Manas Datta Roy, Sujit Kumar Sinha
National Institute of Technology, Jalandhar- 144011, Punjab, India
Correspondence to: Manas Datta Roy, National Institute of Technology, Jalandhar- 144011, Punjab, India.
Email: |  |
Copyright © 2014 Scientific & Academic Publishing. All Rights Reserved.
Abstract
Moisture transport through clothing under transient humidity conditions is an important factor which influences the dynamic comfort of the wearer in practical use. But enlarging the specific area of polyester fibres by changing their shape is a reasonable way to improve the moisture transportation characteristics of polyester textiles. The work has been carried out with the objective to study the impact of different cross-section of polyester fibre on the moisture transportation in yarn and fabrics. Similar types yarns were made from 100% polyester fibre of different cross-sectional shape. The moisture transportation behaviour of these yarns was studied along with the other mechanical properties. The wicking performance of the fabrics from such yarns was also studied to assess the moisture transportation behaviour.
Keywords:
Wicking, Cross-sectional shape, Moisture transmission
Cite this paper: Manas Datta Roy, Sujit Kumar Sinha, Performance of Wicking through Yarn and Fabric Made from Polyester Fibres of Different Cross-sections, International Journal of Textile Science, Vol. 3 No. 3, 2014, pp. 44-50. doi: 10.5923/j.textile.20140303.02.
1. Introduction
Comfort is a pleasant state of psychological, physiological and physical harmony between the human being and the environment. In a regular atmospheric condition and during normal activity levels, the heat is produced by the body for metabolism. When the perspiration is transferred to the atmosphere, it carries heat (latent as well as sensible) thus reducing the body temperature. The fabric being worn should allow the perspiration to pass through to avoid discomfort. During sweating, a slow rate of moisture transfer through clothing may increase the humidity levels of the clothing microclimate suppressing the evaporation of sweat. This will increase rectal and skin temperatures, resulting in heat stress. The degree of moisture transport through clothing under such transient humidity conditions is an important factor which influences the dynamic comfort of the wearer in practical use. Transport of water takes place through the phenomenon of capillarity. Capillarity is the ability of liquids to penetrate into fine pores of yarns and fabric.Polyester is the most widely and popularly used fibre because of its favourable characteristics, namely high strength, dimensional stability, easy care and wrinkle free characteristics for moisture transportation. However enlarging the specific area of fibres by changing their shape is a reasonable way to improve the moisture transportation characteristics of polyester textiles. Porosity in fabric and inter fibre spaces in yarn can play a major role in transportation of moisture. A fabric meant for clothing should be designed according to the area of application and should support wicking [1].The spontaneous flow of moisture or wicking occurs due to a pressure differential or capillary action. The complex contours formed by the fibres in the yarn and the yarns in the fabric constitute the boundaries of the channels along which moisture flows. The rate of travel of liquid water is governed by the fibre arrangement in yarns which controls capillary size, shape and continuity. Moreover, Fibre type, under certain circumstances, can drastically change the structure of the yarn, in turn changing the wicking properties of the fabric. [2]In general, wicking takes place when a liquid travels along the surface of the fibre but is not absorbed into the fibre. More completely, in the absence of external forces, the transport of liquids in a porous media is driven by capillary forces that arise from the wetting of the fabric surface. [2] Spun yarns have very irregular and poor capillary continuity due to the arrangement of fibres affecting water transport rate along its length [3]. Synthetic fibres are mainly hydrophobic and less liable to get wet thereby shows good moisture transportation and release [4]. Enlarging the specific surface area of fibres by changing fibre shape is a reasonable way to improve capillary force of hydrophobic polyester fibre bundle and to meliorate the wicking of polyester fabric. Individual fibre morphology, cross-sectional shape have been reported [5] to improve the liquid transport ability. Hollow fibre can provide greater bulk and provide improved heat and moisture management properties compared to conventional fibre. Researchers reported [6-8] positive correlation with fibre geometrical features to wicking, wettability and speed of capillary migrations. Fabrics of non-circular fibres have been reported to exhibit higher mass flow rate than that of circular fibres [9, 10]. The presence of channels on fibre surface offers a less tortuous path for the liquid to travel. Coarser and modified profiles of polyester can result increased in-plane wicking and higher water vapour permeability both in yarn and fabric stage. The pore structure of fabrics has been found to provide considerable influence on their wickability and water vapour permeability [5].This present work was aimed to study the moisture transportation behaviour of yarns and fabrics from fibres of two different cross-sectional shapes.
2. Materials and Methods
2.1. Yarn and Fabric Preparation
Polyester fibre (6 den, 64mm) of two different cross sectional shapes (viz circular hollow & trilobal) was procured. The fibres were taken for light microtomy for observation of its cross-sectional shape and sizes under microscope and were tested for their mechanical properties on Textechno Statimat Me Test by Fafegraph HR in the Research and Development Laboratory of Reliance Industries Ltd. The fibres were spun into two single component yarns using each one as 100% of nominal count 44 tex in a industrial condition. The yarns were prepared with 3.0 TM. The fibres were difficult to spun presumably due to stiffness. Accordingly the TM was optimised through trials. Then the yarns were taken for observation of fibre distribution in cross-sections by light microscopic microtomy method. This method needed a thorough preparation of the yarn samples ready for its embedding in resin-hardener combination followed by its curing at a specific temperature. The solid, transparent and cylindrical shaped samples contained yarn at its centre. These yarn embedded samples were mounted on a rotary microtome with toughed edge blade of section D. Rotary microtome gave slices of 5µm thickness which were kept on glass slides for observation under microscope. Such slices of each yarn were observed under Nikon E200 microscope. During microscopic observation the Toluene liquid was used as drops on slices to ensure uniformity in images. Images were taken with a uniform pixel density for maintaining clarity & uniformity. A portion of the single yarns were converted to double yarns on Two-For-One twister. Subsequently, plain woven fabrics were prepared on Taiwan made CCL loom using single yarns as weft and doubled yarns as warp for a width of fabric of 17
(43 cm).
2.2. Testing
Fibre: The fibres were tested for mechanical properties on Textechno Statimat Me Test by Fafegraph HR in the research and development laboratory of reliance industries ltd. Yarn: After conditioning under standard humidity and temperature for 48 hours, the single yarns were tested on USTER 5 for measuring mass irregularity followed by the tests of twist and count of all the yarns. Standard test method, ASTM D1422, was followed by the twist-untwist method for twist in spun yarns. After this, the yarn longitudinal views were observed by Leica image analyser and the diameters were calculated from the images. Both the yarns (single & doubled) were tested for mechanical properties on Tinius Olsen Universal Testing Machine (UTM). Standard test method for tensile testing of yarn was ASTM D 2256. At least 50 observations were taken to get the results in 95% confidence limit. The wicking of yarns was carried by fabricating a set up as shown in Figure 1. The single yarns and double yarns were tested for wicking on this instrument under same atmospheric condition.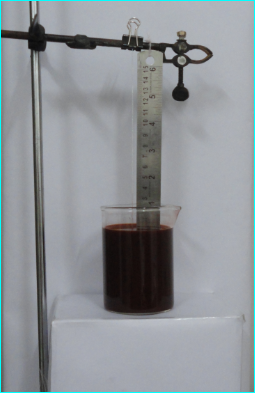 | Figure 1. Wicking set-up for yarn |
The frame of the apparatus was made using stainless steel bar. This bar was supported on the base. A horizontal clamp bar was attached at the top of this bar, which was used to clamp the specimen. A stainless steel scale was attached to the clamp vertically. A glass reservoir was placed on the base of the frame. The reservoir was filled with 250 ml of 1% dye solution. Two clips were used, one for clamping the sample at the top and other at the bottom of sample to keep it in a straight position.The transport of liquids in a porous media is driven by capillary forces that arise from the wetting of yarns. The rise of liquid along the specimen was recorded on the basis of the height shown against the scale. At the same time, a stop watch was also started in order to record the time it took the moisture to travel from mark to mark. This was done in order to compare length travelled by liquid versus time. The rise in length was recorded at different intervals of time. For testing of yarn a length of 180 mm was clamped at the top ensuring immersion of 30 mm in the liquid. Fabric: After conditioning under standard humidity and temperature for 48 hours, the fabrics were tested for ends per centimetre (EPC) and picks per centimetre (PPC). Both the fabrics (single yarn as weft & doubled yarn as warp) were tested for mechanical properties on Tinius Olsen Universal Testing Machine (UTM). Standard test method for tensile testing of fabric was ASTM D 5035-11. The wicking of fabric was carried by fabricated set up as shown in Figure 2. The fabrics were tested for wicking on this instrument under same atmospheric condition in both the directions i.e. warp & weft. 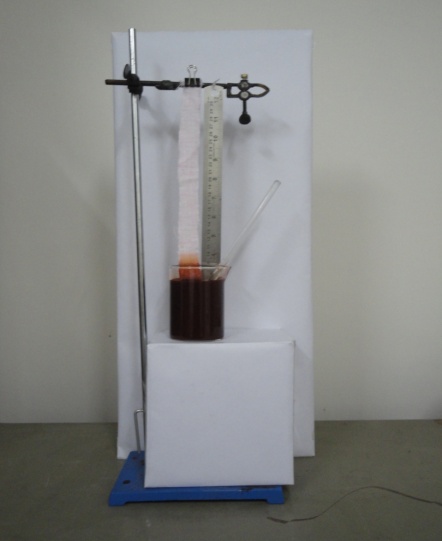 | Figure 2. Wicking set-up for fabric |
Vertical wicking of fabric was carried out as per DIN 53924. Sample size of 200 mm X 25 mm of fabric was clamped and 30 mm of the sample length was kept in immersed condition in reservoir. To study the wicking in fabric in both directions, the samples were taken from both warp and weft direction. At least 10 samples were tested and the average value was taken. For vertical wicking test, above instrument was used. The reservoir was filled with 250 ml of 1% of dye solution. The sample was clipped to the clamp vertically. Once the sample is in place and, the reservoir is filled, wicking started immediately. At the same time, a stop watch was also started in order to record the time it took the moisture to travel from mark to mark. This was done in order to compare length travelled by liquid versus time. The rise in length was recorded at different intervals of time. The test was stopped when liquid uptake becomes constant. 10 tests were performed for each sample.
3. Results and Discussion
3.1. Fibre Physical & Mechanical Properties
The fibre cross-sections were observed under microscope. The images were taken for understanding its shape, hollowness, diameter and cross-sectional area (Figure-3) and the physical properties are given in Table 1. 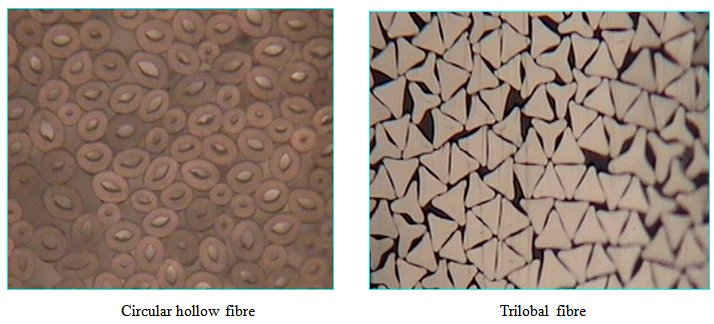 | Figure 3. Cross-sectional view of the fibres in bundle form |
Table 1. Physical and mechanical properties of fibres 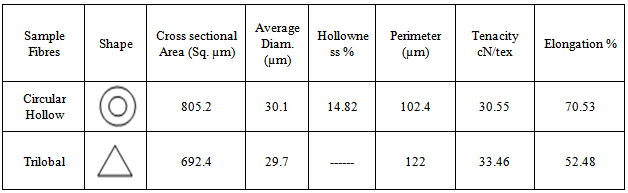 |
| |
|
After this the fibre mechanical test results were obtained (Table 2) by using UTM.Table 2. Fibre mechanical properties |
| Samples | Elongation % | Tenacity cN/Tex | Circular hollow | 70.5 | 30.5 | Trilobal | 52.4 | 33.4 |
|
|
The above observation clearly mentions that elongation % of circular hollow fibres was significantly more than trilobal fibres though their tenacity were similar which indicated the higher rigidness of trilobal fibres over circular hollow fibres.
3.2. Yarn Tensile Properties
The tenacity and elongation% of the yarns are represented in Table 3.Table 3. Yarn Tensile properties |
| Yarn Sample | Tenacity (cN/Tex) | Elongation (%) | E | 10.363 | 18.616 | K | 10.69 | 13.53 |
|
|
Yarns made from fibre of circular cross section was weaker than the yarn from Trilobal cross section. A Trilobal fibre offered more linear surface to the surrounding and encourages better packing with the adjacent fibres with similar linear surfaces & hence better ‘inter-fibre’ cohesion (Fig.4) On the other hand, circular fibres inhibited close association of fibres and lead to lower fibre packing and less interfibre cohesion. Thus, the Trilobal yarns were stronger than yarns from circular hollow cross-sectional fibres. Generally stronger yarn shows higher breaking extension. But in this case, the higher crimp and poor packing of circular hollow fibres were responsible for the higher extension-at-break. This breakage was taking place mainly because of inter fibre slippage along the strand. Where as the yarn with Trilobal fibres, with better packing, shows poor extension at break. 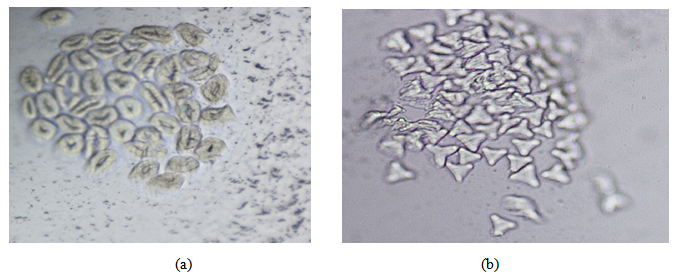 | Figure 4. Cross-sectional view of yarns (a) Circular hollow & (b) Trilobal |
3.3. Fabric Physical & Mechanical Properties
The fabrics were tested for its EPC and PPC. It was found as 13.4 and 12.5 respectively for both the fabrics. The fabrics were tested for mechanical tests in warp way and weft way. The tests results were noted (Table 4). The warp wise tenacity value was comparatively less high than that of weft wise tenacity for circular hollow fabric. Whereas the same was more than double for trilobal fabric. But the extension % of both the directions of both the fabrics were very close. It indicated a better integration of the double yarn (warp) for trilobal yarns which were further enhanced by the formation of fabric. Table 4. Mechanical properties of fabrics 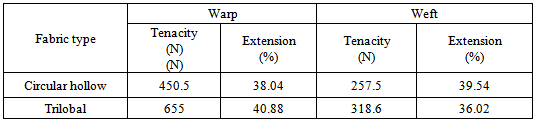 |
| |
|
3.4. Wicking in Yarns
Single yarn: It was observed that the rate of rise of liquid in the yarn from circular hollow polyester was much higher for first few minutes and then the rate reduced. This was probably because of two reasons:1) The hollow fibre provides least resistance for free passage through it favouring the rise of liquid2) The diameter, being more, was likely to provide more inter fibre space as evident from fibre spacing as observed from the cross-sectional view [Fig.4].3) The hollow circular fibre assists the liquid to flow through fibre both through its hollow passage and inter-fibre space.The circular cross section of fibre would allow uniformity in packing leading to uniform capillary shape. The capillary force was more favourable than the limiting force of liquid flow and the difference was more for the first few minutes. The difference decreased when the capillary height reached a specific value. Beyond it, the force assisting the rise of liquid might not be sufficient to maintain the rate due to gravitational pull. Fig.5 showed that the yarn made of circular hollow polyester fibre had always shown better wicking performance than yarn made of trilobal fibre. A similar trend, however, was observed for both the yarns.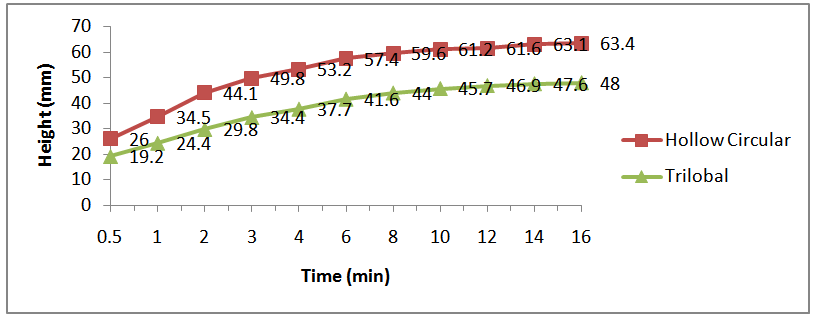 | Figure 5. Wicking in the single yarns |
Doubled yarns: The fabrics were prepared by taking doubled yarn as warp and it was expected the doubled yarns to show different wicking behaviour in fabric stage as well. Accordingly, the wicking behaviour for doubled yarn was also studied. In a doubled yarn the space between the ply component may provide more passage but the ply twist might have resulted more compactness in individual yarn. The resultant effect is the similar wicking behaviour of single and double yarns (Fig.6).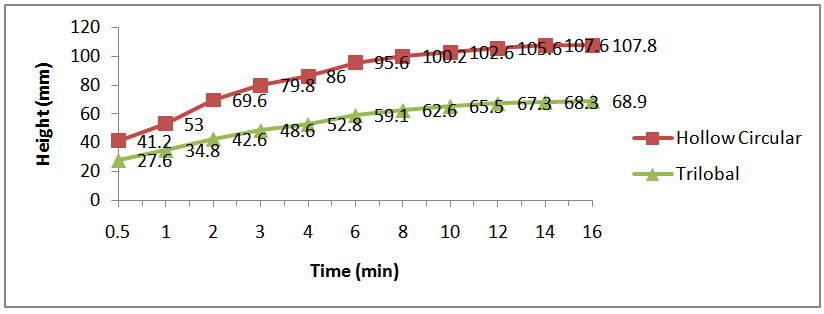 | Figure 6. Wicking in double yarns |
3.5. Wicking in Fabrics
Warp way wicking: The warp way wicking for two fabrics is given in Fig. 7. It is observed from the figure that wicking of fabric made of hollow circular fibres showed higher performance than trilobal fibre made fabric. But the wicking time of fabric made of hollow circular fibres was much more than that of trilobal fibre made fabric. It means that trilobal fibre made fabric is not changing its wicking behaviour even in fabric with respect to its performance at double yarn stage. But the other yarn is showing a much longer wicking time, 23 minutes, with consistency in comparison to its performance at double yarn stage, where the wicking had stopped after 16 minutes. 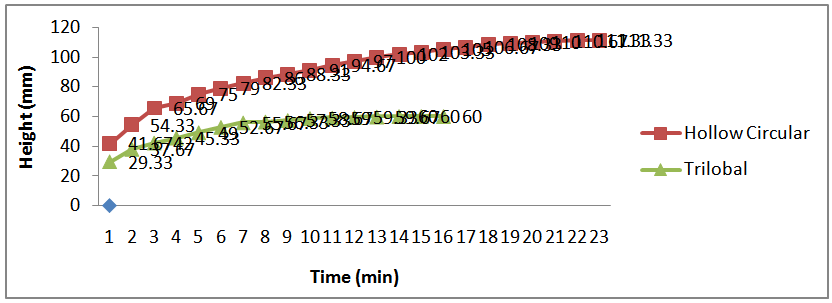 | Figure 7. Warp way wicking in fabrics |
Weft way wicking: The wicking performance of fabric in weft way is similar to that of single yarn for both the cases (Fig.8). Packing density of the yarn made of circular hollow fibres providing more voids or openness because of its circular cross-section whereas yarn made of trilobal fibre is providing more compact yarn with less openness. Circular hollow yarn has more inter fibre capillaries and intra fibre channels (hollow centre). Due to the absence of intra fibre channel & presence of much less inter fibre channels for high packing, trilobal yarn could not show better wicking and time. 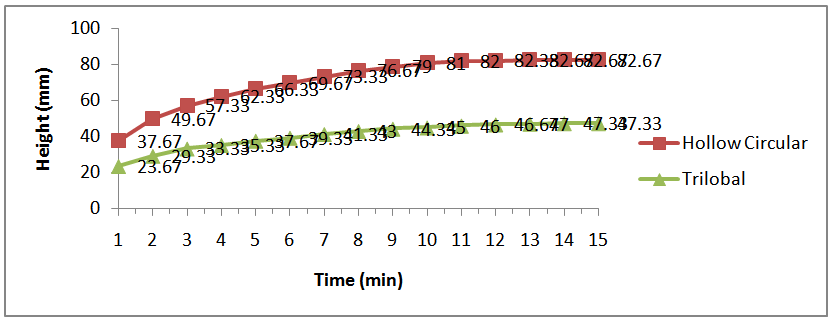 | Figure 8. Weft way wicking in fabrics |
4. Conclusions
1. Single Yarn made of Trilobal fibre shows more tenacity and Circular hollow fibre shows better Elongation %.2. Yarn made of circular hollow fibre shows the maximum wicking speed during the first few minutes. After that the wicking proceeds in a gradual manner.3. The increase in the wicking is almost uniform in case of Trilobal fibre with a little fluctuation at the beginning.4. The yarn made of circular hollow fibre always shows higher wicking performance than yarn made of Trilobal fibre. 5. The single and double yarn wicking performances of both the yarns have shown the similar trends in fabrics i.e. weft wise and warp wise respectively. But the warp way wicking duration of fabric made of circular hollow fibre is much longer.
ACKNOWLEDGEMENTS
The authors great fully acknowledge the assistance provided by Mr. D Dasgupta, President, Nahar Fabrics Ltd., Lalroo, Punjab, India for preparation of the Fabric samples and Mr. D.L. Sharma, Managing Director, Vardhman Spinning & General Mills Ltd., Ludhiana, India for preparation of the Yarn samples.
References
[1] | Brojeswari Das, A. Das, V. K. Kothari, R. Fanguiero And M. De Araujo “Moisture Transmission Through Textiles Part 1: Processes Involved In Moisture Transmission And The Factors At Play” Autex Research Journal, Vol.7, No 2, June 2007. |
[2] | Craig Burton Simile “Critical Evaluation Of Wicking In Performance Fabrics” Georgia Institute Of Technology December 2004. |
[3] | Harnett, P. R. And Mehta, P. N., “A Survey And Comparison Of Laboratory Test Methods For Measuring Wicking”, Text. Res. J., 54, 1984. |
[4] | E. Sema Namligoz, Suleyman Coban And M. Ibrahim Bahtiyari “Comparison Of Moisture Transport Properties Of The Various Woven Fabrics” Tekstil Ve Konfeksiyon 2/2010. |
[5] | R. K. Varshney, V. K. Kothari And S. Dhamija “A Study On Thermophysiological comfort Properties Of Fabrics In Relato To Constituent Fibre Fineness And Cross Sectional Shapes” The Journal Of Textile Institute Vol 101 No 6 June 2010 495-505. |
[6] | Holme I. In Synthetic Fibre Materials. In: Body H (Eds) Longman Scientific And Technical: Essex, 1994, Pp. 93-128. |
[7] | Rwei Sp. J. Appl. Polym. Sci. 2001; 82: 2896-2902. |
[8] | Petrulis D. J. Appl. Polym. Sci. 2004; 92:2017-2022. |
[9] | Miller, B. And Young, R. A. (1975). Methodology For Studying The Wettability Of Filaments. Textile Research Journal, 45(5), 359-365. |
[10] | Wang, H.S., & Gupta, B. S. (2000), Surface Wetting Characteristics Of Cellulosic Fibres, Textile Research Journal, 70(4), 351-358. |