Mainul Morshed
Department of Textile Engineering, Daffodil International University, Dhaka, Bangladesh
Correspondence to: Mainul Morshed, Department of Textile Engineering, Daffodil International University, Dhaka, Bangladesh.
Email: |  |
Copyright © 2015 Scientific & Academic Publishing. All Rights Reserved.
Abstract
This project is on RFT dyeing (Right First Time Dyeing) & determination of its limitations & effect on fabric processing. This is the way to develop new dyeing issue thinking on economic issue. During the production, we waste time, chemicals, dyes, moneys for a small problem. Sometimes fault occurs without having any fault. To find such kinds of occurrence I choose the above topic to get of loses.
Keywords:
RFT Dyeing, Calculation of dyes, Effect of miscalculation of dyes
Cite this paper: Mainul Morshed, RFT Dyeing & Its Effect, International Journal of Textile Science, Vol. 4 No. 1, 2015, pp. 20-26. doi: 10.5923/j.textile.20150401.03.
1. Introduction
Textile sector is the main foreign currency earning sector in Bangladesh because of cheap labor cost, good working environment, world class product & also safe investment. As a result, textile sector has grown up in Bangladesh very rapidly since 1985. Now a day’s thousands of textile industry is available in Bangladesh. On export quantity, we export 80% knit type product & 20% woven type product. These are the good side of our Textile sector. Textile sector can be divided in four groups, 1.Yarn manufacturing sector, 2.Fabric manufacturing sector, 3.Wet processing sector & 4.apparel sector. In Bangladesh textile product has higher % export quantity & most of them are cotton, for why I have done my project on Study on RFT dyeing & determination of its limitations & effect on fabric processing.In my work I’ve tried to find out the obstacles to get RFT dyeing, then I’ve tried to find out solutions of that problems.So in one sentence we may say that: It is a report on RFT dyeing to find out the proper way of dyeing cotton fabric.
2. Literature Review
2.1. Pre-Treatment Process
Before dyeing the textile material we need to treat that to dye or print them properly, such processes are known as pre-treatment process. The main purpose of pre-treatment processes is to obtain fabrics “Free from exterior impurities.” Pre-treatment processes include fabric inspection, batch preparation, singeing, desizing, scouring, bleaching & mercerizing process. [1] Purpose of Pre-Treatment:The purpose of pre-treatment is to produce a substance that has--ð Free from impurities,ð Even & rapid wetting of water,ð Uniform power of absorption of dyes & chemicals,ð Minimum fibre damages,ð High whiteness,ð Free from seed husk,ð Ready for dyeing & finishing. [2]
2.1.1. Inspection of Fabric/Yarn
At first the grey fabric has been checked for faults. It has carried out visually either on a traditional long inspection table otherwise using inspection machine. If the faults exceed more than the requirement & those cannot be mended, the goods will be rejected at this stage. [2]
2.1.2. Singeing
The process of reducing adjacent protruding fibres from the fabric/yarn to improve the smoothness & to get uniform fabric surface is known as singeing. Usually this process has carried out by passing into the burner. [2]
2.1.3. Desizing
Desizing is a process to remove size materials from the yarns of the fabrics. After solubilizing the size compounds are discharged from the surface of the yarn & then the fabric is washed & rinsed. [3]
2.1.4. Scouring
It is a process by which all natural & additive impurities such as oil, wax, fat, hand dust etc. are removed to produce hydrophilic & clean textile material. It is one of the vital processes of wet processing. [2]
2.1.5. Bleaching
Destruction of natural coloring matters to impart pure, permanent & basic white effects suitable for the production of white finisher, level dyeing & desired printed shade with the minimum or no tendering or without reducing the tensile strength is called bleaching. The mostly use bleaching agent is Hydrogen per Oxide (H2O2), which is also known as universal bleaching agent. [2]
2.1.6. Mercerization
It is a physio-chemical process where cotton/yarn is treated with 15-25% caustic soda solution at a temperature of 20-30℃. It is necessary to hold the fabric under tension & wash thoroughly. It is done for increasing lustre, fabric strength, dye affinity, abrasion resistance etc. [3]
2.2. Dyeing
The process of coloring the textile material with the help of dyes & various types of chemicals is known as dyeing. Dyeing process is also known as wet process because the process is saturated with water/solvent. Dyeing process is carried out by using different types of dyes which can impart permanent color & that color cannot be faded by any other conditions such as rubbing, perspiration, light etc. [4]
2.2.1. RFT Dyeing
RFT dyeing means “Right First Time Dyeing.” This term is used to define the dyeing efficiency, if the efficiency is more than the dyeing capability of that company is very good otherwise not good. This term actually defines how we can dye a fabric. If we can complete our dyeing at first time then we can say that this is RFT dyeing but if we cannot than we say that this is not RFT dyeing. So we can say that----“If the dyeing process is completed properly without any fault & there is no need to put the dyed fabric into the bath to get the proper shade then this dyeing is called RFT dyeing.” Objects of RFT dyeing:i) Increase productivity:The productivity of a company can be increased if the RFT efficiency increased.ii) Reduce time consumption:If the dyeing completes in first time then it will take less time than the 2nd time dyeing.iii) Increase profit:If the productivity increases then the profit will be increased too. iv) Less fabric damage:If the dyed fabric put 2nd time in a bath then there is a possibility to damage the fabric. So in a RFT dyeing this possibility is reduced.v) Reduce cost:If the dyed fabric dyeing 2nd time then we need extra dyes & chemicals. In RFT dyeing we do not need this, so cost will be reduced.
3. Analytical Survey
In the floor of production of dyed fabric the main challenge is that to complete the dyeing process without any faults that means to get proper shade after the first bath. But sometimes the shade of the fabric does not match & the fabric again put on the bath to get the proper shade. If the shade is lighter than the sample fabric then we have to bath the fabric with the required dyes & chemicals. If the shade is deeper than the sample fabric then we have to bath the fabric with acetic acid to take out the extra dyes. If we put the fabric in the bath 2nd time, this is not RFT dyeing. By putting the fabric 2nd time in the bath reduce the dyeing efficiency of a dyeing mill. If we can complete our dyeing process first time then the productivity of a dyeing mill will be increased.Now the question is why the shade of the fabric does not match easily & how we can complete our dyeing in 1st time bath. To get the RFT dyeing following problem may be effect the dyeing process.One of the main problem is to achieve the RFT Dyeing is the very little calculation variation of chemicals and dyes. Without our knowledge we make mistakes during getting the chemicals.Table 1. Dyeing Recipe 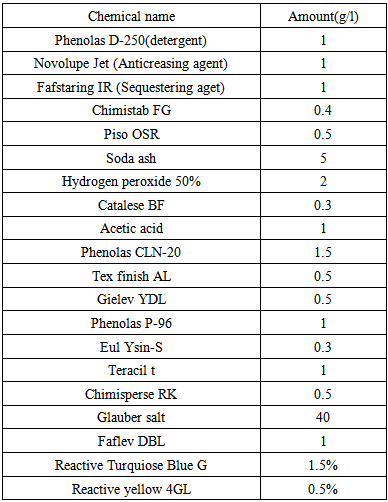 |
| |
|
When we add chemicals or dyes in a bath, there is a possibility of imbalance dozing which may vary from the sample recipe. When we dozes the dyes or chemicals manually, this time we may take dyes or chemicals more or less than the recipe. In a lab the differences of taking more or less chemicals does not seem but they have the effect during dyeing the fabric. For why, in the lab we can get the proper dyed sample according to the buyer recommendation, but in the bulk production the differences are so big & that time the effect of more or less chemicals come in sight. That’s the main reason for the limitation to get RFT dyeing.
3.1. Calculation
Let, we have to dye a knit cotton fabric with reactive dyes & the shade% is 2. Now if we use same recipe in lab & bulk production then what will we get is describing below---
3.1.1. In Lab
Shade% 2 means, we have to take two kg dyes for hundred kg knit cotton fabrics. But in the lab the weight of the fabric sample is so little. That means we require less amount of dye for dyeing sample fabric.For measuring solid dye:Let,Shade % = 2 owfFabric wt. = 5 gramsM: L = 1:40According to the above recipe,We need 40ml water for 1gm. fabricThat means total liquor = (40×5) = 200 mlWe know that,Dye = Shade% × Fabric wt.So that for the above data, required dye is-----
So, we need 0.1 gram dye to dye the 5 gram fabric. But this 0.1 amount is difficult to measure in the digital balance. If we measure then we cannot get proper amount because when we measure it in the balance there are some factors come in sight. They are -----ð Surrounding atmosphere:During the measuring with the balance surrounding atmosphere should be considered. The pressure of air, humidity & temperature of the air may effect on the measurement. During the time of measuring we should work in a standard atmosphere & also neglect the air of pressure.ð Wt. of supporting material:In lab we are using a pot or paper to weigh the chemicals. This supporting material has its own weight. So during the measurement of chemicals the supporting material’s weight should be avoided. ð Accuracy of the machines:The accuracy of the machine is a very important factor. When we measure something with the balance then we cannot take the exact amount. Let, we will take 0.11 gm. dye for 5 gm. fabric. Here, we take 0.01 gm. dye extra which also has the effect on the fabric. That means we dyed the fabric with 0.01 gm. extra dye & after dyeing with that extra dye we get proper shade.First two can be minimized but the third factor we cannot avoid, because we are not able to take exactly the same amount what we look for. Such as, we have to take 0.110gm. or 0.104gm. or 0.101gm. instead of 0.1 gm.
3.1.2. For Measuring Dye Solution
Sometimes we prepare stock solutions to take the proper amounts of dyes & chemicals. It is done when we have to take a very little amount because it is impossible to measure in digital balance.Let, we have to make 5% stock solution of dye.5% stock solution means, a solution of 100ml water which contains 5 gm. solid dyes. If the dye is in liquid form then, 5% stock solution means, a solution of 95 ml water which contains 5ml liquid dyes.For the stock solution the formula of the “Dye” will be --Dye % = (Shade % ÷ Stock solution %) × fabric wt.So that for the above data, required dye is-----
So, we need 2ml dye solution to dye the 5 gram fabric.Now, the problem is we have to add the dye solution in the bath by using the pipette. When we do it manually then we cannot measure proper amount of solution. By seeing the level of solution in the pipette we take the dye solution. We may take little more or less amount of solution in the bath.Let, we take 0.1ml more or less dye solution instead of 2 ml dye solution. Here, we take 0.1ml dye solution more or less than the required dye solution. That means we dyed the fabric with 1.9 or 2.1ml dye solution & after dyeing with that we get proper shade.Here,100ml dye solution contains 5gm. Dye

That means we dyed the fabric by using (0.1- 0.105) or (0.1-0.095) gm. i.e. 0.005 gm. more or less dye. So, we get proper shade by using 0.005 gm. more or less dye.From the above, we find that we are taking 0.005 gm. more or less dye for 5 gm. fabric. Here, 0.005 amounts are very little which is negligible. If we convert in percentage, then we will find the difference.Here, For 5 gm. fabric we take 0.005 gm. more or less dyeFor 1 gm. fabric we take (0.005 ÷ 5) gm. more or less dyeFor 100kg fabric we take (0.005 ÷ 5) × (100 ×1000) gm. more/less dye = 0.001 × (100 ×1000) gm. more/less dye= 100 gm. more or less dye= 0.1 kg more or less dye= 0.1% more or less dye
3.1.3. In Bulk production
Let,Shade % = 2 owfFabric wt. = 1000 kgM: L = 1:8According to the above recipe,We need 8 liter water for 1kg fabricThat means total liquor = (1000 × 8) = 8000 LWe know that,Dye = Shade% × Fabric wt.So that for the above data, required dye is-----
So, we need 20kg dye to dye 1000 kg fabric.For Measuring Solid Dye:In the lab we took 0.11 gm. dye for 5 gm. fabric.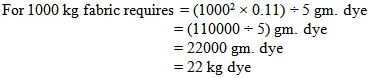
So, in bulk production we dyed the fabric by using 2 kg less dye. For why the shade of the fabric does not match & the fabric will be put in 2nd time with require amount of dyes & chemicals.For Measuring Dye Solution:In the lab we took 0.105 gm. dye for 5 gm. Fabric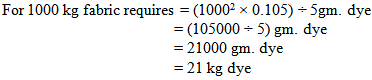
So, in bulk production we dyed the fabric by using 1 kg less dye.Or, In the lab we took 0.095 gm. dye for 5 gm. fabric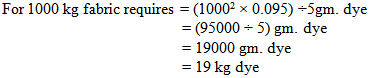
So, in bulk production we dyed the fabric by using 1 kg more dye.So, in bulk production we dyed the fabric by using 1kg more or less dye. For why the shade of the fabric does not match & the fabric will be put in the 2nd time to get the proper shade.
4. Experimental Review
4.1. Lab Work
Table 2. Dyeing Recipe in Lab 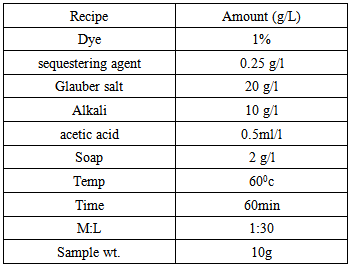 |
| |
|
According to the table (Table 2.) we have to take 1 gm. dye for 100 gm. fabric.So for 10 gm. fabric we need (1×10) ÷ 100 gm. dye = 0.1 gm. dyeNow, during the weighing of dye we took 0.101 gm. dye to dye and we get the following resultant dyed fabric---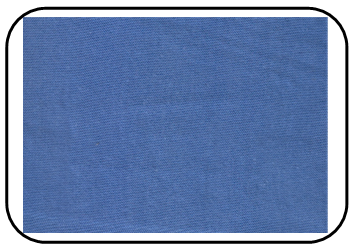 | Figure 1. Lab Sample (dyed with 1.101 gm. dye) |
4.2. Bulk Production
Table 3. Dyeing Recipe in Bulk Production 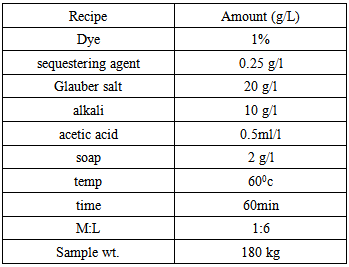 |
| |
|
Now,For 180 kg fabric we need (1×180) ÷ 100 kg dye = 1.8 kg dyeAfter dyeing the fabric with 1.8 kg dye we have got the following resultant dyed fabric---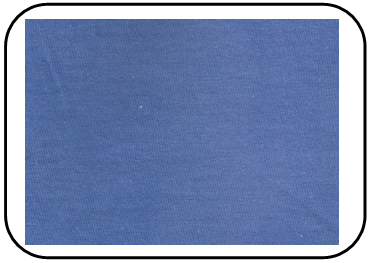 | Figure 2. Bulk Sample (dyed with 1.8 kg dye base on lab receipe) |
From the above two sample we can easily find that the bulk dyeing is not proper due to the less amount of using of dye.We needed (1.101×180) ÷ 100 kg dye = 1.98 kg dyeThat means for the less of 0.18 kg dyes we got light shade fabric.To get the proper shade we need to dye that fabric again. To get that shade we need to run the whole dyeing process again which will increase the process cost.If we took 1.98 kg dye then there was a probability to get the properly dyed shade on first time dyeing.
5. Result & Discussions
5.1. Effect
Let, the cost of dyes are 10 US Dollar/kg.If, a company has an order of 5000 kg fabrics which have to be dyed.For, 5000 kg fabric the amount of required dye is = (Shade% × Fabric wt.) = (2 ÷ 100) × 5000 kg = 100 kg
Above we found that, for 100 kg fabric we used 0.1% more or less dye.Now, for 100 kg fabric if we use 100 gm. more dye,Then, for 5000 kg fabric we are using = (5000 × 100) ÷ 100 gm. more dye = 5000 gm. more dye = 5kg more dyeThat means, we are using 105 kg dyes.

That means we are wasting 3,000 US Dollar in a month. The amount of loss is so huge. If we calculate all chemicals from pretreatment to dyeing then the amount of waste will be increased.
5.2. Probable Solutions
From the above discussions we can easily find out that the limitation to get the RFT dyeing is the manual measurement of dyes and chemicals. If we can minimize this problem then we can get the Right First Time dyeing. For increasing RFT efficiency this problem should be minimized. I am trying to find out the solutions of this problem. The solutions are given below-----
5.2.1. Use Exact Amount of Chemicals
We face problems to get RFT efficiency in bulk production because of not measuring the exact amount. If we indicate the proper amount use in lab then during the bulk production we may not face problems to get RFT Dyeing.Such as, if we use 1.01 gm. dye in lab then we need to write the exactly that amount. So during the bulk dyeing people will calculate according to the 1.01 gm. dye.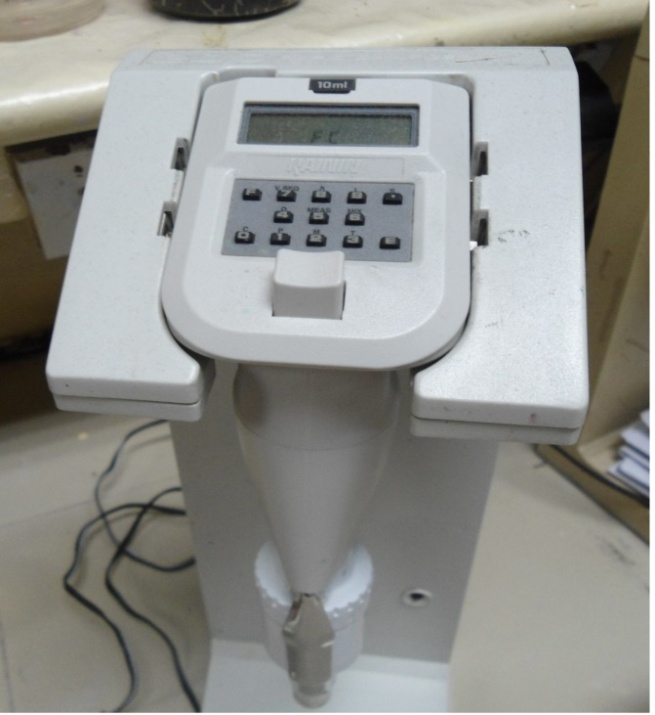 | Figure 3. Pipette Machine |
5.2.2. Computerized Dozing
To get the proper & appropriate amount of the dye solutions in the lab we have to use a machine which can prepare the solutions. Such types of machines are pipette machine, robolab etc.Specifications of Pipette Machine:Ø Model no: 10500T30Ø Manufacturer: USAØ Power: 6V, 100mAØ Capacity: 10 mlFunctions of pipette machine:It helps us to prepare the exact amount of the solutions. It looks like a pipette which contains a measuring device on the upper portion of the pipette. The device contains some buttons & a display. The solutions are made into a pot. Then the pipette machine is filled with the solutions. Then required amount of the dye solutions are set up in the machine & then the machine can put the exact amount of the solutions into the bath.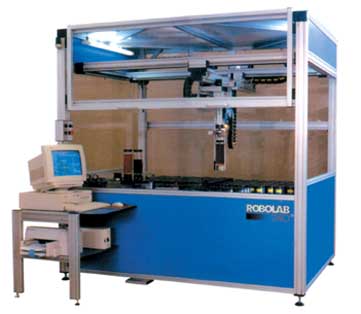 | Figure 4. Robolab Machine |
Specifications of Robolab:Ø Manufacturer: TalosØ Machine name: Talos RoboticsØ Model no: 66100 BramaGRØ Manufacturing year: 2010Ø Serial no: 1069Ø Total weight: 800 kgØ Electrical features: 220VØ Max. current: 20 ampØ Pay load: 2 kgAdvantages of Robolab:Ø 80 powders/different dyes can be taken at a time,Ø Computer controlled,Ø 36 pipette can be used at a time,Ø After giving instruction no need to do anything,Ø Save dyes & chemicals,Ø Time consuming machine,Ø Fully automatic machine.Disadvantages of Robolab:Ø Very costly machine,Ø Need proper care,Ø Skilled operator is required,Ø Need enough space to machine set up.
6. Conclusions
After all of this hard work I had reached to this decision that RFT dyeing is very important terms to get the proper & economical dyeing. If we can increase the RFT efficiency of a dyeing factory we can save money & time & we can also increase the productivity. Whatever the lack of knowledge about RFT dyeing among the worker and also the employer is the main problem to get RFT Dyeing.RFT dyeing can reduce both the time and the dyes & chemical cost. It can provide a more worthy process to dye the fabrics. If we can successfully integrate the RFT process then the fabric faults will be minimized regarding with the dye shade%. In the 21st century we still dye the fabrics in conventional process. To face the challenge of the 21st century we have to increase the RFT % by increasing knowledge about it & apply the processes effectively. I hope in near future we will increase the RFT efficiency & we will get proper dyeing shade at the first time by gathering more knowledge on it & also applying the modern techniques.
ACKNOWLEDGEMENTS
At the very beginning I acknowledge the infinite blessing & profound kindness of "Almighty Allah"- The supreme authority of the universe. I also acknowledge the loving support of my parents & family members.Mr. Md. Rabiul Islam Khan Lecturer, Department of Textile Engineering, Daffodil International University, my supervisor, to whom I am extremely grateful for his tremendous support & guidance throughout my work.Being working with him I have not only earned valuable knowledge but was also inspired by his innovativeness which helped to enrich my experience to a greater extent. His ideas & way of working was truly remarkable. I believe this project could not be finished if he did not help us continuously.I would like to thank Professor DR. Md. Mahbubul Haque, Head of the Department of Textile Engineering, Daffodil International University, who has inspired me to take & continue this project.Last but not the least, thanks go to all the people who have assisted, helped & inspired me to complete this task at various stages.
References
[1] | Karmakar, S.R., Chemical Technology In The Pre-Treatment Processes of Textiles. 1st ed. 1999, Amsterdam: Elsevier. |
[2] | Kan, C.W., A Novel Green Treatment For Textiles, ed. M.C. Cann. Boca Raton. |
[3] | Lacasse, K. and W. Baumann, Textile Chemicals- Environmental Data and Facts. 2004, Dortmund, Germany: Springer. |
[4] | Trotman, E.R., Dyeing And Chemical Technology Of Textile Fibres. 4th ed. 1970, London: Griffin. |