Md. Syduzzaman1, Md. Abu Sayeed Biswas2, Dilruba Yeasmin3
1Department of Textile Engineering Management, Bangladesh University of Textiles, Tejgaon, Dhaka, Bangladesh
2Department of Industrial & Production Engineering, Bangladesh University of Textiles, Tejgaon, Dhaka, Bangladesh
3Production Merchandiser, Next sourcing (Bd.) Ltd. Dhaka, Bangladesh
Correspondence to: Md. Syduzzaman, Department of Textile Engineering Management, Bangladesh University of Textiles, Tejgaon, Dhaka, Bangladesh.
Email: |  |
Copyright © 2016 Scientific & Academic Publishing. All Rights Reserved.
This work is licensed under the Creative Commons Attribution International License (CC BY).
http://creativecommons.org/licenses/by/4.0/

Abstract
Recognition of quality management as an important factor, holds the key to competitiveness in the global market irrespective of the size of the factory. Total Quality Management (TQM) practices are primarily found in larger and multinational organizations, but little has been written on how TQM has been applied in small and medium textile industries of Bangladesh. This research reports the results of a full survey conducted among a sample of the local textile and apparel industry in Bangladesh. The survey is expected to reveal the level of TQM implementation in the industrial sector via a postal questionnaire. The survey covered 50 textile and apparel industries chosen from different industrial zone like Gazipur, Savar, Narayanganj- the prominent industrial area from Bangladesh and produced a very remarkable response rate. The survey findings are analyzed using a statistical analysis package SPSS 20.0. Various remarkable variables of TQM implementation have been thoroughly studied and discussed. Using the statistical analysis, among these variables, a TQM implementation framework has been proposed and implemented in a renowned textile industry named Knit Asia Ltd. Attempts at finding significant differences between the industries having and not having Quality system implemented were successful. It also revealed areas lacking and challenges in implementation among textile and apparel industries in Bangladesh. Bangladeshi textile and apparel sector must be able to adopt TQM to help them meet global challenges in the long run.
Keywords:
Apparel industry, TQM, Quality Tools, Framework, Productivity
Cite this paper: Md. Syduzzaman, Md. Abu Sayeed Biswas, Dilruba Yeasmin, Developing a Framework for Implementing Total Quality Management in the Apparel Industry: Case Study on a Bangladeshi Apparel Manufacturing Factory, International Journal of Textile Science, Vol. 5 No. 5, 2016, pp. 87-95. doi: 10.5923/j.textile.20160505.01.
1. Introduction
TQM refers to a management process and set of disciplines that are coordinated to ensure that the organization consistently meets and exceeds customer requirements. TQM engages all divisions, departments and levels of the organization. TQM companies are focused on the systematic management of data in all processes and practices to eliminate waste and pursue continuous improvement. The goal is to deliver the highest value for the customer at the lowest cost while achieving sustained profit and economic stability for the company [2]. All types of manufacturing industries have reduced costs, increased process efficiency and improved the quality of their products and services by working to meet the needs of the people they serve through the application of total quality management (TQM) principles. With growing global competition, quality management is becoming increasingly important to the leadership and management of manufacturing industries. Quality management principles provide understanding of and guidance on the application of quality management. By applying following quality management principles, organizations will produce benefits for customers, owners, employees, suppliers and society as a whole. Companies actually compete on three major issues; Quality, Price and Delivery. If the choice is to compete in the marketplace on the basis of product or service price, then the level of competition is clearly defined; the low-cost provider wins. However, companies choosing the low cost approach may find themselves losing premium business to competitors while retaining the low-margin business in the long term [3]. Many companies understand that TQM is necessary for them to remain competitive, retaining their market share and to be able to respond to changing 2 competitive demands in to days business world. Based on some studies, not all companies are able to implement TQM successfully. This is because it requires a different implementation approach to cater for the varying needs of the industries in order for effective implementation. Small and medium sized enterprises (SMEs), for example, have been slow in adopting TQM when compared to large companies. Their involvement has focused primarily on ISO 9000 certification, and very few had advanced beyond that [4]. Therefore, the identification of Critical aspects of successful implementation as well as the problems faced by apparel manufacturing industries in implementing TQM is an important area to be understood. The value of this research is one of the primary steps towards reaching the needs of the Bangladeshi RMG sector that are trying to implement TQM in their business. With a better understanding of these issues, it can be a nice groundwork for the development of an appropriate TQM framework for practical implementation of the RMG sector.
2. Literature Review
2.1. Definitions of Quality
The simple definition of quality is meeting the customer requirements. Moreover, and aiming at increasing customers’ satisfaction, many organizations have focused on quality and reduced their costs to gain maximum customer satisfaction, examples of this being Toyota in Japan, Samsung in South Korea. Besides, the term quality has been defined by so many quality experts. Quality refers to the different workmanship of various activities. Consequently, each business or activity has a different definition of quality, for example in sales the term quality is more focused on the services which are provided to the customer, while in manufacture, the term quality is more focused on the production process, and in Apparel Manufacturing, quality refers to both of services provided and output products [5].Quality is "The totality of features and characteristics of a product or service that bears on its ability to satisfy stated or implied needs" [6]. So, most of the quality concepts which mentioned above focuses on providing a product that satisfies and meet the customers’ needs. Quality is therefore extremely necessary for the organizations to ensure that they have delivered their products or services according to the customer expectations and requirements.
2.2. Definitions of Total Quality Management
Numerous definitions have been given on Total Quality Management (TQM) by quality gurus, practitioners and academician. Besterfield defined TQM as both a philosophy and a set of guiding principles that represents the foundation of a continuously improving organization. It integrates fundamental management techniques, existing improvement efforts and technical tools under a disciplined approach [7]. Using a three-word definition, Wilkinson and Wither defines TQM as below-Total: every person is involved (its customers and suppliers)Quality: customer requirements are met exactlyManagement : senior executives are fully committed [8].Berry defined TQM process as a total corporate focus on meeting and exceeding customer’s expectations and significantly reducing costs resulting from poor quality by adopting a new management system and corporate culture [9]. In this context, TQM has emerged as a holistic management model because the concept of TQM is much broader than the traditional quality concepts. It encompasses not only product, service and process improvement, but those relating to costs and productivity and to people involvement and development [10]. TQM has been arguably the most significant approach to the management of organizations and their operations and its improvement and has provided many tools and techniques [11-14].Much research has been conducted about TQM. However, it is evident from the literature that different researchers have adopted different definitions and frameworks based on the context of the application or the theme of the research.
2.3. Quality Tools & Techniques
Chan said ' You cannot manage what you cannot measure' [15]. Consequently, there is a need to establish a process for measurement of quality management system performance, aiming at monitoring data on current and end user customer satisfaction for all essential processes. Therefore the organization needs to establish a sufficient and workable process. TQM tools are technical means used to work in the quality programs, and often include diagrams, statistical graphs, also, used to improve processes or develop products in any organization by identifying, analyzing and evaluating data that is relevant to their business. Therefore, by using the tools and techniques, one can investigate problems, identify solutions and implement them in work practices, by measuring and analyzing the outcome.The seven quality control tools described by Ishikawa are usually perceived as too simplistic and not appropriate [16]. In a study conducted by Scheuermann L. et al., the tools classified as Qualitative tools include flow charts, cause-and-effect diagrams, multi-voting, affinity diagram, process action teams, brainstorming, election grids, and task list), whereas Quantitative tools include Shewaryt cycle (PDCA), Pareto charts, control chart, histogram, run chart, and sampling [17]. TQM tools are practical methods, skills, means or mechanisms that can be applied to particular tasks. A technique has a wider application, often resulting in the need for more thought, skill and training to be used effectively, such as SPC, benchmarking, quality function deployment [18]. The most popular sets of TQM tools are as below- Pareto Principle: Identifying the key problems Control Charts: Variation Control Cause and Effects, Fishbone, Ishikawa Diagram Histogram or Bar Graph Traffic Light System 5S Quality Function Deployment Failure Mode & Effect Analysis.
3. Methodology
This research has been accomplished following the methodology illustrated below- Detailed literature review of TQM that requires a general understanding of TQM; Define the objectives & scope of the research; Gather data from industry by using a questionnaire formed by the researcher; Data analysis using SPSS-20 version; Propose a TQM model; Case study to ensure the feasibility of the model.
3.1. Research Resources and Tools
Various research resources and tools were employed in this research to collect the required data and these resources are:v Factory documents and statistics related to the research objectives.v Literatures and researches related to the research questionsv Interviews with employees of Apparel Manufacturing industry in Bangladeshv Questionnaire to collect data and information necessary for research study, statistical analysis, and get results.v Internet search
3.2. Preparing the Questionnaire and Data Collection
In order to facilitate data collection, the survey method was used. Towards that end, a questionnaire was developed. A lot of preparation goes into a survey. First, the questions must be tailored in such a way that encompasses the scope and objectives of the research. For this research, the survey is designed to investigate level of implementation of TQM in Bangladeshi Apparel industry. The questionnaire was structured and based on an extensive literature review of international and local surveys of quality management and integration of all the best theories articulated by the quality gurus.The survey is conducted using both postal questionnaire survey and physical survey. A postal questionnaire survey is generally cheaper than other methods. Such a questionnaire can be helpful in gathering large amounts of data from a sample of a given population and therefore be used to test research hypotheses [19]. And for physical survey researcher has visited the factories and discussed the questionnaire & relevant issues with the top management especially with quality managers. The questionnaire was designed in a simple table format and a five-point Likert scale was employed for scoring responses.1 = strongly disagree2 = disagree3 = neither disagree nor agree 4 = agree and 5 = strongly agree, that requires the respondent to tick their answer in the appropriate scales so as to save time when answering the questions. Additionally, 9 was also included in the scale as an added option indicating the respondent had “don’t know” or the item was not applicable to their respective factory.Basically, the questionnaire is divided into 2 main parts. Part-A keeps track on the general information of responding industry. In this section, the background aspects of the respondent, such as number of employees, types of industry involves by respondent industry, quality system certification and years of involvement will be obtained. In part-B, its attempted to check the degree of Total Quality Management practices on 10 key quality factors of the factory, which derived mainly from literature. A total of 51 statements are provided to be answered by the respondent industry. The questionnaire has been constructed based on some prominent variables for TQM like as below-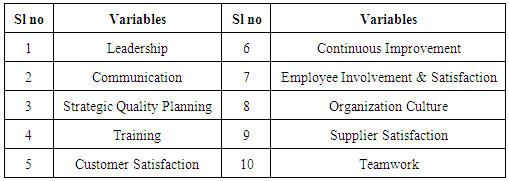
3.3. Data Analysis
Data analysis is “the process of bringing order, structure and meaning to the mass of collected data” [20]. The data obtained from the completed questionnaires has been presented and analyzed by means of various analyses- descriptive and inferential as it comes applicable. The data has been analyzed by using SPSS software (20.0 Version). Various types of statistical analyses have been done in this research but more emphasis has been given on reliability & factor analysis. Here in this research firstly factor analyzed for each variable with 5 or 6 questions which are considered factor for each variable. Then one factor or one question per each variable has been extracted. Finally 10 factors or questions have been found which significantly describe each variable and factor analysis has been conducted among these 10 factors or variable. Based on these factors/variables found after factor analysis, a new framework has been formed based on their significance.
4. The Construction of the TQM Framework
In Bangladesh Apparel industry, there is no well defined and specific TQM implementing frameworks based on which a new framework might be formed. But to form this new framework, researcher had to do dremendous literature review and performed an industrial survey. Then data found from the survey, has been analysed using statistical tools to form the framework. The researcher has formed the model or framework mainly based on the result from data analysis and with the help & guidance of industry experts. Factor analysis has been done on the data of TQM variables (mentioned earlier) and variables have been extracted as per priority to form the model.From the above factor analysis table and scree plot, it is clear that only 4 variables have eigenvalue value more than 1 which is indicating the more significant value and 1st four scales contain almost 60% variance which is good for this study. From the analysis the researcher chose 1st four scales or variables as most significant according to eigenvalue. The newly formed framework for implementing TQM in Apparel industry, has been presented as below- Table 1. Significant factor extraction among ten variables 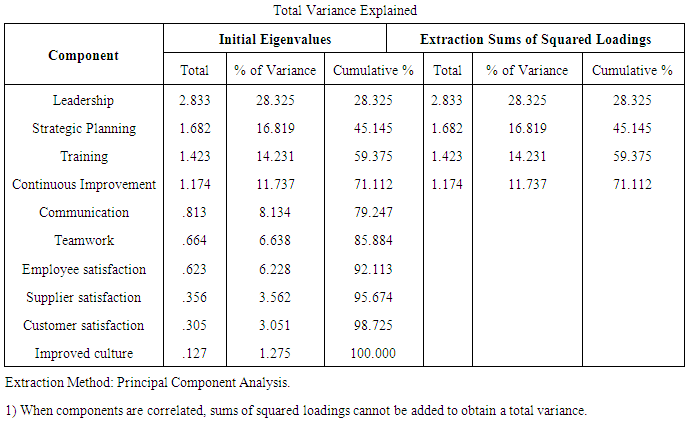 |
| |
|
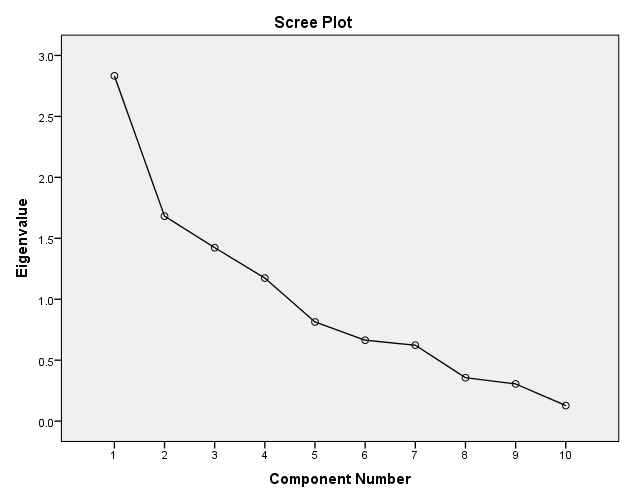 | Figure 1. Scree plot for Significant factor extraction among ten variables |
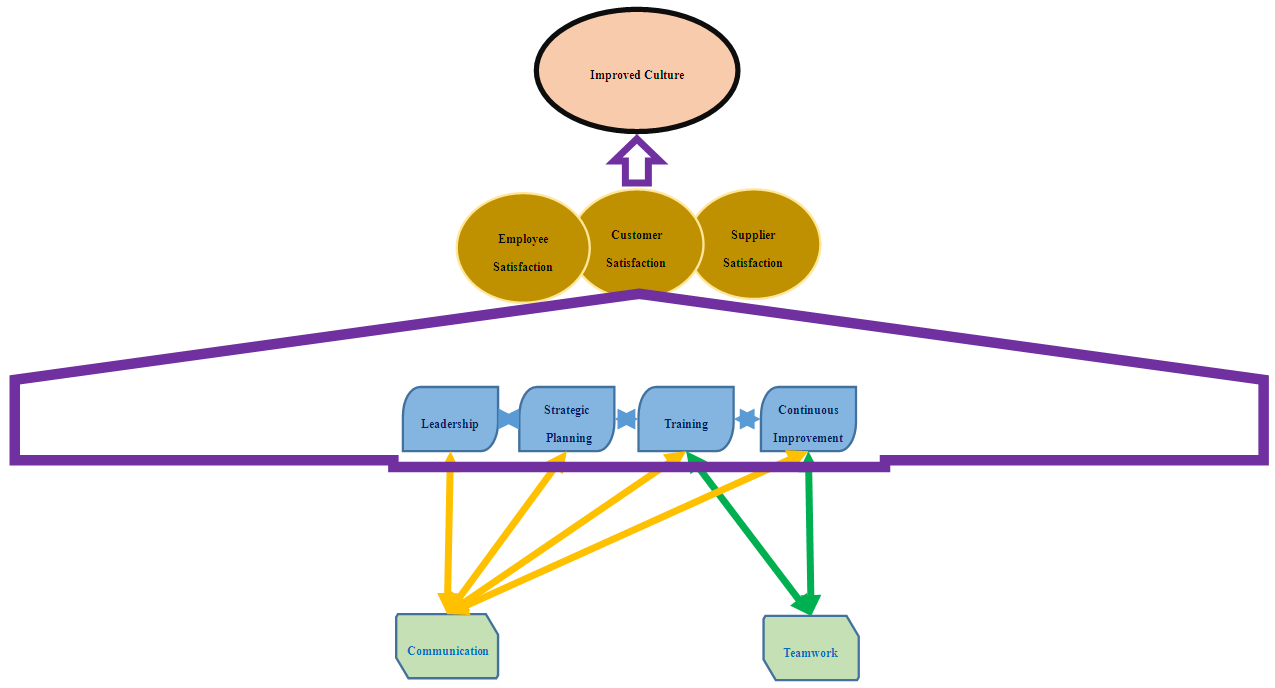 | Figure 2. Proposed framework for implementing TQM in Apparel industry |
The framework of TQM consists of the 10 elements of TQM, where four elements are the main targets in this study. This framework was based on the hypothesis that TQM implementation has effects on employee satisfaction, supplier satisfaction, customer satisfaction, and strategic quality planning. These hypotheses were confirmed by the questionnaire survey data from 50 factories and could coin to a decision, Leadership, Strategic Quality Planning, Training and Continuous Improvement are the most important elements among the 10 TQM elements. From the Framework of TQM, we got the main four phases.
To implement the proposed framework at first we have to implement these four phases which will be ensured the total implementation process.
5. Case Study
As a major part of the research methodology, a case study has been conducted at a very well-known textile factory named Knit Asia Ltd, Bangladesh. The researcher has implemented a proposed framework in this factory. The major aim of the case study was to provide a practical example of how to use the TQM implementation model in practice and to show the effectiveness of TQM application. The framework which has been implemented is as below-6. Result and discussion: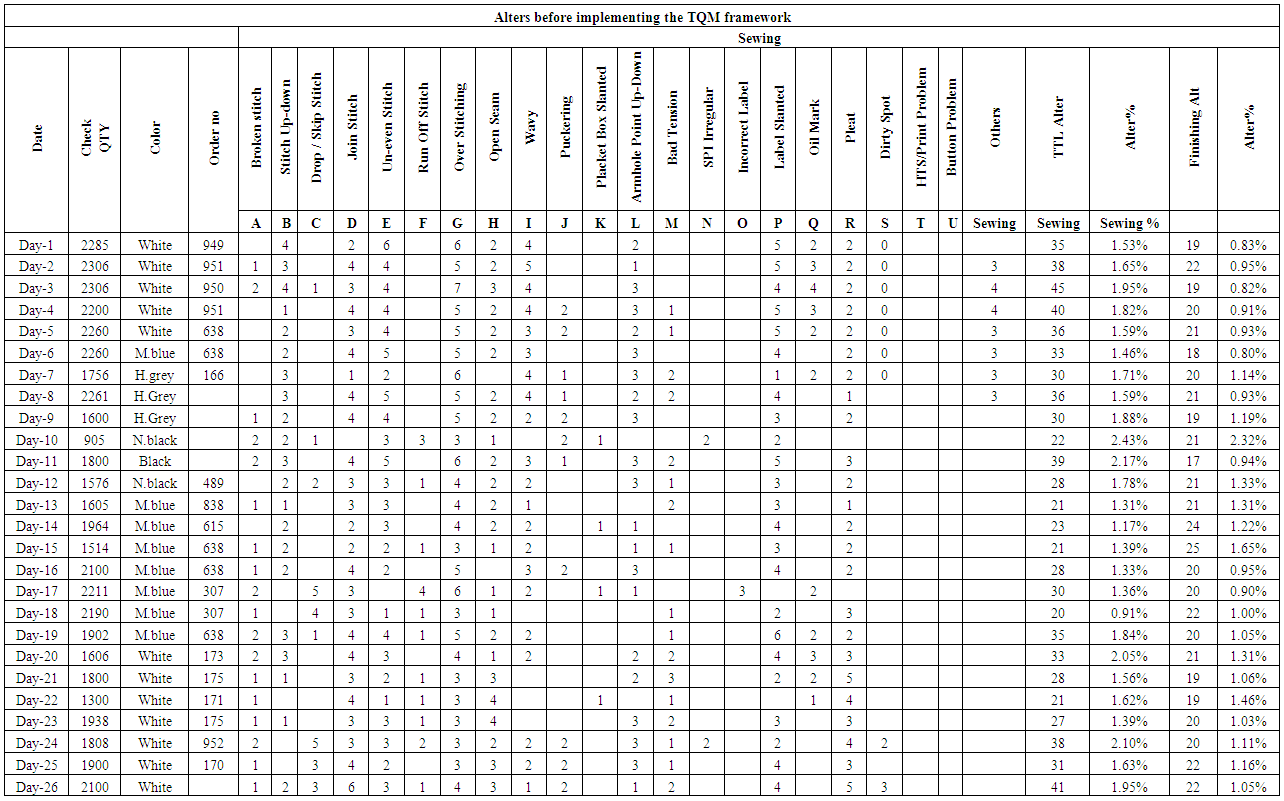 | Table 2. Statistics showing alters or reworks% before TQM implementation |
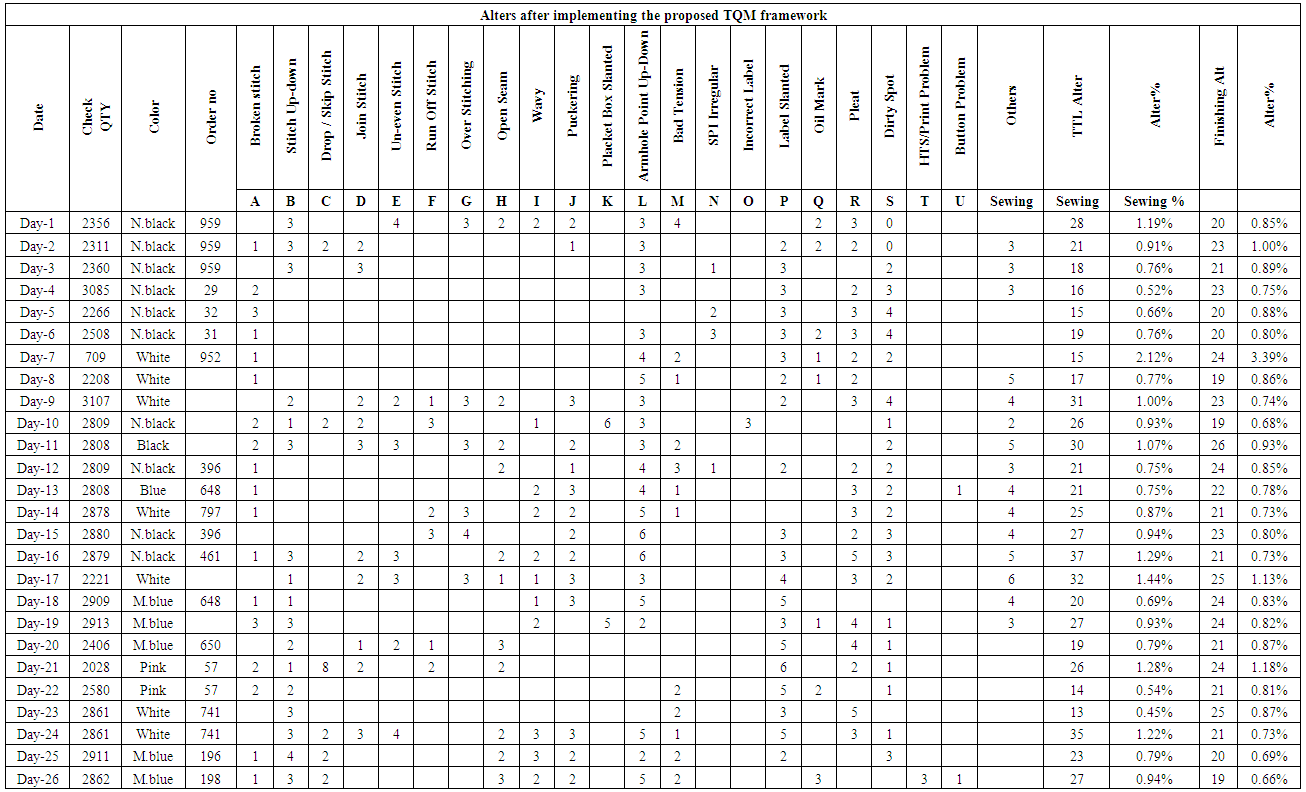 | Table 3. Statistics showing alter or reworks% after TQM implementation |
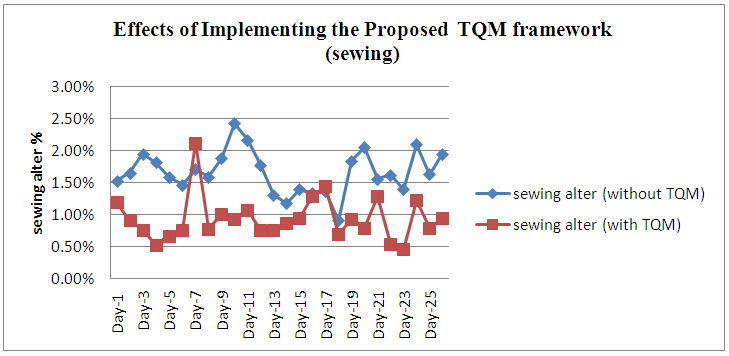 | Figure 3. Comparison of sewing Alter & reject% with & without implementing TQM |
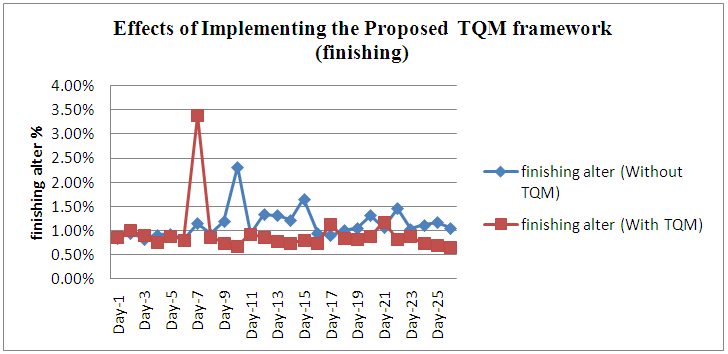 | Figure 4. Comparison of finishing Alter & reject% with & without implementing TQM |
Table 4. Comparative statistics of before and after TQM implementation 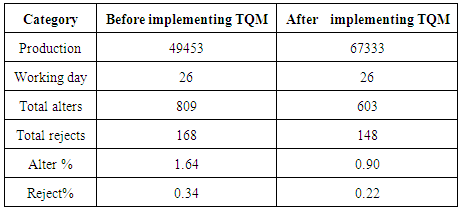 |
| |
|
In apparel manufacturing processes, especially in sewing there are so many faults or alters may occur. Some are repairable alters and some are not (non-repairable) which are unavoidable, but may be reduced in quantity but cannot be removed. To find out the benefits or advantages of implementing the proposed TQM framework, the two experiments have been carried out simultaneously considering so many limitations. Here two sewing floors have been taken into considerations for the experiments. One has been considered “before implementing the proposed TQM framework” that is their ongoing floor and another followed the TQM principles has been considered as “after implementing the proposed TQM framework”. Then both the floors have been observed regularly for about a month: how is the production, how much faults are occurring and what about the status of alters or reworks, etc. From the data mentioned above, it’s been found that production has been improved as total alters and rejections have been considerably reduced after implementing the proposed TQM framework.
6. Conclusions
The ever increasing competitions in the field of product and services, have resulted in the development of frameworks. Nevertheless, the purpose of these frameworks or other term, life cycle models should be to develop quality product. With intense competition and quality being at the forefront of the products and service, more and more revenue generating processes (or profitability elements) are being linked to an organized structure that an organization cannot afford to ignore to keep a leading position in the market. The Customer is never interested in the complex development details of quality. What the customer demands is a quality product and service as an end user. Quality is what the customer needs. Even a little deviation from the customer demands can lead to the poor quality of design. So its very much burning issue that how to ensure industrial quality production. That’s why, researcher has put a tremendous effort to develop a well defined structure or framework for implementing quality tools particularly implementing TQM in the Apparel industry. And finally, the researcher has developed a framework and its been proved successful after conducting a case study in a renowned textile plant.
References
[1] | http://www.dhakatribune.com/long-form/2014/sep/19/rmg-industry-bangladesh-past-present-and-future. |
[2] | Nicoleta Isac , “PRINCIPLES OF TQM IN AUTOMOTIVE INDUSTRY”, Romanian Economic and Business Review, Vol. 5, No. 4 pp187. |
[3] | Tang, Victor & Bauer Roy, (1995) Beyond strategic advantage & TQM, Competitive Dominance: New York, Van Nostrand Reinhold. |
[4] | Yusof, S.M. & Aspinwall, E.M. (2000) Critical Success factors in Small and Medium Enterprises survey results, Total Quality Management, Vol 11, pp. 448- 462. |
[5] | R. Fukui, Y. Honda, H. Inoue, N. Kaneko, I. Miyauchi, S. Soriano and Y. Yagi, (1995). "TQM and QCC Handbook, A Guide for Managers" (Vol. 1). Japan. |
[6] | BS4778. (1987). "Quality Vocabulary" (Vol. 1). London: British Standards Institu-tion. |
[7] | D.H. Besterfield, (1995). Total Quality Management, New Jersey, Prentice Hall Inc. |
[8] | K.M.Ho, Samuel (1999) Change for the better via ISO 9000 and TQM, Manage-ment Decision 37/4, MCB University Press, pp. 381-385. |
[9] | Yusof, S. R. M., & Aspinwall, E. (1999). Critical success factors for total quality management implementation in small and medium enterprises. Total Quality Management, 10(4-5), 803-809. |
[10] | Dale, B.G., A. Van der Wiele V. and J.D. van Iwaarden (2007) Managing Quality. (5th edition): Blackwell Publisher, Oxford. |
[11] | Capon, N., Kaye, M. & Wood, M. (1995) "Measuring the success of a TQM pro-gramme", International Journal of Quality & Reliability Management, vol. 12, no. 8, pp. 8-22. |
[12] | Curkovic, S., Vickery, S. & Dröge, C. (2000) "Quality‐related Action Programs: Their Impact on Quality Performance and Firm Performance", Decision Sciences, vol. 31, no. 4, pp. 885-902. |
[13] | Dean Jr, J.W. & Bowen, D.E. (1994) "Management theory and total quality: improv-ing research and practice through theory development", Academy of management re-view, pp. 392-418. |
[14] | Evans, J. R., and Lindsay, W.M. (2001). "The Management and Control of Quality" (5th ed.). New York: West Publishing. |
[15] | Chan, F. T. (2003). Performance measurement in a supply chain. The international journal of advanced manufacturing technology, 21(7), 534-548. |
[16] | Bamford, D. R., & Greatbanks, R. W. (2005). The use of quality management tools and techniques: a study of application in everyday situations. International Journal of Quality & Reliability Management, 22(4), 376-392. |
[17] | Scheuermann, L., Zhu, Z., & Scheuermann, S. B. (1997). TQM success efforts: use more quantitative or qualitative tools?. Industrial Management & Data Systems, 97(7), 264-270. |
[18] | McQuater, R. E., Scurr, C. H., Dale, B. G., & Hillman, P. G. (1995). Using quality tools and techniques successfully. The TQM Magazine, 7(6), 37-42. |
[19] | Mandal, P., Shah, K., Love, P. E. D., & Li, H. (1999). The diffusion of quality in Australian manufacturing. International Journal of Quality & Reliability Management, 16(6), 575-590. |
[20] | De Vos, A. S. (2002). Scientific theory and professional research. in de Vos. |