Mohd Hudzari Haji Razali 1, Noordin Asimi Mohd Noor 2, Nor Idayu Othman 1, Hamim Izuan Hamdan 1
1Faculty of Agriculture and Biotechnology, Universiti Sultan Zainal Abidin, Terengganu, 21300, Malaysia
2Faculty of Innovative Design and Technology Universiti Sultan Zainal Abidin, Terengganu, 21300, Malaysia
Correspondence to: Mohd Hudzari Haji Razali , Faculty of Agriculture and Biotechnology, Universiti Sultan Zainal Abidin, Terengganu, 21300, Malaysia.
Email: |  |
Copyright © 2012 Scientific & Academic Publishing. All Rights Reserved.
Abstract
Transport could be considered an essential factor in improving agricultural productivity. An improved transportation helps to reduce spoilage and wastage, empower the farmers as well as having a positive impact on their productivity, income and employment. In this study, the main component in the kit is a brick-shaped computer control programming called the NXT brick. It can take input from one to four sensors and could be controlled by up to three motors, via RJ12 cables, very similar to but incompatible with RJ11 phone cords. The experiment was then successfully conducted. The tyre chosen should not be too narrow or too wide. The effect of a machine on the soil depends on the load on the wheel and the ground pressure it exerted. It is important to note that a high load carrying capacity can be achieved by using a larger tyre and/or a tyre that is inflated at high pressures. For machine weight factor, three weights of load had been loaded into the NXT robot tractor and the result obtained was analysed. The result proved that appropriate tyre size selection is important in reducing soil compaction. In overall, the NXT robot tractor acts as a two wheel drive tractor since the there is insufficient servo motor port to connect with to make it acts as a four wheel drive tractor.
Keywords:
Mechatronics , Agriculture Vehicles , NXT Robot Tractor , Sensor , Wheel Design
Cite this paper:
Mohd Hudzari Haji Razali , Noordin Asimi Mohd Noor , Nor Idayu Othman , Hamim Izuan Hamdan , "Mechatronic Application for Agriculture Mechanization Analysis and Education", Software Engineering, Vol. 2 No. 4, 2012, pp. 106-111. doi: 10.5923/j.se.20120204.03.
1. Introduction
Beginning in the mid-1800's, the introduction of mechanization to basic agricultural tasks greatly increased the productivity of farm, allowing a single farm to produce food for a greater number of people. The essentialness of agriculture shown within the righteous book of Al-Quran which is there are about eighty three sentences mentioning about agriculture as indicated for the benefit to mankind. Changes in agriculture leading to crop diversification towards horticulture, animal husbandry fishery, forestry and on-farm agro-processing are going to bring in greater degree of mechanization[1,2]. Transport is considered as an essential factor in improving agricultural productivity. It improve quality of life of the people, creates market for agricultural produce, provides interaction among geographical and economic regions and build up new areas to economic focus. In the past, agricultural mechanization in developing countries has been much criticized since it is often failed to be effective, and was blamed for exacerbating of rural unemployment and lead to other adverse social effects[3].Malaysia was covered with 168,135 hectare of BRIS[Beach Ridges Interspersed with Swales] soil in Malaysia. It was found in the state of Terengganu[67,582.61 hectares], Kelantan [17,806.2 hectares], Pahang[36,017.17] right down along the coast to west coast of Johore and was known as a problematic soil in Malaysia since it lacks in many aspects[4]. Previous studies showed it to be too sandy, weakly structured, having low nutrient and water retention capacity, limited ability to support plant growth and having a relatively high soil temperature[3,4]. In BRIS soil, only vegetable, tobacco, cashew nut, and short term crop can be grown with proper system since it is categorized as sandy coastal soil and not fertile due to lack of organic. These problematic structure of BRIS soil also causes trouble during operation system was done by the weight machine since the structure of the BRIS soil itself which is very loose[4]. The increased weight of machines, combining with changes in tillage systems pose a threat to the soil structure. Compaction of soil causing a reduction in pore space since the packing state of the soil particles was altered. The development of agricultural transportation in BRIS soil face difficulties in operation system since it is too sandy and weakly structured. The increased weight of machines, combining with changes in tillage systems pose a threat to the soil structure. Inappropriate selection of tyre size, machine weight and thread pattern causes the machine failing to work effectively.
1.1. Objective of Study
This project will focus on the new approaches to increase the effectiveness of agricultural transportation in BRIS soil i.e the selection of appropriate tyre size , thread pattern and machine weight, to reduce soil damage. This study is also important in the development of agricultural transportation in BRIS soil. An improved transportation helps to reduce spoilage and wastage, empower the farmers as well as having positive impact on their productivity, income and employment. The main objectives for this project are;• To discover the common problems faced during handling machine in BRIS soil i.e tyre size, machine weight and thread pattern ;• To model a tractor and designing the tyre that can work effectively in BRIS soil and reduce soil damage[soil compaction].
2. Literature Review
The main component in the kit is a brick-shaped computer called the NXT brick. It can take input from up to four sensors and control up to three motors, via RJ12 cables, very similar to but incompatible with RJ11 phone cords. The brick has a 100x64 pixel monochrome LCD display and four buttons that can be used to navigate a user interface using hierarchical menus. It also has a speaker and can play sound files at sampling rates up to 8 kHz. Power is supplied by 6 AA (1.5 V each) batteries in the consumer version of the kit and by a Li-Ion rechargeable battery and charger in the educational version.
2.1. Sensor
One of the most important components of a robot is the sensor. Much of the NXT set’s potential lies in its excellent selection of sensors. The primary purpose of a sensor is to allow the robot to interact with its environment and perform actions based on feedback from its surroundings[5].The NXT set includes three types of Digital Sensors: the ultrasonic sensor, the colour sensor and rotation sensors. An NXT digital sensor has two important characteristics. It has its own microcontroller, which enables the sensor to take readings of its environment itself (as opposed to the NXT doing it), and it sends its data to the NXT using I2C communication, which allows the sensor to operate independently and transmit only its readings to the NXT. For this experiment, ultrasonic sensor was used to measure the level of soil depth by using different tyre size , thread pattern and machine weight .
2.2. Ultrasonic Sensor
The Ultrasonic Sensor is one of the three sensors that gives vision to the robot and enables the robot to see and detect objects[6]. It could also be used to avoid obstacles, sense and measure distance, and detect movement. The Ultrasonic Sensor measures distance in centimetres and in inches. It is able to measure distances from 0 to 255 centimetres with a precision of +/- 3 cm. The Ultrasonic Sensor uses the same scientific principle as bats: it measures distance by calculating the time it takes for a sound wave to hit an object and return – just like an echo.
2.3. The Servo Motor Encoder (Rotation Sensor)
NXT robots can move in many different ways. They can grasp, race, walk, swivel and do much more. These capabilities come from using the NXT servo motors. Servo motors are different from other common Lego motors. They are interactive, meaning that they include a built-in Rotation Sensor or tachometer, to control the robot’s movements precisely. The Rotation Sensor measures motor rotations in degrees or full rotations[accuracy of +/- one degree]. One rotation is equal to 360 degrees, so if the motor is set to turn 180 degrees, its output shaft will make half a turn. For this experiment, the high speed of power[75%] was used since the structure of the soil that is very loose, and may lead the robot being stuck and the tyre remain sticking in the soil if the movement of tyre is set as slow
2.4. BRIS Soil
The Department of Agriculture of Malaysia has identified and recommended seven type of BRIS soil based on soil depth, drainage, and serial profile, namely Rusila, Rhu Tapai, Rompin, Rudua, Baging, jambu and Merchang. The classification system of American Department of Agriculture divided BRIS into two order, namely Entisol and Spodosol. Entisol is a young without podogenetic horizon. It is found near the sea and has high sand content. Spodosol, on the other hand is acidic soil with a sandy texture but unstructured with more humus[ acidic humus ] content. This is what differentiates soil types in a BRIS soil series. The BRIS soil series of Rompin, Rusila, Baging and Jambu are classified as sandy Entisol with a Quartz composition where only Rudua is included in the Spodosol order[7].The problematic structure of BRIS soil causes trouble during operation system and lead to the soil compaction.[4]. Compaction in this research refers to the soil structure damage which occurs due to machinery traffic. There are many factors that affect this machinery-induced compaction. For example soil type (texture, structure, OM content), soil moisture, level of cultivation or looseness prior to traffic, machine weight and tyre size. Loose soils, such as those cultivated deeply like BRIS soil, are more prone to compaction compare to undisturbed soils. In most cropping situations, we have limited control over many of these factors. However, the machinery operation can be controlled by diversify the machine weight, the level of traffic and, in particular, the tyre size fitted to machines[5].
2.5. The Effect of a Machine
As allevation of compaction by deep loosening is not satisfactory, prevention of soil damage is the best approach. The selection of appropriate tyre sizes is very crucial. Tyres must be chosen based on the ground pressure they exerted. The ground pressure required will largely depend on soil conditions. However, machine weight and traffic intensity also play a role. It is important to protect weaker soils and soils where minimum tillage is practiced. The effect of a machine on the soil depends on the load on the wheel and the ground pressure it exerted. The impact of a wheel load on the soil is represented schematically in Fig. 2. The pressure pattern which extends into the soil beneath the wheel was generated by wheel load. For a given soil condition (looseness, type, moisture), the extent and shape of this pressure pattern is determined by the wheel load and the contact area between the wheel and the ground. If the load on the wheel is fixed, a larger contact area (larger tyre) will reduce the ground pressure and, consequently, lessen the soil pressure[8].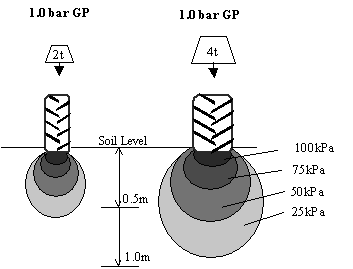 | Figure 2. Distribution of pressure stresses beneath a lightly loaded small tyre and a heavily laden large tyre exerting similar ground pressures[8] |
Theoretically, the major mechanization problems are greatly solved when there is a proper drainage. But in real life, even the existing drainage cannot and do not properly maintenance and hence , the proper drainage function cannot be achieved. So to overcome these problems, farm mechanization comes into picture[9]. Having a broader tyre and proper tyre track pattern is a good option provided the demand for the machine usage (i.e: economic field acreage etc) and the tyre availability & pricing is feasible. The use of double tyre concept to each side of the tractor , so still can use the original tyre & rim etc. Steering response is also improved, while vibrations and noise are considerably reduced,” he concludes.[10]. However, the weight of the tractor also needs attention. Even if the contact surface area had been managed to increase, but if the weight is increased, the contact pressure remaining the same. Then, the target still cannot be achieved[11].
3. Methodology
3.1. Materials
The software application used are :• NXT software[for programming NXT tractor robot], Solidworks software[for modelling tractor & simulate the tractor]Experimental and data collection :• Box, Sand, Scoop, Mini rake and Analytical balance, NXT tractor robot system components (as shown in Figure 3.1)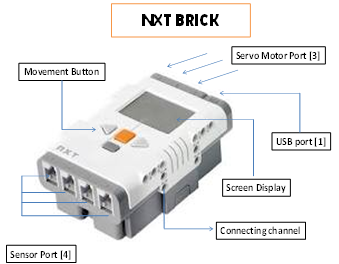 | Figure 3.1. NXT Brick components |
3.2. Experimental Programming
i. The NXT tractor robot was first programmed as shown in Figure 3.2 which is needed by using NXT software before loading it onto the sand for experiment.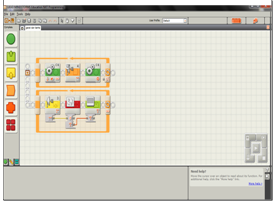 | Figure 3.2. LEGO NXT Robot programming |
3.3. Experimental Setup
i. Filled the 50cm X 30cm X 7cm box with the sand and levelled it.ii. Placed 5 sticks into the box as a check point where the reading will be recorded when the tractor robot moved on the soil.iii. For each rotation, 5 readings will be taken and the step was repeated for 3 rotations.iv. In this experiment, three major factors; tyre thread, tyre size and machine weight that cause difficulties to the machine operation in BRIS soil[loose soil] had been examined.v. In order to examine the effect of each of them, other factors need to be standardized in measurement. So, the design of LEGO NXT tractor needs to be modified.vi. The tractor was then placed onto the sand and moved as programmed. The level of soil compaction was detected by ultrasonic sensor that was attached parallel to the tyre and the readings appeared on the NXT robot screen.vii. Readings were taken at every check point[5 check points] indicated by the sticks that were located on the sand for one rotation. The step was repeated for 3 rotations and the average was calculated as shown in Figure 3.5.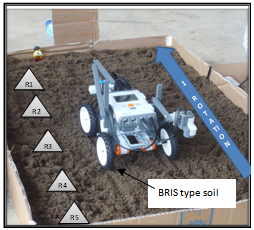 | Figure 3.5. How the readings were recorded |
All the data recorded was represented in the graph. The sinking of tyre into the soil indicates the starting of soil damage that will lead to the soil compaction. The shallower tyre sinks into the soil indicates the less soil compaction and vice versa. The tractor model then will be simulated and analysed to show the effect of the experimental factors to the soil compaction.
4. Results and Disscusion
The experiment then was successfully conducted and all the result obtained was recorded and interpret into the graph form. Figure 4.1 shows Comparison of tyre size against level of soil depth[cm]. According to figure 4.1, the narrow tyre shows the highest level of soil depth followed by the widest and wider tyre. The result proved that appropriate tyre size selection is important to reduce the soil compaction. Figure 4.2 show comparison of machine weight against level of soil depth[cm]. According to figure 4.2, NXT robot tractor with no load loaded on it shows the lowest level of soil depth, followed by NXT robot tractor with one load. While the NXT robot tractor that loaded with two loads showed the highest level of soil depth. Figure 4.3 show the comparison of tyre thread pattern against level of soil depth[cm]. For tyre thread factor, this experiment was focused on the selection of the rear tyre since it determines the effectiveness of the traction on the soil rather than the front tyres that usually standardized in pattern due to it’s functions for steering control. For this experiment, only two types of tyre thread pattern can be tested since there is insufficient tyre thread pattern that are identical in their size . Both of them were differ in their lugs design. Using the simulation and modelling study on the effect of tyre design and tractor analysis, the soil compaction is determined for controlling the plantation process in another agriculture activity. Mohd et al. used the concept of simulation and modelling for prediction agriculture process activity on realizing the smart farming practice[2,12].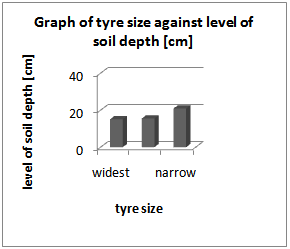 | Figure 4.1. Comparison of tyre size against level of soil depth[cm] |
 | Figure 4.2. Comparison of machine weight against level of soil depth[cm] |
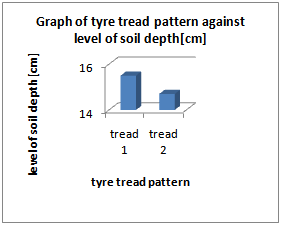 | Figure 4.3. Comparison of tyre thread pattern against level of soil depth[cm] |
According to figure 4.1, the narrow tyre shows the highest level of soil depth followed by the widest and wider tyre. The result proved that appropriate tyre size selection is important to reduce the soil compaction. The tyre that was chosen should not be too narrow or too wide. It is because in certain condition where the load on the wheel is fixed, a larger contact area (larger tyre) will reduce the ground pressure and, consequently, lessen the soil pressure without undue soil compaction[13]. According to figure 4.2, NXT robot tractor with no load loaded on it shows the lowest level of soil depth, followed by NXT robot tractor with one load. While the NXT robot tractor that loaded with two loads showed the highest level of soil depth. The result showed that the level of soil depth increased with the increasing of machine weight. It is because for a given soil condition (looseness, type, and moisture), the extent and shape of this pressure pattern is determined by the load on the wheel and the contact area between the wheel and the ground. A small load only requires a small contact patch, the effect of its load is easily dissipated sideways in the soil. A very large load, however, requires a much larger contact patch which effectively constrains the sideways dissipation of the force resulting in a deeper impact[8].For tyre thread factor, this experiment was focused on the selection of the rear tyre since it determines the effectiveness of the traction on the soil rather than the front tyres that usually standardized in pattern due to it’s functions for steering control. For this experiment, only two types of tyre thread pattern can be tested since there is insufficient tyre thread pattern that are identical in their size. Both of them were differ in their lugs design. Based on the figure 4.3, thread 1 shows higher level of soil depth compare to thread 2. Comparing these two types of tyre thread pattern, thread 1 consist less lugs with deeper lugs depth compare to thread 2. So, it can be conclude that tyre thread that possess more lugs and shallow depth lugs provide better traction in loose soil. In overall, the result obtained fits the theoretical facts that had been made from the previous research. Machinery traffic and foot trampling in loose soil areas can result in varying levels of soil compaction. Increased soil compaction results in higher soil bulk density (mass/unit volume), which can reduce water infiltration, reduce soil surface strength, increase runoff and erosion potential, and reduce site productivity[14, 15].
5. Conlusions
In understanding the effects of compaction to the BRIS Soil, three important factors had been examined; tyre size, thread pattern and machine weight. For this experiment, NXT robot tractor model was introduced instead of the actual tractor that was used in the field. At first, the NXT robot tractor was programmed to move in the BRIS Soil, which is the actual soil type that was examined in this experiment. However, the problem occurred when the narrow tyre faced difficulty to move on the BRIS Soil due to the size of the soil particle which is too big and do not fit with the ratio of NXT tractor tyre which is smaller in size. The situation become worst when the soil particle remain sticking in the hole space of servo motor and cause the NXT robot tractor stuck and failed to move anymore.Alhamdulillah in overall study, the NXT robot tractor acts as a two wheel drive tractor since the there is insufficient servo motor port to connect with to make it acts as four wheel drive tractor. Since the front tyre did not powered by the servo motor and only ride for steering control, it cause the heaping of the soil once it move for a distance. To solve this problem, the NXT robot tractor then re-programmed by increasing the speed power from 50% to 75% to suit with the deeply loose of soil structure and prevent the tyre from remain sticking in the soil and cause other adverse effects.
References
[1] | Razali M.H., Wan Ismail W.I., Ramli A.R. Sulaiman M.N. and Harun M.H. (2009), "Development of Image Based Modeling for Determination of Oil Content and Days Estimation for Harvesting of Fresh Fruit Bunches," Int. Jr. of Food Eng, Vol. 5(2), pp 1633 – 1637. |
[2] | Mohd. Hudzari Razali,Wan Ishak Wan Ismail, Abd. Rahman Ramli, Md. Nasir Sulaiman, and Mohd. Haniff B. Harun (2011a). “Prediction Model for Estimating Optimum Harvesting Time of Oil Palm Fresh Fruit Bunches Jr. Of Food, Agric. & Env., 9(3&4), pp.570-575. |
[3] | Adrianus, G.Rijk. (2011) Agricultural Mechanization Strategy. Retrieved 27, 2011 fromhttp://www.unapcaem.org/publication/CIGR_APCAEM_Website.pdf |
[4] | Anim . (2010) .BRIS soil . In Anim Agriculture Technology. Retrieved July 10,2010, from http://animagro.blogspot.com/ 2010_07_01_archive.htm |
[5] | Mohd. Hudzari Razali, Wan Ishak Wan Ismail, Md. Nasir Sulaiman, Napsiah Ismail and Rashid Sharif (2010), “Computer Simulation Technique for Two Degree of Freedom Agriculture Robot Arm”, International Journal of Computational Intelligence Techniques, Vol. 1(2), pp. 15-17. |
[6] | Razali M.H., Wan Ismail W.I., Ramli A.R. and Sulaiman M.N. (2008), "Modeling of Oil Palm Fruit Maturity for the Development of an Outdoor Vision System," Int. Jr. of Food Eng. Vol. 4(3), pp 1396-1396. |
[7] | Mohd Ekhwan Hj Toriman, Mazlin b. Mokhtar, Muhammad Barzani Gazim, Norazlina Abd Aziz .[2009] . Analysis of the Physical Characteristics of BRIS soil. Research Journal of Earth Science, 1-2. |
[8] | Braunack, M.V. 1986. The residual effects of tracked vehicles on soil surface properties. Journal of Terramechanics 23(1): 37-50. |
[9] | W.I.W.Ishak and R.M Hudzari (2010). “Image Based modeling for oil palm fruit maturity prediction”. Jr. of Food, Agric. & Env., Vol.8 (2): 469-476. |
[10] | Philip J Wright . (2011). Scientific Trial Highlights Varying Impact on Soil Compaction Between Different Harvester Tyres. Press Release, Retrieved July 7 2011. |
[11] | Muhamad Salleh, Forest Research Institue malaysia (FRIM), Kuala Lumpur Malaysia, personal communication, August 11,2011 |
[12] | Mohd. Hudzari Razali,Wan Ishak Wan Ismail, Abd. Rahman Ramli, Md. Nasir Sulaiman, and Mohd. Haniff B. Harun (2011b). “Technique on Simulation for Real Time Oil Palm Fruits Maturity Prediction”, African Journal of Agriculture Research. Vol 6(7): pp.1823-1830. |
[13] | Hamid, A. , Ahmad, D. ,& Rukunuddin, I.H. (2010). Performance of sweet potato transplanting machine on mineral and bris soils. : Agricultural Mechanization In Asia, Africa And Latin America , V.41(1):55-59 |
[14] | Marlia Mohd Hanafiah, Jumaat Hj Adam, Mohd Barzani Gasim, Sahibin Abdul Rahin and Nurulhuda Edy Muslim, 2004. Management and Maintenance of Agriculture Activity in BRIS Soil . (In Malay) In Norhayati Mohd Tahir, Nakisah Mat Amin and Kamaruzzaman Yunus (eds). KUSTEM Third Annual Seminar on Sustainability Science and Management 2004. pp 265-268. Kuala Terengganu. Kolej Universiti Sains dan Teknologi Malaysia. |
[15] | Rooney, D., M. Stelford, and D. Landolt. Undated. Site-Specific Soil Compaction Mapping Using a Digital Soil Penetrometer. Site-Specific Management Guidelines (SSMG) –Potash and Phosphate Institute(http://www.ppi-far.org/ssmg). |