Mercerizing | Textile Fashion Study, Textile Engineering & Fashion Design Blog, 2012. |
[17] | T. Wagaw and R. B. Chavan, "Optimization of Caustic Soda Concentration for Causticization of Cotton," Open Access Scientific Reports, vol. 1, pp. 1-6, 2012. |
[18] | AATCC test method 89-1998, AATCC technical manual 2006. |
[19] | J. J. De Boer and H. Borsten, "An Empirical Relation for the Degree of Penetration of a Mercerization Solution into a Cotton Yarn," J. Textile Inst. Trans., vol. 53, pp. 497-510, June 1962. |
[20] | A. D. Ferguson and T. P. Taylor, "Standard Methods for the Determination of the Colour Fastness of Textiles and Leather," J. Soc. Dyers Color., vol. 96, pp. 18-23, Jan. 1980. |