Md Zulfikar Hasan, Md Shamim Alam
Department of Textile Engineering, South East University, Dhaka, Bangladesh
Correspondence to: Md Shamim Alam, Department of Textile Engineering, South East University, Dhaka, Bangladesh.
Email: |  |
Copyright © 2016 Scientific & Academic Publishing. All Rights Reserved.
This work is licensed under the Creative Commons Attribution International License (CC BY).
http://creativecommons.org/licenses/by/4.0/

Abstract
The presented research work deals with the behavioral change (appearance, immersion and seam strength) of a fabric due to use of different types of dry cleaning solvents. In this research work three types of dry cleaning solvents were used i.e Perchloroethylene, Petrol and Kerosene. During this research different types of dirt (oil, grease, ink, soil and perspiration) were applied on the fabric surface and dry cleaned with different dry cleaning solvents. Some tests were conducted to compare the change in physical properties of dry cleaned fabrics. From this work a trend was observed that Perchloroethylene removed most dust and dirt particles from the surface of the fabric than Petrol and Kerosene during dry cleaning. In addition to that, Perchloroethylene did not affect fabric surface finish, that’s why appearance of fabric dry cleaned with Perchloroethylene was better and seam strength of the fabric was also greater than fabric dry cleaned with other two dry cleaning solvents.
Keywords:
Dry cleaning solvents, Perchloroethylene, Petrol, Kerosene, Garments, Textile
Cite this paper: Md Zulfikar Hasan, Md Shamim Alam, A Comparative Study on the Effect of Different Types of Dry Cleaning Solvent on the Physical Properties of Garments, International Journal of Textile Science, Vol. 5 No. 4, 2016, pp. 67-73. doi: 10.5923/j.textile.20160504.01.
1. Introduction
Dry cleaning is a process to remove grease, oil, dirt from garments or fabrics by treating them in an organic solvent, as distinct from aqueous liquors. Examples of suitable solvents are Tetracholoethylene (Perchloroethylene), white spirit or alternative hydrocarbons [1]. The process of dry cleaning uses solvent to remove soils and stains from fabric. The term "dry cleaning" is misleading. The cleaning is done with a liquid but the solvent contains little or no water and does not penetrate the fibers like water does in a washer [2]. Dry cleaning Technology consists of several steps to clean the fabric staining. Steps of dry cleaning technology is almost same for all types of solvents which are used during dry cleaning process. The steps of dry cleaning are: i) Load garment in the machine ii) Cleaning cycle iii) Centrifuge iv) Per–heating cycle v) Dry cleaning cycle vi) Cooling cycle vii) Solvent recovery [3].Leppin, Betty. March (1992) explained about the types of stains and soiling present in Museum Textile, how the textile is made and what it is made from and what condition should be considered for Dry Cleaning of the textile [11]. Mohr, Thomas K. G. (2001) mentioned about different types of dry cleaning chemicals which are really necessary for dry cleaning [12].Chemicals used in dry cleaning operations can be grouped into different categories: Dry cleaning Solvents {camphor oil, benzene, kerosene, white gasoline, petroleum solvents (primarily petroleum naphtha blends), carbon tetrachloride, perchloroethylene, trichloroethylene, 1,1,1-trichloroethane and liquid carbon dioxide}, other chemicals used in the dry cleaning machine (Detergents, Sizing, optical brighteners, bactericides, fabric, conditioners and anti-static/anti-lint agents), Pre-cleaning/Spotting Agents, Garment Treatment Chemicals [4].Seam strength & appearance tests were carried out on dry cleaned sample to check the change in physical properties of tested sample. Abrasion is one aspect of wear & is the rubbing away of the component fibers & yarns of the fabric. Crocking is a transfer of color from the surface of a colored fabric to an adjacent area of the same fabric or to another surface principally by rubbing action. Crock meter is an apparatus for evaluating the color fastness to rubbing or crocking of dyed or printed textiles [1]. The main object of this paper is to compare the effects of different solvents on physical properties of tested fabric and to find out the best dry cleaning solvent. In case of each solvent, few tests (Immersion Test, Appearance Test, Abrasion Test, Seam Strength and Crocking Test) were carried out. Then the test results for each type of physically tested sample for each type of dry cleaning solvent was compared with the untreated fabric.Property assessment of fabric after dry cleaning are a) Appearance of fabric dry cleaned with perchloroethylene was better than the fabric dry cleaned with other two dry cleaning solvents as perchloroethylene removed most amount of surface finish along with dirt so that immersion time of fabric dry cleaned with perchloroethylene was lowest and as Kerosene removed lowest amount of dirt and surface finish so that immersion time of kerosene was higher than fabric dry cleaned with perchloroethylene and Petrol but lower than untreated fabric, b) seam strength of the fabric dry cleaned with perchloroethylene was lower than fabric dry cleaned with other two solvents that’s why the seam strength was higher than fabric dry cleaned with Kerosene and Petrol, c) as most of the surface finish was removed during dry cleaning with perchloroethylene, so fibres of the fabric faced severe damage during abrasion test and so mass loss was higher than fabric dry cleaned with other two solvents.
2. Materials and Methods
2.1. Materials and Reagents
In this research work 2/1 twill (Z-twill) 100% cotton fabric was used collected from textile factory. Grey Scale, Counting Glass, GSM Cutter, Electronic Balance, Abrasion Sample Cutter, Titan Universal Strength Tester, Martindale Abrasion Tester, Rubbing Fastness Tester were also used. The Dry cleaning solvents like as Perchloroethylene, Petrol, and Kerosene were taken as reagent.
2.2. Analytical Procedure
At first the spots on the fabric were treated with hot water, then compressed air was applied on the spot to dry the fabric. After that “Turgo Oil” was applied onto the spots and slightly rubbed. As a result the fabric spots were removed. Then the fabrics were placed in the washer basket where solvent and detergent along with the motion of the machine carried out the initial washing process. The solvent travelled in a cycle through the washing basket into the filter-where much of the dirt it had collected was removed- and back into the washer, where the fabrics were rinsed. A portion of the solvent was drained off after it passed through the filter. This solvent entered the distilling unit, where it was completely purified. This was done by heating the solvent until it vaporized. The vapour was then run over cold pipes to lower its temperature rapidly and returned it to a liquid state. After distilling, the solvent again entered the washing cycle. By this means the total amount of solvent in the machine was kept at an acceptable level of purity for a long time. At the end of the washing-rinsing period, the flow of solvent was automatically shut off. After extraction, any remaining solvent was reclaimed during the drying process. This was done by tumbling the garments in a stream of warm air that vaporized the solvent. The solvent-landed air was passed over a cooling coil, condensed into liquid solvent, and returned to the storage tank for reuse. The length of the drying cycle depended on the setting of the temperature on the thermostat. Until the temperature setting was reached, the drying cycle continued (for white color 45 minutes, for cream color 35 minutes and for other light colors25-30 minutes). The temperature used for white color 80°C, for cream color 60°C and for other light colors 40°C. Once the desired temperature was reached and the bulk of the solvent reclaimed, the clothes were treated with a stream of fresh air. This portion of the dry-cleaning process was the deodorizing cycle that strips away any remaining odour or solvent vapour that may still be left in the clothes. Then the fabrics were taken out from the machine and then ironed to restore the shape and appearance of the fabric. Finally, the fabrics were packed.
2.3. Appearance Test
At first a piece of untreated fabric was separated. Then the samples which were treated with Oil, Grease, Ink, Soil and Perspiration before dry cleaning were compared with the untreated sample to find out the visual changes on the fabric surface after dry cleaning and finally the results were tabulated.
2.4. Immersion Test
At first 4 samples of size 1cm2 were cut from the untreated fabric and then each of the samples immersion time into the water was recorded with the help of stop watch and tabulated. Then the same procedure was repeated for oil, grease, ink, soil and perspiration treated samples which were dry cleaned with three different solvents.
2.5. Seam Strength Test
At first untreated fabric was cut into a size of 7 inch length and 4 inch width. Then superimposed seam was prepared with a seam allowance of 0.6cm. After that the sewn sample was set between the clamps of the machine as the sewn part remain at the middle of the two clamps. Then the sample was locked between the two clamps. Then the amount of force to break down the seam was taken from the reading of the scale. The process was repeated 3 times more for untreated fabric. The same procedure was done with the fabrics which were treated with oil, grease, ink, soil and perspiration before dry cleaning with three different solvents.
2.6. Abrasion and Rubbing Test Measurement
Abrasion test of the fabric was carried out with test method of ISO 12947-3 (Mass loss) where Martindale Abrasion Tester was used. Determination of Rubbing Fastness for both dry and wet condition was conducted by ISO 105-X12 and here crock meter was used.
3. Results
Different test results are summarized below sequentially.Table 1. Comparison of Appearance among different agents 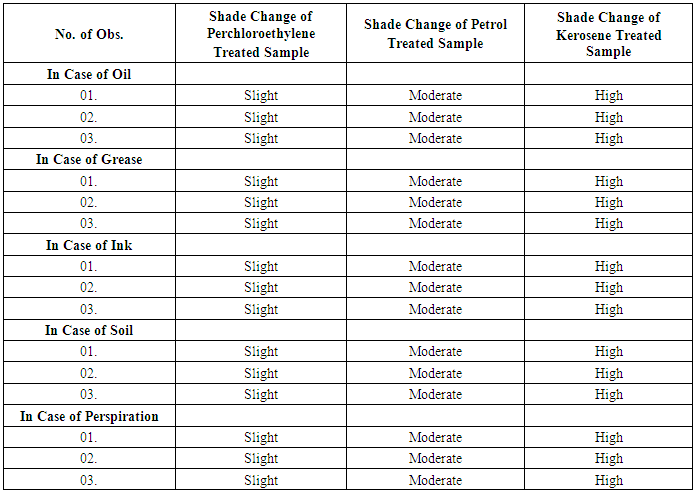 |
| |
|
Table 2. Comparison of Immersion Time among different agents 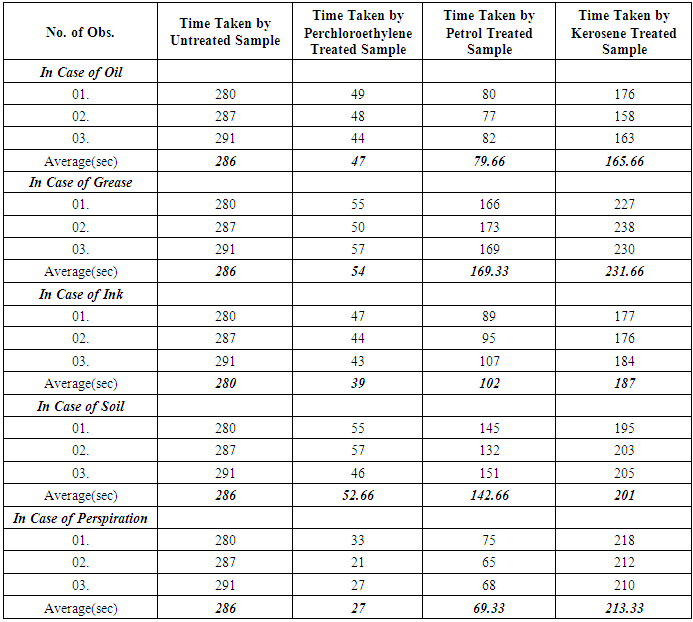 |
| |
|
Table 3. Comparison of Seam Strength among different agents 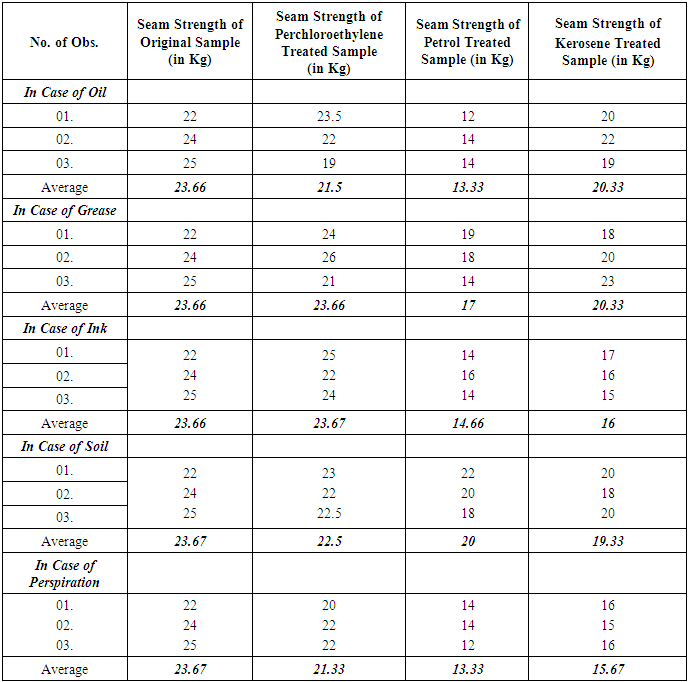 |
| |
|
Table 4. Comparison of Average Mass Loss of Different Dry Cleaning Solvent Treated Fabric 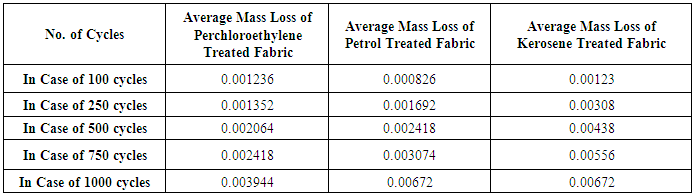 |
| |
|
From the diagram of Comparison of Shade Change, it is seen that after removing oil, grease, ink and soil from the surface of the fabric the shade of the percholoethylene treated fabric changed slightly but for petrol and kerosene treated fabric the change in shades of the fabric were moderate and high respectively. It might be due to the fact that percholoethylene is a volatile compound, and as a result it caused almost no staining on the fabric surface, whereas petrol and kerosene affected the appearance of the fabric. But for kerosene the result was severe. Therefore, for a particular dry cleaned fabric, the Appearance or Shade Change (high to low) sequence is as like: Kerosene Treated (High) > Petrol Treated > Perchloroethylene Treated (Low).From the diagram of Comparison of Immersion Time, it is seen that after removing oil, grease, ink and soil from the surface of the fabric the immersion time of the fabric dry cleaned with Kerosene is higher than fabric dry cleaned with perchloroethylene and Petrol; but lower than Untreated Fabric as Kerosene removed the lowest amount of dust particle from the surface of the fabric. As perchloroethylene removed highest amount of the dirt particles from the surface of the fabric so that the immersion time of the fabric dry cleaned with perchloroethylene was the lowest. As least amount of dirt was removed from the surface of the fabric during dry cleaning with petrol than dry cleaning with perchloroethylene, so that the immersion time of the fabric dry cleaned with petrol was higher than fabric dry cleaned with perchloroethylene. Therefore, for a particular dry cleaned fabric, the Immersion Time (high to low) sequence is as like: Untreated (High) > Kerosene Treated > Petrol Treated> Perchloroethylene Treated (Low).From the diagram of Comparison of Seam Strength, it is seen that after removing oil, grease, ink and soil from the surface of the fabric the seam strength of perchloroethylene treated fabric is slightly lower than original fabric but higher than petrol and kerosene treated fabric. Difference in seam strength occurred due to seam slippage variation. As perchloroethylene removed most amount of dirt from the surface of the fabric so that seam slippage was lower than the fabric dry cleaned with petrol and kerosene. As lower amount of dirt was removed from the surface of the fabric during dry cleaning with petrol than kerosene so that the seam slippage of fabric dry cleaned with petrol was higher than fabric dry cleaned with Kerosene. So for a particular dry cleaned fabric the seam strength sequence (from high to low) is as like: Original (High)> Perchloroethylene Treated > Petrol Treated > Kerosene Treated (Low).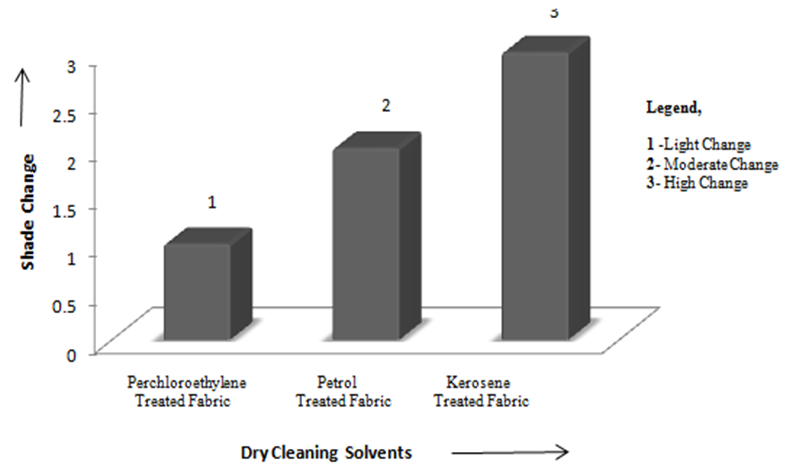 | Figure 1. Comparison of Shade Change (Appearance) of Fabric Dry Cleaned with Different Dry Cleaning Solvents |
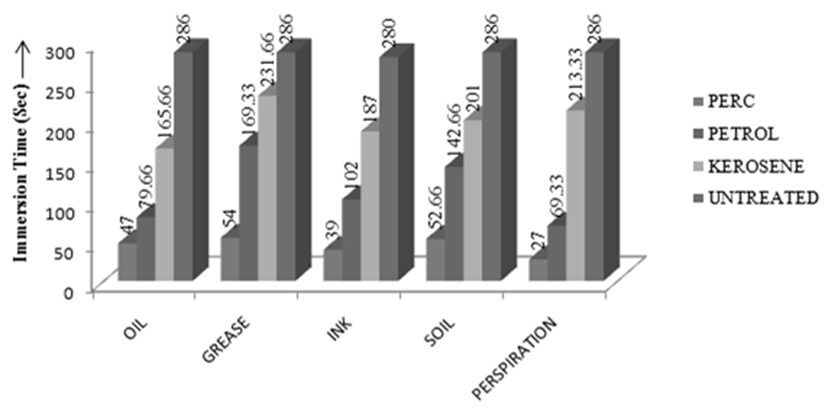 | Figure 2. Comparison of Immersion Time among different solvents |
 | Figure 3. Comparison of Seam Strength among different solvents |
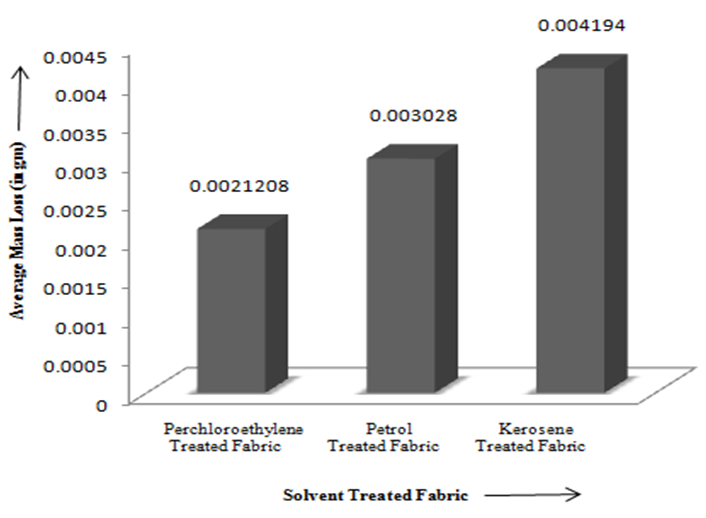 | Figure 4. Comparison of Average Mass Loss Fabric Treated with Different Dry Cleaning Solvents |
From the diagram of Comparison of Average Mass Loss of fabric stained with oil, grease, ink, soil & perspiration it is seen that after using percholoroethylene, petrol and kerosene as dry cleaning solvents, perchloroethylene removed highest amount of dirt from fabric surface. During abrasion test, we found out that the average mass loss of the fabric dry cleaned with perchloroethylene was lower than fabric dry cleaned with petrol and kerosene. It might be due to the fact that, during dry cleaning perchloroethylene damaged the fabric surface to the least extent, whereas the damage of the fabric surface during dry cleaning with kerosene was severe and the damaged caused by petrol on the fabric surface was in between these two solvents. So for a particular dry cleaned fabric the average mass loss sequence (from high to low) is as like: Kerosene Treated (High) > Petrol Treated > Perchloroethylene Treated (Low).
4. Conclusions
The research work on dry cleaning of a fabric using different solvents is an approach to determine the effects of dry cleaning solvents on the physical properties of a fabric. The results found from the project work can be used to find out the best solvent. According to this research work Perchloroethylene was found to be the best as dry cleaning solvent whereas Kerosene was the least. Kerosene produces odour, and it is also flammable. Due to these reasons it is now banned all over the world commercially. Perchloroethylene shows better result than Kerosene and Petrol, that’s why Perchloroethylene is commercially the most used dry cleaning solvent. It is expected that this project work would be beneficial for the dry cleaning sector as well as for the textile industries.
References
[1] | M .J. Denton, P. N. Daniels, Eleventh Edition, “Textile Terms and Definitions”, The Textile Institute, UK (2002). |
[2] | J. Fagliano, M. Berry, F. Bove, T. Burke “Drinking water contamination and the incidence of leukemia: an ecologic study”, American Journal of Public Health (2011), 80:10, 1209-1212. |
[3] | Dieter R. Berndt, Leonard Tachner, “Dry Cleaning Method and Solvent”, United States, Patent Number: 5,865,852, Date of Patent: Feb. 2, 1999. |
[4] | Kyyrönen, Pentti, Helena Taskinen, Marja-Liisa Lindbohm, Kari Hemminki, and Olli P. Heinonen. "Spontaneous abortions and congenital malformations among women exposed to tetrachloroethylene in dry cleaning." Journal of epidemiology and community health 43, no. 4 (1989): 346-351. |
[5] | J.E. Booth, Third Edition, “Principle of Textile Testing”, Heywood Books, UK (1961). |
[6] | McCoy, Michael. "Dry cleaning dreams. "Chemical and engineering news 83, no. 46 (2005): 19-22. |
[7] | Katz, RONALD M., and D. A. V. I. D. Jowett. "Female laundry and dry cleaning workers in Wisconsin: a mortality analysis." American journal of public health 71, no. 3 (1981): 305-307. |
[8] | Lauwerys, Robert, J. Herbrand, Jean-Pierre Buchet, Alfred Bernard, and José Gaussin. "Health surveillance of workers exposed to tetrachloroethylene in dry-cleaning shops." International archives of occupational and environmental health 52, no. 1 (1983): 69-77. |
[9] | Ruder, Avima M., Elizabeth M. Ward, and David P. Brown. "Cancer mortality in female and male dry-cleaning workers." Journal of Occupational and Environmental Medicine 36, no. 8 (1994): 867-874. |
[10] | Cronin Jr, J. Joseph, and Steven A. Taylor. "Measuring service quality: a re-examination and extension." The journal of marketing (1992): 55-68. |
[11] | Leppin, Betty, “Drycleaning Machines”, International Fabricare Institute, Volume 16, No. 1 (1992). |
[12] | Mohr, Thomas K. G., “Solvent Stabilizers White Paper San Jose: Underground Storage Tank Program”, Water Supply Division, Santa Clara Water District (2001). |