Anup K. Nandi, Utpal Banerjee, Debkumar Biswas
Department of Textile Technology, Indian Jute Industries’ Research Association (IJIRA), Kolkata, India
Correspondence to: Debkumar Biswas, Department of Textile Technology, Indian Jute Industries’ Research Association (IJIRA), Kolkata, India.
Email: |  |
Copyright © 2015 Scientific & Academic Publishing. All Rights Reserved.
Abstract
Limited availability of cotton, linen and flax like natural fibres has created good opportunity for the – jute, the ‘Golden Fibre,’ to invade into value-added textiles application e.g. hometextiles. However owing to the inferior aesthetics quality, acceptance of jute fabric as bed linens, sheets, curtains, cushion-cover, draperies etc. is restricted. Experimental results have shown that blending of jute and ramie fibre which bears superior fibre qualities compared to jute can produce high quality blended fabrics with improved aesthetic properties like texture, feel, resiliency, drapability and durability which add values for consumers’ adoration. This paper envisages a customized blending process of jute and ramie fibres for developing fine quality blended yarns and fabrics; additionally the effect of blending in terms of gain in physical and aesthetic properties of fabric has been investigated. Four types of yarns (100% jute, 80:20 jute/ramie, 50:50 jute/ramie and 100% ramie) have been prepared under identical processing conditions and subsequently blended fabrics developed. Effects of ramie fibre blending on tensile, aesthetic and serviceability properties of jute/ramie blended fabrics have been examined and subsequently comparative analysis with 100% jute (control) fabric has been carried out.
Keywords:
Ramie, Ramie blends, Jute blending, Hometextiles, Jute spinning
Cite this paper: Anup K. Nandi, Utpal Banerjee, Debkumar Biswas, Improvement in Physical and Aesthetic Properties of Jute Fabrics by Blending Ramie Fibre in Suitable Proportions, International Journal of Textile Science, Vol. 4 No. 4, 2015, pp. 73-77. doi: 10.5923/j.textile.20150404.01.
1. Introduction
Indian hometextiles market is growing modestly at the rate of 8% CAGR [1] and natural fibre is expected to be the potential contender to consume majority of its market share driven by the human preference towards natural products. Natural fibre based textiles are constantly increasing their acceptance among global consumers due to growing awareness towards sustainability. However global production of textile grade natural fibres is limited and preferential use of these fibres in respective applications can lead to equilibrium between demand and supply. Hometextiles manufactures in India are trying to rationalize the use of cotton or linen like valuable apparel grade natural fibres in home-furnishing products considering their rising global demand for apparels. Thus comparatively coarse bast fibre - Jute - has now been gradually accepted by textile industry as a prospective alternative to cotton, linen or wool fibre. But due to subordinate aesthetic properties, jute based products often fail to qualify the intended standard of value-added hometextiles.Blending is considered as an important technique to combine fibres to get better realization of superior qualities [2]. Branched fibre structure of jute poses limitation in making finer yarn which is essentially required to manufacture good quality hometextils. Higher fibre stiffness and rigidity restrict jute filaments to pack coherently within yarn while wide fibre length distribution tends to generate short fibres during processing which introduce surface roughness [3]. Whereas blending of superior quality fibres like ramie (having lower fibre fineness, regular surface and higher tensile strength) with jute, in suitable proportions, can improve physical as well as aesthetic properties of jute blended textiles facilitating its aesthetic values [4].Ramie (Boehmeria nivea) is a natural fibre having high strength, silky appearance, soft feel and compatibility with other natural fibres. Importantly ramie represents similarities in terms of chemical constituents (Table 1) as well as in fibre properties viz. breaking strength and density of fibre. These two fibres i.e. jute and ramie can suitably be blended in modified jute spinning system. Proportionate blending of jute and ramie, may offer cost effective substitute of cotton or linen based home-textiles and furnishings. Table 1. Chemical constituents and properties of jute and ramie fibre 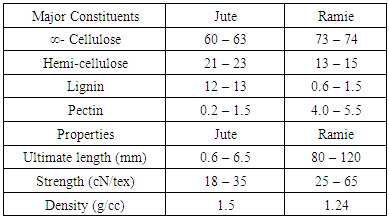 |
| |
|
Few studies on blending of ramie fibre with other natural fibres have been reported earlier but effect of blending on fabric quality has not been elaborated. This paper describes suitable processing technology for jute/ramie blending to produce fine yarns, and further observes improvement in physical and aesthetic properties of jute blended fabrics in comparison to control (100%) jute fabric.
2. Materials
Jute fibre of TD-4 quality (gradation following IS 271-2003) was procured from Jute Corporation of India. Ramie fibre of R-1411 (containing 26 – 28% gummy matters) variety was taken for this study. Freshly decorticated ramie fibres were collected from Ramie Research Station (ICAR), Sorbhog, India and subsequently degummed through enzymatic process [5]. Fibre properties of jute and ramie fibre are shown in Table 2. Table 2. Physical properties of fibres used in the study 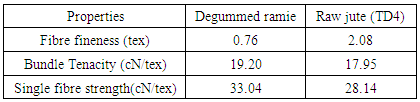 |
| |
|
3. Methods
3.1. Blending of Jute and Ramie Fibres in Customized Spinning System
Due to variation in fibre characteristics (viz. fibre length and fineness) blending of jute and ramie in fibre stage tends to create processing troubles. To avoid such difficulty of ramie and jute fibre blending in conventional jute spinning system, some customization in processing sequence were done (as shown schematically in Figure 1) and the modified system was explored in this study on trial basis to spin ramie and jute/ramie blended yarns.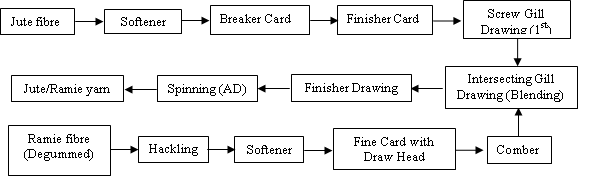 | Figure 1. Processing route of jute and ramie blends |
Jute fibre was processed individually in conventional jute spinning line upto 1st Drawing stage. 2% fibre lubricant (Jute Batching Oil as O/W emulsion) was sprayed over the jute, piled for 24 hours and subsequently processed through Softener, Cards and Drawing machines (as shown in Figure 1). Simultaneously degummed ramie fibre was undergone separately through modified spinning set-up (Figure 1) using same percentage of fibre lubricant. However, ramie fibres were allowed for 36 hours of piling. Jute sliver from 1st Drawing (Mackie, Screw Gill) and ramie fleece from Comber (N. Schlumberger, France) are blended at Intersecting Gill Drawing machine (N. Schlumberger, France). For getting uniform blending, Intersecting Gill Drawing process has been repeated twice. The the jute/ramie blended sliver was run through Jute Finisher Drawing (Mackie, Screw Gill) and subsequently fed to Apron Draft (AD) Spinning machine (Mackie, AD Spinning machine with 4¼” pitch) to produce final yarns.Four types of yarn (100% Jute, 80:20 Jute/Ramie, 50:50 Jute/Ramie and 100% Ramie) were spun under identical spinning conditions. Blending of jute and ramie fibres was restricted only to 80:20 and 50:50 blend ratios to ensure economical viability of the processing. Ramie being a costlier fibre than jute, it might not be a commercially feasible proposition to blend ramie fibre beyond 50%. In subsequent process, four different types of fabric (100% Jute, 80:20 Jute/Ramie, 50:50 Jute/Ramie and 100% Ramie) having identical construction- 69 ends/dm x 69 picks/dm; width - 51” were made using the spun yarns at Sulzer Loom.
3.2. Methods of Characterization of Fibre, Yarn and Fabric Properties
Strength (IS 7032 Part 7: 1986) and Fineness (IS 7032 Part 8: 1985) properties of both jute and degummed ramie fibres were measured in UTM (INSTRON-5500R) and Vibroskope (Lenzing Instruments, Switzerland) respectively. The single fibre strength was measured through window method and average of 50 tests has been taken. For measuring fibre fineness the individual test was repeated for 25 times. Tensile Strength (ASTM D-5035) and Tongue Tear Strength (ASTM D-2261) of four types of yarns and fabrics has been evaluated in INSTRON for comparative analysis. Abrasion-Resistance of yarns was measured in CTT Yarn Abrasion Tester, USA (ASTM 3884). Yarn imperfections and hairiness properties measured in PREMIER TESTER-7000 (ASTM D1425) to observe the effect of ramie blending on evenness properties of the blended yarns.To observe the effect of blending on fabrics, evaluation of physical, aesthetic and serviceability properties were carried out. Stiffness and Crease Recovery properties of fabrics tested in IJIRA Stiffness Tester (ASTM D1388) and Sasmira Crease Recovery Tester (BIS 4681-1968) respectively. Fabric Drape Co-efficient was examined in Cusick Drape Meter (BIS 3857-1977). Serviceability of fabrics was measured at IJIRA Fibre Shredding Tester (IJIRA Method). All the tests of fibre, yarn and fabric carried out in controlled laboratory conditions (65 ± 5% R.H and 80 ± 2°F temperature).
4. Results and Discussion
4.1. Effect of Blending Ramie Fibre on Jute Yarn
4.1.1. Effect of Blending on Yarn Count Realization
Yarns made out of different proportion of jute and ramie (100% Jute, 80/20% Jute-Ramie, 50/50% Jute-Ramie, 100% Ramie) under identical processing parameters were characterized to observed the effect of blending ramie fibre on yarn. Table 3 indicates that incorporation of ramie fibre in jute has improved yarn count realization. Under same processing conditions, 100% jute produces coarser yarn (i.e. 162.84 Tex) as compared to jute-ramie blended yarns (157.65 Tex and 155.94 Tex respectively for 80/20 and 50/50 jute/ramie blends) while 100% ramie yarn exhibits finer yarn (152.49 Tex). Also the count CV% has improved considerably for the blended yarns. So, it is perceivable that incorporation of finer ramie fibres has increased the yarn count realization along with minimized variations in count [6].Table 3. Count of yarns along with their co-efficient of variation (CV)  |
| |
|
4.1.2. Effect of Blending on Yarn Evenness
Introduction of ramie fibres in jute yarn structure tends to improve the yarn evenness by decreasing overall yarn irregularities and imperfections. It has been observed (Table 4) that there is significant reduction in short, medium and long term mass variations in ramie blended yarns compared to control (100%) jute yarn. Neps and Total Imperfections (TI) have also been decreased appreciably with percentage increase of ramie fibres in blended yarn. It can also be realized that due to incorporation of finer ramie fibre (0.76 Tex) with jute (2.08 Tex) in the yarn structure, number of fibres increases in unit cross-section of blended yarns which leads to improved yarn evenness [7]. Table 4. Characteristics of yarns with respect to Evenness Test 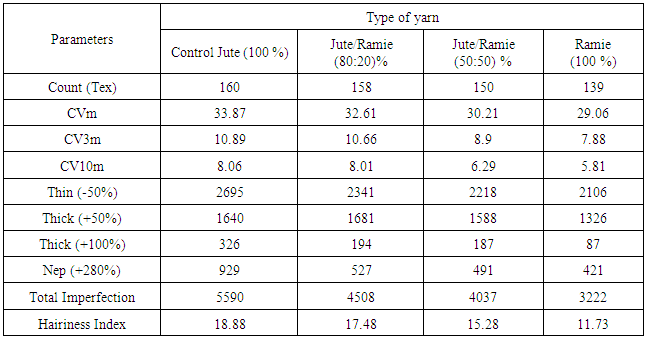 |
| |
|
Importantly, blending of ramie fibres has reduced the yarn hairiness. Table 4. indicates that Hairiness Index has gone down gradually with increase in ramie fibre percentage. Surface characteristic of 100% ramie yarn indicates much lower hairiness index with respect to the control jute yarn spun at same processing parameters. Smooth surface appearance in yarn is an essential aspect for value added hometextiles application. Comparatively longer fibre of ramie (80 – 120 mm) offers uniformity in yarn surface by wrapping the protruding short jute fibres [8].
4.1.3. Effect of Blending on Tensile Properties
Jute-ramie blended yarns represent significant improvement in tensile properties as compared to control jute yarn. Introduction of ramie fibre in yarn structure has increased both tenacity and extensibility of blended yarns as indicated in the Table 5. Individual fibre strength of ramie is almost 10% higher than single fibre strength of jute which has been reflected in the enhanced tensile properties of blended yarns (Table 2 and 5). Higher percentage of ramie fibre in yarns also enhances the strength CV% which strongly indicates improvement in process capability of blended yarns with respect to control jute yarn. Superior tensile properties of ramie fibre have also assisted in improvement in yarn abrasion also. It is evident that improved extensibility of blended yarns together with better abrasion properties supported them to restrict fibre loss during practical uses of ramie blended fabrics (Figure 3). Table 5. Tensile properties of the yarns 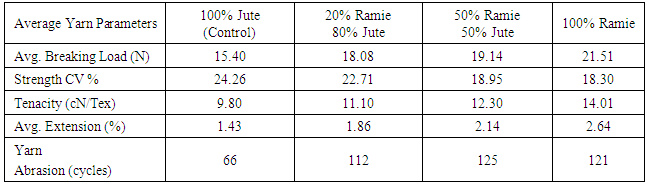 |
| |
|
Figure 2 indicates the Stress-Strain behaviour of 100% jute, 100% ramie and jute/ramie blended yarns (80:20, 50:50). From the graph it is apparent that breaking strength and extensibility of blended yarns increased significantly with increase in percentage of ramie fibre. It is also prominent that 50:50 jute/ramie blended yarns are representing almost equivalent Stress-Strain behaviour of 100% ramie yarn which suggests presence of 50% ramie give a synergistic benefit of tensile properties.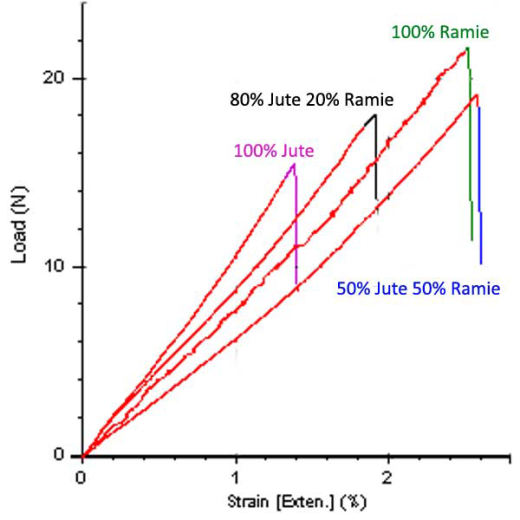 | Figure 2. Stress-Strain behaviour of the yarns |
4.2. Effect of Ramie Blending on Fabric Properties
Four types of fabric were developed with four different type of yarns (100% Jute, 80/20% Jute-Ramie, 50/50% Jute-Ramie, 100% Ramie) without cross mixing them in a single fabric. The construction (69 ends/dm x 69 picks/dm; width-51”) and process parameters were kept identical for preparing the fabrics.
4.2.1. Fabric Tensile Properties
Both warp and weft way tensile strength for ramie and jute/ramie blended fabrics are showing better tensile strength compared to control jute fabric (Table 6). Moreover, tear strength (warp and weft way) jute/ramie blended fabric is considerably higher than control fabric. Improvement in both tensile and tear strength certainly indicates longevity of ramie blended fabrics as hometextiles which are frequently subjected to tearing forces during practical uses. Table 6. Tensile and Tear strength of fabrics 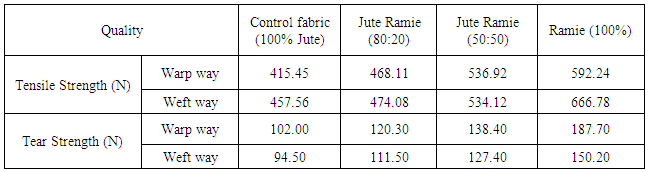 |
| |
|
4.2.2. Fabric Aesthetic Properties
Fabric flexibility and conformity to different product profile are essentially required for application in home-furnishing or hometextiles. Blending of ramie fibre within jute yarn has enhanced the flexibility (reduction of stiffness) of blended fabrics. Simultaneous improvements in drapeability (reduction in Drape Co-efficient) and crease recovery property (shown in Table 7) have enhanced overall aesthetic value of the blended cloths. Interestingly, in aesthetic point of view 50:50 jute/ramie blended fabric produces equivalent quality alike 100% ramie fabric which suggests that optimum property realization is achievable in 50:50 jute/ramie blending. Table 7. Stiffness and Drape properties of the developed fabric 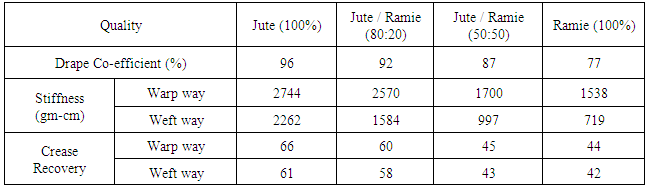 |
| |
|
4.2.3. Fabric Serviceability
Jute fabrics are prone to fibre shedding during actual use [9]. This phenomenon is considered to be detrimental for fabric serviceability while value added applications of jute fabrics are concerned. Actually, it has been observed that blending of ramie fibre along with jute has reduced fibre shredding tendency of control jute cloth considerably (Figure 3) leading to improved long term fabric performance. Fibre shredding quantity has been examined for all four types of fabric which indicates that incorporation of longer ramie fibre in yarn structure has reduced fibre shredding tendency. 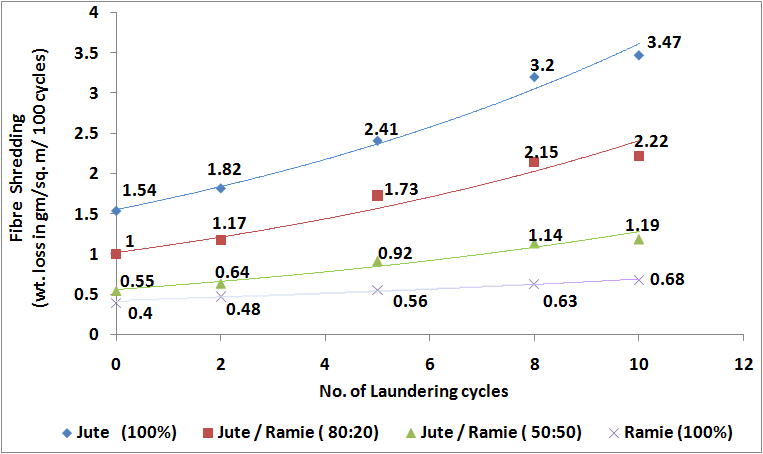 | Figure 3. Fibre shredding results of fabrics after successive laundering |
Fibre shredding of jute fabric is a matter of apprehension particularly when multiple laundering is concerned. However, heavy jute fabric based hometextile products are not subjected to washing frequently, perhaps, they are taken to laundering only couple of times in their entire service life. After multiple washing (2, 5, 8, 10) fibre shredding quantity has been examined for all four types of fabrics which indicates that incorporation of longer ramie fibre in yarn structure has reduced the tendency of jute fibre shredding under cyclic agitation and chafing. This particular characteristic is significant in order to create scope for induction of jute blended fabrics in hometextiles application.
5. Conclusions
In this study, ramie fibre has been efficiently blended with jute under a modified fibre processing set-up which is primarily based on jute spinning system. Three types of jute-ramie blended yarns (80:20 jute/ramie; 50:50 jute/ramie and 100% ramie) of equivalent count have been developed and compared the against control jute yarn (100% jute) in terms of physical and aesthetic properties. Significant improvement has been observed in Tenacity (13.2% and 25.5% increase for 80:20 and 50:50 jute/ramie blended yarns respectively), Extensibility (almost 50% increase for 50:50 jute/ramie blended yarn), Abrasion and Evenness properties of the ramie blended yarns compared to control jute yarn. Surface characteristics of the jute/ramie blended yarns have also improved (19% reduction in hairiness index) radically compared to 100% jute yarn of similar yarn count. Jute based textiles represents high fabric stiffness and rigidity which are limiting its applications in hometextiles. Functional finishing like softening can improve flexibility and feel but it is non-durable. Under this study, it has been clearly indicated that gradual induction of ramie fibre into the jute yarn structure has improved physical, aesthetic and serviceability properties of fabric in effective manner. Blending of ramie fibre has enhanced the drapability (Drape-co-efficient reduces from 96 for control jute fabric to 87 for 50:50 jute/ramie blended fabrics), flexibility, and fibre retention (anti-shredding) properties of the jute fabrics that tend to satisfy the aesthetics requirement of hometextiles. Hence, ramie fibre which bears similar fibre characteristics like jute can be blended with it for improvement of overall physical and aesthetic properties of the fabric which may attain the required qualification for high value textiles applications.
ACKNOWLEDGEMENTS
The authors acknowledge the financial support of National Jute Board, Ministry of Textiles, Govt. of India for carrying out the study. Authors are thankful to Dr. Prabir Ray, Director, Indian Jute Industries’ Research Association for his encouragement and support. M/S AI Champdany Industries Ltd, Kolkata, India, is duly acknowledged for their assistance extended during shop floor trials.
Abbreviations
IJIRA – Indian Jute Industries’ Research AssociationIS – Indian StandardO/W – Oil in WaterASTM – American Society for Testing and MaterialsBIS - Bureau of Indian StandardsUTM – Universal Testing MachineSG – Screw GillAD – Apron DraftCV - Co-efficient of Variation
References
[1] | A. Singhal. (2015), Technopak Advisors (India) [Online]. Available: http://www.technopak.com. |
[2] | Basu G. and Roy A. N., 2007, Blending of Jute with Different Natural Fibres, Journal of Natural Fibres, 4 (4), 13-29. |
[3] | Ganguli A. K., Aditya R. N., and Som N. C., 1980, Development of Products from Blends of Jute and Natural and Synthetic Fibres on Jute Spinning System- I&II, Man-made Textiles in India, 23 (7 & 8), 317-331; 410-417. |
[4] | S. K. Dey and S. K. Bhattacharya, 2002, Perspective use of Ramie Fibre in Blends with Jute., Proc., 24th IJIRA Technological Conference, Kolkata, India, 123-127. |
[5] | Biswas D., Nandi A., Chakrabarti S. K. and Ray P., Development of Sustainable Technology to Produce Jute-Ramie Blended Textile and Its Applications., Conference Paper in Materials Science, vol. 2013, article ID 578690, 109. |
[6] | Booth J. E., Principles of Textile Testing, 1983, Newnes-Butterworths, London. |
[7] | Goswami B. C., Martindale J. G. & Scardino F. L., 1976, Textile Yarns, John Wiley & Sons Inc., USA. |
[8] | Banerjee B. L., 1981, Variation of fibre length in jute - yarn sections of varying thickness and its possible role in controlling the unevenness of yarn caused by drafting., Journal of The Textile Institute, 72 (2), 63-68. |
[9] | Ghosh P., Das D., and Samanta A.K., 1994, Effect of selective pretreatment and different resin post treatment on jute/viscose upholstery fabric, Indian Journal of Fibre & Textile Research, 19, 277-282. |