Engr. Reashad Bin Kabir, Engr. Nasrin Ferdous
Department of Apparel Manufacturing Management & Technology Shanto-Mariam University of Creative Technology. Uttara, Dhaka-1215, Bangladesh
Correspondence to: Engr. Reashad Bin Kabir, Department of Apparel Manufacturing Management & Technology Shanto-Mariam University of Creative Technology. Uttara, Dhaka-1215, Bangladesh.
Email: |  |
Copyright © 2012 Scientific & Academic Publishing. All Rights Reserved.
Abstract
Kevlar is high modulus para-aramid synthetic fiber. This fiber is one of the heaviest fibers of all time. In this paper there are some discussions about the Kevlar’s properties, function and uses. Although in the past there were some research works had done and papers also been published, but this paper just simplifies the things as well as highlight some superb features of the Kevlar fiber. However this is not a research article rather than a review article.
Keywords:
Inventions, Chemical Structure, Properties, Uses
Cite this paper:
Engr. Reashad Bin Kabir, Engr. Nasrin Ferdous, "Kevlar-The Super Tough Fiber", International Journal of Textile Science, Vol. 1 No. 6, 2012, pp. 78-83. doi: 10.5923/j.textile.20120106.04.
1. Introduction
Kevlar is a manmade fibre, it as an organic fibre in aromatic polyamide family. The unique properties anddistinct chemical composition of wholly aromatic polyamides (aramids) distinguish them from other man-made fibre.Kevlar has a unique combination of high strength, high modulus, toughness and thermal stability. It was developed for demanding industrial and advanced-technology applications. Currently, many types of Kevlar are produced to meet a broad range of end uses.
2. Invention of Kevlar
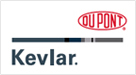 | Figure 1. Registered Kevlar Fibre Logo |
Kevlar® is a manmade fibre developed in 1965 by two research scientists, Stephanie Kwolek and Herbert Blades. The two scientists worked for the DuPont Company. Their product offered a number of benefits that led to its commercial introduction in the early 1970's.While working for DuPont in their Wilmington labs. In anticipation of a gas shortage, in 1964 the DuPont research group led by Kwolek began searching for a new lightweight but strong fibre to use for tyres. One day in 1965, while trying to dissolve one of her polymers, something strange happened. Stephanie Kwolek reported:"Ordinarily a polymer solution sort of reminds you of molasses, although it may not be as thick. And it’s generally transparent. This polymer solution poured almost like water, and it was cloudy. I thought, ‘There’s something different about this. This may be very useful.'"Normally such a "cloudy, opalescent, and low viscosity" solution would just be thrown away. However the technician, Charles Smullen, who ran the "spinneret" persuaded Kwolek to test her solution. When spun into a fibre, they were amazed to find that, unlike the other well-known fibre of the time, nylon, this new fibre did not break. Both her supervisor and laboratory director understood the significance of her discovery and a new field of aramid polymer chemistry were born. It then took six years to produce Kevlar commercially, finally reaching the market in 1971.
3. Chemical Structure
Kevlar is a type of fibre called an aramid, short for 'aromatic polyamide', in which the molecules form long, highly-oriented chains. The fibres can be spun or woven into mats or fabrics to exploit these exceptional properties.Kevlar is made by a condensation reaction of an amine (1, 4-phenylene-diamine) and acid chloride (terephthaloyl chloride).The Kevlar chains are relatively rigid and tend to form mostly planar sheets, similar to those of silk. This is due to the Para-orientation of the benzene rings. When Kevlar is spun the chains lock together via H-bonds to form a sheet that has a very high tensile strength. The sheets also stack radically, like the spokes on a wheel, allowing additional interactions between the face-to-face aromatic groups on neighbouring sheets to help to increase the strength of the overall fibre.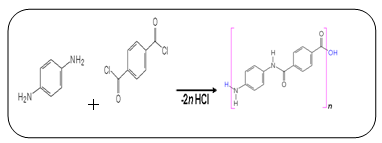 | Figure 2. Terephthaloyl chloride |
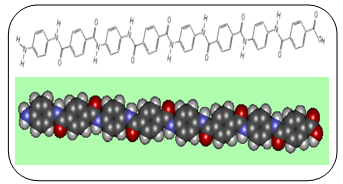 | Figure 3: A section of an individual Kevlar chain |
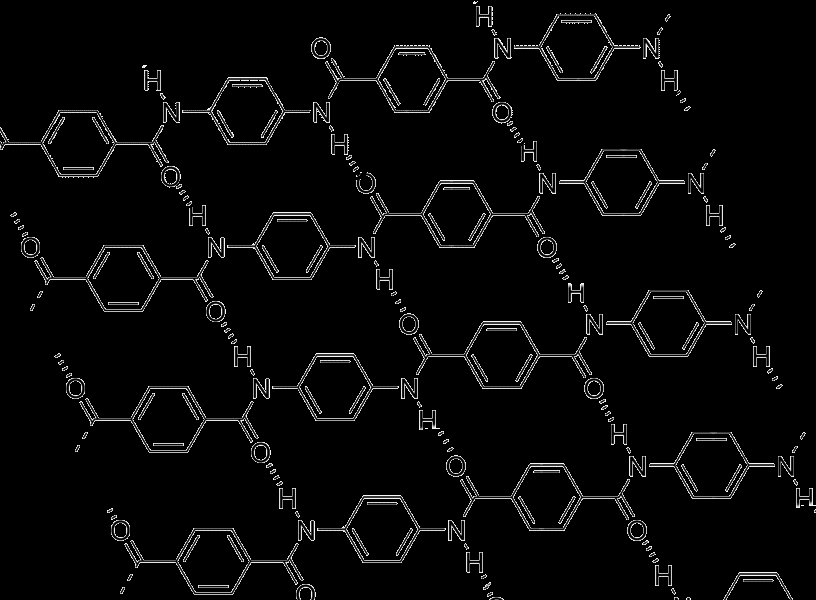 | Figure 4. Molecular structure of Kevlar (bold represents a monomer unit, dashed lines indicate hydrogen bonds.) |
4. Methods of Kevlar Production
Kevlar (poly paraphenylene terephthalamide) production is expensive because of the difficulties arising from using concentrated sulphuric acid, needed to keep the water-insoluble polymer in solution during its synthesis and spinning. 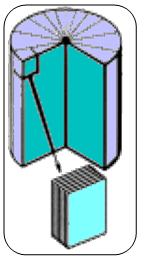 | Figure 5. Sheets Stacked Together |
Several grades of Kevlar are available:[1] Kevlar K-29 – in industrial applications, such as cables, asbestos replacement, brake linings, and body/vehicle armour.[2] Kevlar K49 – high modulus used in cable and rope products.[3] Kevlar K100 – coloured version of Kevlar[4] Kevlar K119 – higher-elongation, flexible and more fatigue resistant.[5] Kevlar K129–higher tenacity for ballistic applications.[6] Kevlar AP – has 15% higher tensile strength than K-29. 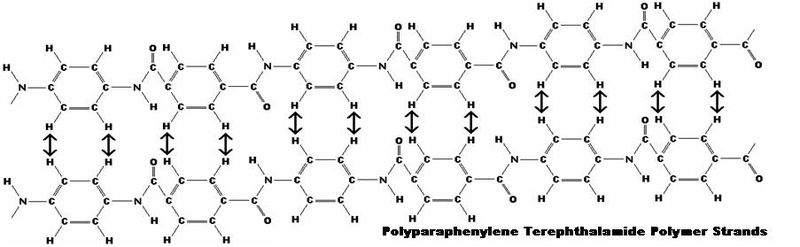 | Figure 6. Kevlar XP – lighter weight resin and KM2 plus fibre combination |
[1] Kevlar KM2 – enhanced ballistic resistance for armour applications.The ultraviolet component of sunlight degrades and decomposes Kevlar, a problem known as UV degradation, and so it is rarely used outdoors without protection against sunlight.
5. Objectives of Kevlar & Properties
Kevlar is a type of aramid that consists of long polymeric chains with a parallel orientation. Kevlar derives its strength from inter-molecular hydrogen bonds and aromatic stacking interactions between aromatic groups in neighbouring strands. These interactions are much stronger than the Van Der Waals interaction found in other synthetic polymers and fibres like Dyneema. The presence of salts and certain other impurities, especially calcium, would interfere with the strand interactions and has to be avoided in the production process. Kevlar consists of relatively rigid molecules, which form a planar sheet-like structure similar to silk protein. These properties result in its high mechanical strength and its remarkable heat resistance. Because it is highly unsaturated, as the ratio of carbon to hydrogen atoms is quite high, it has a low flammability. Kevlar molecules have polar groups accessible for hydrogen bonding. Water that enters the interior of the fibre can take the place of bonding between molecules and reduce the material's strength, while the available groups at the surface lead to good wetting properties. This is important for bonding the fibres to other types of polymer, forming a fibre reinforced plastic. This same property also makes the fibres feel more natural and "sticky" compared to non polar polymers like polyethylene.In structural applications, Kevlar fibres can be bonded to one another or to other materials to form a composite. Kevlar's main weaknesses are that it decomposes under alkaline conditions or when exposed to chlorine. While it can have a great tensile strength, sometimes in excess of 4.0 GPa, like all fibres it tends to buckle in compression.
5.1. Superb Properties of Kevlar
●It is strong but relatively light.●Unlike most plastics it does not melt: it's reasonably good at withstanding temperatures and decomposes only at ~450°C (850°F).●Kevlar can be ignited but burning usually stops when the heat source is removed.●Very low temperatures have no effect on Kevlar. There is no appreciable embrittlement or degradation down to -196°C (-320°F), which makes it excellent for Arctic conditions.●Like other plastics, long exposure to ultraviolet light (in sunlight, for example) causes discoloration and some degradation of the fibres.●Kevlar can resist attacks from many different chemicals, though long exposure to strong acids or bases will degrade it over time.●Kevlar remains virtually unchanged after exposure to hot water for more than 200 days and its properties are virtually unaffected by moisture.
6. Uses & Applications
The worldwide recognition Kevlar® brand fibre has earned as a high-performance material for helping to protect human life extends far beyond the body armour used by the military and law enforcement community. A unique combination of properties makes Kevlar® the first choice for an ever-growing number of applications where a reduction of weight, increase in strength and resistance to corrosion produce significant improvements in safety and efficiency. Today, Kevlar® is used in everything from airplane parts to reinforced suspension bridge structures to suspension bridge cables to fibre optic cables, not to mention a variety of consumer goods. Chances are you either use Kevlar® or come into contact with it on a regular basis.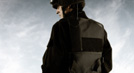 | Figure 7. Jacket by Kevlar in Military Uniform |
6.1. Military Body Armor & Jackets
Americans serving in every branch of the Armed forces since the 1970s have depended upon body armour and flak jackets made with Kevlar® to help protect them from combat hazards, such as ballistic projectiles and explosive fragmentation.Military body armour and flak jackets made with DuPont™ Kevlar® fabric is extremely lightweight and comfortable enough to improve mobility and reduce fatigue for soldiers in the field. Yet Kevlar® fibre is five times stronger than steel on an equal weight basis, offering superior protection against fragmentation and ballistic threats in military body armour and flak jackets. Kevlar® is inherently flame resistant, providing thermal protection from and fire. 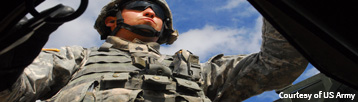 | Figure 8. Kevlar in Protection Vest |
6.2. Protection Vests
Since DuPont first started helping protect officers with protection vests made with Kevlar®, DuPont has been committed to developing new technologies to improve officer safety. From higher-level bullets to knives, needles and explosions, protection vests made with Kevlar® help protect against the ever increasing array of threats officers face
6.3. Military Helmets
Military helmets made with Kevlar® meet demanding requirements for protection against a wide range of threats, including bullets, shrapnel and fragmentation.State-of-the-art military helmets made with Kevlar®, like the U.S. Army Advanced Combat Helmet, absorb 20% more kinetic energy than the Personnel Armour System for Ground Troops (PASGT) military helmets they are replacing, and offer protection from submachine gun bullets.
6.4. Automotive Uses
DuPont™ Kevlar® brand fibre helps improves the safety, performance and durability of automotive components for a wide variety of vehicles, from passenger cars and light trucks to professional race cars. It is not uncommon for a new vehicle to have several crucial parts that employ products made of Kevlar® brand fibre. Kevlar® is available in several different product forms making it useful for a wide range of automotive applications:● Kevlar® fibre is a continuous filament yarn available in a broad range of deniers. It is often woven into fabric and twisted and plied into cords.● Kevlar® stable and flock are short fibre versions suitable for textile applications, and for reinforcement of thermoplastic and thermo set matrices.● Kevlar® pulp is a fibrillated short fibre widely used in friction and sealing applications.● Kevlar® Engineered Elastomer is a concentrate of short fibre materials pre-dispersed in a thermo set or thermoplastic matrix.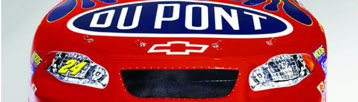 | Figure 9. Kevlar in Automobile Cars |
● Kevlar® also use in following parts● Belts● Brake pads● Clutches● Gaskets● Hoses
6.5. Kevlar as a Composite
Kevlar® is replacing fibre glass-reinforced plastic in NASCAR™ race car bodies and air dams because it doesn't shatter or leave hazardous debris on the track after a crash. In the HANS Device—the life-saving restraining linkage that supports the driver's head and neck— Kevlar® absorbs impact forces that are strong enough to pulverize neck vertebrae.Formula 1 cars use Kevlar® straps to hold onto wheels that break off during crashes, which helps prevent them from bouncing off the track and into the stands.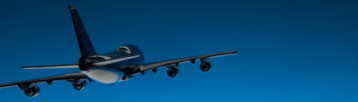 | Figure 10. Kevlar in Aircraft |
6.6. Mass Transportation
The remarkable performance characteristics of DuPont™ Kevlar® helps enable manufacturers to build aircraft, ships and rail cars that are lighter and more durable, resulting in increased fuel efficiency and lower operating and maintenance costs.Kevlar® in Aero Plane:●Aircraft cabin, flooring and interiors●Landing gear doors●Wing boxes and control surfaces●Filament-wound pressure bottles●Engine nacelles●Engine containment rings●Aircraft tires●Rotor blades●Spacecraft●Maritime vessels
6.7. Kevlar® in Fiber Optics
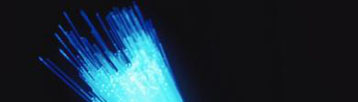 | Figure 11. Fibre Optics by Kevlar |
Kevlar® is used as a strength member in optical fibre cables. The optical fibres in the cable have to be safeguarded against mechanical stresses to ensure their optimal performance. Kevlar®, normally applied in the periphery of the cable, provides the necessary protection. Kevlar® also brings additional functionalities that address the dielectric, light weight, small diameter, flexibility and handling requirements in a fibre optic cable. When used as a central strength member, it is commonly combined with resins to form a Kevlar® Reinforced Plastic (KRP) where properties such as compression, flexibility and low diameter are required.
6.8. Ropes and Cables
For more than two decades, DuPont™ Kevlar® brand fibre has provided a lightweight, flexible and dimensionally stable means of strengthening ropes and cables used across several industries, from mountaineering ropes and fishing lines to electro-mechanical cables and fine gauge cables for electronic device applications such as mobile phone cables, computer power cords, USB cords, and MP3 ear phone cables. Kevlar® delivers performance and value to customers in the fine gauge cable industry by helping to provide better robustness, fatigue resistance, shrinkage and durability.Its resistance to chemicals and temperature extremes make it an ideal component for ropes and cables under severe loads in harsh environments, from the bottom of the ocean to the surface of Mars. Ropes made with Kevlar® brand fibre appear in a variety of constructions, including 4-strand, wire lay, braided and parallel yarns and strand ropes. They range in diameter from 1mm to 250mm, and have been strength-rated up to 1500 tons.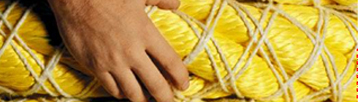 | Figure 12. Different use of ropes & cables in different fields |
6.9. Consumer Applications
The widespread adoption of DuPont™ Kevlar® across multiple industries has inspired consumer goods manufacturers to offer products that feature Kevlar® in their designs. Signature Kevlar® performance benefits such as exceptional strength, cut resistance, and light weight appeal to consumers looking for longer-lasting products that are easier to use, carry and store. The strength-to-weight advantage that Kevlar® has over many other materials means that product designs that use Kevlar® are often not only lighter than their non-Kevlar® equivalents, but less bulky as well. Other Uses like●DuPont™ Storm Room with Kevlar® ●Kevlar® in Sports Equipment ●Kevlar® in Personal electronics
6.10. Other Uses
DuPont™ Kevlar® goes into several items that defy simple categorization, but are nonetheless prevalent in everyday life.1. The Ove Glove™2. Air pack harnesses3. Kevlar® in fire resistant mattresses
7. Conclusions
Kevlar mainly use for two reasons, and both are about performance: It’s lightweight and easy to integrate. A thin blanket can serve as structural reinforcement or ballistic protection, everywhere from seismic shear walls to bank counters. Sprinkle the fibres into carbon composites to cut weight and boost strength: The grades Kevlar 49 and 149 are the lightest and most robust; Kevlar 29 is comparable in potency to glass fibre, but weighs less. The fact is, Kevlar is still expensive costs need to come down.
References
[1] | J W S Hearle (2001), High-performance Fibers. |
[2] | "What is Kevlar". DuPont. Retrieved 2007-03-28. |
[3] | J. K. Fink, Handbook of Engineering and Specialty Thermoplastics: Polyolefin’s and Styrene’s, Scrivener Publishing, 2010, p. 35. |
[4] | "Inventing Modern America: Insight — Stephanie Kwolek:". Lemelson-MIT program. Archived from the original on May 24, 2009. Retrieved May 24, 2009. |
[5] | Kevlar KM2 Technical Description. dupont.com. Retrieved on 2012-05-26. |
[6] | Krishan Kumar Chawla (2005), Fibrous Materials. |
[7] | Frederick T. Wallenberger, Norman E. Weston (2004), Natural fibers, Plastics and Composites. |
[8] | Frederick T. Wallenberger (2002), Advanced Fibers, Plastics, Laminates and Composites. |
[9] | Richard P. Wool, Xiuzhi Susan Sun (2005), Bio-based Polymers and Composites. |
[10] | D. Tanner, J. A. Fitzgerald, B. R. Phillips (1989). "The Kevlar Story – an Advanced Materials Case Study". Angewandte Chemie International Edition in English 28 (5): 649–654. doi:10.1002/anie.198906491 “Aramids.” About.com. 1996. (15 Nov. 2000). |
[11] | Chang, Alen: Hung, Richard; Lew, Katherine, Function and Performance of Kevlar, pdf file,http://www.mse.berkeley.edu/classes/matsci102/Kevlar.pdf. |
[12] | DuPont, Website: “Kevlar” (15 Nov. 2000). |
[13] | "Stephanie Louise Kwolek Biography". Bookrags. Archived from the original on May 24, 2009. Retrieved May 24, 2009. |
[14] | Quinn, Jim. "I was able to be Creative and work as hard as I wanted". American Heritage Publishing. Archived from the original on May 24, 2009. Retrieved May 24, 2009. |
[15] | How Kevlar® works: a simple introduction. Explain that stuff.com (2009-12-07). Retrieved on 2012-05-26. |
[16] | H. H. Yang (1993), Kevlar Aramid Fiber. |
[17] | Michael C. Petty, Molecular electronics: from principles to practice, John Wiley & Sons, 2007, p. 310 . |
[18] | KEVLAR Technical Guide. dupont.com. Retrieved on 2012-05-26. |
[19] | Body Armor Made with Kevlar. (2005-0604). DuPont the Miracles of Science. Retrieved November 4, 2011. |
[20] | Kevlar – DuPont Personal Protection. .dupont.com. Retrieved on 2012-05-26. |
[21] | Audio speaker use. Audioholics.com (2009-07-23). Retrieved on 2012-05-26. |
[22] | Carbon fiber bows for violin, viola, cello and bass. CodaBow. Retrieved on 2012-05-26. |
[23] | Carbon fiber bows for violin, viola, cello and bass. CodaBow. Retrieved on 2012-05-26. |
[24] | M.Rubinstein, R.H.Colby, Polymer Physics, Oxford University Press, p-337. |
[25] | Fabric Produces Electricity As You Wear It. Scientific American (2008-02-22). Retrieved on 2012-05-26. |