Diego Christoforo Petrassi1, Felipe Nascimento Arroyo2, Diego Henrique de Almeida3, André Luis Christoforo2, Francisco Antonio Rocco Lahr4
1Production Engineering Department, UniSEB University Center (UniSEB), Abrahão Issa Halack Street, Ribeirão Preto, Brazil
2Centre for Innovation and Technology in Composites – CITeC, Department of Civil Engineering (DECiv), Federal University of São Carlos, São Carlos, Brazil
3Department of Engineering, Pitágoras College, Poços de Caldas, Brazil
4Department of Structural Engineering, University of São Paulo, São Carlos School of Engineering (EESC/USP), São Carlos, Brazil
Correspondence to: André Luis Christoforo, Centre for Innovation and Technology in Composites – CITeC, Department of Civil Engineering (DECiv), Federal University of São Carlos, São Carlos, Brazil.
Email: |  |
Copyright © 2017 Scientific & Academic Publishing. All Rights Reserved.
This work is licensed under the Creative Commons Attribution International License (CC BY).
http://creativecommons.org/licenses/by/4.0/

Abstract
This research has the proposal create a simulator to valuate and simulate the capacity of a sugar factory, supporting the strategic decision making process. The process of creating simulator starts when processes are mapped and all most important variables are defined. After that it was necessary to transmit measured data through the calculations for spreadsheet, which in this case was used Excel (because it is a simple language and a common program). In sequence, several tests were performed to check results obtained by simulation. The results refer to the simulator reliability, with comparison of SIMULSUGAR results with simulation conducted in sector. Creating a table was necessary to demonstrate the accounting comparison between SIMULSUGAR results with simulation performed in the sector.
Keywords:
Capacity, Simulation, Sugar manufacturing
Cite this paper: Diego Christoforo Petrassi, Felipe Nascimento Arroyo, Diego Henrique de Almeida, André Luis Christoforo, Francisco Antonio Rocco Lahr, Development of Alternative Simulator for the Sugar Manufacturing Process, Science and Technology, Vol. 7 No. 2, 2017, pp. 54-60. doi: 10.5923/j.scit.20170702.03.
1. Introduction
Based on data, forecasts and market analyzes, sugar and alcohol industry plants practice the continuous search for improvements. This fact indicates that it is necessary and extremely important create indicators to control production and create technical parameters or standards. Standards created from process indicators should be considered as operational rules, thus optimizing production, reducing losses and improving industrial performance.With indicators creation for the processes, comes up the necessity to control them, so that programs, software’s or simulators meets as interesting alternatives. The advantage of using a simulator is that, with little information, there are complex and well-directed responses to productive processes.Employing simulation for planning and decisions in production of sugar with relation to its productive capacity are essential strategies for its development, related with the industrial power of growth [1].Objectifying identify possible process problems, its necessary to point out the critical points of productive system, responsible for inhibiting productive capacity and reducing industrial performance [1].It is understood that production capacity variations require attention. There are two types of variation, the smaller than productive capacity and the one that for some reason is larger than productive capacity. It is important understand them and especially identify them, because if the capacity is limited by any process or equipment, this process or equipment, in a possible expansion, should be resized. Already when this capacity of the process or equipment is greater than productive capacity, this process or equipment cannot be resized, since any action in this direction is unnecessary investment.In this sense, when it comes the sugar manufacture and encompassing all specifications, it is understood that sugar factory is nothing more than an extraction industry, considering the fact that sugar is produced naturally by sugar cane. Then, sugar factory only concentrates this product during process, following the proper specifications [6, 7, 8, 10, 11, 15, 16, 19, 22, 24 and 25].It is known that one of the major concerns in sugar production is how much sugar can be recovered and how much by-product is generated. These by-products are stored, and are reprocessed in order to extract as much sucrose as possible.In this way, the production line must be properly calibrated so you can receive the broth in order to concentrate it and extract the sugar. Following this, the intermediate equipment capacity, that receives the broth and has the function of storing, processing and sending it to continue the process, must be fully known. Knowing these capabilities is necessary so that there are no surprises during manufacturing time, knowing that the production is continuous.The constant changes in the market forces professionals to constantly change the process. Because they do not have quick and accurate knowledge of the effect on final products, these actions, incur the underutilization of equipment, and especially efficiency losses [6, 7, 8, 10, 11, 15, 16, 19, 22, 24 and 25].Finally, to make changes, it is necessary to foresee the processes and mainly equipment capacity. Thus, developing a tool that generates a strategic vision for making decisions regarding new goals and goals established for organization is the proposal of this work. Thus, software was developed to evaluate problems inherent to the production cycle, making use of a case study.The general objective of this work is develop a simulator that assists in planning and operational decisions related to the productive capacity of sugar and alcohol industry plants, specifically in sugar manufacturing process.THEORETICAL REVIEWSugar and alcohol industrySugar cane was introduced in Brazil along with Portuguese colonization in 16th century, more precisely in 1532, when Martin Afonso de Souza founded the town of São Vicente in São Paulo, creating the first sugar mill in Brazil, named São Jorge. In 1550, Brazil assumed the position of largest producer of sugar in the world. The first sugar mill was founded in the captaincy of Pernambuco, which belonged to Duarte Coelho, due to the ideal soil and climate capacity of region and driven by the disposal ease of sugar produced for Europe [4].The sugarcane sector came increasing, when crisis of 1929 made explicit problem that the sector faced. In this period, organs were established to regulate the sector and directed actions that should be taken, the DCSP - Defense Commission for Sugar Production and later SAI - Sugar and Alcohol Institute. Since then, sector has achieved great growth in domestic market, as well as in international market. Certain historic landmarks made possible the country obtain new markets to commercialize sugar cane products, such as Revolution in Cuba, making it open to new markets such as North American, since most exports would To Europe [4].It is known that around 1990, the 'Proálcool’, a measure taken to protect produced alcohol in the country, adopted a percentage of alcohol that should be added in gasoline, forcing production in the country. However, this percentage increase further, creating greater incentives for sector production and establishing fiscal incentives, causing invest even more in ethanol. Finally, market had a rise when alcohol vehicles appeared and recently was expanded with the emergence of flex-fuel vehicles, which run on both: ethanol and gasoline [1, 3, 5, 14 and 21].The sugar and alcohol industry is responsible for harvesting and processing about 32.7 million tons of sugarcane, and is intended to increase by 3.25% through the 2018/19 harvest, corresponding to a processing of 47.34 million tons. The estimated projection of ethanol production is around 58.8 billion liters and domestic consumption market is estimated in 50 billion liters, with 8.8 billion going to foreign market. The ethanol produced in Brazil is subject to expansion in the coming years, also due to the consumption growth by domestic market [13].Table 1 present sugar production projections, consumption and exports, comparing the harvest (2012/13) with estimate for 2021/22 harvest. These data indicate the expected growth for domestic and external sectors.Table 1. Projection for 2021/22 and 2012/13 harvest 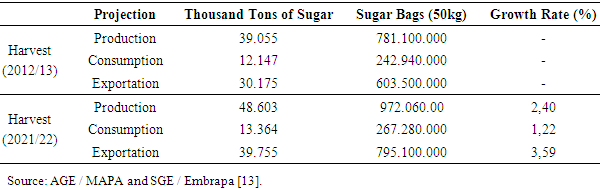 |
| |
|
SimulationDictionaries define simulation as: "functioning representation of one system or process by the operation of another (computer simulation of an industrial process); the analysis of problem not always subject to direct experimentation, by use of a simulation device." And simulator: "what simulates; specifically a tool, which enables operator to reproduce or represent a phenomenon under test conditions, just as it does in its actual performance” [23].For being versatile, flexible and powerful, simulators can be applied to any study or research. There are large ranges of applications; we mention some of following simulator applications [18]:Computational Systems: hardware components; software; computer networks; database structures and management; information processing; and hardware and software reliability.Manufacturing: material handling and storage systems; assembly lines; automated production and storage facilities; inventory control systems; maintenance studies; plant layout; and machine design.Business: commodity analysis; pricing policy; marketing strategies; business acquisition studies; cash flow analysis; forecasting; transportation alternatives; and workforce planning.Government: military armaments and tactics; population growth forecast; land use; health system; fire systems; police; criminal justice; road projects; traffic control; and sanitation services.Ecology and Environment: water pollution and purification; waste control; air pollution; pest control; weather forecasting; earthquake and storm analysis; mineral exploration and extraction; and solar energy systems.Society and Behavior: food / population analysis; educational policies; organizational structure; analysis of social systems; and university administration.Biosciences: analysis of sports performance; biological life cycles; and biomedical studies [18].Simulation predicts the complex systems behavior by calculating movement and interaction of system components. By flow evaluating of parts through machines and workstations, and examining demand conflicts for limited resources, we can evaluate Layouts, equipment selection, and operating procedures. Simulation gives us the experiment ability in model preferably to real system [23].It is known that simulations have advantages and difficulties. Among advantages is productive bottlenecks identification. To simulate new situations related for future events, it is necessary identify causes and consequences from simulations. As difficulties, there is a need to carry out trainings, enabling those involved with the simulation [18], besides the high costs involved with processors to be used. For simulation represent actual process well, the level of detail must be large. However, how bigger the level of detail is, greater will be susceptibility of simulation to convergence of its mathematical models.Phases of a simulation projectKnowing that simulation projects are not literally identical each other, it is possible to identify three distinct phases: Modeling; Programming; and Experimentation [20].Programming represents 30 to 40% of total project time (or study). It is understood that much of this time is concentrated in stage 1 (modeling) and experimentation obtains the smallest part of time in simulation projects [12]. Figure 1 shows simulation steps.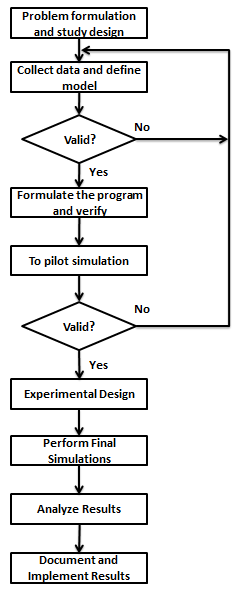 | Figure 1. Simulation steps Flowchart [12] |
Sector SimulationWhen we talk about simulation in sugar and alcohol industry, we always think in simulation taking into account a production mixture, which is divided into sugar, ethanol (being anhydrous and hydrated), yeast production and consumption and energy generation [6, 7, 8, 10, 11, 15, 16, 19, 22, 24 and 25]. In this case, it is interesting note that the vast majority of works found and commercial software follow the production line as a whole.Sugar production processNowadays and as a general trend for sector, sugar manufacturing process seeks a highly qualified product with good recovery from sugar factory, which is the goal for sugar mills. Knowing that bad quality of sugar due to abnormal sugarcane factors, like the physical-chemical and microbiological characteristics of this raw material, has as fundamental quality factor of the raw material. It reinforces the concern with sugar technologies manufacturing process, in order to meet the increase in sugar demand and also quality standards demanded by market, both internal and external [2].
2. Material and Methods
SettingsIt is necessary know some concepts that are important for methodology part understanding. Are they:- Soluble solids: are all dissolved solids in solution of cane (broth). Among them are: sugars, organic sugars, amides, salts, gums, pectins, etc.;- Brix: represents the soluble solids percentage present in the solution. It is the most used parameter in sugar and alcohol industry, for process control;- Recovery: indicates the sucrose amount that has been converted into final product. Generally speaking, a high recovery from sugar factory indicates that it extracts much of the sucrose and loses fewer sugars in the by-products.Assembly simulatorSimulator construction is aimed to calculating the capacity of sugar manufacturing equipment. The initial work part, which is linked to modeling, encompasses the equipment capacity and layout of the same. It is important note that equipment capacity is linked to sugar production, which is accounted for daily.To better understand the studies carried out, is important to know a little about manufacture of sugar, products and by-products generated. Figure 2 illustrates sugar manufacturing process.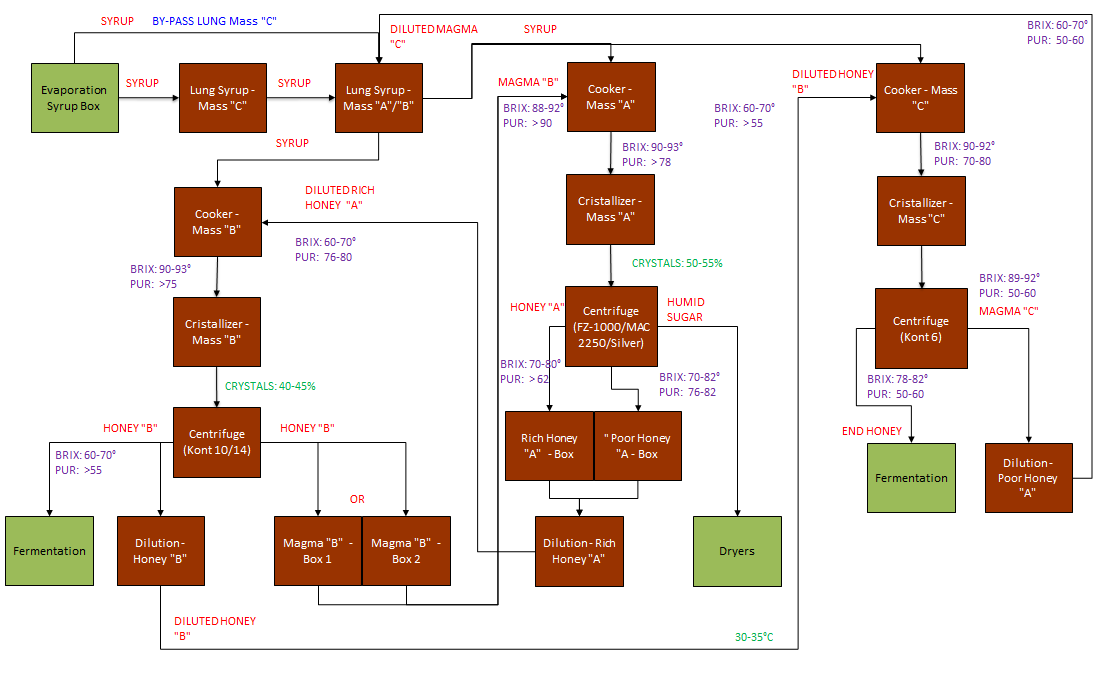 | Figure 2. Sugar manufacturing process |
Then, starting from daily production, it was possible to make mass balance of sugar manufacture and also verified the quantity generated of each product, by-product and how much would be sent to sugar loading line. Loading part of sugar has also been studied, being important note that all sugar produced is obliged to go through loading line, and this line has a disarming system, which can undermine the previous process. Knowing that theory and reality should complement each other, this being the main purpose of simulation, it was necessary to research and assess the individual design capacity of all equipment that was on sugar way. Allied this factor, individual availability of equipment is also followed. This indicator was taken into account for calculation base and made the simulator even closer to reality.Fieldwork and research were carried out in a sugar-alcohol plant located in vicinity of Guariba-SP, with processing capacity of 42,000 tons (75,000 bags, considering 50kg sugar bags) sugar cane per day. After completing calculations and balances performed, then the work programming phase enters. In this case, programming platform used was Excel, which presents simple and familiar interface and friendly language. In this phase, information checked for spreadsheets was passed.Finally, after performing the programming in Excel, tests and part of experimentation are performed. At this stage, carry out simulations is necessary and confront with real data taken from process, the greater interest is show the reliability of simulator created (SIMULSUGAR).SIMULATOR USINGTable 2 presents simulator interface. As a general rule, all spaces that are filled with light blue should be filled with industry information. At every cooking is necessary to cut half of the mass. This cutting process is referred as “Cuts Number” in this table.Table 2. Simulator interface – First Step 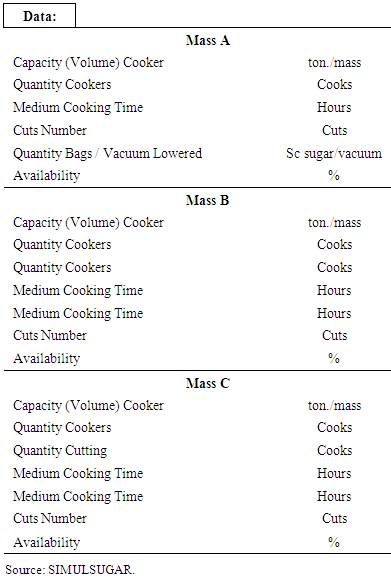 |
| |
|
Table 2 shown above is the first step within SIMULSUGAR. Informed data must contain information on the process and company equipment. Such information is processed and interacts with percentage of crystals in cooked mass. As represented in following formula. | (1) |
Amount of sugar, represented by
indicates the amount of sugar when processing "A" mass, amount of magma when processed "B" and "C" mass. In this case, mass processed in centrifuges continues and discontinues. The
refers to the mass cookers volume "A", "B" and "C". The TCM indicates the content of mass crystals, being 50% in mass "A", 45% in mass "B" and 45% in mass "C". [9, 17] | (2) |
Honey amount generated,
indicates the honey amount that will be generated in three masses ("A", "B" and "C"). This fact is important as we have seen. Companies are looking for a good factory recovery, nay, and a good use of sugar in process. This fact indicates how much material is being processed or will be in processing. [9 and 17]It is also known that in addition iterations with equipment capacity, also allied with amount of existing equipment in order to identify the actual capacity of plant and/or equipment.Therefore, the part concerning new installations should be filled in. In this case, indicated places are supplied with data referring to processes and equipment. Table 3 shows the part referring to new installations.Table 3. Part related to New Installations 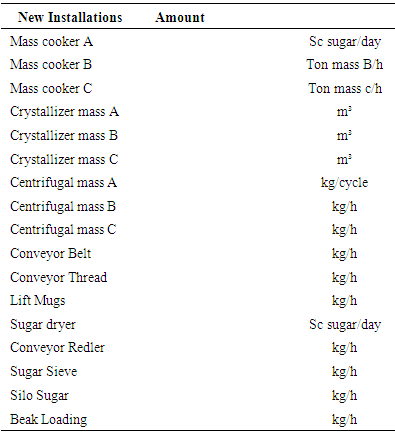 |
| |
|
In related area to new SIMULSUGAR installations, again in light blue guides, it is necessary supply with information regarding the equipment capacity. Such information interacts with performed calculations in data area of worksheet, and with simple functions within Excel as conditional formatting crosses the entire production line (sugar path in process) and informs whether it is capable or not. If you are unable, SIMULSUGAR makes simple suggestions, such as installing new equipment.In Figure 3, SIMULSUGAR interface will be shown.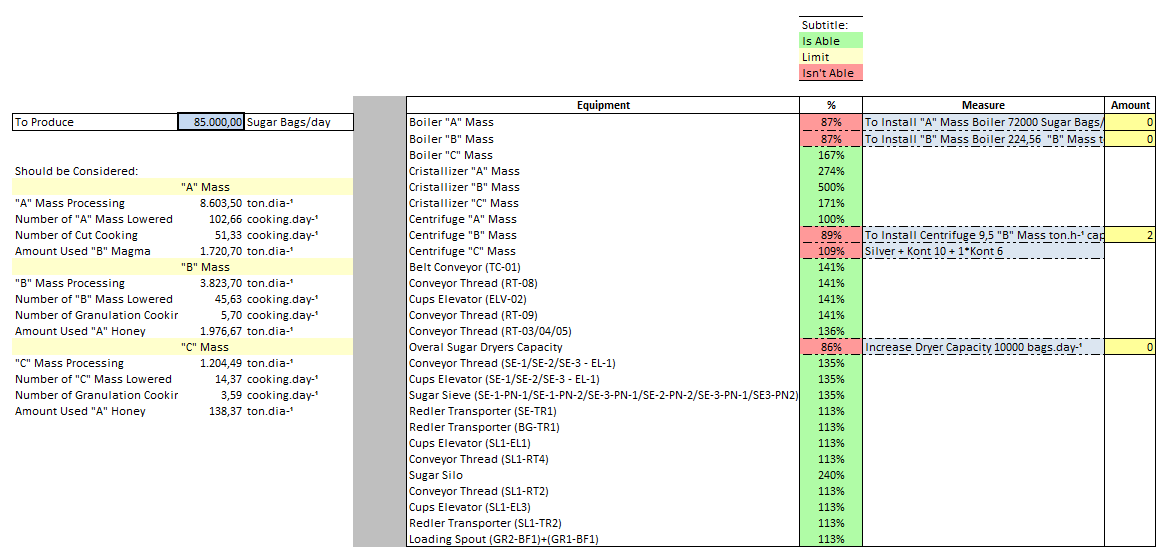 | Figure 3. SIMULSUGAR Interface |
Finishing simulation, the main parameter of sugar production in bags per day (bags of 50 kg) must be placed. In this way, iterations are performed and the quantity of each product in process in masses "A", "B" and "C", whether the equipment is capable or not.Adopted a color reference, where green color indicates that the equipment is capable, red color is not able and if the color is yellow the equipment has its limit of capacity. In the case of red light, it would be necessary to take some measures to make the equipment capable. It is still observed how much the capacity of equipment(s) is lacking, presenting value in percentage.
3. Results and Discussion
Evaluating SIMULSUGAR's efficiency and confidence, a comparison was made with mass and energy balance of the case study carried out. It is important note that the objective of simulator is to evaluate productive capacity and assist in decision-making process. Ergo, balance used as comparative only evaluates how much material will be generated and will be in process.The existing equipment and tanks in process have capabilities stipulated in their respective projects. To evaluate these capacities, design capacity product of each equipment was found by availability of equipment time, demonstrating the actual capacity of this equipment’s. Subsequently, these capacities were compared with masses capacity calculated, finding the equipment capacity.Comparisons made correspond to capacity calculated, in other words, the technical power of SIMULSUGAR was evaluated. Table 4 shows some comparison data.Table 4. Comparison of SIMULSUGAR with Mass Balance Report and Energy of Sugar Manufacture 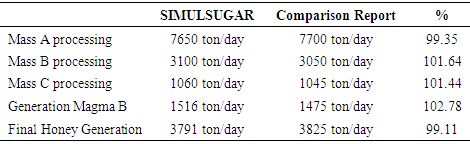 |
| |
|
The comparison presented in Table 4 shows how much mass should be processed from "A", "B" and "C" and also how much should be generated from Magma "B" (from Mass processing "B") and how much must be generated from Final Honey (from Mass processing "C"). These are the most important data in the process, as it indicates how much material will pass to all subsequent equipment on production line.Data are taken from SIMULSUGAR, as well as from mass and energy balance used for comparison, simulating a production of 74,904 sacks of sugar/day, which is equivalent to 3,745.2 tons of sugar/day. Table 4 also shows the SIMULSUGAR discrepancy compared to Comparison Report.
4. Conclusions
SIMULSUGAR besides simple interface has the advantage of using Excel, which is a common and simple programming tool.Analyzing parameters that were used for comparison, it was observed that ratio between SIMULSUGAR and Comparison Report is small, even being disregarded. Parameters evaluated in comparison were found in surveys carried out and are the process indicators that should be taken into account, since such points are essential to identify problems of productive capacity.SIMULSUGAR presents an interesting feature, despite need to supply it with process information, the difference is realize that it does not require so much data to perform simulations. It is necessary supply the program with data of equipment in process and then it becomes simple. In this case, only put the desired sugar production value (in 50 kg sugar bags) and it will bring the main information of line production. It is also shown if the equipment restricts production in specific cases.SIMULSUGAR was able to reproduce a real production situation of a sugar-alcohol plant located in vicinity of Guariba-SP city.In this sense it is possible perceive the power of SIMULSUGAR, which becomes a powerful tool to aid decision-making process with respect to productive capacity.
References
[1] | AIAA – Associação das Indústrias de Açúcar e de Álcool do estado de São Paulo, 1991. O setor canavieiro e sucroalcooleiro no ano 1990. (não publicado). |
[2] | Albuquerque, F.M. Processo de Fabricação de Açúcar. Editora Universitária UFPE, 2011. |
[3] | Baccarin, J.G. A constituição da nova regulamentação sucroalcooleira. Brasília, Universidade de Brasília (caderno do Ceam). São Paulo, Editora UNESP, 2005. |
[4] | Ciclo da Cana de Açúcar – História Brasileira <www.historiabrasileira.com>. Acesso em:20.fev.2013. |
[5] | Costa, M. L. O. Setor sucroalcooleiro: da rígida intervenção ao livre mercado. São Paulo, Editora Método, 2003. |
[6] | Dal Bem, A.J.; Koike, G.H.A; Passarini, L.C. Modelagem e simulação para o processo industrial de fabricação de açúcar e álcool. São Paulo, 2004. |
[7] | Yu, D.; Wensheng, L.; Yi, P. A relationship model of brand marketing strategy and agribusiness dynamic capability. Advances in Intelligent Systems and Computing, 8th International Conference on Management Science and Engineering Management, Portugal, v. 280, p. 385-396, 2014. |
[8] | D´Haese, M. A net chain development perspective on wool farmers’ associations in poor communities a case study in South Africa. Journal on Chain and Network Science, Wageningen, v. 7, n. 1, p. 11-20, 2007. |
[9] | Fernandes, A.C. Cálculos na Agroindústria da Cana-de-Açúcar. Editora EME, 2003. |
[10] | Kelton, D. W.; Sadowski, R.P.; Sadowski, D.A. A simulation with arena. New York: McGraw-Hill, 1998. |
[11] | Gergely, P; András, P.; László, M. Generic data structure and validation methodology for simulation of manufacturing systems. International Journal of Computer Integrated Manufacturing, v. 29, n. 12, p. 1272-1286, 2016. |
[12] | Frantzen, M.; Amos, N. H. C. Production simulation education using rapid modeling and optimization: Successful studies. Proceedings – Winter Simulation Conference, p. 3526-3537, 2016. |
[13] | MAPA – Ministério da Agricultura, Pecuária e Abastecimento. Projeções do agronegócio Brasil – 2011/12 a 2021/22. Acesso em: 06.mar.2013. |
[14] | Natale Netto, J. A saga do álcool: fatos e verdades sobre os 100 anos do álcool combustível em nosso país. Novo Século Editora, 2007. |
[15] | Neves, M.F.; Conejero, M.A. Estratégias para a cana no Brasil: um negócio classe mundial. São Paulo: Editora Atlas, 2010. |
[16] | Neves, M.F.; Trombin, V.G.; Milan, P.; Lopes, F.F.; Cressoni, F.; Kalaki, R. O retrato da citricultura brasileira. MARKESTRAT - Centro de Pesquisa em Marketing e Estratégia. Ribeirão Preto, 2010. |
[17] | Payne, J.H. Operações unitárias na produção de açúcar de cana. Editora Nobel, 1989. |
[18] | Albert, P.; Francesc, C.; Jan, R. A computer-aided simulation analysis tool for SIMAN models automatically generated from petri nets. International Mediterranean Modelling Multiconference, p. 57-62, 2006. |
[19] | Pessoa, P.F.A.P.; Cabral, J.E.O. Identificação e análise de gargalos produtivos: impactos potenciais sobre a rentabilidade empresarial. Porto Alegre, 2005. |
[20] | Oslin, B. Technology of simulation modeling by using universal programming languages. Proceedings - KORUS 2003: 7th Korea-Russia International Symposium on Science and Technology, v. 2, p. 193-195, 2003. |
[21] | Ramos, P.A. A evolução da agroindústria canavieira e os mercados de açúcar e de álcool carburante no Brasil: a necessidade de planejamento e controle. Rio Branco, 2008. |
[22] | Slack, N.; Chambers, S.; Johnston, R. Administração da produção. 2ª Edição São Paulo: Atlas, 2002. |
[23] | Vieira, M.C.A.; Lima, J.F.; Braga, N.M. Setor Sucroalcooleiro Brasileiro: Evolução e Perspectivas. Santa Catarina, 2011. |
[24] | Deogratias, K.; Guodong, S.; Bjorn, J. Framework for standardization of simulation integrated production planning. Proceedings - Winter Simulation Conference, p. 2970-2981, 2016. |
[25] | Borrero, M. A. V.; Pereira, J. T. V.; Miranda, E. E. An environmental management method for sugar cane alcohol production in Brazil. Biomass and Bioenergy, v. 35, n. 3, p. 287-299, 2003. |