Mohammad Gias Uddin1, Nayon Chandra Ghosh2, Md. Shamim Reza3
1Department of Textile Engineering, Faculty of Engineering, Ahsanullah University of Science and Technology, Dhaka, Bangladesh
2Department of Textile Engineering, Primeasia University, Dhaka, Bangladesh
3Aswad Composite Mills Ltd., Shreepur, Bangladesh
Correspondence to: Mohammad Gias Uddin, Department of Textile Engineering, Faculty of Engineering, Ahsanullah University of Science and Technology, Dhaka, Bangladesh.
Email: |  |
Copyright © 2014 Scientific & Academic Publishing. All Rights Reserved.
Abstract
Dyeing was carried out on cotton fabric using Novacron Blue FN-R and Novacron Brilliant Red FN-3GL dyes in 0.5%, 1.5% and 4% shades using soda ash and eco-alkali. One-half, one-fourth, one-sixth and one-eighth amount of eco-alkali was used to analyze the performance of eco-alkali in comparison to the required amount of soda ash for the three shade%. Then color yield (K/S value), fixation efficiency (%), pH of wash liquor after dyeing, washing fastness and color uniformity results of dyed fabrics were analyzed and compared. Color yield was found better using one-fourth amount of eco-alkali in 0.5% and 1.5% shades and using half amount of eco-alkali in 4% shade. Fixation efficiency was found better using one-fourth amount of eco-alkali. pH of the wash liquor after dyeing was found less in case of using eco-alkali. Washing fastness and color uniformity of dyed fabrics were also comparable using lower amount of eco-alkali.
Keywords:
Cotton, Reactive dye, Eco-alkali, pH, Color yield, Fixation efficiency, Color uniformity
Cite this paper: Mohammad Gias Uddin, Nayon Chandra Ghosh, Md. Shamim Reza, Study on the Performance of Eco-Alkali in Dyeing of Cotton Fabric with Reactive Dyes, International Journal of Textile Science, Vol. 3 No. 3, 2014, pp. 51-58. doi: 10.5923/j.textile.20140303.03.
1. Introduction
Reactive dyes are the widely used dyes all over the world. Most of the dyeing operations of cellulosic fibers are done by reactive dyes which have the worldwide acceptance to the dyeing technologists. This water soluble dyes get exhausted on the cellulosic fiber in the presence of glauber’s salt at neutral pH. Under alkaline conditions fixation is carried out in which covalent bond forms between reactive sites of fiber and cellulosic material [1]. But this alkaline condition also facilitates the reaction of reactive group with the dye liquor, resulting in deactivation or hydrolysis of the dye [2]. Normally soda ash is used as the most commonly used alkali in the dyeing bath. The important point is not the type or amount of alkali, but the pH of the bath. However, dye fixation on cellulosic fibers is generally low (Often less than 70%) [2]. This results in a highly colored dye house effluent which is not favorable for the environmental grounds. As much as 50% of the total cost of a reactive dyeing process is attributed to the washing off stages to remove unfixed or hydrolyzed dyes and treatment of the resulting effluent [1]. Furthermore, the higher concentrations of alkali required in cellulosic dyeing may pose additional effluent problems. Under this circumstance, eco-alkali can be used in place of soda ash in dyeing of cotton fabric with reactive dyes. Due to having higher fixation%, it can produce better color yield on cotton fabric, hence dye wastage can be less in reactive dyeing and consequently can create less effluent problem. Furthermore, as less amount of eco-alkali can be used to produce better color yield, the pH of wash liquor after dyeing can be reduced which facilitates the post-dyeing neutralization process. The unfixed and hydrolized dyes causes difficulities if not washed and neutralized properly, as a result, in the soaping process, soaping bath will act as a dyeing bath in the presence of alkali and high temperature which can cause color change in the dyed fabric.That is why, pH of wash liquor need to be measured after dyeing in both cases using soda ash and eco-alkali.In this study, cotton fabric was dyed with reactive dyes using soda ash and its lower amount of eco-alkali; then color yield and fixation efficiency were compared. After dyeing, pH of the wash liquor was compared in both cases. Color uniformity and washing fastness test of the dyed fabric were also compared in both cases.
2. Materials and Methods
2.1. Materials
2.1.1. Fabric
The grey 100% cotton knit fabric (Single Jersey) of about 164 gm/m2, procured from Dulal Brothers Limited, Nayapara, Kashimpur, Gazipur, Bangladesh was used throughout the present study.
2.1.2. Dyestuffs
Bi-hetero type Novacron Blue FN-R and Novacron Brilliant Red FN-3GL reactive dyes were purchased from Huntsman, Bangladesh.
2.1.3. Eco-alkali
Soda ash substitute, also called updated soda ash. It is a mixture of multiple alkalis and a perfectly optimized alkali buffer of Zhejiang Runhe Chemical New Material Co. Ltd. China, taking place of sodium carbonate in reactive dyeing process of cotton fabric. It is available as white powder form, anionic and soluble in water. Manufacturer claims that it is eco-friendly and saves cost compared to soda ash as its 1/8th to 1/10th amount is sufficient to get required shade than what soda ash does, its reproduction from lab to bulk is excellent, its fixing performance is slow and stable, also improves the leveling problem specially for Turquoise blue and green color.
2.1.4. Chemicals and Auxiliaries
All the chemicals and auxiliaries used for the experimental work were of laboratory grade reagent.
2.2. Experimental Methods
2.2.1. Preparatory Process
For scouring and bleaching purposes, grey fabric was prewashed with the bath liquor containing 4 ml/l hydrogen peroxide (35%), 3 g/l caustic soda, 1.25 g/l sodium silicate as stabilizer, 1 g/l wetting agent and 1 g/l sequestering agent at pH 10.5, material to liquor ratio 1:50, temperature 90°C for 60 minutes, then washed thoroughly with 2g/l detergent followed by neutralization with 1 g/l acetic acid.
2.2.2. Dyeing
Dyeing was carried out in isothermal method using alkali and eco-alkali with the three shade% (0.5%, 1.5% and 4%) at 60°C for 60 minutes, keeping material to liquor ratio 1:10 (Weight of fabric in gm; amount of liquor in ml) in the laboratory IR sample dyeing machine. Then dyed fabric was washed with water at 60°C, and pH of the wash liquor was measured followed by neutralization with 1% acetic acid at room temperature for 10 min, and finally soaping with 1 g/l soaping agent at 80°C for 10 min.Dyeing recipe for different shades of reactive dyes is given in Table 1.Table 1. Dyeing recipe 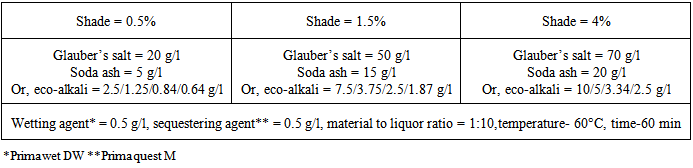 |
| |
|
2.2.3. Color Yield of Dyed Fabrics
Dyed textile samples were analyzed by measuring the reflectance curve between 350 and 750 nm with a dual beam reflectance spectrophotometer with illuminant D65 at 100observer. The minimum of the curve (Rmin) was used to determine the ratio of light absorption (K) and scatter (S) via the Kubelka-Munk function (Equation 1) [3, 4].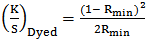 | (1) |
2.2.4. Fixation Efficiency
Fixation efficiency was measured by the equation 2 [5-9].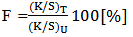 | (2) |
Where,‘T' refers to fabric treated in soap solution after dyeing,‘U’ refers to untreated sample after dyeing.
2.2.5. Color Uniformity
Color uniformity was calculated by measuring K/S values on 10 random sample spots at maximum absorption wave length
using equation 3 and equation 4 [10].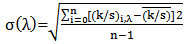 | (3) |
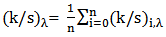 | (4) |
Where,
is the standard deviation of each random spot K/S value with
is the maximum absorption wave length, n is the number of measured spot,
is the K/S value of each random spot. Color uniformity, expressed by
improves when
value decreases.
2.2.6. Color Fastness to Washing
Color fastness to washing test was carried out following ISO 105 C06 [11].
3. Results and Discussions
3.1. Color Yield of Dyed Samples
The K/S values of dyed samples were expressed through Figure 1 and Figure 2.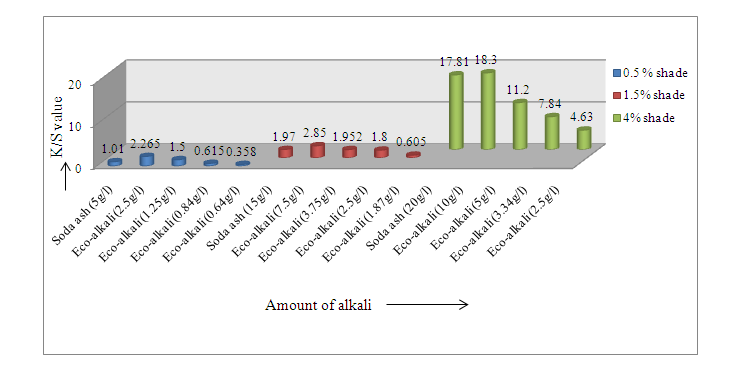 | Figure 1. K/S value for samples dyed with Novacron Blue FN-R |
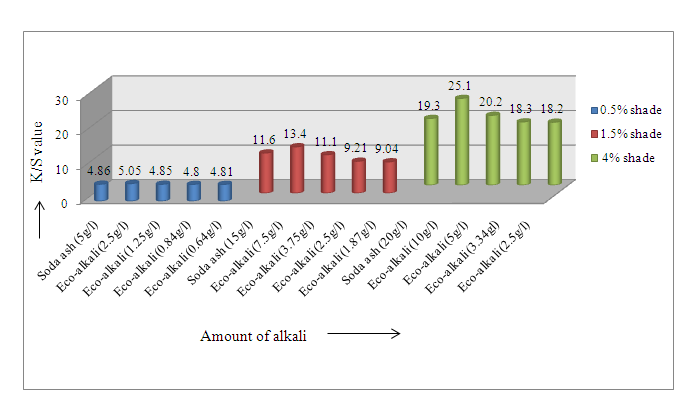 | Figure 2. K/S values for samples dyed with Novacron Brilliant Red FN-3GL |
From the Figure 1 it was noticed that for 0.5% shade (Novacron Blue FN-R) K/S value was found 1.01 using 5 g/l soda ash whereas the value was found 1.50 using 1/4th eco-alkali. So using 1/4th eco-alkali, color yield was found higher. Again, for 1.5% shade, K/S values were found 1.97 using 15 g/l soda ash, while using its 1/4th amount of eco-alkali is suitably comparable to required 15 g/l soda ash in terms of color yield. For 4% shade half amount of eco-alkali gave higher color yield than using 20 g/l soda ash.Similar results were found for Novacron Brilliant Red FN-3GL that 1/4th amount of eco-alkali gave the similar comparable color yield for 0.5% & 1.5% shades and half amount of eco-alkali showed better color yield for 4% shade than using required amount of alkali.
3.2. Fixation Efficiency
The fixation efficiency data are shown in Table 2 and Table 3 for Novacron Blue FN-R and Novacron Brilliant Red FN-3GL dyes respectively.From Table 2, fixation efficiency was found 85.75% for 0.5% shade (Novacron Blue FN-R) using 5 g/l soda ash whereas for its 1/4th amount of eco-alkali fixation efficiency was found 85.23% and this can be improved to 89.74% using half amount of eco-alkali. Again, for 1.5% shade (Novacron Blue FN-R), fixation efficiency was found 74.4% using 15g/l soda ash and its 1/4th amount of eco-alkali showed fixation efficiency 80.50%. Also in case of 4% shade (Novacron Blue FN-R), the achieved fixation efficiency was 71.64% using 20 g/l soda ash. But using its 1/4th amount of eco-alkali, the achieved fixation efficiency was 74.67% which was higher and comparable. This can be further improved to 94.82% using half amount of eco-alkali.Table 2. Fixation efficiency% of Novacron Blue FN-R 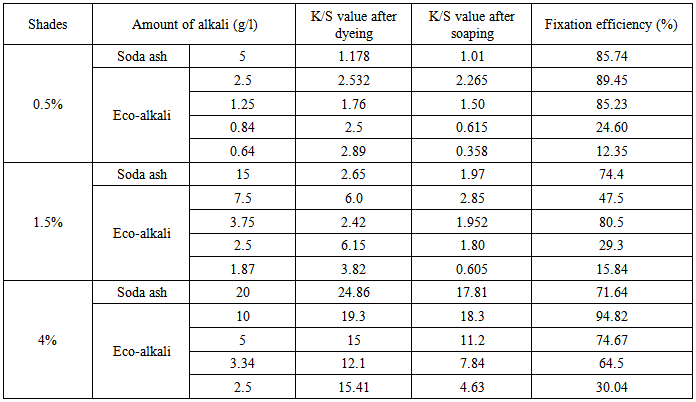 |
| |
|
Table 3. Fixation efficiency% of Novacron Brilliant Red FN-3GL 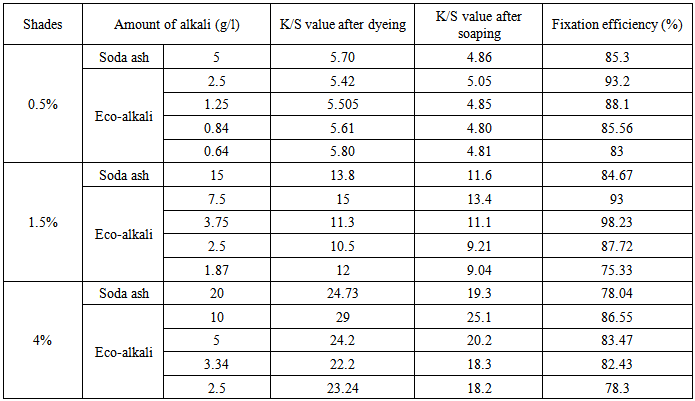 |
| |
|
From Table 3, it was found that in case of Novacron Brilliant Red FN-3GL dye, 1/6th amount of eco-alkali showed comparable fixation efficiency for 0.5% and 1.5% shades and can be improved using higher amount of eco-alkali. All the four amounts of eco-alkali, showed better fixation efficiency for 4% shade than the required amount of soda ash (20 g/l).
3.3. Analysis of pH of Wash Liquor after Dyeing
The data regarding pH of the washing liquor are shown in Figure 3 and Figure 4 respectively. Wash liquor pH was found to be 10 as shown in Figure 3, in three shades (Novacron Blue FN-R) using soda ash. As eco-alkali was used in lower amount, hence in this case, pH of wash liquor gradually decreased. For all the blue shades, pH varied from 7.5 to 8.5.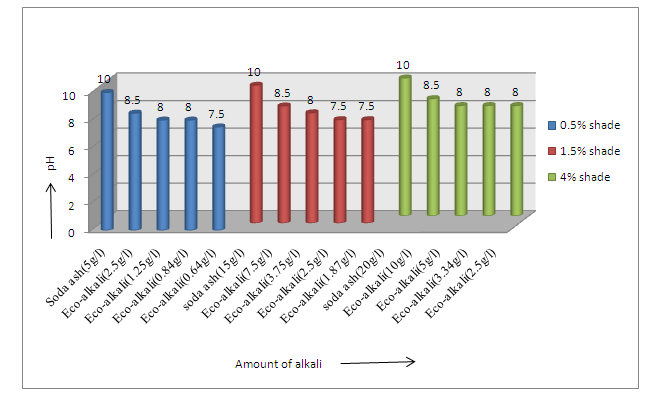 | Figure 3. pH of wash liquor after dyeing for Novacron Blue FN-R |
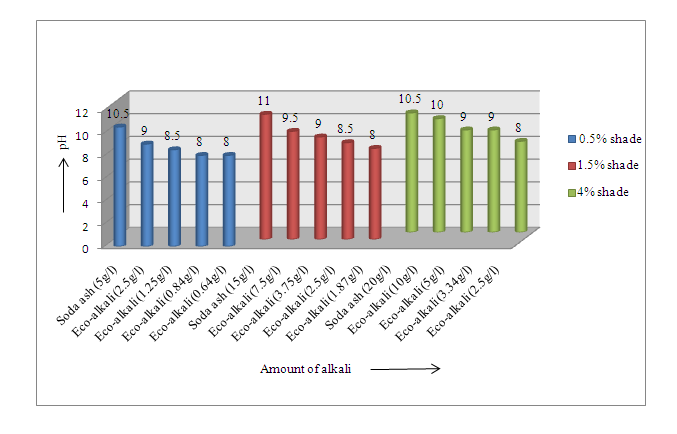 | Figure 4. pH of wash liquor after dyeing for Novacron Brilliant Red FN-3GL |
Again, wash liquor pH was found less as shown in Figure 4 for Novacron Brilliant Red FN-3GL, which varied from pH 8 to 10 using eco-alkali than using soda ash. pH gradually decreased with the decrease of eco-alkali. As pH was found decreased using eco-alkali, the amount of acetic acid in the neutralization process will also be required lower and hence there will be savings.
3.4. Analysis of Washing Fastness Property
Reactive dyes on cellulose fiber have superior washing fastness property [2]. Here for all shade%, rating for color change was found 4/5 to 5 that means good to excellent both for Novacron Blue FN-R and Novacron Brilliant Red FN-3GL dyes, which were shown in Table 4 and Table 5 respectively. In case of color staining ratings, it was found 4 (Good) in case of bleached cotton in 4% shade both for red and blue shades using soda ash, using lower amount of eco-alkali ratings were improved from 4 to 5 in case of bleached cotton. Staining was in between 4/5 to 5 in other cases. The reason of good washing fastness both in terms of color change and color staining was due to the formation chemical bondings (Covalent bonds) between cotton polymer and dye molecules [1].Table 4. Rating of color fatness to wash ((Novacron Blue FN-R) 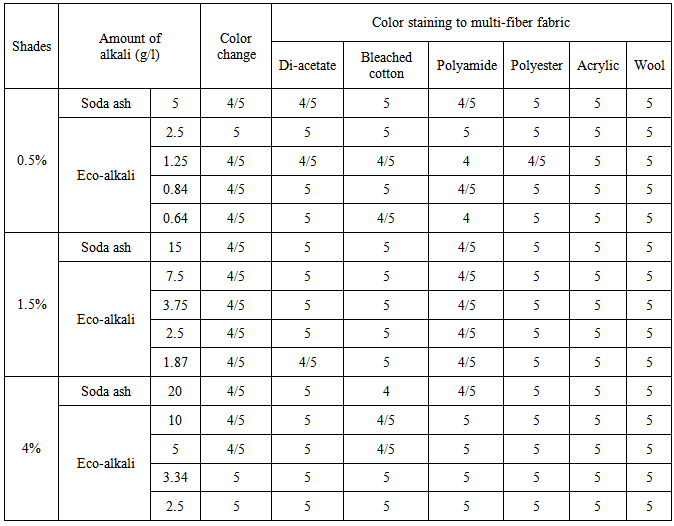 |
| |
|
Table 5. Rating of color fastness to wash (Novacron Brilliant Red FN-3GL) 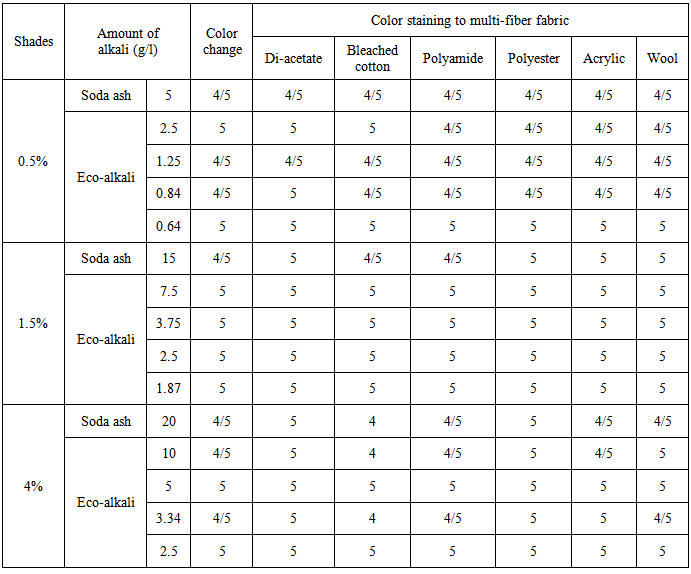 |
| |
|
3.5. Analysis of Color Uniformity of the Dyed Samples
Color uniformity can be easily interpreted in terms of standard deviation values of the K/S which are shown in Table 6 and Table 7 respectively for blue and red dyes.From Table 6 and Table 7, it was found that using lower amount of eco-alkali in most cases the standard deviation values were found lower and consequently color uniformity was found better. It was also found that using soda ash, standard deviation value of K/S was found lower in 0.5% shade and gradually increased in case of 1.5% and 4% shades. Again, comparable standard deviation values of K/S were found using 1/4th amount of eco-alkali both for blue and red dyes of different shades.Table 6. Standard deviation of K/S values of dyed samples for Novacron Blue FN-R 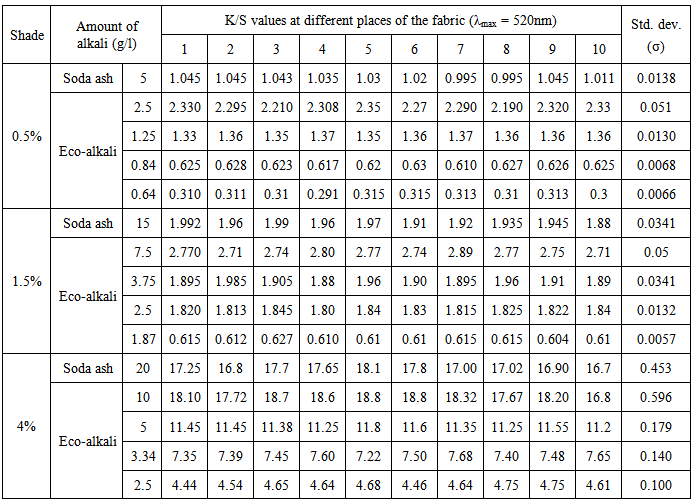 |
| |
|
Table 7. Standard deviation of K/S values of dyed samples for Novacron Brilliant Red FN-3GL 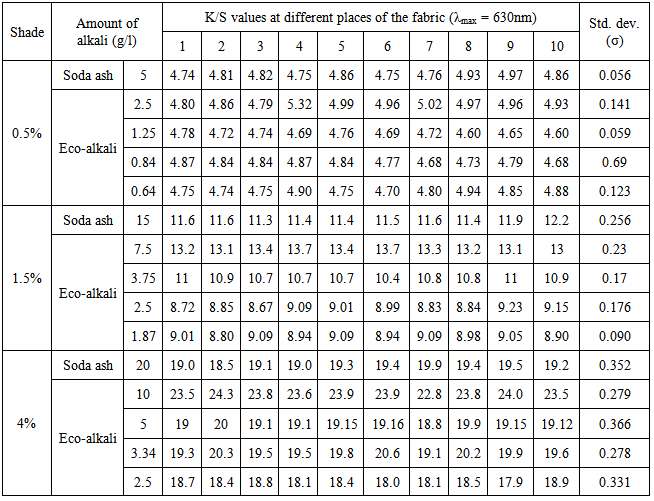 |
| |
|
3.6. Major Findings
Ø One-fourth amount of eco-alkali was found to be better substitute to soda ash for light and medium shades; for deep shade one-half amount of eco-alkali showed better color yield than what was achieved using recommended amount of soda ash.Ø Comparable fixation efficiency was ensured using one-fourth amount of eco-alkali for the observed light, medium and deep shades.Ø Using soda ash, pH of wash liquor after dyeing was found more (pH: 10-11); whereas using lower amount of eco-alkali pH was found lower which varied from 7.5-10 for all shades of blue and red dyes.Ø Washing fastness of the dyed sample was found within good to excellent using both soda ash and eco-alkali.Ø Comparable or better color uniformity effect can be achieved using one-fourth or one-sixth amount of eco-alkali.
4. Conclusions
This study was planned to use eco-alkali in dyeing of cotton fabric with reactive dyes as a substitute of soda ash and for that purpose its half, one-fourth, one-sixth and one-eighth amount of eco-alkali was used. For light and medium shades, 1/4th amount of eco-alkali produced better color yield in comparison to dyeing with standard amount of soda ash whereas in case of deep shade one-half amount of eco-alkali produced better color yield. Comparable fixation efficiency was ensured using 1/4th amount of eco-alkali in the observed three shade percentages of blue and red dyes. Savings can be possible in case of neutralization process due to achieve lower pH in wash liquor using lower amount of eco-alkali in all the cases. In addition, it was also found that using 1/4th amount of eco-alkali, comparable washing fastness results and color uniformity effects can be achieved. It can be concluded that eco-alkali can be used commercially in replacement with the excessive amount of soda ash for any shade in reactive dyeing of cotton fabric.
ACKNOWLEDGEMENTS
I am grateful to Mr. A.S.M. Atiquzzaman for his co-operation.
References
[1] | Choudhury, A.K.R., 2006, Textile Preparation and Dyeing. (Special Indian edn) Mohan Primlani for Oxford and IBH Publishing Co. Pvt. Ltd. 514-515. |
[2] | Broadbent, A.D., 2001, Basic Principles of Textile Coloration. Society of Dyers and Colorists, 335-36, 338, 345. |
[3] | Mcdonald, R., Ed. 1997, Color Physics for Industry, 2nd ed., Soc. Dyers and Colorists, Bradford. |
[4] | Garland, C.E., 1993, Textile Chemistry, Gultekin, C., Ed. New York: American Association of Textile Chemists and Colorists, 107. |
[5] | Subramanian, M., Kannan, S., Gobalakrishnan, M., Kumaravel, S., Nithyanadan, K.J., 2006, “Influence of cationization of cotton on reactive dyeing”, JTATM, 5(2): 4. |
[6] | Khatri, A., Peerzada, M.H., 2012, “Improved Reactive Dye-fixation in Pad-Steam Process of Dyeing Cotton Fabric Using Tetrasodium N, N-Biscarboxylatomethyl- L-Glutamate”, Mehran University Research Journal of Engineering & Technology, 31(2): 254 [ISSN 0254-7821]. |
[7] | Srikulkit, K.., Santifuengkul, P., 2000, “Salt-Free Dyeing of Cotton Cellulose with a Model Cationic Reactive Dye”, Coloration Technology, 116: 398-402. |
[8] | Wang, H., Lewis D.M. 2002, “Chemical Modification of Cotton to Improve Fiber Dyeability”, Coloration Technology, 118: 159-168. |
[9] | Wang, L., Ma, W., Zhang, S., Teng X, Yang J., 2009, “Preparation of Cationic Cotton with Two-Bath Pad- Bake Process and its Application in Salt-Free Dyeing”, Carbohydrate Polymers, 78: 602-608. |
[10] | Ristić, N., Ristić I., 2012, “Cationic Modification of Cotton Fabrics and Reactive Dyeing Characteristics”, Journal of Engineered Fibers and Fabrics, 7(4): 115. |
[11] | ISO 105-C06/A2S:1994, Textiles – Tests for color fastness; Part C06: Color fastness to domestic and commercial laundering. |