Deepak Tomar
Northwest Missouri State University, Maryville, USA, Visa Inc, USA
Correspondence to: Deepak Tomar, Northwest Missouri State University, Maryville, USA, Visa Inc, USA.
Email: |  |
Copyright © 2020 The Author(s). Published by Scientific & Academic Publishing.
This work is licensed under the Creative Commons Attribution International License (CC BY).
http://creativecommons.org/licenses/by/4.0/

Abstract
To discuss how important is the Quality management in the organization. The quality is something that evaluates how good is the organization and can satisfy customer by providing best quality in their product and the processes. It is not about building a project but it is also to build through a process of continuous quality management which embraces terms like ISO 9000, Six Sigma and capability maturity model integration. ISO 9000 provides a standard which is simply to provide guidelines that defines how a product or a process should be. The organization follows these standards to define software, hardware, products and support their products delivered to the customers. When it is necessary to create the new processes, at the same time, there is an equal need of finding issues with the existing process and that is where Six Sigma helps. Six Sigma focuses on measuring the existing process and finds flaws in that process. In a real environment, Six Sigma has been really helpful to find out flaws in the design, process and product. Last but not the least, Capability Maturity Model integration also provides a process improvement approach that provides organizations with the essential elements of the effective process. The below research gives more insight to the Total quality management and the terms associated with this process.
Keywords:
Total Quality Management, ISO 9000, Six Sigma, CMMI, DMAIC, Six Sigma Certification, Six Sigma Team, Accreditation, Capability scale
Cite this paper: Deepak Tomar, TQM, ISO 9000, Six Sigma and CMMI Project Management in Business and Technology, Software Engineering, Vol. 9 No. 1, 2020, pp. 1-8. doi: 10.5923/j.se.20200901.01.
1. Introduction
Before talking about total quality management, ISO 9000, Six sigma, and capability Maturity Model Integration, it is fairly important to talk about why do we need all these terms. It is because the awareness of quality in the organizations is very important so we need Total Quality Management approach in organizations to focus and manage it. TQM is like an umbrella embracing other terms like, ISO 9000, Six sigma, and capability Maturity Model Integration. The aim of writing this paper is to discuss these terms precisely. (Dr ferg)Quality is a key factor and it has two different views which is customer and producer view. Customer view is more subjective and it can be a look, feel and function of the product. Producer view is objective which is conformance requirements and costs. Quality of a product can also be evaluated with certain factors like performance which states that whether product is capable of doing its intended job or not, reliability that is how often product will fail, durability which is how long product will last, serviceability which define as how easy it is to repair, aesthetics related with product looks and appearances and conformance to standards. These all are in fact are maintained by ISO 9000, six sigma and CMMI.Dr Edward Deming has also said that quality is fitness for use. There are three ways by which product development can be viewed. Product is designed for a particular customer, for a mass consumption and may be designed on a customer requirement and it is essential to maintained quality in all these ways of development. (Hammett)There are many definitions to explain quality and its evaluation. If explained in simple words than it will be such as quality in terms of product’s quality, product process quality which is focused on a process producing product, service quality process which can be a service after product is availed or launched, and business planning which apparently set a goal to achieve quality. In Business planning goal is divided into sub goals, and also involving customers and suppliers in strategic quality planning. (Juran, Joseph M., 2002).
2. What is Total Quality Management
Total quality management is an approach to maintain quality and focus on the cost in order to maintain it. “A process for managing quality; it must be a continuous way of life; a philosophy of perpetual improvement in everything we do”. (U, Prakash). If we try to look at evaluation of TQM then it will a series of four terms which are inspection, quality control, quality assurance, and TQM. The basic aim is to satisfy customers by improving the processes involved to develop a product, and this is done by comprising experiences of the workers. TQM states that customer decides quality, workers produce it and top management leads it and provides necessary support. TQM mainly laid emphasis on multifunctional teams. (Waxer, Charles., 2007)
2.1. Principles of TQM
The five main principles are Management Commitment, Employee Empowerment, Fact Based Decision making, Continuous Improvement, and Customer Focus. In management commitment, the first step is to design and plan followed by deployment. After getting it deployed the product is processed for critique, examined and revised. It is also called as Dr. Deming’s PDCA cycle. In the employee empowerment, training is conducted for employees and excellent teams are developed. It also comprises of recognition. These teams are put forth for decision making purposes so as to assure quality, and for this aim SPC (statistical process control) and TOPS (Team oriented problem solving) are used. Since customer needs to be satisfied, TQM brings in systematic improvement in process and measurements. TQM also focus on customer relationship with producers and take care of customer driven standards. All these features explain how TQM manage quality. (Waxer, Charles., 2007). The key factor of TQM is to prevent errors and not detect errors. It says that mistakes can be avoided and defects can be prevented.
2.2. Concept of Continuous Improvement
It gives three ways to make product better and better. The first measure is to avoid mistakes while developing a product. Inspection at each step can also be another important step to avoid errors so that these errors cannot proceeds to next step and become a cause for new errors. The solution for this step is to stop at the point where error is found, go back and make corrections, test that module and then proceed further. This will lead a better process cycle. (Dr. Ferg)
2.3. W. Edward Deming Philosophy
Dr. Edward Deming (Oct 14, 1900- Dec 20, 1993) was an American statistician. He included an application of statistical methods such as analysis of variance (ANOVA) and hypotheses testing. He also gave a formula for quality which is Quality = result of work efforts/ total costs.He also gave a system of profound knowledge which is to look into system from outside and then approach for a quality product. According to him, this system involves producers, customers and suppliers. Deming also gave his fourteen points in order to justify his philosophy about quality. Some of points are creation of constancy, adopt a new philosophy of cooperation, institute training, drive out fear and build trust, put everyone to work to accomplish the transformation.Deming PDCA cycle gives a chain of steps to solve quality problems. This cycle involves plan which is to get data, analyze problem, and plan the solution. ‘D’ stands for ‘do it’, ‘C’ is to check for faults and ‘A’ stands for modify as needed. Finally go back to the first step of plan and so on. This cycle is similar to Carnegie plan but it does not have one more phase and that is to define the problem being as the first phase according to Carnegie plan. (Quality Based Problem-Solving)
2.4. Why TQM Fails?
TQM can also fail and the reason behind is that the organizations are unplanned and so anxious to start that they forgot about some important tasks. Other cause of failure is that not all issues are considered like service after the product is delivered and which in turn may not satisfy customer because of this poor customer service. It is also noticed that TQM experts are usually hired and manager does not learn those skills which in case can be use in future. Managers are also assumed to take training from institutes so as to learn how to lead an organization. This is also an important principle given by Deming. (Bacal, Robert)
2.5. The Impact of National & International Quality Awards on Total Quality Management
There can be an interrogation at this point. Why there is a need for an award for terms like TQM, ISO 9000, Six Sigma etc and how it affects the quality of product? The reason to give award is to evaluate and understand an organizational performance as compared to others. This helps in accessing organization’s current performance against a set of guidelines which others followed and gave a quality product. Donald Peterson, chairman of ford motors said that find out the other companies best in that industry and benchmark operations against the most efficient. There are awards like Malcolm baldrige European quality award which is given to small business and companies whereas Deming award is for individual, and companies known for outstanding results.
2.6. Quality Control Process
Although it is very important to invest in the continuous quality improvement process, it is also very important to have proper quality control procedures in place. It is not impossible to completely define and test all possible scenarios and outcomes of a product during software development but the process must be terminated at a point when it confirms to the requirements and satisfy almost all the possible expectations and outcomes.
3. What is ISO 9000
What is standard? “A standard is simply a definition of how something should be.” (Seaver, Matt, 2001). ISO is a set of internationally recognized and accepted standards and it is originated for business quality systems. (Quality-Based Problem-Solving)ISO 9000 is the standard which is most widely known among all the standards given by ISO and it gives guidelines for selecting a project. In order to get through this standard, the businesses need to give quality and pass with audits. There have been standards developed before but they were not sufficiently consistent for widespread use. (Juran, Joseph M. 2002. ISO 9000)ISO 9000 is generic and applied to all generic product categories which can be hardware, and software. These standards are widely accepted worldwide and have an effect on national and international trade. These standards are used by management systems in an organization to design, produce and support their products. (Juran, Joseph M. 2002. ISO 9000)
3.1. VISION 2000
The first meeting of ISO/TC 176 was held in 1980 and ISO series was first published in 1987 which consist of guidelines given by ISO 9000, three standards to assure quality like ISO 9001, ISO 9002, ISO 9003, and quality management guidelines ISO 9004. In year 2000, the standards were revised and they were named as ISO 9000:2000, ISO 90001:2000 and 9004:2000. This paper basically discusses about ISO 9000, ISO 9001 and ISO 9004. (Seaver, Matt, 2001)
3.2. ISO 9000:2000
ISO 9000 series gives guidelines for selecting a product. ISO 9000 series standards are applied in government and other organizations and make easier and faster development and maintenance of products. It also develops a leadership and good customer and supplier relations. The advantage of giving guidelines is that the customer is aware beforehand and can get quality in terms of performance and efficiency of the product. If any system conforms to standard that mean it will perform well and will be satisfying customer’s need. (International organization for standardization)
3.3. ISO 9001:2000
Seaver Matt has called ISO 9001 series as quality management system requirements. It is not concerned with the cost and finance effectiveness but on those purposes that indirectly affects the quality of the product. So, it does not help any organizations to deal with economic states and money affairs. The factors on which ISO 9001 focus are the personal aspects like specific sales and marketing of the product. The product should match the standards set in order to advertise it for use. ISO 9002 and ISO 2003 are designed for organizations that require it for testing and final inspection to see that whether the product meet the required specifications. But these ISO 9002 and ISO 9003 are merged in ISO 9001. ISO 9001 has major stages of setting up any product for quality assurance. These are taking requirements, process, resources, and control and inspect. There are two ways like Manufacturing and service level by which ISO 9001 can be discussed in terms of product. In service operations, solutions to clients are provided and in manufacturing phase product is manufactured, calibrated and tested. (Seaver, Matt 2001)
3.4. ISO 9004:2000
‘ISO 9004 is recommended as a guide for organizations whose top management wishes to move beyond the requirements of ISO 9001 in pursuit of continual improvement of Performance.’ (Seaver, Matt.). It covers a large scope creep and is deliberately positioned between ISO 9000 and award criteria. It consists of those features which directly affects the product quality and provide a guideline to enrich and improve the ISO 9001 baseline.These all above defined standards series together improves product quality and service to customer. (Seaver, Matt, 2001)
4. Six Sigma
4.1. Introduction
Six Sigma is different from the other processes in a way that it mainly concentrates on measuring the existing process while the other provides a way to create a new process for producing a product. Six Sigma measures existing process and will modify it in a way that number of defects is reduced. Using Six Sigma we can only reduce the number of defects but we cannot produce zero defective system. In Six Sigma we can have a maximum of 3.4 defects per one million chances of having defects. It means that if we produce a million products we can just have 3 to 4 defective products. As it is used to measure and modify the existing process it is normally paired up with other processes such as CMMI or ISO 9000. (Persse, James R., 2006)
4.2. Why is It Six Sigma
Six Sigma concentrates on the variation of data in a data set. Variation of data will be in a very predictable manner, most of the data will fall under the middle. We measure variation in terms of Standard deviation. “Standard deviation is a well-founded measure of the range of variation from the average for a group of measurements” (Persse, James R., 2006). So, if we plot a graph between standard deviation and number of values under each deviation we will get a curve which is in a bell shape, normally referred to as bell curve. Example of bell curve is shown below in figure 1.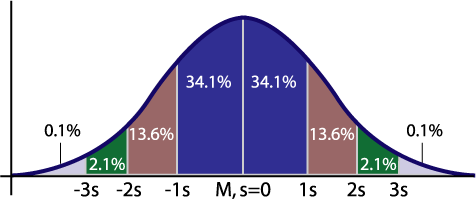 | Figure 1. Standard Deviation Diagram (From: http://en.wikipedia.org/wiki/Image:Standard_deviation_diagram.png) |
According to the above diagram it is clear that 68.2% of data will be with in first standard deviation and almost 95% of data will be with in second standard deviation. Above diagram just plots the graph until 3 standard deviations but if we can plot until 6 standard deviations almost 99.9997% of data will be within that 6 standard deviations. This percent takes us nearly to what Six Sigma wants “3 to 4 defects per million opportunities for defects”. Sigma (σ) means Standard Deviation (SD) and six is because of the reason explained above. So, this process is called Six Sigma. (Persse, James R., 2006). Six in Six Sigma is not mandatory it depends on the type of business we are doing, customer requirements, quality we want and so on. (Persse, James R., 2006)
4.3. History of Six Sigma
Six Sigma was created at Motorola around 1979 by two engineers named Art Sundry and Bill Smith. They were in the pagers business and those pagers have quality problems, so they want to find a way to measure their existing process and want to find defects in that process. Then they created this Six Sigma process. Motorola has recorded almost $16 Billion from 1985 using Six Sigma process. In that way it became very popular. In 1995 Jack Welch adopted this process of Six Sigma into General Electronics (GE). He and his team made many changes to the original process. The Six Sigma what we right now using is mostly the one developed by Jack Welch and his team. (Persse, James R., 2006).
4.4. Ownership of Six Sigma
“Folks at Motorola created it Honeywell added to it GE refined it, Ford put its spin on it” (Persse, James R., 2006). As these many companies developed no body actually owns Six Sigma. It is an open source product and has no governing body which is the chief weak point of Six Sigma. As there is no governing body many companies hesitate to implement this process. “Respectable institutions like Villanova University, the American Society for Quality, an organization called iSixSigma have training guidance programs. GE has a well-maintained Six Sigma website” (Persse, James R., 2006). All these institutions are developing and maintaining Six Sigma but not have coordination between them.
4.5. Cycle of Seven Steps
Six Sigma is a “process measuring” process which typically involves seven steps and has a feedback loop. Those seven steps are1. The first step is looking at the product in which we study what the product is, quality of the product and the way we are producing it.2. Next, we try to identify the defects in the product. “Defect means anything that holds your product from being its best.” (Persse, James R., 2006)3. After identifying the defects in the product, we will look at the process. Here we understand the complete process which we are using to produce a product. If we have some defects in the product it is very likely to have defects in the process that is used to produce that product.4. Then we identify the sources for the defects. 5. Once we know the actual sources for the defects then we improve the existing process by eliminating the actual sources for defects. 6. Then we will use the new process.7. Again, we will go to step 1 which indicates the feedback loop and also clearly states that Six Sigma is a continuous process and always tries to make process better and better. (Persse, James R., 2006)
4.6. Structure and Design
If wanted to express the whole process of Six Sigma in a very simple manner we can say as “Deliver Quality”. The Quality in that term is very important and very different from what actually quality means here Quality means what customer wants. The main aim of Six Sigma is to deliver what customers want. GE calls this process of knowing what customer wants as “Voice of Customer” (VOC). The first step in Six Sigma is gathering what customer wants and then it concentrates on measuring the existing process. (Persse, James R., 2006)Consider a simple equation X= f(Y). Here X and Y are two variables and according to the equation it is clear that X depend on Y. It is the simple equation to express the cause and effect relation. Here Y is the cause and X is the effect we cannot directly control effect, the only way to control X is to control Y. Six Sigma concentrates on Y. Once heard the VOC we can define our own X=f(Y) which is specific to the product we are developing. After X is known we decompose it into several smaller parts to find Y. Here we start modifying Y so as to reduce the number of defects in overall process. In order to modify Y, we have two steps to follow, first we have to know how our product works in the real time environment that means in the typical floor conditions. If the performance of it varies a lot from the ideal performance then we have to know the reasons why it is varying so? These are the original reasons for the defects and we can modify them to increase the quality of our process. (Persse, James R., 2006)This is how Six Sigma is implemented on any process to improve that process by reducing the number of defects.
4.7. Methodologies of Six Sigma
There are two methodologies implemented by Six Sigma first one called DMIAV for improving the existing process, on which Six Sigma mainly concentrates on. Second one called Design for Six Sigma (DFSS) used for designing a new process for a new product. (Persse, James R., 2006)
4.7.1. DMAIC (Define, Measure, Analyze, Improve and Control)
-- Define: This phase still includes some more sub processes which are• Defining the problem in which we define the actual target of the program• Defining the project in which we define the scope of the project• Defining the goal in which we state the approach of doing the project• Defining the boundary conditions in which the boundary of the project is defined so that our project does not go out of scope• Developing the project plan in which the project plan is prepared using the above statements • Initiating the plan in which the prepared plan is implemented-- Measure: Measuring is done in three phases they are• Prepare to measure: Sometimes measuring can be invisible but most of the time measuring the existing product may disturb the present working atmosphere. So all the people who might be disturbed must be well prepared before the actual measuring process takes place.• Measure: In this phase we actually measure the existing process. All the things that need to be measured and the procedure to measure must be well defined in the define phase• Protect the data: As the data that we get from measuring is very important we have to protect the data from being tampered and from being stolen. -- Analyze: In this phase we actually analyze the data that we collected from the measuring phase to determine the root cause for the defects and then we establish an empirical basis for improving the existing process. Six Sigma concentrates on improving the quality quantitatively so establishing an empirical basis is extremely important.-- Improve: Next phase in DMAIC is improving the existing phase this is the most important phase and the improvement of your process is mainly dependent on this phase. This is again done in several small steps• Assess: We assess the present state of the process• Develop: Several alternative approaches are developed based on the above assessments to improve the process• Select: We select one of the above developed alternatives to implement • Modify: modify the existing process with the above selected alternative • Pilot: we implement the modified process • Verify: Again, verify the modified process for the flawsAt the last phase “Verify” we are almost going to the first phase and all these steps are repeated again and thus this phase itself forms a feedback loop-- Control: As we are changing the existing process we have to control the change and even this has got 3 steps involved in it. They are• Control Plan: This provides us with all the users and the systems that are going to be affected by the present change• Control Tools: These provides all the available things that can be used to adopt the change. This may include things like manuals and tutorial sessions and so on.• Project Closeout: Though Six Sigma is an ongoing process practically implementation of Six Sigma closes here.
4.7.2. Design for Six Sigma (DFSS)
This is used when we want to create a new process. This is often referred to as DMADV (Define, Measure, Analyze, Design, and Verify). All these steps are almost similar to DMAIC which is discussed above. (Persse, James R., 2006)
4.8. Six Sigma Certification
There is no particular single body that is designated to give Six Sigma Certification. As Six Sigma is an open source any one can train people on Six Sigma and can certify them as Six Sigma trained. A company has to spend almost $30,000 on an individual to train on Six Sigma and this one of the major reasons that every company that trains people on Six Sigma will also certify the people. Certification typically involves three steps. 1. Training2. Written test3. Hands on competency displayThe major disadvantage of this certification is that there is no particular measure to say whether any individual pass of fail to display competency. (Beth, M., Konrad, M.C. and Shrum, S.)
4.9. The Six Sigma Team
From the above discussion it is clear that implementing Six Sigma is not easy to implement so we have a Six Sigma team to implement Six Sigma in any organization. The team contains several designations which we will discuss in detail. (Persse, James R., 2006)ChampionChampions are the one who initiates any Six Sigma projects. They are the high-level managers in any organization. They act as executive sponsors to the project. They direct and develop Six Sigma projects. They are responsible for implementing the project across the organization in an integrated way. Along with the above duties they have authority to• Control resources• Allocate budgets• Assign responsibility• Set strategic directionMaster Black BeltThis is the highest level of certification in Six Sigma. They must have good understanding of DMAIC and can be able to apply statistics to complex applications. These people assist champions and will guide the next level designation Black belt people. They must be able to manage Six Sigma projects as well as Six Sigma teams. In order to claim to be a master black belt one must have save at least hundreds of thousands of dollars for the company.Black BeltBlack belt people lead the Six Sigma project teams. They must have good working knowledge on DMAIC and DFSS. These people concentrate on implementing Six Sigma to a particular project. “Black Belts focus on project execution while Champions and Master Black Belts concentrate on identifying the projects for Six Sigma” (Persse, James R., 2006).Green BeltThese people are the team members of the Six Sigma team and so often referred to as field soldiers in Six Sigma projects. Even they should have a knowledge about DMAIC as they are the people who actually implement Six Sigma.Yellow BeltThis is the least designation in Six Sigma and not widely recognized.
5. Capability Maturity Model Integration
5.1. Introduction
“CMMI is a process improvement approach that provides organizations with the essential elements of effective process” (SEI, what is CMMI). When compared to remaining process improvement methodologies this is very compact and is proved both quantitatively and qualitatively. In acceptance and use around the world, CMMI runs 2nd only to ISO 9001 program, and in terms of momentum, CMMI is probably leading. Even CMMI don’t have any official accreditation. (Persse, James R., 2006)
5.2. History
Before CMMI we have a process named Capability Maturity Model (CMM) which is developed by Software Engineering Institute (SEI) at Carnegie Mellon. But since 1991 CMM had developed several models and companies started using them. After sometime they realize that they are using different models to do almost similar things but using different models of CMM. Then SEI concentrated on integrating all the different models of CMM. Main target of CMMI development team is to reduce the difficulties in using multiple CMM’s. So, they combined three different and popular models to form CMMI. They are1) The Capability Model for Software (SW-CMM): This is used to develop software2) The System Engineering Capability Model (SECM): This is used to develop all the systems which may or may not include software3) The Integrated Product Capability Maturity Model (IPD- CMM): “IPPD is a systematic approach that archives a timely collaboration of relevant stake holders throughout the life of product to satisfy customers’ needs, expectations and requirements” (Persse, James R., 2006). Normally this is combined with either one of the above-mentioned models. (Persse, James R., 2006)
5.3. Ownership
CMMI is developed by SEI which is funded by the department of Military. American people pay for it so they own it. This is the only program that is both free to use and well maintained by some institute. (Persse, James R., 2006)
5.4. Structure and Design
This is probably the only program that is specifically designed for the IT industry. The whole process is divided into 22 Process Areas (PAs) “PA is collection of best practices that help a technology organization manage its activity and control its quality” (Persse, James R., 2006). Each PA has some goals to implement so we consider this design as goal-oriented design. (Persse, James R., 2006)
5.5. Implementation of CMMI
CMMI can be implemented in 3 ways- Continuous representation- Staged representation- “Anyway, you want way” (Persse, James R., 2006)
5.5.1. Continuous Representation
This method is used when we want to implement CMMI in a particular area in our project. This method provides us a way to implement any process areas we want to implement on any area in our project. Capability Scale has 6 values in it from 0 through 5 each is represented by a phrase0. Incomplete1. Performed2. Managed3. Defined4. Quantitatively Managed5. OptimizingAlthough this way has an advantage of implementing in our own way staged representation has more popularity, so we will look at that type in detail. (Persse, James R., 2006)
5.5.2. Staged Representation
Unlike the continuous representation in this representation we have to implement all the predefined process areas. It has 5 maturity levels 1 through 5 and each represented by a phrase. They are1. Initial2. Managed3. Defined4. Quantitatively Managed5. OptimizingEach of the level is discussed in detail in the below sections.1. Initial: At this level organization will not have any process to implement. Products are developed without any process. The term “hero dependent” can be used in these types of organizations. There will be some key people in team and they complete the project. In spite of having no process in use they do complete some projects but they frequently exceed time and cost.2. Managed: At this level organizations will just enter into phase where they start using some sort of process to produce a product. In this level organizations concentrate on two thingsa. Project management which gives us a strategic way of effectively planning, managing and controlling project components.b. Process management which concentrates on implementing a program to ensure that the established process is being honoured in a company.3. Defined: Organizations at this level already have a process existing and they thoroughly defined and studied their process. Not only that but also the organization have good process management and improvement program. The organization’s management establishes process objectives and make sure that these objectives are addressed appropriately throughout the organization.4. Quantitatively Managed: The term itself tells us what it actually means. At this level organizations have some empirical basis to measure their quality of the process. As they have some sort of measurement of their quality they have some quantitative targets for their quality. Here most of the decisions are data driven similar to Six Sigma. The major difference between this level and the previous level is the process is measured qualitatively in previous stage while we measure process quantitatively in this stage. 5. Optimizing: This is the last level of maturity any organization can attain in CMMI levels. At this level the process improvement becomes an ongoing process. The above established quantitative measurements are revised based on the project needs. The major difference between this level and the previous level is that in this level we concentrate on the general reasons for the process variation while in the previous level we concentrate on special causes for process variation. (Persse, James R., 2006)
5.5.3. Any Way You Want
This is the most flexible way of implementing CMMI. We can define our own process areas and can implement in any area of project we want. The difference between this and the continuous representation is that here we can implement process areas in any way we want but in continuous representation we can only implement the process areas in CMMI designated fashion. (Persse, James R., 2006)
6. Conclusions
The below tables summarize about all the process improvement techniques that are discussed above.Table 1. Process Improvement Techniques 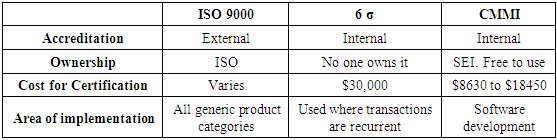 |
| |
|
The above-mentioned process improvement techniques are used to improve the existing process but if they are applied at the places where innovative is most important thing then they won’t produce good results as quality and innovativeness are always inversely proportional.
References
[1] | S. M. Metev and V. P. Veiko, Laser Assisted Microtechnology, 2nd ed., R. M. Osgood, Jr., Ed. Berlin, Germany: Springer-Verlag, 1998. |
[2] | Bacal, Robert. Why TQM Fails? Retrieved 12, June 2007 from http://performance-appraisals.org/Bacalsappraisalarticles/articles/whytqm.htm. |
[3] | Deming W, Edward. The W Edward Deming Institute. Retrieved 12, June 2007, from http://www.deming.org/. |
[4] | Dvir. Ron, Evans Stephen, A TQM Approach to the Improvement of Information Quality retrieved 12, June 2007 from http://web.mit.edu/tdqm/papers/other/evans.html. |
[5] | Green Larry, (December 2003). A Simplified TQM Diagnostic Model. Retrieved 12, June 2007 from http://www.skyenet.net/~leg/tqm.htm. |
[6] | Hackman, J. Richard, Wageman Ruth. (1995). Total Quality Management: Empirical, Conceptual, and Practical Issues retrieved 12, June 2007 from http://www.questia.com/googleScholar.qst?docId=5000391103. |
[7] | Hasmi, Khurram, Introduction and Implementation of Total Quality Management (TQM) Retrieved 12, June 2007 from http://www.isixsigma.com/library/content/c031008a.asp. |
[8] | Juran, Joseph M. (2002). Total Quality management. Retrieved June 4, 2007 from ebrary database. |
[9] | Persse, James R. (2006). Process improvement essentials: CMMI, ISO 9001, Six Sigma. Sebastopol, CA, USA: O'Reilly. |
[10] | Seaver, Matt (2001). Implementing ISO: 2000. Retrieved June 4, 2007 from ebrary database. |
[11] | U Prakash Kumar. Defining Quality Retrieved 12, June 2007, http://www.aifdonline.com/enew/Sep06/Sep06p4.htm. |
[12] | Waxer, Charles. (2007). What is Six Sigma certification. Retrieved June 9, 2007 from http://www.isixsigma.com/library/content/c010827b.asp. |
[13] | Quality-Based Problem-Solving / Process Improvement Retrieved June 5, 2007 from http://www.brecker.com/quality.htm. |
[14] | Hammett. The Philosophy of TQM An Overview. Retrieved from http://www.engin.umich.edu/class/eng401/003/LCNotes/phil.pdf. |
[15] | Juran, Joseph M. (2002). ISO 9000 Family of International Standards. McGraw-Hill Professional Book Group Retrieved (June 4, 2007) [ebrary] database from http://jzi6.cn/NwGLX6. |
[16] | International organization for standardization. Retrieved June 11, 2007 from http://www.iso.org/iso/en/aboutiso/introduction/index.html#two. |
[17] | Bamford, Robert. Auerbach Publisher, Incorporated. SO 9001:2000 for Software and Systems Providers: An Engineering Approach. Retrieved 12, June 2007 from Ebrary database. |
[18] | Beth, M., Konrad, M.C. and Shrum, S. Cmmi: Guidelines for Process integration and Product Improvement. USA: Addison-Wesley. |