Evgeniy A. Bogoslov1, Nikolay P. Gerasimov2, Maxim P. Danilaev1, Sergey A. Mikhailov1, Yury E. Polsky1, Olga Y. Bogomolova1
1Department of Engineering and Technology, Tupolev’s Kazan National Research Technical University (KNRTU-KAI), Kazan, 420111, Russian Federation
2Department of Physical education, Tupolev’s Kazan National Research Technical University (KNRTU-KAI), Kazan, 420111, Russian Federation
Correspondence to: Olga Y. Bogomolova, Department of Engineering and Technology, Tupolev’s Kazan National Research Technical University (KNRTU-KAI), Kazan, 420111, Russian Federation.
Email: |  |
Copyright © 2012 Scientific & Academic Publishing. All Rights Reserved.
Abstract
A comparative analysis of cross-country skis sliding surfaces made of ultra-high-molecular-weight polyethylene, pure Teflon and Teflon with special conductive filler are presented in this paper. It is shown that the use of Teflon sliding surface increases the coasting distance by 20-27%, and decreases the distance clearance time by 20%. Sliding efficiency of cross-country skis with Teflon sliding surface is higher than of cross-country skis with ultra-high-molecular-weight polyethylene sliding surface in wide range of temperatures (-15;0°C) and high snow humidity (~97%).
Keywords:
Sliding Surface of Skis, Skis Sliding, Teflon
Cite this paper: Evgeniy A. Bogoslov, Nikolay P. Gerasimov, Maxim P. Danilaev, Sergey A. Mikhailov, Yury E. Polsky, Olga Y. Bogomolova, Efficiency of Teflon Sliding Surface, International Journal of Sports Science, Vol. 3 No. 6, 2013, pp. 224-228. doi: 10.5923/j.sports.20130306.07.
1. Introduction
Sliding surface of modern skis is made of ultra-high-molecular-weight polyethylene with various additives[1]. Before each contest the sliding surface is being waxed to improve the sliding quality[2,3]. Today the most widely used type of gliding wax is fluorine-contained wax[4]. However, wax fluorine coatings are being destroyed during skis exploitation, even with use of modern coating technologies. That causes the repetition of coating procedure before each race[5]. Because of absence of single proven gliding wax selection method and of impartial quantitative gliding wax effectiveness test, not always the servicemen can choose the right wax, that worsens the results of sporting events.Today there is an active search for gliding waxes compositions and the coating technologies that can improve the effectiveness of cross-country skis sliding. Use of gliding waxes has a number of restrictions[6,7,8], because waxes:- work at a short range of temperatures and air and snow humidity;- depend on a snow type and its structure;- can’t provide the same effectiveness of skis sliding on complex tracks with variable track conditions, such as temperature and humidity, snow structure etc.;- require the choice of a gliding wax before each race.As a result, a new type of sliding surface is needed to provide effective sliding in wide range of track conditions without gliding waxes.For analysis of skis sliding on a snow a common theory of snow crystals melting, based on heat emission during friction and formation of melted water film between the skis sliding surface and the snow surface, is used[9]. According to this theory, two types of sliding conditions exist: hydrodynamic and quasihydrodynamic. Hydrodynamic condition works at snow temperature above -5°C and is characterized by big amount of melted water between the sliding surface and the snow surface; as a result, surfaces are completely separated. Quasihydrodynamic condition works at temperature below -5°C and is characterized by small amount of melted water; as a result, top points of undulations of skis sliding surface and snow surface begin to connect, and part of the pressure is transferred to these top points. Following the theory of sliding on a melted water film, it is necessary in both conditions to use the sliding surface with high hardness (sliding surface material must be harder than snow crystals), water repellency (adhesion between the sliding surface and the snow decreases with the increase of water repellency) and low thermal conductivity (low thermal conductivity of the sliding surface saves the heat emitted from friction; this heat produce additional amounts of gliding lubricant – melted water).Comparative analysis of modern materials used for making the cross-country skis sliding surface and Teflon is presented in Table 1.Table 1 shows that the use of sliding surface made of pure Teflon, as well as of filled conductive material (such as PTFE CSC 1,2), provides low friction ratio and good conductivity. The latter removes the problem of static charges[10,11] that takes place during the exploitation of skis with Teflon sliding surface. On the one hand, low friction ratio and weak adhesion of Teflon provide effective sliding of cross-country skis in wide range of track conditions. On the other hand, low adhesion leads to restrictions in use of this material for making the skis sliding surface, because it doesn’t provide the necessary adhesive strength between monolith Teflon coating and skis base[12].The aim of this study is experimental testing of sliding efficiency of cross-country skis with Teflon sliding surface.
2. Technology
A plasma-chemical technology of nanostructured polymer coatings formation in two-phase gas flows with use of plasma at atmospheric pressure has been developed In Tupolev’s Kazan National Research Technical University (KNRTU-KAI). This technology provides Teflon tape surface modification that imparts high adhesive properties and ensures solid connection with ski base[13,14]. A plasma-chemical technology of nanostructured polymer coatings formation in two-phase gas flows with use of plasma at atmospheric pressure is based on the initiation of grafting radical polymerization reaction of surface molecules of Teflon with monomer molecules that form a thin layer (up to monomolecular thickness, but not more than 100 nm). It results in breaking of chemical bonds and generation of free radicals (including long-lived radicals) that undergo chemical and recombination transformations, such as cross-linking, creation of double-bonds and polar groups etc. With use of that a thin layer of a different polymer material is formed on one side of a Teflon sliding surface. Polymer molecules are covalently attached to Teflon surface molecules. Monomer (or mix of monomers) and carrier-gas are chosen based on their ability to perform the radical (or anion/cation) polymerization of monomer or mix of monomers by nucleation of radicals (or anions/cations). Afterwards, Teflon tape’s modified side is being attached to the surface by any known method. The second side remains unmodified. This allows the use of high water repellency and low adhesion of the outer side of Teflon coating.Structure chart of the experimental setup is shown on Figure 1.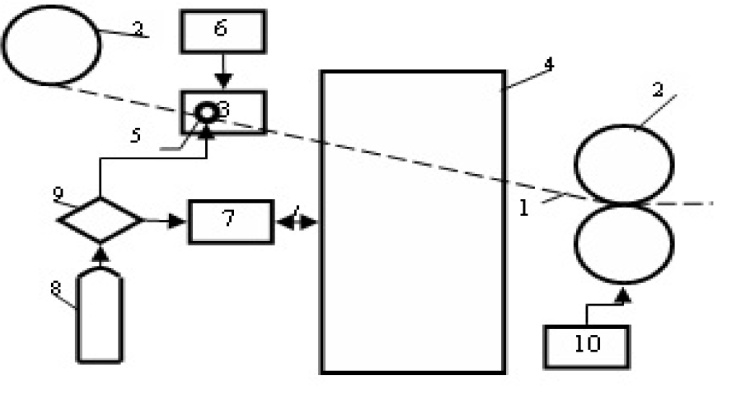 | Figure 1. Structure chart of the experimental setup |
Table 1. Comparative Analysis of Modern Sliding Surface Materials and Teflon 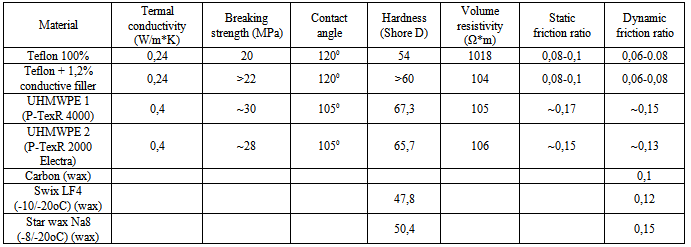 |
| |
|
Table 2. The results of adhesion strength testing 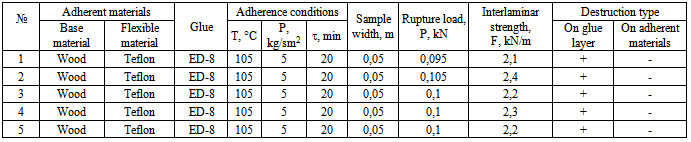 |
| |
|
Polymer film 1 was pulled by the stretch rolls 2 through the discharge chamber 3 and monomer deposition chamber 4. The discharge chamber is made of two electrodes: plane and needle. The distance between electrodes is varied from 1 to 2 cm with 10% accuracy. For extension of radicals lifetime scale on the surface of polymer film and for stabilization of corona discharge inert gas (Ar) inputs 5 were made in side walls of the discharge chamber.Gas consumption through the side walls inputs was ~0.5 cm3/sec. Monomer particles were ejected into monomer deposition chamber 4 with the ejector 7. Argon was used as the carrier gas 8 for creation of two-phase gas flow. The discharge chamber was installed in the exit nozzle of the ejector 7 to provide the possibility of monomer particles charging in the corona discharge. Power source’s output voltage of the discharge chambers ranged between 0 and 50kV with 5% accuracy. Two-phase (monomer particles and inert gas) gas flow’s consumption was regulated by reducer 9, installed in the entrance of the mixing chamber. Polymer film speed was determined by drive assembly 10 at ~15sm/sec. The distance l between the discharge chamber and monomer deposition chambers was chosen according to radicals lifetime scale on the surface of polymer film, l~1sm. In experimental studies a styrene was used as monomer that creates a thin cohesive layer after polymerization. Styrene was chosen because of its ability to perform radical polymerization with formation of copolymer with surface molecules of polymer (Teflon) film.The testing of adhesion strength between monolith Teflon tape and ski base took place on a testing stand imitating the ski work in the ‘Laboratory of strength’ of KNRTU-KAI (Figure 2).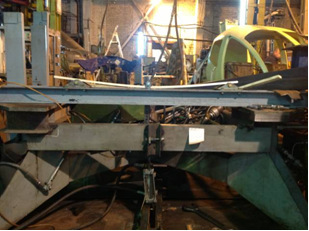 | Figure 2. Testing stand imitating the ski work |
The adhesion strength was tested after 350000 cycles of bending that corresponds to more than a 1000 km of skiing. The results showed no signs of adhesion failure.The adhesion interlaminar strength was tested on the tearing machine IR 5046-5. Loading rate was 100-200mm/min. At least five samples were prepared from a 1,5 mm thick Teflon tape, the size of samples was 50x125mm. The samples were pasted in the wooden bricks. An epoxy-diane glue (ED-8) was applied on a 110 mm length; ends of a sample were fixed in the tearing machine’s claws.Interlaminar strength was defined by the formula: | (1) |
where Р – average load of tape delamination, N; b – glue layer thickness, m. An arithmetical mean of interlaminar strengths of all samples was taken as a test result. Based on a gathered data, the adhesion strength of surfaces’ interactions was estimated. The results of testing are shown in Table 2. Thus, adhesion interlaminar strength between modified Teflon tape and wooden brick was at least 2 kH/m (kg/sm).To estimate the efficiency of Teflon coating of a skis sliding surface, a number of experiments on downhill coasting distance with and without skier were performed.
3. Experiments
A series of experiments on downhill coasting distance of weighted skis were made in the end of a 2012-2013 winter season to gain a rough estimate of sliding effectiveness of cross-country skis with Teflon sliding surface. The experiments were made without a skier. The scheme is shown on Figure 3.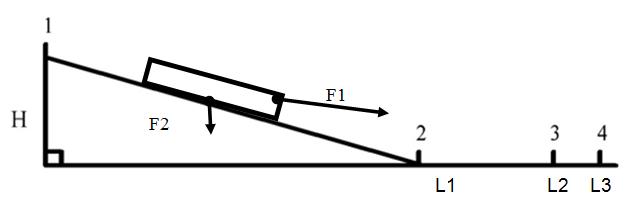 | Figure 3. The scheme of an experiment on downhill coasting distance of weighted skis |
On the Figure 3: 1 – start point; 2 – finish point of a ski with waxed sliding surface; 3 – finish point of a ski with sliding surface with pasted-in 50 micron thick Teflon film; 4 – finish point of a ski with sliding surface with pasted-in 1mm thick Teflon tape; H – slope height (H~1,5-2 m); L1 – coasting distance of a ski with waxed sliding surface; L1+L2 – coasting distance of a ski with sliding surface with pasted-in Teflon film; L1+L2+L3 - a ski with sliding surface with pasted-in Teflon tape.The experimental conditions were:- air temperature: ~0°C;- snow temperature: ~-5°C;- relative air humidity: ~80%;- stable waterlogged snow cover. Eighty-five experiments on downhill coasting distance were made in total, using the scheme, shown on Figure 2. It is worth nothing that thickness of cross-country skis is usually 1 to 1,5 mm, so using of 50 micron thick film was necessary only for optimization of pasting-in technology. The results are presented in Table 3 (normalized velocity V0 was calculated comparatively to the velocity of ski with waxed sliding surface).Table 3. The results of experiments on downhill coasting distance (without a skier) 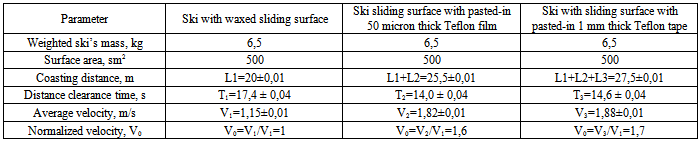 |
| |
|
Table 4. The results of experiments on downhill coasting distance (with a skier) 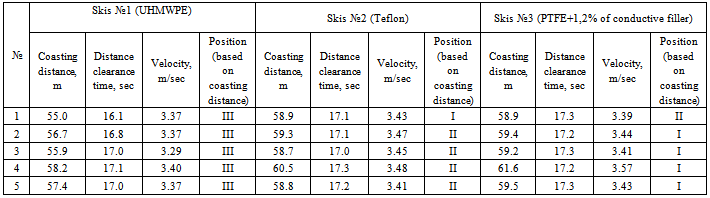 |
| |
|
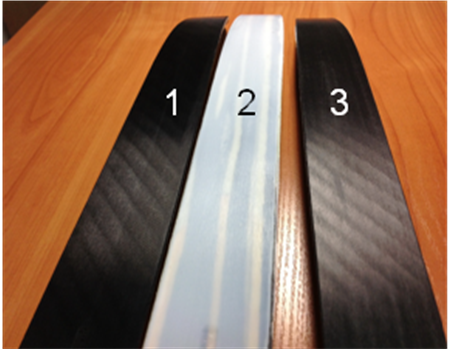 | Figure 4. Cross-country skis with SS made of: 1 – PTFE+1,2% of conductive filler; 2 – Teflon-4; 3 - UHMWPE |
The experimental results analysis shows that the use of Teflon as a sliding surface improves the coasting distance by 20-27% and also improves distance clearance time speed by 20% that indicates the increase of skis sliding efficiency.For more thorough experimental research a test cross-country skis for skate skiing with three different types of a sliding surface (SS) were made (Figure 4):1) SS made of ultra-high-molecular-weight polyethylene with gliding wax for appropriate weather conditions (skis №1);2) SS made of ‘pure’ PTFE (Teflon) (skis №2);3) SS made of PTFE+1,2% of conductive filler (skis №3).Experimental studies took place in a time period from January 11th, 2013 to January 21st, 2013 using the scheme, shown on Figure 3. Test skis were preliminary mechanically treated; all three pairs had the same pattern marked on the sliding surface. Experiments were conducted at different temperatures to realize two types of sliding conditions: hydrodynamic and quasihydrodynamic. Eighty-five experiments on downhill coasting distance were made in total, using the scheme, shown on Figure 3. The sliding efficiency was judged by skier’s coasting distance. During experiments, estimations of time and distance measuring inaccuracies were made. Measuring inaccuracy:− of coasting distance δ1~1%− of distance clearance time δ2~1%.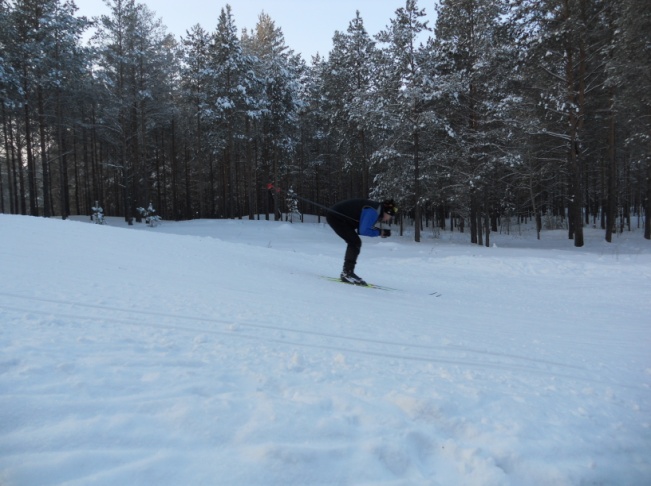 | Figure 5. Experiment on downhill coasting distance (with a skier) |
The results of five experiments (Figure 5) are presented in Table 4. The results of other eighty experiments were similar to the presented five and with the same measuring inaccuracies, so they are not presented for conciseness.The results show that skis №2 and №3 had the longest coasting distance and highest speed. The coasting distance advantage was 2-9 m comparing to skis №1. Skis №2 and №3 were winning by turns, depending on the weather conditions
4. Conclusions
The results analysis shows that:- the use of Teflon SS not only increases the coasting distance by 20-27%, but also decrease the distance clearance time by 20%; which is the evidence of increase of sliding efficiency;- efficiency of sliding of test skis with Teflon SS depends on a weather conditions. A comparative analysis of experimental results shows that sliding efficiency of cross-country skis with Teflon SS is higher than of cross-country skis with waxed UHMWPE SS in wide range of temperatures (-15;0°C) and high snow humidity (~97%). The results comply with the theoretical analysis of sliding of skis with Teflon SS.Thereby, use of Teflon SS is promising for different sports equipment, such as sledge, snowboards etc.
ACKNOWLEDGEMENTS
Authors acknowledge Y.F.Zolotov, a professor of a ‘Physical education’ department of KNRSU-KAI, for his help in preparation and making of the experiments.
References
[1] | C.Stamboulides, P.Englezos, S.G.Hatzikiriakos, “Ice friction of ultra-high molecular weight polyethylene: The effects of fluorine additives and plasma (PECVD) treatment”, Tribology International, vol. 57, pp. 177-183, Jan. 2013. |
[2] | N.P.Gerasimov, Y.F.Zolotov. Ski training on a Physical culture classes in high school. Methodological guide. Kazan, 2011. |
[3] | V.I.Aparin, A.P.Bezrukov, B.A.Gubatenko, E.A.Dukhovsky, A.Y.Lyapunov, N.N.Rozhkova, “Ski wax”, RU Patent 2203300, Apr. 27, 2003. |
[4] | I.Rogowski, D.Leonard, J.-Y.Gauvrit, P.Lanteri, “Influence of fluorine-based additive content on the physical and physicochemical properties of ski gliding wax”, Cold region science and Technology, vol. 49(2), pp. 145-150, Aug. 2007. |
[5] | L.Kuzmin. Surface sliding friction of skis: nature, paths and methods of improvement. All-Russian scientific-practical conference ‘Modern system of sports training in biathlon’. Omsk, 2012. |
[6] | L.Kuzmin, M.Tinnsten, “The contamination, wettability and gliding ability of ski running surfaces”, Science and Nordic skiing, pp. 286–292. 2007. |
[7] | L.Kuzmin, M.Tinnsten, “Dirt absorption on the ski running surface – quantification and influence on the gliding ability”, Sports Engineering, vol.9(3), pp. 137-146. 2006. |
[8] | L.Kuzmin, M.Tinnsten, “Estimation of dirt attraction on running surfaces of cross-country skis”, The Impact of Technology on Sport II, pp.851-856, 2007. |
[9] | V.A.Balakin, O.V. Pereverzeva, “Frictional heating and melting of sliding surfaces”, Journal of Friction and Wear c/c Trenie i Iznos, 1994. 15(4): p. 118-131. |
[10] | M.Yekta-Fard, A.B.Ponter, “Factors affecting the wettability of polymer surfaces”, Journal of Adhesion Science and Technology, vol.6, pp. 253-277, 1992. |
[11] | G.Sandford, “Perfluoroalkanes”, Tetrahedron, vol.59(4), pp. 437-454, 2003. |
[12] | A.D.Zimon. Adhesion of films and coatings. Moscow, 1977. |
[13] | Y.E.Polsky, S.A.Mikhailov, M.P.Danilaev, “Methods of polymer films modification (options) and device for its realisation”, RU Patent 2439096, Jan. 10, 2012. |
[14] | E. A. Bogoslov, M.P.Danilaev, M. V. Efimov, S.A. Mikhailov, Y.E.Polskii, K.V.Faizullin Experimental Studies of a Method of Formation of Multilayer Polymer Films with Given Physicochemical Properties of Individual Layers// Protection of Metals and Physical Chemistry of Surfaces, 2013, Vol. 49, No. 3, pp. 332–335. |