Md. Kamruzzaman1, Md. Eman Talukder1, Manikandan N2, Md. Forhad Hossain1, Asaduzzaman1, Muhammad Usman3
1School of Textile Chemistry & Chemical Engineering Wuhan Textile University, Hubei, China
2School of Textile Science & Engineering, Wuhan Textile University, Wuhan, Hubei, China
3School of Management, Wuhan Textile University, Wuhan, Hubei, China
Correspondence to: Md. Eman Talukder, School of Textile Chemistry & Chemical Engineering Wuhan Textile University, Hubei, China.
Email: |  |
Copyright © 2016 Scientific & Academic Publishing. All Rights Reserved.
This work is licensed under the Creative Commons Attribution International License (CC BY).
http://creativecommons.org/licenses/by/4.0/

Abstract
In cotton woven and knit fabric resin finishing was not only applied to protect from crease trait but also makes it cleaned care durable press material. The finishing process was acquired thru forming go hyperlinks between adjacent cellulose polymer chains and the linking agent was the fundamental requirement for this cause. In this study prime crosslinking agent was DMDHEU ((Dimethylol Dihydroxy Ethylene Urea) that acts with magnesium chloride to make crosslink in the amorphous regions of the fiber structure. To imitate the reaction magnesium chloride plays the roles of the acid catalyst with the resource of trial mistakes approach, we've obtained the positive concentration of the cross-linking agent. The very best exceptional recipes were located to be 60g/L concentration of cross-linking agent, 20g/L catalyst for easy care and 100g/L concentration of cross-linking agent, 30g/L catalyst for a non-iron finish at 170°C curing temp. Those recipes were used for resin finishing with the aid of way of pad – dry - remedy method. Physical & chemical properties of each woven and knit fabric such as tensile strength ,bursting strength, crease recovery angle, DP rating, formaldehyde content was investigated through testing and analysis. It is recommended that resin finishing with the most advantageous concentration of DMDHEU offers higher crease resistance and crease healing property.
Keywords:
DMDHEU, Concentration of the cross linking agent, Pad-Dry-Cure technique, DP rating, Crease recovery angle
Cite this paper: Md. Kamruzzaman, Md. Eman Talukder, Manikandan N, Md. Forhad Hossain, Asaduzzaman, Muhammad Usman, Optimum Concentration of Cross-Linking Agent for Crease-Resistant Finishing Using DMDHEU on Knit and Woven Fabric in the Field of Ease Care Durable Press, International Journal of Textile Science, Vol. 5 No. 4, 2016, pp. 74-81. doi: 10.5923/j.textile.20160504.02.
1. Introduction
Finishing is generally the last stage of modern textile production. Its aim is to transform the bleached, dyed or published material by way of mechanical and chemical remedy into a suitable state on the market and making up. There are 3 styles of finishing manner mechanical, chemical and non-everlasting each of which commonly included the non-stop remedy of woven and knitted fabrics in open width form. The most essential thing is chemical finishing also called resin finishing, clean care finishing or wash - put on completing. Resin finishing has been capable of hold its function inside the completing of textiles based on cellulosic fibers not withstanding some un favorable conditions which include energy losses, shade modifications, decreased whiteness and controversy approximately formaldehyde content material [1].Cellulose fibers are made of molecule chains shaped by means of masses of heaps of glucose companies [2]. The molecular chains of cellulose in part include crystalline regions rigidly orientated and compact, and partially of amorphous, free and random-orientated layers; small covalence forces or electrostatic bonds purpose their concord. By means of drawing the molecular chains, a stretching effect is taken place due to the breaking of weak bonds and to the subsequent sliding of the unmarried chains over every other, a phenomenon which become irreversible on every occasion the molecular chains (and consequently the cellulose fibers count on a new position. If supposed to transfer the drawing pressure and therefore the stretching of the external bending of a positive factor inside the fiber subjected to creasing, the bending perspective is counted on a permanent role on account of the irreversibility of the phenomenon, therefore turning into an everlasting crease. above all, cellulose fibers wealthy in amorphous regions and macromolecules, which generally tend to form bonds within the new positions imparted by mechanical stresses, could be laid low with these deformation phenomena along with stretching, creasing and wrinkling [3].Cellulose move-linking entrepreneurs should meet a number of stringent necessities to be considered for realistic is use to increase proof or durable Press (DP) completing. Crease properties actually depend on hydrogen bond of cellulose molecule that makes cellulose crease proof. To impart crease resistance end to the cotton cloth, the hydrogen bond formation of the hydroxyl corporations is needed to be either masked or definitely removed. The maximum crucial cotton etherification treatments are people who produce wrinkle resistance in fabrics [4]. Cross-linking produces resiliency inside the fiber to offer the needed dimensional stabilization, wrinkle resistance, and crease retention for current durable- press cellulosic fabric. move-hyperlinks primarily based on etherification reactions historically had been used due to their sturdiness to repeated laundering and put on The chemical name of this reagent is 1,3-bis(hydroxymethyl)-4,five-dihydroxy-imidazolidinone- 2 but it also is included referred to as DMDHEU or the glyoxal reactant as it is ready from glyoxal, urea, and formaldehyde [5]. DMDHEU blended with magnesium chloride as the acid catalyst, to improve the formation of go-linking bonds among the molecules of cellulose chains. The development of those bonds in the amorphous areas of the fiber, have improved the resistance to distortion and is enhanced elasticity properties [3]. Our research ambition is to optimize the high concentration of crease-resistant finishing agent DMDHEU and other finishing properties like tensile strength, bursting strength, DP rating, crease recovery angle.
2. Materials and Methods
2.1. Materials
Undyed white and dyed (blue, pink) cotton as a woven fabric, ash, orange and green as a knit fabric. 150 -160 are the GSM range.Chemicals: Fixapret Resin CL (dihydroxy methyl - four, 5 – di hydroxyethyleneurea), Fixapret catalyst F-M, Perapret Additive PEP, Siligen Softener SIE, Kieralon Wash XC- J concentration, Reactive dye (Red, Yellow, Blue and Turquoise).
2.2. Methods
The pretreated and dried fabric has exceeded in a solution containing resin, catalyst, softener and wetting agent. The padding pressure has maintained at 1.5 bars. The padded material is dried at 120°C for 2 min and the curing procedure has executed at 170°C for 45 sec. Then the fabric has washed and tumble dried.
2.2.1. Optimization of Concentration for DMDHEU
For various trial was made on cotton fabric using different concentration of DMDHEU at 20 g/L, 40 g/L, 60 g/L, 80 g/L, 100 g/L, 120 g/L respectively along with catalyst (20 g/L), curing temp (170°C) and time 45sec.
2.2.2. Determination of Physical and Chemical Properties of Treated and Untreated Woven, Knit Fabrics
Durable press score was measured thru AATC smoothness appearance rating. was used to measure the tensile energy become determined via Vertical energy tester .James H. HEAL to measure the bursting energy; crease recuperation attitude evaluated by Shirley crease recuperation attitude; formaldehyde was measured by using the spectrophotometer.
2.2.3. Determination of Fastness
Wash fastness turned into evaluated in line with ISO 105 C03,Water fastness become decided through ISO a hundred and five E01 in line with ISO a hundred and five E04 Perspiration fastness changed into investigated. Rubbing fastness was determined in line with ISO one zero five-X12 technique.
3. Result and Analysis
3.1. Optimization of Concentration for DMDHEU
It’s far clean from the Figure 1 that resin finish with lower concentration offers a low level of DP score and better concentration offers an excessive degree of DP score. However, DP rating of 2.5 and above is considered for clean care and DP rating of 3.5 above is taken into consideration for the non-iron end. We have permitted 60g/L & 100g/L concentration of cross-linker for easy care and non-iron end respectively.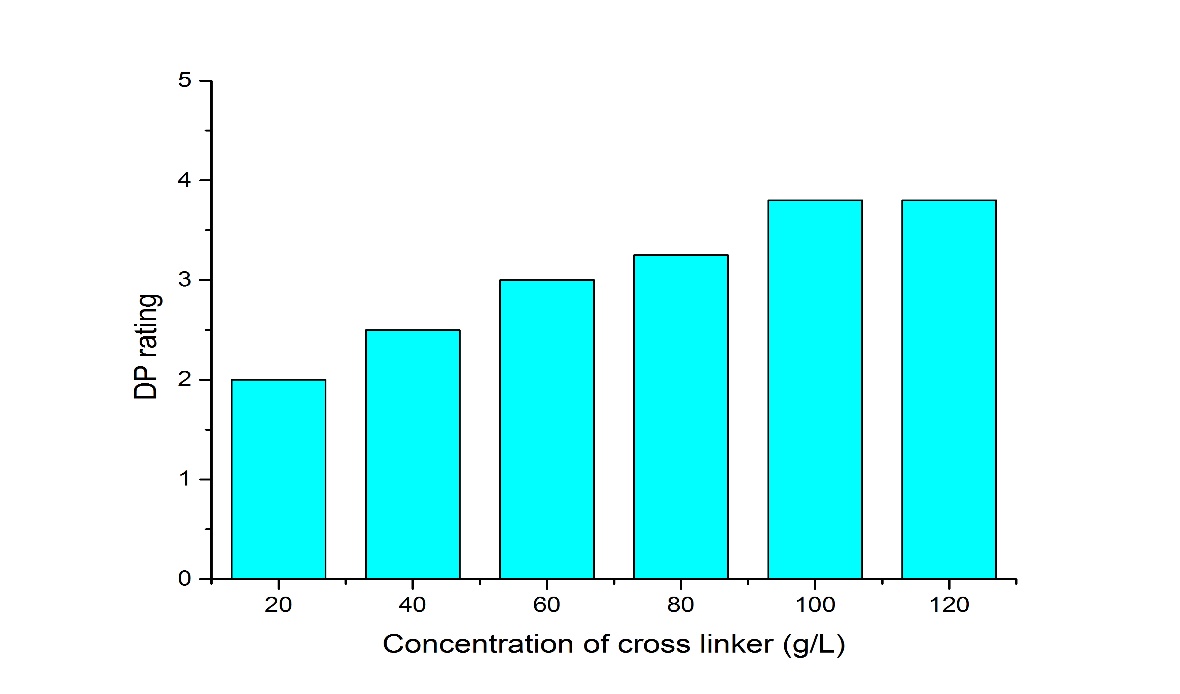 | Figure 1. Relationship between cross-linker and DP rating |
Figure 2 suggests that tensile electricity falls down with the growth of resin concentration but 30 to forty five% lack of tensile power must be taken into account. From the desk we have discovered that percentage lack of tensile electricity exceeds to fifty-one. 88% for 100g/L resin concentration but we've considered it as non-iron end due to the fact DP score for 100g/L resin concentration was set 3.8.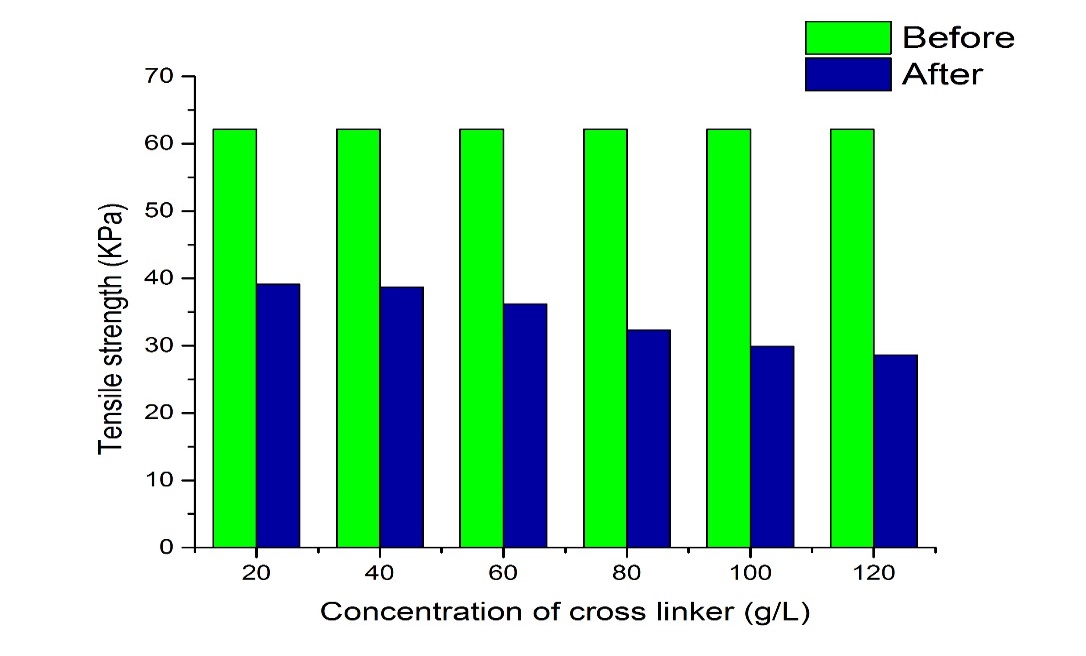 | Figure 2. Tensile strength in dependence on the cross-linker concentration at a curing temp 170°C and time of 45sec |
There was a significant effect on crease recuperation angle of fabrics finished with pass-linker concentration Crease restoration angle is increased with the boom of cross-linker concentration according to Figure 3. It is meant that cloth becomes stiffer.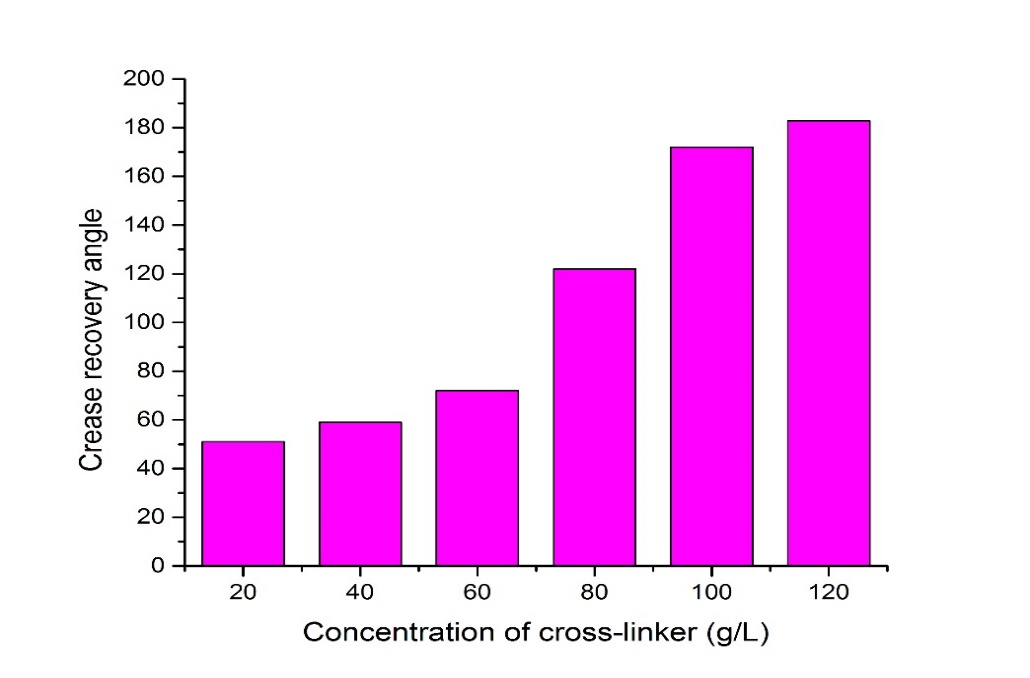 | Figure 3. Crease recovery angle in dependence on the cross-linker concentration at a curing temp 170°C and time of 45sec |
Optimizing the recipe after considering DP score, tensile strength, and crease restoration attitude with respect with concentration: 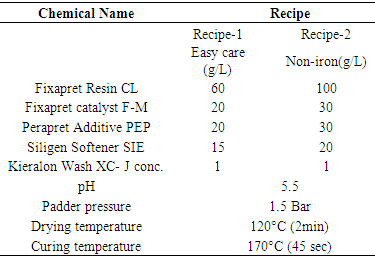
3.2. Determination of Physical and Chemical Properties of Treated and Untreated Woven, Knit Fabrics
Physical and chemical homes of untreated and dealt with woven fabric the usage of unique recipes. Recipe-1 for 60 g/L and recipe – 2 for 100 g/L concentration of cross linking agent.Value of DP rating was investigated from Figure 4. According to this it was transparent that DP of resin treated woven was comparatively higher than untreated woven fabric. However recipe-2 DP was greater than recipe-1 DP when made a comparison upon different condition.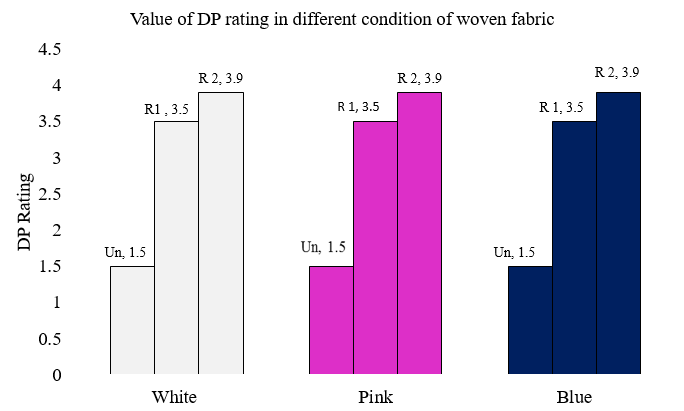 | Figure 4. Value of DP rating in different condition of woven fabric |
In keeping with analysis of tensile energy of various colored woven fabric from Figure 5, it changed into apparent that tensile energy of resin handled woven became relatively much less than untreated woven material. However, recipe-2 show lower tensile strength when as compared with recipe-1 tensile electricity in unique degree.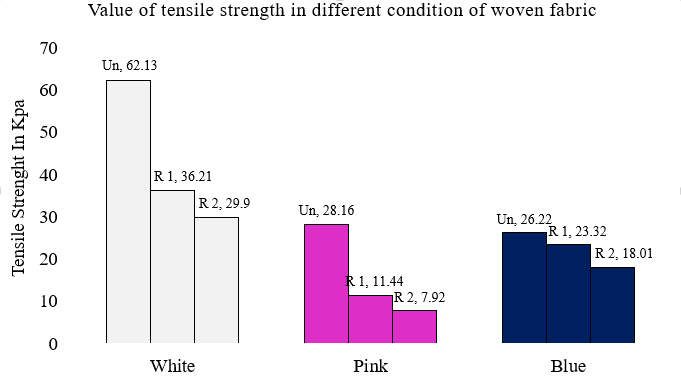 | Figure 5. Value of tensile strength in different condition of woven fabric (white, pink, blue fabric) |
The price of crease recovery angle turned into investigated from Figure 6. In step with this, it became transparent that crease recovery attitude of resin treated woven changed into comparatively better than untreated woven fabric. However, recipe-2 crease recuperation attitude become extra than recipe-1 crease recuperation perspective when made a contrast upon a different situation.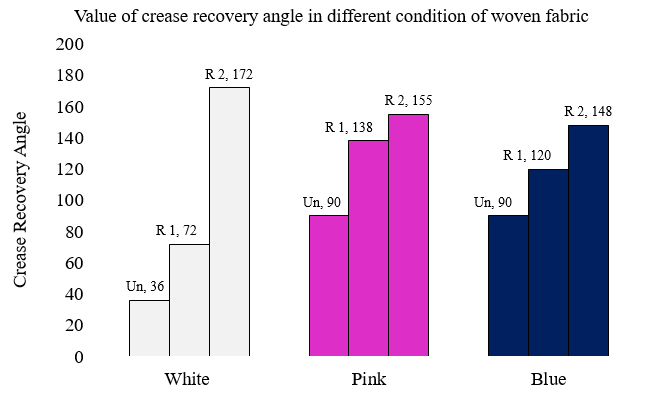 | Figure 6. Value of crease recovery angle in different condition of woven fabric (white, pink, blue fabric) |
A fee of formaldehyde became investigated from Figure 7. In keeping with this it is come to be transparent that formaldehyde attitude of resin dealt with woven changed into comparatively higher than untreated woven cloth. However, recipe-2 formaldehyde attitude turn out to be more than recipe-1 formaldehyde angle while made an assessment upon a different situation like white and blue colored. In contrast recipe-1 gives better formaldehyde content while made the assessment with recipe-2 for crimson colored fabric. Physical and chemical homes of untreated and dealt with knit fabric the usage of unique recipes. Recipe – 1 for 60 g/L and recipe – 2 for 100 g/L concentration of cross linking agent.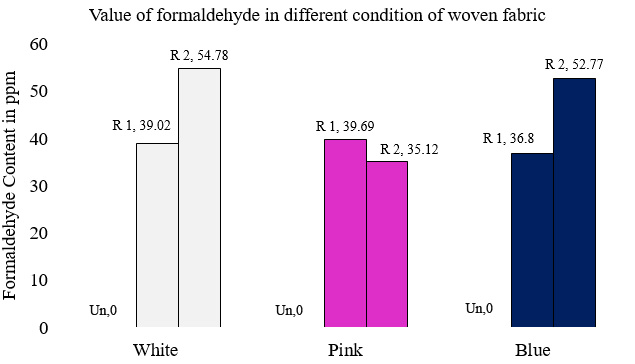 | Figure 7. Value of formaldehyde in different condition of woven fabric (white, pink, blue fabric) |
In line with evaluation of bursting power of diverse colored knit fabric from Figure 8, it modified into apparent that bursting power of resin handled knit have become fantastically a whole lot less than untreated knit fabric. However, recipe-2 display decreases bursting electricity while as compared with recipe-1 bursting electricity in precise degree for orange and green material .In comparison recipe-1 bursting power turned into better than recipe-2 bursting electricity in keeping with ash colored fabric.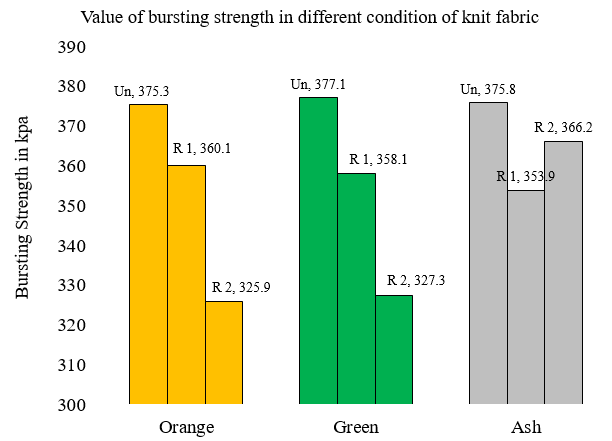 | Figure 8. Value of bursting strength in different condition of knit fabric (orange, green, ash color fabric) |
A fee of formaldehyde became investigated from Figure 9 according to this, it become transparent that formaldehyde of resin treated knit turned into comparatively better than untreated knit material. However, recipe-2 formaldehyde become greater than recipe-1 formaldehyde while made an evaluation upon one of a kind situation.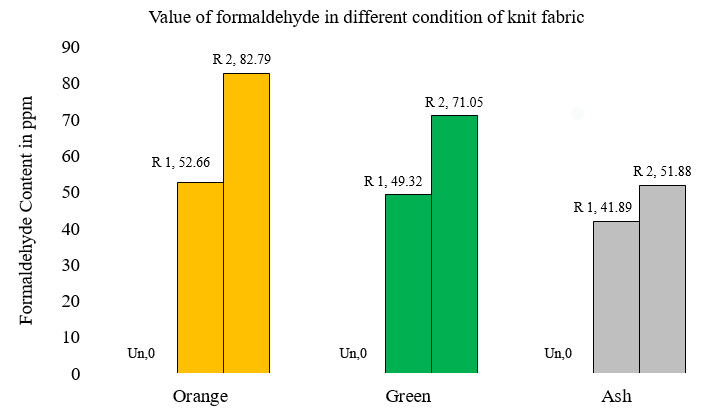 | Figure 9. Value of formaldehyde in different condition of knit fabric (orange, green, ash color fabric) |
3.3. Determination of Fastness
3.3.1. Wash Fastness
Analysis of wash fastness from Table 1 it was turned into obvious that 60 g/L and 100 g/L conc. of cross linking agent dealt with woven and knit fabric offers better to excellent fastness rather than untreated woven and knit cloth.Table 1. Analysis of wash fastness (according to ISO 105 C03) 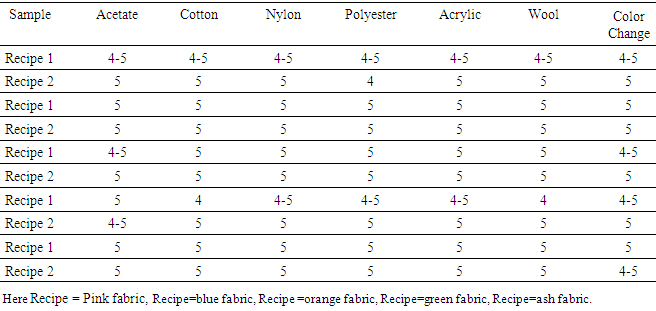 |
| |
|
3.3.2. Water Fastness
Assessment of water fastness from Table 2 it was apparent that 60 g/L and 100 g/L concentration of cross linking agent treated woven and knit material offers outstanding fastness in place of untreated woven and knit fabric.Table 2. Analysis of water fastness (according to ISO 105 E01) 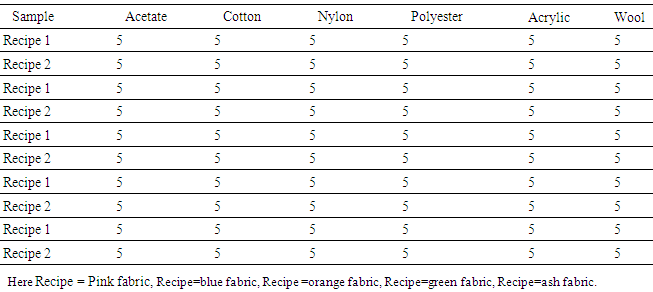 |
| |
|
3.3.3. Perspiration Fastness
Evaluation of perspiration fastness from Table 3 it become apparent that 60 g/L and a hundred g/L concentration of cross linking agent dealt with woven and knit fabric offers excellent fastness in area of untreated woven and knit fabric.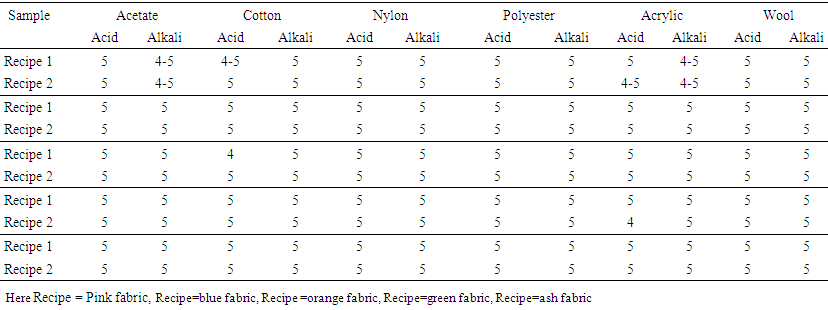 | Table 3. Evaluation of perspiration fastness (according to ISO 105 E04) |
3.3.4. Rubbing Fastness
Assessment of rubbing fastness from Table 4 it was emerged as obvious that 60 g/Land 100 g/L concentration of by-pass linking agent handled woven and knit cloth offers moderate fastness in region of untreated woven and knit fabric.Table 4. Assessment of rubbing fastness (according to ISO 105 -X12) 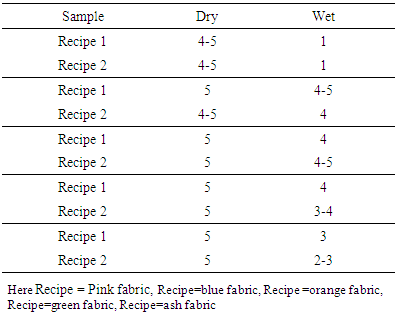 |
| |
|
4. Conclusions
On this observed to advice that DMDHEU (di hydroxyl methyl – 4, di hydroxyl ethylene urea) was one of the handiest crosslinking dealers for crease resistant finish due to containing four hydroxyl institution, N– methyl organizations of DMDHEU can cross-link cellulose. Tensile power reduced with concentration of DMDHEU The first-rate crease recovery attitude shown at 170°C fabrics finished by means of the pre – treatment or pad – dry – cure process was not simplest provided extraordinary strength however additionally offer proper abrasion resistance and delivered high-quality wash wear properties. For effect it was made resist wrinkle wearing. It was miles concluded that 60 g/L of DMDHEU, 20 g/L catalyst for smooth care and 100 g/L of DMDHEU, 30 g/L catalyst for non-iron at 170°C curing temp were the optimized manner parameters to gain better material residences.
ACKNOWLEDGEMENTS
This research paper is viable to write down even though the help and corroboration each Author’s. We would really like to babble precise gratitude and honor toward the member of Micro Fiber organization for their type co-operation, encouragement, the spur which assist us in finishing touch of this research paper.
References
[1] | Basf products for resin finishing. (January 2000 (RV). http://prismadye.com/Files/BROCHURES/BASF%20Products%20for%20Resin%20Finishing.pdf. |
[2] | F B Pietro Bellini, Ester Franzetti and Sergio Vago (2001) Textile reference book for finishing. In. Fondazione Acimit, p 139. |
[3] | F B Pietro Bellini, Ester Franzetti and Sergio Vago (2001) Textile reference book for finishing. In. Fondazione Acimit, p 140. |
[4] | M Lewin, E M Pearce (1998) Handbook of fiber chemistry, revised and expanded. In. Crc Press, p 591. |
[5] | M Lewin, E M Pearce (1998) Handbook of fiber chemistry, revised and expanded. In. Crc press, p 592. |