Diego Amorim Caetano de Souza, Sérgio Luiz Moni Ribeiro Filho, André Luís Cerávolo de Carvalho, Neimar Soares Silva, Samuel Marques Barcelos, André Luis Christoforo
Department of Mechanical Engineering, Federal University of São João del-Rei, São João del-Rei, 36307-352, Brazil
Correspondence to: André Luis Christoforo, Department of Mechanical Engineering, Federal University of São João del-Rei, São João del-Rei, 36307-352, Brazil.
Email: |  |
Copyright © 2012 Scientific & Academic Publishing. All Rights Reserved.
Abstract
The study of the structural components of an aircraft such as landing gear, wheel and triquilha are elements that undergo constant changes, depending on the project requirement and efforts. Among these mechanisms stands the wheel, because it is the element that makes the connection between aircraft and ground. Designed to withstand small displacements and strains without losing its characteristics, is an element in which studies with software using the Finite Element Method are present and important to better design component. The development of an Aeronautical Design, since its inception, detailed design and construction is a major challenge to the designer by the intense complexity of aerodynamic factors and dimensional parameters, integrated to a large multidisciplinary. The present study aimed to use topological optimization processes present in Ansys ® software coupled with genetic algorithms and statistical methods, software ModeFrontier®, analyze and get an optimal form for the wheels used in aircraft cargo to Aerodesign SAE competitions. Bound methods allowed a reduction of 40% compared to previous projects and found that the structural parameter Lane Width is that present the most influence on the mechanical performance of the aircraft.
Keywords:
Topological Optimization, Finite Element Method, Genetic Algorithms, Aerodesign
Cite this paper: Diego Amorim Caetano de Souza, Sérgio Luiz Moni Ribeiro Filho, André Luís Cerávolo de Carvalho, Neimar Soares Silva, Samuel Marques Barcelos, André Luis Christoforo, Topological Optimization and Genetic Algorithms Used in a Wheel Project for a Drone, International Journal of Statistics and Applications, Vol. 3 No. 5, 2013, pp. 155-161. doi: 10.5923/j.statistics.20130305.02.
1. Introduction
The competitiveness between teams stimulates the study of light materials with satisfactory mechanical properties to the development of aircrafts with lower bulk and higher charging capacity. The quest for development of lighter and more efficient products was always an obsession to the engineering. Some decades ago, the development process of products was based on the attempt and mistake, and on the draftsman experience[1]. This way, the use of numeric simulation softwares becomes a tool to obtaining displacement and tension results without the immediate necessity of a prototype to future analysis and corrections, reducing the time and the expenses.On the aircraft project, the multidisciplinary optimization (MDO) gained momentum in the last decade, the use of optimization methods to solve project problems incorporating various subjects – aerodynamic, structural analysis, propulsion, economical engineering and control theory.Among these, optimization methods is highlighted the genetic algorithms coupled to statistical tools, that aim to minimize the takeoff weight and maximize the bulk of charge. Giunta[2], for instance, employed the classic statistical methods and the bayesian inference coupled to the approach of Kriging to define a polynomial model approached, and through these classic convex optimization methods, minimize the takeoff weight of a supersonic aircraft.Obayashi[3] applied a multiobjective genetic algorithm to the drawing of a plan shaped wing, aiming to minimize the dragging and maximize the available bulk to fuel storage. The same period was marked by the development of unmanned aircrafts (VANT), with both military and civil finalities. It is natural, therefore, that has been applied the MDO to his projects, as attest the research’s developed by Batill et al.[4]; Gundlach[5]; Neufeld and Chung[6] and Lee et al.[7].
2. Literature Review
2.1. Finite Element Method
The Finite Elements Method (FEM) shows itself as an excellent tool for calculation used to analyze the behavior of the materials used in structural projects, such as the one of evaluating the mechanical performance of these structures.Historically, the MFE emerged in 1955, as an evolution of the matrix analysis of bar models, motivated by the computer advent and elaborated with the aim of design structures of continuous models.The FEM can be considered as a technique to generate approach functions that can be used to interpolate displacements, efforts, tensions and deformations along the element’s domain.To the approximate resolution of structural problems according FEM, the form functions can be directly applied to its differential equation (Weighted Residuals) or to energetic principles, such as the Virtual Works Principle (VWP).The displacement in structural elastic problems is taken as a fundamental unknown , obtained by the resolution of a equations system, such as expresses the Equation1, taken that its construction stays in function of the provision mesh, and consequently, of the nodes from the finite elements on the structure, as can be observed on Figure 1.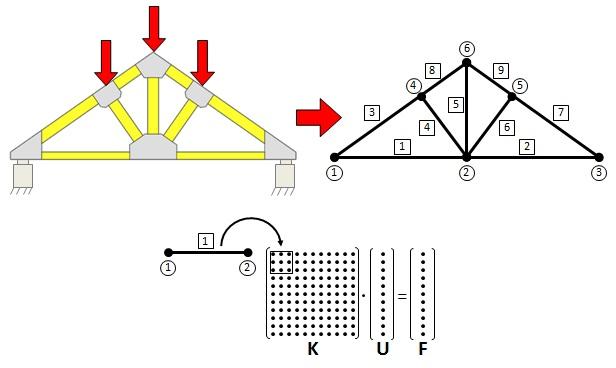 | Figure 1. Example of the discretization of a finite elements mesh in a truss |
 | (1) |
In which:[K] – stiffness matrix of the structure; {U} - vector of nodal displacements of the structure;{F} - equivalent nodal force vector of structure.
2.2. Topological Optimization
Topological optimization consists in a computational method that allows to determinate, by interactive means, the optimal geometry of structural components according to a certain cost criterion, among them it is highlighted the maximum stiffness and lower bulk.The topological optimization method distributes the material in the interior of a fixed domain, in other words, the predetermined geometry in order to maximize or minimize a cost function, in the case, the maximum stiffness and the lower bulk of material, consequently resulting in lower bulk.The material in each domain point can vary from 0, where there is no material, until 1, where there is total presence of material, take intermediate densities according to a defined material model[8].An optimization algorithm is used to find in an interactive way the optimal distribution of material. On the acceleration process, the optimization methods use the information of the derivative from the cost function related to the material quantity in each element. The distribution of material is represented, for instance, associating a density value to each element obtained from the discretization of the initial domain[8].This way, topological optimization essentially combines optimization methods with a numerical method of analysis, for instance, the Finite Element Method (FEM). Another numerical methods of analysis can be used, however, must be generic enough due to dealing with structures with complex shapes that result from the optimization.
2.3. Optimization via Genetic Algorithms
Genetic algorithms are constituted of computational models developed through the natural selection principles which were developed by the naturalist Darwin (1859), in which beings that have characteristics that allow larger adaptability and compatibility with the environment they live, have its surviving and reproducing probability increased, allowing a bigger spreading of their genes to their descendants.In this method, a random population is initially generated and from this population are selected the best individuals, that are combined between themselves and creating the next generation. To this, are used mutation techniques, selection and cross-over, to ensure the population variety of the later groups. The individuals that have superior characteristics increase the capacity of influencing the genetic variety of future descendants[9].A characteristic of this methodology is that all the population tends to evolve converging to groups that are even more improved and next to a common optimum[10], showing itself very effective and robust in applications with increased number of input variables, in which the environment and the analysis conditions are very complex to traditional optimization methods.To this research, is understood optimization as a research for an individual that after successive generations keep itself in the restrictions imposed by the project’s limits and that be the most able related to the defined objectives compared to the rest of the population.
3. Material and Methods
T Was used a 2D simplified model to the application of the topological activity, selecting the reduction of 50% of the pieces bulk, maximum of 100 iterations and precision of 1.10-5. The wheel was outlined with external diameter of 85mm with central hole of 10mm. It should be emphasized that this last dimension refers to the diameter of the external runway of the rolling to be used.As the rolling selection is intrinsically related to the estimated loads to the critical cases, and these values are subject to changes due to the various iterations of the aeronautical design, it is noteworthy the simplified character of this stage. Was objectified to find with the topological optimization of possible favorable geometries related to the bulk reduction, being one of the optimization’s characteristics, obtain the best distribution of material to the domain[11].As contour condition was adopted the restriction of the freedom degrees of the nodes localized in the central hole and was applied a distributed pressure along the external runway of the wheel. The use of this resource serves to simplify the model to be used, avoiding the necessity of programming various load cases to the impact in each point.The material used was Aluminum 7075-T651 with mechanical properties by the manufacturer AlumiCopper® (Table 1).Table 1. Aluminum 7075-T651 mechanical properties |
| Density (g/cm3) | MOE (MPa) | Rigidity Modulus (MPa) | Fusion Temperature (oC) | 2,80 | 73000 | 27500 | 475-630 |
|
|
Through the topologic optimization is gotten an initial geometry idea, but it is still necessary the use of parametric process to determine the best dimensions that allow the adequacy of the wheel to the requests and restrictions of the project. To this was used the software Ansys Workbench® to do the structural simulations relative to the efforts, calculate the tensions and deformations, and calculate the bulk, output variables to the optimization phase.The charges employed correspond to the critical landing situation in a wheel on the landing angle multiplied by the factor of the active charges. This corresponds to a vertical charge of 342,35 N and horizontal charge of 85,59 N to the present situation. The application point of the charges is the point situated between two radius, considering as being the most critical, as during the simulations. Corrections related to the initial geometry of the topological stage were done, as the relief in the central part of the radium.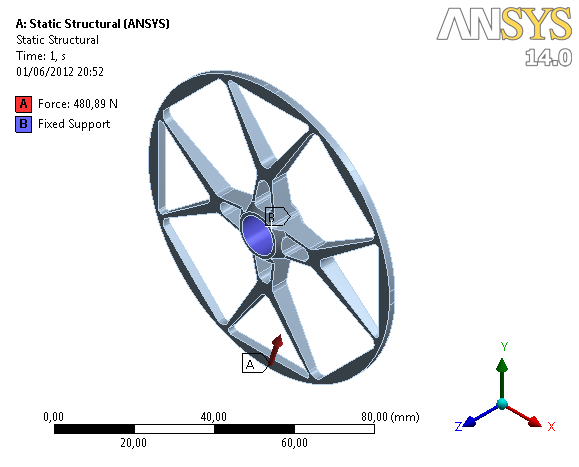 | Figure 2. Charges and restrictions on the wheel |
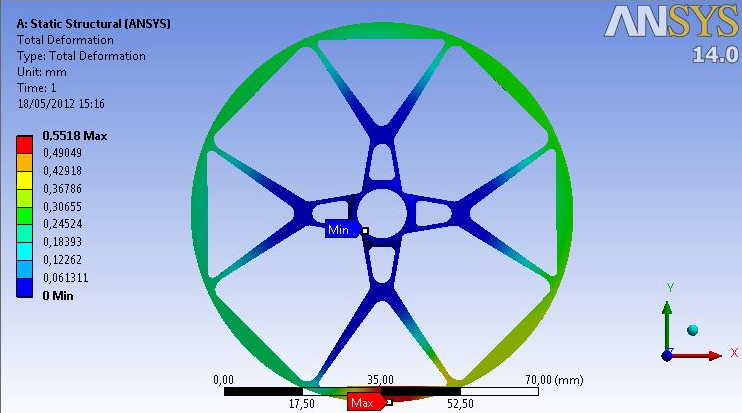 | Figure 3. Typical deformation occurred due to the charges in one of the individuals |
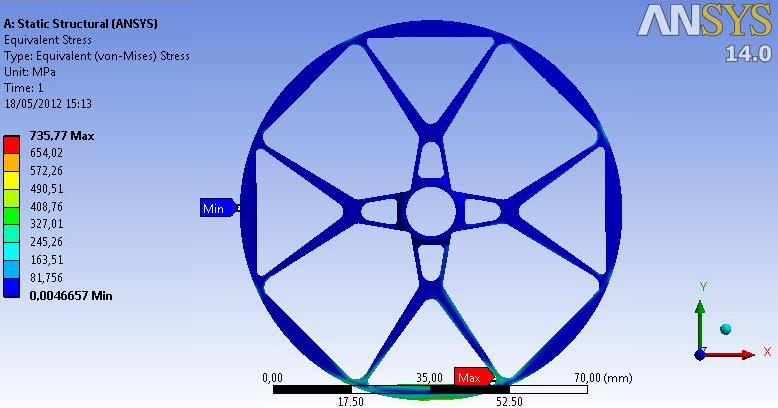 | Figure 4. Occurred tensions in one of the individuals due to the charges |
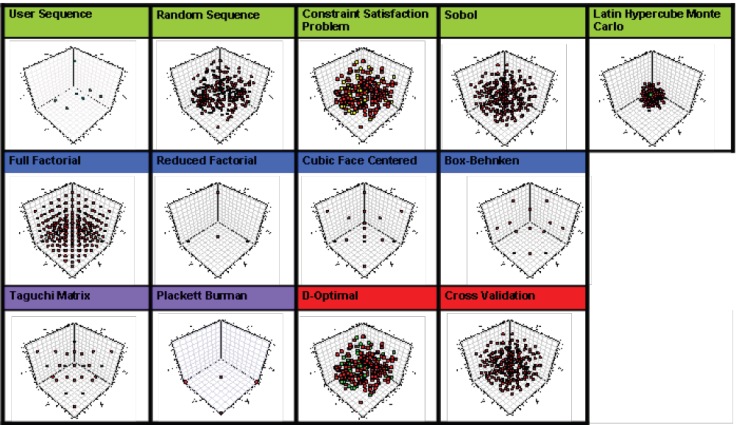 | Figure 5. Three-dimensional space of the experimental design. Some DOE are very well structured while others are just a point cloud. The choice of the statistical method depends on the number of samples and the kind of investigation. EESTECO[12] |
Table 2. Structural factors and answers from the optimization |
| DESIGN SOBOL | Geometric and structural factors | Response | Height base radius | Von Misses | Outside diameter cube | Deformation | Inside diameter wheel | Minimum Bulk | Fillet bifurcation | | Fillet Cube | | Fillet external | | Fillet Internal | | Width base arm | | Width runway | | Width tip arm | |
|
|
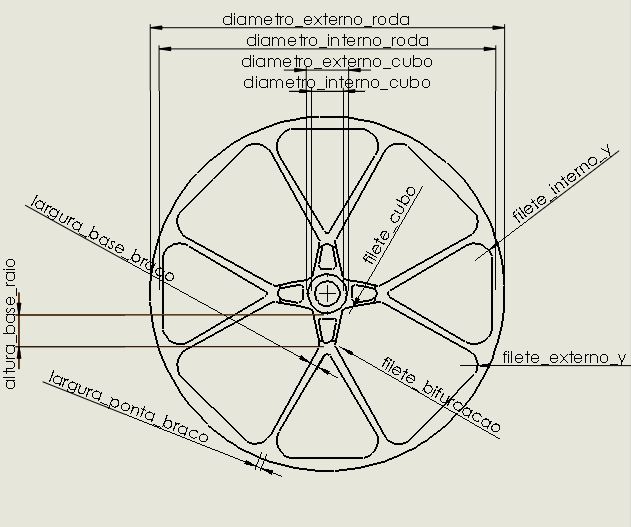 | Figure 6. Dimensional factors |
Table 3. Factors and Levels of the SOBOL experimental design 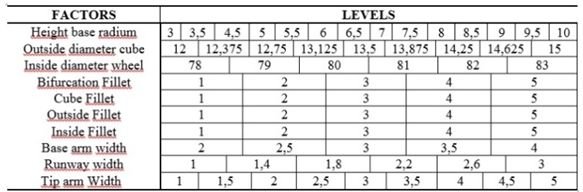 |
| |
|
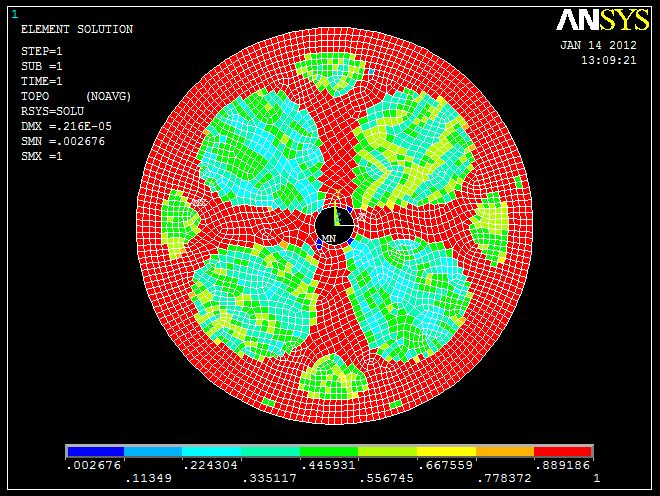 | Figure 7. Geometry generated by the topological optimization |
The optimization is done through the software modeFRONTIER®, that links the structural simulation to the optimization through genetic algorithms and statistical methods, coordinating the alteration of the input variables values to the new individuals, acting on the selection of the best along the successive generations. We decided the use of the model MOGA-II because of its quick convergence and low computational cost required, proposing the use of 300 generations with mutation rate of 1%.The initial population created constitutes of more than 40 individuals generated by the experimental planning SOBOL that generates the individuals evenly distributed in all the possible sample space.Ten variables related to the principal initial geometry dimensions were selected, with length and width of the radium, width of the runway and rounding of the corners to be improved (Figure 6).The optimization was mono objective, looking for minimizing the wheel’s bulk, and the restrictions used were the maximum tension allowed selected in the design, that corresponds to the approximated value of 342 MPa.
4. Results
Figure 7 shows the configuration of the optimum geometry of the structural components of the wheel, with four radium on the center that bifurcate each other next to the center.Figure 8 shows the bulk relief and final geometry obtained by the topological optimization linked to the genetic optimization. The individual number 688 was considered great, having mass 10,13 grams and representing a bulk reduction of 63,8% related to the wheels from the previous projects (figure 8b).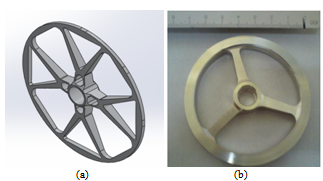 | Figure 8. (a) Final geometry after genetic optimization. (b) TKV 2011Wheel |
Table 4 presents the analysis of variances to the averages of the deformation, Von Misses stress and minimum bulk, found underlined the P-values that are lower or equals 0,05 (5%), considered significant to a level of significance of 95%.Table 4. Variance analysis 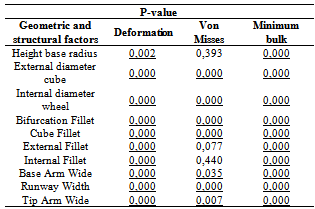 |
| |
|
4.1. Deformation
The simulated values of the wheel to the deformation vary between 0,4561 mm and 0,8038 mm. All the structural factors were significant to the deformation of the aircraft’s wheel, according to what’s presented on the Table 4. Figure 9 shows the Overall Student distribution to deformation, is observed that the factor Runway Width was the fact that most influenced in the deformation response, 16,90%, of the optimized wheel.
4.2. Von Misses
The results of the Von Misses response varied between 392,102 MPa to 787,824 MPa. The base arm wide, internal and external fillet were not significant to the Von Misses Tension. Is observed on the Figure 10, that the parameter Runway Width was the structural parameter that most influenced the Von Misses tension, with 32,3%.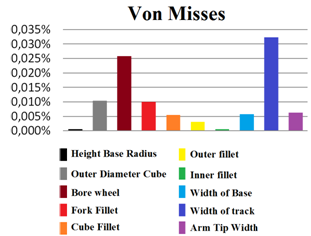 | Figure 10. Influence of the structural factors to the Von Misses Tension response |
4.3. Minimum bulk
The minimum bulk answer varied between 0,0101288 g and 0,0109893 g. All the structural parameters were significant on the wheel’s minimum bulk, showing a P-value beneath 0,05. The Runway Width was the geometric parameter that most influenced the reduction of the optimized wheel’s bulk, with 23,20%.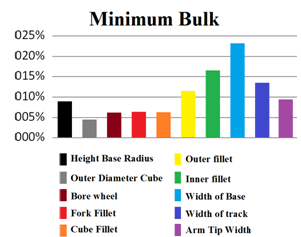 | Figure 11. Influence of the structural factors to the minimum bulk response |
5. Conclusions
The application of topological optimization via genetic algorithms showed itself extremely effective to the reduction of bulk from the analyzed component, reducing about 60% of the wheel’s bulk, compared to the previous projects.The Runway Width was the structural factor that most influenced the mechanical performance of the wheel.The width (basis, runway and tip arm) and diameter (internal and external) were the parameters that most influenced the deformation, the Von Misses tension and the reduction of the bulk, corresponding about to 80% of the structural optimization of the wheel.
References
[1] | Mosmann, R. M. Otimização topológica de estruturas contínuas submetidas a restrições de flexibilidade, volume e frequência natural. Porto Alegre. Dissertação de Mestrado em Engenharia. Porto alegre. Brasil, 2003. |
[2] | Giunta, A. Aircraft multidisciplinary design optimization using design of experiments theory and response surface modeling methods. Doctoral thesis, Virginia Polytechnic Institute and State University, 1997. |
[3] | Obayashi, S. Multidisciplinary design optimization of aircraft wing planform based on evolutionary algorithms. Systems, Man, and Cybernetics, 1998. IEEE International Conference, 4: 3148–3153, 1998. |
[4] | Batill, S. M., Stelmack, M. A., Qing Y U, X.Multidisciplinary design optimization of an electric-powered unmanned air vehicle. Aircraft Design, 2(1):1–18, 1999. |
[5] | Gundlach, J. Multi-Disciplinary Design Optimization of Subsonic Fixed-Wing Unmanned Aerial Vehicles Projected Through 2025. Doctoral thesis, Virginia Tech, 2004. |
[6] | Neufeld, D. E Chung, J. Development of aircraft conceptual design optimization software. In IEEE Fifth International Conference on Computational Science and Applications. 2007. ISSN 0-7695-2945-3/07. doi:10.1109/ICCSA.2007.18. |
[7] | Lee, D., Gonzalez, L., Srinivas, K., Auld, D., Wong, K. Aerodynamic shape optimization of unmanned aerial vehicles using hierarchical asynchronous parallel evolutionary algorithms. International Journal of Computational Intelligence Research, 3:229–250, 2007. |
[8] | Bendsoe, M. P.; Sigmund, O. Topology Optimization – Theory, Methods and Applications, Springer Ed., 2003. |
[9] | Milare, C. R. Extração de conhecimento de redes neurais artificias utilizando sistemas de aprendizado simbólico e algoritmos genéticos. Tese de doutorado. ICMC – USP. São Carlos, 2003. |
[10] | Sobrinho, C. Uma Análise das Aplicações dos Algoritmos Genéticos em Sistemas de Acesso à InformaçãoPersonalizada, 2003. |
[11] | Sant’anna, H. M. Otimização topológica de estruturas bidimensionais contínuas submetidas a restrições de flexibilidade e tensão. Porto Alegre. Dissertação de Mestrado em Engenharia. Porto alegre. Brasil, 2002. |
[12] | ESTECO. Manual do Software ModeFRONTIER 4.3, 2012. |