Yeshiareg Temtime , Worku Jimma , Mniyichel Belay
Department of Information Science, Jimma University, Jimma, Ethiopia
Correspondence to: Worku Jimma , Department of Information Science, Jimma University, Jimma, Ethiopia.
Email: |  |
Copyright © 2017 Scientific & Academic Publishing. All Rights Reserved.
This work is licensed under the Creative Commons Attribution International License (CC BY).
http://creativecommons.org/licenses/by/4.0/

Abstract
This study identified knowledge management practices that exercise in Dire Dawa national and Ture cement factories by examines the relationship between knowledge management practices and organizational productivity. Qualitative and quantitative approach was used to investigate the existing gaps. To carry out this investigation a descriptive research method was used. Purposive and simple random sampling was used for selected 143 employees. Questionnaire, interviews and observation check list were used as data collection instrument. From the present study knowledge creation, knowledge capture, knowledge share and knowledge application are knowledge management practices that exercise in the selected cement factories and the study area used knowledge management practices for business process achievement. The relationship between productivity and available knowledge depends on people, ICT facility and organizational existing policy available in the factories. The limited functionality of ICT facility, the non functionality of knowledge management policy and the limited capacity of knowledge expert are problems that hinder implementation of knowledge management practices in the factories.
Keywords:
Knowledge Management Practices, Organizational Productivity, Productivity and available Knowledge
Cite this paper: Yeshiareg Temtime , Worku Jimma , Mniyichel Belay , Knowledge Management Practices on Product Improvement for Dire Dawa National and Ture Cement Factories in Ethiopia 2015; Cross-Sectional Survey Method, Science and Technology, Vol. 7 No. 3, 2017, pp. 61-71. doi: 10.5923/j.scit.20170703.01.
1. Introduction
Most companies like banks, cement industry, health center and university library have knowledge management (KM) inside their organizations. However, KM in organizations reflects the identification and use of collective knowledge (Churchill, 1999). KM also a trans disciplinary field aimed at doing what was needed to get the most out of knowledge resources (DeVaus, 2001). According to Smith and Mills, managing knowledge resources effectively is vital for individual and the organizations that want to utilize their knowledge assets for competitive advantage in an organization with knowledge management. Various authors argued that nowadays, knowledge management practices (KMP) provide companies with a competitive advantage as a result of their impact on the organization’s ability to act in more efficient, sustain able and innovative ways. Through the practices of knowledge management, an organization focuses on the systematic exploitation and reuse of knowledge. Jennex (2008), also studied about measures of KMP outcomes in terms of organizational performance as enhancement of product and service quality; productivity; competitive capacity and position in the market; and customer satisfaction; employee satisfaction; knowledge sharing; transparency and its retention. Addicott and Ferlie, stated that many large companies and non - profit organizations have resources dedicated to internal KMP efforts, often as a part of their business strategy, information technology, or human resource management departments. According to Meron, in Ethiopia cement factories the production capacity utilization rate in the country is below 50%, so this level of capacity utilization is substantially low compared to global average of 60 – 70% or recommended acceptable optimum production capacity utilization rate that range between 80 – 85%.Problem Statement In Ethiopia, there is a recognizable competition among the existing cement factories by improving productivity and quality of the products through the application of KMP. However, Dire Dawa national and Ture cement factories are affected by the problem of lack of implementations of KMP, shortage of information about organizational knowledge source, skill gap on KM expert, Un understandable KMP outcomes, unwisely use of information and invisible relationship among KMP and product process. So this area needs research in Dire Dawa national and Ture cement factories. Therefore, this research was initiated with the main aim to investigate KMP for product improvement on Dire Dawa national and Ture cement factories. According to Maingi, (2007) study the need to develop KM as supplementary measure of the organizational profitability, sustainability and continuity, outside the usual measures. In this study one of the main issues that employees are still not aware is what KM is all about, and this issue need research according to the current selected area. The study by Mosoti and Mesheka, (2010) focused on KMP in organizations revealed that, most of the challenges experienced by organizations were how to create and implement KMP as part of organizational culture, organizational strategy and organizational leadership; so, research must be done in the current study area. Ruggles in 1999, Knowledge sharing depends on the habit and willingness of the knowledge worker to seek out and be receptive to these knowledge sources and Fugate in 2009 conducted a study in a logistics operations context and prove the existence of a strong positive relationship between a KMP and operational and organizational performance. But, by this study, justified as there is no understanding on how different KMP affect organizational performance. Therefore it is necessary for this research to answer the following research question:Research questions1. What is the current status of KMP in the selected cement factories?2. What is the contribution of KMP on product improvement in the selected cement factories?Objectives of the StudyThe main objective of this study is to assess knowledge management practice for product process improvement in Dire Dawa national and Ture cement factories and the specific objectives of this research are as follows:-ü To identify the current status of KMP available in the selected cement factories.ü To identify the contributions of KMP on productivity in the selected cement factories.Significance of the studyThe significance of the present research includes identify KMP exercise and show KMP helps organizations (private and public) sectors, manufacturing industry and business process in problem solving and supporting decision making. It also create employee’s understanding about KM within organizational information context by identifying and defining the main types of KMP exercise by pointing out the critical factors of KMP and find suitable ways of management of knowledge in that context.KMP helps to remove resource constraint, decrease cost of products and create innovative applications for mature products that make companies move ahead of their competitors. This research gives information for all community of the organization about KM as supplementary measure of the organizational profitability, sustainability and continuity with challenges experienced by organizations to implement KM inside their factories. This study was also very significant in a number of ways that include help for top managers of the factories have clear understanding about KM and KMP in the factories also takes the necessary measures to improve individual and organizational competitiveness.
2. Related Work
Knowledge management practice in industryKMP refers to practical aspects of KM, given that manufacturing is the organizations nature of business, there is a link between KMP and operational benefits which suggests that the main reason is because the role of KM is aimed at improving manufacturing processes which are embedded in the organization’s business strategy. KMP improved their industries operational activity in a variety of ways, such as reducing the design cycle time, lead time, cost, reducing time product- to- market, and improving the quality of product. Rod Coombs (1998), studied in CRIC working paper no 6 on KM but the main interest has been in KMP which contributes directly to the creation of novel business propositions, these practices are concerned primarily with the accumulation, analysis; management and dissemination of evolving stocks of knowledge in a firm, covering three main areas those include, technology; knowledge about technologies used and developed within the company, as well as those available and under research in other companies, markets; market- based knowledge concerning: the requirements of customers, their behavior and the market opportunities which might be feasible in the future, current offerings and plans of competitors and regulatory and standards developments affecting all players and company processes; knowledge about internal administrative, technical management operations through which the organization identifies and delivers products and services.The study conducted by Wiig in 1993 also considers KM in organizations, the study cover from three perspectives, each with different horizon and purposes; business perspective: focusing on why, where, and to what extent the organization must invest in or exploit knowledge. Strategies, products and services, alliances, acquisitions, or divestments should be considered from knowledge- related points of view, management perspective; focusing on determining, organizing, directing, facilitating, and monitoring knowledge- related practices and activities required to achieve the desired business strategies and objectives and hands- on perspective :focusing on applying the expertise to conduct explicit knowledge- related work and tasks. Girbert and Probset (1969), studied on practical KM in an organization, the first organizational practice is KM identification that means organization identifies what knowledge and experience exist both inside an d outside their walls. According to them knowledge development, knowledge distribution, knowledge use and knowledge preservation are KMP in industries. Khalid 2009 studied KMP in united Arab Emiret (UAE) Bank industry by using explanatory research methods and the study was conducted in UAE, the concern with his study depend on KMP today and future in the bank industry. The results of Khalid study show in Bank industry KMP, today is infant stage, but he suggests in future by using KM enablers KMP in Bank industry rich high stage.Knowledge management in EthiopiaKM in Ethiopia is not yet developed well but there are some related works in this area like the study of Ermias (2011) on innovative approach of KM in agriculture the case of IPMS by using theoretical approach in 10 pilot districts of 4 regional states of the country. The results of his study shows IPMS project followed systematic and step - wise approaches of KM and capacity development by support of various ICT and non ICT tools that facilitated multidirectional knowledge flows, empowerment of practitioners and linkage creation to improve productivity, profitability and sustainability of market oriented agricultural development. According to Ermias the major tools and processes are establishment of agricultural knowledge centers for up to date and relevant information resource delivery, enhancement of program delivery and technical skills through participatory training; establishing partnership with various stakeholders and institutions at all levels and developing a web based platform, Ethiopian agriculture portal, www.eap.gov.et, for availing agricultural resources relevant to Ethiopian agriculture. A lesson from IPMS on implementing the above components with the need for an overall understanding of knowledge as a critical ‘input’ to agricultural development being internalized among program implementers at all levels and importance in building capacity of actors, not only to have implementers but also to have those who forge linkages, identify need s and manage partnership processes. Another study done in Ethiopia was KMP in development and humanitarian aid organization in Ethiopia by Hermella, 2000 the research done by using qualitative research methods via online survey. The results of this study depend on Kruger & Synman KM maturity assessment instrument and the general KM maturity model (G- KMMM) by Pee & Kankanhalli provides a useful framework through which to assess knowledge management. According to this author, organization is aware of and has t he intention to manage its organizational knowledge, but it might not know how to defined basic infrastructure is put in place to support KM to managed, KM initiatives are well established in the organization and optimized where KM is adequately integrated into organizational processes. Her result also prove main pillars of the G- KMMM and Kruger and Synman in the study area that ICT as an enabler of KM and information management's role for KM in an organization describe the technological readiness of the organization. Similarly formulation of KM principles, policy and strategy in an organization and 'implementation of KM in an organization' touch upon the processes involved for the smooth implementation of KM and facilitator are essential for establishing a successful KM initiative in aid organization. According to Hermella result staff and knowledge workers in these organizations are actively involved in sharing information and knowledge resources when required for speeding up working processes. In another way her result shows absence of proper organizational guidelines on knowledge sharing, lack of knowledge of what colleagues need and shortage of time and resources to facilitate knowledge sharing.Knowledge management practice with organizational product processProductivity means improve organizational performance by becoming more efficient in specific areas; this is done by applying specific methods, tools, metrics, knowledge and the end result is organizational excellence. Productivity also evaluated in terms of the output of an employee in a specific period of time. The success of any organization relies upon the productivity of its workforce; KM with employee productivity is an important consideration for businesses (Margaret, 2014). Study conducted by Amir ashka in 2012 on the relationship between KM and productivity in teaching hospitals of Hamedan, Iran by using multi _stage random method and the result of this study showed that KM in the healthcare organizations and especially in the hospitals can have a main role, the guidance and allocation of the human resources, information, equipment and proper decision making along with conditions and needs of the organizations.
3. Methodology
This research used cross- sectional survey method and questionnaire, interviews and observation check list used as a data collection instrument. This research analyzed by using a descriptive statistics like percentage, means and standard deviation. This study was used 143 employees as a sample population, they are the once directly involve in the KMP and also using the ICT facilities for the purpose of KM.
4. Results and Discussion
Knowledge management practices in Dire Dawa and Ture cement factoriesThe respondents answer to different questions posed to them for elicit information about KMP is depicted in Figure 4.1 below: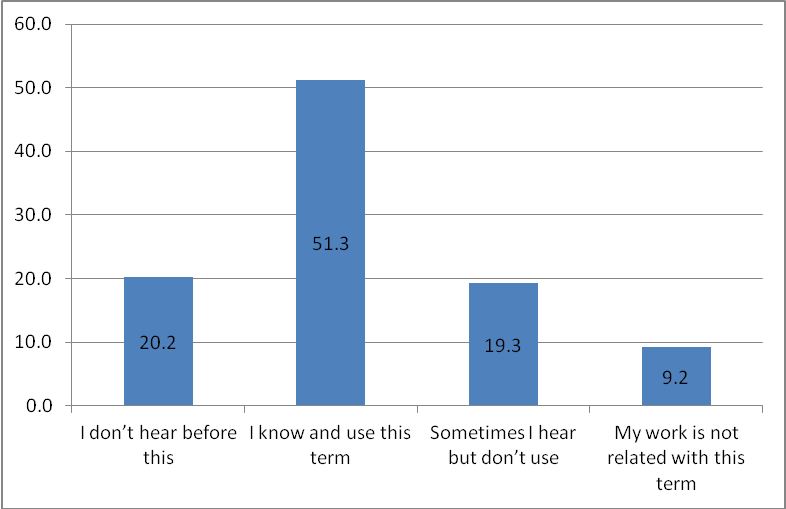 | Figure 4.1. Awareness of knowledge management practice |
In the case of understanding about the knowledge management practice, respondents answered, “I know and use this term” were 61 (51.3%) followed by “I don’t hear before this” 24(19.3%). These imply that majority employee’s work in Dire Dawa national and Ture cement factories were familiar with the term knowledge management practice and use in the work place when they are need. However, some of the employees who work in both factories did not hear or were not familiar with the term and meaning of knowledge management practice in their workplace.The other indicator of knowledge management practice in Dire Dawa national and Ture cement factories is know about the availability of knowledge management in those factories. Summary of the response about knowledge management availability is presented in Figure 4.2: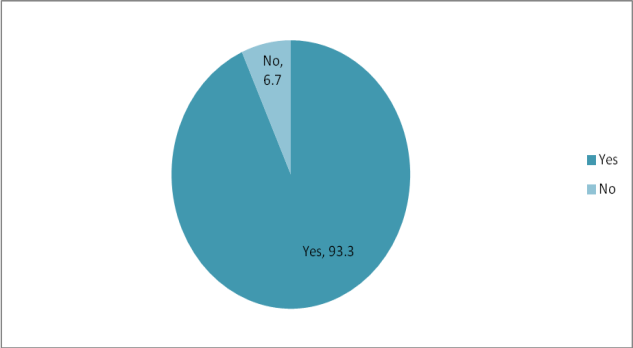 | Figure 4.2. Knowledge management availability |
Figure 4.2 shows that the vast majority of the respondents answered yes the question on “the availability of knowledge management practice” in both factories. 111(93.3%) of the respondents were answered knowledge management practice was available in Dire Dawa national and Ture cement factories.Professional understanding about knowledge management practice is another indicator of knowledge management practice in those selected factories. The summary of the responses for those questions are presented in Figure 4.3: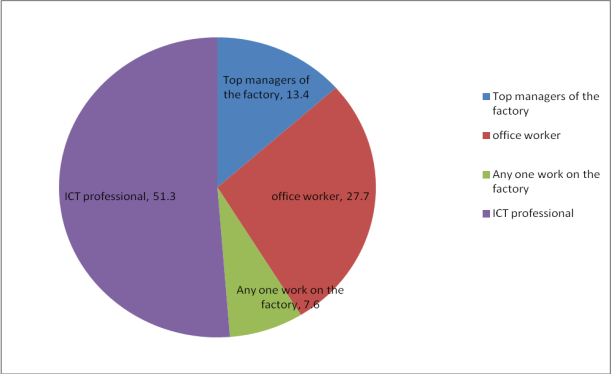 | Figure 4.3. Professional understanding of knowledge management practice |
As depicted in figure 4.2 above, Knowledge management practices were available both in Dire Dawa national and Ture cement factories but figure 4.3 show awareness about knowledge management practices were different in the work environment or profession, according to the respondents 61(51.3%) ICT professionals have more awareness about the term and purpose of knowledge management practice followed by most office workers with 33(27.7%) value. This shows both in Dire Dawa national and Ture cement factories, ICT professionals have better understanding about the meaning and the benefit of knowledge management and most offices workers are familiar with knowledge management practice.Knowledge creation, knowledge capture, knowledge share and knowledge application are knowledge managmment practice avaliable in both Dire Dawa natinal and Ture cement factories. The responses are summarized in Figure 4.4 below: 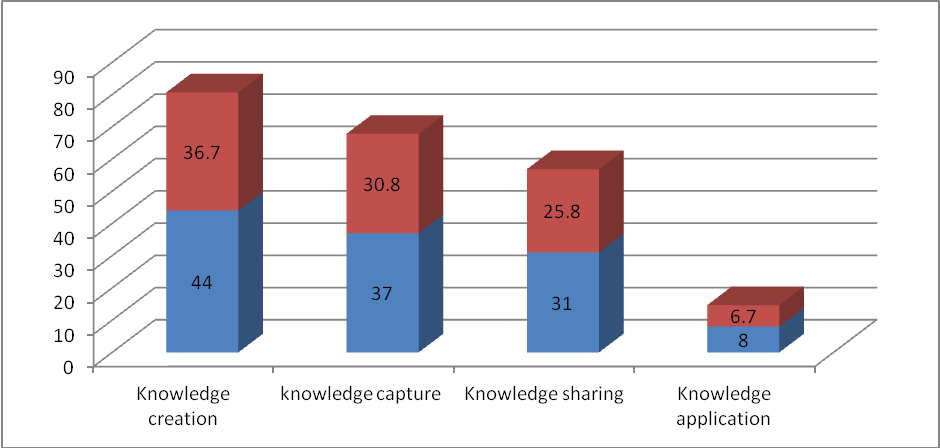 | Figure 4.4. Types knowledge management practice availability |
As depicted in the figure above, the question “types of KMP availability”, according to respondents knowledge creation, knowledge capture, knowledge share and knowledge application were types of knowledge management practice available in both factories with the values 36.7%, 30.8%, 25.8% and 6.7% respectively. From this result it is possible to say that KMP was well exercise, except knowledge application.Knowledge management practice was available in both Dire Dawa national and Ture cement factories but those practice is different in Dire Dawa national and Ture cement factories. The responses are summarized in Figure 4.5 below: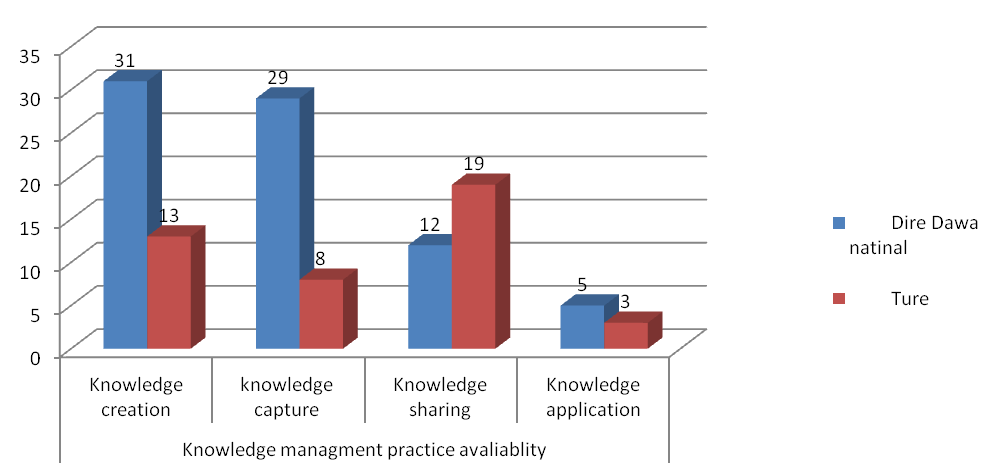 | Figure 4.5. Availability’s of knowledge management practice by the work place |
Knowledge management practices, available in the employee’s workplace are varying from Dire Dawa national to Ture cement factories. Frequency of knowledge management practice available in Dire Dawa national and Ture cement factories were difference, from the respondents opinion knowledge creation and knowledge capture were the most understandable and useable KMP available in Dire Dawa national but knowledge sharing and knowledge creation were also knowledge management practice more familiarity with employees in Ture cement factory in day to day activity. From the above respondents result knowledge application doesn’t create familiarity with employees work in both Dire Dawa national and Ture cement factories. Benefit of knowledge sharing, level of knowledge sharing, common practice available in the factory and factory’s Common activity are activity that indicate knowledge management practice in Dire Dawa national and Ture cement factories. Summaries of the respondents response is presented in table 1 below: Table 1. Knowledge management practices in the cement factories by considering different activities 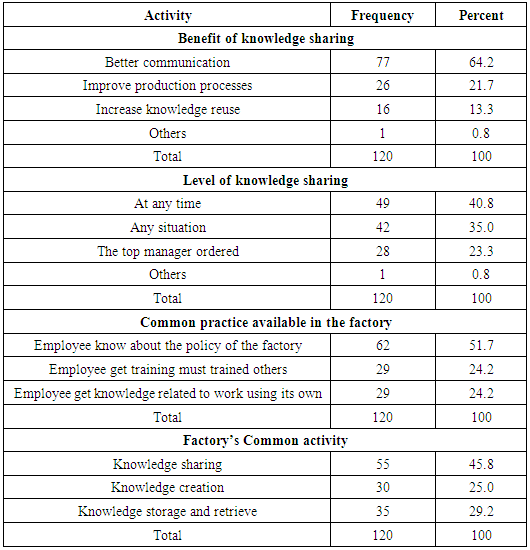 |
| |
|
From the above table 1 Knowledge sharing is one of knowledge management practice available in Dire Dawa national and Ture cement factories. The question posed to know the “benefit of knowledge sharing practice” in cement factories. For the benefit of knowledge sharing majority of the respondents answered knowledge sharing for better communication 77(64.2%) followed by improving production processes 26(21.7%). From the result, it can be observed that knowledge sharing is the best mechanism to create better communication between employees this also improves production process. Regarding to knowledge sharing level in the factories, 49(40.8%) of the respondents say at any time employees are willing to share their knowledge followed by 42(35.0%) that answered in any situation employees also willing to share their knowledge. From this it can be said that knowledge sharing rich a culture that shows at any time, in any condition the employees working in Dire Dawa national and Ture cement factories were willing to share their knowledge. The respondents were asked to give their opinion about common practices available in both factories. The result presented in Table 1 above showed that employees know about the policy of the factory, employee get training must trained other employees and employee get knowledge related to work using its own work are common practice exercise by all employees in day to day activity both in the case of Dire Dawa national and Ture cement factories. According to the respondents every employee knows about the policy of the factories and employee get training must train other are common practice available in the factories with the value 62(51.7%) and 29(24.2%) respectively. This shows that majority of employees knows about the policy available in the factory because this is common practice and familiar with employees day to day activity. From respondents’ opinion knowledge sharing 55(45.8%), knowledge creation 30(25.0%), knowledge storage and retrieve 35(29.2%) are most common activity in both Dire Dawa national and Ture cement factories. Even if knowledge creation, knowledge capture, knowledge share and knowledge application are knowledge management practice available in those factories, knowledge sharing, knowledge creation, knowledge storage and retrieve also common activity available and familiar with majority employees in both factories. Knowledge sharing is culture and common activity practice both in Dire Dawa national and Ture cement factories. Examining respondent’s opinion about knowledge management practice in both factories by identifying the respondent level of satisfaction and summaries of the respondents’ response is presented in the following table 2 below: Table 2 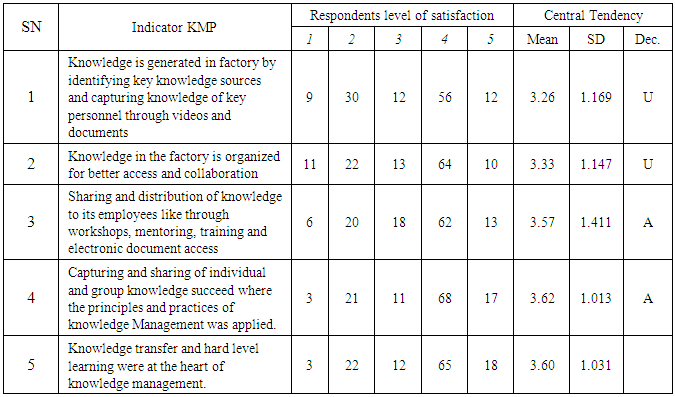 |
| |
|
Knowledge sharing mechanism and knowledge generated by identifying knowledge source, knowledge in the factories organized for better access and collaboration, sharing and distribution of knowledge to its employees through workshops, mentoring, training and electronic document access, capturing and sharing of individual and group knowledge succeed where the principles and practices of knowledge management was applied and knowledge transfer with hard level learning were at the heart of knowledge management were all knowledge management practice indicators listed in the above table was scored undecided and agree with the mean value 3.26, 2.33, 3.57, 3.62 and 3.260 respectively because the mean value score 3 to 3.49 close to 3 that is undecided and the score line 3.5 to 4 close to 4 that is agree.In the case of “knowledge generation by identifying knowledge source”, most respondents’ decision was neither undecided nor agree but close to undecided with the mean value 3.26. Employees, written document, external document and electronic document are sources of knowledge in the case of Dire Dawa national and Ture cement factories. The result confirms that the mean value 3.26 line between undecided and agree ,this shows there are respondents that is not identify knowledge source that is available in the factories but identifying knowledge source available in the factories contribute for better result and product improvement. For the question “knowledge was organized for better access and collaboration” respondents decision was neither undecided nor agree but close to undecided with the mean value 3.33, this indicated that there is confusion on the use of organized knowledge. The main benefit of organized knowledge in the factories is for better access. Due to this organized and accessed knowledge in the factories have better impact for organizational productivity and also increase productivity. “Based on knowledge sharing mechanism” most respondents’ decision was neither undecided nor agree but close to agree with the value of mean 3.57. Workshops, training and electronic document access are the mechanism to use for knowledge sharing in Dire Dawa national and Ture cement factories. This showed that knowledge sharing is one of knowledge management practice in both factories and those factories has knowledge sharing mechanism to creating better organizational culture for product improvement. “Principles and practice of knowledge management” with the grater mean value 3.62, the respondents’ decisions was neither undecided nor agree but close to agree, the success of capturing and sharing individual and group knowledge in organization by applying the principle and practice of knowledge management for product improvement. The decision of respondents in one of the availability of knowledge management practice indicator that is “knowledge transfer is the heart of productivity” was close to agree. According to the respondents’ knowledge transfer is common activity available in both factories and also knowledge transfer was the heart of productivity by increase quality of product in the factories. From table 4 the researcher summarized that in Dire Dawa national and Ture cement factories knowledge management practice has its own principle and practice, knowledge transfer is the heart of productivity with knowledge sharing mechanism in the factories and knowledge in the factories also organized for better access and collaboration with others knowledge by identifying knowledge source available in the factories all this gives potential or positive impact on product improvement. Employees awareness about KMP, availability of KMP, professional understanding about KMP, types of KMP available in the factories, benefit of KMP, level of KMP inside the factories and common practice with common activity practice by employees inside the factories were discuses in the point of KMP in Dire Dawa national and Ture cement factories. All those the above indicator shows the existence and use inside the factories but the researcher wants to know about whether those KMP indicators have relation with organizational productivity. The researcher cheeks some of those KMP indicators with organizational productivity by doing Pearson correlation and this correlation is presented in table 3 below:Table 3. Pearson correlation between understanding of KMP and productivity 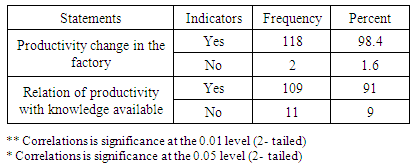 |
| |
|
From the above table 3 the researcher wants to see the relationship between people understanding of KMP and organizational productivity, all asterisks inside the table indicate statistical significance. There are negative, moderate and positive relations between people understanding about KMP indicators and organizational productivity. From the above table the researcher wants to know or answer the question of “Is there a relation between people understanding about KMP available in the factories and organizational productivity”? Awareness of KMP has negative relation on who knows KMP but .000 sig < 0.01 this means any professionals know about KMP has a great impact for organizational productivity. All the above negative relationship and 000 sig. value shows the result of one KMP indicator is not affect the other KMP indicator but both the availability of KMP indicator has significant to organizational productivity. Knowledge management practices with productivity in Dire Dawa national and Ture cement factoriesTable 4 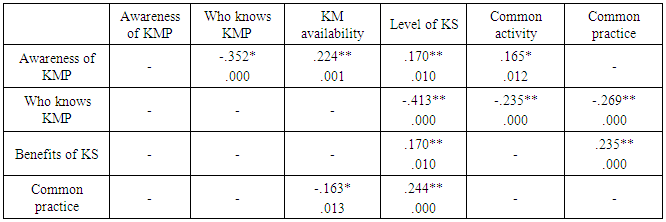 |
| |
|
Table 5. Satisfaction level of respondent for organizational productivity 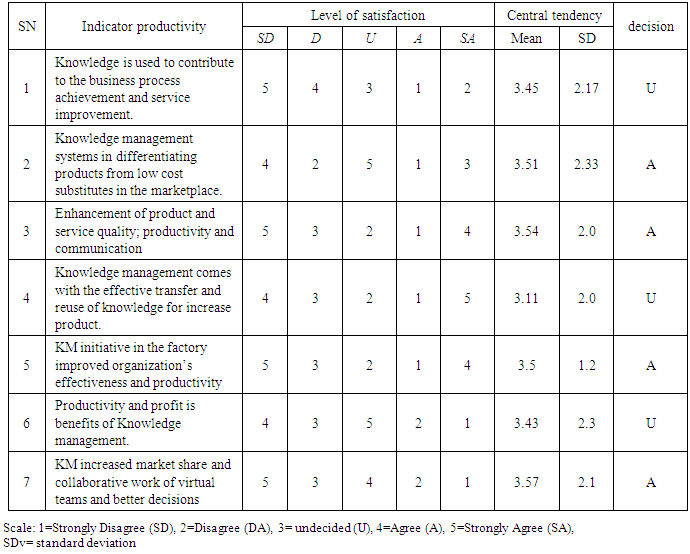 |
| |
|
Today, when customers have questions about an organization’s products or services, they have many options from which to choose. To determined knowledge management practice for productivity, Question that is identifying the relation between knowledge management practices with productivity was asked to Dire Dawa national and Ture cement factories employee. The responses given by the respondents are given in table 5 above.In the above table the percent of respondents decision was undecided and agree in all statements, it is the relation to consider indicator listed from 1-7 as knowledge management practice on productivity. In Dire Dawa national and Ture cement factories “knowledge is used to contribute to business process achievement and service improvement, knowledge management systems in differentiate products from low cost substitutes in the market place, enhancement of product and service quality for productivity and communication.Knowledge transparency and retention was the major outcome of knowledge management, knowledge management in both factories deal with the effective transfer and reuse of knowledge for productivity. KM initiatives in the factory improved organization’s effectiveness and productivity this productivity and profit was the benefits of KM, increased market share; better achievement of strategic objectives ,collaborative work of virtual teams for better decisions and improved sharing of knowledge with employees, customers; increase in knowledge reuse are all indicator of knowledge management practice for organizational productivity with the mean value of the statements 3.45, 3.51, 3.54, 3.11, 3.5, 3.43, 3.57 and 3.6 respectively. The important findings of this research with majority respondents’ decision neither undecided nor agree but close to undecided and also neither agree nor strongly agree but close to agree on the above statements are indicator of availability of knowledge management practice for organizational product change in Dire Dawa national and Ture cement factories. Organizational product and service improvement come with available knowledge inside that factories, from the respondents decision, the highest percent of agreement came on knowledge management system in different product with low cost, over the indicator of increase knowledge reuse improve production process, improved sharing of knowledge with employees, customers and increases knowledge reuse for improved production processes. Knowledge management initiative improved organizational effectiveness and productivity, enhancement of product and service quality and communication were the major outcome of knowledge management and the importance of knowledge management is increased market share; better achievement, improved transparency, collaborative work of virtual teams and better decisions were another indicator of knowledge management for organizational productivity with mean values of 3.5,3.51 and 3.54 respectively, the respondents decision on the above statements neither undecided nor agree but close to agree. This respondent’s decision of agree indicated that knowledge management give strength for organizational effectiveness and productivity with customer need. Similarly, knowledge management come with effective transfer and reuse of knowledge for increase product by respondents opinion with the small mean value 3.11 is another indicator of knowledge management with organizational productivity, this respondents decision indicates some respondents doesn’t have clear idea about organizational knowledge management with the effective transfer and reuse of knowledge in the factories because they haven’t know about knowledge transfer and reuse.The final Pearson correlation cheek by the researcher was identify the relation between KMP with productivity by checking the current statuses of the organization and indicator of productivity in the factories. Finally the researcher wants to identify the relation between KMP and organizational productivity by asking the question “Is there relation between KMP and organizational productivity”. The response of Pearson correlation is summarized in table 6 below:Table 6. Pearson correlation between KMP and productivity 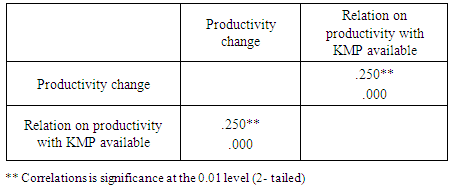 |
| |
|
From the above table the researcher get the answer “Is there relation between KMP and organizational productivity”; KMP has positive relation with productivity because organizational productivity change has positive relation with available KMP in the factories. Similarly KMP available in both factories come with organizational productivity with .000 sig. value, this indicates that the impact of KMP on organizational productivity change and KMP has positive relation with productivity.Proposed Framework for product improvementImproving manufacturing productivity involves collecting and analyzing data and makes effective decisions. Knowledge management was an integrated approach to create, capture, share and apply knowledge to enhance organizational productivity, profitability and growth. From the result of the present study, knowledge management has a relation with productivity in Dire Dawa national and Ture cement factories. Knowledge management, technology, policy and culture were the main input or facilitator for organizational productivity. The proposed framework has created collaboration with the above productivity facilitator with organizational culture and also creates collaboration between knowledge management environments with a business environment. The availability of knowledge management practice was the strength of Dire Dawa national and Ture cement factories. The result of the current study showed that knowledge application is nearly not practiced/ less practiced, which shows a gap in KMP, because application of the existing and created knowledge was a very important practices and this needs correction. Even if the factories identify and create what knowledge needed, then captured for reuse purpose and share for an employee that needs this knowledge, the final result was applying knowledge towards improving productivity. Knowledge management practices without full life cycle was difficult to accept as fully functional, so knowledge should be applied in the factories with full cycle and life cycle of knowledge management needs technological support.Knowledge management controls the effective transfer and reuse of knowledge, increase productivity and profit. The statement productivity was benefit of knowledge management was found to be below 50% agreement because the total respondents of current study do not fully accept productivity was benefit of knowledge management, this problem creates the other separate environment that was knowledge management and business environment, this needs improvement or both environments work each other. From the current study the ultimate goal of knowledge management practice was improving organizational productivity and profit. The proposed framework, depicted in figure 4.6 below contains two environments, knowledge management process environment and business process environment. Under knowledge management process environment, knowledge was processed and in business environment business was applied. In the proposed knowledge management framework, knowledge was available in the form of tacit and explicit inside and outside the organization. Knowledge expert was the main attribute in this proposed framework; those experts accept tacit or explicit knowledge. Knowledge management experts have been using techniques for accepting tacit and explicit knowledge that techniques was social network analysis, systems analysis, processing map, focus group sessions, and one-on-one interviews with key employees. The ultimate goal of this proposed framework was by using managed knowledge inside the factories inside knowledge management environment collaborate with the business environment to facilitate or increase organizational productivity. Externalization, internalization and socialization were the process of knowledge around the organization, top manager, middle manager and employees were actors or facilitators inside the organization. Knowledge may be tacit or explicit and knowledge process takes by externalization from the outside world, by internalization takes knowledge available in the factories or knowledge process in a socialized way in between them. Knowledge flows inside the factories take from the top manager to the employees or vice-versa. Knowledge management environment was attribute of the proposed knowledge management framework, in knowledge management environment knowledge management practice was processed that was knowledge create, knowledge capture, knowledge share and knowledge application. Capture was the first knowledge management practice in the proposed knowledge management framework. Knowledge evaluation comes at the time of knowledge capture, before knowledge capture it needs evaluation because knowledge it may or may not be importance for the factory. Value, accuracy and relevance were way of knowledge evaluation. Knowledge filter was the second knowledge management practice in the proposed framework; knowledge filter takes after knowledge to be relevant for the factories or after knowledge capture. Organization, classification and categorization were preparation or filtering methods of knowledge filtering when knowledge store in the factories database. Knowledge sharing takes after once knowledge organized, classified and categorized in the database, once knowledge filter and stored in the database then knowledge easily share inside the factories and finally knowledge application takes place when the request came from business environment. Business environment was the second main attribute in the proposed framework, this environment encompasses all internal and external factors that affect a company’s operations and include strengths, weaknesses, internal power relationships and orientations of the organization, nature of economy and economic conditions, social and cultural factors, demographic trends, natural factors, global trends and cross-border development, clients and suppliers, technological developments, laws and government activities. Surrounding, which have direct or indirect bearing on the functioning of business, knowledge application depend on business environment request, the request comes in the form of subjective or objective, finally the system answered the request by the support of knowledge expert with considering the factory people, policy culture and technology that was available in the factories. People, policy, culture and technology were actors and facilitator in business environment. The final goal of this proposed framework was to use knowledge management environment inside business environment and give organizational productivity for the cement factories. The final attribute or output in the proposed framework was productivity, quality and profitability, accordingly, the following framework is proposed. 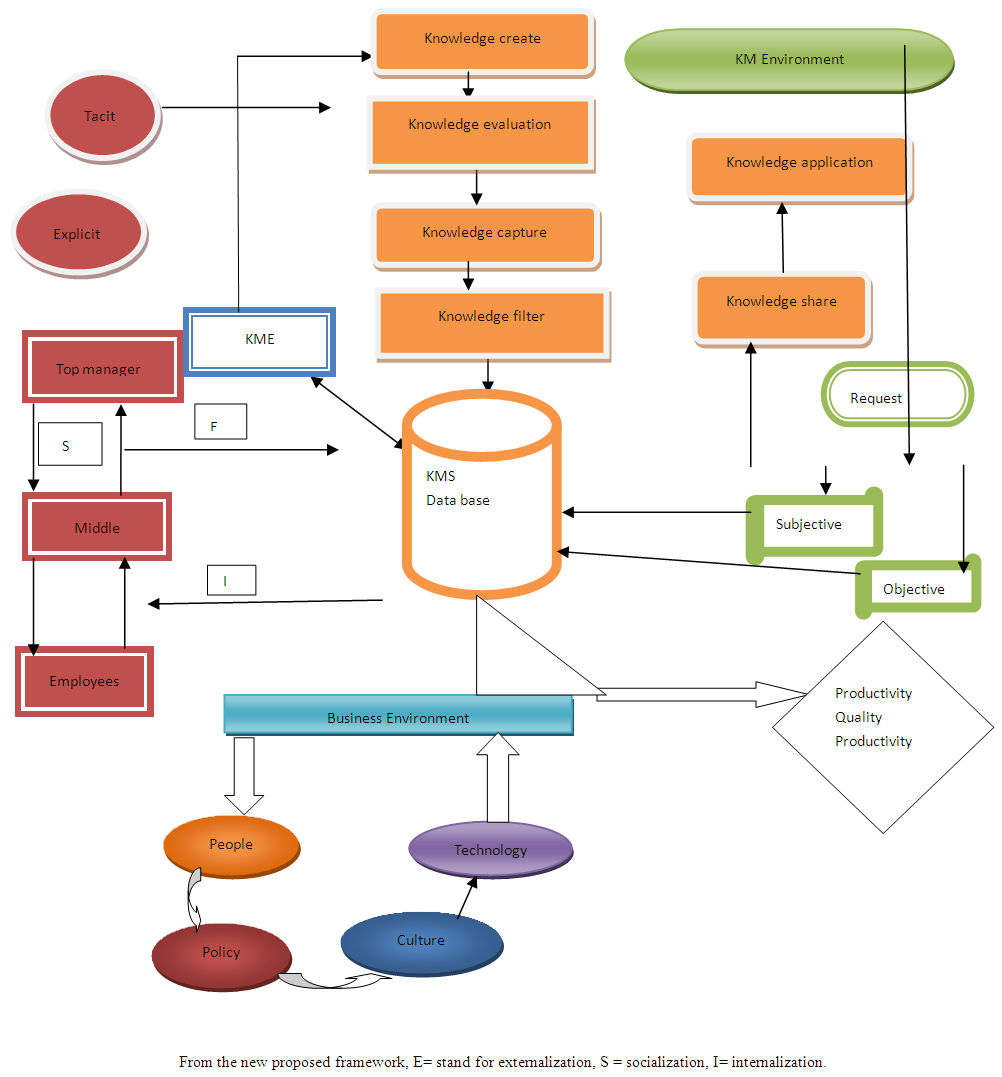 | Figure 4.6. Proposed knowledge management frameworks |
5. Conclusions and Recommendations
ConclusionsThe study showed that, KMP such as knowledge creation, knowledge capture; knowledge share, knowledge preservation and knowledge application are available and exercised in both factories. The applicability of organizational knowledge is affected by organizational knowledge capturing process. Awareness about KMP increased among employees through time to time. Incentive was the main issue when KMP exercised; whereas, workshop; training and document are used as knowledge sharing mechanism. KMP is used for business process to achieve product quality, market share, and collaboration among employees. The relationship between productivity and available knowledge in the factories depends on people, ICT facility and organizational existing policy available in the factories. The non availability of KM policy and limited capacity knowledge expert are problems that hinder implementation of KMP in their factories. The study also concludes currently both cement factories have two environments those were KM processes and business process environment, this two environment works separately, so the research propose KM framework for creating collaboration for those environment.RecommendationsWillingness of managers and employees who participate in create, capture, share and application of knowledge in both factories depends on their motivation, since there was a meaningful relationship between KMP and organizational productivity, both factories must consider all those people who participate in KMP and gave the necessary training on KMP, approaches, policy, objectives and the importance of knowledge management. They also give incentive strongly to motivate the employees in order to ensure sustainable participation in KMP. Even though KMP were available, knowledge application was the final KMP and this practice have relation with knowledge capture in those factories. Therefore, the managers of both factories should give due attention to knowledge capture because it is the base of knowledge application and develop a strategy so that each and every knowledge that could contribute towards productivity improvement and increase organizational productivity be capture for application. An increased understanding the role of knowledge and KMP for those types of manufacturing industry in particular will most probably lead to good returns in productivity and social benefits. Both factories create knowledge center and introduced the use and available good practices in their factories.Effective KM helps an organization adjust quickly its business processes in accordance with current conditions, which especially becomes noticeable in times of frequent and dynamic changes. Efficient KM enables employees to use knowledge, and other resources more efficiently, both factories create efficient KM enables in the facility. In both factories, education was the base of organizational productivity and everyone in their factories needs to learn, so organization more work on culture of education and proved educational chance for employees. KM environment and business environment have link. Therefore the researcher strongly recommends for both Dire Dawa national and Ture cement factories to implement the proposed framework.
ACKNOWLEDGEMENTS
The authors would like to thank all of the participants of Jimma University and thanks to Jimma University, college of Natural Science for funding this research.
References
[1] | Adish K., (2006). Survey of KMP in Indian manufacturing industries, journal of knowledge management, Vol. 10 Iss: 6. |
[2] | Ajmal, M., Helo, P&Kekale, T. (2010). Critical factors for KM in project business, journal of knowledge management, 14 (1), 156- 168. |
[3] | Alan Hughes and Michael S. Scott Morton (2005). ICT and productivity growth – the paradox resolved? c enter for business research, university of Cambridge, working paper No. 316. |
[4] | Alavi, M. And Leidner, D. E. (2001). KM and KM systems: conceptual foundations and research issues, MIS Quarterly, 25 (1), 107- 113. |
[5] | Amir Honarpour, Ahmad Jusohand KhalilMd (2012). Nor journal of technology management & innovation university dada lberto Hurtado, Facultay de Economíay Negocios, 2012. |
[6] | Arthur Andersen and APQC (1996). The KM assess ment tools: external benchmarking version. |
[7] | Beimborn, D., Moos, B., Wagner, H.- Th. (2010). The impact of KM on absorptive capacity”, proceedings of IFIP 8.2/organizations and society in information s ystems (OASIS), sprouts: working papers o n information sy stems, Vol. 10. |
[8] | Fischer, Ulli; et. al (2000). System Concept, The project PICK (IST–1999-10442), improvement in manufacturing companies e-Business and eWork Conference, Public report Madrid, October 2000. |
[9] | Fugate, B.S., Stank, T.P. & Mentzer, J.T. (2009). Linking improved knowledge management to operational and organizational performance, Journal of Operations Management, 2009. |
[10] | Martin, V. A. et al. (2005). Cultivating knowledge sharing through the relationship management Maturity model, The Learning Organization, Drivers, and Performance Implications, working-paper, Boston: Harvard Business School, 2005, 12 (4), 340–354. |
[11] | Nonaka, I. (1994). Dynamic Theory of Organizational Knowledge Creation', Organization Science (1): 14-17. |
[12] | Zheng, W., Yang, B. & McLean, G.N. (2009). Linking organizational culture, structure, Strategy and organizational effectiveness mediating role of knowledge management, article in press, 2009. |