Mst. Murshida Khatun
Textile Engineering Department, Daffodil International University, Dhaka, Bangladesh
Correspondence to: Mst. Murshida Khatun, Textile Engineering Department, Daffodil International University, Dhaka, Bangladesh.
Email: |  |
Copyright © 2012 Scientific & Academic Publishing. All Rights Reserved.
Abstract
The purpose of this research is to investigate the effect of yarn count on the dyeing performance of reactive dye in exhaust method. To carry out investigation five different count of cotton yarn e.g. 10Ne, 20Ne, 30Ne, 40Ne and 50Ne were taken. After scouring and bleaching each count of yarn are dyed with reactive dye in exhaust process, 60°C isotherm. Different shades for each yarn count were used. After dyeing the reflectance and exhaustion as well as the fixation percentage (the most important criteria) are measured by the Spectrophotometer. Many samples which can be compared with each other i.e. different fixation has been got for different count for the same exhaust method and shade percentage. There is gradual order of these data. This generally reflects the theoretical concept of higher the cotton count, less the color strength & higher the brightness.
Keywords:
Yarn Count, Exhaust Dyeing, Dyeing Performance, Reactive Dye
Cite this paper: Mst. Murshida Khatun, Effect of Yarn Count on the Dyeing Performance of Reactive Dye in Exhaust Method, International Journal of Textile Science, Vol. 2 No. 4, 2013, pp. 92-104. doi: 10.5923/j.textile.20130204.03.
1. Introduction
The dye that consist a reactive group which is capable of reacting chemically with a substrate (cotton, wool etc.) to form a dye-substrate covalent bond is known as reactive dye[9].Reactive dyes can be applied to cotton, silk and polyamide fibers successfully. But in this research reactive dyes were applied to cotton fibers substrate. The reason of taking cotton fiber is too much logical from the consumption point of view of this fiber. Cotton is extensively used natural fiber throughout the world (about 31% of the fiber consumed). Again the reaction manner of cotton dyeing is large. Moreover reactive dye is mainly used for cotton fiber dyeing and silk or polyamide fibers dyed with acid dyes[8].Cotton is a soft, staple fiber that grows in a form known as a boll around the seeds of the cotton plant, a shrub native to tropical and subtropical regions around the world, including the Americas, India and Africa. The fiber most often is spun into yarn or thread and used to make a soft, breathable textile. Cotton is the oldest and the most important of the textile fibers. It has been used in the East and Middle East for thousands of years and was found in use in America when the continent was discovered[2]. Despite the increased variety of manufactured fibers available to the textile industry, demand for cotton remains high because of its suitability on the basis of price, quality and comfort across a wide range of textile products.Here the reactive groups present in the dye molecule act as an integral component of the fiber polymer after dyeing in a favorable condition. Mainly the reaction occurs in an alkaline condition (PH>10). The covalent bond is formed between the dye molecule and –OH group of cellulose or NH2 (amino group of polyamide or wool fiber. The general reaction between dye molecules and the fibers are as below:
Exhaust dyeing also is known as batch, or discontinuous, dyeing. It is the process used for most commercial fabric dyeing. Essentially, the process involves loading fabric into a bath, originally known as a batch, and allowing it come into equilibrium with a solution, or suspension, of dye[16].Exhaust dyeing is the ability of the molecules to move from the solution onto the fabric fibers (substantivity) in a set time. During that time, it diffuses or migrates into the interior of the fiber & is fixed. The dye liquor with initial high dye content becomes gradually exhausted while the dye accumulates in the fiber[17].Count is the numerical expression of fineness or coarseness of yarn. A definition of yarn count is given by the Textile Institute: “Count, a number indicating the mass per unit length or the length per unit mass of yarn"[9] .
2. Experimental
2.1. Material & Method
2.1.1. Cotton Yarn
Five different count of cotton yarn e.g. 10Ne, 20Ne, 30Ne, 40Ne and 50Ne.[Where Ne means yarn count]
2.1.2. Chemicals & Auxiliaries Used in Pretreatment
Sirrix 2UD liquidAn ecofriendly, organic special product for the protonic (H+) treatment of textiles.Ø It enables the replacement of the sodium hypochlorite bleach (AOX) by the protonic treatment before the peroxide bleachØ It dematerializes cotton and removes stubborn pigments. Ø It replaces organic acids (formic or acetic acid) in the neutralization process after alkaline treatments such as scour boiling, mercerizing or bleaching.Imerol PCLFA very low foaming wetting agent and scouring agent for all types of fiberØ Excellent scouring agentØ Removes mineral oil contamination and sizing agents and imparts excellent cleanliness and good absorbency to the materialStabilizer SOF LiquidA specific stabilizer for the silicate-free, alkaline peroxide bleaching of cotton and its components in fiber blends.Ø Sodium silicate is completely replacedØ Complexes heavy metal ions and thus prevents catalytic damageØ Is non foamingCaustic sodaØ It is used to remove the natural impurities in cotton and other cellulosic fibers.Hydrogen peroxideØ It is used to destroy the chromophoric groups of the natural dyes in the cotton.
2.2. Experimental Investigation
2.2.1. Recipe for Pretreatment of Cotton Yarn
Table 1. The recipe for different shades |
| Chemicals | Quantity(g/L) | Imerol PCLF | 1.00 | Sirrix 2UD | 1.00 | Stabilizer SOF | 0.80 | NaOH solid | 2.50 | H2O2 50% | 3.00 | Temperature | 98°C | Time | 60 min. | M:L | 1:20 |
|
|
Pretreatment Evaluation○ Absorbency: Good○ Degree of Whiteness: avg. CIE White 86%○ Weight loss: avg. 5%○ PH of yarn =7
2.2.2. Dyeing Recipe
In this research the scoured & bleached cotton yarns of different count were dyed with reactive dyes of various colors in different shades to study the relation between the yarn count & shade% (which is a measure of dyeing performance). The recipe is given below:
In this recipe, shade% has been gradually increased for different colors. With the increase of shade% the brightness of color will be increased for higher count yarn.
2.2.3. Dyeing & after Treatment Curves
In this research 60°C Isotherm Exhaust method was used for dyeing process.In this method the temperature is kept 60°C & the time for dyeing is 60 minutes.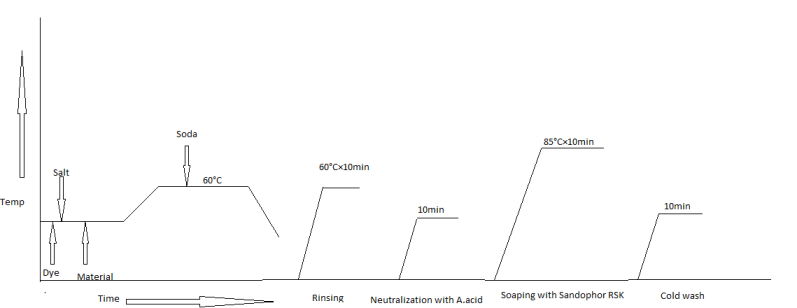 | Figure 1. Dyeing (standard and other parameters than temp) and after-treatments |
In this figure dyeing and after treatment process has been shown by curve.In the dye bath at first dye, salt and material were added. At 60°C soda was added. After dropping the dye bath rinsing was carried out for 10 minutes. Neutralization was done by acetic acid. After it soaping was done at 85°C for 10 minutes. Finally cold was carried out for 10 minutes.
3. Result & Discussion
3.1. For 0.2% Drimaren Blue HF-RL Shade
Table 2. Recipe For 0.2% Drimaren Blue HF-RL Shade 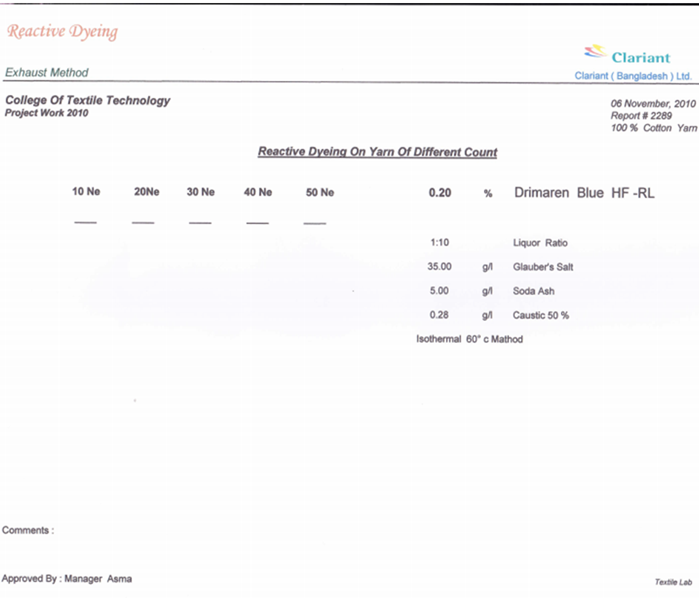 |
| |
|
3.1.1. For 0.2% Drimaren Blue HF-RL Shade, Spectrophotometric Value for Different Yarn Count Is Given Below
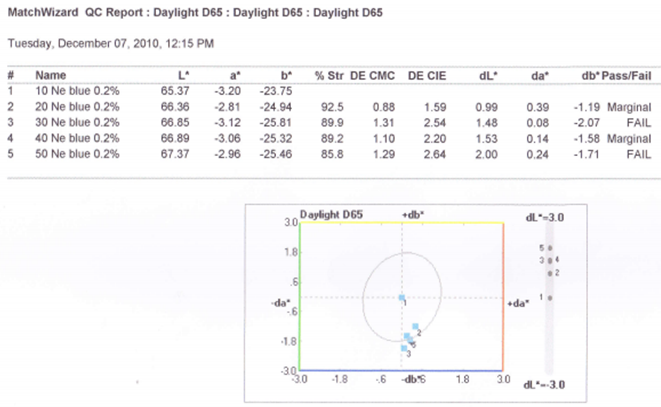
3.1.2. Graphical Representation
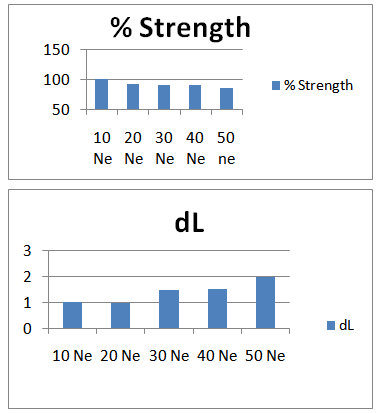 | Figure 2. Difference of strength% & dL (brightness) in different count of yarn |
3.1.3. Comments
Here from increasing count from 10Ne to 50Ne, color strength% is gradually decreasing for 0.2% Drimaren Blue HF-RL shade.In case of brightness the scenario is just opposite to the color strength%. Here from increasing count from 10Ne to 50Ne, the dL* value is gradually increasing.This generally reflects the theoretical concept of higher the cotton count, less the color strength & higher the brightness.
3.2. For 0.2% Drimaren Red CL-5B Shade
Table 3. Recipe for 0.2% Drimaren Red CL-5B Shade 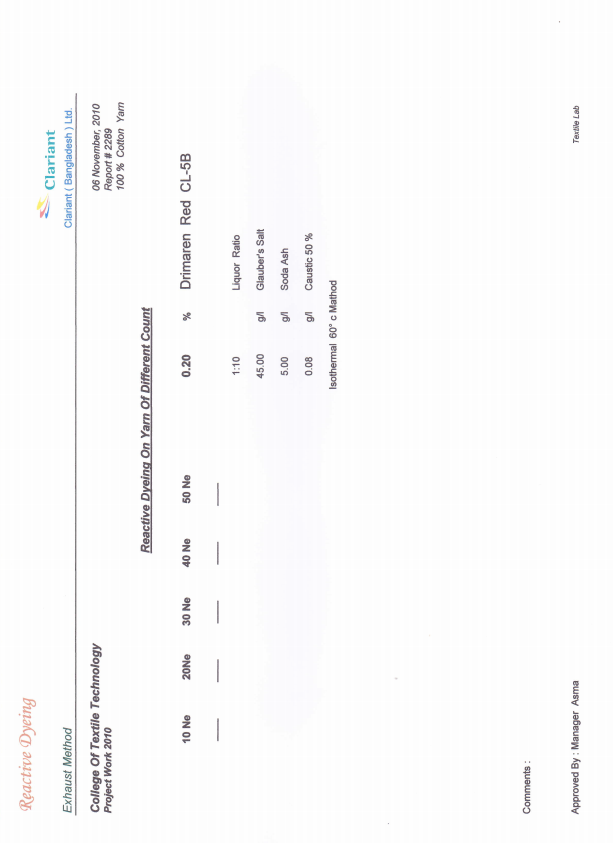 |
| |
|
3.2.1. For 0.2% Drimaren Red CL-5B Shade, Spectrophotometric Value for Different Yarn Count is Given Below
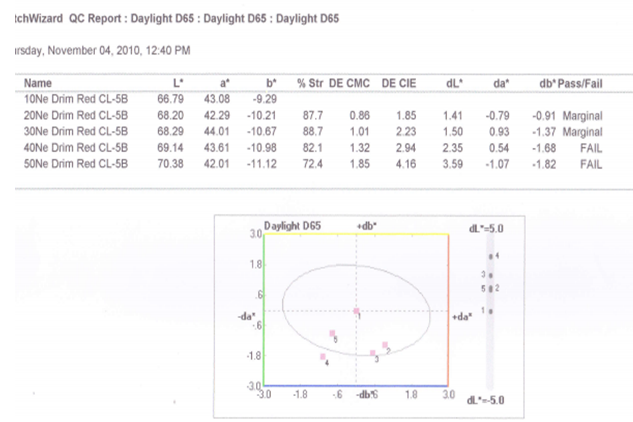
3.2.2. Graphical Presentation
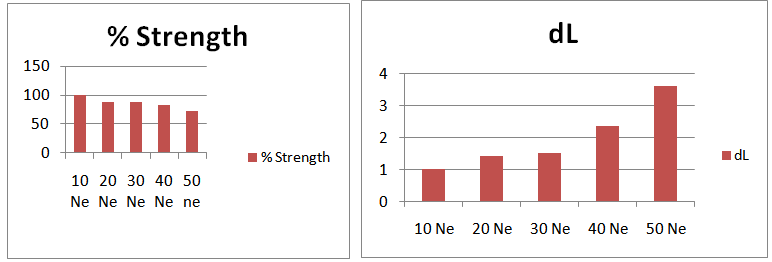 | Figure 3. Difference of strength% & dL (brightness) in different count of yarn |
3.2.3. Comments
Here from increasing count from 10Ne to 50Ne, color strength% is gradually decreasing for 0.2% Drimaren Red CL-5B shade.In case of brightness the scenario is just opposite to the color strength%. Here from increasing count from 10Ne to 50Ne, the dL* value is gradually increasing.This generally reflects the theoretical concept of higher the cotton count, less the color strength & higher the brightness.
3.3. For 0.2% Drimaren Yellow CL-2RShade
Table 4. Recipe for 0.2% Drimaren Yellow CL-2RShade 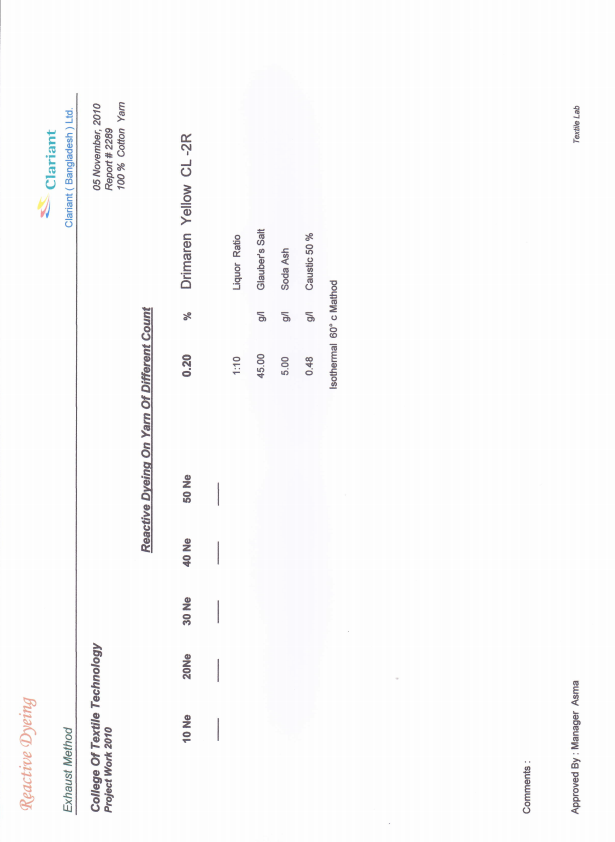 |
| |
|
3.3.1. For 0.2% Drimaren Yellow CL-2R Shade, Spectrophotometric Value for Different Yarn Count is Given Below
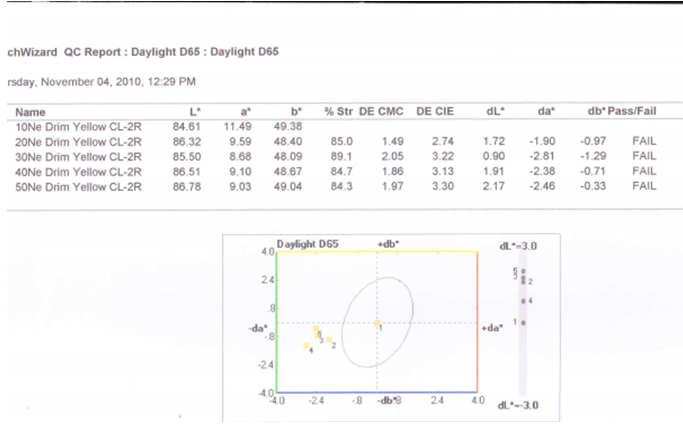
3.3.2. Graphical Presentation
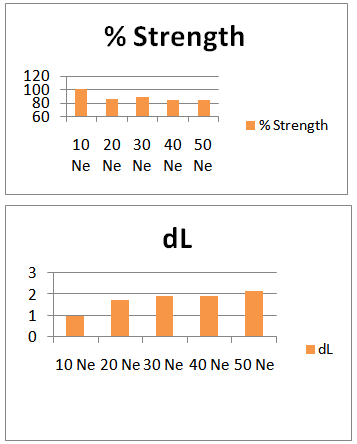 | Figure 4. Difference of strength% & dL in different count of yarn |
3.3.3. Comment
Here from increasing count from 10Ne to 50Ne, color strength% is gradually decreasing for 0.2% Drimaren Yellow CL-2R shade.In case of brightness the scenario is just opposite to the color strength%. Here from increasing count from 10Ne to 50Ne, the dL* value is gradually increasing.This generally reflects the theoretical concept of higher the cotton count, less the color strength & higher the brightness.
3.4. For 3% Drimaren Blue HF-RL Shade
Table 5. Recipe for 3% Drimaren Blue HF-RL Shade 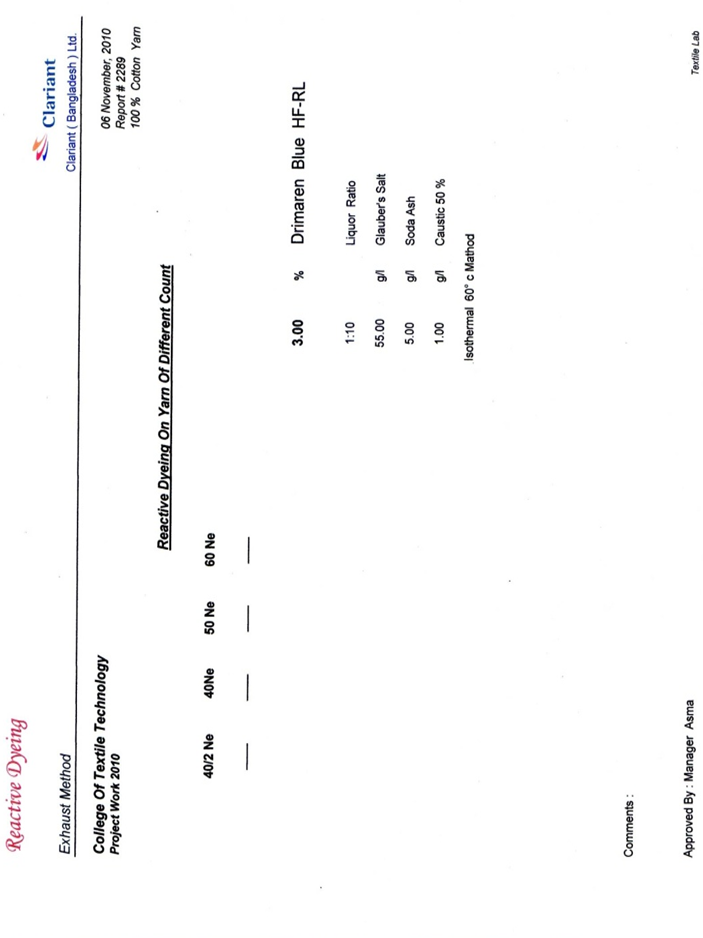 |
| |
|
3.4.1. For 3% Drimaren Blue HF-RL Shade, Spectrophotometric Value for Different Yarn Count is Given Below
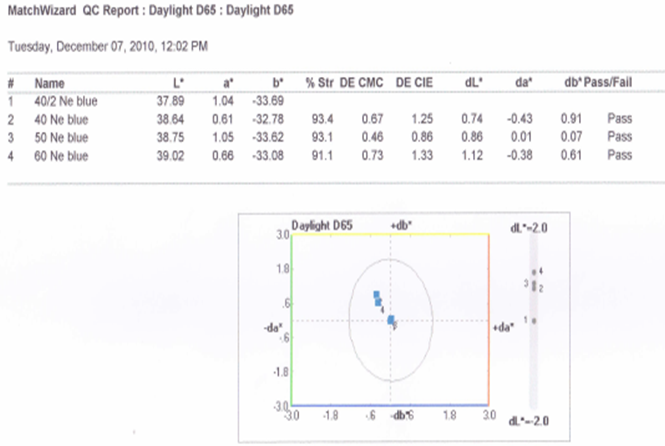
3.4.2. Graphical Presentation
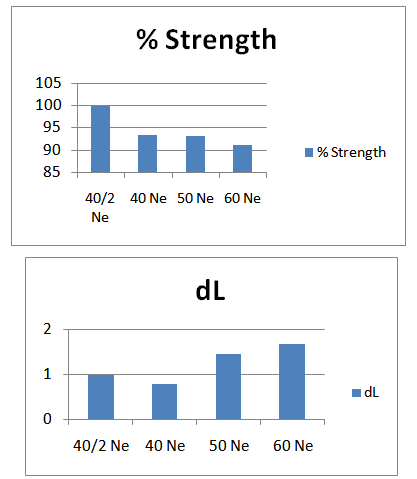 | Figure 5. Difference of strength% & dL in different count of yarn |
3.4.3. Comment
Here from increasing count from 40/2Ne to 60Ne, color strength% is gradually decreasing for 3%Drimaren Blue HF-RL shade.In case of brightness the scenario is just opposite to the color strength%. Here from increasing count from 40/2Ne to 60Ne, the dL* value is gradually increasing.This generally reflects the theoretical concept of higher the cotton count, less the color strength & higher the brightness.
3.5. For 3% Drimaren Red CL-5B Shade
Table 6. Recipe for 3% Drimaren Red CL-5B Shade 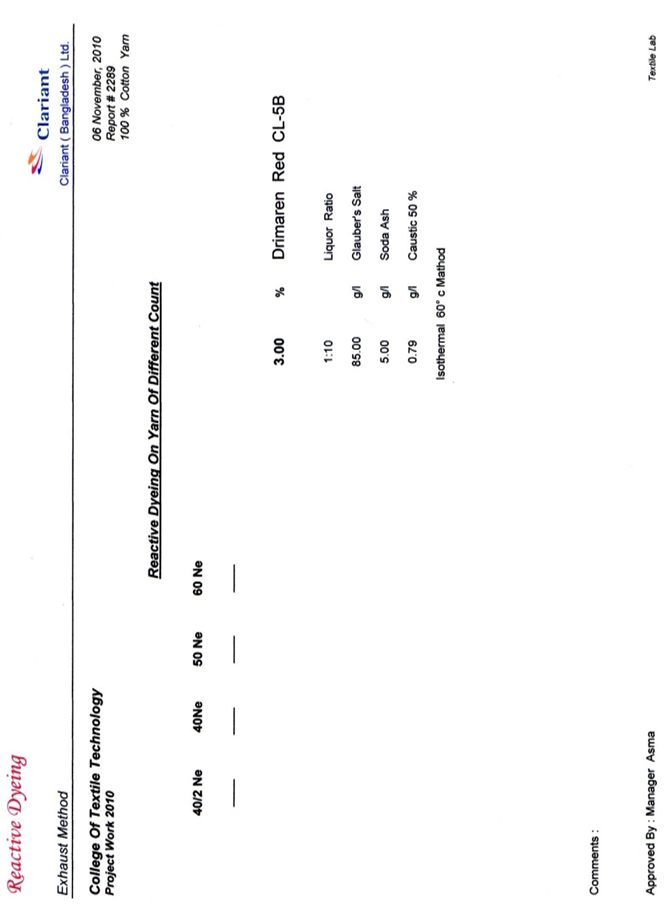 |
| |
|
3.5.1. For 3% Drimaren Red CL-5B Shade, Spectrophotometric Value for Different Yarn Count is Given Below
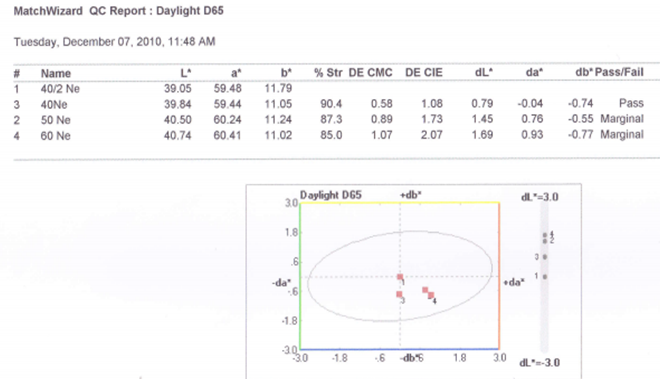
3.5.2. Graphical Presentation
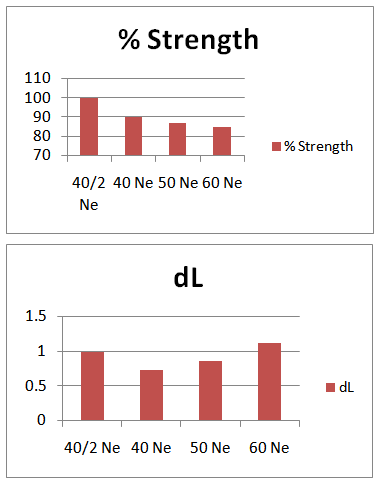 | Figure 6. Difference of strength% & dL in different count of yarn |
3.5.3. Comment
Here from increasing count from 40/2Ne to 60Ne, color strength% is gradually decreasing for 3%Drimaren Red CL-5B Shade.In case of brightness the scenario is just opposite to the color strength%. Here from increasing count from 40/2Ne to 60Ne, the dL* value is gradually increasing.This generally reflects the theoretical concept of higher the cotton count, less the color strength & higher the brightness.
3.6. Final Comment
From the spectrophotometric result, we come to this point that coarser yarns have higher build up property than finer one. As a result finer yarn becomes lighter than coarser yarn when these are dyed with the same dye in the same shade% under the same condition. So if we want to get the same depth of shade both in finer & coarser yarns then we should apply more dyes in case of finer yarn corresponding to the coarser yarn. In the dyeing of finer yarn in the same depth of coarser yarn higher amount of dye is needed so that dye consumption is increased in case of finer yarn.
4. Conclusions
In this research yarn has been collected from different sources but for better result yarn must be collected from the same lot and which is the output of the same spinning process.Latest spectrophotometer equipped with all the modern facilities required for the data was unavailable. Taking the research as a guide line, some further research is possible such as Finding out the fixation rate for each yarn count; various effects can be produced on the fabric, Development of the exhaust method.In this research the effects of yarn count on the dyeing performance of reactive dye in exhaust method were shown in various graphs. A general outline was drawn for future scope of work related to dyeing of yarn of different count with reactive dye in exhaust method. Comments were made, to show the relation between the theoretical data and practical experiments.
References
[1] | E.P.G. Ghol & L.D. Vilensky, Textile Science (1983), CBS Publishers & Distributors, 41-42. |
[2] | S. Gordon and Y-L. Hsies, Cotton: Science and technology (2007), Woodhead Publishing Ltd, 3-5. |
[3] | A.D. Broadbent, Basic Principle of Textile Coloration9201), SDC, 72. |
[4] | E.R. Troatman, Dyeing & Chemical technology of Textile Fibers (1975), Charles Giffin & Company Ltd, 44. |
[5] | Menachem Lewin & Stephen B. Sello, Handbook of Fiber Science and Technology Vol I part B (1993), CRC Press, 10-11. |
[6] | Warner & B. Steven, Fiber Science (1995), prentice-hall, 217. |
[7] | Md. Ashraful Islam, Science of Textile Raw Materials (1998), 3-8. |
[8] | http://en.wikipedia.org/wiki/cotton |
[9] | Textile terms & Definitions (1997), The Textile Institute, 272. |
[10] | J.R. Aspland, Textile Dyeing and Coloration (1997), AATCC, 113. |
[11] | Heinrich Zollinger, Color Chemistry: synthesis, properties, and applications of organic dyes and pigments9203), Helvetica Chimica Acta, 226. |
[12] | Prof. V.A. shenai, Technology of Textile Processing (Vol II): Chemistry of Dyes and Principles of Dyeing (1993), Sevak Publications, 519-522. |
[13] | John shore, Cellulosic Dyeing (19950, SDC, 212-213. |
[14] | John Shore, Colorants and Auxiliaries (Vol II): Chemistry of Dyes and Principles of Dyeing (1993), Sevak publications, 519-522. |
[15] | Prof. V.A. shenai, Technology of Textile Processing (Vol II): Chemistry of Dyes and Principles of Dyeing (1993), Sevak Publications, 519-523. |
[16] | http://www.ehow.com/facts_7843922_exhaust-dyeing-process.html#ixzz1FGFbZr7r17. |
[17] | A.K.R. Chowdhury, Textile Preparation & Dyeing (2000), Sevak Publications, 276-278. |
[18] | http:// www.devileye.net/.../useful_exhaust_dyeing.htm. |
[19] | Md. Ashraful Islam, Science of Textile Raw Materials (1998), Books Fair Publications, 87-89. |
[20] | Md. Ashraful Islam, Quality Control in Cotton spinning (2000), Books Fair Publications, 32-33. |