Md Nazmul Haque
Lecturer, Department of Textile Engineering, Southeast University, Dhaka, Bangladesh
Correspondence to: Md Nazmul Haque, Lecturer, Department of Textile Engineering, Southeast University, Dhaka, Bangladesh.
Email: |  |
Copyright © 2016 Scientific & Academic Publishing. All Rights Reserved.
This work is licensed under the Creative Commons Attribution International License (CC BY).
http://creativecommons.org/licenses/by/4.0/

Abstract
At present, textile industries have to strictly control their costs to survive and continue their success. Fabric cost constitutes about maximum of a garment cost. Garment cutting is essential process before garments making. For cut plan different sorts of markers are created according to garments production suitability. Sometimes due to different fabric design, repeat size and fabric shade variation problem marker maker bound to make different types of marker which completely different from regular marker. For this experiment a reputed buyer product mans long sleeve shirt pattern used to make different sorts of marker in fix width. For pattern modification and design Lectra Modaris V6R1 6.1 software and marker making Lectra Diamino Fashion V6 software used. After marker making a comparative analysis of different sorts of marker in fix width has been made to see which one more efficient marker as well as reduce fabric consumption. A comparative analysis of more efficient marker with rest of the different types marker has been made to see how much it varies both in fabric consumption and marker efficiency and also how fabric design, repeat size and shade variation changes marker efficiency and fabric consumption.
Keywords:
Marker, Marker Efficiency, Pattern, Pattern Grading, Fabric consumption, Fabric shade variation
Cite this paper: Md Nazmul Haque, Impact of Different Sorts of Marker Efficiency in Fabric Consumption, International Journal of Textile Science, Vol. 5 No. 5, 2016, pp. 96-109. doi: 10.5923/j.textile.20160505.02.
1. Introduction
The garments industry in Bangladesh has been expanded almost uninterruptedly since the late 1970s. It survived Multi-fiber Arrangement (MFA) phase out at the end of 2004 and remains internationally competitive to date [9]. Garment industry contributes a high percentage in the country’s total revenue but still facing many challenges. Ten years ago if a catalog order was placed, the expected delivery was four to six weeks. Today after two or three days, consumer begins to wonder where and why their merchandise is being delayed [6]. These days, customers have become more demanding and always looking for new styles and designs in the stores more frequently, which affects the turnaround time from concept to consumer. With the increasing competition and decentralized manufacturing garment industries are looking forward to the different software solutions to systematize the processes and to overcome their challenges [11]. It is therefore, of paramount importance that government and industry have to formulate a concrete program for modernization, technology up gradation etc [4]. In apparel manufacturing, fabric cutting is done before assembly. The performance of the cutting department, which is generally neglected by manufacturers, is a critical factor on the smoothness of downstream operations in sewing lines and hence the overall efficiency of the apparel manufacturing plant [16]. After that marker making is one of the crucial processes before garments cutting for bulk production. One of the most crucial activities that take place in cutting room is Cut Order Plan. Cut Order Planning is deciding the combination of markers, and lays for a particular order. A marker is a diagram of a precise arrangement of pattern pieces for a specific style and the sizes to be cut from a single spread, or marker, is a thin paper which contains all necessary pattern pieces for all sizes for a particular style of garments in such a way that, fabric wastage would be least. The minimization of fabric wastage is crucial to the reduction of production costs. A higher efficiency marker results in better savings. Marker planning is always a very open & creative process. Marker planning is a highly skilled activity and different people have different attitudes for this kind of work [5]. Before garment designing has been made by hand using sketches drawn in paper or draping fabric on a dress form. Now with the CAD/CAM software this marker can be made in computer and after that printed marker paper lays on the top of the fabric and cutting has been done. Marker efficiency and fabric consumption shows on screen which has been impossible in manual system marker making [15]. Efficiency is the major points in any manufacturing organization in order to stay alive in competitive market. An efficient marker will help factory to reduce fabric consumption and increases profitability [13]. A study done by the Clothing Industry Productivity Association and National Productivity Institute of South Africa revealed marker utilization as one of the six key ways to improve material utilization. The efficiencies can be checked and monitored by checking the area of the pattern versus the area of the marker. Corners of patterns can often be reduced without affecting the sew-ability or wear-ability of the garment. It may also be possible to tilt the pattern slightly or to eliminate or to add seams. While adding seams may increase the sewing cost, significant fabric savings may be the result. The use of computers to aid in the development of markers has led to these more efficient markers being generated very quickly [2]. By introducing the new technologies into the process of garment production, we can achieve a substantial increase in productivity and quality of work. Consequently, the clothing industry is being transformed from a traditional, labor intensive industry, into a highly automated and computer-aided industry [14]. For mass customization as such, advance computer technology is being utilized extensively in the apparel industry from product planning to manufacturing and marketing. Particularly for past and accurate production in the apparel manufacturing process, flexible computer aided manufacturing system being applied to apparel manufacturing process such as apparel pattern making, grading and marker making [7]. Some of the apparel CAD system suppliers do offer "automatic marker making". These special packages generally use simple rules to generate markers automatically, with no aid from the operator. Because the rules are necessarily simple for computational efficiency, the systems cannot consistently outperform the human being with respect to fabric utilization [3]. The cutting department of a garment manufacturing factory supplies the cut panels required for the production modules. Therefore, the cutting process is one of the main value adding processes in a factory [12]. Garment manufacturing process consists of series of different steps between that cutting is one of the important portion. These steps are broadly divided into two categories pre-production and production process. The preproduction process consists of designing the garment, pattern design, sample making, production pattern making, grading and marker making. Once the sample is approved for commercial production, final marker is made for cutting. The production process consists of cutting, stitching (preparatory and assembly) and finishing [10]. For marker making use of CAD helps economize on fabric usage in addition to improving stage times. Technological advances during the past decade have opened many new doors for the Textile and Apparel industries, especially in the area of rapid prototyping and related activities [8]. This clearly shows that CAD investments are considerable with respect to savings, not only in labor costs but also in fabric usage, which amounts to 60% of total garment costs [17]. Fabric is the biggest cost driver of the garments industry, accounting to 50 to 80 percent of the garments cost, so even a small fabric saving of 2 percent can add a good amount to garments manufacturer pockets [1]. Due to different fabric design and fabric faults like shading problem marker maker bound to make different marker. One point of time it was a comparison between manual markers vs. computerized marker. It times to make comparison between different sorts of marker produced by computerized marker.
2. Experimental
2.1. Materials
2.1.1. Mans Long Sleeve Shirt
To create pattern for this experiment will have to choose a product of certain style. These mans long sleeve shirt is order placed by a reputed buyer. These garments order includes seven different sizes of garments which are XS, S, M, L, XL, XXL and 3XL. Description of measurement in cm for all sizes has been given in Table 1. This measurement has been used to create pattern for different sizes of garments.
2.1.2. Pattern Making
At first with the help of Lectra Modaris V6R1 6.1 software and Table 1 measurement chart, pattern for XXL size has been made. Pattern for different parts of XXL size garments has been shown in Figure 1. Pattern grading has been done to convert pattern for different sizes of garments from XS to 3XL sizes.Table 1. Measurement of different sizes of garments for mans long sleeve shirt 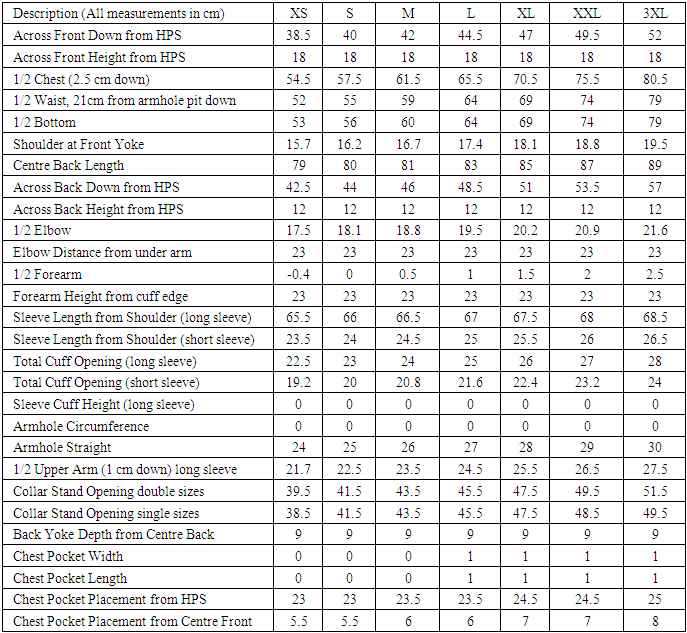 |
| |
|
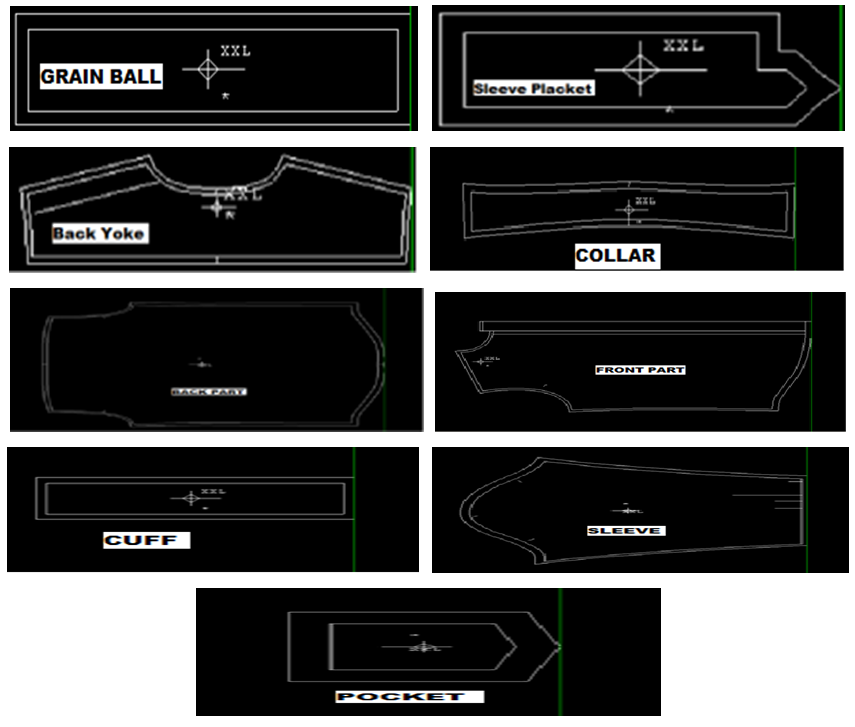 | Figure 1. Pattern for different parts of XXL size garments |
2.2. Methods
2.2.1. Marker Making
Pattern grading helps to create different sizes of pattern for different sizes of garments from XS to 3XL. For pattern grading Lectra Modaris V6R1 6.1 software has been used. For that experiment marker width is fixed which is 56 inch and marker length will be defined the fabric consumption. Total garments quantity to make every marker is 12 pc where different sizes of garments included in different portion of marker length and width depending on which marker need to be make.
2.2.1.1. Solid Marker
Solid marker is one in where one particular size garments different parts of garments pattern has been used to make marker. Here XS is the smaller size marker and XXL largest size marker. Marker efficiency of XS, S, M, L, XL and XXL sizes are 87.75 (%), 87.72 (%), 87.99 (%), 88.11 (%), 89.37 (%) and 88.01 (%). Marker length or Fabric consumption of XS, S, M, L, XL and XXL sizes are 14.903 meter, 15.695 meter, 16.459 meter, 17.274 meter, 17.580 meter and 19.728 meter.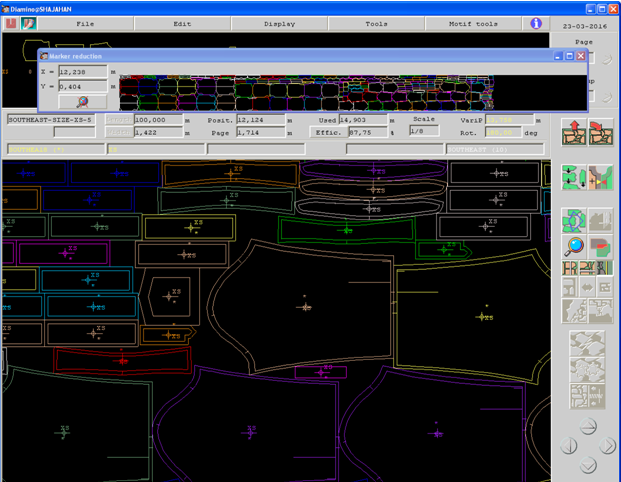 | Figure 2. XS size solid marker (Garments quantity 12 pc) |
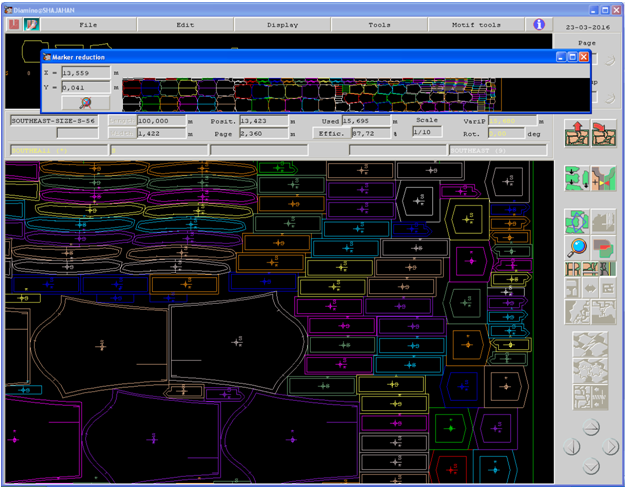 | Figure 3. S size solid marker (Garments quantity 12 pc) |
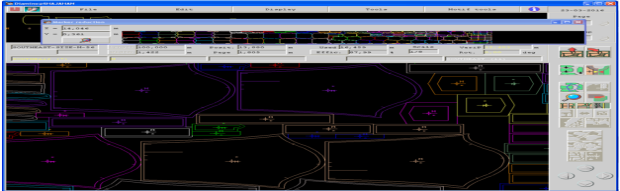 | Figure 4. M size solid marker (Garments quantity 12 pc) |
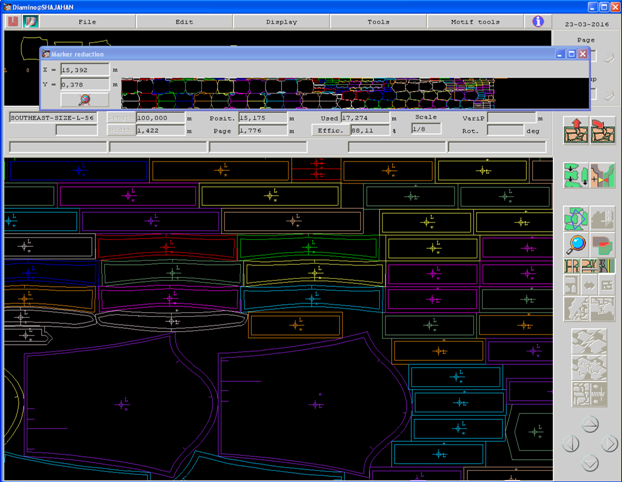 | Figure 5. L size solid marker (Garments quantity 12 pc) |
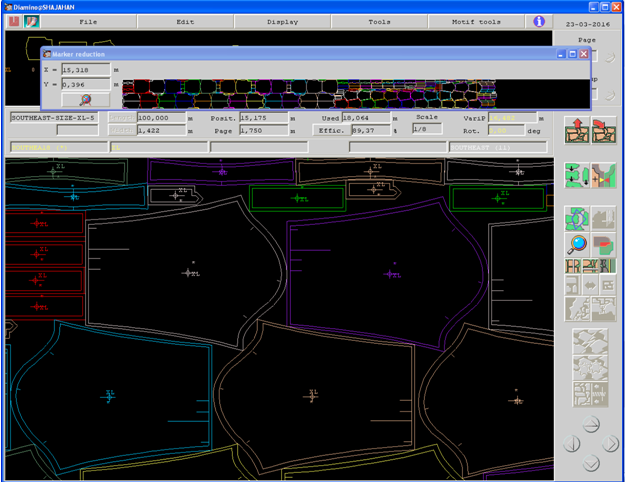 | Figure 6. XL size solid marker (Garments quantity 12 pc) |
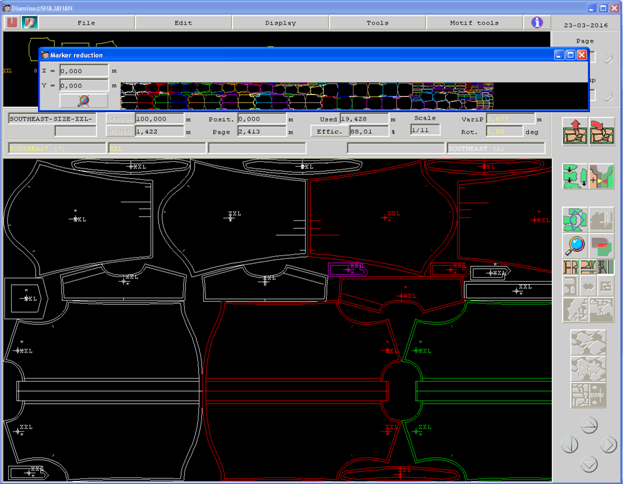 | Figure 7. XXL size solid marker (Garments quantity 12 pc) |
2.2.1.2. Mixed Marker
12 pieces of different size garments are kept together by maintaining the ratio XS: S: M: L: XL: XXL = 2:2:2:2:2:2.Marker efficiency 89.05 (%) and Marker length or fabric consumption 16.803 meter.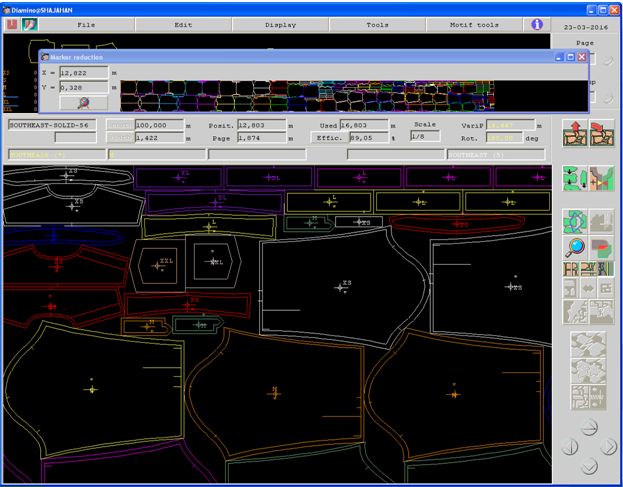 | Figure 8. Mixed marker (Garments quantity 12 pc) |
2.2.1.3. Ratio Marker
Ratio marker is one where one or more particular size of garments order quantity will be more compare with rest of the sizes. Here 3XL size is added instead of XS. If there is excess increment of marker pattern’s size we want to see whether or not it has any effect on marker efficiency or consumption. Here the ratio is S: M: L: XL: XXL: 3XL = 1:2:3:3:2:1. Marker efficiency 85.35 (%) and Marker length or fabric consumption 16.803 meter.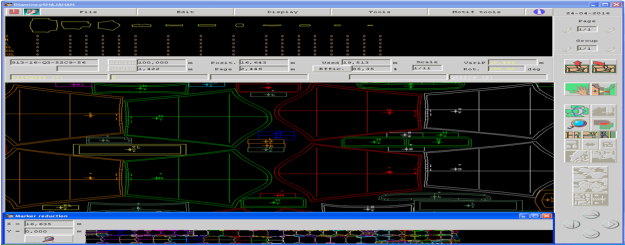 | Figure 9. Ratio Marker |
2.2.1.4. Check Marker
In addition to check fabric sometimes we found check fabric repeat 1″-1.5″. For thats sort of fabric factory bound to make check marker. Here the ratio is XS: S: M: L: XL: XXL = 2:2:2:2:2:2:2 = 12 pieces. Marker efficiency 86.48 (%) and Marker length or fabric consumption 17.303 meter.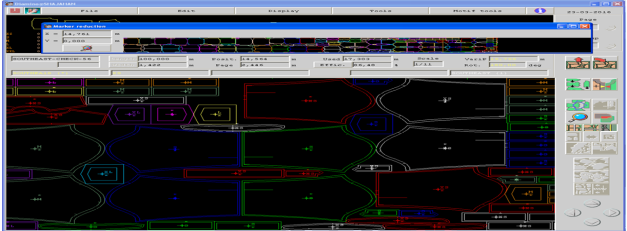 | Figure 10. Check Marker |
2.2.1.5. Balancing Marker
If the fabric repeat size is equal or more than 5″ on fabric then need to make balancing marker. Here the ratio is XS: S: M: L: XL: XXL = 2:2:2:2:2:2:2 = 12 pc. Marker efficiency 86.12 (%) and Marker length or fabric consumption 17.376 meter.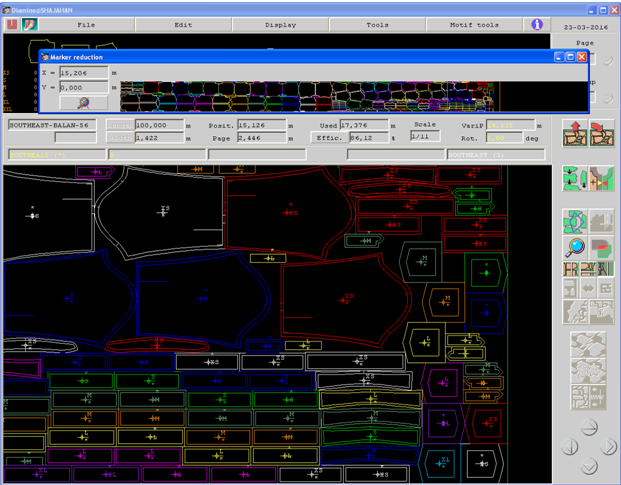 | Figure 11. Balancing Marker |
2.2.1.6. Selvedge Marker
Sometimes fabric width wise shading has been found closer to two selvedge because of dyeing faults. In selvedge markers, all the patterns are set according to the direction of fabric length closer to fabric selvedge. Fabric width is divided into two section in selvedge direction becuase of shading difference between two selvedge. So selvedge marker has been made where marker width is divided into two section. One section pattern pieces of one particular size of garments can not be mixed with the another section another size of garments pattern pieces pattern pieces. Here the ratio is XS: S: M: L: XL: XXL = 2:2:2:2:2:2:2 = 12 pc. Marker efficiency 84.87 (%) and Marker length or fabric consumption 17.633 meter.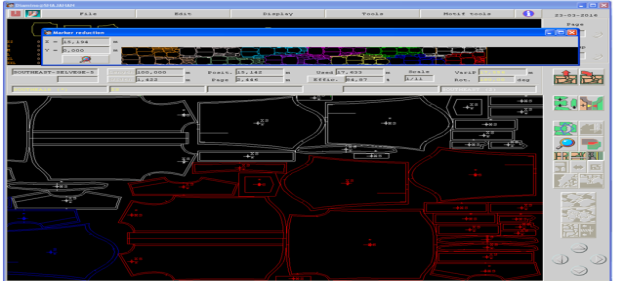 | Figure 12. Selvedge marker |
2.2.1.7. Group Marker
If running shade has been found in fabric then group marker is made. The term running shade in dyeing means different shade has been found in lengthwise in fabric. Each section contains different shade compare with other section. So one particular size garments pattern laid down in one section of marker so they don’t mix up with other section. In marker length each individual section has been created to laid down pattern for each individual size. Here the ratio is XS: S: M: L: XL: XXL = 2:2:2:2:2:2:2 = 12 pc. Marker efficiency 84.95 (%) and Marker length or fabric consumption 17.616 meter.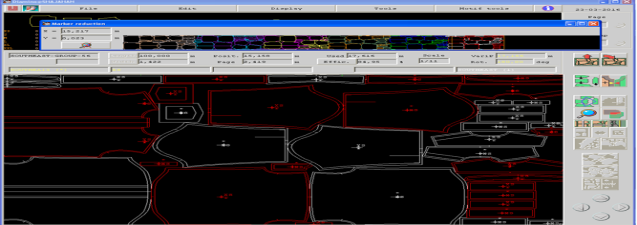 | Figure 13. Group Marker |
2.2.1.8. All Garments One way Marker
It is one kind of marker where all garments pattern are kept in one direction. These sort of marker has been made specially in case of asymmetrical fabric like corduroy fabric. Here the ratio is XS: S: M: L: XL: XXL = 2:2:2:2:2:2:2 = 12 pc. Marker efficiency 87.59 (%) and Marker length or fabric consumption 17.085 meter.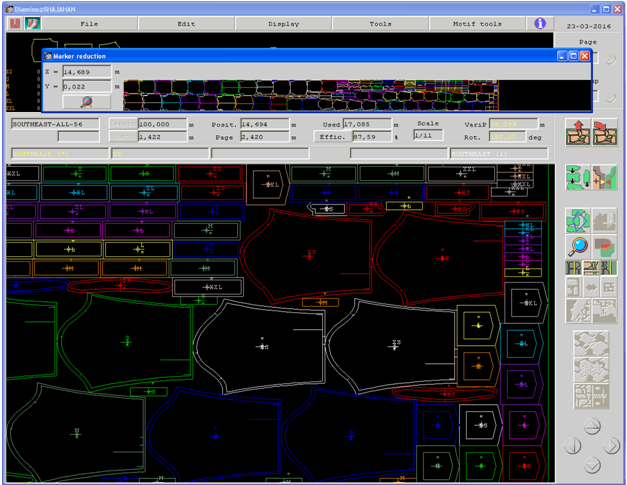 | Figure 14. All Garments One Way Marker |
3. Results and Discussion
3.1. Impact of Pattern Grading in Marker Efficiency and Fabric Consumption
Pattern grading has been done to convert one sizes pattern into another sizes pattern. Figure 15 it has been seen that if size wise markers efficiency increases, then consumption will also increase except XXL sizes garments. From XS size to XL size, efficiency increases side by side consumption will also increases. Because marker width is fixed, so when size of the garments increases it becomes difficult to give big sizes pattern in the space of marker width. Table 2 shows that When XS graded to convert S size, the measurement of the big pattern of garments like front part, back part and sleeve section increases more rather than small pattern pieces like grain ball, collar and sleeve placket etc. when the size of the garments is increased it becomes difficult to marker maker to accommodate big pattern pieces into marker width. As a result his pattern takes the position in marker length, as a result during pattern grading when the size of the garments increases marker efficiency and consumption also increases. We all know that the more marker length, the more will be fabric consumption.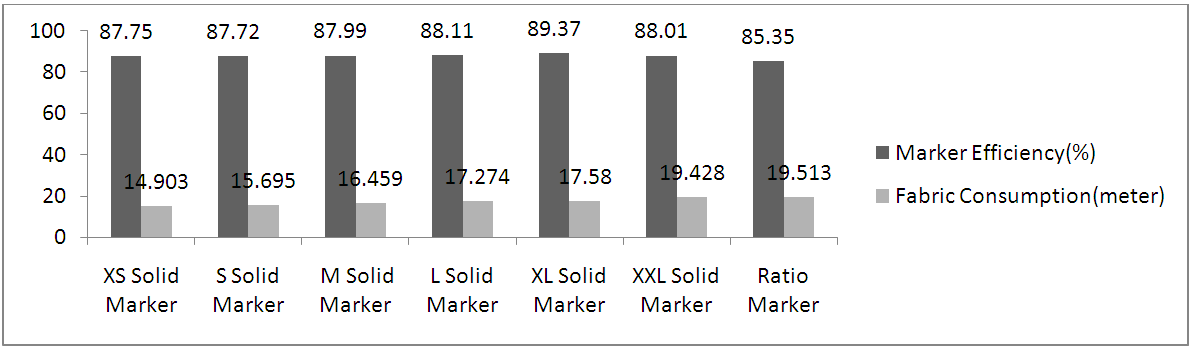 | Figure 15. Sizewise solid marker and Ratio marker efficiency and consumption |
Table 2. Different types of size wise Solid Markers & Ratio Marker’s Efficiency & Consumption 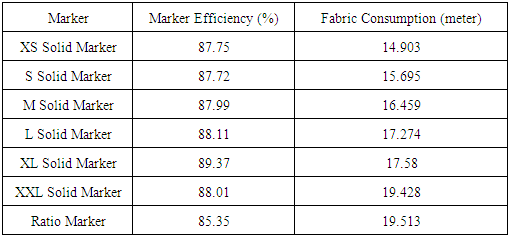 |
| |
|
Reverse happen in case of XXL solid marker. Here consumption increases but efficiency decreases. When we convert from XL marker to XXL marker, then consumption rate from XL to XXL goes higher.Table 3 where fabric consumption and marker efficiency difference between two consecutives marker has given. Figure 16 it has been seen that marker efficiency difference between XXL to XL marker is -1.36 and fabric consumption difference 1.848 meter which is comparatively greater than rest of the two consecutive marker efficiency and fabric consumption difference.Table 3. Marker efficiency and consumption difference between two consecutive solid Markers 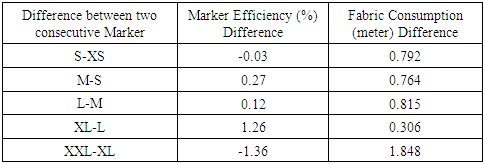 |
| |
|
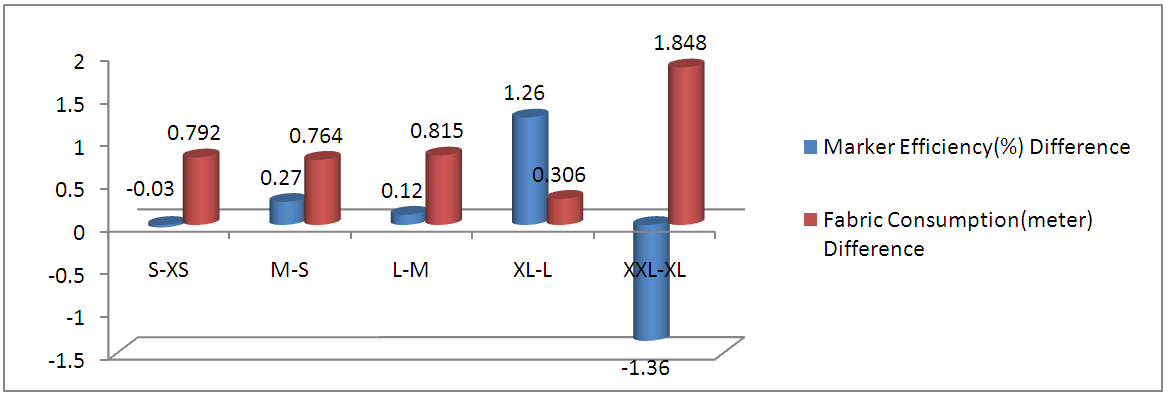 | Figure 16. Graphical representation of difference between two consecutive solid markers |
Because of XXL size large pattern parts measurements are increasing more than the XL size large parts measurement. That’s why consumption is increasing but efficiency is decreasing because, XXL marker parts are larger and those have to set length wise. Because XXL is a big size garments compare with XL size, in marker not only empty space created between two large pattern pieces but also reduce the space for small parts to fill that gap in marker width. Excessive increment of large sizes pattern pieces of XXL size compare with XL size are main reason for that scenario.To confirm that’s scenario, we introduced the ratio marker to this experiment because we wanted to see whether or not there is any effect on efficiency or consumption if there is excess increment of large sizes pattern pieces. So, we added 3XL size instead of XS size for this marker. The ratio for this marker is S: M: L: XL: XXL: 3XL = 1:2:3:3:2:1 where the introduction of large sizes garments are more. Table 2 it is found that marker efficiency = 85.35 (%) and Marker length or fabric consumption=19.513 meter. Because of 3XL size measurements are greater than X XL sizes, it can be said that too much increment in large sizes pattern pieces during pattern grading, marker efficiency decreases but marker length increases or fabric consumption increases.
3.2. Mixed Marker: A Solution to Reduce Fabric Consumption but Increase Marker Efficiency
Solid marker actually makes with one particular size. For example if solid size of M marker has been made then M garments bodies different pattern like front part, back part, sleeve placket, collar and back yoke will be used. For this experiment to make every marker 12 pc garments are considered. In Bangladesh most of the factory make solid marker. Reason behind that when a particular order received from buyer at first they make large size solid marker. For example this experiment if order is different sizes like S, M, L, XL and XXL. Factory will prefer to make XXL sizes solid marker. Benefit is that if in case of garments production any body parts of XL sizes pattern are short or distorted or destroyed, it is possible to cut XXL pattern part into XL pattern part. But a XL sizes pattern part could not be converted into XXL sizes pattern part. That’s why they choose XXL sizes production first, then XL sizes production, then L size and this way production procedure goes to bigger sizes first and smaller sizes in the last. Problem in that’s sorts of marker making and garments production procedure is that it actually slow down the garments production procedure. One garments line will only produce one particular size at a certain time of period. Possibilities of using different garments line to produce varieties of sizes are reduced and productivity also becomes low.To reduce that’s of limitation during production mixed marker can be introduced. For this experiment at first solid marker of different sizes has been made. Fabric consumption and marker efficiency for each individual size has been calculated. After that average of solid marker fabric consumption and marker efficiency has been calculated in Table 4. Then 12 pc mixed marker has been made where different size garments are kept together by maintaining the ratio XS: S: M: L: XL: XXL = 2:2:2:2:2:2. Figure 17 shows that average of solid marker efficiency 88.158 and fabric consumption 16.880. Mixed marker efficiency 89.05 (%) and fabric consumption 16.803 meter. Difference between average of solid marker and mixed marker efficiency is 0.892 (%) and fabric consumption 0.077m. This result just shows that mixed marker is more efficient marker than solid marker.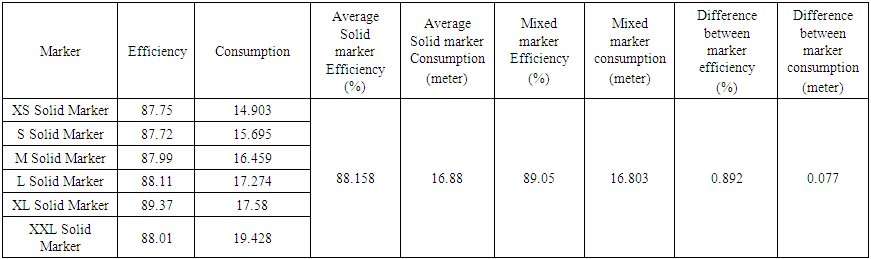 | Table 4. Marker efficiency and consumption difference between mixed marker and average solid marker |
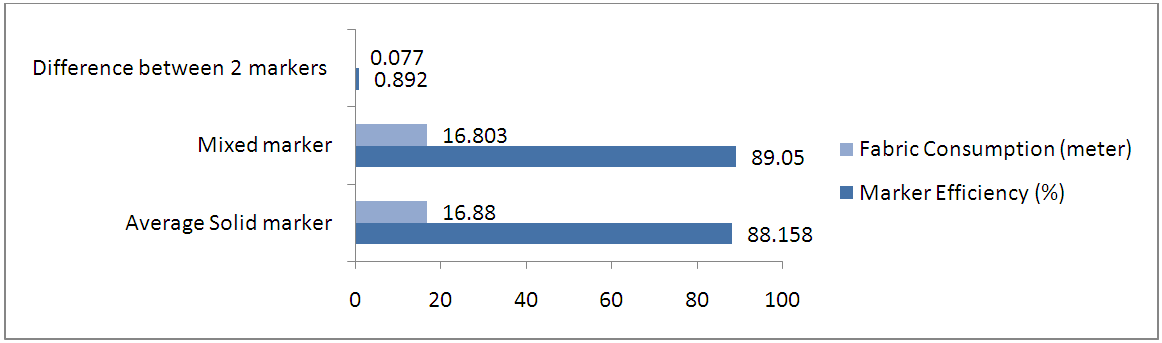 | Figure 17. Graphical representation of difference between mixed marker and average solid marker |
In Mixed marker, here, all sizes are used together and equal ratio like XS: S: M: L: XL: XXL = 2:2:2:2:2:2. As there different sizes are used, it is possible to use maximum width of marker. If there is a gap created in marker width, it is possible to fill that gap width any sizes pattern part like S, M, L, XL and XXL. As varieties of size created different parts of body parts pattern in different measurement as a result scope of using marker length reduces rather than marker width. Between two consecutive patterns parts in marker length and width less empty space are created. In case of marker, width is fixed, length is not fixed. As a result, marker length is decreases and consumption is decreased. Figure 18 comparison of mixed marker with rest of the marker with due to different reason factory bound to make, it has been seen that mixed marker is one of the best marker which marker efficiency high but fabric consumption is low.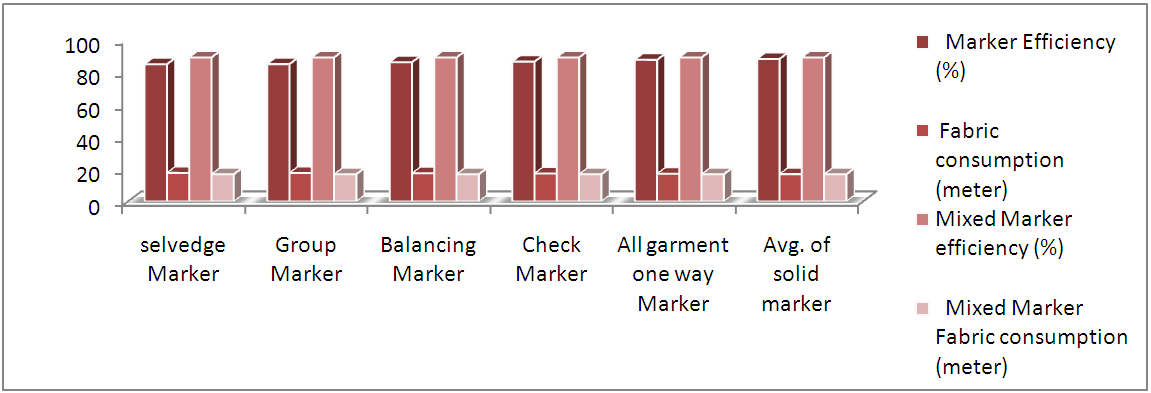 | Figure 18. Comparison of mixed marker and different types of marker |
3.3. Analysis of Mixed Marker with Different Types of Marker
It has been said that mixed marker is best marker. Sometimes due to different fabric design, repeat size and fabric shade variation problem marker maker bound to make different types of marker which completely different from mixed marker. All sorts of marker mention in Table 5 are 12 pc marker and fabric width is fixed which is 56 inch. Figure 19, it has been seen that efficiency of selvedge maker is minimum. This marker is used for length wise color shading on solid fabric. That’s why the fabric is divided by two parts. For that reason possibility of free space is increased. The efficiency reduced because in selvedge, marker patterns are laid along length wise closer to two selvedge portion which bear two different shade of same color fabric. So it is difficult to use maximum width of marker. Table 5. Efficiency of different types of marker 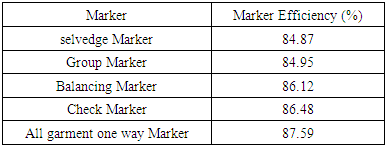 |
| |
|
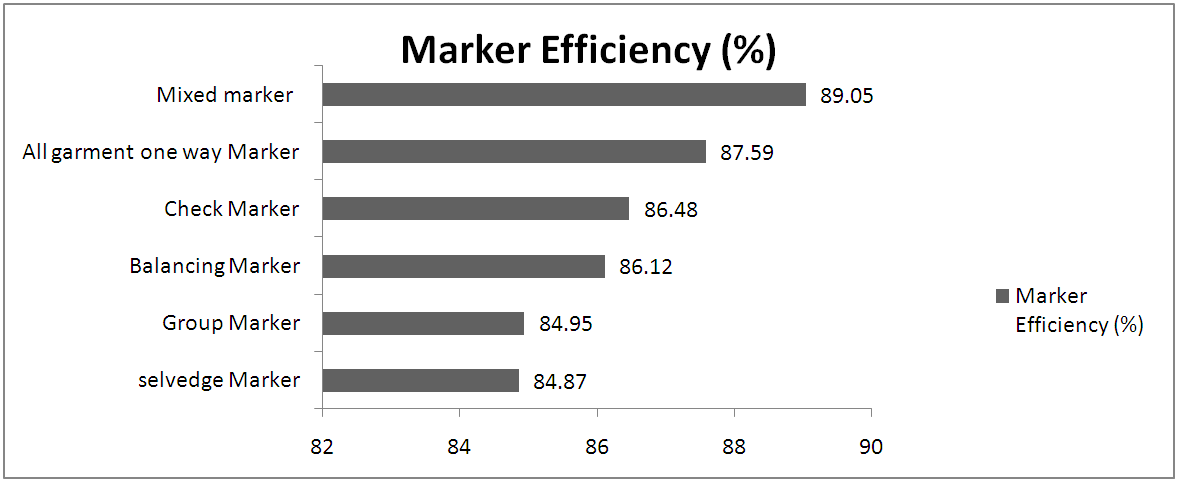 | Figure 19. Graphical representation of different types of marker efficiency |
Table 6 it has been seen that fabric consumption of selvedge is too much high which is 17.633 meter. Figure 20, it also observed that fabric consumption of selvedge marker is higher compare with the rest of the marker. In selvedge markers, all the patterns are set according to the direction of fabric width closer to fabric selvedge. The consumption is more because both side of fabric selvedge contain different shade. So fabric width is divided into two section. One section pattern pieces can not be mixed with the another section pattern pieces. That’s why we can’t use proper marker width because lots of gap has been created between middle of marker which remains unused. All patterns pieces set along the marker length. The more use of fabric length, the more will be fabric consumption.Table 6. Marker consumption of different types of marker 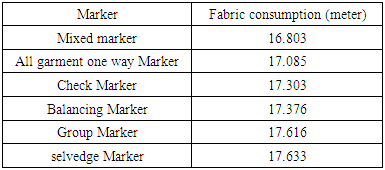 |
| |
|
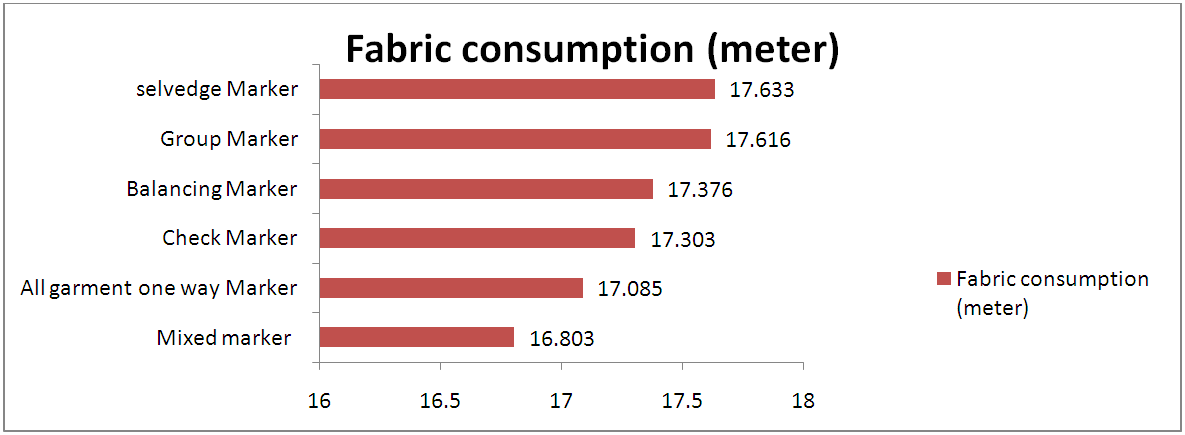 | Figure 20. Graphical representation of different types of marker consumption |
Table 7 determined the percentage of variation of other markers assuming the efficiency of mixed marker ideal, found that the efficiency variation is most when compared with selvedge marker; i.e. 4.69%. Lots of void space created in the middle of marker which remains unused. This just indicates that how much shade variation can effects marker making efficiency to a marker planner.Table 7. Marker efficiency comparison of mixed marker with others marker 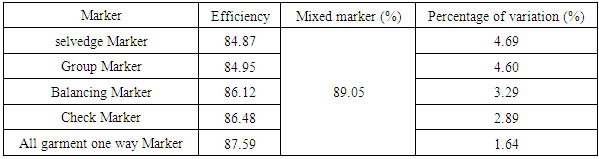 |
| |
|
On the other hand, the efficiency variation is the least in all garments one way marker. This marker is used for corduroy fabric. In this marker all size patterns are kept in same direction. Small gapes created after placing big pattern pieces are filled up by the smaller patterns of body parts. That’s why maximum use of length and width of marker, so the Marker efficiency is better compare with rest of the marker.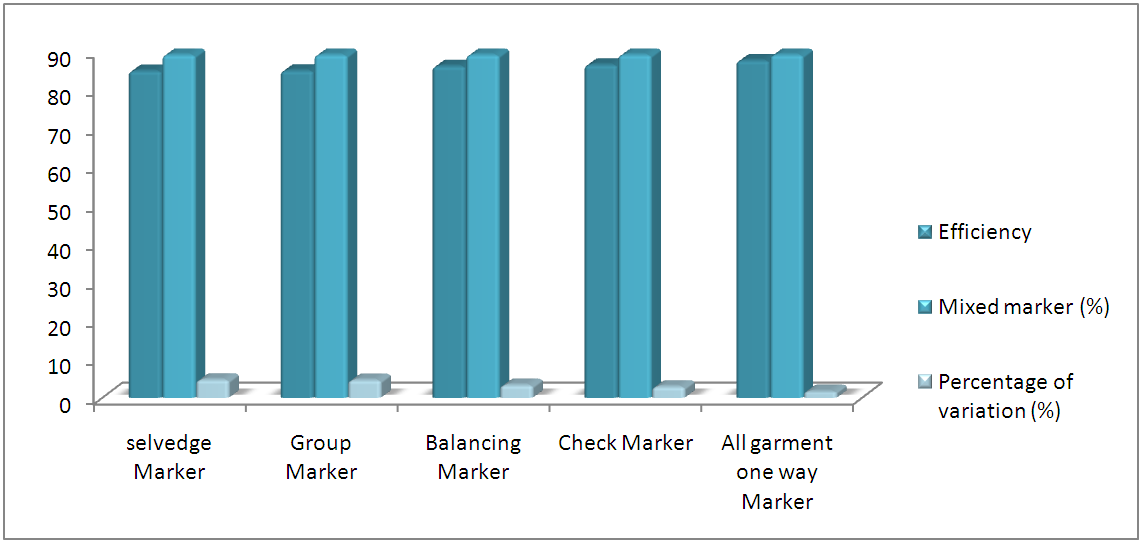 | Figure 21. Percentage of variation of mixed marker with others marker |
Table 8, determined the variation of consumption among all the markers comparing with mixed marker. Here it is found that the consumption variation between mixed marker and check marker is least. In case of check marker, the check or repeat size is 1” to 1.5”. To match that repeat along with rest of the pattern pieces marker width is best choice than marker length. So it is possible to utilize more pattern pieces on marker width rather than marker length. Thus it reduces consumption compare width with rest of the marker.Table 8. Fabric consumption comparison of mixed marker with others marker 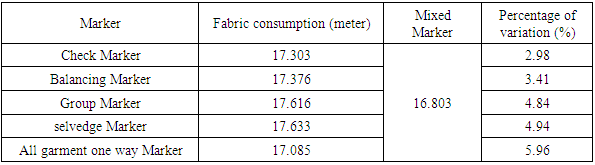 |
| |
|
Fig 22 it has been found that, the variation of consumption between mixed marker and all garments one way marker is high compare with rest of the maker which 5.96%. In all garments one way marker all pattern pieces will have to be in same direction. All garments one way marker actually done for asymmetrical or corduroy fabric. When pattern could not be laid on both directions as marker maker wish to do, there is less utilization of marker width. More spaces created between two side by side pattern pieces in marker width and more utilization of marker length. As a result fabric consumption increases as compare with mixed marker.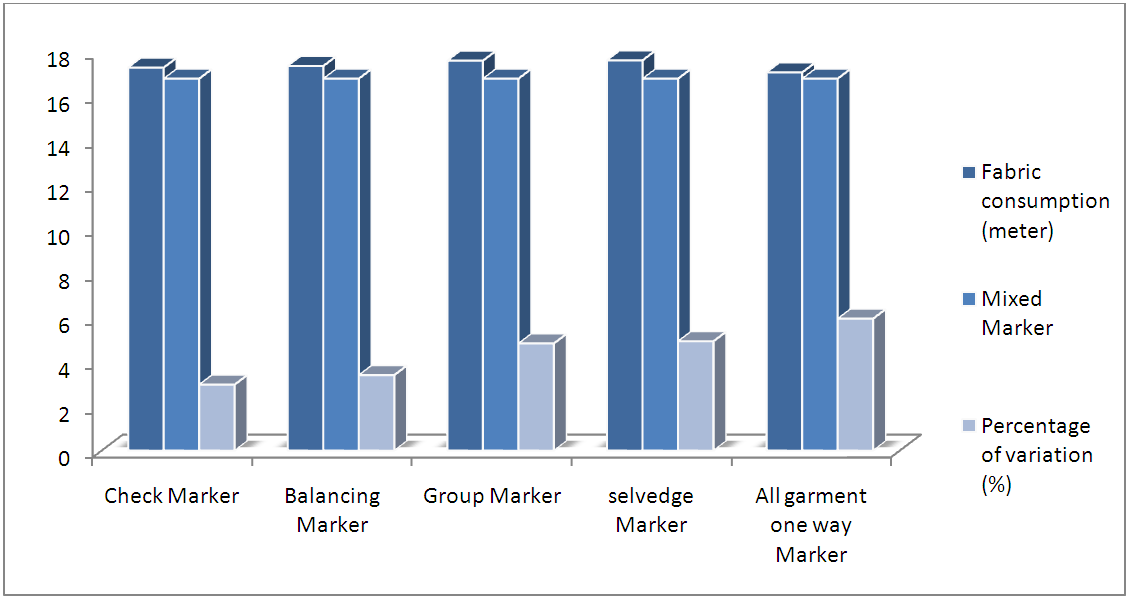 | Figure 22. Percentage of variation of mixed marker with others marker |
3.4. Relation between Marker Efficiency and Fabric Consumption
Table 9 it is found that if marker efficiency is increases then consumption is decreases. Fig 23 analyzing fabric consumption and marker efficiency data by regression analysis, it is found co-efficient of determination, R2 = 0.999.Table 9. Different types of marker with marker efficiency and fabric consumption 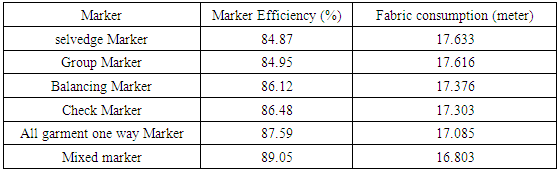 |
| |
|
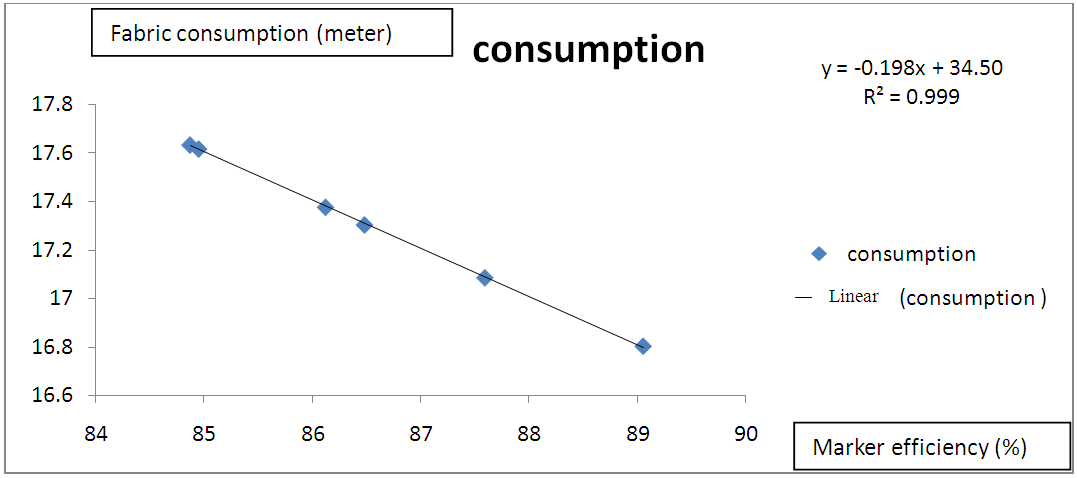 | Figure 23. Regression analysis of marker efficiency and consumption |
The resultant value of co-efficient of determination proves that there is a strong relationship between marker efficiency and fabric consumption. Relationship can be stated that the more efficient marker, more utilization of marker width rather than marker length and as result consumption of fabric also decreases.
3.5. Overall Summary of Research
Pattern grading has a direct impact on marker efficiency and fabric consumption. When a certain size of garments converted into another of size garments, large pattern pieces like front part, back part and yoke etc increases more rather than small pattern pieces. As a result marker efficiency increases and fabric consumption also increases. But for the extreme large sizes like XXL or introduction of big sizes like 3XL in ratio marker, marker efficiency decreases but fabric consumption increases. Because big pattern pieces difficult to place marker width wise and this pattern pieces will have to give the position in marker length. Between two large pieces more space are created which become unused, as a result efficiency decrease but consumption increases.Due to different reason like fabric design or shading problem factory bound to make different marker. If mixed marker is the best marker, then a percentage of variation chart for both marker efficiency and fabric consumption has been given to show how much it gives variation compare with best marker like mixed marker. In the middle of production or starting of production factory may face less of fabric or profit margin will be low because of this sorts of marker.Fabric consumption and marker efficiency got a strong relationship and which vice-versa. If marker efficiency increases, more use of pattern in marker length and width and as a result fabric consumption will be decreases which shown in regression analysis.
4. Conclusions
Marker making procedure has a direct impact on fabric consumption. For mans long sleeve shirt it has been found that mixed marker is one of the best marker for this particular style of garments. However this may vary for different style of garments. Different situation in garments industry bound marker maker to make different types of marker. This research can be frame work to garments industry to show the difference between different types of marker. This research showed situation that’s a marker maker faces during marker making procedure and how marker efficiency and fabric consumption varies for different design, repeat size and shading problem in fabric .Most of the factory may face financial losses if they dont have idea about different sorts of marker.Fabric cutting is core process to produce garments and marker making is primary requisite before fabric cutting. Proper planning and proper marker making may help them to minimize these financial losses.
ACKNOWLEDGEMENTS
This research has been done AMTRANET group factory-Export village limited which is a garments factory. Their CAD software and facilities has been used with their own interest. This research may be a guideline to the factory for further future work or development in marker making procedure.
References
[1] | Ambastha, M. (2013). Stitchdiary. Retrieved from www.stitchdiary.com: http://stitchdiary.com/wp-content/uploads/2013/07/SW_JUNE_2013-article.pdf. |
[2] | Hands, C., Heregth, H.H.A. & Hudson, P. (1997). Marker making in small clothing companies - Part 1. International Journal of Clothing Science and Technology , 9 (2), 154-165. |
[3] | Blecha, C.J., & Ria, W. (1991). THE FEASIBILITY OF IMPROVING THE MARKER MAKING PROCESS. International Journal of Clothing Science and Technology, 3 (4), 13-24. |
[4] | Choudhary & Singh, A. (2015). COST ANALYSIS IN GARMENT INDUSTRY. International Journal of Recent Advances in Multidisciplinary Research, 2 (9),703-704. |
[5] | Dumishllari, E. & Guxho, G. (2015). Impact of Marker on Cut Plan in Garment. International Journal of Innovative Research in Science, 7377-7381. |
[6] | Fralix & T, M. (2001). From mass production to mass customization. Journal of Textile and Apparel, Technology and Management, 1 (2), 1-7. |
[7] | Lim H, C. L. (2012). Automatic pattern generation process for made to measure. Journal of Textile and Apparel, Technology and Management, 7 (4), 1-11. |
[8] | Istook, C.L. (2000). RAPID PROTOTYPING IN THE TEXTILE & APPAREL INDUSTRY:A PILOT PROJECT. Journal of Textile and Apparel, Technology and Mnagement , 1 (1), 1-14. |
[9] | Yunus M., & Yamagata T. (2012). Dynamic of the garments industry in low income countries:Experience of Asia and Africa. IDE-JETRO, pp. 1-28. |
[10] | Paneru, N. (2011). Implementation of Lean Manufacturing Tools in Garment. Oulu: Oulu University of Applied Sciences. |
[11] | Puri, A. (2013). Efficacy of Pattern Making Software in Product Development. Cloud Publications, 1 (1), 21-39. |
[12] | Upendra, R., Kaluarrachchi, P., Weerasekara K & Ratnayake, VS. (2013). Developing a System to Calculate Cutting Process Time of Garments. (pp. 26-32). MORATUWA, SRI LANKA: 19th National Engineering Conference. |
[13] | Ahmad, S., Khalil, A.A.B & Rashed, C.A.A (2012). IMPACT OF EFFICIENCY IN APPAREL SUPPLY CHAIN. ASIAN JOURNAL OF NATURAL & APPLIED SCIENCES, 1 (4), 36-45. |
[14] | Stjepanovic, Z. (1995). Computer-aided processes in garment production: Features of CAD/CAM hardware. International Journal of Clothing Science and Technology, 7 (2), 81-88. |
[15] | Spahiu, T., Shehi, E & Piperi, E. (2014). Advanced CAD/CAM systems for garment design and simulation. Advanced CAD/CAM systems for garment design and simulation (pp. pp. 1-6). Tirana, ALBANIA: 6th INTERNATIONAL CONFERENCE OF TEXTILE. |
[16] | Wong, W.K., Kwong, C. K., Mok, P.Y., Ip, W.H. & Chan, C.K. (2005). Optimization of manual fabric-cutting process in apparel manufacture. Int J Adv Manuf Technol , pp. 152-158. |
[17] | Ondogan, Z., & Erdogan, C. (2006). The Comparison of the Manual and CAD Systems for Pattern Making, Grading and Marker Making Processes. FIBRES & TEXTILES in Eastern Europe, 14 (1), 62-67. |