Uday Kumar V., Mastan Shareef. R. Md., Abbaiah. R.
Department of Statistics, Sri Venkateswara University, Tirupathi, 517502 (A.P.), India
Correspondence to: Uday Kumar V., Department of Statistics, Sri Venkateswara University, Tirupathi, 517502 (A.P.), India.
Email: |  |
Copyright © 2012 Scientific & Academic Publishing. All Rights Reserved.
Abstract
In this paper a study of theoretical applications in real life situations in an industry have been attempted. On the analysis, it is observed that Preventive maintenance is always better.
Keywords:
Reliability, Preventive Maintenance, Quality Control, Failure Rate, Survival Rate, Mean Time between Failures
Cite this paper: Uday Kumar V., Mastan Shareef. R. Md., Abbaiah. R., Some Practical Aspects of Reliability in an Industry, International Journal of Statistics and Applications, Vol. 4 No. 1, 2014, pp. 1-17. doi: 10.5923/j.statistics.20140401.01.
1. Introduction
The growth and development of ‘reliability’ is closely associated with quality control problems which were vividly discussed in statistical quality control. The importance of reliability and quality control was originated from the demands of modern technology used in world war-II. Complexity and automation of equipment used in the war resulted in several problems of maintenance and repair[1].Failures in the sophisticated equipments forced to analyse the failure data. Hence the qualitative techniques were introduced for reliability measurement.Several committees and organisations such as Vacuum Tube Development Committee of USA in 1948, Bell Laboratories and Aeronautical Radio, INC, Advisory group on reliability of electronic Equipment AGREE in 1957. National council for quality and reliability 1961 etc., were formed to promote the concepts of reliability and quality among both manufactures and users. The application of this subject achieved a remarkable progress in the application of reliability principles in industries and government departments in almost all developed and developing countries during the last three decades. Today reliability has become a catch-word in day-to-day life[2].Reliability is a study of the survival life of a product or a process through probability approach. For improving the quality of any product the machinery should be under good condition where the production should not be stopped an uninterrupted[without failure of the machine] as well as the sub components associated with that machine should be also should survive. So the failure probability of the machine tools an importance place in order to product the qualitative product.
1.1. Mean Time between Failures [MTBF]
Average time of between failures is called mean time between failures starting the failure occurs at time t=0, later first failure occurs at time t1 and next failure occurs at time t2 and so on. Here t1, t2, t3, ….., are between failures times and it is applicable for repairable items. Here in the situations like the large machinery is dealing with the production of the pistons may have the failures some time to avoid the failures of the machinery we have calculated the data of the breakdown frequency of the machinery.While in the each line we have collected the data of failures [breakdowns] of the machinery.
1.2. Preventive Maintenance
A system which has life and eventual failure can be achieved to attain longer average life or higher reliability by attending to its service mechanism at equal intervals of time in such a way that by the end of every service the product is brought back to as good as a new one. This procedure is called as preventive maintenance.In preventive maintenance, parts are replaced lubricants changed or adjustments made before failure occurs. The objective is to increase the reliability of the system over the long terms by staying off the aging effects of wear, fatigue and related phenomena. Failure is postponed or prevented by using maintenance[3].
2. Break Down Analysis
To calculate the mean time between failures for the optimum preventive maintenance,There are two types of break downs data[4].1. Mechanical.2. Electrical.We have taken the mechanical data for one year in 2011 from the industry. There are 7 types of machines.
We have seven lines in machine shops each line consists of one OEB, ROD, SFB, CGR, OHD, RGR, and FOD. We consider all lines machine break downs frequency, cumulative frequency and also averages. Fit the trend line for each machine among 8 lines we consider serial number on x-axis and frequency Y- axis.If the trend line is increasing, the failure of the machine break downs is good. Break downs of machines are high, if the trend line is decreasing or fall down. Now calculate the average of the machine among seven lines that is nothing but the mean time between failures [MTBT].Average time of between failures is called MTBT. Starting the failure occurs at time t=0, later first failure occurs at time t1 and next failure occurs at time t2 and so on. Here t1, t2, t3… are between failures times and it is applicable for repairable itemsTable 1. OEB L1 MACHINE-MTBF 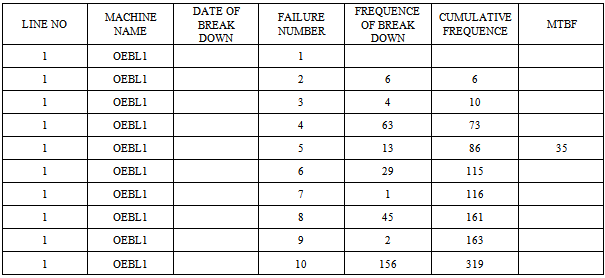 |
| |
|
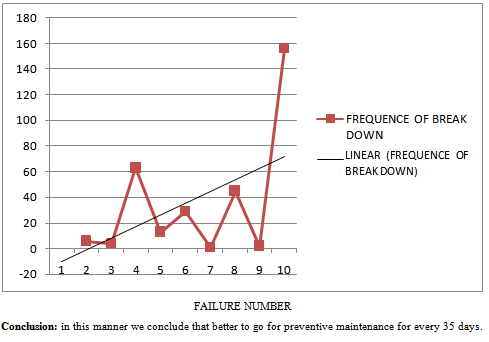 | Figure 1. Frequency of Break-Down of OLE L1, Machine |
Table 2. OEB L2 MACHINE-MTBF 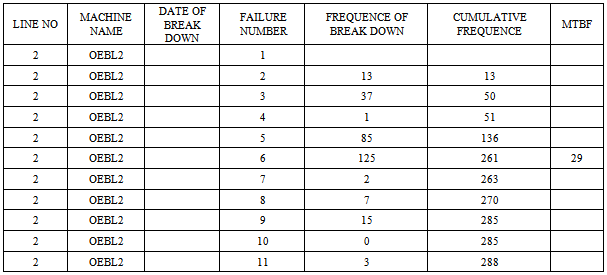 |
| |
|
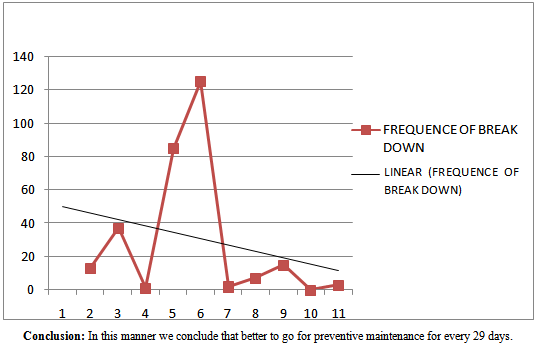 | Figure 2. Frequency of Break-Down of OEB L2 Machine |
Table 3. OEB L3 MACHINE-MTBF 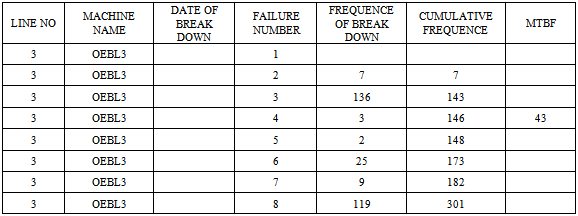 |
| |
|
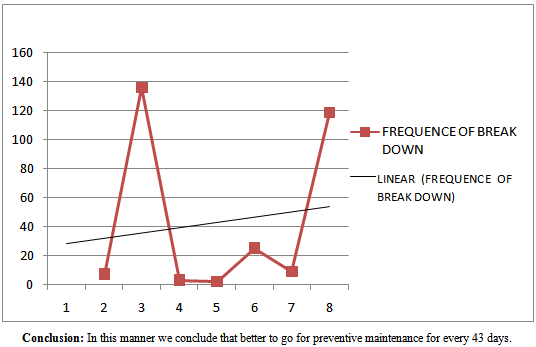 | Figure 3. Frequency of Break-Down of OEB L3 Machine |
Table 4. OEB L4 MACHINE- MTBF 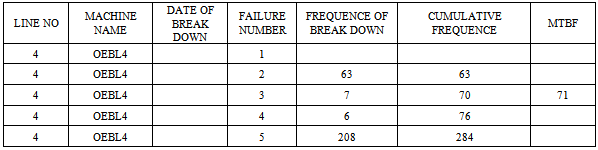 |
| |
|
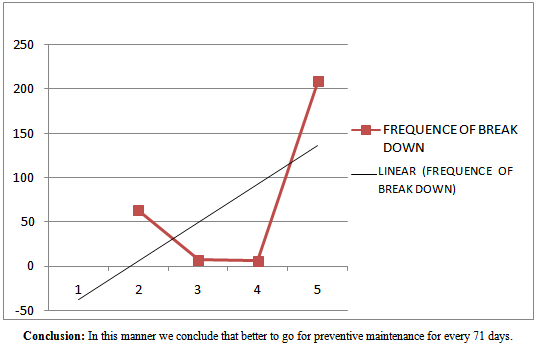 | Figure 4. Frequency of Break-Down of OEB L4 Machine |
Table 5. OEB L5 MACHINE-MTBF 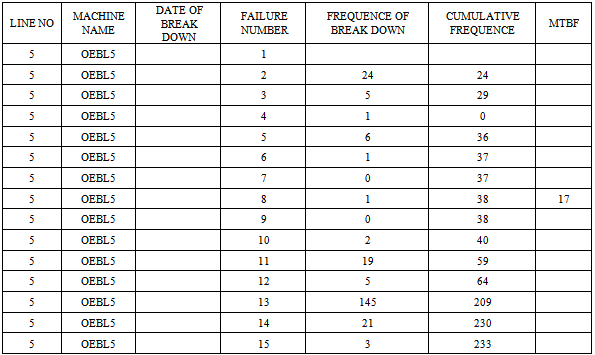 |
| |
|
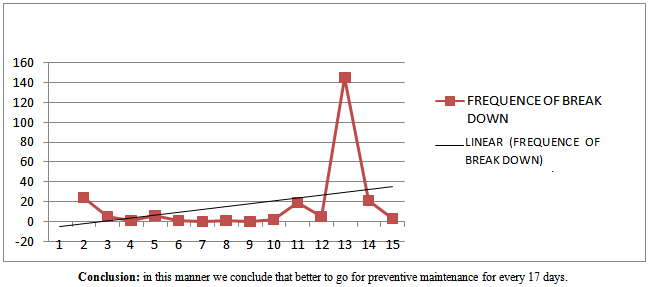 | Figure 5. Frequency of Break-Down of OEB L5 Machine |
Table 6. OEB-L6 MACHINE-MTBF 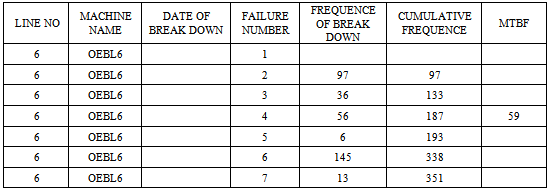 |
| |
|
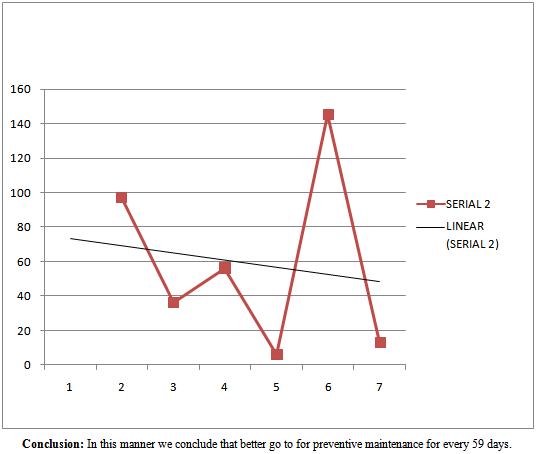 | Figure 6. Frequency of Break-Down of OEB L6 Machine |
Table 7. OEB L7 MACHINE-MTBF 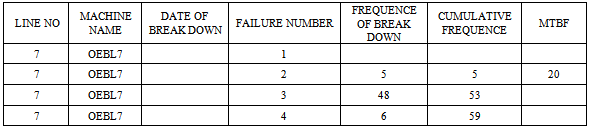 |
| |
|
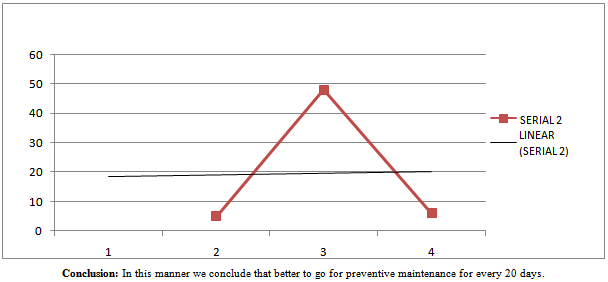 | Figure 7. Frequency of Break-Down of OEB L7 Machine |
Table 8. ROD L2 MACHINE-MTBF 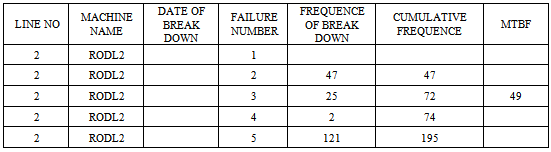 |
| |
|
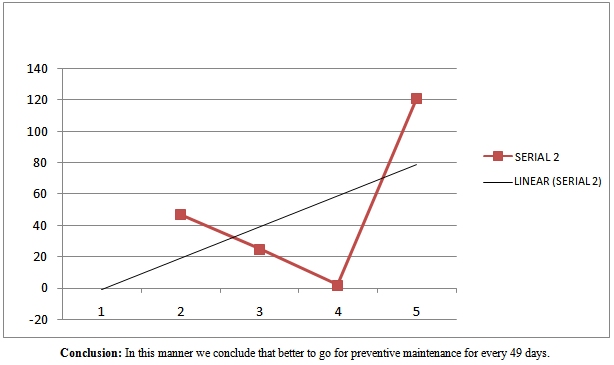 | Figure 8. Frequency of Break-Down of ROD L2 Machine |
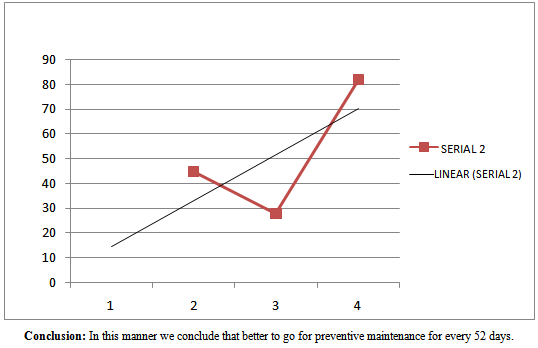 | Figure 9. Frequency of Break-Down of ROD L7 Machine |
Table 9. OD L7 MACHINE-MTBF 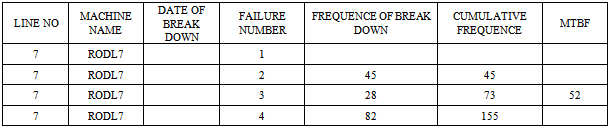 |
| |
|
Table 10. ROD L8 MACHINE-MTBF 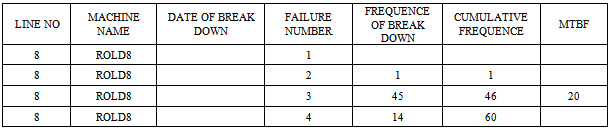 |
| |
|
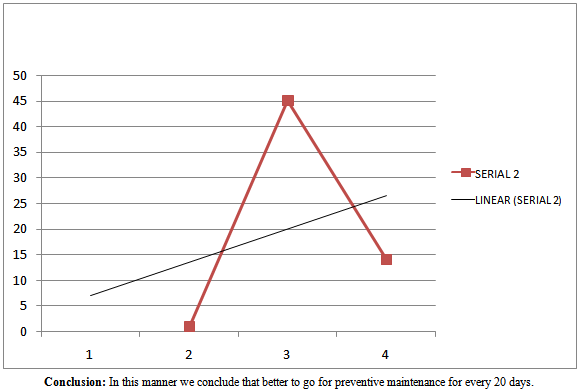 | Figure 10. Frequency of Break-Down of ROD L8 Machine |
Table 11. SFB L1 MACHINE-MTBF 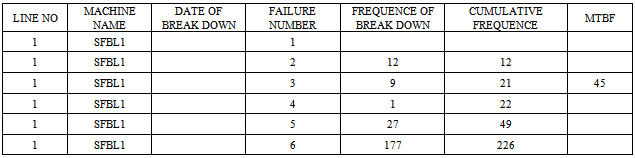 |
| |
|
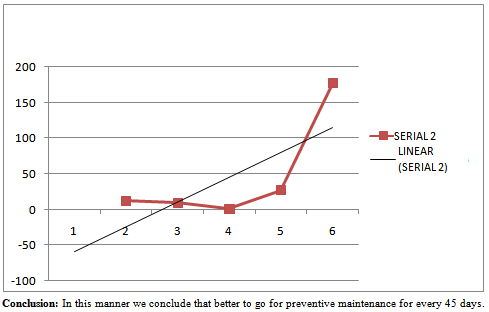 | Figure 11. Frequency of Break-Down of SFB L1 Machine |
Table 12. SFB L4 MACHINE-MTBF 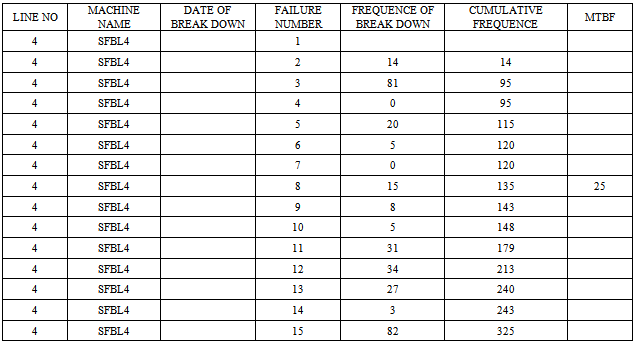 |
| |
|
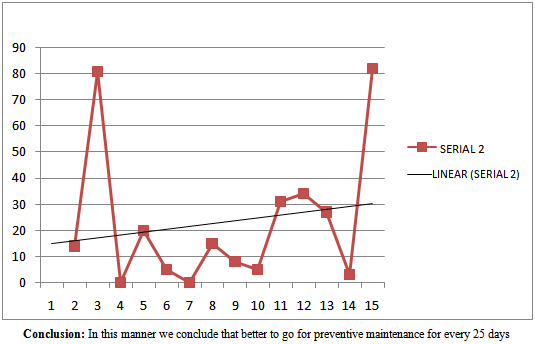 | Figure 12. Frequency of Break-Down of SFB L4 Machine |
Table 13. CGR L1 MACHINE-MTBF  |
| |
|
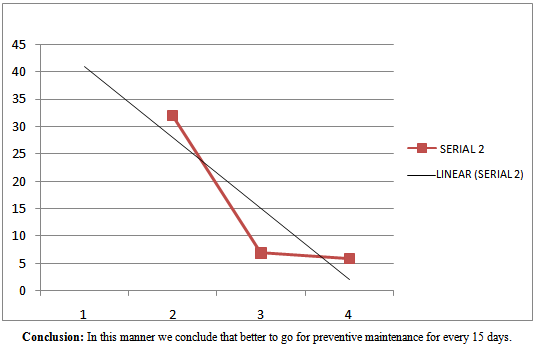 | Figure 13. Frequency of Break-Down of CGR L1 Machine |
Table 14. CGR L4 MACHINE-MTBF 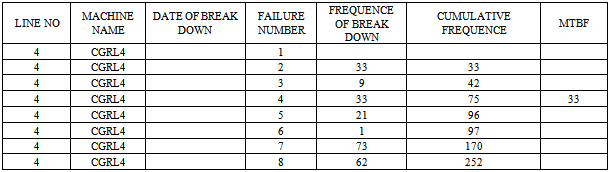 |
| |
|
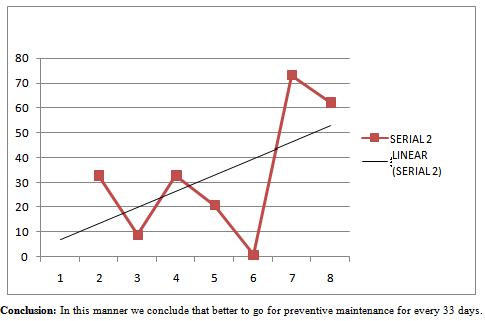 | Figure 14. Frequency of Break-Down of CGR L4 Machine |
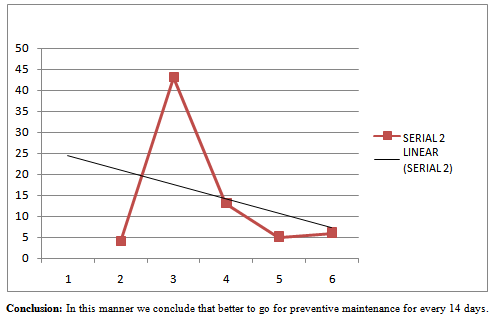 | Figure 15. Frequency of Break-Down of CGR L6 Machine |
Table 15. CGR L6 MACHINE-MTBF 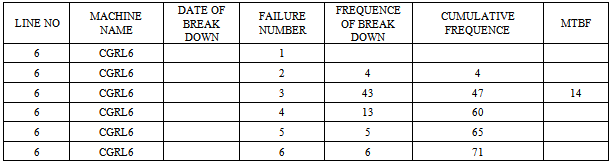 |
| |
|
Table 16. OHD L1 MACHINE-MTBF 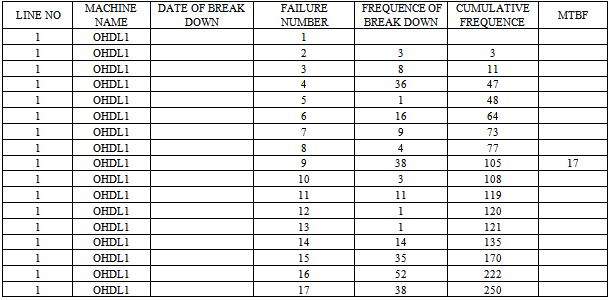 |
| |
|
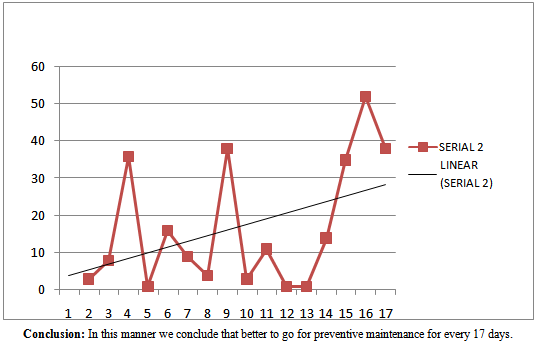 | Figure 16. Frequency of Break-Down of OHD L1 Machine |
Table 17. OHD L7 MACHINE-MTBF 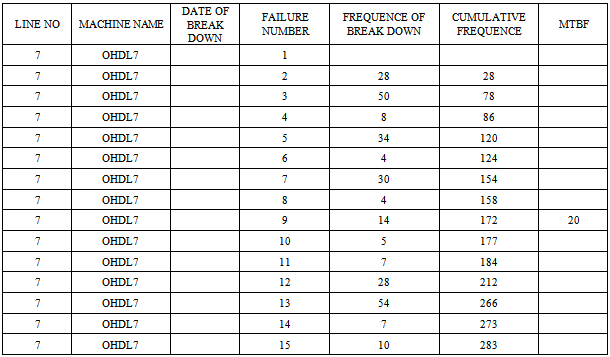 |
| |
|
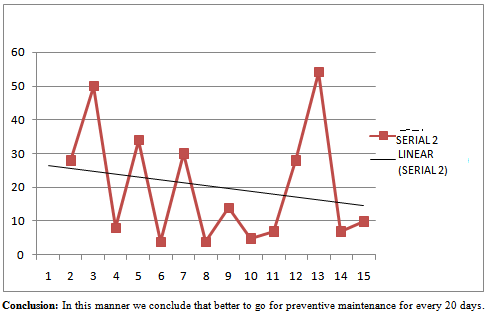 | Figure 17. Frequency of Break-Down of OHD L7 Machine |
Table 18. OHD L8 MACHINE-MTBF 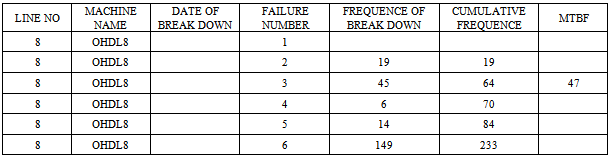 |
| |
|
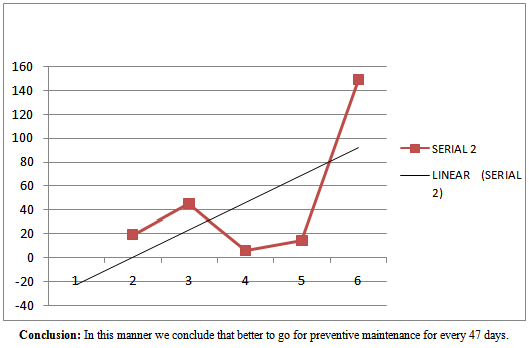 | Figure 18. Frequency of Break-Down of OHD L8 Machine |
Table 19. R.GR L2 MACHINE-MTBF 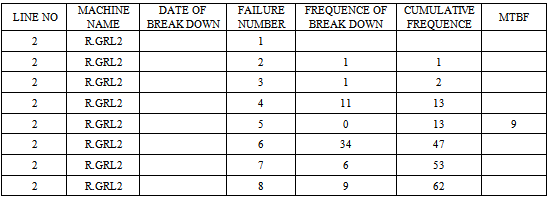 |
| |
|
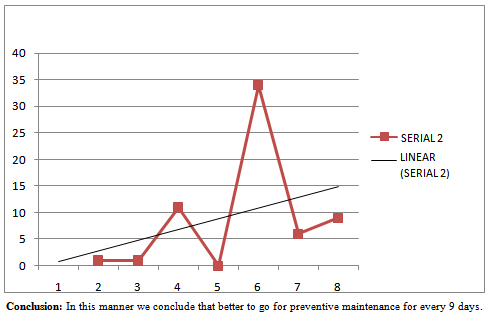 | Figure 19. Frequency of Break-Down of R.GR L2 Machine |
Table 20. R.GR L6 MACHINE-MTBF  |
| |
|
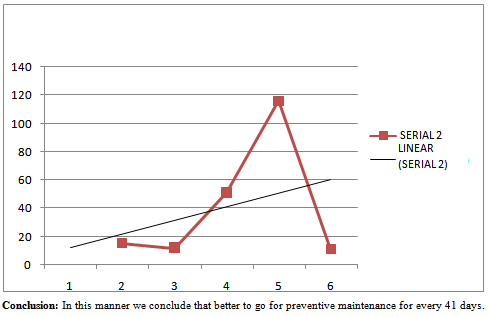 | Figure 20. Frequency of Break-Down of R.GR L6 Machine |
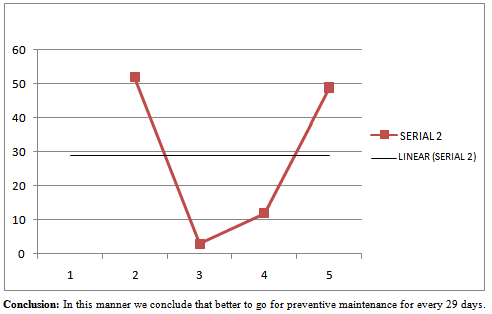 | Figure 21. Frequency of Break-Down of FOD L3 Machine |
Table 21. FOD L3 MACHINE-MTBF 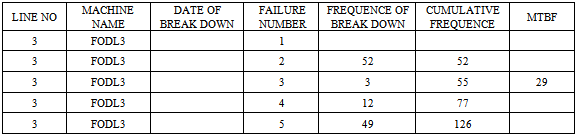 |
| |
|
Table 22. FOD L5 MACHINE-MTBF 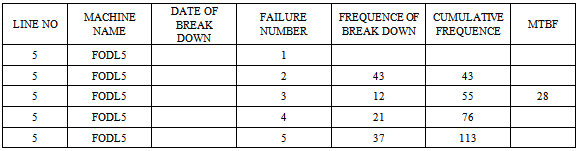 |
| |
|
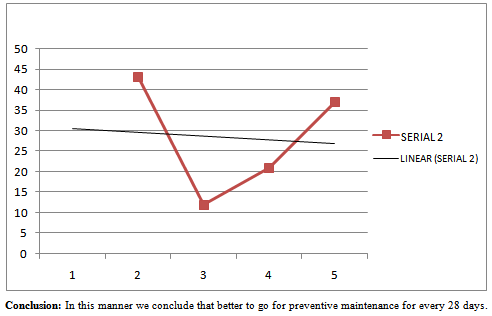 | Figure 22. Frequency of Break-Down of FOD L5 Machine |
Table 23. FOD L6 MACHINE-MTBF 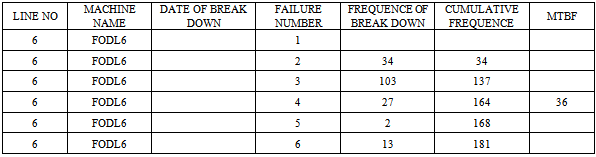 |
| |
|
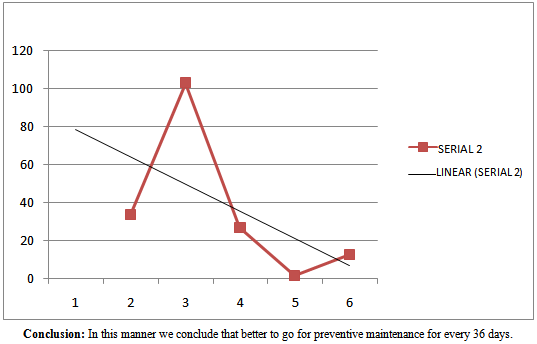 | Figure 23. Frequency of Break-Down of FOD L6 Machine |
3. Conclusions
From the above data and analysis it is concluded that the preventive maintenance is always essential for better machine functioning. Various conclusions drawn for each tools are given at the end of each table and graph. It is always better to prevent the eventuality rather than repair it.
ACKNOWLEDGEMENTS
We sincerely thank the Management of the firm (on their request we are not mentioning the name of the firm) who allowed us to do this academic work.
References
[1] | Duncun, A.J. (2008): Qualit Y Control And Industrial Statistics, Richard D., Irwin, Inc., Home wood Illinois |
[2] | A.I. Khuri., J.A. Cornell. (1996): Response Surfaces Design And Analysis, Second Edition, Revised and Expanded, Marcel Dekker, INC., |
[3] | Montgomery, D.C. (2001): Introduction To Statistical Quality Control, Third Edition, John Wiley & Sons, Inc. |
[4] | Amitava Mitra, (2001): Fundamentals Of Quality And Improvement, Second Edition, Pearson Education Asia. |