M. A. M El-Sayed 1, G. König 2, J. Schaller 3, S. H. Sanad 1
1Cotton Research Institute. Agric. Res. Center, Giza, Egypt
2Trützschler GmbH & Co. KG, Mönchengladbach, Germany
3Oerlikon Schlafhorst Zinser, Germany
Correspondence to: M. A. M El-Sayed , Cotton Research Institute. Agric. Res. Center, Giza, Egypt.
Email: |  |
Copyright © 2012 Scientific & Academic Publishing. All Rights Reserved.
Abstract
The carding process has a major influence on the sliver quality and the resulting yarn characteristics because it is the first sliver forming process step. The effect of opening, carding, drawing and combing on single fiber and bundle cotton properties were studied by employing AFIS and HVI testers. The basic purpose of this study was to determine the carding delivery speed for extra-fine compact yarns by using Egyptian cotton variety Giza 87 as super extra-fine, extra-long fiber quality. Giza 87 Egyptian combed cotton was used to produce extra-fine counts, i.e. Ne 135 and Ne 180 compact yarns, spun on Zinser 351 C3 compact spinning machine.
Keywords:
Egyptian Cotton, Carding Machine, Delivery Speed and Extra-Fine Count
1. Introduction
Since carding is a complicated process – it involves a number of parameters and variables - and embraces different technologies, improving the carding productivity has been made possible by the developments in several sciences and fields, such as machinery, materials science, automation and control. These developments allow several ways for increasing carding productivity.The carding quality is primarily determined in the area of the cylinder. Here, the revolving flat is of particular importance. With an optimal number of flat bars, it is responsible for cleaning as well as extracting neps and short fibers. This job is assigned to the pre-carding area with its cleaning and carding elements. As a rule: The higher the pre-opening, the more intense the carding, which results in increased production. The purpose of high-speed carding is to increase the card productivity without reducing carding quality, or even improve it. It had been thought that increasing carding speed would increase fiber breakage, but there is no evidence why fiber breakage should increase as card speed increases (Atkinson, 1986). It was necessary to increase the production rate of the carding machine because new technologies with considerably higher production levels were started to be implemented.Carding action can be described as the combing of fibers between two surfaces, which carry a set of angled wires (card clothing) oriented in opposing directions, when their relative speed is greater than zero. What individualizes the fibers and gives parallelism to the fiber mass flow is the interaction between the saw-tooth clothing of cylinder, the flats/workers and the fiber mass (Lawrence et al., 2000).According to Deussen (1992), fiber length gains its importance as the most important quality parameter for three reasons: a) Yarn count that can be spun from cotton depends on its fiber length. Other properties being equal, finer yarns can generally be spun from the longer cottons. b) At the same count, yarns spun from longer cottons, other fiber properties being equal, are stronger than those from shorter cottons. c) Fiber length has a direct bearing on yarn strength because the longer the fibers in yarn, the greater the number of points of contact and cohesion between them, and consequently increased yarn strength.Artzt (2000) reported that in the light of today’s knowledge, compact spinning produces yarns which represent a superior ring yarn. It is therefore really a new spinning process, although the yarn looks very much like ring yarn. Spinning without spinning triangle results in uniform fiber integration tension through the yarn cross-section, and consequently in different behavior in downstream processing. In compact spinning, the fibers are compacted into a narrow sliver after a virtually tension-free drafting process within a compacting zone and they are twisted after the nipping point as a compact sliver. As in the classic spinning triangle, peripheral fibers are eliminated.The basic purpose of this study was to determine carding delivery speed on extra-fine compact yarns by using Egyptian cotton variety Giza 87 as super extra-fine, extra-long fiber quality.
2. Materials and Methods
When processing this study jointly by the Spinning Research Department, Cotton Research Institute, Giza-Egypt, Trützschler GmbH & Co. KG, and Oerlikon Schlafhorst, Modern Nile Cotton Company offered two bales of Egyptian cotton variety Giza 87. Fiber samples were collected before and after each processing machine. Fiber samples were tested on Uster AFIS and HVI Spinlab 910, IIC Shirley, and Microdust and Trash Analyzer “MDTA”.Each of the two bales was processed through opening and carding. The cottons were processed through a Universal Bale Opener BO-U, Cleanomat CL-C1 with material-friendly cleaning technology. Single carding was performed on a Trützschler TC 07 card. The production rate used on all the bales was 25 kg/h and 35 kg/h. Waste was collected from all major processing stages, weighed and expressed as a percentage of the total weight fed as shown in Table 1.The effect of opening, carding, drawing and combing on single fiber and bundle cotton properties was studied by employing AFIS (Advanced Fiber Information System) and HVI (High Volume Instrument) testers. The single fiber quality data before and after every stage were compared against yarn properties to study the relationship between fiber quality data and yarn quality data.Each bale sample card sliver was processed through Trützschler drawframe without autoleveling TD 03, lap winder and comber and finally drawframe with autoleveling TD 03. Then the single drawn sliver went through a Zinser 670 BigPack roving frame to Zinser 351 C3 compact spinning frame operating at 13700 rpm spindle speed. For compact spinning, both the 25 kg/h and 35 kg/h roving samples were spun into Ne 135/1 and Ne 180/1 at a constant 4.24 twist multiplier as presented in Table 2.Table 1. Trash content from raw cotton to combing noil 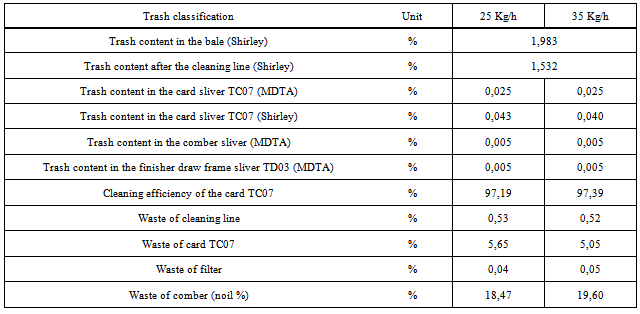 |
| |
|
Table 2. Production/delivery speed and sliver count 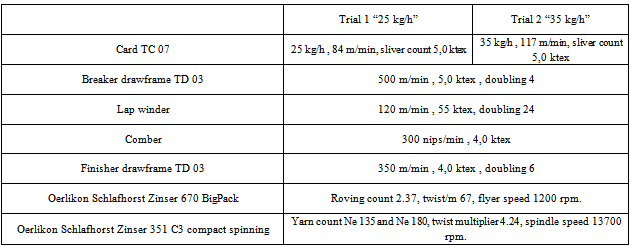 |
| |
|
All fiber and spinning preparation was done at Trützschler Textile Technology Center, Mönchengladbach, Germany. On the other hand, roving and spinning were done at Oerlikon Schlafhorst Zinser laboratories, Stuttgart, Germany.
3. Results and Discussion
The proverbs of the experts “The card is the heart of the spinning mill” and “Well carded is half spun” demonstrate the immense significance of carding for the final result of the spinning operation. The ordinary concept was a strong relationship between increase in production and reduction in quality: the higher the performance, the more sensitive becomes the carding operation and the greater the danger of a negative influence on quality, especially with very fine fibers. Nowadays, carding manufacturers adds a new concept to the carding process, i.e. increasing the production of carding machine without any sacrifice in quality even in extra-fine, extra-long fibers. It was necessary to increase the production rate of the carding machine because new technologies with considerably higher production levels were started to be implemented.Effect of carding machine delivery speed on fiber quality propertiesThe AFIS length/w (Figures 1 and 2) increased slightly after each cleaning stage. In the card sliver and the drawing slivers, the fibers are oriented and paralleled, this removes the crimp. As expected, the fiber length parameters all increase when the cotton is combed, with the exception of the short fiber content, (Simonton et al., 2000).The drawing seems to also have an effect on the upper quartile length, mean fiber length and short fiber content. The only logical explanation is an artifact effect.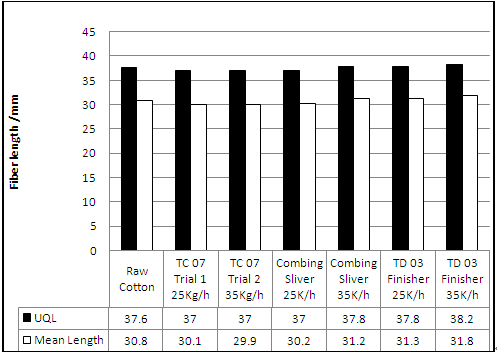 | Figure 1. Evolution of the AFIS-L(w) UQL and Mean Length |
There are slight AFIS variations in the apparent fiber maturity ratio and fiber fineness when going from a processing stage to another. It seems that the AFIS results in a slight increase, which could be due to the removal of dead fibers in the opening line. Consequently, fiber strength increased after each processing stage, The HVI strength (Figure 2) also increases with combing, because of the removal of dead fibers.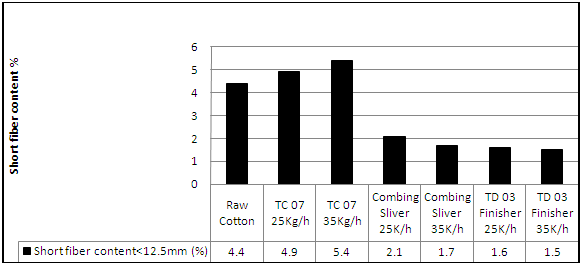 | Figure 2. Evolution of the AFIS-L(w) short fiber content <12.5 mm |
Certainly the card also removes neps and dead fibers; however, the maturity ratio and fiber fineness appears to increase slightly (Figure 3).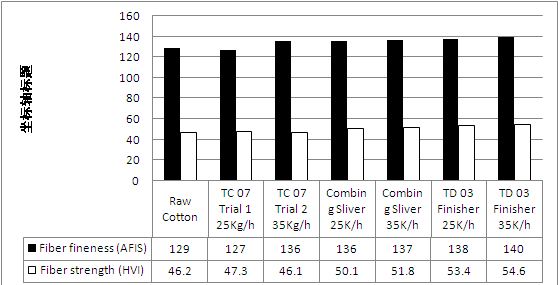 | Figure 3. Evolution of the AFIS fiber fineness and strength HVI |
The AFIS nep counts (Figure 4) decrease with passage of the fibers through the preparation line. Carding decreases the nep count from 194 for raw cotton to 26 and 30 for both delivery carding speeds (84 m/min and 117 m/min). On the other hand, the drawframes have no effect.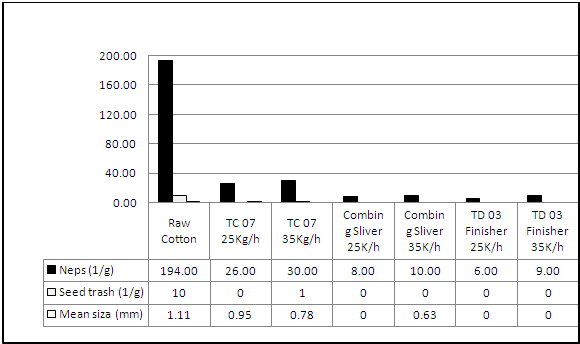 | Figure 4. Evolution of the AFIS Neps, seed trash and mean size |
As expected, the AFIS trash and dust counts (Figure 5) decrease after each processing stage. The card is also extremely effective, removing all of the remaining trash. The cleaning efficiency for dust is very similar to the trash removal efficiency.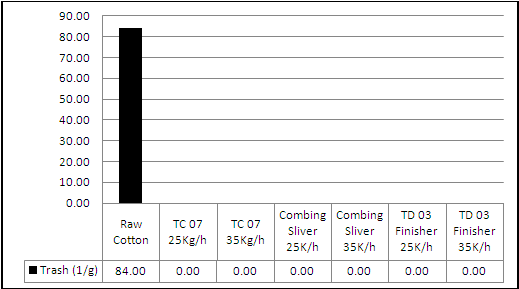 | Figure 5. Evolution of the AFIS Trash |
Table 3. Yarn quality data. 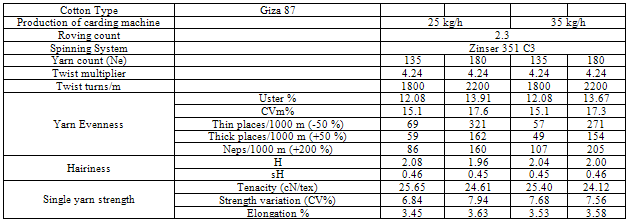 |
| |
|
Yarn quality propertiesProducing super-fine counts with high-quality yarns at high carding speed and with minimum waste levels are the challenges facing both machinery manufacturers and spinners everywhere. For cotton spinners, these goals are even more critical, as they have the potential for significant profitability gains if they can overcome a unique set of challenges, for which Trützschler and Oerlikon Zinser are proposing effective and unique solutions.The effect of card delivery speed on yarn quality was taken into consideration. For this purpose Ne 135/1 and Ne 180/1 compact yarn counts with constant twist multiplier 4.24 were produced by using the slivers produced at 84 m/min and 117 m/min.After analyzing the Uster%, CVm%, imperfections, hairiness and tensile yarn strength values of both yarn counts, it was observed that the yarn quality data were very close with increasing card delivery speed, even in extra-fine count Ne 180. These differences were found statistically insignificant. Table 3 shows the yarn quality data. The reason for this similar result can be attributed to the decreasing short fiber content of slivers produced at both carding speeds. Regarding the fiber quality properties “AFIS and HVI” in relation to yarn quality, fiber length and length uniformity ratio were the primary factors in determining yarn uniformity and defect level. Short fibers are usually used as an evidence of fiber breakage and negatively affect yarn uniformity. An increasing number of short fibers will cause a great amount of floating fibers in the drafting zone and the yarn evenness will be impaired. Fiber fineness determines the number of fibers per yarn cross-section at a given yarn count. Finer fibers, those with lower linear density in mtex, increase the number of fibers in any bundle of specified mass. Yarn strength tends to increase as more fibers become active in sharing the load when tensile forces are applied to the yarn. The number of fibers per yarn cross-section has a considerable impact on yarn uniformity.The compact spinning technology is yielding a real advance in yarn quality. The advance consists primarily in greater utilization of the fiber substance and reduced yarn hairiness.
4. Conclusions
Trützschler carding machine TC 07 adds a new concept to the carding process, i.e. increasing the production of carding machine without any sacrifice in quality even in extra-fine, extra-long fibers. The AFIS length/w increased slightly after each cleaning stage. In the card sliver and the drawing slivers, the fibers are oriented and paralleled, this removes the crimp. As expected, the fiber length parameters all increase when the cotton is combed, with the exception of the short fiber content. After analyzing the Uster%, CVm%, imperfections, hairiness and tensile yarn strength values of both yarn counts, it was observed that the yarn quality data were very close with increasing card delivery speed, even in extra-fine count Ne 180.
References
[1] | Artzt, P. 2000. The special structure of compact yarns - advantages in downstream processing. Proceedings of the Beltwide Cotton Conference. Volume 1:798-803 (2000). National Cotton Council, Memphis TN |
[2] | Deussen, H. 1992. Improved cotton fiber properties - the textile industry’s key to success in global competition. “Cotton Fiber Cellulose: Structure, Function and Utilization” Conference. Savannah, Georgia. October 29, 1992 |
[3] | Lawrence C.A., A. Dehghani, M. Mahmoudi, B., Greenwood, C., Iype, “Fiber Dynamics in the Revolving-Flats Card, Part 1, A Critical Review”, AUTEX Research Journal, Vol. 1, No. 2, 64-77,( November 2000) |
[4] | Atkinson, K.R., Harrowfield, B.V., Plate, D.E.A., Robinson, G.A., “Increasing Card Productivity”, “Wool Scouring And Worsted Carding: New Approaches”, CSIRO Division Of Textile Industry Symposium, (November 1986) |
[5] | Simonton. J.L., W.D. Cole and P. Williams. 2000. Effect of cotton preparation on AFIS and HVI measurements. Proceedings of the Beltwide Cotton Conference Volume 1:726-731 (2000). National Cotton Council, Memphis TN |