Fareha Asim1, Muzzaffar Mahmood2
1Department of Textile Engineering, NED University of Engineering, Technology Karachi, Pakistan
2Department of Mechanical Engineering, NED University of Engineering, Technology Karachi, Pakistan
Correspondence to: Fareha Asim, Department of Textile Engineering, NED University of Engineering, Technology Karachi, Pakistan.
Email: |  |
Copyright © 2012 Scientific & Academic Publishing. All Rights Reserved.
Abstract
A single step fixation for reactive printing and crease resistance finishing of cotton fabric has been explored in this research work using an experimental design technique (DOE).22.41 mixed factorial design have been conducted to efficiently identify the active set of factors and their interaction. All of the three factors namelychroma, concentration of crease resistant and fixation conditions were found to be significant.The results further show that apart from the influence of individual factors, the said properties of cotton fabric are also reliant on the interaction effect of the significant factors. The influence of individual factors and their interactions on color yield (K/S) and Dry Crease Recovery Angle (DCRA) has been critically examined using software Design Expert 7.0.The results showed that combination of the Econtrol* process at 130˚C without urea has been verified experimentally to be the best selection for the single step fixation of reactive printing and crease resistance finishing for the cotton fabric using the pad-dry-print-fix method. The uncertainty analyses for measurements shows that the predicted values are in good agreement with experimental data and are sufficiently accurate.
Keywords:
DOE, Econtrol, Reactive Printing, Crease Resistance Finishing, K/S, DCRA
Cite this paper:
Fareha Asim, Muzzaffar Mahmood, "Reactive Printing and Crease Resistance Finishing of Cotton Fabrics-Effects of Fixation Modes by 22.41 Mixed Factorial Design", International Journal of Textile Science, Vol. 1 No. 6, 2012, pp. 94-100. doi: 10.5923/j.textile.20120106.06.
1. Introduction
Modern textile processes have high demand for development of a combined application of crease resistance finishing and reactive printing. A number of experimental and numerical studies on simultaneous fixation of reactive dyeing and crease resistance finishing have become available in recent years. However, some studies have reported on combined application of reactive printing and crease resistance finishing that probably due to contradictory application and fixation conditions of both processes, it is difficult to develop an acceptable combination. There are numerous factors that influence the printing process of cotton fabric with reactive dyes. A number of theoretical and experimental studies exist providing detailed information about the effect of process parameters and operating conditions[1-9]. Since the 1950s many researchers [10-15] have attempted to combine reactive dyeing and crease resistance finishing processes into one step to capture the potential time, energy, and other savings associated with the combined process. Some research[16] was conducted on combining CR finishing and pigment printing. Such combined application of finish and print, may not be favourable due to the differential finish effects resulting from the localisation of paste to an area of print design on the treated substrate.In summary, most prior studies did not experimentally evaluate the single step fixation process of reactive printing and crease resistance finishing. To make this technology practical, a new approach needs to be developed that gives high dye fixation, excellent crease recovery in a one step process.
2. Experimental
2.1. Materials
2.1.1. Fabric
Commercially singed, desized, scoured, bleached and mercerized cotton fabric with satin weave structure, 40x40 s, 130 ends/inch x 73 picks/inch, and an area density of approximately 136 g/m2.
2.1.2. Chemical and Colorants
The Crease recovery finishing agent used was Arkofix NEC (Clariant), based on modified dimethyloldihydroxy ethylene urea. Magnesium chloride (MgCl2) was used to catalyze the CR finishing, Solusoft MW (Silicon softener), Ceranine-L (An ionic Softener) and Imercol PCLF (Wetting Agent).The reactive dye used was Drimarine Red P2B (Clariant), based on the MCT reactive group. Other chemicals used were commercially available thickener Lamitex HP (sodium alginate), sodium bicarbonate, urea, reduction inhibitor (RevatolS) and sodium hexametaphosphate as a sequestrant.
2.2. Methods
Print-finish paste manufactureA concentration of 2.50-3.00% w/w(30g/kg) of thickener Lamitex HP (to maintain the 60-65 dPa viscosity range) was added to produce stock paste with continuous high speed stirring to the required volume of water. This was followed by the gradual addition of urea 200 g/kg, sodium bicarbonate 30 g/kg, Revatol S 10 gm/kg and sodium hexametaphosphate 5 gm/kg with continuous stirring giving a final stock paste viscosity of 60-65dPa. However, urea is not added in the stock paste manufactured for the experiments conducted using the Econtrol without urea method for fixation. The printing pastes of different concentrations were prepared with Drimarine Red P2B as outlined in Table 1. During stock and print paste preparation a vigorous high speed stirring for 10 min was required to obtain a homogenous paste after adding all reagents. The viscosities of all types of pastes were measured using a Brookfield Viscometer (Type LV). The CR finishing liquor was prepared by using Magnesium Chloride 25% of CR but not greater than 30 g/l, Solusoft MW 20g/l, Ceranine-L 20g/l and Imercol PCLF 1g/l. The final finish bath was prepared with Arkofix NEC as outlined in Table 1.Table 1. Factors and respective levels used in 22.41 mixed factorial design |
| Factor Name | Levels | A | Chroma | 1% | 3% | B | Conc. Of Crease Resistant | 100g/l | 200g/l | C | Fixation Conditions | Saturated Steam102˚C-8min | Hot Air150˚C-5min | EcontrolUrea 0g/kg | EcontrolUrea 50g/kg |
|
|
Print-finish ProcedureThe CPF process was carried out as follows: In the first stage the fabric was immersed in an aqueous solution of CR finish liquor, and then squeezed to obtain a 70% wet pickup. The wet fabric was then dried at 100°C for 1 min. In the second stage the treated fabric was printed by the lab scale Rotary Printing machine (Zimmer). The printed fabric going to be fixed though steaming and curing process was again dried at 100℃ for 1 min. However, the printed fabrics fixed through the Econtrol process was not dried. In the third stage, the print-finish fabric was fixed. The preparation of finish bath, printing recipe and fixation method and temperature were employed in accordance with the experimental design arrangement as stated in Table 1 and 2. The fixed samples were finally washed in 1g/l non-ionic detergent until all unreacted dyes and chemicals were removed from the fabric surface.
3. Evaluation of Fabric Properties
Color yield measurementThe printed fabrics were conditioned (at temperature 25±1 C and relative humidity 65±1%) before color yield measurement with a Tex-Flash spectrophotometer. The condition for measurement was set under specular excluded with large aperture. The fabric was folded twice to ensure opacity. The color yield (k/s value) was calculated for wavelengths 400-700nm at 20nm intervals within the visible spectrum. The k/s was calculated according to Eqn 1: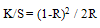 | (1) |
Where, kis the absorption coefficient, s is the scattering coefficient and R is the reflectance of the colored samples. The higher the k/s value is, the greater the color yield and dye uptake.Evaluation of Crease Recovery AngleThe print-finish fabrics were conditioned (at temperature 25±1C and relative humidity 65 ±1%) before the measurement of easy-care properties imparted by the CR finish. The dry crease recovery angle (DCRA) of the fabric was measured using AATCC test method 66-1990, using Shirley Crease recovery tester. The wider the DCRA is, the higher the crease recovery.
4. Experiment Design
22.41mixed factorial design was used to explore the effect of different factors namely: (i) chroma, (ii) concentration of crease resistant, (iii) fixation Conditions on combined reactive printing and crease resistance finishing.A 22.41 mixed factorial design of 16 trials with two repetitions were run according to the design matrix shown in Table 2. The experiments were performed in random order. The results were analyzedusing software Design Expert 7.0. The responses investigated were the colour yield and dry crease recovery angle.The details of the experimental design arrangement are shown in Tables 1 and 2.
5. Results and Discussion
The results from the experiment suggest that all of three factors and two interactions were significant. The significant interactions are chroma and fixation conditions and concentration of crease resistant and fixation conditions. The experimental results, ANOVA for K/S and DCRA are shown in Table 2, 3 and 4 respectively.Table 2. 22.41 mixed factorial design matrix (Run Order) 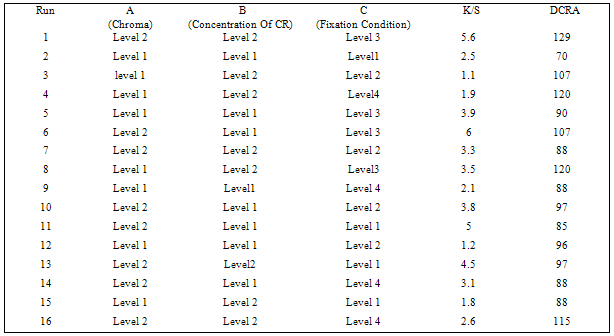 |
| |
|
Table 3. ANOVA for response K/S of screening experiment Set-03 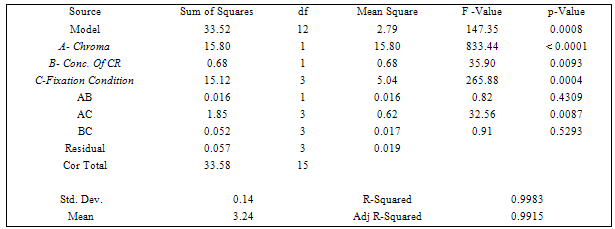 |
| |
|
Table 4. ANOVA for response DCRA of screening experiment Set-03 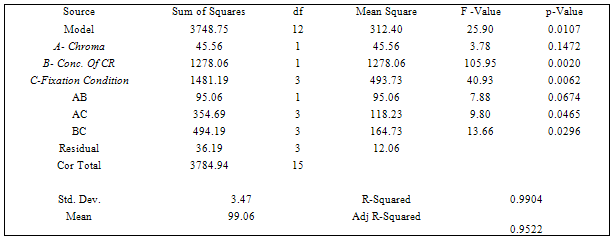 |
| |
|
5.1. Assessment of the Significant Interactions in Combo Process
Influence of Chroma and fixation conditions The interaction of chroma and fixation condition found to be significant for both the responses K/S and DCRA. The interaction plots of Figure 1and Figure 2clearly illustrate that the Econtrol without urea process give highest K/S and DCRA as compared any other fixation method. Increasing the chroma results in a radical increment of K/S (Figure 2) shows that by increasing the concentration of dye, DCRA also increases in the case of Econtrol without urea and steaming process of fixation. This is highly probable when covalent bonding of reactive dye results in entrapping of crease resistant in the fiber system.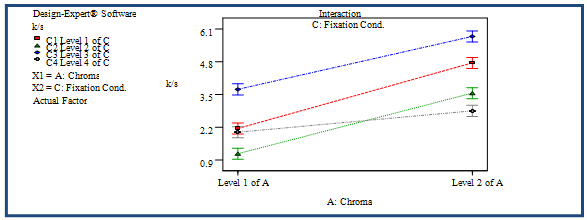 | Figure 1. Interaction plot of chroma and fixation condition with respect to K/S |
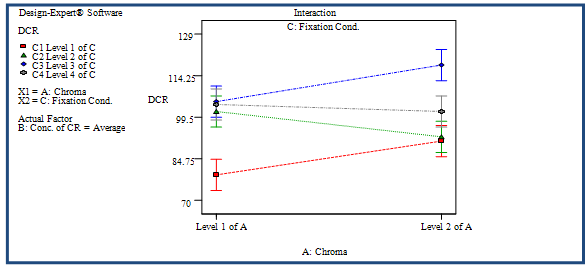 | Figure 2. Interaction plot of chroma and fixation condition with respect to DCRA |
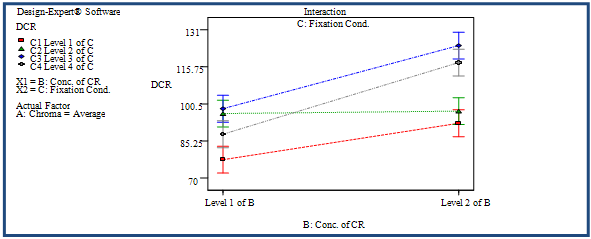 | Figure 3. Interaction plot of concentration of CR and fixation condition with respect to DCRA |
Influence of concentration of CR and fixation conditionsThe interaction of the concentration of CR and fixation conditions was found to be significant for DCRA. As was observed earlier, the Econtrol without urea process yields the best results. Figure 3 illustrates with the increase in concentration of crease resistant, the increment in DCRA is highest in the Econtrol process as compared to other fixation methods.
5.2. Assessment of the Significant Factors
Influence of chromaThe main factor plot of chroma is shownin Figure 4 which reveals that as chroma increases, K/S increases while other factors are kept at average values.Influence of concentration of CR The main factor plots of concentration of CR are shown in Figure 5 and 6. Figure 5 showed that as the concentration of CR increases, K/S decreases keeping other factors at average values. However, Figure 6 illustrates that as the concentration of CR increases, DCRA increases keeping other factors at average values. Influence of fixation condition The main factor plots of fixation conditions are shown in Figure 7 and 8. The plots of fixation condition showed that the final colour yield and DCRA attained the maximum value for the Econtrol without urea process.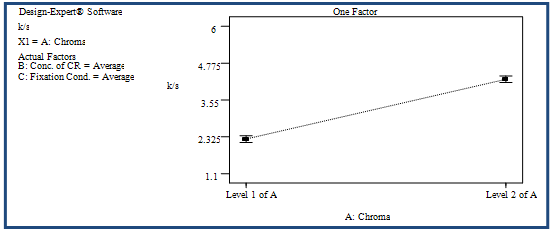 | Figure 4. Effect of chroma on K/S |
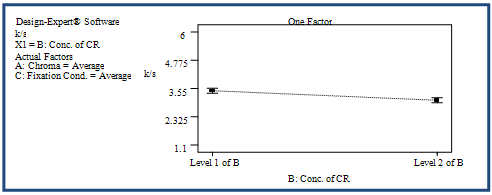 | Figure 5. Effect of concentration of CR on K/S |
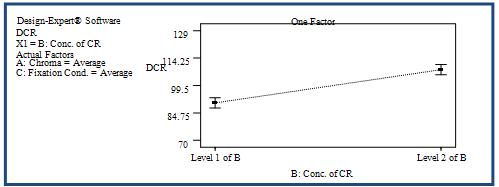 | Figure 6. Effect of concentration of CR on DCRA |
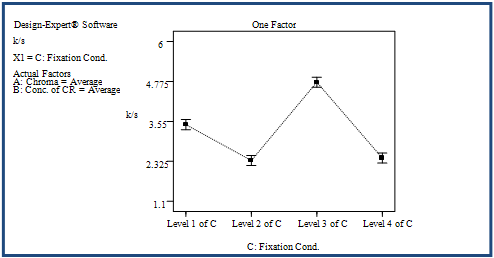 | Figure 7. Effect of fixation conditions on K/S |
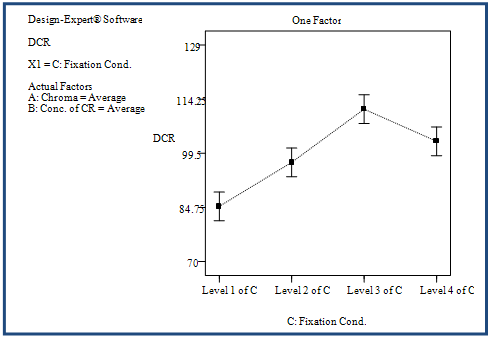 | Figure 8. Effect of fixation conditions on DCRA |
6. Conclusions
The statistical analysis of the influential factors revealed the interaction effect of each factor on the response variables of reactive printing and crease resistance finishing process. For both the responses K/S and DCRA, the Econtrol without urea process yields the most favorable results as compared to any other fixation method for the CPF process.The high values of coefficient of determination as indicated in Table 3 and 4 implied that the models effectively explained the combined process. The interaction graphs forchroma& fixation conditions and concentration of CR & fixation conditionsdemonstrate that the Econtrol method of fixation at 130°C using the pad-dry-print-fix-wash method provides an efficient system for imparting single step fixation of reactive printing and crease resistance finishing.The graphical analyses of factors revealed the significant effect of chroma, concentration of crease resistant, fixation condition on the comnbined process. Based on the experimental design study, it has been further confirmed that each factor had an interaction effect with other factors. Furthermore, the models have been tested for adequacy and found that the assumption of normality and independency are not violated. R2 values were very high, suggesting that models accounted for most of the variability.
ACKNOWLEDGEMENTS
The authors acknowledge the permission given by Clariant Pakistan Ltd, for carrying out the necessary experimental work
References
[1] | Y. H. El Hamaky, S. Tawfeek, D. F. Ibrahim, D. Maamoun, S. Gaber, “Printing Cotton Fabrics with Reactive Dyes of High Reactivity from an Acidic Printing Paste”, Coloration Technology, 123(6), 365-373 (2007) |
[2] | N. S. E. Ahmed, Y. A. Yourself, R. M. El-Shishtawy, A. A. Mousa, “Urea/Alkali Free Printing of Cotton with Reactive Dyes”, Coloration Technology, 122(6), 324-328 (2006) |
[3] | Y. Yang, V. Naarani, “Effect of Steaming Conditions on Colour and Consistency of Ink-Jet Printed Cotton Using Reactive Dyes”, Coloration Technology, 120(3), 127-131 (2004) |
[4] | C. W. M. Yuen, S. K. A. Ku, P. S. R. Choi, C. W. Kan, “Study of the Factors Influencing Colour Yield of an Inkjet-Printed Cotton Fabric”, Coloration Technology, 120(6), 320-325 (2004) |
[5] | V. Vassileva, E. Valcheva, Z. Zheleva, “The Kinetic Model of Reactive |
[6] | D. Heywood, “Easy-Care Finishing of Cellulosics”, Society of Dyers and Colourists 337-338 (2003) |
[7] | Y. Can, M. Akaydin, Y. Turhan, E. Ay, “Effect of Wrinkle Resistance Finish on Cotton Fabric Properties”, Indian Journal of Fibre & Textile Research, 34, 183-186 (2009) |
[8] | S. M. Mortazavi, P. E. Boukany, “Application of Mixtures of Resin Finishing to Achieve some Physical Properties on Interlining Cotton Fabrics: I-Effect of Stiffening and Cross-Linking Agents”, Iranian Polymer Journal, 13(3), 213-218 (2004) |
[9] | N. F. Getchell, N. R.S. Hollies, “Two Component Wet Fixation Process for Imparting Durable Press to Cellulose Containing Materials”, US Patent 3,472,606, November (1965) |
[10] | A. Chakraborty, C. Dutta, “Kinematics of Concurrent Dyeing and Finishing–A Critical Study”, Proceedings of International Conference on Energy and Environment, March (2009) |
[11] | H. M. Choi, M. Srinivasan, N. M. Morris, “Single-Step Dyeing and Finishing Treatment of Cotton with 1, 2, 3, 4-Butanetetracarboxylic Acid”, Journal of Applied Polymer Science, 54(13), 2107-2118 (1994) |
[12] | Y. Dong, J. Wang, P. Liu, “Dyeing and Finishing of Cotton fabric in a Single Bath with Reactive Dyes and Citric Acid”, Coloration Technology, 117(5), 262-265 (2001) |
[13] | B. Herman, B. Arthur, A. Hans, “Process for the Dyeing or Printing and Simultaneous Finishing of Cellulose Materials”, US Patent 3983588, May (1976) |
[14] | M. Montazer, M. G. Afjeh, “Simultaneous X-linking and Antimicrobial Finishing of Cotton Fabric”, Journal of Applied Polymer Science, 103(1), 178-185 (2007) |
[15] | M. M. G. Fouda, A. El Shafei, S. Sharaf, A. Hebeish, “Microwave Curing for Producing Cotton Fabrics with Easy Care and Antibacterial Properties”, Carbohydrate Polymers, 77(3), 651-655 (2009) |
[16] | F. Uddin, Mike Lomas, “Combined Crease Recovery Finishing and Pigment Printing”, Coloration Technology, 121(3), 158-163 (2005) |