Ratul Rehman 1, 2, Sakil Mahmud 1, 3, Md Ahsan Habib 1, 3, Ashraful Islam 1, 3
1M. Sc. in Textile Chemistry and Dyeing & Finishing Engineering, School of Chemistry & Chemical Engineering, Wuhan Textile University, Hubei, China
2B. Sc. in Knitwear Manufacturing Technology, BGMEA Institute of Fashion & Technology, Dhaka, Bangladesh
3B.Sc. in Textile Engineering (Wet Processing Technology), School of Science & Engineering, Southeast University, Dhaka, Bangladesh
Correspondence to: Md Ahsan Habib , M. Sc. in Textile Chemistry and Dyeing & Finishing Engineering, School of Chemistry & Chemical Engineering, Wuhan Textile University, Hubei, China.
Email: |  |
Copyright © 2015 Scientific & Academic Publishing. All Rights Reserved.
Abstract
Silk is the royal fibre and its coloration is also an art. There are wide ranges of dyestuff accessible for silk dyeing. Nearly every type of dyestuff used for cotton and/or wool can be used for dyeing silk. In overall the dyestuffs are useful by techniques similar to those of wool or cotton dyeing. Dyeing of silk with acid dyes required more than boiling temperature, resulting fiber damage and more energy. In this study, silk fabric was dyed with three commercial dyes. There are Lanasol reactive dyes (which are manufactured specially for protein fibers like silk & wool dyeing) then Liyuansol reactive dye (fluorine based dye which is specially manufactured for cotton dyeing) and finally, Lanacron acid dyes (which is commercially available for protein dyeing). The first and foremost aim of this study is to introduce fluorine based cotton-reactive dyes in silk under boiling temperate. On the basis of a number of experiments, influences of temperature, sodium sulfate consumption, time duration, sodium carbonate dosage and different pH were disclosed. Through orthogonal experiment, the optimum conditions of silk dyeing with above defined three dyes are defined. Results revealed that, fluorine based cotton reactive Liyuansol dyes has excellent or equal application performance at 90OC dyeing temperature like the dyes that is specially manufactured for protein fiber (Lanasol) or specially manufactured acid dye (Lanacron).
Keywords:
Reactive dyes, Acid dyes, Silk dyeing, Fastness, Protein fiber dyeing, Fluorine based reactive dyes
Cite this paper: Ratul Rehman , Sakil Mahmud , Md Ahsan Habib , Ashraful Islam , A Revolution of Silk Dyeing with FL Based Cotton-Reactive Dyes, International Journal of Textile Science, Vol. 4 No. 2, 2015, pp. 42-52. doi: 10.5923/j.textile.20150402.03.
1. Introduction
Silk is one of the most popular protein fiber extruded from animal. Because of its unique properties like wearing comfort, soft handle, good air permeability & elegant appearance its makes as the symbol of royalty [1]. It has been used as textile materials for a decade due to its excellences in super lustered, comfort, brilliant color shades obtained in dyeing & printing, tensile strength and so on. Although it containing all technical properties of fiber like strength, elasticity, resilience, drape ability, heat conductivity, absorbency, cleanliness & wash ability, shrinkage, effect of heat & light, resistance to mildew & insects and dye affinity but due to its serious inferiority in function performance, crease recovery, colorfastness to wash, dry and/or wet rub fastness, pholoyellowing resistance, colorfastness to perspiration, washing & wearing properties still limits its conventional uses in textile [2]. According to the customer demand, it is the right time for process the challenging goods of silk with outstanding features [3]. Up to present research, some researchers show in this field to improve the properties of fiber & fabric. This paper explains the major components of silk fiber, acid dyes and reactive dyes. This paper also enclosed with some evidence on the silk properties, silk chemistry and about acid & reactive dyes chemistry, methods of silk with Fluorine (Fl) based reactive dye which is specially designed for cotton dyeing & an acid dyes which is usually used for protein fiber. Finally, comparing the results between silk dyeing with acid & reactive dyes as well as fruitful discussions was presented. The fast & foremost aim of this research work is due to define the unique & even color dyeing process of silk dyeing with fluorine based cotton-reactive dyes. Of course dyeing performance is strongly prejudiced by the time, appropriate pH, dye bath concentration, fixing time, alkali dosage, amount of salt dosage as well as promoter consumption. The efficient dyeing principle was computed by altering the important variable parameters on dyeing equilibrium.
2. Literature Review
Protein is a sensitive fiber. Even dyeing with acid dyes at the boil caused some degradation, particularly on the prolonged boiling to promote dye migration. This causes hydrolysis of various proteins [4]. The dyeing of silk with acid dye is uneven even though the distribution of the dye liquor is perfect. Found the problems like (1) undyed, (2) particularly or ring dyed, (3) completely but light dyed, (4) completely but heavily dyed [5]. To overcome the above-mentioned problems dyeing should be carried out at boil for period of 1-8 hours, under a variety of pH (3-7). Dyeing at boil more than 1 hour is essentially unnecessary. But the bulk shade is 10% weaker than the laboratory matching or previously obtained bulk samples. So, it is required to topping additional dyes. It is expected that the future research in this field will be the automatic color matching, dyeing weighting and dispensing, and automatic dye bath control [6].
3. Silk Review
3.1. Chemical Composition of Silk
Various types of chemical components are composed in the chemical structure of the silk fiber. Here, I have presented a chemical composition of raw silk fiber. Fibroin (75%), Ash of Silk Fibroin (0.5%), Sericin (22.5%), Fat and Wax (1.5%), Mineral Salt (0.5%). This composition is calculated in 100%. It is important to know that, the fibroin is composed of 16 various amino acids. Raw Silk is composed of two filaments which are produced by the fibroin. These two filaments are adjusted by the gum which is known as sericin and different types of mineral salt, fat and wax also involved with it. This raw silk is treated for remove the gummy materials and various types of impurities from the silk by scouring process. Then the silk fiber is collected and supplied for producing silk fabric by weaving process [7].
3.2. Chemical Constituents of Silk
Silk is a natural protein, like wool fiber, due to this, mechanism of dyeing silk is dependent not only on free amino and carboxyl groups but also on phenolic with accessible –OH group. Because of slightly cationic character of silk with isoelectric point at above pH 5.0, it can be dyed with anionic dye such as acid, metal complexes, reactive and selected direct dyes. But the main objective of coloration of a textile fiber is that the permanency of the color and should not allow damage of natural abstract of fiber. This implies that it should not destroy its color during processing following coloration and dyeing & subsequent useful life (i. e. washing, light, rubbing, perspiration, and saliva) [8]. So whatever dyestuff we use for silk dyeing it is very essential to have permanency of that dyestuff. In this study there are three major components, which are silk fiber, acid dyes and reactive dyes. This paper starts with some information on the silk fiber and about acid dyes and re active dyes for silk are discussed. Finally, the results and discussions are presented [9].
3.3. Chemical Properties of Silk
Chemical properties of the silk fiber are given below [10]:1. Effect of acids and bases: Acids and alkalis cause hydrolysis of polypeptide chain present in the fibroin fiber. Acid hydrolysis causes more damage to fiber than alkaline hydrolysis. Acid hydrolysis attacks at nearly all the peptide linkages as compared to alkali hydrolysis which occurs at the end of the peptide chain. Concentrated sulphuric acid and hydrochloric acid will dissolve the fiber and nitric acid result in change of color of silk. Dilute acid do not attack the fiber under mild condition. Hot caustic alkalis readily dissolve the fiber. Weak alkalis attack fibroin when the treatment time at boiling point is prolonged.2. Effect of organic solvents: Organic solvents are used as dry cleaning solvents and they do not dissolve the silk fiber.3. Effect of oxidizing agents: Oxidation reactions are considered to take place at the side chains of tyrosine, the amino terminal residues of the main chains and at the peptide bonds. Silk fiber is susceptible to oxidizing agents. Therefore care is required during bleaching. Hydrogen peroxide and some peracids are used in bleaching of raw silk.4. Effect of reducing agents: Fibroin resists the reducing agents such as hydrosulphite, sulphurous acid and its salt.5. Color-fastness: The luster of silk will cause its dyed and printed silk textile materials to appear much brighter in color.
3.4. Physical Properties of Silk
There have a lot of physical properties of silk. Followings are the physical properties of silk:§ Color: The color of silk fiber could be yellow, brown, green or grey.§ Tensile Strength: Cotton is a strong fiber. It has a tenacity of 3.5 – 5 gm/den. The strength is greatly affected by moisture; the wet strength of silk is 75 – 85%, which is higher than dry strength.§ Elongation at break: 20 -25% at break.§ Elastic Recovery: Not so good.§ Specific Gravity: Specific gravity is 1.25 to 1.34.§ Moisture Regain (MR %): Standard moisture regain is 11% but can absorb up to 35%.§ Effect of Heat: Silk will withstand at higher temperatures than wool. It will remain unaffected for prolonged periods at 140C. Silk decompose at 175C.§ Effect of Sun Light: Sun light tends to encourage the decomposition of silk by atmospheric oxygen.§ Luster: Bright.
4. Dyes Review
4.1. Acid Dyes
Acid dyes are usually sodium salts of sulphonic acids, or less frequently of carboxylic acids, and are therefore anionic in aqueous solution. They will dye fibers with cationic sites. These are usually substituted ammonium groups in fibers such as wool silk & nylon. These fibers absorb acids. The acids can protonates the fibers amino groups, so they become cationic. Dyeing involves exchange of the anion associated with an ammonium ion in the fiber with a dye anion in the bath [4]Fiber-NH2 (s) + H+ (aq) + HSO4- (aq) → Fiber-NH3 + HSO4- (s)Fiber-NH3 + HSO4- (s) + Dye-SO3- → Fiber-NH3+ Dye-SO3 (s) + HSO4- (aq)An acid dye should have highly solubility in water and gives anion in acidic aqueous solution and which can react with cationic parts of the fibers. An acid dyes should have higher molecular weight in the range 300-1000 g/mole. The dyes with larger molecules have higher substantively for wool and nylon. Such dyes have slower diffusion in the fiber and therefore less ability to migrate and dye level. The more hydrophobic, high molecular weight dyes therefore have better fastness to the wet process. Anionic (Acid) dyes include many compounds from the most varied classes of dyes, which exhibit characteristic differences in structure (e.g., azoic, anthraquinone, triphenylmethane, and nitro dyes) but possess as a common feature water-solubilizing, ionic substituents. Sulphonated azo (acid) dyes constitute the major group and are mainly mono-azo & bis-azo compounds ranging in color from yellow, through red to violate & brown. There are some navy blue bis-azo dyes that can build up to gives black.
4.2. Reactive Dyes
Reactive dyes have proven to be one of the most successful classes of modern synthetic dyes. The reasons for this success lie in their shade versatility, their flexibility in application and the all-round good fastness properties obtained from dyeings produced with reactive dyes on wool, silk, cotton and regenerated cellulosic fibers [11].Reactive dyes may be loosely defined as chromophores which contain pendant groups capable of forming covalent bonds with nucleophilic sites in fibrous substrates. Providing these covalent bonds are stable to conditions encountered in laundering, the wash-fastness properties of the colorations will be outstanding [11].Reactive dye contain reactive group that allows fiber to react with dye by nucleophilic addition or substitution. One single dye can contain more than one reactive group (Figure 1). Difluorochloropyrimidine reacts with cellulose by nucleophilic substitution of labile chlorine, fluorine leaving group activated by adjacent nitrogen in a heterocyclic ring. In the other hand vinylsulphone group reacts with the cellulose by nucleophilic addition to a carbon-carbon double bond, usually activated by an adjacent electron attracting sulphone group (Figure 1). The sodium sulfonate groups make the dyes water soluable. Also –NH2; -OH; -SO3-; -N=N- can form covalent bonds with the cellulose containing –OH group [4].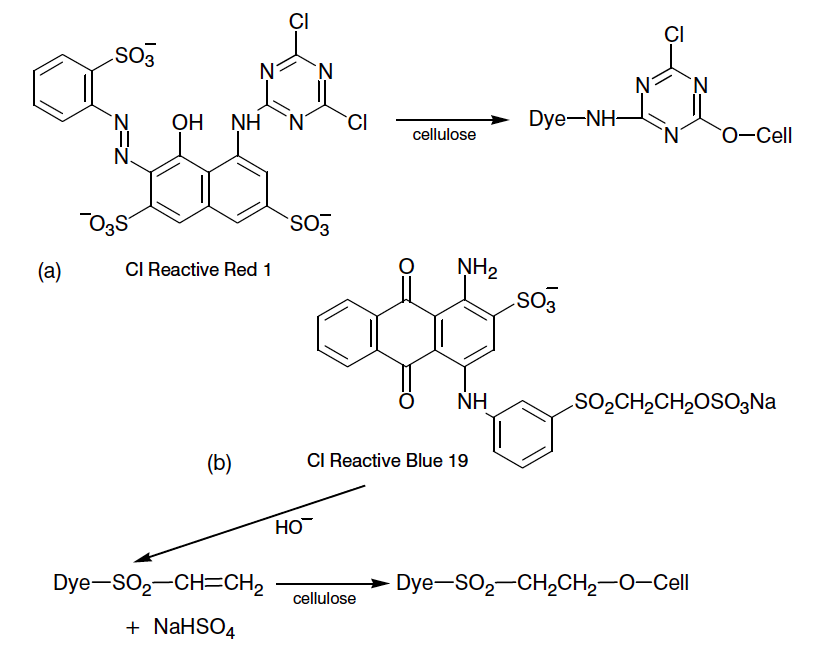 | Figure 1. Nucleophilic substitution (a) and addition reactions (b) of reactive dues with cellulose |
5. Dyeing of Silk
5.1. Dyeing of Silk with Acid Dyes
Dissolution of dyes in aqueous solvent produces a colored anion,
The protein and polyamide fibers produce cationic sites in water under acidic conditions, as the acidity of the solution is increased more cationic sites are produced under these strongly acidic conditions. These cationic sites are thus available for the acid dye anions to combine with through hydrogen bonding, vander waals forces or ionic bonding. These linkages are strong enough to break, and thus dyeing produced is fast. These contain acid groups, such as –COOH and –SO3H which form attractions to the slightly basic –NH groups in the amide links of wool, silk and nylon [12].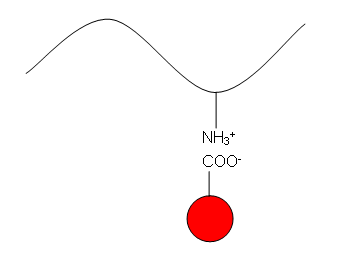 | Figure 1. How Acid dye attached with silk |
5.2. Dyeing of Silk with Reactive Dye
Exhaustion and fixation by a one-step process in an acidic or a neutral bath was the mode of dyeing used in silk & wool dyeing. Like cellulose dyeing, theory of dyeing of silk & wool was focused initially adsorption of the dye to the fibre surface from the dyeing bath, secondly diffusion of the dye into the interior of the silk fibre and finally fixation of the dye with reaction centers in fibroin [13]. At last but not least, changing the important dyeing parameters like fixation time, dyeing temperature, dye bath concentration, pH of the solution etc of dyeing equilibrium to develop a unique dyeing process of silk & wool with reactive dyes [14].
6. Experimental
6.1. Materials
All the used raw materials were of commercial grade and used without further purification. Silk sample was obtained from Hangzhou Dali Silk Co., Ltd. Sodium Carbonate (Na2CO3), Sodium sulphate (Na2SO4), Acetic Acid (CH3COOH) & Detergent are used from lab. LIYUANSOL FL: These fluorine based reactive dyes were obtained from Color Root (Hubei) Technology Company Ltd., China. Liyuansol series is a fluorine based reactive dyes contain a vinyl sulphone and a triazine group, they are economic and often used in the dyeing and printing process. Full range of shades and have some brilliant dyes. Those series are widely used for cotton dyeing. LANASOL: These reactive dyes were obtained from Huntsman Dyes. The LANASOL® range consists of sulfo-group-containing reactive dyes which have been especially developed for wool dyeing. They contain 1 or 2 bromo-acrylamide reactive groups which form a covalent bond with the nucleophilic groups of the wool’s amino acids during the dyeing process, resulting in outstanding wet fastness properties.
6.2. Methods
Here dyeing process was carried out by the common process of reactive in a bath having material to liquor ratio of 1:50 with different condition of the dyeing equilibrium in an automatic laboratory dyeing machine. Of course the dye manufacturers recommended processes were also followed initially. The dye solution was prepared initially by adding dye (owf) and distilled water at room temperature. Wet fabric was added to dye-bath then the dyeing process was inaugurated after 5 minutes. Raising the temperature at 80C & continue up to 25 minutes. The temperature was raised again to 90C temperature and dyeing was carried out 95 min. The pH of dyeing solution was maintained with acetic acid and sodium carbonate. The dyed material was then rinsed at hot (90C) water for 10min followed by cold water to remove the unfixed dye and dried at room temperature. 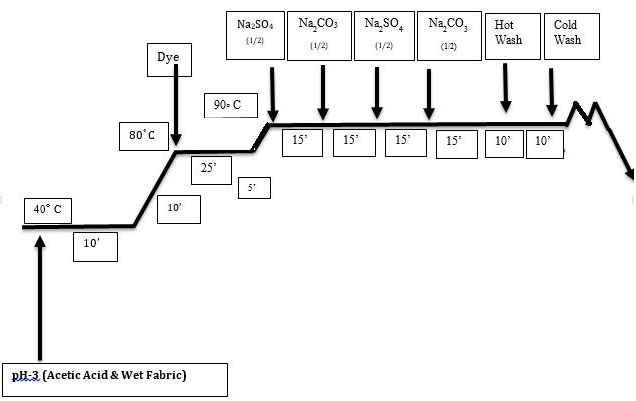 | Figure 2. Process curve of silk dyeing with reactive dyes |
6.2.1. Determination of K/S Value
K/S value of the dyed fabric is measured by using spectrophotometer (DATACOLOR®-110).
6.2.2. Determination of Dye Uptake%
Dye concentration was measured by a UV/VIS spectrophotometer and calculated dye uptake according to following equation:
C0 → Concentration of the Dye in solution before dyeingC → Concentration of the Dye in solution after dyeing (solution of after dyeing + solution after hot wash).For the accuracy of the result above equation was applied both dyeing & washing step. Finally resultant dye take up % was calculated.
7. Result & Discussion
7.1. Evaluation of Silk Dyeing with Reactive Dyes
Here dyeing performance is assessed by the time, appropriate pH, dye bath concentration, fixing time, alkali dosage, amount of salt dosage as well as promoter consumption to calculate an efficient dyeing principle by altering the important variable parameters on dyeing equilibrium.
7.1.1. Effect of pH on Silk Dyeing with Reactive Dyes on Dye Uptake and K/S Value
During observe the dyeing result under different pH, the other conditions were as follows- • Material and liquor ratio is 1:50• Dye is 3% (owf)• Na2SO4: Na2CO3 = 1:1• Time 100-120 min and • Temperature 80-90C.pH has a great influence on silk dyeing. Silk containing –NH2 groups are protonated (-NH2+) in the acidic solution. The more amounts of -NH2+ groups mean more chemical bonds with dyes. The Figure 4 shows that for both types of reactive dyes the dye uptake % is decreasing with the increasing of pH value of the dye bath. The dye uptake for both Lanasol (81.80%) and Liyuansol (67.00%) are highest at pH 3. Although at pH 4 the uptake of dye for Liyuansol is very good (62.03%) but for Lanasol has dramatically decreased (38.26%). 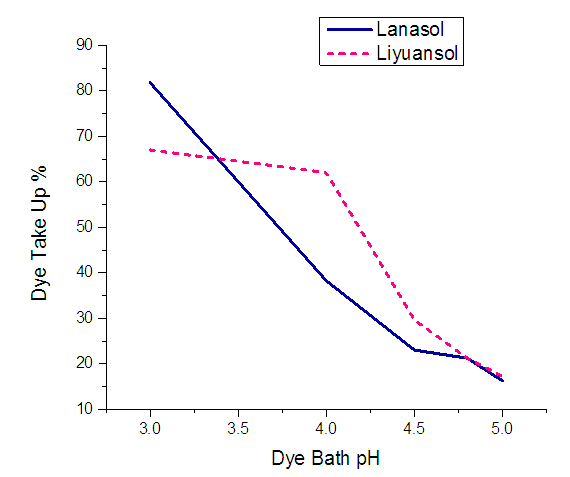 | Figure 3. Effect of pH on dye up % for Lanasol & Liyuansol Dyes |
As well as dye uptake the K/S of silk dyeing shows the similar result under different pH. K/S value is very high for both Lanasol and Liyuansol at very low pH; 3. When the pH increased at 4, the K/S of Lanasol decreased directly (6.95) and the K/S of the Liyuansol is almost stable (11.27). But for both dyes the K/S has decreased with the increase of the dye bath pH. 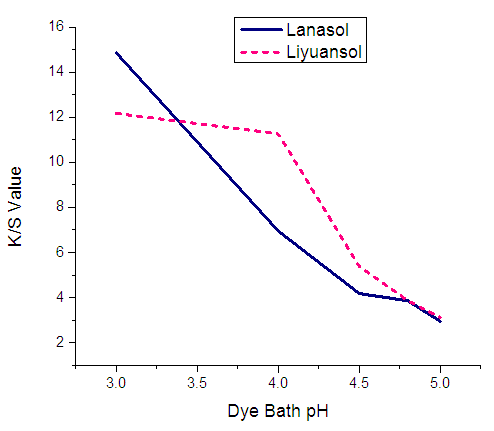 | Figure 4. Effect of pH on K/S value for Lanasol & Liyuansol dyes |
From Figure 3 & Figure 4 it is clear that the dye uptake and K/S both are very high at pH 3. And for Lanasol the results are changed noticeably while the results are stable for Liyuansol pH between 3-4.
7.1.2. Effect of Time on Dye Uptake and K/S Value during Silk Dyeing
The parameters were remaining unchanged except (see section 7.1) time (during the observation under different pH).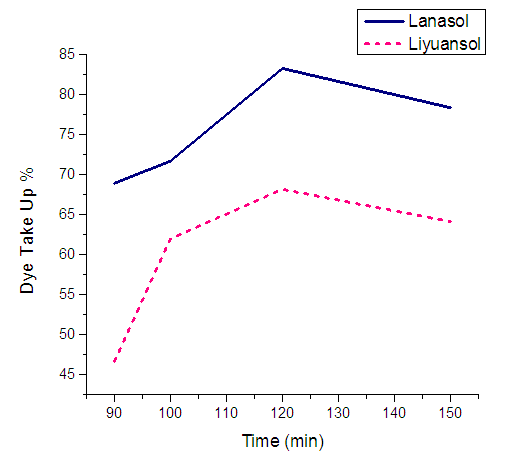 | Figure 5. Effect of dyeing time on dye uptake |
The optimum dye uptake and K/S value were found at dyeing time 120 min. (2hrs) at constant temperature 90C. Below 120 min and above 120 min the results were unsatisfactory. When the time goes more than 120 min the dye uptake decreased due to hydrolysis of some of the dyes. 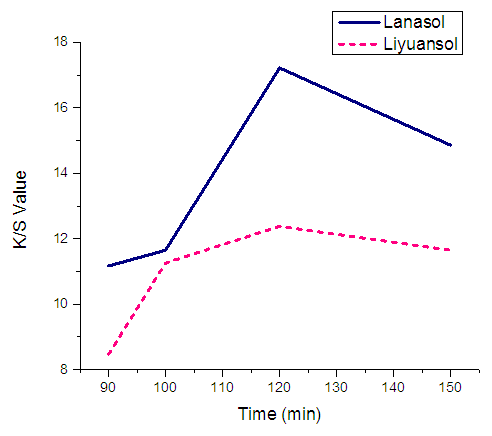 | Figure 6. Effect of dyeing time on K/S value |
The dye uptakes for Lanasol and Liyuansol at 120C are respectively 83.26% & 68.15%; and the K/S values are 17.22 & 12.38 respectively.
7.1.3. Effect of Na2SO4 & Na2CO3 on Dye Uptake & K/S Value of Silk Dyeing
Firstly the effect of salt is observed by dosing Na2SO4 & Na2CO3 after the dosing the dyes and acetic acid, and then dyeing is finished by above-mentioned method. But it was found huge color spot and uneven shade on the fabric. The effect of Na2SO4 & Na2CO3 are observed under the dyeing condition as follows- Material and liquor ratio is 1:50, dye is 3% (owf), pH 3.5, time 100-120 min and temperature 80-90C. Na2SO4 & Na2CO3 both salts are used during dyeing. The ratio of Na2SO4 & Na2CO3 is changed like 1:4, 2:3, 3:4, 4:1 and 1:1. The results for both dye uptake and K/S value are recorded in Table 1.The results were good at 1:1 for Lanasol. Although the results for Liyuansol was very good at ratio 3:4 but, to reduce the salt consumption the ratio of Na2SO4 & Na2CO3 is used 1:1. Table 1. Effect of Na2SO4 & Na2CO3 on dye uptake & K/S |
| |
|
8. Application Performance Testing
After getting of optimum dyeing condition above dyeing process evaluation, silk fabric was dyed in different dye concentration (1%, 3% & 5% owf) by using two commercial reactive dyes. Their different application performance tests were tested and compared with acid dyed silk sample that was dyed followed by general acid dying procedure.
8.1. Effect of Dye Concentration on Dye Uptake
Dye uptake enlarged gradually as dye concentration increased. With cumulative concentration, further dye moved to fabric and the deepness of color became stronger. From the above column illustration it is clear that the reactive dyes exhibit advanced dye uptake than acid dyes at higher colorant concentrations.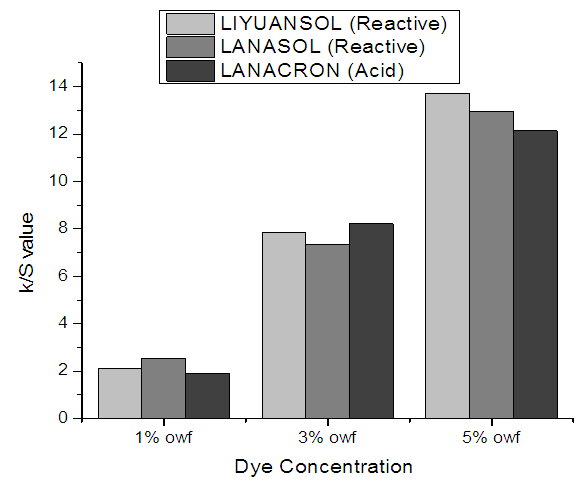 | Figure 7. Effect of dye concentration on K/S value |
8.2. Color Fastness to Wash
Dyed sample is prepared with sized 10 x 4 cm is taken and is sandwiched between two adjacent fabrics and stitched. The sample and the adjacent fabric were washed together. The washing solution was preheated to the required temperature of washing. The liquor ratio 1:50. After soaping treatment, the specimen is removed, rinse twice in cold water and then in cold running tap water. Squeezed and dried in air at a temperature not exceeding 60°C. The value is evaluated with the help of grey scales.Figure 8 Shows that CF to wash results was excellent for all concentration above 4. Only for Lanacron 5% shade the ratting is 4.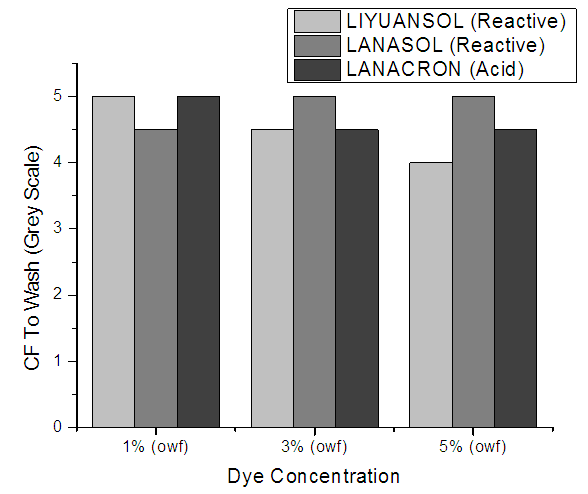 | Figure 8. CF to Wash for different Dye concentration |
8.3. Color Fastness to Dry-Rubbing
The test is quite sensitive and for getting consistent result, it is necessary to use standard crockmeter cloth, maintain uniform pressure for applying rubbing strokes and number of strokes. Degree of staining is visually assessed using Grey scale for change of color.The test showed excellent results on CF to dry rub. Figure 9 shows that, the result of CF to dry rub for both dyes (Lanasol, Liyuansol & Lanacron) excellent (4-5 & 5) for all dye concentration.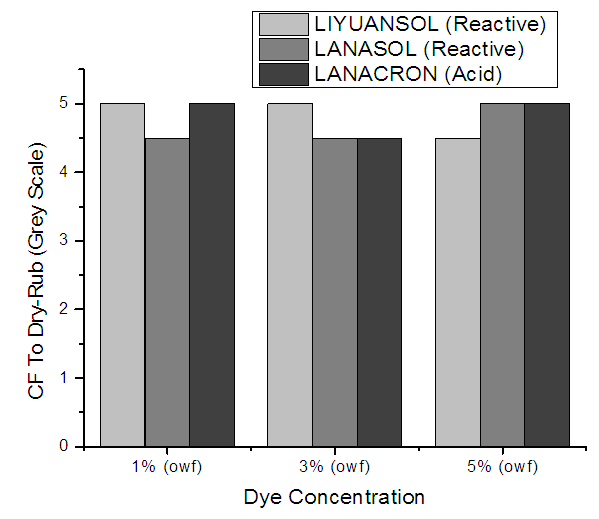 | Figure 9. CF to Dry-Rub for different dye concentration |
8.4. Color Fastness to Wet-Rubbing
In the case of wet rubbing, %moisture on the crock‐cloth has to be kept to uniform level and rubbing cloth that has been wetted with water, has to be squeezed to contain its own weight of water. For AATCC 116‐1995 methods, wet pick up is to be maintained between 65 ±5% by squeezing the wet crockmeter cloth using a AATCC blotting paper. Any variation in the moisture content can lead to deviation in the rating. With high amount of moisture i.e.., wet pick up, ratings will be lower. The Figure 10 shows the CF to wet rub for 5% dye concentration is a bit lower than the 1% & 3% but the overall results shows very good results.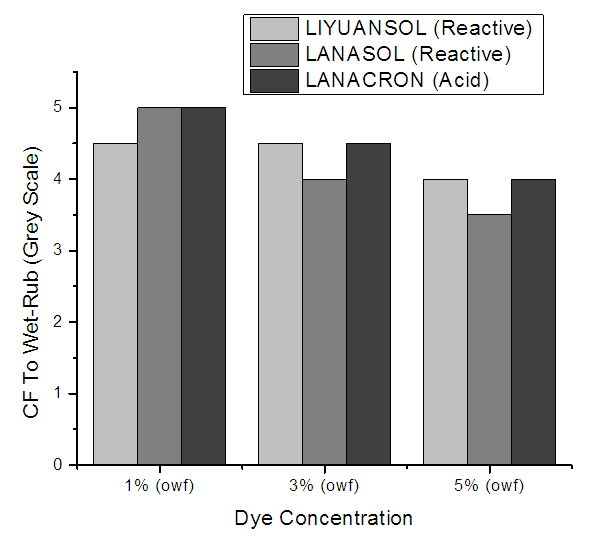 | Figure 10. CF to Wet-Rub for different dye concentration |
8.5. Color Fastness to Perspiration
The fastness of dyed fabric with respect to acidic & alkaline perspiration was evaluated. For the alkaline (pH‐8) and acidic (pH‐5.5) liquors were prepared and the composite specimens were dipped in acidic and alkaline solution separately for 30 minutes. After ensuring of good and uniform penetration solution, the liquor was poured off and the excess water and air bubbles, if any were removed by passing the specimens in between two glass rods. Composite specimens were then placed between glass/acrylic plates with a pressure of 12 kpa perspirometer. The perspirometer was kept for four hours at a temperature of 37 (±2C) Afterwards, the fabrics were removed, separated and dried in air below 60°C. The values were rated as per the grey scale. The assessment of colorfastness to perspiration for applied dyes and result change according to the greys scale reading for color change are shown in the Table 2. Table 2. Color fastness to perspiration (Result for color change) |
| |
|
From the assessment of Table 2, it can be said that the color fastness to perspiration for the color change according to grey scale for applied dyes both specially manufactured reactive dyes for protein fibre (Lanasol), commercial Fl based cotton-reactive dyes (liyuansol) and available acid dyes (lanacron) for silk/wool are shows satisfactory result.
9. Conclusions
This research shows that the specialized reactive dyes (Lanasol) specially designed for protein fiber (wool) dyeing exhibit good properties on silk. Also another Reactive dye (Liyuansol FL); that is fluorine based which is specially manufactured for cotton dyeing is suitable for silk dyeing. The dyeing procedure and auxiliaries were same for both dyes. So, fluorine based reactive dyes (Liyuansol Fl) for cotton can be used for dyeing silk fiber. The quality test result of silk with Fluorine based reactive dye shows very good to excellent result as the specialized wool dye (Lanasol) shows. It is also found an excellent or equal application performance as the acid dyes (Lanacron) which specially used protein fibre dyeing. The dyeing temperature was below boil so; the less or no degradation of protein as well as less dye migration will be happened. So, it can be recommend to use fluorine based reactive dyes for silk dyeing in textile industry to overcome the quality as well other processing problem that occurs with during protein fiber dyeing with Acid dye. Also it will be cost effective in term of using less auxiliaries, low energy to boil, less finishing chemicals to improve quality of acid dyed fabric. The homogeneity of the dye on various textile products in real baths needs further studies.
ACKNOWLEDGEMENTS
We would like to express our gratitude to Professor Jiang Huiyu (Vice Professor, School of Chemistry & Chemical Engineering, Wuhan Textile University) for his inspiring guidance, encouraging attitude and valuable suggestions throughout this research work. We would also like to thanks Mr. Chen for his co-operation during practical experiment. We also want to mention the mane of Color Root (Hubei) Technology Company Ltd.; because this work was financially supported by this company.
References
[1] | Shin, Y., Dyeing Properties and Color of Silk Fabrics Dyed with Safflower Yellow Dye. Journal of the Korean Society of Clothing and Textiles, 2008. 32. |
[2] | Liu, J. and H. Wang, Union Color of One Bath Dyeing to Silk/Flax Fabrics with reactives. Advanced Materials Reserch, 2011. 332-334. |
[3] | Zhang, G., L. Lu, et al., Dyeing Acceleration Theory of Molecule Companion on Silk with Reactie Dyes. Advanced Materials Research, 2102. 549. |
[4] | Broadbent, A.D., Basic Principles of Textile Coloration. 2001, England: Society of Dyers and Colourists |
[5] | Rush, J.L., Dyeing Primer. AATCC Journoul. 1981. 7-9. |
[6] | Lewis, D., Damage in wool dyeing. Review of Progress in Coloration and Related Topics. Society of Dyers and Colourists, 2008. 19(49–56). |
[7] | Silk fibre, Physical and Chemical Properties of Silk Fibre, . June 27, 2012 [cited 2015 April 05, 2015]; Available from: http://textilefashionstudy.com/silk-fiber-physical-and-chemical-properties-of-silk/. |
[8] | Bae, J.S., J.H. Park, et al., Dyeing and Fastness Properties of a Reactive Disperse Dye on PET, Nylon, Silk and N/P Fabrics. Fibers and Polymers, 2006. 17. |
[9] | Uddin, M.K. and M.S. Hossain, A Comparative Study on Silk Dyeing with Acid Dye and Reactive Dye. International Journal of Engineering & Technology IJET- IJENS 10(6). |
[10] | Protein fiber, the silk polymer and its system, NPTEL, E-learning courses from the IITS and IISC. |
[11] | LEWIS, D.M., Handbook of textile and industrial dyeing. Vol. 1. 2011, UK: Woodhead Publishing Limited. |
[12] | How dyes attach themselves to fabric, Salter’s Chemistry. April 05, 2015]; Available from:http://www.4college.co.uk/a/Cd/fabric.php. |
[13] | Koussoulou, T., Photodegradation and photostabilization of historic silks in the museum environment. Institute of Archaeology UCL, 1999. |
[14] | Hossain, M.F., Practice of textile coloration. Vol. 1. 2007, Dhaka: Book Fair Publications. |