FarehaAsim1, Naheed Kausar2, Muzzaffar Mahmood3
1Textile Engineering Department, NED University of Engineering & Technology Karachi, Pakistan
2Research Industrialization Division, PCSIR Laboratories Complex Karachi, Pakistan
3Mechanical Engineering Department, NED University of Engineering & Technology Karachi, Pakistan
Correspondence to: FarehaAsim, Textile Engineering Department, NED University of Engineering & Technology Karachi, Pakistan.
Email: |  |
Copyright © 2012 Scientific & Academic Publishing. All Rights Reserved.
Abstract
The mechanism of dye fixation on cotton fabric using single step fixation of reactive printing and crease resistance finishing has been examined in this research work. Monochlorotriazine based reactive dyes can chemically combine with hydroxyl groups of cellulose fabric by a nucleophilic substitution reaction and as a result an ether linkage is formed. In contrast, modified DMDHEU mainly contains N-alkoxymethyl groups and during the finishing process, the most preferable reaction of N-methylol anions is with hydroxyl groups of the cellulose. The developed reaction mechanism indicates that MCT based reactive dyes can be chemically combined with hydroxyl groups of cellulose as well as modified DMDHEU that is cross linked with cellulose fabric in a single step fixation of reactive printing and crease resistance finishing.
Keywords:
Crease Resistance Finishing, DMDHEU, MCT, Reactive Printing
Cite this paper: FarehaAsim, Naheed Kausar, Muzzaffar Mahmood, Reaction Mechanism of Single Step Fixation Process of Reactive Printing and Crease Resistance Finishing of Cotton Fabrics, International Journal of Textile Science, Vol. 2 No. 2, 2013, pp. 26-29. doi: 10.5923/j.textile.20130202.02.
1. Introduction
The theoretical fixation mechanism of Monochlorotriazine based reactive (MCT) dye and modified dimethyloldihydroxy ethylene urea (modified DMDHEU) using single step fixation process is being discussed in this research work.Reactive dyes are the most popular application class used to dye cellulose fibres. It forms covalent bond with cellulose. Due to the strong primary bonding between dyes and fibres, it possesses high level of fastness. The major drawback of reactive dyes is hydrolysis in which dye instead of reacting with fibre reacts with the hydroxide anion of the base[1].Cotton is an important fibre in textiles, because of its numerous advantages. One of the main disadvantages of cotton is creasing after washing[2]. On creasing the cotton fabrics, the molecular chains in the amorphous region slip past each other, breaking the weak hydrogen bonds. The stretched chains then form hydrogen bonds in the stretched places and thus the fabric holds the creases. The mechanism of the crease recovery process in cotton fibres is based on introducing stable cross-links so as to prevent slippage of molecular chains[3].Different types of formaldehyde based crease resistants have been used for crease resistance finishing of cotton fabric. Dimethyloldihydroxy ethylene urea (DMDHEU) based crease resistants are commonly used in the textile industry due to their numerous advantageous[4]. In the present research work, modified DMDHEU has been used which has low formaldehyde content unlike unmodified DMDHEU[4]. As discussed, MCT based reactive dye and modified DMDHEU can react with the hydroxyl groups of cotton fabric. The rate of bond formation between substrate and crease resistant finish or MCT dye is not only influenced by various external parameters but it is also greatly dependent on the nature of the alkyl group attached with modified DMDHEU and various other functional groups attached with the MCT dye.Various attempts[5-10] have been made on combining crease resistance finishing with reactive dyeing and finishing process to capture the potential time, energy, and other savings associated with the single step process. Some research[11-14] was found regarding a single step process of reactive printing and crease resistance finishing. However, there were no data reported regarding the reaction mechanism of the reactive dye and the crease resistant in the single step print-finish fixation of cotton fabrics.
2. Single Step Fixation Process
2.1. Preparation of Print Paste
A concentration of 3% w/w of Alginate thickener was added to produce stock paste, with continuous high speed stirring, to the required volume of water. This was followed by the gradual addition of alkali: sodium bicarbonate 30 g/kg, reduction inhibitor: Revatol S 50 gm/kg and sequestrant: sodium hexameta phosphate 5 gm/kg with continuous stirring giving a final stock paste viscosity of 60-65dPa. The 3% Drimarine Red P2B(Clariant) based on MCT reactive group is finally added to the stock paste.
2.2. Preparation of Crease Resistance Finish Liquor
The crease resistant finishing liquor was prepared by using modified dimethylol di hydroxyl ethylene urea: Fixapert F-ECO (BASF) 100 g/l, silicon softener:Solusoft MW 20g/l, Ionic softener: Ceranine-L 20g/l, wetting agent: Invadine PBN 5g/l and Catalyst: MgCl215 g/l.
3. Application Method
The single step fixation process is carried out as follows;In the first step the fabric was immersed in an aqueous solution of crease resistant finish liquor containing, and then squeezed to obtain a 70% wet pickup. The wet fabric was then dried at 100°C for 1 min. In the second stage the treated fabric was printed by the lab scale Rotary Printing machine (Zimmer).The print-finish fabric is simultaneously fixed through the Econtrol process at 130-135˚C for 5 minutes The fixed samples are finally washed in 1g/l non-ionic detergent until all unreacted dyes and chemicals were removed from the fabric surface.
4. Reaction Mechanism
Modified DMDHEU mainly contains N-alkoxymethyl groups (Fig. 1). During the finishing process, the most preferable reaction of N-methylol anions is with hydroxyl groups of the cellulose (Eq. 1). 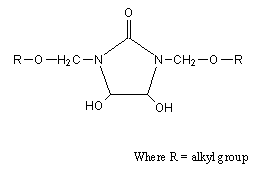 | Figure 1. General structure of modified DMDHEU |
N-methylol anion may also react with themselves or with reaction NH groups if splitting of acetylic bonds is catalytically accelerated by acids or bases (Eq. 2 and 3)[15]. Hydroxyl groups attached with the heterocyclic ring of modified DMDHEU can also be substituted by o-cellulose residues under certain reaction condition[16].A general structure of MCT based reactive dye is shown in Fig. 2.MCT based reactive dyes are chemically combined with hydroxyl groups of cellulose fabric by a nucleophilic substitution reaction and as a result an ether linkage is formed (Eq. 4)[17].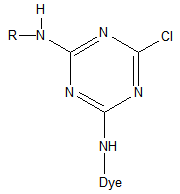 | Figure 2. General structure of MCT reactive dye |
 | (1) |
 | (2) |
 | (3) |
The rate of hydrolysis and the reaction of MCT dye with the hydroxylate anion of cotton are influenced by the nature of the subsituent groups, attached to the monochlorotriazine heterocyclic nucleus, and many other factors[18]. Alkaline pH is the cause of the hydrolysis (Eq. 5), while at the same time it increases the ionizing power of hydroxyl groups of cellulose (Eq. 6) and helps to fix the dye with the substrate (Eq. 7). Chemically, if crease resistant pick up is 100%, MCT reactive dyes can be chemically combined with hydroxyl groups of modified DMDHEU, cross linked with cotton fabric (Eq. 8) or with hydroxyl groups (Eq. 4) of cellulose as well as modified DMDHEU that is cross linked with cellulose fabric (Eq. 8) if crease resistant pick up is less than 100%.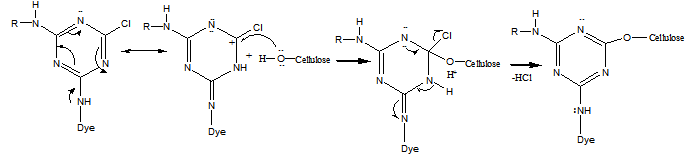 | (4) |
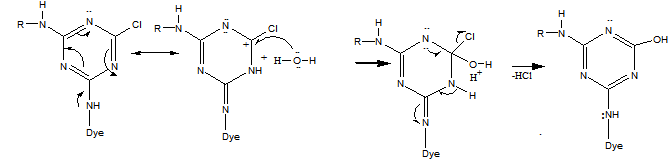 | (5) |
 | (6,7) |
As discussed earlier,in the developed single step print-fix fixation process, the crease resistant pickup is 70%. Therefore, MCT based reactive dye and modified DMDHEU may fix to the cotton fibre following the reaction mechanism stated in Equations 4 and 8.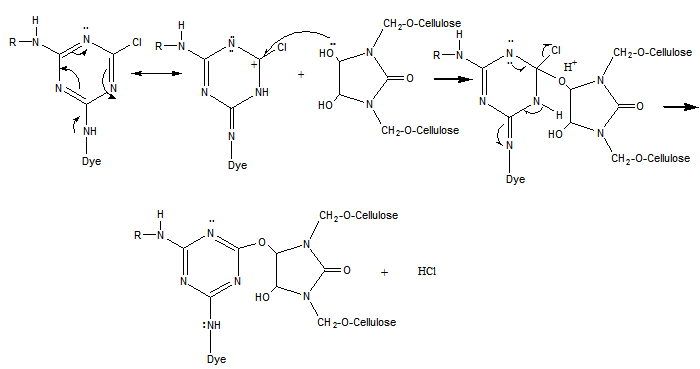 | (8) |
From the above chemical equations it is clear that reaction mechanism of single step print-finish process consists of the following steps.1. Adsorption of crease resistant and reactive dye on fibre surface.2. Diffusion of crease resistant and reactive dye into pores of the fibre.3. Cross linking of crease resistant with hydroxyl group of cotton fibre as well as reactive dye. 4. Covalent bonding of dye with hydroxyl group of cotton fibre, thus entrapping the crease resistant inside the fibre by covalent bonding with cellulose chains.
5. Conclusions
A reaction mechanism for the single step process with a Monochlorotriazine based reactive dye and modified dimethyloldihydroxy ethylene urea based crease resistant has been developed validating the premise that the reactive dyes do chemically combine with hydroxyl groups of the cotton fabric as well as a crease resistant that is cross linked with the cotton fabric in the single step fixation process under certain reaction conditions.
ACKNOWLEDGEMENTS
The authors acknowledge the permission given by Gul Ahmed Textile Mills Ltd, for carrying out the necessary experimental work and PCSIR for their assistance.
References
[1] | D. R. Waring, G. Hallas, “The Chemistry and Application of Dyes”, Plenum Press (1990) |
[2] | W.D. Schindler, P.J. Hauser, “Chemical Finishing of Textiles”, The Textile Institute, 51 (2004) |
[3] | J. T. Marsh, “Introduction to Textile Finishing”, Chapman and Hall (1996) |
[4] | W.D. Schindler, P.J. Hauser, “Chemical Finishing of Textiles”, The Textile Institute, 58-66 (2004) |
[5] | A. Chakraborty, C. Dutta, “Kinematics of Concurrent Dyeing and Finishing – A Critical Study”, Proceedings of International Conference on Energy and Environment, March (2009) |
[6] | H. M. Choi, M. Srinivasan, N. M. Morris, “Single-Step Dyeing and Finishing Treatment of Cotton with 1, 2, 3, 4-Butanetetracarboxylic Acid”, Journal of Applied Polymer Science, 54(13), 2107-2118 (1994) |
[7] | Y. Dong, J. Wang, P. Liu, “Dyeing and Finishing of Cotton fabric in a Single Bath with Reactive Dyes and Citric Acid”, Coloration Technology, 117(5), 262-265 (2001) |
[8] | B. Herman, B. Arthur, A. Hans, “Process for the Dyeing or Printing and Simultaneous Finishing of Cellulose Materials”, US Patent 3983588, May (1976) |
[9] | M. Montazer, M. G. Afjeh, “Simultaneous X-linking and Antimicrobial Finishing of Cotton Fabric”, Journal of Applied Polymer Science, 103(1), 178-185 (2007) |
[10] | M. M. G. Fouda, A. El Shafei, S. Sharaf, A. Hebeish, “Microwave Curing for Producing Cotton Fabrics with Easy Care and Antibacterial Properties”, Carbohydrate Polymers, 77(3), 651-655 (2009) |
[11] | S.M. Mortazavi, M.A. Alsharif, M. Jannesari, “A study on Simultaneous Fixation of Reactive Dye Printing and Crease Resist Finishing on Cotton Fabric (Effect of DMDHEU Concentration, Types of Catalyst and Drying Conditions)”, http://140.134.132.124:8080/dspace/bitstream/2377/3912/1/ce05atc902007000039.pdf |
[12] | F. Asim, M. Mahmood, “Reactive Printing & Crease Resistance Finishing of Cotton Fabrics. Part-I Study of Influential Factors by an Experimental Design Approach”, Journal of Textile & Apparel, Technology and Management, Volume 7, Issue of Spring (2011). |
[13] | F. Asim, M. Mahmood, “Reactive Printing and Crease Resistance Finishing of Cotton Fabrics-Effects of Fixation Modes by 22.41 Mixed Factorial Design”, International Journal of Textile Science, 1(6), 94-100 (2012). |
[14] | F. Asim, M. Mahmood, “Effects of Process Parameters on Single Step Fixation of Reactive Printing and Crease Resistance Finishing of Cotton Fabrics using 23 Factorial Design”, International Journal of Textile Science”, 2(1), (2013). |
[15] | B. Voncina ,D. Bezek, A. M. le Marechal, “Eco-Friendly Durable Press Finishing of TextileInterlinings”, Fibre and Textile in Eastern Europe , 68-71, July/September (2002) |
[16] | H. Petersen, “Recent Developments in the Chemistry of Cross-Linking Agents”, Textile Research Journal, 40 (4), 335-344 (1970) |
[17] | K. Hunger (Editor), “Industrial Dyes; Chemistry, Properties, Applications”, Third Edition, 350-353 (2003) |
[18] | S. Abata, K. Akahor, U. Meyer, H. Zollinger, “Cellulose Dyeing Parameters of 18Isomeric Phenylazo-H-Acid Dyes Containing Two Different Reactive Groups”, Journal of the Society of Dyers and Colourists, 107(1), 12-19 (1991) |