Abu Yousuf Mohammad Anwarul Azim1, Kazi Sowrov2, Mashud Ahmed2, H. M. Rakib Ul Hasan3, Md. Abdullah Al Faruque2
1Department of Textile Engineering, Primeasia University, Dhaka, 1213, Bangladesh
2Department of Fabric Manufacturing Engineering, Bangladesh University of Textiles, Dhaka, 1208, Bangladesh
3Department of Textile Engineering, Daffodil International University, Dhaka, 1207, Bangladesh
Correspondence to: Abu Yousuf Mohammad Anwarul Azim, Department of Textile Engineering, Primeasia University, Dhaka, 1213, Bangladesh.
Email: |  |
Copyright © 2014 Scientific & Academic Publishing. All Rights Reserved.
Abstract
The dimensional and physical Properties of Cotton/elastane single jersey fabrics varies as compared with fabrics knitted from 100% cotton yarn. The object of this study is to investigate how it varies when the fabrics are made from 100% cotton yarn and cotton/elastane blended yarns & also to study the effect of elastane on the basic principle physical properties like GSM, Air Permeability, Pilling, Spirality, Loop length, Course Spacing, Wale Spacing, course/cm, wales/Spacing, Stitch density, Bursting Strength & Shrinkage test. This would help commercial knit manufecturer to understand the effect of elastane on fabric properties. On Going with this work we have considered two different fabrics made from above mentioned raw materials and have tested some important dimensional and physical properties of those fabrics. The results will be presented further ahead with comparing tables and charts.
Keywords:
Knit fabrics, Elastane, Cotton, Fabric properties, Comparison
Cite this paper: Abu Yousuf Mohammad Anwarul Azim, Kazi Sowrov, Mashud Ahmed, H. M. Rakib Ul Hasan, Md. Abdullah Al Faruque, Effect of Elastane on Single Jersey Knit Fabric Properties - Physical & Dimensional Properties, International Journal of Textile Science, Vol. 3 No. 1, 2014, pp. 12-16. doi: 10.5923/j.textile.20140301.03.
1. Introduction
Due to the use of elastane fiber in single jersey knit fabric various physical properties will be changed. The physical properties which are to be considered: GSM, Air Permeability, Pilling, Spirality, Loop length, Course Spacing, Wale Spacing, course/cm, wales / Spacing, Stitch density, Bursting Strength & Shrinkage.The weight and thickness of the elastane containing fabrics are higher, fabrics tend to be tighter but spirality, air permeability and pilling grade gets lower. The fabrics knitted from elastane yarns, have the largest tension values under a constant draw ratio which give the highest weight, wales/cm, courses/cm, stitches/cm, thickness and lowest air permeability values. The width of the fabric decreases and simultaneously the thickness of the fabric increases because of the greater stretched structure of the spandex yarns that have shorter loop length values. The wear comfortability of outer clothing, leisure-wear, underwear and sportswear is generally ensured by the use of fabrics knitted from elastane. Today a huge number of articles on elastane are available in the circular knit fabric collections. An important number of patents describing the design of new plated fabrics was registered during the last decades [1-4]. Elastane fibers are synthetic fibers which are made up of linear macro-molecules of high molecular weight. The first process of the industrial-scale production of elastane that is dry spinning was developed in 1962 by J.C. Shevers and colleagues in the Pioneering Research Division of E.I. Du Pont de Nemours & Co., Inc. (U.S.A.). This multifilament has since been on the market as the name of "Lycra". The stretch elasticity of elastanes can be as high as 500% while the elastic recovery reaches 95%. In recent years the use of woven and knitted fabrics of elastane has increased remarkbly. This is due to a particular fact that these articles are characterized by excellent wear comfort and fit. The industry anticipates an annual increase of 8-10% for the coming years [5]. Elastanes are predominantly used in tights, underwear, swim-wear, beachwear, sports articles, corsets and medical support stockings. Elastanes are always blended with one or more other fibers than as an individual fibre. If bare elastane is processed to form a loop it must always be knitted together with a ground yarn. This measure is necessary because there is a risk to the breakage of the elastane yarn if the knitted fabric is stretched too far.Elastane blended with native or man-made fibers is called plating. Plating means the simultaneous formation of one loop from two threads. so that one thread will lie on the face of the fabric. The mechanisms where the unwinding elastane bobbin is driven have become the most common feed systems in large-diameter circular knitting when processing elastane yarns. The bobbin is positively driven in these delivery systems. After unwinding, the yarn passes through an electric stopping device and then fed to the needle through the plating roll. Elastane yarn percentage is one of the most important parameter of single jersey plated fabric. The percentage of elastane influences fabric characteristics [7]. The adjustment of elastane percentage is obtained by setting speed of elastane delivery system. There is no rigorous physical law that enables to determine with precision the necessary elastane consumption for given fabric properties. The relation between elastane percentage with fabric width, weight or elasticity is not well known. Most of knit manufacturers have to carry out some tests and adjust according to knitting parameters in order to reach the exact elastane proportion for the right fabric properties. These adjustments serves as a base for further settings. 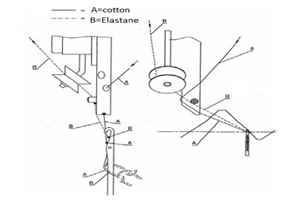 | Figure 1. Ground & elastane yarns position in a roll plating yarn guideother thread is fed to the needles in such a way that it forms the back or reverse of the final fabric. In the case of single-bed circular knitting machines elastane must always be feed in via a plating yarn guide. This guide presents generally a feeding roll permitting Lycra® guiding with minimum friction [6, 7]. Positive feed |
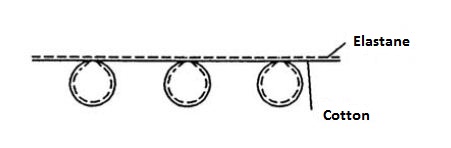 | Figure 2. Elastane plated single jersey plain knitted fabric pattern |
2. Literature Survey
Papers describing the effects of the elastane in knitted fabrics are generally related to dimensional properties of the fabrics (1, 2 and 3). Schulze [1] investigated the dimensional properties of single jersey, lacoste and fleece fabrics knitted with cotton/elastane blended yarns. He found that the weight and loop densities of cotton / elastane blended fabrics were higher than they were in cotton fabrics. He also reported the extension both widthwise and lengthwise that increased as relaxation progressed. Ceken [2] knitted single jersey and 1x1 rib samples with various tightness factors using cotton and various count of elastic yarn. Apparently the widthwise dimensional variations for fabrics knitted with cotton alone were higher while the lengthwise variations for the same fabrics were less after relaxation. Tasmaci [3] researched the dimensional properties of single jersey fabrics knitted from cotton, viscose and PES yarns with or without elastane. He found that fabrics containing elastane were higher variations both in width and weight. Furthermore the appearance of fiber surfaces was smoother.Meriç B., Gürarda A [4] studied the mechanical properties of fabrics containing elastane and concluded that high elastane content makes the yarn flexible; however the yarn that will be used with elastane should allow the fabric to move freely and shouldn’t cause any deformation in the fabric.A. B. Marmarali [5] investigated the physical and dimensional properties of elastic single jersey fabrics and A. Marmarali, N. Özdil and S. D. Kretzschmar [6] studied the effect of the elastane content in fabrics on their thermal properties and relative water vapor permeability.In the literature, some studies aimed to conceive new plating devices or to design new plated fabrics [7 & 8]. Cuden et al. studied experimentally the evolution of the characteristics of Lycra® plated plain knitted fabric after finishing and relaxation but did not investigated the effect of elastane ratio on these characteristics [9]. Studies which specifically treat the relation between elastane percentage and plated fabric performances are extremely rare. Some researchs available in literature [10 & 11] described the relation between the rate of elastane and some fabric properties such as extensibility and fatigue but they concerned only weaved fabrics made with elastane core-spun weft yarns.
3. Materials & Methods
3.1. Materials
Two separate single jersey samples were knitted: one with cotton alone and the other one as cotton/elastane blended fabrics (elastane in every course). Samples were obtained at medium loop length values, representing a medium fabric. Both the samples are produced in Mayer & Cie Single jersey Circular Knitting Machine of 30 dia & 24 gauge. 30/1 ring spun cotton yarn & 20 Denier Elastane were used in the experiment. An IRO MER2 system was used to feed the elastane, and yarn tension was 6 cN.The samples were subjected to the dyeing, washing and finishing processes. Here two samples marked as 1(a) which is 100% Cotton and another is 1(b) which is cotton/elastane mixed.
3.2. Methods
Table 1 shows the various testing methods and equipments used for this experiment.Table 1. Testing methods and equipments |
| Tests | Methods | Equipments | Fabric Weight | ISO 33071 | GSM Cutter, Electric Balance | WPC & CPC | Manually | Magnifying Glass, Needles | Stitch Density | Manually | N/A | Pilling | ISO 12945-1:2000 | ICI Pilling Test Box | Shrinkage | ISO 6330 | Wascator | Bursting | ISO 13938-2 1999 | Tru Burst Machine | Spirality | AATCC 179 | N/A | Air Permeability | ISO 9237 | Air Permeability Tester |
|
|
4. Results & Discussion
4.1. Fabric Weight
Table 2. Experimental results of these two samples are shown below by a table and a chart |
| Sample no. | Fabric weight (gm/m2) | 1(a) | 132.8 | 1(b) | 182.4 |
|
|
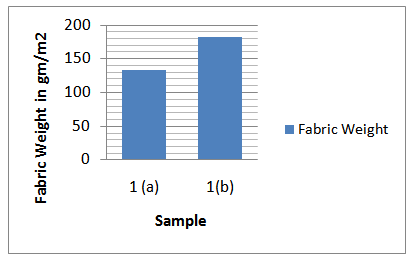 | Figure 3. Bar chart showing the two different samples weight |
4.2. Fabric Density: Wales / cm (WPC) & Course /cm (CPC)
Table 3. Comparison among these two samples based on Wales / cm and Course/cm |
| Sample no | Wales / cm | Course / cm | 1(a) | 37 | 52 | 1(b) | 40 | 59 |
|
|
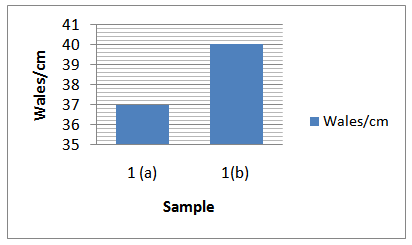 | Figure 4. Bar chart showing the wales/cm of two different samples |
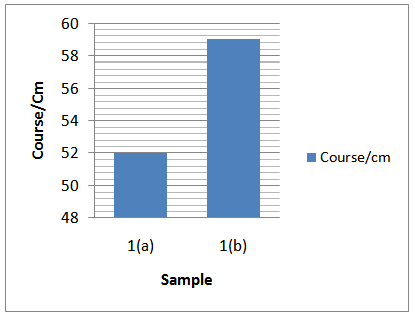 | Figure 5. Bar chart showing the course/cm of two different samples |
4.3. Stitch Density
Table 4. Calculation of stitch density followed by a chart |
| Sample | Wales/cm | Course/cm | Stitch density=WPCXCPC | 1(a) | 37 | 52 | 1924 | 1(b) | 40 | 59 | 2360 |
|
|
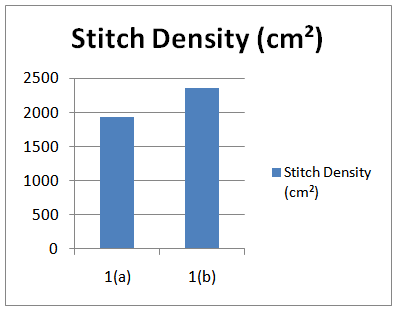 | Figure 6. Bar chart showing the stitch density of two different sample |
4.4. ICI Pilling Test Report
Table 5. Sample no 1(a): 100% cotton single jersey 30 Ne |
| Serial no. | No. of cycles | Rating in Wales direction | Avg. rating in Wales direction | Course direction | Avg. rating in Course direction | 1. | 14400 | 4 | 4 | 4 | 4 | 2. | 14400 | 4 | 4 |
|
|
Comparison among these two samples based on ICI Pilling test. Sincere observation on above tabulated value obtained from ICI Pilling test shows that rating is not influenced by the use of Elastane as an Elastane yarn.Table 6. Sample no 1(b): 30/1 cotton (96%) and 20D Lycra (4%) S/J (full feeder) |
| Serial no. | No. of cycles | Rating in Wales direction | Avg. rating in Wales direction | Course direction | Avg. rating in Course direction | 1. | 14400 | 4 | 4 | 4 | 4 | 2. | 14400 | 4 | 4 |
|
|
4.5. Shrinkage Test
Table 7. Observation shows that using elastane yarn can reduce the shrinkage percentage |
| Sample no. | Shrinkage in length direction | Shrinkage in width direction | 1(a). | -5.1 | -4.6 | 1(b). | -4.0 | -2.0 |
|
|
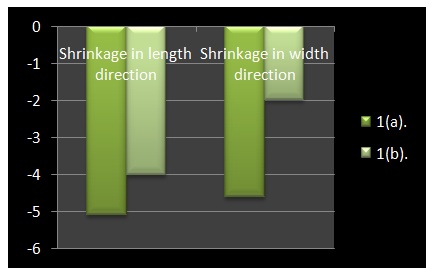 | Figure 7. Bar chart showing the shrinkage of two different sample |
4.6. Bursting Strength Test
Table 8. Comparative table between these two samples with chart |
| Sample no. | Bursting Strength (KN/m²) | 1(a) | 124.1 | 1(b) | 146.3 |
|
|
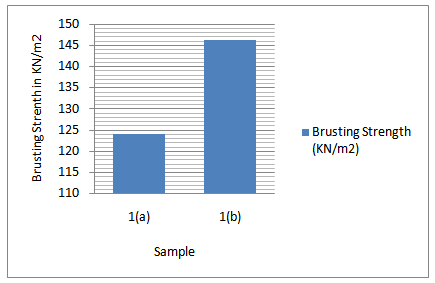 | Figure 8. Bar chart showing the bursting strength of two different sample |
4.7. Air Permeability Test
Table 9. Air permeability test results |
| Sample No. | Air Permeability (l/m²/s) | 1(a) | 663.6 | 1(b) | 30.6 |
|
|
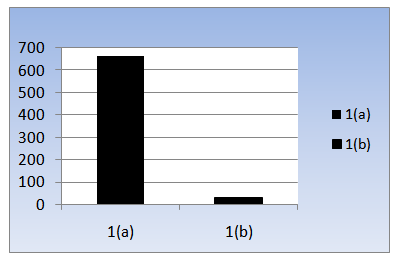 | Figure 9. Bar chart showing the air permeability of two different sample |
4.8. Spirality Test
Table 10. Spirality test results with table and chart |
| Sample No. | Spirality (%) | 1(a) | 1.1 | 1(b) | 1.9 |
|
|
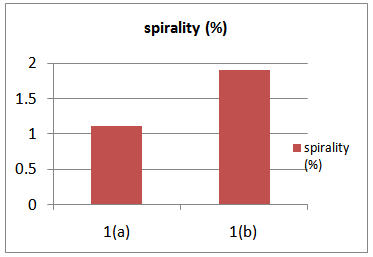 | Figure 10. Bar chart showing the spirility % of two different sample |
5. Discussion
The weight of the samples increase as the loop length decreases and the amount of elastane increases because the greater the amount of elastane percentage, the tighter the fabric.Air permeability is lower for full feeder cotton/elastane fabrics and greatest for cotton samples because tighter fabrics are obtained with elastane in the knitted structures. The difference between the air permeability values of these two samples is consistently higher. The variation in air permeability values of samples knitted from cotton yarn is significantly high in accordance with loop length. But for full feeder samples, there are no important changes related to loop length. The pilling grades of both the samples are same. Therefore presence of elastane doesn’t affect the pilling property.The percentage of spirality is greater in cotton/elastane fabric.The course spacing is less in the full feeder fabric because of reduction of loop length. It is same in wales spacing.Course per cm & wales per cm increases in the cotton / elastane fabric because of the reduction of loop length. As a result Stitch density increases in cotton/elastane fabric.Bursting strength of cotton/elastane fabric is higher than the 100% cotton s/j because the use of elastane helps the fabric to expand more than the 100% cotton s/j and it needs more pressure and more time to burst the sample.The shrinkage percentage of cotton/elastane fabric is less than the 100% cotton s/j fabric. Because elastane fibre helps to retain the fabric’s original dimension as far as possible after washing.
6. Conclusions
In this paper, we discuss the dimensional and physical properties of cotton and cotton / elastane single jersey fabrics and we conclude that these parameters are affected by the amount of elastane in the fabric and the loop length. The weight and thickness of full feeder cotton / elastane fabrics are higher but air permeability and the degree of spirality are lower than 100% cotton knitted fabrics respectively. It is also apparent that the widthwise dimensional variations for fabrics knitted with cotton alone are higher while the lengthwise variations for the same fabrics are less after relaxation.
References
[1] | Schulze, U. (1993), “Rechts/Links-Rundstrick-Bindungen ın Dur Kombinationmit Dorlastan”, Wirkerei und Strickerei Tech., 5, p: 456. |
[2] | Ceken, F., 1995, “Some Investigations of the Dimensional Properties of Knitted Fabrics Containing Different Materials”, Doctoral thesis, Ege University, Izmir. |
[3] | Tasmaci, M., 1996, “Effects of Spandex Yarn on Single Jersey Fabrics Knitted with Naked Lycra Yarn”, Tekstilve Konfeksiyon, 6, p: 422-426. |
[4] | Meriç B., Gürarda A., Proceeding of The XIIth Textile and Leather Romanian Conference, October 2002, pp. 17-19. |
[5] | Marmaralı, A., 2003, “Dimensional and Physical Properties of Cotton /Spandex Single Jersey Fabrics”, Textile Research Journal, 73(1), p: 11-14. |
[6] | Marmaralı, A., Özdil, N. and Dönmez Kretzschmar, S., 2006, “Thermal Comfort and Elastic Knitted Fabrics”, International Conf. CIRAT- 2, Monastir-Tunisia. |
[7] | Baozhu, K., Weiyuan, Z., "The optimal design of three-layer plated fabrics", Fibres & Textiles in Eastern Europe, 15, 2007, 59-61. |
[8] | Bruer, S. M., Powell, M., Smith, G., "Three dimensionally knit spacer fabrics: a review of production techniques", Journal of Textile and Apparel, Technology and Management, 4, 2005, 1-31. |
[9] | Cuden, A. P., Srdjak, M., Pelko, H., "Optimization of the cotton/Lycra plain knitted Fabric parameters", International Journal of Polymeric Materials, 47, 2000, 633 – 648. |
[10] | Özdil, N., "Stretch and Bagging Properties of Denim Fabrics Containing Different Rates of Elastane", Fibres and Textiles in Eastern Europe, 1, 2008, 63-67. |
[11] | Gorjanc, S., Bukosek V., "The behaviour of fabric with elastane yarn during stretching”, Fibres and Textiles in Eastern Europe, 3, 2008, 63-68. |
[12] | M. Senthilkumar. “Effect of Sapndex Input Tension, Spandex Linear Density And Cotton Yarn Loop Length on Dynamic Elastic Behaviors of Cotton/Spandex Knitting Fabrics”, Journal of Textile and Apparel, Technology and Management, Vol 7(4), 2012, 1-16. |