Salah. M. Saleh1, Yasser. A. Abd-El-Hady1, Kh. El-Badry2
1Cotton Research Institute, ARC, Chemistry Department, Giza, Egypt
2Faculty of Education, Industrial Education Division, Helwan University, Cairo, Egypt
Correspondence to: Salah. M. Saleh, Cotton Research Institute, ARC, Chemistry Department, Giza, Egypt.
Email: |  |
Copyright © 2012 Scientific & Academic Publishing. All Rights Reserved.
Abstract
This Work aimed to use pigments extracted from banana leaves as natural waste source to dye some Egyptian cotton fabrics. Both alkaline and acetone extracted solutions were analyzed by high performance thin layer chromatography (HPTLC) analysis technique. The solutions were applied to the pre-mordanted bleached and mercerized cotton fabrics made from Giza 86 and Giza 90 cotton varieties. Ferrous sulphate, copper sulphate and potassium dichromate were used as mordant. The factors affecting the fixation of the extracted dye with cellulose was studied. The treated and untreated fabrics samples were tested for their mechanical properties expressed as tensile strength (kg/force) and elongation%. Dyeing performance in terms of colour parameters (K/S, ∆L*, ∆a*, ∆ b* and ΔE), and fastness properties (wash, perspiration, and light fastness) were studied. The samples show high tensile strength, high colour strength, and high fastness properties. These results are very important for industrial application with the production of a natural dye as an inexpensive source from banana leaves as a by-product. Another objective is to increase the production of eco-textile garments with a good price for the Egyptian customers.
Keywords:
Egyptian Cottons, Banana Leaves, Natural Dye, Eco-Textile
Cite this paper: Salah. M. Saleh, Yasser. A. Abd-El-Hady, Kh. El-Badry, Eco-friendly Dyeing of Cotton Fabric with Natural Colorants Extracted from Banana Leaves, International Journal of Textile Science, Vol. 2 No. 2, 2013, pp. 36-40. doi: 10.5923/j.textile.20130202.04.
1. Introduction
The use of synthetic dyestuffs during their application in the dyeing and printing industries has been criticized due to introduction contaminants into the environment[1]. The beginning of the new millennium is sure to bring about many drastic changes in the life of mankind. One of them is going to be the shift towards natural dyes and their efficient usage compared to synthetic counterpart who have been slowly losing, mainly due to international awareness to environment and ecology preservation[2]. Calls for the use of natural dyes on textiles have been just one of the consequences of increased environmental awareness[3]. The use of natural dyes for the coloration of textiles has mainly been confined to craft dyes and printers. Recently, more interests have been devoted to the use of these dyes and a limited number of commercial dyes and small business have started to look at the possibilities of using natural dyes for dyeing and printing of textiles[4]. Natural dyes are less toxic, non pollutant, less health hazard, very brilliant, rare colour idea, and allergic reactions[5-7]. The annual cultivated area from banana plant in Egypt was about 620000 feddans in 2010. It gave about 464 tons dry matter (about 1116 tons fresh weight) of banana products. These by products are collected from the field and burned after being sun dried, causing environmental pollution.The objective of this study is to produce a natural dye as an inexpensive source from banana leaves as a waste and to increase the production of eco-textile garments with a good price for the Egyptian customers.
2. Materials and Methods
2.1. Materials
Unbleached long staple Egyptian cotton fabrics made from Giza 86, and Giza 90 were purchased from Misr-El-Mehala Company for Spinning and Textile- Egypt. The fabrics have the following specification: plain woven warp 36 yarn/cm, weft 30 yarn / cm, and fabric weight 150g/m2.
2.2. Chemicals
All chemicals used were of analytical grade using doubly distilled water (18.5 MΏ.cm-1). NaOH was analytical grade (Koch-Light Co.), Hydrogen peroxide (30% LR grade) from Aldrich. Sodium carbonate (LR grade), sodium silicate (136ْ Tw, 27% SiO2), the wetting agent was the commercially Ttiton 100 supplied by Merck. Acetontrile, and formic acid was of HPLC grade.Scouring, bleaching and mercerizing treatmentsThe fabric samples were scoured, bleached and mercerized was carried out according to our previous work[15].
2.3. Banana Leaf Pigments Extraction
2.3.1. Alkaline Extraction
About 100 g of the banana leaves boiled in one litre in a solution of 0.1% NaOH and concentrated to 500 cc. The slurry was left to react for a period of time and then filtered to discard any solid material. The extracted liquor was used as the foundation of the dye.
2.3.2. Acetone extraction
About 100g of Banana leaves was added in one litre acetone in sohxselt apparatus (closed system) until pieces colourless. The solution is then filtrated from any solid material. The extracted liquor was used as the foundation of the dye. Acetone was then recycled and used again for the continuous processes.
2.4. Dyeing bath Process
2.4.1. Fabrics dyed with Alkaline Extraction
The cotton fabrics were dyed using the alkaline banana leaves extraction liquors in the dyeing bath at 80◦C for 90 minutes under stirring conditions. The pH of the dye was adjusted to 9, the liquor ratio (1:40). After completion of dyeing, the fabrics were washed with water and air dried.
2.4.2. Fabrics dyed with Acetone Extraction
The cotton fabrics were dyed in a closed dyeing bath at 56℃ for 5 minutes under stirring conditions, the liquor ratio (1:40). After completion of dyeing, the fabrics were washed with water and air dried.
2.5. Evaluation the Properties of the Treated Fabrics
2.5.1. Tensile Properties
The tensile strength (kg/force) and elongation (%) were measured according to ASTM D412-98a using Zwick testing machine of model Z010 and equipped with 10Kn load cell and the testing was conducted at speed of 100mm/min. The results obtained were based on an average of ten tests in the wrap direction of each sample.
2.5.2. Dyeability Measurements
The colour strength (K/S) of the treated samples using the untreated samples as blank was determined using Perkin Elmer Spectrophotometer, Model Lambda 35 equipped with integrated sphere with applying the Kubelka-Munk equation: K/S =[(1-R) 2/ 2R]The colour parameters ∆L* (lightness-darkness), ∆a* (red-green), ∆b* (blue-yellow component), and ∆E were measured by using the Win lab software CIE TC1-29 proposed colour difference equation.
2.5.3. Fastness Properties
(a) Washing fastness (WF)Washing fastness of the untreated samples was done according to ISO 105- C01:1998(E). Two single fiber adjacent fabrics complying with the relevant sections of F01 to F08 of ISO 105-F: 1989. The first one is adjacent fabric of cotton and the second of wool.(b) Perspiration fastness (PF)Fastness to synthetic perspiration was measured according to ISO-E04: 1994.(c) Light fastnessFastness of light was measured according to the ISO 105:1997 using standard wool serge as reference in all testes.
2.6. High Performance thin Layer Chromatographic Analysis (HPTLC)
A CAMAG TLC system comprising of a Linomat-5 applicator, CAMAG TLC scanner and single pan balance of Shimadzu model was used, for the present study. Stationary phase used was silica gel G60F254, 20x10 cm TLC plate activated at 75◦C for 20 min, the mobile phase used was forestal solvent conc. HCl:HOAc:H2O (3: 30: 10). The plates were developed by ascending method in a CAMAG twin through glass chamber (20 x 10 cm) saturated with filter paper for 10 minutes. Distance of solvent front 80 mm, band length 8 mm, slit dimension 6.00 x 0.30 mm, detection wavelength 254 nm, temperature 26.4◦C and humidity 61% were used for the present study.Banana leaves extracts were used as stock solution spotted on pre-coated TLC plates using Linomat 5 applicator, plates were developed and scanned using CAMAG TLC scanner 3. The plate was developed and the spots were scanned, peak, height, areas and Rf values were measured
3. Results and Discussion
Alkaline extraction of the Banana leaves characterize the pigment compounds luteolin and apigenin. HPTLC chromatogram of these compounds was shown in Figure 1. The spectral data show the maximum absorption for the chromatographic peak as Luteoline Rf of 66 and Apigenin Rf of 82 respectively. Luteolin and Apigenin are the more common flavones most often found in leaves, but it is also present in rinds, barks, and clover blossom and ragweed pollen[16]. Acetone extraction of the banana leaves characterize the pigment compounds chlorophyll a, b and β-Carotene as shown in Figure 2The spectral data show the maximum absorption for the chromatographic peak as Chlorophyll b Rf of 24, Chlorophyll a Rf of 71, and β-Carotene Rf of 82 respectively, its due to the green colour of chlorophyll,it may be used as dye and pigments and used in coloring soaps ,oils ,waxes, and conjectomany .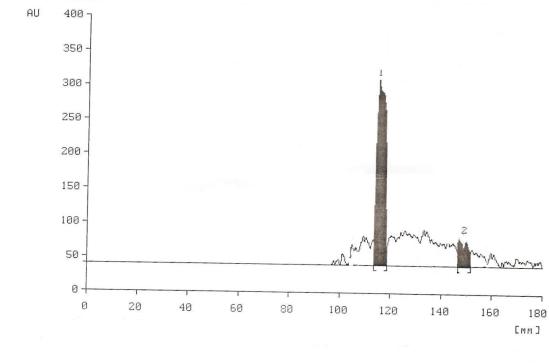 | Figure 1. HPTLC chromatogram of the alkaline banana leaves crude extracted |
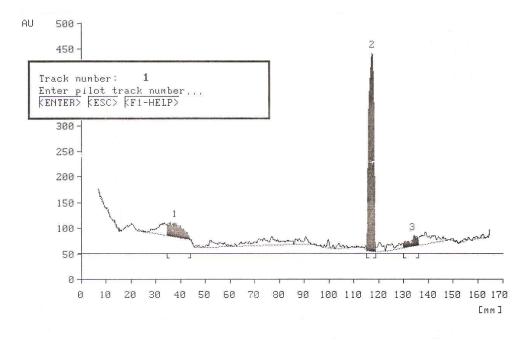 | Figure 2. HPTLC chromatogram of the banana leaves crude extracted by acetone |
Table 1. Mechanical properties of the scoured, bleached and mercerized cotton (Giza 86 and Giza 90) dyed with banana leaves alkaline & acetone extract 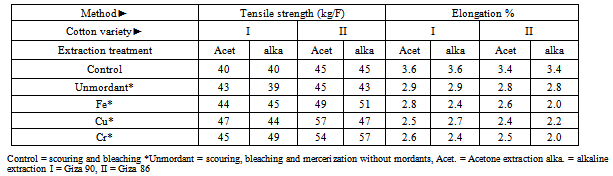 |
| |
|
Table 2. Colour measurements of cotton Giza 86 and Giza 90 fabrics dyed with alkaline Banana leaves extraction 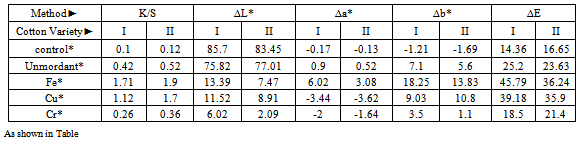 |
| |
|
Table 3. Colour measurements of cotton Giza 86 and Giza 90 fabrics dyed with acetone Banana leaves extraction 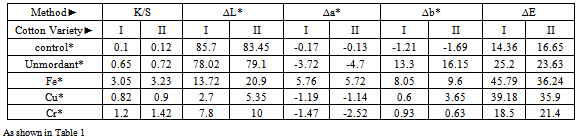 |
| |
|
Table 4. Fastness properties of Giza 86 and Giza 90 fabrics dyed with alkaline and acetone banana leaves extract 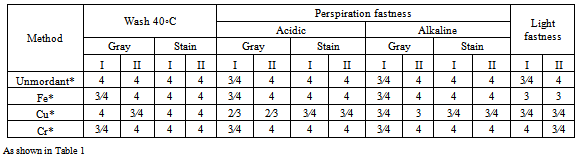 |
| |
|
3.1. Tensile Properties
The results obtained from Table 1 revealed that fabric tensile strength and elongation (%) for the alkaline or the acetone dyeing fabric of Giza 86, and Giza 90 (raw material) had higher tensile strength among the unmordanted fabrics. This is due to the damage effect of the scouring and the bleaching materials on the cellulosic polymers within the cotton fibers. The addition of the mordant increases the tensile strength for the two fabrics due to the formation of cross linking due to the reaction of the metals with the free hydroxyl ions of cotton causing orientation of the cellulose chain. The results obtained showed maximum value of tensile strength by the addition of Cr, and minimum value by the addition of Cu. The tensile strength of scoured, bleached, and mercerized fabric samples decreased than the scoured and bleached fabric samples. This is due to increase the amorphous region. Giza 86 also shows increase in tensile strength than that of Giza 90. On the other hand, both the two fabrics control (raw materials) had higher elongation% among the unmordanted fabrics. This is due to the damage effect of the scoured or the bleached agents on the elongation (%) of the fabrics. The addition of the mordant decreases the elongation (%) for the same reason. The results obtained showed maximum value of elongation% by the addition of Cu, and minimum value by the addition of Cr. The scoured, bleached, and mercerized fabric samples showed higher elongation% than the scoured and bleached fabric samples, and Giza 86 also shows decrease in elongation (%) than that of Giza 90.
3.2. Measurement of the Dyeability
Table (2), and (3) shows K/S (measure of colour strength), ∆L* (lightness-darkness), ∆a* (red-green), ∆b* (blue-yellow component) and total colour difference (∆E ) of the scoured, bleached and scoured, bleached and mercerized of both Giza 86, and Giza 90 cotton fabrics before and after mordanting treatment. The results obtained revealed that there were a higher K/S values for both mercerized Giza 86, and 90 samples. However, the mordant samples had a higher K/S values than the unmordanted samples. Giza 86 cotton samples shows a higher K/S values than those of Giza 90 at all conditions. The results obtained revealed that the values of ∆L*, ∆ a*, and ∆b* have been changed by the addition of the mordents which shift the colour of the dye due to the reaction between the metal ion and the mordant used. It has been noted that mordanting with iron gave a maximum ∆E, which is mainly attributed to the lower values of ∆L*, due to the high stability formation of the complex between the Fe and luteoline as a phenolic compound and luteoline. For the alkaline extraction, it was observed that iron gave a stronger yellowish brown colour, while Cu produced a greener colour, and Cr produced a very fade yellow colour. For the acetone extraction, it was observed that iron gave a stronger yellowish brown colour, while Cu and Cr produced a yellowish-green colour, Fastness propertiesThe results listed in Table (4) illustrate the effect of various mordants on the fastness properties of Giza 86, and Giza 90 cotton fabrics. When the dyeing after mordanting were compared with the unmordanted samples, it is clear that the mordanted fabrics showed a slight fastness improvement. It is evident that, the stronger the dye-fiber bond, the easier is the transfer of the excitation energy from the dye molecule to the fiber macromolecular chain. Thus, the dye –fiber bond serves as a bridge for transferring the excitation energy between the two components of the dye fiber ambient system. If this bond promotes the energy transfer, the light fastness increases. There were no significant difference of the fastness properties for all Giza 86 and Giza 90 fabric samples.
4. Conclusions
The use of pigments extracted by acetone and alkaline solution from banana’s leaf as natural waste source to dye some Egyptian cotton fabrics has been achieved. The treated and untreated fabrics samples were tested for their mechanical properties expressed as tensile strength (kg\f) and elongation (%). Dyeing performance in terms of colour parameter (K/S, ∆L*, ∆a*, ∆b* and ΔE), and fastness properties (wash, perspiration, and abrasion) were studied. The samples show a high tensile strength, high colour strength, and high fastness properties. We believe that the results obtained here are interesting for industrial application due to the production of a natural dye as an inexpensive source from banana peel as a by product. Another objective is to contribute in solving or decrease the problem of burning banana leaf, causing environmental pollution.
References
[1] | Lokhande H.T. Vishnu A. Dorugade 1999. American dyestuff Reporter, February, 29-34. |
[2] | Bhattacharya S.C. and Santhosm Mathew. 2002. Colourage. Sept., 19-23. |
[3] | Chavan R. B. 1998. Colourage, XLII. No.4, April. P 27. |
[4] | Das, S. 1992. colourage, XXX1X, No. 9, Sept., p.52. |
[5] | Katyaynini V. K. and Jacob M. 1998. The Ind. textile journal., 108, No.4, p. 86 |
[6] | Gupta V.K. Sachon R. A. Singh V. P. and Sharma V.P. 1998. The Indian Textile Journal, 108, No.4,p.16American Association for Textile Chemist and Colorist, AATCC test method 16-1972 |
[7] | Mehra R. H. and Mehra A. R. 1994. Colourage, XL1, No.12, p.25 |
[8] | Zaffari G.R., Peres L.E.P., and Kerbauy G.B. 1998. J Plant Growth Regul., 17, p. 59- 61. |
[9] | Inderpal R., 2005, Current Science, 88, No. 9, 10 May, p. 1370. |
[10] | Von Loesecke H. 1929. J. Amer. Chem. Soc., 51, 2439-2443. |
[11] | Subagio A, Morita N, Sawada S. 1996. J. Nutr. Sci. Vitaminol (Tokyo). Dec. 42, No.6, 553- 66. |
[12] | Simmonds N. W. 1954. Nature 173, 402 - 403. |
[13] | American Society for Testing and Materials, ASTM D (412-98a) |
[14] | Bobby G. United States Patent 6013260, 01/11/2000 |
[15] | Salah Mansour Saleh. 2012. Antibacterial Activity and UV Protection Property of Some Egyptian Cotton Fabrics Treated with Aqueous Extract from Banana PeelInternational Journal of Clothing Science, 1 (1):1-6. |
[16] | Kerley M.S., Garleb K.A., Fahey G.C., Jr., Berger L.L., Moore K.J., Phillips G.N. and Gould J.M. 1988. J..Anim. Sci. 66: 3235- 3244 |