Md. Abdus Shahid1, Md. Ismail Hossain2, Delwar Hossain1, Ayub Ali3
1Dhaka University of Engineering & Technology (DUET), Department of Textile Engineering, Gazipur, Bangladesh
2University of Malaya (UM), Department of Mechanical Engineering, Kuala Lumpur, Malaysia
3BGMEA University of Fashion and Technology (BUFT), Department of Apparel Manufacture & Technology, Dhaka, Bangladesh
Correspondence to: Md. Abdus Shahid, Dhaka University of Engineering & Technology (DUET), Department of Textile Engineering, Gazipur, Bangladesh.
Email: |  |
Copyright © 2016 Scientific & Academic Publishing. All Rights Reserved.
This work is licensed under the Creative Commons Attribution International License (CC BY).
http://creativecommons.org/licenses/by/4.0/

Abstract
Color fastness and color strength are very crucial facts in case of colored textile material which are intimately related to various dyeing parameters viz. concentration of dye, salt, alkali and dyeing temperature. In the present work, the effect of concentration of reactive dye (1%, 3%, 5%, 7% & 9%), salt (20g/l, 30g/l & 40g/l) and alkali (5g/l, 8g/l & 10g/l), and the effect of dyeing temperature (40°C, 60°C & 80°C ) on color fastness and color strength properties of cotton-elastane (CE) and lyocell-elastane (LE) fabrics were studied remaining the constant of dyeing duration time at 45 minutes. The results were compared for variation in fastness values and color strength under the same conditions as being employed in textile industry. Some of the factors behave linearly and some are not. Result reflects that the color fastness values to dry and wet rubbing are more at low dye concentration, low salt and alkali concentration and at low temperatures for both cotton-elastane and lyocell-elastane fabrics which reaches up to 4-5 to 5. But in case of washing fastness property, both fabrics reflect a fixed value i.e.4-5 irrespective of dye concentration, salt and alkali concentration, dyeing time and temperature. On the other hand, the color strength results evinced that temperature has more influence on LE than CE for acquiring higher color strength. LE fabric exhibited better dye ability with higher color uptake compared to CE fabric. In addition the concentrations of salt and alkali have almost linear proportional effect on both CE and LE within a range.
Keywords:
Cotton-Elastane, Lyocell-Elastene, Color Fastness, Color Strength, Reactive Dye, Salt, Alkali
Cite this paper: Md. Abdus Shahid, Md. Ismail Hossain, Delwar Hossain, Ayub Ali, Effect of Different Dyeing Parameters on Color Strength & Fastness Properties of Cotton-Elastane (CE) and Lyocell-Elastane (LE) Knit Fabric, International Journal of Textile Science, Vol. 5 No. 1, 2016, pp. 1-7. doi: 10.5923/j.textile.20160501.01.
1. Introduction
The generations of regenerated cellulose fibers, such as viscose, modal and lyocell fibers are among the most important fibers from the point of textile and environmental aspects due to the natural structures and properties [1]. Lyocell is the generic name for a regenerated cellulosic fiber obtained by spinning of dissolved wood pulp in an organic solvent. These regenerated cellulosic fibers are produced by a more environmentally friendly procedure where cellulose is dissolved in the organic solvent N-methyl morpholine-N- oxide (NMMO). Regeneratedcellulosic yarns with various chemical reagents had been the subject of research for several years for NMMO or lyocell fibers, produced by the amine oxide process [2, 3] are solvent spun. More than 99% of the solvent is recycled within the process, making the fiber production ecofriendly. Very small quantities of NMMO emitted via waste water are readily degraded in the biological waste water treatment plants. NMMO with its favorable toxicological properties has been found to be less toxic than ethanol. The solvent spinning technique so adopted is an environmentally responsible process [4]. This manufactured fiber shows round cross-sections and a smooth surface. Their high degree of crystallinity, molecular orientation and higher molecular weight causes special properties such as high wet fiber strength and comparatively low elongation, leading to the remarkable dimensional stability of fabrics produced from them. Lyocell fiber’s degree of crystallinity is 16 % higher than that of modal fibers and much higher (43%) compared to viscose fibers. The fibrils in lyocell fibers are thinner than in modaland viscose fibers and molecular orientation is nearly the same (orientation function of lyocell fibers is 3% higher) as in modal fibers but much higher compared to viscose standard fibers (18%). Lenz and Schurz [5] determined the size of crystalline regions of regenerated cellulose fibers: length 12 - 14 nm, width 8 - 10 nm, and thickness 3 - 4 nm. The broad plane of the platelet-shaped crystallites is situated parallel to the 101 - lattice plane. The crystallites form strands with a length of 150 nm - 550 nm. They are partly bundled up in clusters with diameters of 30 - 60 nm, partly separated by less dense spacing regions. Since lyocell is cellulose based fiber and therefore can be dyed with any class of dyestuff suitable for other cellulosic fiber. On the other hand cotton fibers are widely applied in textile industry due to its excellent properties of hygroscopicity, air permeability, biodegradability, no static electricity, etc. The dyeing of these fibers are generally done with reactive dyes due to its brilliancy, variety of hue, high wet fastness, convenient usage and high applicability. These reactive dyes contain a reactive group, either a halo-heterocyclic or an activated double bond, that, when applied to a fiber in an alkaline dye bath, forms a chemical bond with hydroxyl group on the cellulosic fiber [6]. In recent years, reactive dyes maintain the largest annual consumption in the world among the dyes used for which establishes its important status in the dye manufacture industry. But some problems, such as low dye utilization, large amount of electrolyte used and high volume of wastewater discharged, always exist in the application of reactive dyes. The dyeing of one kilogram of cotton with reactive dyes demands from 70 to 150 litre water, 0.6-0.8 Kg NaC1 and from 30 to 60 g dyestuffs [7]. Spandex/elastane is an elastomeric which is always blended with other natural and synthetic fibers such as cotton, wool, silk, and linen. Different types of spandex material exist on the markets with different counts, this impose engineering the use of every type at different spun materials and fabric construction. The percentage of spandex used in the knitting industry depends on the fabric stretch required and fabric properties [8]. The reactive dyes have higher natural affinity for LE fabric than for CE fabric because of its structure as a result it shows higher K/S value in comparison with CE fabric. Hence, reactive dyes with good migration properties will be best suited for LE fabric providing level dyeing effect. Thus, the electrolyte recommendations can also be significantly reduced, as compared to the dyeing to the same depth of shade on CE fabric. Consequently, there is reduction in chemical cost, handling and total dissolved solids. Lower electrolyte also facilitates quicker removal of unfixed hydrolysed dye from the fiber in washing stage after dyeing, thus reducing the process cycle time and hence the cost [9]. Traditionally disperse dye was used to dye spandex/ superfine polyester fabric and some auxiliaries were also approached for dyeing of elastic fiber with disperse dye [10, 11]. Later on reactive dyes are in fact seen as the major dye class used on LE fabric and CE fabric. However, it is revealed that cotton with less elastane percentage shows better fastness property in case of reactive dyeing [12]. There are several studies done on the optimization of process parameter for obtaining improved dyeing behavior. The process parameters have a great influence on the dyeing performance [13, 14]. Some pretreatment process and treatments give better result in colorfastness property of polyester-spandex fabric [15]. In case of dyeing the CE fabric, ways of getting better color fastness property has been explained by using auxiliaries (HYS-422 auxiliaries) [16]. However, the effect of variation of different conditions (temperature and dye concentration) and auxiliaries (salt and alkali) have not been found during researching by the authors. Furthermore another most eco-friendly fiber LE fabric dyed with reactive dye and the influence the process parameters along with their comparison with CE in respect to color fastness and color strength requires clarification. The aim of this study was to investigate and compare the effect of temperature, amount of alkali, amount of salt and dye concentration ondyability characteristics especially on color fastness (rubbing and wash) and color strength of CE and LEknit fabric.
2. Materials and Methods
2.1. Procedure of CE and LE Knit Fabric Manufacturing
In this investigation, single jersey cotton-elastane (CE) and lyocell-elastane (LE) knit fabrics were manufactured by single jersey knitting machine having 32 inches diameter, 24 gauges (needles/inch) and 104 yarn feeders (Brand: Fukuhara, Model: MXC-S3.2RE, Origin: Japan). CE knit fabric was made from 95% cotton & 5% elastane yarn and LE grey fabric was made from 95% lyocell & 5% elastene yarn. The yarn count was 32s/1for cotton, 18 tex for lyocell, 30 denier for lycra. 100% cotton yarn was sourced from Square Spinning mills Ltd. Bangladesh, lyocellyarn (Brand: Tencell) from Austria, and elastence yarn (Brand: Texlon) from Korea.
2.2. Pre-treatment & Dyeing Procedure
Both types of grey fabrics were scoured and bleached using single bath. Recipe for CE fabric was NaOH @1.2 g/l, H202@2.5 g/l at 98°C for 60 minutes during scouring & bleaching. On the other hand, recipe for LE fabric was Na2CO3@4 g/l, H202@2.5 g/l at 80°C for 60 minutes. Single bath scouring and bleaching process was done in a laboratory dyeing machine (Brand: Starlet, Model: DL-6000, Origin: Korea) maintaining the material & liquor ratio of 1:6. Average grams per square meter (GSM) of scoured & bleached fabric were 185. All pre-treated CE and LE knit fabric samples were dyed using exhaust dyeing methods with reactive dye (Remazol Blue RR) in a laboratory dyeing machine (Brand: Starlet, Model: DL-6000+, Origin: Korea) according to Table 1 at material and liquor ratio of 1:8. Forty five experiments were carried out altering the dyeing parameters viz. concentration of dye, salt & alkali and temperature remaining the constant of dyeing duration time at 45 minutes that is showed in Table 1. Table 1 shows that five different level of dye concentration namely 1%, 3%, 5%, 7% and 9% with different salt & alkali concentration and dyeing temperature were used for preparing the samples during this study. After dyeing all samples were cold rinsed and then hot washed by washing machine (Brand: LG, Model: WD-1203 CDP, Origin: Korea), at 90°C for 10 minutes. Next, the samples were dried by tumble dryer machine (Brand: SDL, Origin: UK).and conditioned for 2 hours at (65±2) % RH (relative humidity) and (20±2) °C temperature.Table 1. Experimental design considering the dyeing parameters 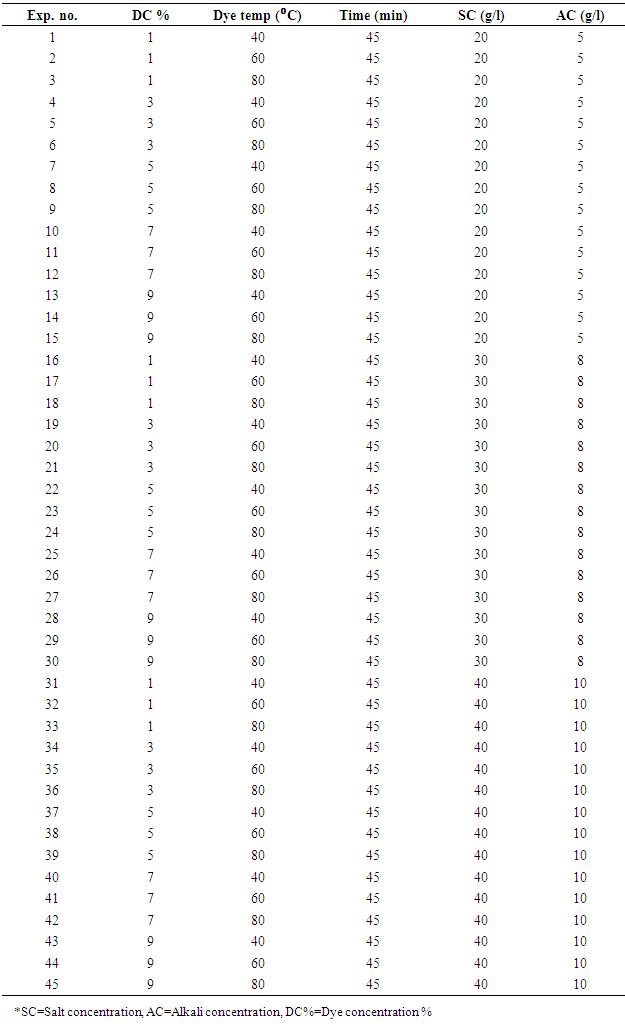 |
| |
|
2.3. Measurement of Color Strength and Color Fastness Properties
Reflectance values of all dyed samples were measured using spectrophotometer (Brand: Datacolor Spectrum, Origin: USA, Model: 650TM), in a visible region with wavelength of 650nm. The color strength (K/S) was calculated using the Kubelka-Munk equation:
Color fastness properties of all dyed samples were determined using the crock meter (Brand: SDL, Origin: UK) and multi-fiber. The color fastness values were assessed using grey scale both for color fastness to rubbing and color fastness to washing. Rubbing fastness properties were examined by applying BS EN ISO-105-X12:2002 method and color fastness to washing were examined applying BS EN ISO 105 CO6:2010 method.
3. Result and Discussion
3.1. Effect of Temperature on Color Strength and Fastness
3.1.1. Effect of Temperature on Color Strength
K/S value in Figure 1(a), Figure 2(a) and Figure 3(a) reflects that dyeing temperature has a great impact on dye uptake for both fabrics. A dramatic change occurs in fiber polymer system when temperature is applied as a medium of energy. This scenario is best viewed from the plotted curves. As the temperature increases, the molecular structure becomes open which facilitate the dye uptake and hence the higher K/S value is obtained. An interesting relation was obtained when the temperature was increased at different level of dye, salt and alkali concentration. In case of cotton-elastane, the results show that K/S value of dyed fabric increased gradually with the increase of temperature from 40°C to 60°C. In fig 3, at 60 °C for cotton-elastane shows optimum dye uptake but the K/S value in the plotted figure shows that at 80°C the dye uptake results getting down which may be due to diffusion of dye from the core of the fiber. At 1%, 3% and 5% the results shows near parallel effect. On 7% dye it shows slightly higher differences but at 9% dye concentration with 60°C and 80°C shows less difference in results whereas at 40°C it shows declined value. Again, for LE fabric samples, the plotted curves show different action. At 1%, 5% and 7% of dye concentration of 40°C and 80°C shows small value difference. But high level of dye uptake was shown at 60°C for LE. In addition, at 9% dye concentration with 80°C the LE fabrics show a highest peak but decreasing rate of dye uptake at 40°C.The reason for this is obvious and indicates of the effects of different structure for cotton and lyocell. Due to higher degree of crystalinity in the polymer structure of CE to LE causes less dye uptake of CE fabrics. | Figure 1. Effect of dye concentration and temperature at 20 g/l salt & 5g/l alkali |
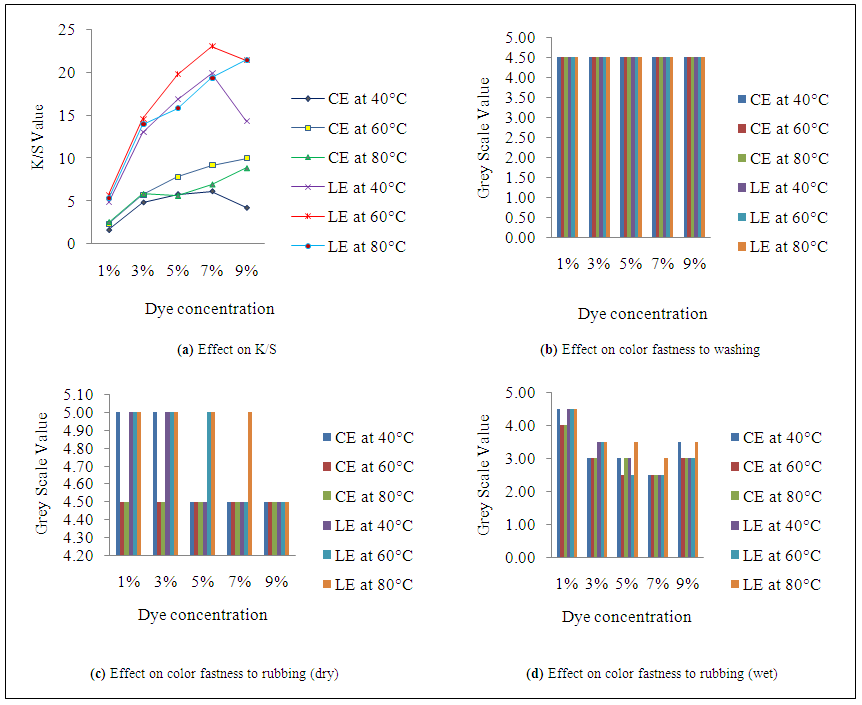 | Figure 2. Effect of dye concentration and temperature at 30 g/l salt & 8g/l alkali on color strength & fastness properties |
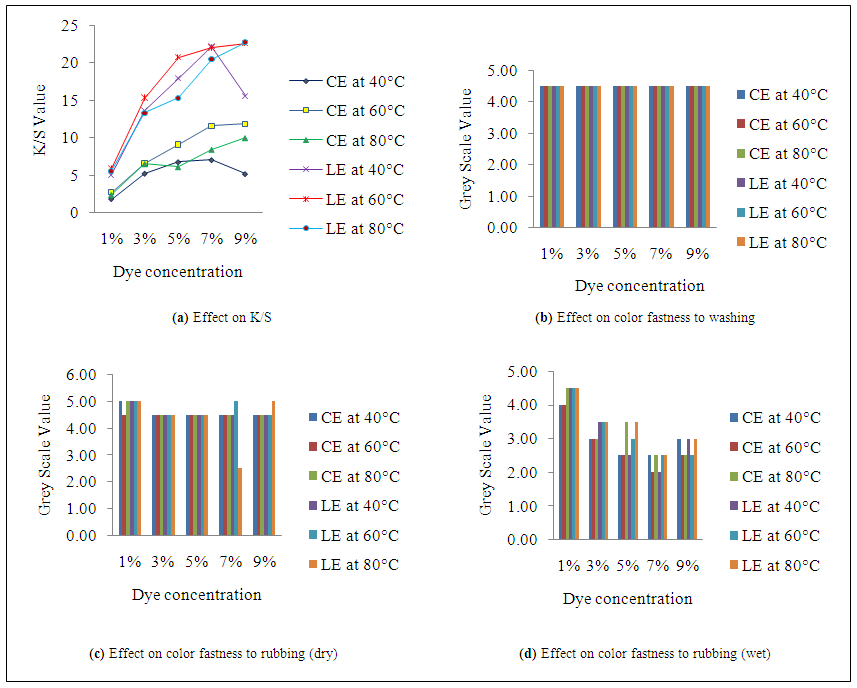 | Figure 3. Effect of dye concentration and temperature at 40g/l salt & 10g/l alkalion color strength & fastness properties |
3.1.2. Effect of Temperature on Color Fastness
As the temperature increases, the depth of shade also increases. As a result, when the dyed samples are rubbed against an object, more dye molecule comes out from the fabric surface hence the value become less which means rubbing fastness property is not good. From the Figure 1 (c & d) and Figure 2 (c & d) for both fabrics, the rubbing fastness values are higher at a particular temperature. In some cases, the rubbing fastness value increases with temperature which may be due to good fixation of the dye molecule at that temperature to these particular fiber. However, the effects of temperature on washing fastness properties of the dye molecule are not as visible as in case of rubbing fastness. Figure.3.b reflects that irrespective of dyeing temperature and fabric type, color staining values to multi-fiber (DW) are same at all temperature for both fabrics.
3.2. Effect of Salt and Alkali on Color Strength and Fastness
3.2.1. Effect of Salt and Alkali on Color Strength
The plotted curves of Figure 1(a), Figure 2(a) and Figure 3(a) indicate that with the increased amount of salts and alkali the dye uptake also increased. The plotted data shows a gradually increased curve with linear relation. The highest value of dye uptake was observed 11.85 for CE and 22.6 for LE with the amount of 40g/l salt and 10g/l of salt and alkali concentration respectively. The least value of salt and alkali concentration i.e. 20 g/l and 5 g/l shows the minimum K/S value for CE and LE fabrics which mean that this concentration has less impact at the values of dye uptake for fabrics. However, the effect of salt and alkali concentration on dye uptake is also affected by other factors such as-dye concentration, dyeing temperature and time etc.
3.2.2. Effect of Salt and Alkali on Color Fastness
The plotted curves in Figure 1(d) & Figure 2(d) indicate that with the increased amount of salts and alkali, the dye uptake also increased for both fabrics as a result more dye molecule comes out during wet rubbing. The higher value of grey scale in Figure 2 (c & d) indicates that dyed sample contained less dye molecule at low concentration of salt and alkali. At low concentration of alkali and salt, the grey scale value for dry and wet rubbing reached upto 4.5-5 which means good rubbing fastness. However, salt and alkali concentration has no significant effect on wash fastness properties of the both samples as shown in Figure 3(c).
3.3. Effect of Dye Concentration on Color Strength and Fastness
3.3.1. Effect of Dye Concentration on Color Strength
K/S value in Figure 1(a), Figure 2(a) and Figure 3(a) reflects that dye concentration has an unavoidable impact on dye uptake for both fabrics. Generally as the dye concentration increases, the availability of the dye molecules in the dye bath also increases as a result more dye molecule can attach to the fiber and hence the higher K/S value is obtained. In case of CE fabric, the results show that K/S value of dyed fabric increased gradually as the dye concentration shifted from 1 to 9% along with others parameters i.e. temperature, salt and alkali concentration with some exceptions. Certainly, the maximum K/S values (11.85) for CE and 22.68 for LE fabric were achieved at 9% dye concentration with some deviations in temperature. The deviation in K/S value at dye concentration 7% and 9% for both fabrics is similar than other values.
3.3.2. Effect of Dye Concentration on Color Fastness
The effect of dye concentration on rubbing fastness properties of the dyed samples for both fabrics is more significant than other parameters. Generally as the dye concentration increases, the availability of the dye molecules in the dye bath also increases as a result more dye molecule can attach to the fiber and hence depth of shade increases. From Figure 1(c & d) and Figure 2(c & d), the result shows that as the dye percentage shift from 1 to 9%, the grey scale value declines because dye molecule from dyed sample easily came out during rubbing. On the other hand, irrespective of dye concentration for both fabrics in Figure 3(b), it can say that color staining values are less. This may be happen due to two factors; for low dye concentration few dye molecules came out during washing as a result staining of multi-fiber was less and for higher dye concentration, dye molecules may be fixed strongly which increased the resistance to washing of the dye molecules.
4. Conclusions
A correlative study was made on color fastness properties &color strength of cotton-elastane (CE) and lyocell-elastane (LE) for different dyeing parameters. The color fastness values for both fabrics show maximum value i.e.4-5 to 5 at a particular temperature with some exceptions. The fastness values of lyocell-elastane fabrics is more in comparison with cotton-elastane fabrics for dry and wet rubbing which may be due to its high fixation rate. In case of washing fastness properties both fabrics show any differences in their values of 4-5. Therefore, it can be stated that rubbing fastness properties is inversely related with dye concentration excluding washing fastness with respective salt and alkali concentration, dyeing time and temperature. In case of color strength assessment, results showed that highest K/S value for CE fabric was obtained at dye concentration 9%, salt concentration 40g/l, alkali concentration 10 g/l and dyeing temperature 60°C whereas highest K/S value was recorded at dyeing temperature of 80°C with same concentration of salt & alkali in LE fabric. In case of CE fabric, the maximum K/S value has reached up to 11.85 and for LE fabric, K/S was 23.03.
ACKNOWLEDGEMENTS
The authors are thankful to the management of Alim Knit (BD) Ltd for providing the laboratory facilities for this study.
References
[1] | Albercht. W at al. “Lyocellfibres”, Chem Fibers Int, 47, (1997): 289-304. |
[2] | Krassig, H., and Structure Cellulose. "Accessibility and Reactivity Gordon and Breach Science Publishers." (1992). |
[3] | Stana-Kleinschek, K., Ribitsch, V., Kreže, T., Sfiligoj-Smole, M., & Peršin, Z. Correlation of regenerated cellulose fibres morphology and surface free energy components. Lenzinger Berichte, 82(1), (2003):83-95. |
[4] | Chavan, R. B., and A. K. Patra. "Development and processing of lyocell." Indian journal of fiber and textile research” 29.4 (2004): 483. |
[5] | Lenz, J., J. Schurz, and E. Wrentschur. "Comparative characterization of solvent spun cellulose and high wet modulus viscose fibers by their long periods." Actapolymerica 43.6 (1992): 307-312. |
[6] | Rattee, I. D. "Reactive dyes for cellulose 1953–1983." Review of Progress in Coloration and Related Topics 14.1 (1984): 50-57. |
[7] | Allegre, C., et al. "Treatment and reuse of reactive dye effluents." Journal of Membrane Science 269.1 (2006): 15-34. |
[8] | Haji, M. A.Properties of cotton/spandex single jersey fabrics. The Indian Textile Journal (2013). |
[9] | Taylor, James M., Michael J. Bradbury, and Stephen Moorhouse. "Applied Technology-Dyeing Tencel and Tencel A100 with poly-functional reactive dyes." AATCC Review-American Association of Textile Chemists and Colorists 1.10 (2001): 21-24. |
[10] | Jiangang, L. Dyeing of Spandex/Superfine Polyester Knitgoods. Dyeing and Finishing, 7, (2003):006. |
[11] | Hong_fei, Q. I. A. N., & Xin_yuan, S. O. N. G.. “The Effect of Auxiliaries on Dyeing Spandex With Disperse Dyes. Textile Auxiliaries”, 2, (2001): 007. |
[12] | GAO, X. H., & SONG, X. Y. Research on the dyeing and finishing processes of the new cotton/spandex elastic fabrics. Textile Auxiliaries, 6, (2005): 010. |
[13] | Kabir, S. F., Iqbal, M. I., Sikdar, P. P., Rahman, M. M., & Akhter, S. “Optimization of Parameters of Cotton Fabric Whiteness”. European Scientific Journal, 10(36) (2014). |
[14] | Shaohua, L. Pretreatment Parameters and Dyestuffs Optimization before Ink Jet Printing. Dyeing and Finishing, 12, (2001):001. |
[15] | QIAN, Q. F., ZHANG, J. F., ZHANG, J. G., & JIN, X. H. Wet processing of polyester/spandex fabric. Dyeing & Finishing, 7, (2013):005. |
[16] | LI, X. J., LI, Y. Y., & MA, D. F. Technology Practice of Dyeing and Finishing Cotton/Spandex Undershirt Cloth. Shandong Textile Science & Technology, 2, (2004):006. |